
Effect of hot plastic deformation on microstructure and
mechanical property of Mg-Mn-Ce magnesium alloy
JIAN Wei-wei(简炜炜), KANG Zhi-xin(康志新), LI Yuan-yuan(李元元)
School of Mechanical Engineering, South China University of Technology, Guangzhou 510640, China
Received 15 July 2007; accepted 10 September 2007
Abstract: Hot plastic deformation was conducted using a new solid die on a Mg-Mn-Ce magnesium alloy. The results of microstructural examination through OM and TEM show that the grain size is greatly refined from 45 μm to 1.1 μm with uniform distribution due to the occurrence of dynamic recrystallization. The grain refinement and high angle grain boundary formation improve the mechanical properties through tensile testing with the strain rate of 1.0×10-4 s-1 at room temperature and Vickers microhardness testing. The maximum values of tensile strength, elongation and Vickers microhardness are increased to 256.37 MPa, 17.69% and HV57.60, which are 21.36%, 133.80% and 20.50% more than those of the as-received Mg-Mn-Ce magnesium alloy, respectively. The SEM morphologies of tensile fractured surface indicate that the density and size of ductile dimples rise with accumulative strain increasing. The mechanism of microstructural evolution and the relationship between microstructure and mechanical property of Mg-Mn-Ce magnesium alloy processed by this solid die were also analyzed.
Key words: magnesium alloy; plastic deformation; grain refinement; microstructural evolution; mechanical property
1 Introduction
Magnesium is one of the lightest metals commonly used, which is thus very attractive for application as structural materials. It also has a number of other desirable features including good ductility, better damping characteristics than aluminum and excellent castability[1-3]. Due to these characteristics, magnesium and its alloys have high potential as metallic structural materials for saving the increasing shortage of natural resources and the world-wide implement of stricter environmental regulation. However, the hexagonal close-packed(HCP) lattice structure of these alloys provides limited number of slip systems and a consequent difficulty in forming structural components through common processing procedures[4-5] at relatively low temperature. This disadvantage is now regarded as the main reason that limits the application of magnesium alloys.
Nowadays, many plastic deformation procedures at elevated temperature have been investigated to prepare magnesium alloy products. In all these methods, equal-channel angular pressing(ECAP) attracted the growing interest of specialists in materials science. This is due to the several advantages of ECAP procedure. Firstly, the materials processed by ECAP can possess the ultrafine grained structures of a granular type containing mainly high angle grain boundaries. Secondly, the samples can provide the stable properties by forming the uniform nanostructures within the whole volume[6]. The solid die used in ECAP contained two channels with the same cross-sectional area and the angle of intersection of two channels is usually 90?. So their repeat deformation is possible and intense plastic strain is introduced into materials without changing the cross-sectional area of billets[7].
Inspired by the configuration of ECAP die, a new solid die was designed in this experiment and several passes of hot plastic deformation were conducted to produce the samples with different grain sizes. Grain refinement and mechanical property of Mg-Mn-Ce magnesium alloy deformed by this solid die were analyzed.
2 Experimental
2.1 Solid die
The solid die used in this experiment consisted of two channels: a perpendicular channel and a horizontal channel. The bottom of perpendicular channel intersected with horizontal channel at the middle position of the top wall of horizontal channel to form a special path liking a conversed capital letter “T”, as shown in Fig.1.
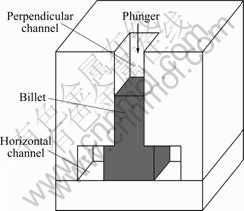
Fig.1 Schematic diagram of solid die
The two channels had the same cross-sectional area that can be a square or a circle. The angle of intersection of these two channels was 90?. Before deformation, the billet was machined to make sure that it can be inserted into the perpendicular channel and then the plunger was used to press the billet through perpendicular channel into horizontal channel. After that, a pass of deformation was completed, then the sample can be taken out and repeatedly deformed. Although the true strain imposed on the billets is still under investigation until now, it is apparent that the deformation is severely plastic.
2.2 Materials and procedure
The experimental samples with the size of 60 mm× 22 mm×22 mm were spark erroded from as-received magnesium alloy plates, whose chemical composition is listed in Table 1.
Table 1 Chemical composition of investigated alloy (mass fraction, %)

Before deformation, the samples were polished to get rid of any defects on surface. The solid die was heated in a special furnace that was very similar to the well furnace. After heating at 623 K for 30 min, the thermal equilibrium in the furnace was obtained and then a sample was inserted into the perpendicular channel and kept at that temperature for another 10 min. The lubricant in the experiment was MoS2. The hydraulic press with a total 5 000 kN pressure was imposed on the sample into the horizontal channel at the speed of 2 mm/s. Because the cross-sectional area of the two channels was the same, the repeated deformation was possible. When the selective deformation passes were finished, the samples were water quenched immediately and cut parallel to longitudinal axis.
Specimens for microstructural investigation were cut from the center of the as-pressed samples with the direction perpendicular to the longitudinal axis. The metallographic microstructures of the alloy were examined with an Olympus optical microscope(OM). Specimens were ground mechanically to a mirror-like surface using abrasive papers and 0.5 μm diamond paste and then etched in mixed acid solution of 4.2 g picric acid, 10 mL of acetic acid, 10 mL of distilled water and 70 mL of ethanol. The mean grain size, d, was determined from measurement conducted on the 80-100 grains using the linear intercept method.
The internal microstructure observation were conducted using JEM-100CXⅡtransmission electron microscopy(TEM). Samples were machined into thin disks with thickness of about 0.3 mm and diameter of 3 mm, and then ground to the thicknesses of about 0.08 mm. After that, the disks were electropolished using a twin-jet facility with a mixed solution of 10% HNO3 and 90% C2H5OH.
The tensile properties of the alloy were investigated. The gauge length of the sample was 20 mm and the cross-sectional diameter was 4 mm. The orientation of the tensile specimen was parallel to the longitudinal axis. The tensile tests were conducted at room temperature using a testing apparatus operating at a constant rate of cross-head displacement with initial strain rate of 1.0×10-4 s-1. All tensile specimens were pulled to failure to obtain the total elongation. The fractured surface of the specimens pulled to failure was observed by SEM. After being polished to a mirror-like surface using 2 μm diamond paste, the Vickers microhardness testing was conducted on the cross-section of the samples and for each sample there were 15 measurements taken at equal-distant points. The testing pressure was 0.98 N.
3 Results and discussion
3.1 Microstructural evolution
Fig.2 shows optical micrographs of the as-received billets and as-pressed billets after various passes. In the microstructure of the as-received billet in Fig.2(a), the average grain size is 45 μm. It is clear that the grain structure is not homogeneous but a mixed one of coarse grains and relatively small grains. In Fig.2(b), the sample is pressed by two passes. It is apparent that some fine equiaxed grains appear around the boundaries of the coarsened grains. This is the evidence that dynamic recrystallization takes place.
The main driving force of recrystallization is the stored energy of dislocations, and dislocation density increases with increasing amount of deformation[8]. Since the experimental material has a mixed structure, its deformation is not uniform due to the fact that the neighboring grains need to accommodate each other. Dislocations generated during deformation do not distribute uniformly in the whole sample and dynamic recrystallization tends to take place at these zones where dislocation densities are high[9]. Therefore, mixed grain structures are formed at the first stage and even during the middle stage, as seen in Fig.2(b). Once dynamic recrystallization takes place and new grains are formed, the dislocation density decreases sharply at these places.
In the next pass, dislocations generated by continuous deformation will accumulate in the coarse grains and consequently induce dynamic recrystallization at these places, as shown in Fig.3 Therefore, the fraction of fine grains increases with deformation pass number. Finally, after the fourth pass, the average grain size of the experimental alloy is refined to 1.1 μm, as shown in Fig.2(c). In the following pass, the average grain size nearly remains the same and the distribution is homogenous, as seen in Fig.2(d).
During deformation by using this solid die, the angles of grain boundaries are also increased. Fig.4 shows the TEM images of the experimental alloy pressed by three passes and six passes. It is apparent that the grain boundary angles in Fig.4(a) are relatively low (<90?), as illustrated by the arrows. After the sixth pass deformation, high angle grain boundaries are attained as shown by arrows in Fig.4(b). The grain boundaries meet at angles of about 120? at the triple point, which indicates that the fine structure is near the equilibrium state.
3.2 Mechanical properties
Fig.5 shows the true stress versus strain curves for the as-received, the third pass and the sixth pass pressed samples pulled to failure. It is seen that the mechanical properties of experimental alloy are improved after hot plastic deformation using the solid die after the third pass and the sixth pass.
The mechanical properties of experimental alloy pressed from one to six passes are represented in Fig.6. It is obvious in Fig.6(a) that the tensile strength slightly goes up to 216.56 MPa at the second pass and then increases sharply to 254.6 MPa at the fourth pass. After the fourth pass, the strength nearly remains constant. The maximum value of tensile strength during deformation is 256.37 MPa at the fifth pass, which is about 21.36% more than that of as-received alloy.
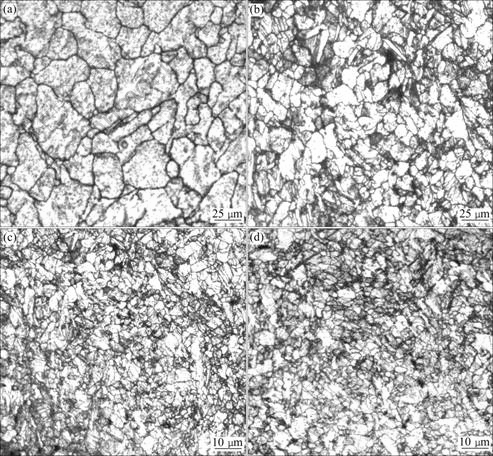
Fig.2 OM images of Mg-Mn-Ce magnesium alloy: (a) As-received; (b) 2nd pass; (c) 4th pass; (d) 6th pass
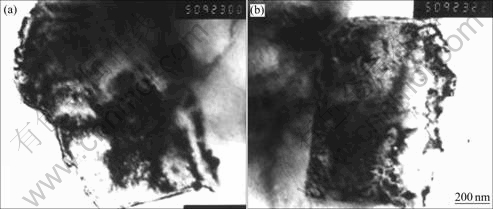
Fig.3 TEM images of fine structure: (a) 5th pass; (b) 6th pass
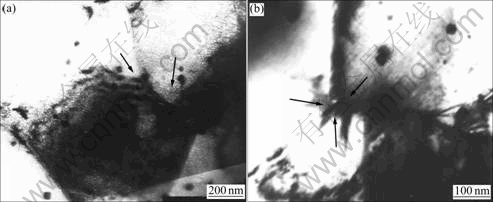
Fig.4 TEM images of fine structure: (a) 3rd pass; (b) 6th pass
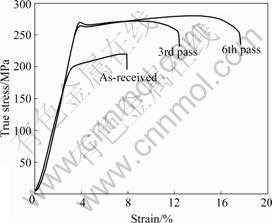
Fig.5 True stress vs strain for as-received, 3rd pass and 6th pass samples
Although the mechanical property of crystalline materials is determined by several factors, the average grain size of the materials plays a very significant and often a dominant role[7]. The relationship between strength and average grain size can be stated by Hall-Petch equation[10-11], which means the strength increases as the average grain size is reduced. As illustrated in the Fig.2, finer microstructures are obtained during the first several passes with the dynamic recrystallization mechanism. Accordingly, the tensile strength increases at the same time. When it comes to the fifth pass, the average grain size reduces to the minimum value as well as the tensile strength reaches the maximum value. In the following deformation, the average grain size remains constant and the plot of tensile strength is also horizontal.
Fig.6(b) represents the relationship between elongation and number of pass. It is apparent that the elongation to failure increases as the deformation pass increases before the fourth pass and then nearly remains constant. The maximum value of elongation reaches 17.69% at the sixth pass, which is 133.80% more than 7.60% of the as-received sample. It is well known that magnesium alloy exhibits poor ductility at ambient temperature because its hexagonal close packed lattice provides limited slip system[12-15]. In this experiment,the fraction of fine equiaxed dynamic recrystallized grain increases with the deformation pass increasing, which makes the accommodation between adjacent grains more easy during deformation.
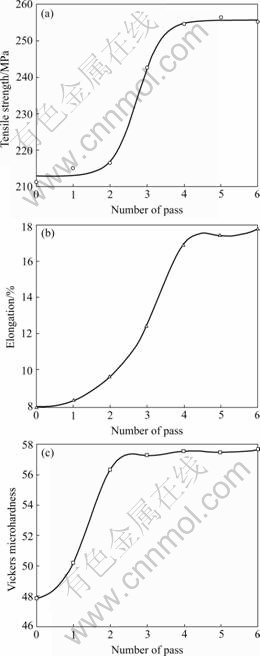
Fig.6 Mechanical properties of Mg alloy after pressing: (a) Tensile strength; (b) Elongation; (c) Vickers microhardness
Fig.6(c) shows the curve of Vickers microhardness vs. the number of pass. The value of microhardness increases from HV47.8 to HV56.31 before the second pass and remains nearly constant from the third pass to the sixth pass. The maximum value of Vickers microhardness is HV57.60, which is about 20.50% more than the value of as-received one.
SEM morphologies of tensile fractured surface of as-received and pressed alloy after the fourth pass are shown in Fig.7. The fractured surface of the as-received alloy possesses few ductile dimples, therefore it is the brittle fracture mechanism. However, after four passes deformation, the density of ductile dimples increases greatly and there are some small dimples in the relatively big dimples. This is the evidence that the ductility is improved.
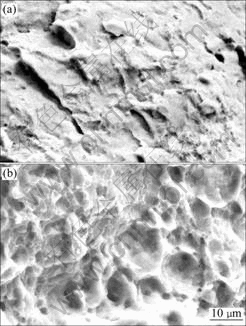
Fig.7 Fractured surface morphologies of Mg alloy: (a) As- received; (b) 4th pass
4 Conclusions
1) The new solid die in this study can introduce severe plastic strain to Mg-Mn-Ce magnesium alloy during hot deformation. The coarse grains with the average grain size of 45 μm are greatly refined to equiaxed homogenous grains with grain size of 1.1 μm due to dynamic recrystallization as well as the fine structures formed with high angle grain boundaries.
2) Tensile testing indicates that the hot plastic deformation can improve the mechanical properties of Mg-Mn-Ce magnesium alloy. The maximum values of tensile strength, elongation to failure at room temperature and Vickers microhardness are 256.37 MPa, 17.69% and HV57.60, which are 21.36%, 133.80% and 20.50% more than those of the as-received Mg-Mn-Ce magnesium alloy, respectively.
References
[1] MORDIKE B L, EBERT T. Magnesium properties-applications- potential [J]. Materials Science and Engineering A, 2001, 302(1): 37-45.
[2] ELIEZER D, AGHION E, FROES F H. Magnesium science, technology and applications [J]. Advanced Performance Materials, 1998, 5(3): 201-212.
[3] KANG Z X, MORI K, OISHI Y. Surface modification of magnesium alloys using triazine dithiols [J]. Surface and Coatings Technology, 2005, 195(2/3): 162-167.
[4] KUBOTA K, MABUCHI M, HIGASHI K. Processing and mechanical properties of fine-grained magnesium alloys [J]. Journal of Materials Science, 1999, 34(10): 2255-2262.
[5] MATSUBARA K, MIYAHARA Y, HORITA Z, LANGDON T G. Developing superplasticity in a magnesium alloy through a combination of extrusion and ECAP [J]. Acta Materialia, 2003, 51(11): 3073-3084.
[6] VALIEV R Z, ISLAMGALIEV R K, ALEXANDROV I V. Bulk nanostructured materials from severe plastic deformation [J]. Progress in Materials Science, 2000, 45(2): 103-189.
[7] VALIEV R Z, LANGDON T G. Principles of equal-channel angular pressing as a processing tool for grain refinement [J]. Progress in Materials Science, 2006, 51(7): 881-981.
[8] LI Y Y, ZHANG D T, CHEN W P, LIU Y, GUO G W. Microstructure evolution of AZ31 magnesium alloy during equal channel angular extrusion [J]. Journal of Materials Science, 2004, 39(11): 3759-3761.
[9] KIM W J, AN C W, KIM Y S, HONG S I. Mechanical properties and microstructures of an AZ61 Mg alloy produced by equal channel angular pressing [J]. Scripta Materialia, 2002, 47(1): 39-44.
[10] HALL E O. The deformation and ageing of mild steel(Ⅲ): Discussion of results [J]. Proceedings of the Physical Society of London, Section B, 1951, 64(9): 747-753.
[11] PETCH N J. The cleavage strength of polycrystals [J]. Journal of the Iron and Steel Institute, 1953, 174(5): 25-28.
[12] AGNEW S R, MEHROTRA P, LILLO T M, STOICA G M, LIAW P K. Texture evolution of five wrought magnesium alloys during route A equal channel angular extrusion: Experiments and simulations [J]. Acta Materialia, 2005, 53(11): 3135-3146.
[13] WANG Q D, CHEN Y J, ZHANG L J, LIN J B, ZHAI C Q. Microstructure and mechanical properties of AZ31-0.5%Si alloy processed by ECAP [J]. Trans Nonferrous Met Soc China, 2006, 16(S3): 1660-1663.
[14] FIGUEIREDO R B, CETLIN P R, LANGDON T G. The processing of difficult-to-work alloys by ECAP with an emphasis on magnesium alloys [J]. Acta Materialia, 2007, 55(14): 4769-4779.
[15] SEGAL V M. Equal channel angular extrusion: From macromechanics to structure formation [J]. Materials Science and Engineering A, 1999, 271(1/2): 322-333.
(Edited by YANG Bing)
Foundation item: Project(2005B10301020) supported by the Science and Technology Development Program of Guangdong Province, China
Corresponding author: KANG Zhi-xin; Tel: +86-20-87112948; E-mail: zxkang@scut.edu.cn