J. Cent. South Univ. Technol. (2007)04-0452-04
DOI: 10.1007/s11771-007-0088-y 
Effect of homogenization treatment on microstructure and properties of Al-Mg-Mn-Sc-Zr alloy
NIE Bo(聂 波)1,2, YIN Zhi-min(尹志民)1, ZHU Da-peng(朱大鹏)1, PENG Yong-yi(彭勇宜)1,
JIANG Feng(姜 锋)1, HUANG Ji-wu(黄继武)1
(1. School of Materials Science and Engineering, Central South University,Changsha 410083, China;
2. Northeast Light Alloy Co. Ltd., Harbin 150060, China)
________________________________________________________________
Abstract:The effect of homogenization on the hardness, tensile properties, electrical conductivity and microstructure of as-cast Al-6Mg-0.4Mn-0.25Sc-0.12Zr alloy was studied. The results show that during homogenization as-cast studied alloy has obviously hardening effect that is similar to aging hardening behavior in traditional Al alloys. The precipitates are mainly Al3(Sc,Zr) and Al6Mn. When homogenization temperature increases the hardness peak value is declined and the time corresponding to hardness peak value is shortened. The electrical conductivity of the alloy monotonously increases with increasing homogenization temperature and time. The decomposition of the supersaturated solid solution containing Sc and Zr which is formed during direct chilling casting and the precipitation of Al3(Sc, Zr) cause hardness increasing. The depletion of the matrix solid solubility decreases the ability of electron scattering in the alloy, resulting in the electrical conductivity increased. Tensile property result at hot rolling state shows that the optimal homogenization treatment processing is holding at 300-350 ℃ for 6-8 h.
Key words: Sc; Zr; Al-Mg-Mn alloy; homogenization; Al3(Sc, Zr) precipitation; microstructures; tensile properties; hardness
________________________________________________________________
1 Introduction
Al-Mg-Mn alloy with medium strength, good corrosion resistance and good welding property are used widely in aviation, spaceflight and machine-building[1]. With the development of spaceflight, aviation and naval vessel technology, the strength of this kind of alloy needs further increase, composite adding of Sc and Zr to Al-Mg-Mn alloy can get this effect[2-4] and this kind of alloy has been put into the National 10th Five-Year Plan Program. The increase of strength mainly comes from grain refining strengthening, substructure strengthening and precipitation strengthening caused by Al3(Sc, Zr) particles[5-7]. Al3(Sc, Zr) particles are formed during homogenization of as-cast alloy and homogenization processing has great influence on precipitation behaviour of Al3(Sc, Zr) particles. So in this study the effect of homogenization processing on the hardness, tensile properties, electrical conductivity and microstructure of as-cast Al-Mg-Mn-Sc-Zr alloy was studied, and then the optimal homogenization processing of this kind of alloy was obtained.
2 Experimental
The Al-6Mg-0.4Mn-0.25Sc-0.12Zr flat ingot with size of 70 mm×300 mm×1 000 mm was melted and cast by semi-continuous chill casting method. The specimens were taken in the middle of the ingot and were homogenized at 250, 300, 350, 400 and 450 ℃ for 0-12 h. The hardness was tested using HW187.5 hardness tester. The electrical conductivity was measured using 7051 whirling current conductivity gauge. The optical microscopy of the specimens was observed by polar light after electro-polishing using fluorboric acid. The specimens for TEM were made by mechanically thinning and two-jet electrolyte polishing with 30%HNO3+70% methanol below -25 ℃.
3 Results
3.1 Effect of homogenization on hardness and electrical conductivity
The effect of homogenization on the hardness and electrical conductivity of studied alloy is shown Fig.1. It can be seen that during homogenization the as-cast alloy has obvious hardening effect that is similar to aging hardening behavior in traditional Al alloys. First, at the giving temperature, the hardness of the alloy increases at beginning then decreases with homogenization time. Second, when the homogenization temperature increases the hardness peak value declines and the time correspond-ing to hardness peak value is shortened. On the other hand, the results in Fig.1(b) show that during homogenization the electrical conductivity of the alloy monotonously increases with increasing homogenization temperature and time.
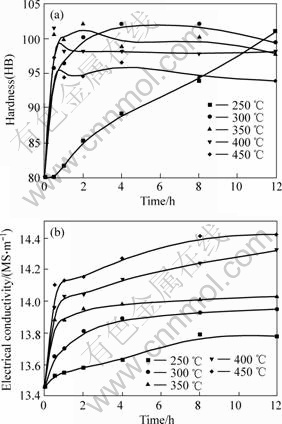
Fig.1 Hardness(a) and electrical conductivity(b) of studied alloy under different homogenization conditions
3.2 Effect of homogenization temperature on tensile properties
The effect of homogenization temperature (homogenization time is fixed at 8 h) on the tensile properties of as-hot rolled alloy is shown in Fig.2. It can be seen that the optimal homogenization treatment processing is holding at 300-350 ℃ for 8 h.
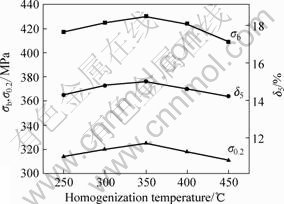
Fig.2 Tensile properties of as-hot rolled alloys under different homogenization treatment conditions
3.3 Microstructures at different homogenization processings
The typical optical and TEM microstructures of as-cast and different homogenization treatment alloys are shown in Figs.3 and 4, respectively.
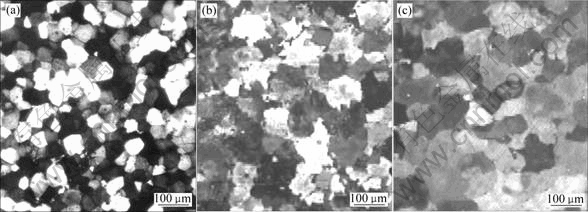
Fig.3 Optical microstructures under different homogenization processings
(a) as-cast alloy; (b) 300 ℃, 8 h; (c) 450 ℃, 8 h
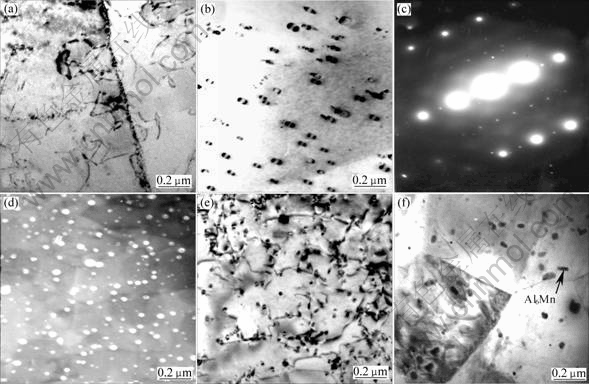
Fig.4 TEM microstructures of studied alloy under different homogenization treatment conditions
(a) As-cast alloy; (b) 300 ℃, 8 h , Al3(Sc, Zr) bright field; (c) 300 ℃, 8 h, diffraction pattern[133] Al;
(d) 300 ℃, 8 h, Al3(Sc, Zr),dark field; (e) 450 ℃, 8 h, bright field, two-beam condition; (f) 450 ℃, 8 h, bright field
It can be seen from Fig.3 that the grain size of as-cast alloy is 30-40 μm and that of the alloy after homogenization treatment at 450 ℃ for 6 h is 40-50 μm, showing the grain size of the alloy does not grow up obviously during homogenization treatment.
It is noted from Fig.4 that no second phase particles can be found within as-cast alloy (Fig.4(a)). After homogenization treatment at 250 ℃ for 6 h, Al3(Sc, Zr) particles begin to precipitate homogeneously within the matrix. The special coherent contrast of Al3(Sc, Zr) particles shows that this kind of Al3(Sc, Zr) particles is coherent with the matrix(Figs.4(b) and (c)). When homogenization temperature is higher than 400 ℃, the distribution density of Al3(Sc, Zr) particles begins to decrease and Al6Mn particles occur (Figs.4(e) and (f)).
4 Discussion
4.1 Reason for hardness variation of alloys during homogenization
In direct chill casting condition, supersaturated solid solutions containing Sc and Zr are formed in Al-6Mg-0.4Mn-0.25Sc-0.12Zr alloy ingot. It was pointed[8-9] that when the ingot is heated this kind of aluminum solid solution is very unstable and begins to decompose rapidly and then Al3(Sc, Zr) and Al6Mn particles precipitate. The lattice parameter of Al3(Sc, Zr) particles is nearly equal to that of the aluminum solid solution and Al3(Sc, Zr) phase can easily nucleate because its nucleation critical size is very small. The results in Refs.[8, 10-11] indicate that the pregnant period of Al-Sc alloy solid solution is three or four times less than that of Al-Mn and Al-Zr alloy. Adding of Zr to Al-Sc alloy can decrease the coagulating and coarsening speed of Al3Sc particles. This phenomenon has very great practical value because it guarantees Al-Mg-Mn- Sc-Zr alloy to keep good performance.
It is known from Fig.1 that with homogenization temperature rising, hardness peak value is reduced and the time corresponding to hardness peak value is shortened. This is because the yield stress is dependent on the cutting between dislocation and Al3(Sc, Zr) particles. In the giving temperature, at the beginning of homogenization Al3(Sc, Zr) particles are very small and the yield stress is low. With increasing of homogenization time, the volume fraction and size of Al3(Sc, Zr) particles increase, then yield stress is also increased. When homogenization temperature increases, the precipitation rate of Al3(Sc, Zr) particles is faster and the particles is easy to be coarsened, so the time corresponding to hardness peak value is shortened, at the same time, hardness peak value is reduced. From Fig.4, it can be seen that in the condition of homogenization at 300 ℃ for 8 h, Al3(Sc, Zr) precipitates homogenously distribute and volume fraction of the precipitates is the largest, so the yield stress of as-hot rolled plate is the highest, showing the optimal homogenization processing of as-cast Al-Mg-Mn-Sc-Zr alloy is holding at 300- 350 ℃ for 6-8 h.
4.2 Reason for electrical conductivity variation of alloy during homogenization
According to Mathiessen theory[10], the electrical resistibility of the alloy can be expressed as follows:

where Δρs is the electrical resistance caused by the solid soluble atoms; Δρp is the electrical resistance caused by the precipitated phase; Δρv is the electrical resistance caused by the vacancy; Δρg and Δρd is the electrical resistance caused by the grain boundaries and dislocations, respectively.
Many researches[12-14] have pointed out that the most influence factor for electrical resistance is Δρs, follows by Δρp, Δρg, Δρv and Δρd. This is because the scattered ability to electron caused by the solute atoms that distort the aluminum matrix lattice is much greater than that caused by others, such as the precipitate phases. In the condition of direct chill casting, most of Mg, Mn, Sc and Zr elements are solutioned in the aluminum matrix, which raises Δρs, so the conductivity of the alloy is very low. During homogenization, supersaturated solid solution is decomposed and Al3(Sc, Zr) and Al6Mn particles precipitated, thus the solid solution depletes and Δρs greatly decreases. At the same time, the precipitation of Al3(Sc, Zr) and Al6Mn particles causes additional scattering and gives the increment of the electrical resistance, Δρp, but in the whole, the electrical conductivity of the alloy will increase along with the precipitation of Al3(Sc, Zr) and Al6Mn. And the more the precipitates, the greater the electrical conductivity of the alloy.
5 Conclusions
1) During homogenization as-cast Al-6Mg-0.4Mn- 0.25Sc-0.12Zr alloy has obviously hardening effect that is similar to aging hardening behavior in traditional Al alloys.
2) During homogenization the decomposition and precipitation of the supersaturate solid solution containing Sc and Zr which is formed during direct chilling casting are responsible for the hardness and electrical conductivity variation of the alloy.
3) The optimal homogenization processing of the as-cast alloy is holding at 300-350 ℃ for 6-8 h.
Reference
[1] TIAN Rong-zhang. Hand Book of Aluminum Alloy and Processing[M]. Changsha: Central South University Press, 2000: 232-250. (in Chinese)
[2] PARKER B A, ZHOU Z F, NOLLEX P. The effect of small additions of scandium on the properties of aluminum alloys[J]. Journal of Materials Science, 1995, 30(2): 452-458.
[3] YIN Zhi-min, PAN Qing-lin, JIANG Feng. Effect of minor Sc and Zr on the microstructure and mechanical properties of Al-Mg based alloys[J]. Materials Science and Engineering A, 2000, A280(1): 151-155.
[4] FILATOR Y A, YELAGIN V I, ZAKHAROV V V. New Al-Mg-Sc alloys[J]. Materials Science and Engineering A, 2000, A280(1): 97-101.
[5] KENDIG K L, MIRACLE D B. Strengthening mechanisms of an Al-Mg-Sc-Zr alloy[J]. Acta Materialia, 2002, 50(16): 4165-4175.
[6] MARQUIES E A, SEIDMAN D N. Nanoscale structural evolution of Al3Sc precipitates in Al(Sc) alloys[J]. Acta Materialia, 2001, 49: 1909-1919.
[7] YIN Zhi-min, JIANG Feng, PAN Qing-lin, et.al. Microstructure and mechanical properties of Al-Mg and Al-Zn-Mg based alloys containing minor Sc and Zr[J]. Trans Nonferrous Met China, 2003, 13(3): 515-520.
[8] BEREZINA A L. Structural state and decomposition kinetics in rapidly quenched Al-Sc, Al-Mg-Sc alloys[J]. Materials Science Forum, 2002, 396/402: 763-768.
[9] AIURA T, SUGAWARA N, MIURA Y. The effect of scandium on the as-homogenized microstructure of 5083 alloy for extrusion[J]. Materials Science and Engineering A, 2000, A280(1): 139-145.
[10] IWAMURA S, NAKAYAMA M, MIURA Y. Coherency between Al3Sc precipitate and the matrix in Al alloys containing Sc[J]. Materials Science Forum, 2002, 396/402: 1151-1156.
[11] BEREZINA A L, CHUISTOV K V, KOLOBNEV N I, et al. Sc in aluminum alloys[J]. Materials Science Forum, 2002, 396/402: 741-746.
[12] BATAWI E, MORRIS D G, MORRIS M A, et al. Effect on small alloying additions on behavior of rapidly solidified Cu-Cr alloy[J]. Materials Science and Technology, 1990, 6(9): 892-899.
[13] TIAN Shi. Physical Properties of Metals and Alloys[M]. Beijing: Aeronautical Industry Press, 1994.(in Chinese)
[14] ZHANG Sheng-long, YIN Zhi-min, SONG Lian-peng, et al. Effect of aging treatment on electrical conductivity[J]. Rare Metals Materials Engineering, 2003, 32(2): 126-129. (in Chinese)
____________________________
Foundation item: Project(2005CB623705-01) supported by the National Key Fundamental Research and Development Program of China; Project(MKPT-2004-16ZD) supported by the National 10th Five-Year Plan Program
Received date: 2006-12-24; Accepted date: 2007-03-27
Corresponding author: NIE Bo, Senior Engineer; Tel: +86-451-86562066; E-mail: nnbbyyxx@163.com
(Edited by ZHAO Jun)