J. Cent. South Univ. Technol. (2010) 17: 967-971
DOI: 10.1007/s11771-010-0585-2

Zinc leaching from electric arc furnace dust in alkaline medium
LI Hong-xu(李宏煦)1, 2, WANG Yang(王洋)1, 2, CANG Da-qiang(苍大强)1, 2
1. School[U1] of Metallurgy and Ecology Engineering, University of Science and Technology Beijing,Beijing 100083, China;
2. Key Laboratory of Ecological and Recycling Metallurgy of Ministry of Education,University of Science and Technology Beijing, Beijing 100083, China
? Central South University Press and Springer-Verlag Berlin Heidelberg 2010
Abstract: Physical and chemical properties of electric arc furnace (EAF) dust from Tianjin seamless Pipe Company were measured and analyzed. The zinc leaching tests in alkaline medium were carried out under variation of leaching agent concentration, leaching temperature, leaching cumulative time and solid-to-liquid ratio. The thermodynamics and kinetics of the zinc leaching process were also analyzed. The results show that the EAF dust contains 10% (mass fraction) zinc and the median particle size is 0.69 μm. The zinc recovery of 73.4% is obtained under the condition of 90 ℃, 6 mol/L NaOH, and 60 min leaching time. With the increase of concentration of NaOH and the cumulative time, zinc leaching will be significantly increased. The kinetics study demonstrates that the leaching reaction is chemically controlled and the reaction activation energy is 15.73 kJ/mol.
Key words: electric arc furnace (EAF) dust; zinc leaching; hydrometallurgy; thermodynamics; leaching kinetics; recycling
1 Introduction
Production of steel in the electric arc furnace (EAF) generates a dust by-product mainly composed of iron oxides and non-ferrous metals. World production of crude steel up to 132.9 Mt in 2008, a further 31% of steel is produced in EAF; the mass of dust collected in a typical EAF is 15-20 kg/t of steel produced, leading to a global dust quantity ranged between 6.1 and 8.2 Mt/a around the world. The average iron concentration in the dust is approximately 30% (mass fraction). Among the non-ferrous metals in the dust, zinc is the most important, which varies between 7% and 40% as ZnO and ZnFe2O4, depending on the ratio of galvanized scrap utilized. With an average zinc content of 20%, EAF dusts represent a possible recovery of zinc from 0.86 to 1.14 Mt/a. Thus, the beneficiation of rich zinc-bearing wastes like EAF dust becomes necessary as primary minerals are exhausted [1-3]. However, EAF dusts are classified as hazardous waste due to the presence of significant amounts of dissoluble compounds of lead (Pb), cadmium (Cd), and chromium (Cr). As the quantity of scrap coming from the automotive industry is used with an ever-increasing ratio, the amount of Zn, Pb, Cu, Cr, and Cd in EAF dusts is on the rise [4-6].
Now there are two possibilities to manage these by-products. The most commonly used method is disposal in hazardous wastes landfills after a solidification/stabilization treatment using hydraulic binders. However, with this way the cost of the treatment is high and the valuable metals cannot be recovered. The other method of treatment is beneficiation by hydrometallurgy or pyrometallurgy. The treatment of these wastes and the recovery of metallic values are good examples to as material recycling. At present, most of the commercially available processes for the treatment of EAF dusts are pyrometallurgical, such as rotary kilns, plasma, and flame reactor processes. This enables the recovery of zinc bonded in a stable ZnFeO4 structure and creates an iron oxide slag, which complies with environmental regulations. But the major drawbacks of the pyrometallurgical methods are high-energy consumption and requirements of dust collecting/gas cleaning systems [8-12]. The major impetus for the development of hydrometallurgical processes for the treatment of EAF dust is that a small-scale, environmentally suitable, on-site process can be economic due to low capital and operating costs as well as potential recovery of the valuable metal-containing product. Many acidic or alkaline leaching processes have been or are being developed worldwide to recover values from EAF dust or render them nonhazardous for the hydrometallurgical treatment of EAF dusts [13-16]. In this work, sodium hydroxide (NaOH) was chosen as leaching agent as it is effective in the dissolution of zinc,cadmium and other toxic heavy metals, without significant dissolution of iron, aiming at recovering zinc effectively and reducing the hazardous character of the solid residues.
2 Experimental
2.1 Sample characterization
A sample of EAF dust was collected from the Tianjin Steel Company. Particle size analysis was tested by JL-1177 type laser diffraction particulate size analyzer, X-ray diffractometer (Philips PW 3710) was used for mineralogy analysis, and an atomic absorption spectrometer (AAS) of Shimadzu AA-6300 was utilized for the analysis of the aqueous samples from the leaching experiments.
2.2 Leaching tests
The leaching experiments were conducted in a glass reaction vessel heated by a thermostatically controlled heating mantle. Stirring was done by variable-speed electromagnetic motor. NaOH was used as leaching agent at a solid-to-liquid ratio of 1:10, 5 g electric arc furnace dust was added under constant agitation and in a 1 L closed flask, a water-cooled condenser as flask cover in order to avoid solution loss by evaporation.
The NaOH concentration varied from 2 to 6 mol/L at 30-90 ℃ and the duration was 100 min. Liquor samples were collected after setting periods of time and analyzing for zinc by AAS.
3 Results and discussion
3.1 Characterization of EAF dust
Before size analysis the sample was dried to make the water contain the dust of 2.3%. The particle size distribution of the EAF dust is presented in Fig.1. It shows that the median particle size is around 0.69 μm, only about 13% of the particles are coarser than 1 μm. This fine size distribution indicates that physical concentration methods, such as gravity or magnetic separation, are not suitable to treat such a material. Further, its size distribution suggests that the material will be difficult to dry, if no previous agglomeration is used. On the other hand, reaction kinetics involving this dust should be fast, due to the prevailing fine particle sizes, which suggests that leaching may be an attractive route to treat this material when zinc recovery is of interest. The chemical analyses of the dust show that the Zn content is 10.06%, Fe 38.70% and Cu 0.08%, as shown in Table 1. It can be observed that Fe and Zn are the main components of the dust, which also presents small amounts of very toxic heavy metals, including
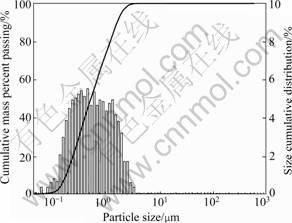
Fig.1 Particle size distribution of EAF dust (Median particle size 0.69 mm; surface area 17.033 8 m2/cm3)
Table 1 Chemical composition of dust (mass fraction, %)

chromium, cadmium and lead. The zinc content in this dust is considered low for a pyrometallurgical treatment for zinc recovery, which leads to the greater interest in the hydrometallurgical treatment.
The X-ray diffraction pattern of the dust is shown in Fig.2. As seen from Fig.2, zincates (ZnO) and zinc ferrite (ZnFe2O4) are the two predominant phases, zinc in this EAF dust is in the forms of zincite (zinc oxide, ZnO) and franklinite (zinc ferrite), and iron is in the form of hematite and franklinite.
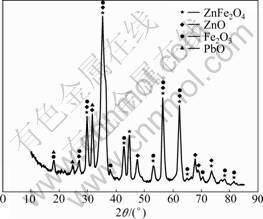
Fig.2 X-ray diffraction pattern of EAF dust
3.2 Thermodynamics of zinc leaching
The solubility of zinc oxide in water at 25 ℃ can be described by the following reactions [9,11,14]:

Zn2++H2O, Ks0=1.58×1011 (1)

ZnOH+, Ks1=1.58×102 (2)


Ks3=1.26×107 (3)


Ks4=2.00×10-30 (4)
where Ksi are the constants for the solubility equilibria. Eqs.(1)–(4) allow to determine the total concentration of zinc in an aqueous solution as a function of pH, according to the following equation:
c(Zn)T=Ks0c2(H+)+Ks1c(H+)+Ks3/c(H+)+Ks4/c2(H+) (5)
Eqs.(1)-(5) are used to calculate the equilibrium diagram of solid zinc oxide and the zinc ionic species, as shown in Fig.3. The equilibrium diagrams indicate that zinc can be dissolved in either acidic or alkaline media, whereas iron, which is the metal that predominates in the dust, is more readily soluble in acidic media. Therefore, alkaline leaching becomes the more attractive alternative, as no additional purification step for iron removal is necessary.
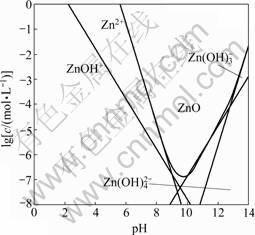
Fig.3 Solubility of ZnO as function of pH at 25 ℃
3.3 Leaching results
3.3.1 Effect of stirring speed
The effect of stirring speed at 600, 700 and 800 r/min was studied by keeping the other conditions constant at 2.0 mol/L NaOH, 60 ℃, 20% solid (percent solid here is defined as dust mass (g)×100/leachant volume (cm3)). Fig.4 shows the effect of stirring speed on zinc leaching from the dust at 60 ℃, 2.0 mol/L NaOH and 20% solid. It is found that stirring speed of 600, 700 and 800 r/min has no effect on zinc leaching. Based on these results, a stirring speed of 800 r/min was selected for all the subsequent experiments. The maximum extraction appeared to be reached after 60 min.
3.3.2 Effect of lixiviant concentration
The concentrations of NaOH were 2, 4, 6, 8, and 10 mol/L, while keeping the stirring speed at 800 r/min, 20% solid, and solution temperature at 60 ℃. The leaching results are shown in Fig.5.
The rate of zinc extraction increases with increasing NaOH concentration up to 10 mol/L, where about 65% Zn is extracted in 100 min. The leaching rate drops down

Fig.4 Effect of stirring speed on zinc extraction (2.0 mol/L NaOH, 60 ℃, and 20% solid)
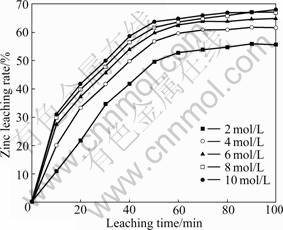
Fig.5 Effect of NaOH concentration on zinc extraction (800 r/min, 60 ℃, 20% solid)
at 8.0 and 10.0 mol/L NaOH because the high NaOH concentration increases the viscosity of the solution. This will tend to reduce the diffusion rate of the ions.
3.3.3 Effect of leaching temperature
The leaching temperature changed from 30 to 90 ℃. The leaching results are shown in Fig.6. It is demonstrated that the increase of leaching temperature will increase the rate of zinc leaching. Dissolution of zinc increases immensely at 60 ℃ and above, and when the leaching temperature is increased to 90 ℃, the zinc leaching rate reaches its maximum.
3.4 Kinetic investigation
3.4.1 Rate constant
To investigate the reaction order constant, the following equation was utilized to calculate the leaching reaction constant:
(6)
where XZn is the leached zinc fractional change; k′ is the
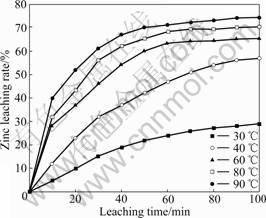
Fig.6 Effect of leaching temperature on zinc extraction (800 r/min, 20% solid, 6 mol/L NaOH)
coefficient that includes the rate constant; and k is the leaching reaction rate constant.
The plots of 1-(1-XZn)1/3 versus kt to determine the leaching kinetics of the experiments and fractional changes of zinc were calculated from the leached zinc concentrations at certain time intervals of the experiments and constant temperature, then the values of 1-(1-XZn)1/3 were calculated from these calculated fractional changes in a certain period. At different temperatures the curves of 1-(1-XZn)1/3 versus kt are drawn and shown in Fig.7, such a plot is linear, from the slope the reaction constant k at different temperatures can be obtained, at the same time, the linear relationship between 1-(1-XZn)1/3 and reaction time t shows that under the designed experimental conditions the leaching process is controlled by chemical reaction step [9, 14-16].
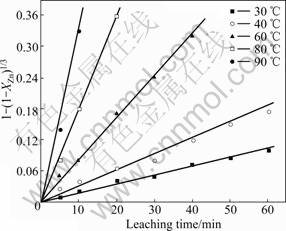
Fig.7 1-(1-XZn)1/3 versus leaching time at different temperatures (800 r/min, 20% solid, 6 mol/L NaOH)
3.4.2 Activation energy
k, as a reaction rate constant, is described in Arrhenius equation as
(7)
where E is the apparent activation energy; R is the universal gas constant; k0 is the frequency factor; and T is the thermodynamic temperature. From Eq.(7) the following equation can be obtained:
(8)
The relationship between ln k and 1/T is plotted in Fig.8. The slope of the line gives E/R by Eq.(8). So the apparent activation energy (E) is calculated to be 15.73 kJ/mol, indicating that the chemical reaction controls the rate of leaching reaction between 30 and 90 ℃.
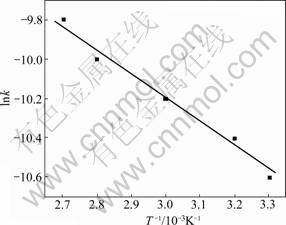
Fig.8 Arrhenius plot for leaching of zinc from EAF dust
4 Conclusions
(1) Leaching zinc test from EAF dust of Tianjin Seamless Pipe Company using alkaline is carried out. Under the optimum conditions of 800 r/min, 20% solid, 90 ℃, 6 mol/L NaOH for 60 min the zinc leaching rate can reach up to 73.4%. The median particle size of the EAF dust is around 0.69 μm. X-ray diffraction results show that zincates (ZnO) and zinc ferrite (ZnFe2O4) are the two predominant phases.
(2) Kinetics studies of leaching process demonstrate that under the designed experimental conditions the process of leaching zinc from the EAF dust is controlled by chemical reaction. By Arrhenius plot the apparent activation energy is calculated to be 15.73 kJ/mol.
References
[1] CHENG T W. Combined glassification of EAF dust and incinerator fly ash [J]. Chemosphere, 2003, 50(1): 47-51.
[2] NYIRENDA R L. The processing of steelmaking flue-dust: A review [J]. Minerals Engineering, 1991, 4(7/8/9/10/11): 1003-1025.
[3] HAGNI A M, HAGNI R D, DEMARS C. Mineralogical characteristics of electric arc furnace dusts [J]. JOM, 1991, 43(4): 28-30.
[4] JHA M K, KUMAR V, SINGH R J. Review of hydrometallurgical recovery of zinc from industrial wastes [J]. Resour Conserv Recycl, 2001, 33(1): 1-22.
[5] IONESCU D, MEADOWCROFT T R, BARR P V. Glassification of EAF dust: The limits for Fe2O3 and ZnO content and an assessment of leach performance [J]. Canadian Metallurgical Quarterly, 1997, 36(4): 269-281.
[6] SOFILIC T, RASTOVCAN-MIOC A, CERJAN-STEFANOVIC S, NOVOSEL-RADOVIC V, JENKO M. Characterization of steel mill electric-arc furnace dust [J]. J Hazard Mater B, 2004, 109(1): 59-70.
[7] SMITH S M, ZHOU X, NASSARALLA C L. A novel process for recycling steel-making dust [J]. Iron and Steel Maker, 2000, 27(2): 69-76.
[8] HAVLIK T, TURZAKOVA M, STOPIC S, FRIEDRICH B. Atmospheric leaching of EAF dust with diluted sulphuric acid [J]. Hydrometallurgy, 2005, 77(1): 41-50.
[9] HILBER T, MARR R, SIEBENHOFER M, ZAPFEL W. Solid/liquid extraction of zinc from EAF-dust [J]. Sep Sci Technol, 2001, 36(12): 1323-1333.
[10] LECLERC N, MEUX E, LECUIRE J M. Hydrometallurgical extraction of zinc from zinc ferrites [J]. Hydrometallurgy, 2003, 70(2): 175-183.
[11] DUTRA A J B, PAIVA P R P, TAVARES L M. Alkaline leaching of zinc from electric arc furnace steel dust [J]. Minerals Engineering, 2006, 19(2): 478-485.
[12] LINDBLOM B, SAMUELSSON C, SANDSTROM A, YE G. Fine-particle characterization—An important recycling tool [J]. JOM, 2002, 54(12): 35-38.
[13] YOUCAI Z, STANFORTH R. Integrated hydrometallurgical process for production of zinc from electric arc furnace dust in alkaline medium [J]. J Hazard Mater B, 2000, 80(1/3): 223-240.
[14] MIKHAIL S A, TURCOTTE A M, AOTA J. Thermoanalytical study of EAF dust and its vitrification product [J]. Themochimica Acta, 1996, 287(1): 71-79.
[15] G?KHAN O. Leaching and cementation of heavy metals from electric arc furnace dust in alkaline medium [J]. Hydrometallurgy, 2005, 78(2): 236-245.
[16] JARUPISITTHORN C, PIMTONG T, LOTHONGKUM G. Investigation of kinetics of zinc leaching from electric arc furnace dust by sodium hydroxide [J]. Mater Chem Phys, 2002, 77(2): 531-535.
(Edited by YANG You-ping)
Foundation item: Project(20876014) supported by the National Natural Science Foundation of China
Received date: 2010-01-04; Accepted date: 2010-04-08
Corresponding author: LI Hong-xu, PhD, Professor; Tel: +86-10-82376226; E-mail: lihongxu2001@126.com