
Growth behavior of interfacial compounds in galvanized steel joints with CuSi3 filler under arc brazing
YU Zhi-shui(于治水), LI Rui-feng(李瑞峰), QI Kai(祁 凯)
College of Materials Engineering, Shanghai University of Engineering Science, Shanghai 201620, China
Received 28 February 2006; accepted 26 September 2006
Abstract: The galvanized steels were joined using a TIG arc brazing process with CuSi3 as the filler metal. The arcing time ranged from 1 s to 5 s with arcing current of 70 A in flowing argon. The possible reaction products at the interface were confirmed using thermodynamics, SEM, and EDS methods. The results show that a fragmention behavior in some whisker-like intermetallic compounds happens, and that there are two layers of Fe2Si and Fe5Si3 formed at the interface of the galvanized steel and copper filler. From this, the schematic cycle of the interface growth behavior of Fe/Si compounds and the fragmentation behavior of whisker-like intermetallic compounds are developed.
Key words: arc brazing; interfacial behavior; compounds; thermodynamics
1 Introduction
Arc brazing is a relatively new joining technique. The main advantages over existing commercially available joining processes are its low cost and potential for being easily incorporated as a workstation in the production chain. This will significantly reduce the inventory cost for parts that otherwise would have to be prepared separately and stored for assembly line needs. Other advantages include no vacuum requirement even when joining superalloys or titanium alloys, controlled joint interfaces with limited reactions, few microstructure or property changes in the base materials after joining due to rapid processing, and potential for localized heating for joining large machine parts. So far, arc brazing techniques of steels, nickel based superalloys, titanium alloys, aluminum alloys, and titanium-matrix composites have been successfully developed[1-4].
Arc brazing or plasma arc brazing of galvanized steel sheets using CuSi3 filler metal was studied, and was observed to give satisfactory joint strength, sometimes even higher than that in the base materials[5-8]. Up to now, studies mainly consider the brazing equipment and brazing process, and few researchers report the reaction and products at the interface and the interfacial layer growth behavior during the arc brazing process. LI et al
[9] studied the intermetallic compound at the copper filler, but he didn’t tell the reaction behavior at the interface of galvanized steel and copper filler. In this present paper, the studies on galvanized steels that were arc brazed using CuSi3 as the filler material were reported. The interfacial reactions and products generated were studied and determined using SEM, EDS, and thermodynamic analysis methods. These studies were undertaken to improve the practical applications of arc brazing.
2 Experimental
2.1 Materials
The experimental base materials were galvanized steel sheets of 40 mm×40 mm×2 mm suitable for tungsten inert gas(TIG) arc brazing. The filler metal was CuSi3. The galvanized steel and CuSi3 specimens were cleaned with alcohol and acetone prior to brazing.
2.2 Methods and procedure
To determine the interfacial reaction between the base material and the filler metal, spreading experiments of filler metal were conducted on the base metal surface during arc heating, i.e. TIG brazing. During the TIG brazing process, the arc current was 70 A, the arcing time was 1-5 s, and the voltage was 11.1-11.2 V. Each time, 200 mg of brazing filler metal was spread on the surface of the base material. Arc brazing was accomplished using a Fronius welding machine(FK-2600) with direct current straight polarity(DCSP) mode.
For microstructural studies, the cross-sections of the specimens were polished and eroded in sequence. The interfacial structure and compositions were investigated using SEM (JXA 840 A) and EDS. The component materials at the interface between brazing filler metal and base material were analyzed using energy spectrometry.
3 Results and analysis
Fig.1 shows the cross-section SEM micrographs of specimens prepared for 1, 3, 4 and 5 s at an arc current of 70 A. It can be seen that Fe-Si compounds nucleate at the interface and grow in wavelike form into the copper filler zone. Then compounds with ‘sprout-like’ form grow from the top of the wavelike interface, and these compounds grow larger and deeper into the copper filler zone with increasing arcing time. Later these compounds are fragmented by the arc stirring force into block-like form and are distributed there. Fig.1 also shows some flowerlike or star-like particles in the copper filler zone. With increasing arcing time, these particles increase and become well dispersed in the copper filler zone.
On the other hand, Fig.1(a) also shows that at the beginning there are already many Fe particles in the filler zone. It can be concluded that these particles are resulted from the ‘anode spots’ action of the arc. Because the welding machine is operated in DCSP mode, there is high density electric current flow from cathode to anode. Therefore a large number of anode spots exist on the galvanized steel surface[10]. During the arc brazing process, many high bright spots are observed on the surface of the base material, and these spots are the anode spots. The ‘anode spots’ action causes micro iron particles to melt and migrate, and to become distributed throughout the filler metal zone.
To see in more detail the interface growth of Fe-Si compound and the fragmentation of the whisker-like compounds, a magnified micrograph of part of the interface shown in Fig.1 is shown in Fig.2. It can be seen that there are two layers, layer Ⅰ and layer Ⅱ, at the interface, and these two layers grow wider with increasing arcing time. However, when the arcing time reaches 4 s, the width of layer Ⅰ becomes narrow. It also can be seen from Fig.2 that the interface of the copper filler metal and base material grows in a wavelike form, and there are some whisker-like Fe-Si compounds growing from the top of the wavelike layer Ⅱ, and then these whisker-like compounds fragmentate into ‘short stick’ form. As arcing time is greater than 4 s, most of the whisker-like compounds are fragmentated and very few of the long whisker-like compounds re main at the interface.
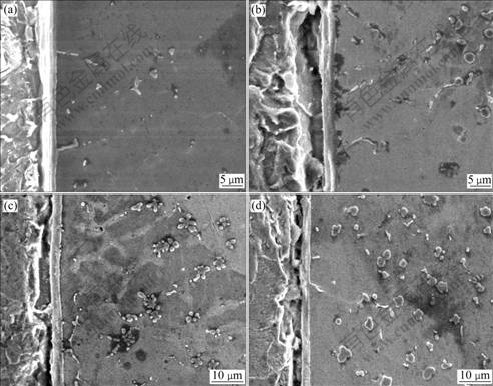
Fig.1 Influence of arcing time on microstructure of brazing joint (Iarcing=70 A): (a) 1 s; (b) 3 s; (c) 4 s; (d) 5 s
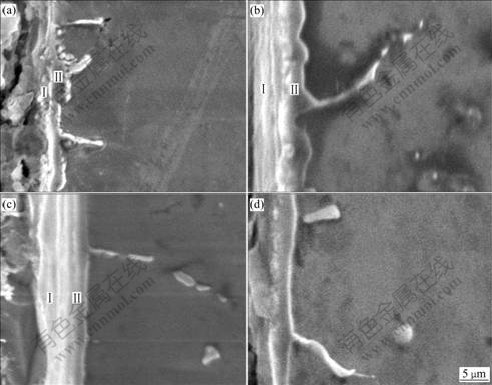
Fig.2 Influence of arcing time on Fe-Si interface compound growth behavior (Iarcing=70 A): (a) 1 s; (b) 2 s; (c) 3 s; (d) 4 s
4 Discussion
4.1 Gibbs free energy and diffusion coefficient analysis for Fe-Si compounds
To determine the possible phases produced by arc brazing, and their distribution at the interface, the Fe-Si binary phase diagram was studied[11]. There are several kinds of Fe-Si compounds produced at high temperatures, such as ε-FeSi, ζ-FeSi2, η-Fe5Si3 and β-Fe2Si. However, such Fe-Si compounds will not be produced and grow at the same time. It is necessary to determine the Gibbs free energy and diffusion coefficient of each compound using thermodynamic calculations.
The formation Gibbs free energy of Fe-Si compound, the reaction free energy between Fe and Si and free energies of Fe, Si were calculated using a method described in detail elsewhere [12-14].
Fig.3(a) shows the formation Gibbs free energy of each Fe-Si intermetallic compound. It can be seen that the Fe5Si3 and Fe2Si intermetallic compounds have relatively lower formation Gibbs free energy than that of FeSi2 and FeSi intermetallic compounds. So Fe and Si will have a preference for producing Fe5Si3 and Fe2Si compounds.
The possible reactions between Fe2Si, Fe5Si3 and Fe, Si should be reactions(1)-(4), and their reaction Gibbs free energies are shown in Fig.3(b). It can be seen that reactions (1) and (4) have relatively lower Gibbs free energy than reactions (2) and (3). Thus, reactions (1) and (4) have more tendencies to happen than reactions (2) and (3).
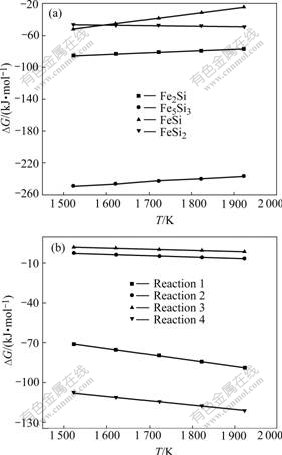
Fig.3 Gibbs free energy changes of Fe-Si compound in arc brazing: (a) Formation of Fe-Si intermetallic compounds; (b) Reaction between Fe-Si compounds and Fe, Si
5Fe2Si+Si=Fe5Si3 (1)
Fe2Si+3Si=2FeSi2 (2)
Fe5Si3+7Si=5FeSi2 (3)
Fe5Si3+Fe=3Fe2Si (4)
The diffusion coefficients of element Si in each Fe-Si compound were also calculated. It is concluded that the diffusion coefficients of Si in FeSi2, FeSi, Fe5Si3, and Fe2Si decrease in order. From the analysis above, it can be concluded that although the diffusion coefficients of Si in FeSi2 and FeSi are relatively low, when these two compounds are difficult to produce, Fe5Si3 and FeSi2 are the primary products in the Fe-Si reaction during the arc brazing heating process.
The growth mechanisms of Fe-Si compounds at the interface layers are determined as follows. Because of the relatively lower Gibbs free energy, Fe5Si3 is the primary phase produced at the interface; with diffusion of Fe and Si atoms, the Fe5Si3 layer (layer Ⅱ) becomes thicker; as time increases, a Si concentration gradient builds at the Fe/Fe5Si3 interface. At the Fe side, there is a Fe rich zone and the Si concentration is low, and the Fe atoms may react with Fe5Si3 as Fe5Si3+Fe=3Fe2Si. With the growth of layer Ⅰ, the diffusion rate of Fe atoms decreases, and at the same time, the diffusion quantities and activities of Si atoms at the interface increase. So the reaction between Fe2Si and Si, 5Fe2Si+Si=2Fe5Si3, occurs at the interface; layer Ⅱ is widened, and layer Ⅰ becomes a little narrower. Fig.4 shows the EDS analysis results of layer Ⅰ, layer Ⅱ, whisker-like compound, and flowerlike compound shown in Figs.1 and 2. The mole fractions of Fe and Si in these compounds are also shown in this figure. All of the proportions of Fe and Si are consistent with the thermal analysis and product analysis conducted above.
4.2 Schematic cycle of growth behavior of Fe-Si compound
The analyses above can be represented by the physical illustration of growth behavior and interface behavior of Fe-Si compound shown in Fig.5, where the growth process is divided into 7 steps.
1) With the rapid heating of arc, the copper filler soon melts. Fe atoms diffuse into the copper filler zone, and Si and Cu into the interfacial zone. Because of the‘anode spots’ action of the arc, some Fe atoms are introduced into the copper filler zone. At this step, there are no interfacial layers at the interface because of the short arcing time.
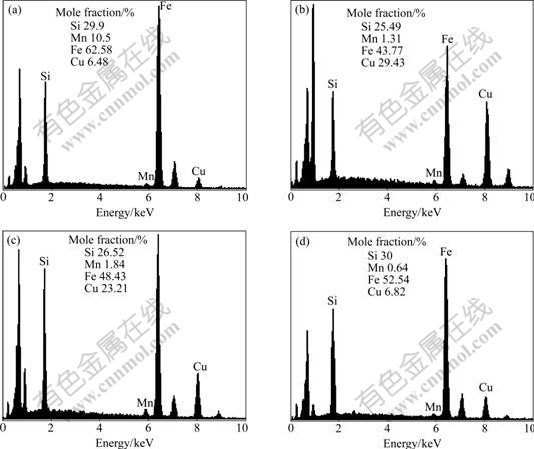
Fig.4 EDS analysis results of interface production (Iarcing=70 A, tarcing=4 s): (a) Layer Ⅰ; (b) Layer Ⅱ; (c) Whisker-like compound; (d) Flower-like compound
Fig.5 Physical models of Fe-Si intermetallic compound growth behavior
2) As arcing time increases, Fe atoms react with Si atoms to produce Fe5Si3(Cu) intermetallic compound in the copper filler zone. At the interface, a Fe5Si3 layer is also produced having wavelike form and some intermetallic Fe5Si3 ‘sprouts’ form on the top of the wavelike layer.
3) During this step, the whisker-like compounds grow deeper into the copper filler zone and more and more Fe5Si3 intermetallic compounds form in the copper filler zone. The Fe5Si3 layer thickens, and at the same time, Fe2Si forms as a result of the reaction between Fe base and the Fe5Si3 layer.
4) At this step, both the Fe2Si layer and the Fe5Si3(Cu) layer thicken with increasing arcing time. The whisker-like compounds fragmentate into ‘short-stick’ form because of the strong stirring force of the arc and the sweeping force of liquid flow at the solid/liquid interface.
5) Some of the fragmentated stick-like compounds are in-situ solidified in the copper filler zone. If they reach their melting temperature in the filler zone, the compounds are unlikely to survive long enough to become sources of equiaxed grains until the liquid becomes supercooled or unless they are swept into cooler regions by imposed stirring. In the arc brazing process, heating and cooling processes are rapid, and stirring forces are strong, so that many particles can be swept into the filler zone and survive and grow by an Ostwald ripening mechanism[15].
6) The compound concentrates, grows into star-like form, and disperses in the copper filler zone.
7) Some of the star-like compounds grow slowly into flower-like form. Finally, the quantities and dimensions of the ball-like, star-like and flower-like intermetallic compounds increase and they become widely dispersed in the copper filler zone.
5 Conclusions
1) At the interface of Cu filler and Fe base, the fragmention behavior of some whisker-like intermetallic compounds happens. There are some ball-like, star-like, flower-like intermetallic compounds at the copper filler zone.
2) Thermodynamic and EDS analyses reveal that Fe5Si3(Cu) intermetallic compound is the most likely to be generated, and that there are two layers of Fe2Si and Fe5Si3 formed at the interface.
3) A schematic cycle with 7 steps for interfacial growth behavior during arc brazing of galvanized steel sheet using CuSi3 filler is developed.
References
[1] FUJII H, SHIRAKI S. Development of arc-brazing welding method and application of pulsed MIG welding to various thin plates [J]. National Technical Report, 1997, 23(2): 23-31.
[2] YU Z S, QIAN Y Y, WU M F, WANG F J. Interface behaves and formation mechanism of MIG-brazed galvanized steel joint [J]. Materials Science and Technology, 2002, 9: 1045-1048.
[3] FRINGS A, STOCKEL S. Fully mechanized inert-gas metal-arc brazing of galvanized thin steel sheet [J]. Welding and Cutting, 1989, 41(11): 577-583.
[4] YU Z S, LI R F, QI K, ZHOU F M. Numerical simulation of copper based filler metal droplets spreading under arc brazing [J]. Trans Nonferrous Met Soc China, 2005, 15(4): 819-822.
[5] YU Z S, ZHOU F M, QI K, WU M F. Fracture behavior of MIG brazed joints using copper based filler [J]. Transactions of the China Welding Institution, 2001, 22(6): 29-32.
[6] ANDY J, CHRIS W, MIKE H. Variable polarity improves weld brazing of galvanized sheet [J]. Welding Journal, 2001, 80(10): 36- 40.
[7] BOUAIFI B. Low-heat process enhanced jointing of coated sheet metals [J]. Welding Journal, 2003, 82(1): 26-31.
[8] BOUAIFI B, OUSAISSA B, HELMICH A. Plasma arc brazing in sheet metal construction [J]. Science and Technology of Welding and Joining, 2002, 7(5): 326-330.
[9] LI R F, YU Z S, QI K. Interfacial structure and joint strengthening in arc brazed steels with copper based filler [J]. Trans Nonferrous Met Soc China, 2006, 16(2): 397-401.
[10] LANCASTER J F. The Physics of Welding [M]. Oxford: Pergamon Press, 1986.
[11] YU J Q, YI W Z,CHEN B D, CHEN H J. Binary Alloy Phase Diagrams [M]. Shanghai: Science and Technology Press, 1987: 375.
[12] GOSELE U, TU K N. Growth kinetics of planar binary diffusion couples [J]. Journal of Applied Physics, 1982, 53(4): 3252-3260.
[13] KIM K, TU K N. Kinetic analysis of the soldering reaction between eutectic SnPb alloy and Cu accompanied by ripening [J]. Physical Review B, 1996, 53(6): 16027-16034.
[14] YU Z S. Wetting and Spreading and Interfacial Behavior in Galvanized Steel Sheet Argon Arc Brazing [D]. Harbin: Harbin Institute of Technology, 2003.
[15] ELDER K R, GRANT M, GUO H. Theory and simulation of ostwald ripening [J]. Physical Revivew B, 1993, 50: 14110-14124.
(Edited by LI Xiang-qun)
Foundation item: Project(50475051) supported by the National Natural Science Foundation of China
Corresponding author: YU Zhi-shui; Tel: +86-21-67791198; Fax: +86-21-62759779; E-mail: yu_zhishui@163.com