
Influence of vacuum heat treatment on structure and micro-hardness of electroless Ni-P-SiC composite coating
LONG Shi-guo(龙士国)1, MA Zeng-sheng(马增胜) 1, HU Wen-bin(胡文彬)2, ZHOU Yi-chun(周益春)1
1. Key Laboratory of Low Dimensional Materials & Application Technology, Ministry of Education,
Faculty of Materials, Photoelectronic & Physics, Xiangtan University, Xiangtan 411105, China;
2. State Key Laboratory of Metal Matrix Composites, Shanghai Jiao Tong University, Shanghai 200030, China
Received 15 July 2007; accepted 10 September 2007
Abstract: The electroless Ni-P-SiC composite coatings were prepared and the influence of vacuum heat treatment on its structure and properties was analyzed. The Ni-P-SiC composite coatings were characterized by morphology, structure and micro-hardness. The morphology and structure of the Ni-P-SiC composite coatings were studied by scanning electron microscopy (SEM) and X-ray diffractometry (XRD), respectively. A great deal of particles incorporation and uniform distribution were found in Ni-P-SiC composite coatings. XRD results show a broad peak of nickel and low intensity SiC peaks present on as-deposited condition. Micro-hardness of as-deposited Ni-P-SiC composite coatings is improved greatly, and the best micro-hardness is obtained after heat treatment in a high vacuum at 400 ℃.
Key words: electroless Ni-P-SiC composite coating; vacuum heat treatment; micro-hardness; X-ray diffraction
1 Introduction
Nickel-phosphorous (Ni-P) is widely used as an electroless coating in different industries because of its high hardness, excellent corrosion and wear resistances and its uniform coating thickness. Co-depositing another metallic or non-metallic elements or abrasive/lubricate particles or combination of them in binary Ni-P matrix can further enhance these properties [1-3]. Recently, electroless nickel composite coatings have gained more attention in research community due to their ability to produce coatings that possess improved wear, abrasion and lubrication properties than Ni-P deposits. Several particles have been incorporated in the nickel matrix, and among them, the combinations that have received considerable attention are electroless nickel with SiC [4], B4C [5], Si3N4 [6], CeO2, TiO2 [2], Al2O3 [7] and PTFE [8] and the particles used are of the micron size. Among these coatings, the combination Ni-P-SiC has proved to be the most cost-effective and best-performing combination [3].
In general, a very important aspect in the characterization of a composite material containing hard particles is the bonding between the matrix and the reinforcement. Since electroless particle co-deposition processes take place at low temperature, no chemical interaction between the particles and nickel matrix is favoured, and the particles are only physically entrapped in the nickel matrix. In the as-deposited state, the nickel matrix is metastable (i.e. a supersaturated solid solution of phosphorus in nickel), and therefore these coatings are often heat-treated in order to promote phase transitions, which will influence their properties. The final properties of these coatings depend on the phosphorous content of the Ni-P matrix, which determines the structure of the coatings, and on the characteristics of the embedded particles such as type, shape and size. Most studies concerning Ni-P-hard particle systems are performed using some given or no-vacuum heat treatment and some commercial processes to obtain such composites. However, they ignore the influence of the different temperatures and atmosphere in the no-vacuum heat treatment on the structure, micro hardness and corrosion resistance of the composite coatings [9-10].
The major advantages of vacuum heating process are the absence of gas to chemically react with the heated surface, and degassing of the adsorbed hydrogen from the volume of the coatings and gas removal by the vacuum [11]. The purpose of this study was to investigate the influence of vacuum heat treatment on structure and micro-hardness of the coatings.
2 Experimental
Electroless Ni-P-SiC and Ni-P particle-free coatings were deposited on 30 mm×30 mm×0.1 mm mild carbon steel. The average size of SiC particles was approximately 3 μm. The mild carbon steel substrate was pre-treated before immersed in the bath. The pretreatment procedure of substrates is shown in Fig.1 (rinsing samples with de-ionized water).
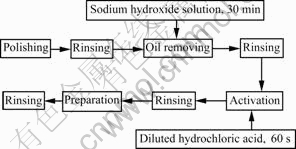
Fig.1 Pretreatment procedure of substrates of electroless plating
The main solution composition and experimental conditions for the two different coatings are listed in Table 1. All chemicals used were of analytic grade. In addition, a small count of stabilizer agents and complex non-ionic surfactant agents containing polyethylene glycol were introduced into the bath. Electroless composite bath contained particles pretreated by hydrofluoric acid. The bath was air-agitated and the agitation magnitude was adjusted for different SiC particles during plating. Mechanical stirring was used to keep particles from sediment.
Table 1 Composition of electroless plating solution and plating conditions
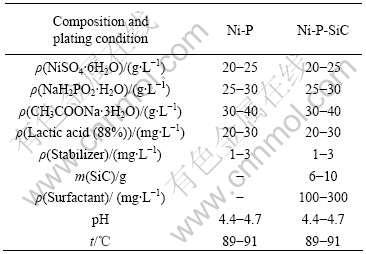
In order to study the change of the properties, the fabricated samples were thermally treated in a high vacuum environment pumped by a 300 l/s diffusion pump. The coatings were isothermally heat-treated for 1 h at different temperatures, i.e. 100, 200, 340, 400, 500 and 600 ℃. During the heating process the total pressure in the chamber was maintained below 4 mPa. Then the samples were allowed to cool down, for at least 15 min in the high vacuum environment prior to their exposure to the atmosphere.
Philips Sirion 200 field emission scanning electron microscope (SEM) was used to show the surface and cross-section morphology of composite coatings. The chemical composition of coatings was determined by energy dispersive spectrum (EDS) using SEM with a Noran Instruments microanalysis system. XRD was performed on a Bruker-AXS D500S theta-theta diffractometer with a diffracted beam graphite monochromator, using Cu Kα radiation. 2θ analyzed was 20?-90? with a step size of 0.01?. The micro-hardness of coatings was measured on the surface using HX-100 Vickers hardness tester at the load of 10 g (0.098 N). The lap time for each indentation was 20 s and the values reported represent the average and standard deviation of a minimum of five measurements.
3 Results and discussion
3.1 Micrograph and structure
SEM images of the polished coatings are shown in Figs.2(a) and (b). Fig.2(a) shows the surface morphology of Ni-P-SiC composite coatings. Obviously, SiC particles are uniformly distributed on the surface. Fig.2(b) shows that SiC particles uniformly and largely distributed in the coatings by virtue of surfactant and mechanical stirring. The presence of the SiC in the Ni-P layer affects the heterogeneity of the surface and increases the number of boundaries between Ni and other particles in the matrix. The embedded SiC grains into the amorphous matrix distinctly enlarge the surface development of the composite Ni-P-SiC layer, compared with Ni-P.
In general, electroless Ni-P coating structure and properties mainly depend on the amount of phosphorus present in the deposit. Hence, EDX analysis was carried out to study the effect of co-deposition of SiC particles on the chemical composition of the coating. The chemical content of as-deposited Ni-P and Ni-P-SiC composite coatings is given in Table 2. A marginal variation in phosphorus content is noticed for Ni-P and Ni-P-SiC composite coatings, i.e., 9.7% and 8.2%(mass fraction), respectively. Thus the chemical composition of the Ni-P matrix influences much with the incorporation of SiC particles.
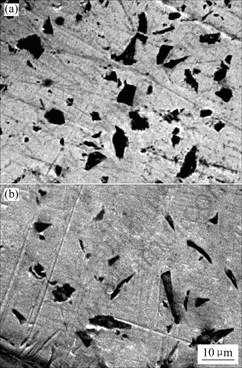
Fig.2 SEM morphologies of electroless Ni-P-SiC composite coatings: (a) Polished surface; (b) Cross-section
Table 2 Composition of as-deposited electroless Ni-P and Ni-P-SiC composite coatings*
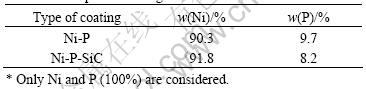
XRD patterns of the Ni-P-SiC layer at different vacuum heat treatment temperatures are shown in Fig.3. It is found that the structure of this type of coatings exhibiting a nickel matrix in the range of 2θ corresponds to the amorphous matrix of the Ni-P layer in up right corner of Fig.3 prepared under the same conditions. It is confirmed that structural changes from amorphous state to crystalline state can be obtained in Ni-P electroless coatings over 250 ℃ [12]. Fig.3(b) shows that the phase of the Ni-P-SiC composite coating doesn’t change distinctly, but vacuum heat treatment (400 ℃ for 1 h) of both Ni-P-SiC and Ni-P leads to complete crystallization of the amorphous matrix. After heat treatment at 400 ℃ for 1 h, the nickel phosphide (Ni3P) phase precipitates in the matrix and diffraction patterns show well-defined peaks corresponded to crystalline Ni, Ni3P and embedded particles shown in Fig.3(c).
3.2 Micro-hardness
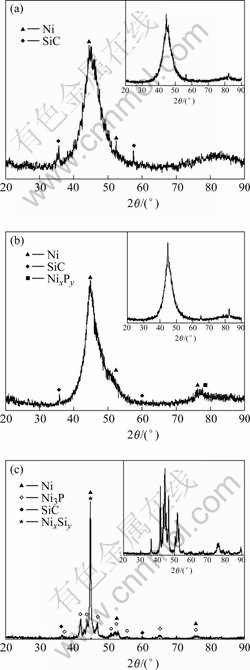
Fig.3 XRD patterns of Ni-P-SiC composite coatings after 1 h of annealing at different temperatures: (a) As-deposited; (b) 200 ℃; (c) 500 ℃
The micro-hardness of the Ni-P and Ni-P-SiC composite coatings is shown in Fig.4. As for as- deposited alloy, the micro-hardness HV50 of Ni-P-SiC composite coatings is 628.45, not too high compared with 573.24 of the electroless Ni-P coatings. After vacuum heat treatment, the micro-hardness of the composite Ni-P-SiC coatings significantly increases (Fig.4) signifying the increased adhesion between the particles and the matrix. This increased adhesion has a
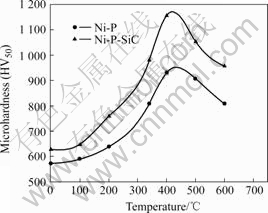
Fig.4 Microhardness of Ni-P and Ni-P- SiC composite coatings after vacuum heat-treatment at different temperatures
favorable impact on the abrasive wear resistance of the coatings.
The level of incorporation of particles and heat-treatment influence the hardness of the coatings. For ceramic (hard) particles, like SiC, an increase in the level of incorporation increases the hardness of the coatings. However, the influence of phosphorous can be seen on these annealed coatings arising from the formation of large amounts of hard Ni3P phase. The influence of heat treatment on the hardness of electroless Ni-P-SiC coatings in comparison with electroless Ni-P coating is shown in Fig.4.
The improvement of hardness after heat treatment exhibits a similar trend for these coatings, which suggests that the hardening mechanism upon annealing is the same for both electroless Ni-P-SiC and Ni-P composite coatings. Increase of hardness up to 400 ℃ is due to hardening because of the formation of the intermetallic Ni3P phase. The decrease in lattice defects and coarsening of the Ni3P particles cause a reduction in hardness when these coatings are annealed beyond 400 ℃. The reason is that the reaction takes place as following:
3Ni+SiC=Ni3Si+C (1)
According to the data in Refs.[13-14], the decrease of volume of the system is 1.244 cm3/mol [9]. This indicates that shrinkage, even porosity, will occur in electroless composite coatings after reaction of Ni with SiC. The mechanical properties of Ni-P-SiC composites deteriorate and the micro-hardness decreases after heat treatment at high temperature. Therefore after vacuum heat treatment the particles are coherent to the precipitated Ni3P and Ni grains, giving rise to a very high hardness of the coatings. However, with an increase of temperature, larger particles or their agglomerates are formed in the coatings and it will eventually be easier for a dislocation to loop between particles rather than to shear them.
4 Conclusions
1) Electroless deposited composite coatings exhibit an amorphous structure of the Ni-P matrix, in which crystalline silicon carbon is incorporated. Particles have not much influence on chemical composition, structure and crystalline phase.
2) During heating, the amorphous alloy in electroless Ni-P-SiC composite coatings crystallizes, and then reacts with SiC at high temperature.
3) The micro-hardness of electroless Ni-P-SiC composite coatings is higher than that of Ni-P alloy coating due to the existence of SiC particles, and the micro-hardness HV50 reaches to the maximum value (about 1 158) after heat treatment at 400 ℃ for 1 h.
References
[1] GROSJEAN A, REZRAZI M, TAKADOUM J. Hardness, friction and wear characteristics of nickel-SiC electroless composite deposits [J]. Surface Coating Technology, 2001, 137(1): 92-96.
[2] BALARAJU J N, SANKARA NARAYANAN T S N, SESHADRI S K. Electroless Ni-P composite coatings [J]. J Appl Electrochem, 2003, 33(2): 807-816.
[3] KALANTARY M R, HOLBROOK K A. Optimisation of a bath for electroless plating and its use for the production of nickel-phosphorus-silicon carbide coatings [J]. Trans Inst Met Finish, 1993, 71(1): 55-61.
[4] GROSJEAN A, REZRAZI M, BERCOT P. Some morphological characteristics of the incorporation of silicon carbide (SiC) particles into electroless nickel deposits [J]. Surface Coating Technology, 2000, 130(2/3): 252-256.
[5] GE J P, CHE R X, WANG X Z. Structure and properties of electroless Ni-P-B4C composite coatings [J]. Plate Surface Finish, 1998, 85(1): 69-73.
[6] BALARAJU J N, SESHADRI S K. Synthesis and corrosion behavior of electroless Ni-P-Si3N4 composite coatings [J]. J Mater Sci Letter, 1998, 17(10): 1297-1299.
[7] APACHITEI I, DUSZCZYK J, KATGERMAN L. Electroless Ni-P composite coatings: The effect of heat treatment on the microhardness of substrate and coating [J]. Scr Material, 1998, 38(9): 1347-1353.
[8] Ger M D, Joe H B. Effect of surfactants on codeposition of PTFE particles with electroless Ni-P coating [J]. Mater Chem Phys, 2002, 76(1): 38-45.
[9] GAO J Q, LIU L, WU Y T, SHEN B , HU W B. Electroless Ni-P-SiC composite coatings with superfine particles [J]. Surface Coating Technology, 2006, 200(20/21): 5836-5842.
[10] SARRET M, M?LLER C, AMELL A. Electroless NiP micro- and nano-composite coatings [J]. Surface Coating Technology, 2006, 201(1/2): 389-395.
[11] NOVAKOVIC J, VASSILIOU P, SAMARA K L. Electroless NiP-TiO2 composite coatings: Their production and properties [J]. Surface Coating Technology, 2006, 201(3/4): 895-901.
[12] DERVOS C T, VASSILIOU P, NOVAKOVIC J. Vacuum heated electroless nickel plated contacts [J]. IEEE Trans Compon Packag Technology, 2004, 27(1): 131-137.
[13] EINSPRUCH N G, LARRABEE G B. VLSI Electronics: Microstructure science, Vol. 6[M]. New York: Academic Press Inc, 1983.
[14] DEAN J A. Lange’s handbook of chemistry. 15th ed[M]. New York: McGraw-Hill, 1999.
(Edited by CHEN Can-hua)
Foundation item: Projects(05B008) supported by Scientific Research Fund of Hunan Provincial Education Department; project(104014) supported by Fok Ying Tong Education Foundation of Ministry of Education
Corresponding author: LONG Shi-guo; Tel: +86-13607325816; E-mail: longsg@xtu.edu.cn