J. Cent. South Univ. Technol. (2009) 16: 0385-0391
DOI: 10.1007/s11771-009-0065-8

Characteristics of activated carbon prepared from Chinese fir sawdust by zinc chloride activation under vacuum condition
QIU Ke-qiang(丘克强), YANG Su-wen(杨素文), YANG Juan(杨 娟)
(School of Chemistry and Chemical Engineering, Central South University, Changsha 410083, China)
Abstract: The preparation of activated carbon from Chinese fir sawdust by zinc chloride activation under both nitrogen atmosphere and vacuum conditions was carried out in a self-manufactured vacuum pyrolysis reactor. The effects of the system pressure and the activation condition (nitrogen or vacuum) on pore development were investigated. The results show that both high quality activated carbon and high added-value bio-oil can be obtained simultaneously via vacuum chemical activation. The characteristics of the activated carbons produced under vacuum conditions are better than those prepared under nitrogen atmosphere. The performance parameters of the activated carbon obtained under vacuum conditions are as follows: the pore size distribution is mainly microporous, the Brunauer-Emmett-Teller (BET) surface area is 1 070.59 m2/g, the microporous volume is 0.502 4 cm3/g, the average pore size is 2.085 nm, and the iodine adsorption value and the methylene blue adsorption value are 1 142.92 and 131.34 mg/g, respectively. The activated carbon from vacuum chemical activation has developed micropores, and the N2 adsorption equilibrium constant of the corresponding activated carbon gradually increases with the decrease of reaction system pressure.
Key words: activated carbon; bio-oil; Chinese fir sawdust; system pressure; vacuum chemical activation
1 Introduction
Activated carbon is one of the most important microporous adsorbents. It has a developed internal pore structure. With successfully controlled pore size and pore size distributions, activated carbon can be used in supercapacitors [1]. Activated carbon has good adsorption properties. Its adsorption capacity depends on not only its surface area, but also its internal pore structure, surface characteristic and the functional group present on the pore surface. Since all these properties are decided by both the precursor and preparation method [2-3], it is very important to choose an appropriate precursor and a reasonable preparation method to produce high quality activated carbon.
Nowadays, wood and prime coal are the main materials used for the preparation of activated carbon around the world [4-7], thus the high cost of raw materials becomes the key factor limiting the universal application of activated carbon. Therefore, in recent years, there have been many studies focusing on the preparation of activated carbon using inexpensive waste as raw materials. These wastes include nut shells, crop stalks, and biomass pyrolysis residual carbon [8-14]. However, there is no report related to the preparation of activated carbon from Chinese fir sawdust. In this work, the Chinese fir sawdust was used as the precursor for the preparation of activated carbon because of its high volatile content, high fixed carbon content, low ash content, zero sulfur content and low nitrogen content. Fir is one of the Chinese fast-growing timber species and occupies a very important role in the forest reserves and timber production in China. According to the statistics of the State Forestry Administration in 2002, the intermediate cuttings material production of Chinese fir was about 3.796 9×106 m2 [15].
Generally, the activated carbon can be prepared via physical or chemical activation method. In the chemical activation process, the precursors are first impregnated with an activating agent solution. As a dehydrant and deoxidant, the activating agent such as zinc chloride [14, 16], phosphoric acid [14, 17-18], potassium carbonate [19], sodium hydroxide [14, 20], and potassium hydroxide [21-22] influences the pyrolytic process and retards the formation of tars during the carbonization process, thus enhancing the yield of carbon [23]. In chemical activation process, the activation temperature is lower than that in physical activation process, and the pore development in the carbon structure is significantly improved.
Various carbonaceous materials were prepared via chemical activation with ZnCl2, and the effects of different preparation conditions on the characteristics of the activated carbons were studied [14, 16]. The preparation of activated carbons by chemical activation in an inert atmosphere such as helium gas [24], or by physical activation in steam or flue gas for char obtained from vacuum pyrolysis was carried out by many researchers [10-12]. LUA and YANG [25] prepared activated carbon by chemical activation under vacuum from pistachio-nut. However, preparation of activated carbon by chemical activation under vacuum from Chinese fir sawdust has not been reported yet in the literatures. Therefore, in this work the preparation of activated carbon from Chinese fir sawdust by chemical activation with ZnCl2, and the effects of the system pressure and the activation condition (nitrogen or vacuum) on the pore development were investigated.
2 Experimental
2.1 Materials
Chinese fir sawdust was obtained from local timber industries. The proximate and ultimate analyses of Chinese fir sawdust are listed in Table 1. It can be seen that the Chinese fir sawdust has high volatile content, high fixed carbon content, low ash content, zero sulfur content and low nitrogen content.
The particle size of sawdust is 0.28-1.00 mm. After natural air drying, the sawdust was dried at 105 ℃ for 48 h to reduce the moisture content. ZnCl2 pellets were dissolved in water and then impregnated into the Chinese fir sawdust. The mass ratio of ZnCl2 to sawdust was 1?1. The mixture was allowed to dry in an oven at 105 ℃ and then placed in the dryer for later use.
Table 1 Proximate and ultimate analyses of Chinese fir sawdust (mass fraction, %)
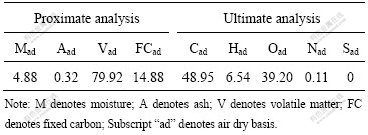
2.2 Equipment and reagents
The equipment used was as follows: stainless steel reactor (self-manufactured), vertical tubular electric furnace (self-manufactured), temperature controller (WTS-1-20Y, Southeast University Institute of Automation Instrumentation, China) and vacuum pump (DP-A, Nanjing Sangli Electronic Equipment Factory, China). The reagents used were as follows: ZnCl2 (analytical reagent, Chemical Reagent Factory of Hunan Normal University, China) and HCl solution (analytical reagent, Zhuzhou Quartz Glass Ltd, China).
2.3 Experimental procedure and methods
2.3.1 Experimental procedure
The schematic diagram of the experimental procedure for vacuum activation of biomass is shown in Fig.1.
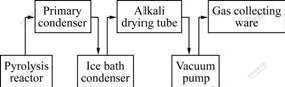
Fig.1 Schematic diagram of experimental procedure for vacuum activation of biomass
2.3.2 Experimental methods
(1) Chemical activation under vacuum. About 8 g ZnCl2-impregnated sawdust was first placed in the reactor, then the reactor was inserted into an electrical furnace for chemical activation under various vacuum conditions (total system pressure around 70.5, 50.5, 30.5, 20.5 and 10.5 kPa respectively). The sample was raised from room temperature to 500 ℃ with a heating rate of 10 ℃/min and held at this temperature for 60 min for activation. After that, it was heated to 700 ℃ with a heating rate of 20 ℃/min and held at this temperature for 90 min. Thereafter, it was cooled to room temperature again. The heating and cooling processes were carried out under vacuum.
In order to collect bio-oil, the temperature of the cold trap was set at -20 ℃. The solid products were first marinated in 0.1 mol/L HCl solution for 12 h. After being heated to boil for 20 min, the products were washed with 0.1 mol/L HCl solution, and then washed with distilled water to remove the residual ZnCl2 until the pH value of the washed solution was between 6 and 7. Finally, the activated carbons as-prepared were dried at 120 ℃ for 12 h. After being ground and sieved to 76 μm, the activated carbons were placed in reserve. The bio-oil was obtained by collecting the liquid products from the condensation pipe and collectors in cold traps.
(2) Chemical activation under nitrogen. About 8 g ZnCl2-impregnated sawdust was first placed in the reactor, and activation process was carried out in N2 gas (99.99% purity) at a flow rate of 150 cm3/min. Other steps were similar to those of the activation process under vacuum.
2.4 Characterization
The pore structure characteristics of the activated carbons were determined by nitrogen adsorption at 77.35 K using a Micromeritics ASAP-2020 volumetric auto-sorption analyzer. The Brunauer-Emmett-Teller (BET) surface area was calculated from the N2 adsorption-desorption isotherms by the BET equation [26]. The micropore volume and micropore surface area were determined by application of Dubinin-Asthakov (DA) analysis software available with the instrument. The micropore structure was characterized by the Halsey equation, and the pore size distribution of activated carbon was determined from nitrogen adsorption isotherm data using the Barrett-Joyner-Halenda (BJH) software. The adsorption equilibrium constant was obtained from the N2 adsorption-desorption isotherms by Langmuir adsorption isothermal equation [27].
The scanning electron microscope of the activated carbon was done with a Thermo Noran Jeol JSM-6360LV microscope.
The iodine adsorption capacity and methylene blue absorption capacity of the activated carbon were determined according to the national standards GB/T 12496.8-1999 and GB/T 12496.10-1999, respectively.
The composition analysis of the bio-oil was performed on a gas chromatography/mass spectrometer (GC/MS-QP2010, Shimadzu, Japan).
3 Results and discussion
3.1 Purification of activated carbon
(1) In order to detach the unreacted ZnCl2 as much as possible, the reactant was heated from 500 ℃ to 700 ℃. ZnCl2 was then drawn off the reactor in the form of steam. During this process, some disorder carbon was burned off, which may widen the micropores [28].
(2) Washing the products with HCl solution can remove the remnants of ZnCl2. Meanwhile, inorganic impurities such as calcium oxide and magnesium oxide in the porous structure can be washed away and thus improve the pore structure.
3.2 Effect of system pressure
3.2.1 Pore structure
Pore evolution of the as-prepared activated carbon with varying system pressure is shown in Fig.2, and the detailed textural properties of these activated carbons are listed in Table 2.
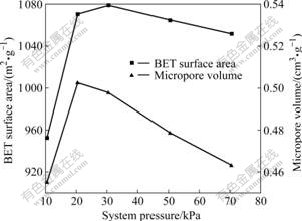
Fig.2 Variation of BET surface area and micropore volume of activated carbon with system pressure
Table 2 Variation of activated carbon pore structure with system pressure
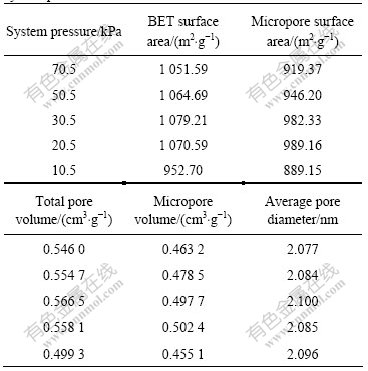
From Fig.2, it can be seen that the BET surface area and micropore volume exhibit similar trends. The BET surface area and micropore volume curves exhibit peaks with the variation of system pressure. Decreasing the system pressure from 70.5 to 20.5 kPa increases the evolution of volatiles from raw materials by drawing off organic vapor and uncondensable gas formed during the activation process in the reactor, resulting in pore development increasing in the activated carbon. However, further decreasing the system pressure to 10.5 kPa results in significant decline in both the BET surface area and micropore volume of the activated carbon. This can be attributed to too fast volatilization of the volatiles generated during the activation process, which may effect the formation of activated carbon and decrease the number of micropore and even destroy the micropore structures.
From Table 2, it can be seen that the micropore surface area and the micropore volume of the activated carbon exhibit identical trends. At the system pressure of 20.5 kPa, the micropore surface area and the micropore volume have maximum values of 989.16 m2/g and 0.502 4 cm3/g, respectively. The BET surface area, the total pore volume and the average pore diameter all reach the maximum at the system pressure of 30.5 kPa, but the micropore surface area and micropore volume are lower than those obtained at the system pressure of 20.5 kPa. The result indicates that system pressure of 20.5 kPa is beneficial to develop the micropore structure of activated carbon during chemical activation under vacuum. Under the experimental conditions, the average pore diameter of the obtained activated carbon ranges from 2.077 to 2.100 nm, which demonstrates that the activated carbons prepared from Chinese fir sawdust via chemical activation under vacuum have abundant micropores.
3.2.2 Iodine adsorption value
From Fig.3, it can be seen that the iodine adsorption value of the activated carbon exhibits identical trends with the micropore volume. Results show that iodine absorption value gradually increases with the decrease of system pressure. At the system pressure of 20.5 kPa, there is a maximum. The iodine adsorption value of activated carbon is related to its micropores. The more the micropore, the higher the iodine absorption value. This further proves that the system pressure of 20.5 kPa is beneficial to the formation of microporous structure.
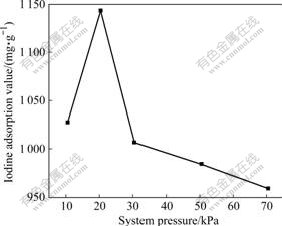
Fig.3 Variation of iodine absorption value with system pressure
3.2.3 Adsorption equilibrium constant
From the experimental results, it can be remarked that, the N2 adsorption isothermal line of the activated carbon obtained under the experimental system pressure accords with Langmuir adsorption isothermal line. Its adsorption equilibrium constant is calculated, as listed in Table 3.
From Table 3, it can be seen that the saturation adsorptive capacity of the activated carbon exhibits identical trends with the BET surface area. At the system pressure of 30.5 kPa, the saturation adsorptive capacity has a maximum of 366.24 cm3/g. The adsorption equilibrium constant gradually increases with the decrease of system pressure, which is from 1.98 to 3.24 kPa-1.
Table 3 Variation of activated carbon adsorption equilibrium constant with system pressure
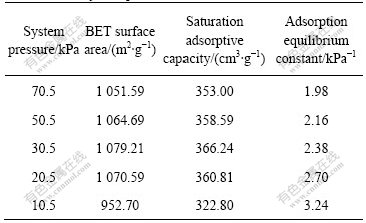
3.3 Effect of activation condition
The effects of activation condition (under nitrogen or vacuum) on pore structure and absorption value of the activated carbon are listed in Table 4.
From Table 4, it can be seen that the BET surface area, micropore surface area, total pore volume, micropore volume, iodine absorption value, methylene blue adsorption value of the activated carbon obtained from vacuum chemical activation are higher than those of the activated carbon obtained from the nitrogen atmosphere. The micropores of activated carbon A are more developed. It is because, under the vacuum condition, the organic vapor and uncondensable gas formed during activation process in the reactor can be drawn off in time, which benefits the formation of microporous structure. While in chemical activation process under N2 atmosphere, the time for organic vapor and uncondensable gas produced in the reaction process to diffuse from internal of raw material to the position where they can be taken away by nitrogen is longer. That is to say, the retention time of organic vapor in the reactor is considerably longer than that in vacuum activation process. In this condition, the secondary reactions of these organic vapor and thermal degradation of the micropore wall will occur and lead to the collapsing of the carbon structure, which increases disorder carbon and results in less microporous.
Fig.4 shows the SEM images of the activated
Table 4 Comparison of two kinds of activated carbon
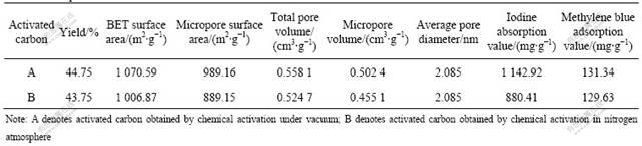
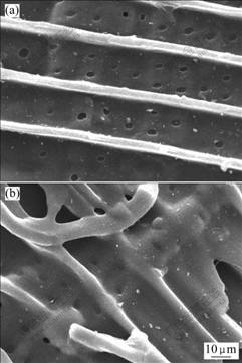
Fig.4 SEM images of activated carbon A (a) and activated carbon B (b)
carbon obtained by chemical activation under vacuum and by chemical activation in nitrogen atmosphere. It can be seen that activated carbon A exhibits a surface with greater porosity compared with activated carbon B (also confirmed by BET analysis). It is because, under vacuum condition, the volatiles released can be quickly removed from the pores and the sample surface, thereby reducing the possibility of volatile deposition on the pores and sample surface, which will otherwise clog up the pores and reduce the pore surface area and volume.
Activated carbon A has higher iodine absorption value and higher methylene blue absorption than activated carbon B, which further confirms that the pore structure of activated carbon A is superior to that of activated carbon B.
Fig.5 shows the pore size distribution of the chemically activated carbon under nitrogen and vacuum. From Fig.5 and Table 4, it can be seen that the pore sizes of the activated carbon obtained under nitrogen and vacuum are mainly micropore and mesopore, and the number of the micropores of the activated carbon prepared under vacuum conditions is more than that of the micropores of the activated carbon prepared under nitrogen atmosphere.
3.4 GC/MS analysis of bio-oil
During the chemical activation process of biomass under vacuum condition, high added-value bio-oil is
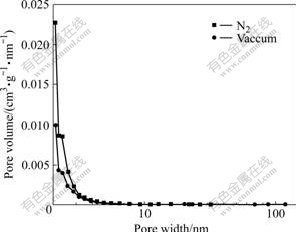
Fig.5 Effects of activation condition on pore size distribution of activated carbons using BJH model
obtained simultaneously. Bio-oil is a complex mixture of organics. GC/MS analysis was carried out to identify the organic compounds in bio-oil. The GC/MS spectrum of the bio-oil from vacuum chemical activation is shown in Fig.6, while the elemental compositions of the bio-oil are listed in Table 5. As can be seen in Fig.6 and Table 5, aromatics and some species of polar compounds are the main components, among which the phenol derivatives are predominant with yields of 69.21%. After being separated and purified, some phenol derivatives can be used as concernful chemical feedstock and intermediates. Some phenol derivatives possess anti-diarrhea and anti-motility properties, germicidal activity, herbicidal and antiseptic properties. They were used in tanning of leather, or used as dyes, thermal insulating material and food additives [29]. 2-methoxy-4-(2-propenyl)-phenol (Eugenol), with yield of 6.97%, for example, is a medicinal perfume oil. It has some pharmacological actions such as antiseptic properties, strengthening the stomach, and hypotensive activity.

Fig.6 GC/MS total ion chromatogram of bio-oil
Table 5 Component analysis of bio-oil by GC/ MS
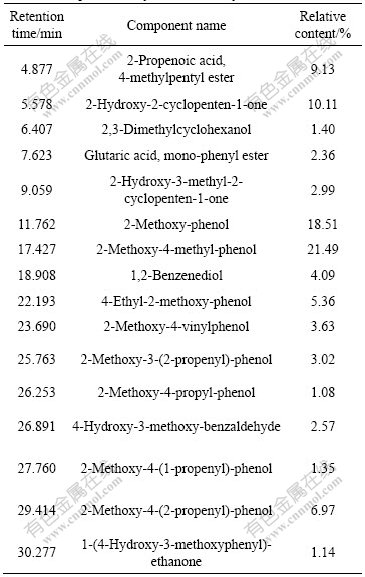
4 Conclusions
(1) Activated carbons are prepared from chemical activation of Chinese fir sawdust with ZnCl2 under nitrogen atmosphere and vacuum condition. It is found that the BET surface area and pore volume of the activated carbons prepared under vacuum condition are superior to those of the activated carbons produced under nitrogen atmosphere. The activated carbon prepared under vacuum condition exhibits a surface with greater porosity compared with the activated carbon obtained under nitrogen atmosphere condition. The system pressure of 20.5 kPa is beneficial to the development of pore structure.
(2) The activated carbon obtained by chemical activation under vacuum condition has developed micropore, the BET surface area is 1 070.59 m2/g, the microporous volume is 0.502 4 cm3/g and the average pore width is 2.085 nm. It has high iodine absorption value of 1 142.92 mg/g and high methylene blue absorption value of 131.34 mg/g.
(3) The N2 adsorption equilibrium constant of the corresponding activated carbon gradually increases with the decrease of reaction system pressure.
(4) It is feasible to prepare activated carbon by chemical activation under vacuum. Both prime activated carbon and high added-value bio-oil can be obtained simultaneously. The commercial run of this process is of vital significance not only on sufficiently using reproducible biomass energy but also on easing energy shortage pressure and resolving the environmental pollution from biomass direct-combustion.
References
[1] LAI Yan-qing, LI Jing, SONG Hai-shen, ZHANG Zhi-an, LI Jie, LIU Ye-xiang. Preparation of activated carbons from mesophase pitch and their electrochemical properties [J]. Journal of Central South University of Technology, 2007, 14(5): 633-637.
[2] WU Feng-chin, TSENG Ru-ling, HU Chi-chang. Comparisons of pore properties and adsorption performance of KOH-activated and steam-activated carbons [J]. Microporous and Mesoporous Materials, 2005, 80(1/3): 95-106.
[3] OLIVARES-MARIN M, FERNANDEZ-GONZALEZ C, MACIAS-GARCIA A, GOMEZ-SERRANO V. Preparation of activated carbon from cherry stones by chemical activation with potassium hydroxide [J]. Applied Surface Science, 2006, 252(17): 5980-5983.
[4] KLIJANIENKO A, LORENC-GRABOWSKA E, GRYGLEWICZ G. Development of mesoporosity during phosphoric acid activation of wood in steam atmosphere [J]. Bioresource Technology, 2008, 99(15): 7208-7214.
[5] AHMED-HARED I, DIRION J L, SALVADOR S, LACROIX M, RIO S. Pyrolysis of wood impregnated with phosphoric acid for the production of activated carbon: Kinetics and porosity development studies [J]. Journal of Analytical and Applied Pyrolysis, 2007, 79(1/2): 101-105.
[6] LI Dong-yan, ZHOU Hua-lei, TIAN Ya-jun, WEI Lian-qi, WU Xiao-feng, LI Wen-jun, CHEN Yun-fa. High-specific-surface-area activated carbon from anthracite [J]. Rare Metal Materials and Engineering, 2007, 36(Suppl.1): 583-586. (in Chinese)
[7] MA Rong, ZHANG Li-fang, ZHANG Shuang-quan, WANG Xin-hong, TANG Zhi-hong, ZHU Wen-kui, YAN Hong. Experimental study on the manufacture of activated carbon in the presence of additives [J]. New Carbon Materials, 2004, 19(1): 57-60. (in Chinese)
[8] MARTINS A F, de CARDOSO A L, STAHL J A, DINIZ J. Low temperature conversion of rice husks, eucalyptus sawdust and peach stones for the production of carbon-like adsorbent [J]. Bioresource Technology, 2007, 98(5): 1095-1100.
[9] CHEN Jian, LI Ting-chen, YAN Yong-jie, REN Zheng-wei, ZHANG Su-ping. Preparation of activated carbon from the residual carbon obtained by fast pyrolysis of biomass [J]. Journal of East China University of Science and Technology, 2005, 31(6): 821-824. (in Chinese)
[10] ISMADJI S, SUDARYANTO Y, HARTONA S B, SETIAWAN L E K, AYUCITRA A. Activated carbon from char obtained from vacuum pyrolysis of teak sawdust: Pore structure development and characterization [J]. Bioresource Technology, 2005, 96(12): 1364-1369.
[11] CAO N, DARMSTADT H, ROY C. Activated carbon produced from charcoal obtained by vacuum pyrolysis of softwood bark residues [J]. Energy & Fuels, 2001, 15: 1263-1269.
[12] LUA A C, YANG T. Effects of vacuum pyrolysis conditions on the characteristics of activated carbons derived from pistachio-nut shells [J]. Journal of Colloid and Interface Science, 2004, 276(2): 364-372.
[13] DARMSTADT H, PANTEA D, SUMMCHEN L, ROLAND U, KALIAGUINE S, ROY C. Surface and bulk chemistry of charcoal obtained by vacuum pyrolysis of bark: Influence of feedstock moisture content [J]. Journal of Analytical and Applied Pyrolysis, 2000, 53(1): 1-17.
[14] KALDERIS D, BETHANIS S, PARASKEVA P, DIAMADOPOULOS E. Production of activated carbon from bagasse and rice husk by a single-stage chemical activation method at low retention times [J]. Bioresource Technology, 2008, 99(15): 6809-6816.
[15] State Forestry Administration. The National Forestry Statistics of the main indicators in 2002 [EB/OL]. [2002] http://www.forestry.gov.cn/lytj. (in Chinese)
[16] IMAMOGLU M, TEKIR O. Removal of copper (II) and lead (II) ions from aqueous solutions by adsorption on activated carbon from a new precursor hazelnut husks [J]. Desalination, 2008, 228(1/3): 108-113.
[17] SUAREZ-GARCIA F, MARTINEZ-ALONSO A, TASCON J M D. Activated carbon fibers from Nomex by chemical activation with phosphoric acid [J]. Carbon, 2004, 42(8/9): 1419-1426.
[18] SUAREZ-GARCIA F, MARTINEZ-ALONSO A, TASCON J M D. Nomex polyaramid as a precursor for activated carbon fibres by phosphoric acid activation. Temperature and time effects [J]. Microporous and Mesoporous Materials, 2004, 75(1/2): 73-80.
[19] ADINATA D, DAUD W M A W, AROUA M K. Preparation and characterization of activated carbon from palm shell by chemical activation with K2CO3 [J]. Bioresource Technology, 2007, 98(1): 145-149.
[20] PERRIN A, CELZARD A, ALBINIAK A, KACZMARCZYK J, MARECHE J F, FURDIN G. NaOH activation of anthracites: Effect of temperature on pore textures and methane storage ability [J]. Carbon, 2004, 42(14): 2855-2866.
[21] ZUBIZARRETA L, ARENILLAS A, PIRARD J P, PIS J J, JOB N. Tailoring the textural properties of activated carbon xerogels by chemical activation with KOH [J]. Microporous and Mesoporous Materials, 2008, 115(3): 480-490.
[22] NABAIS J V, CARROTT P, RIBEIRO-CARROTT M M L, LUZ V, ORTIZ A L. Influence of preparation conditions in the textural and chemical properties of activated carbons from a novel biomass precursor: The coffee endocarp [J]. Bioresource Technology, 2008, 99(15): 7224-7231.
[23] KANDIYOTI R, LAZARIDIS J I, DYRVOLD Bo, RAVINDRA-WEERASINGHE C. Pyrolysis of a ZnCI2-impregnated coal in an inert atmosphere [J]. Fuel, 1984, 63(11): 1583-1587.
[24] CASTRO-MUNIZ A, MARTINEZ-ALONSO A, TASCON J M D. Microporosity and mesoporosity of PPTA-derived carbons. Effect of PPTA thermal pretreatment [J]. Microporous and Mesoporous Materials, 2008, 114(1/3): 185-192.
[25] LUA A C, YANG T. Characteristics of activated carbon prepared from pistachio-nut shell by zinc chloride activation under nitrogen and vacuum conditions [J]. Journal of Colloid and Interface Science, 2005, 290(2): 505-513.
[26] BRUAUER S, EMMETT P H, TELLER E. Adsorption of gases in multimolecular layers [J]. J Amer Chem Soc, 1938, 60(2): 309-319.
[27] FU Xian-cai, SHEN Wen-xia, YAO Tian-yang. Physical chemistry [M]. 4th ed. Beijing: Higher Education Press, 1990: 934-978. (in Chinese)
[28] HASBON J W. Activated carbon purification [M]. LIN Qiu-hua, translates. Beijing: China Architecture & Building Press, 1980. (in Chinese)
[29] MURWANASHYAKA J N, PAKDEL H, ROY C. Separation of syringol from birch wood-derived vacuum pyrolysis oil [J]. Separation and Purification Technology, 2001, 24(1/2): 155-165.
(Edited by YANG You-ping)
Received date: 2008-09-21; Accepted date: 2008-12-08
Corresponding author: QIU Ke-qiang, Professor, PhD; Tel: +86-731-8877364; E-mail: qiuwhs@sohu.com