
Microstructure and thermal expansion of Ti coated diamond/Al composites
YANG Bo(杨 博), YU Jia-kang(于家康), CHEN Chuang(陈 闯)
State Key Laboratory of Solidification Processing, Northwestern Polytechnical University, Xi’an 710072, China
Received 16 September 2008; accepted 14 January 2009
Abstract: A titanium coating fabricated via vacuum vapor deposition for diamond/Al composites was used to improve the interfacial bonding strength between diamond particles and Al matrix, and the Ti coated diamond particles reinforced Al matrix composites were prepared by gas pressure infiltration for electronic packaging. The surface structure of the Ti coated diamond particles was investigated by XRD and SEM. The interfacial characteristics and fracture surfaces were observed by SEM and EDS. The coefficient of thermal expansion(CTE) of 50% (volume fraction) Ti coated diamond particles reinforced Al matrix composites was measured. The Ti coating on diamond before infiltration consists of inner TiC layer and outer TiO2 layer, and the inner TiC layer is very stable and cannot be removed during infiltration process. Fractographs of the composites illustrate that aluminum matrix fracture is the dominant fracture mechanism, and the stepped breakage of a diamond particle indicates strong interfacial bonding between the Ti coated diamond particles and the Al matrix. The measured low CTEs (5.07×10-6-9.27×10-6 K-1) of the composites also show the strong interfacial bonding between the Ti coated diamond particles and the Al matrix.
Key words: composites; coating; diamond; infiltration; coefficient of thermal expansion
1 Introduction
In the semiconductor industry, the increasing extent of integration and the decreasing feature size of electronic chips have led to a significant increase in power density[1]. In order to dissipate the heat generated in chips and to increase the reliability of electronic packaging effectively, some new materials which have higher thermal conductivity(TC) and more suitable coefficient of thermal expansion(CTE) should be adopted. Moreover, the low density is desirable in avionics and portable systems such as lap-top computers and cellular telephones.
The traditional packaging materials cannot meet the requirements of rapidly developing semiconductor industry. The currently used packaging materials include ceramics such as AlN, Al2O3 and SiC, and metal matrix composites such as Cu/W, Cu/Mo, Al/Si and Al/SiC [2-7]. Their CTE mismatches are moderate for chip materials, but TCs are insufficient to remove the generated heat from devices.
Diamond has a extremely high modulus, a very low coefficient of thermal expansion and the highest thermal conductivity in all natural materials[8-10]. Therefore, it is an attractive thermal management material used in modern electronic packaging, especially it is regarded as an ideal reinforcement for aluminium matrix composites owing to the low cost of metal matrix. Nevertheless, Al4C3 was formed in uncoated diamond particles reinforced aluminum matrix composites prepared by gas pressure infiltration. It is undesirable because Al4C3 is a hydrophilic and brittle phase, and prone to act as the thermal diffusion barrier at the interface, so the long-term stability of uncoated diamond/Al composites during thermal cycling and exposure to moist environments remains to be evaluated[11-12]. SiC coating on diamond particles was shown to be effective to prevent the formation of Al4C3, however, the thermal conductivity of composites was impaired by the additional interfacial layer[13], as a result of the poor interfacial bonding between the diamond particles and the SiC coating.
In the present study, Ti coating is used to prevent the formation of Al4C3 and to improve the interfacial bonding strength between diamond particles and Al matrix. The Ti coated diamond particles reinforced Al matrix composites are prepared via gas pressure infiltration. The surface structure of the Ti coated diamond particles is investigated by X-ray diffractometer and scanning electron microscope. The interfacial characteristics and fracture surfaces are observed by scanning electron microscope and energy dispersive spectrometer. The CTE of 50% (volume fraction) Ti coated diamond particles reinforced Al matrix composites is also measured.
2 Experimental
2.1 Materials
Al-7Si alloy was used as a matrix material. Synthetic diamond single crystals with designated average particle diameter of 54 μm and anomalous shapes were produced by high pressure and high temperature(HPHT) processing and Ti coating on the diamond particles was fabricated via vacuum vapor deposition. The mass increase of the coated diamond particles is about 1%-3% corresponding to different particle sizes. The Ti coated diamond particles preform was tap-packed with approximate 50% volume fraction for all samples.
2.2 Composites preparation
A graphite crucible containing the Al-7Si alloy melt superheated to 800 ℃ was placed in the lower chamber of infiltration apparatus, and the diamond preform that was in a steel pipe was placed in the upper chamber of the infiltration apparatus. Infiltration was fulfilled including heating the preform in air at about 0.1 MPa to a temperature of 700 ℃ for 10 min and infiltrating the Al-7Si alloy melt into the perform at an air pressure of 1.2 MPa. Cooling of composites to 500 ℃ occurred in less than 4 min after pressurizing the melt. The samples obtained were of cylindrical shape with a diameter of 5 mm and a height of 20 mm. A detailed description of gas pressure infiltration processing was given in Ref.[14].
2.3 Characterization
A Philips X′ Pert MPD Pro X-ray diffractometer (XRD) was applied to investigating the phase composition of the Ti coated diamond particles. Zeiss SUPRA 55 scanning electron microscope(SEM) and Oxford INCA energy dispersive spectrometer(EDS) were used to characterize the morphology of the Ti coated diamond particles and fracture surfaces of the composite samples. The microstructure and the chemical composition of the composites were studied by SEM and EDS. The CTE was measured on a DIL 402C thermal dilatometer (NETZSCH Co.) with a heating rate of 5 ℃/min. And argon atmosphere with a flowing rate of 50 mL/min was used to keep the chamber temperature consistent. To diminish systematic errors, the dilatometer was calibrated by measuring an alumina sample under identical conditions.
3 Results and discussion
3.1 Microscopy and phase composition of Ti coated diamond particles
To improve the interfacial bonding strength between diamond particles and aluminium matrix and to inhibit the formation of Al4C3 resulting from direct contact between the diamond particles and the Al melt, strong carbide-forming element, titanium, was deposited on the surfaces of the diamond particles to obtain the Ti coated diamond particles. Fig.1 and Fig.2 illustrate the morphologies of the Ti coated diamond particles. Fig.3 shows the phase composition of the Ti coated diamond particles by XRD.
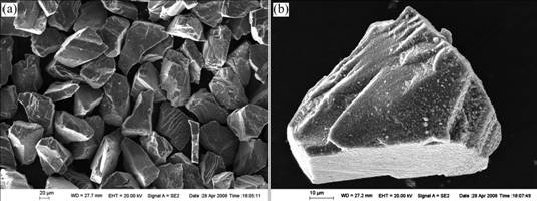
Fig.1 SEM micrographs of Ti coated diamond particles: (a) Anomalous diamond particles; (b) Ti coating
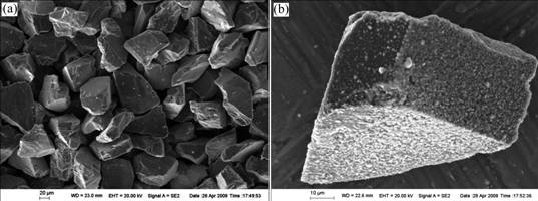
Fig.2 SEM micrographs of Ti coated diamond particles before infiltration: (a) Morphology; (b) Oxidation of Ti coating

Fig.3 Phase composition of Ti coated diamond particles: (a) After deposition; (b) Oxidation before infiltration
The Ti coated diamond particles feature anomalous shapes with sharp edges and obvious cleavage steps resulting from mechanical milling (Fig.1(a)). Ti coating is continuous and compact, spreading on the surface of the diamond particles uniformly, and some white Ti particles are adhered to the surface of the diamond particles (Fig.1(b)). Fig.2 shows the SEM micrographs of the Ti coated diamond particles before infiltration. The morphology of them is not changed visibly, but the surfaces of the diamond particles are more black and gray. This alteration is attributed to the oxidation of the Ti coating.
Fig.3(a) displays the phase composition of the Ti coated diamond particles by XRD analysis, suggesting that TiC has already been formed via deposition processing. Titanium atoms can react with carbon atoms on the surface of diamond at high temperatures, generating a stable inner TiC layer between the surfaces of the diamond and outer Ti layer. The inner TiC layer can be combined with the diamond metallurgically, and the outer Ti layer could be wetted by aluminum matrix very well, so the interfacial bonding strength between diamond particles and aluminum matrix can be enhanced significantly.
Fig.3(b) indicates that the oxide on the Ti coating is TiO2. With the temperature increasing, titanium reacts with adsorbed oxygen and residual oxygen in the preform at experimental temperature of 700 ℃:
Ti+O2=TiO2 (1)
It could be seen from Fig.3(b) that the Ti peaks have disappeared completely, which is a proof to justify the phase transition of Ti to TiO2 caused by oxidation. It is worth noting that some very low TiC peaks have disappeared. QIN et al[15] studied the oxidation behavior of in situ synthesized TiC/Ti-6Al composites and they found that the oxidation of the composites was prior to TiC particulates because of the higher reactivity of TiC and O2. So the disappearance of some TiC peaks may be caused by the oxidation reaction of TiC at 700 ℃:
TiC+2O2=TiO2+CO2 (2)
Therefore, the Ti coating on the diamond particles via oxidation before infiltration consists of the inner TiC layer and the outer TiO2 layer.
3.2 Microstructure and interface of Ti coated diamond/Al composites
It is true that the optical microscopy of diamond/Al composites is quite difficult to achieve, especially for micro-sized diamond particles reinforced composites with the increase of volume fraction of diamond, because of the exceptional hardness of diamond excluding the use of classical metallographic techniques.
Thus, SEM is used in this study to reveal the microstructure of the Ti coated diamond/Al composites. Fig.4 shows the microscopy of the composites after coarse grinding with silicon carbide waterproof abrasive papers. As illustrated, the diamond particles are distributed throughout the Al matrix uniformly with a volume fraction of about 50%. Complete infiltration of the packed diamond particles is achieved and no pores or obvious defects are observed in the composites. Generally speaking, the infiltration quality of the Ti coated diamond/Al composites is excellent and the diamond particles appear to be well bonded to the Al matrix.
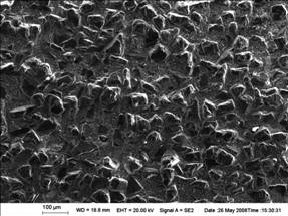
Fig.4 Microstructure of Ti coated diamond/Al composites
Fig.5 shows the results of EDS analysis on a Ti coated diamond particle via coarse grinding. It can be seen that titanium element exists popularly and encloses the diamond particle. The titanium element comes mainly from the inner TiC layer,hence, it is concluded that the inner TiC layer is very stable and cannot be removed during infiltration process. The inner TiC layer can prevent direct contact between the Al melt and the diamond particle, and it cannot react with Al melt. Thus, it can protect the diamond particle from possible thermal deterioration and inhibit the formation of undesirable Al4C3 caused by the reaction between Al melt and diamond.
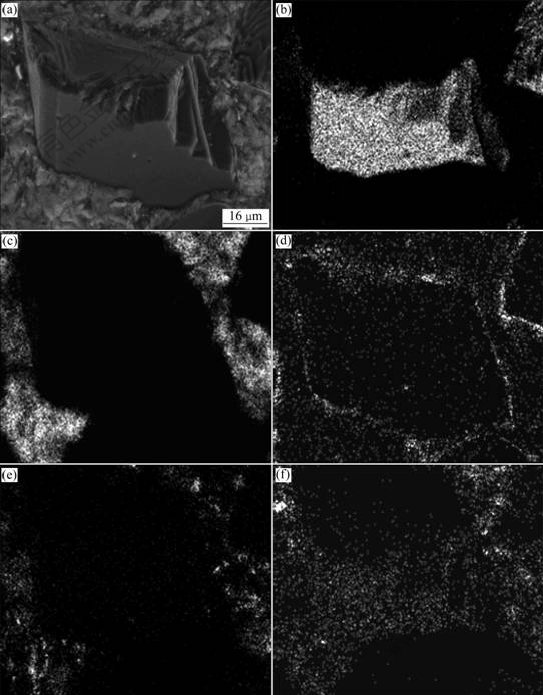
Fig.5 Morphology (a) and EDS area mapping on Ti coated diamond particle with distribution of C (b), Al (c), Ti (d), Si (e) and O (f)
It is also noted that another source of Ti element comes from the reducing reaction at 700 ℃:
Al+TiO2→Al2O3+Ti (3)
The whole TiO2, however, cannot be reduced completely by the Al melt due to the quick cooling of the composites to 500 ℃ occurring within 4 min after pressurizing the melt, so the outer layer of diamond particle consists of Ti and TiO2 after infiltration. At the same time, the reaction between Ti and Al melt cannot proceed because of the same reason mentioned above. Thus, most of Ti atoms gather on the surface of the diamond particle and a few Ti atoms diffuse in the Al matrix, as illustrated in Fig.5(d) (distribution of Ti). The existence of Al and Si close to or overlapping the region of Ti can also be seen on the diamond surface, suggesting a good bonding between the Ti coated diamond particles and the Al matrix.
Fig.6 presents the elemental compositions of interfacial reaction products between the Ti coated diamond particles and the Al matrix. According to the process conditions, Ti-Al and Ti-Si binary compounds may be difficult to form, and the formations of Ti-Al and Ti-Si solid solutions are more possible and reasonable as a result of the diffusion of Si atoms and Ti atmos.Therefore, the interface structure of diamond/TiC/ Ti(TiO2)/Ti-Al(Ti-Si) solid solution for the Ti coated diamond/Al composites is expected.
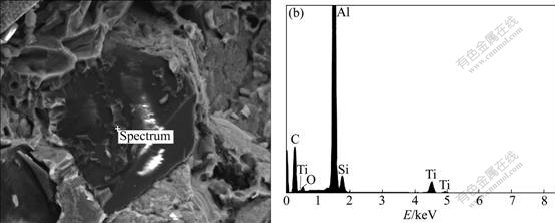
Fig.6 Chemical composition of interfacial reaction products between Ti coated diamond particles and Al matrix (a) and elemental composition of interface reactions products (b)
In general, the Ti coating can enhance the interfacial bonding strength between the diamond particles and the Al matrix, and improve the thermal stability of the diamond particles as well. These effects are difficult to be verified only by SEM and EDS. TEM analysis is considered a useful method even though the TEM specimen of diamond/Al composites is difficult to be prepared.
3.3 Fractography
The fracture surface morphologies of the ruptured composites are shown in Fig.7. As presented in Fig.7(a), the Ti coated diamond/Al composites with a high volume fraction of diamond can be fabricated by gas pressure infiltration with uniform distribution of diamond particles. A tight adhesion between the diamond particles and the Al matrix could be observed on the fracture surface. Fig.7(b) shows that the Al matrix adheres to the surfaces of some diamond particles, indicating that the interfacial bonding strength is higher than the tensile strength of the Al matrix. As shown in Fig.7(c), the Al matrix fails in a ductile manner on the surface of the diamond particle. It is worth noting that interfacial debonding is observed in Figs.7(c) and (d), but this is not the dominant fracture mechanism. Besides, the stepped breakage of a diamond particle is observed in Fig.7(d), suggesting a high interfacial bonding strength between the Ti coated diamond particles and the Al matrix.
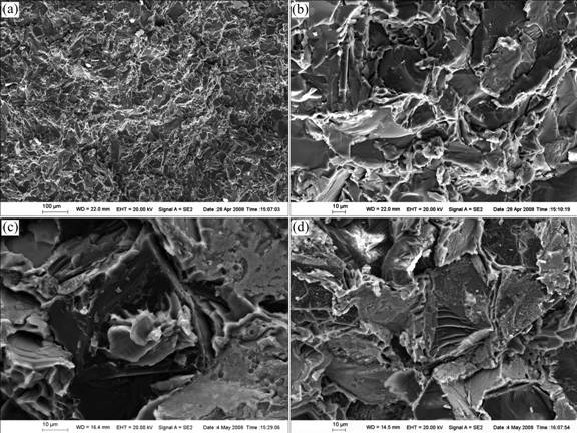
Fig.7 Fracture surface morphologies of Ti coated diamond/Al composites: (a) Uniform distribution of diamond particles; (b) Al matrix adhesion to diamond particles; (c) Ductile fracture of Al matrix; (d) Stepped breakage of diamond particle
3.4 Coefficient of thermal expansion
From 30 ℃ to 50 ℃, 100 ℃, 150 ℃ and 200 ℃, the measured CTEs of the Ti coated diamond/Al composites with about 50% (volume fraction) reinforcement are 5.07×10-6, 6.39×10-6, 8.29×10-6 and 9.27×10-6 K-1, respectively. It can be seen that the CTEs of the composites increase with increasing temperature, for reason of the thermal expansion nature of matrix alloy and the restriction at the interface between the Ti coated diamond and the Al matrix. The Ti coated diamond particles/Al composites, whose CTEs lie between the upper bound limit (10×10-6 K-1), given by the rule of mixtures, and the lower bound limit (3.7× 10-6 K-1), calculated by Turner’s model which assumes a homogeneous strain throughout the composites, account for the elastic material constants[16-17]. The CTE are not found to exceed the upper bound limit (10× 10-6 K-1) at 200 ℃, indicating strong interfacial bonding between the Ti coated diamond particles and the Al matrix.
4 Conclusions
1) Al matrix composites reinforced with Ti coated diamond particles are fabricated by gas pressure infiltration successfully. The diamond particles are dispersed in the Al matrix uniformly with about 50% volume fraction and the interfacial bonding between the diamond particles and the Al matrix is tight.
2) The Ti coating on the diamond particles before infiltration consists of inner TiC layer and outer TiO2 layer. The inner TiC layer is very stable and cannot be removed during infiltration process.
3) The matrix fracture is the dominant fracture mechanism for the composites. In addition, the stepped breakage of a diamond particle indicates strong interfacial bonding between the Ti coated diamond particles and the Al matrix.
4) Between 30 ℃ and 50 ℃, the CTE of 50% (volume fraction) Ti coated diamond/Al composites is only 5.07×10-6 K-1, and it is less than 9.27×10-6 K-1 between 30 ℃ and 200 ℃.
References
[1] ATLURI V P, MAHAJAN R V, PATEL P R, MALLIK D, TANG J, WAKHARKAR V S, CHRYSLER G M, CHIU C P, CHOKSI G N, VISWANATH R S. Theme article-critical aspects of high-performance microprocessor packaging [J]. Mater Res Bull, 2003, 28(1): 21-34.
[2] ZWEBEN C. Metal matrix composites for electronic packaging [J]. JOM, 1992, 44(7): 15-23.
[3] ZWEBEN C. Advances in composite materials for thermal management in electronic packaging [J]. JOM, 1998, 50(6): 47-51.
[4] JIN S H. Advances in thermal management materials for electronic applications [J]. JOM, 1998, 50(6): 46.
[5] CHUNG D D L. Materials for thermal conduction [J]. Appl Therm Eng, 2001, 21(16): 1593-1605.
[6] WEI Yan-guang, XIONG Bai-qing, ZHANG Yong-an, LIU Hong-wei, WANG Feng, ZHU Bao-hong. Property measurements on spray formed Si-Al alloys [J]. Trans Nonferrous Met Soc China, 2007, 17(2): 368-372.
[7] QIN Zhen-kai, YU Jia-kang, ZHANG Xiao-yu. Infiltration kinetics of pressureless infiltration in SiCp/Al composites [J]. Trans Nonferrous Met Soc China, 2005, 15(2): 321-324.
[8] WITEK A. Some aspects of thermal conductivity of isotopically pure diamond—A comparison with nitrides [J]. Diam Relat Mater, 1998, 7(7): 962-964.
[9] COE S E, SUSSMANN R S. Optical, thermal and mechanical properties of CVD diamond [J]. Diam Relat Mater, 2000, 9(9/10): 1726-1729.
[10] SCHUBERT T, TRINDADE B, WEISSGARBER T, KIEBACK B. Interfacial design of Cu-based composites prepared by powder metallurgy for heat sink applications [J]. Mater Sci Eng A, 2008, 475(1/2): 39-44.
[11] KLEINER S, KHALID F A, RUCH P W, MEIER S, BEFFORT O. Effect of diamond crystallographic orientation on dissolution and carbide formation in contact with liquid aluminium [J]. Scripta Mater, 2006, 55(4): 291-294.
[12] RUCH P W, BEFFORT O, KLEINER S, WEBER L, UGGOWITZER P J. Selective interfacial bonding in Al(Si)-diamond composites and its effect on thermal conductivity [J]. Compos Sci Technol, 2006, 66(15): 2677-2685.
[13] JOHNSON W B, SONUPARLAK B. Diamond/Al metal matrix composites formed by the pressureless metal infiltration process [J]. J Mater Res, 1993, 8(5): 1169-1173.
[14] YU J K, LI H L, SHANG B L. A functionally gradient coating on carbon fibre for C/Al composites [J]. J Mater Sci, 1994, 29(10): 2641-2647.
[15] QIN Y X, ZHANG D, LU W J, WEI P. Oxidation behavior of in situ synthesized (TiB+TiC)/Ti-Al composites [J]. Mater Lett, 2006, 60(19): 2339-2345.
[16] DELANNAY F. Thermal stresses and thermal expansion in MMCs [C]// KELLY A, ZWEBEN C. Comprehensive Composite Materials. Amsterdam:Elsevier Science Ltd, 2007: 341-369.
[17] BEFFORT O, KHALID F A, WEBER L, RUCH P, KLOTZ U E, MEIER S, KLEINER S. Interface formation in infiltrated Al(Si)/diamond composites [J]. Diam Relat Mater, 2006, 15(9): 1250-1260.
Foundation item: Project(60776019) supported by the National Natural Science Foundation of China
Corresponding author: YU Jia-kang; Tel: +86-29-88494987; E-mail: jkyu@nwpu.edu.cn
DOI: 10.1016/S1003-6326(08)60423-9
(Edited by YANG Bing)