
Multi-powder dam concrete with high performance and
low adiabatic temperature rise
LI Xin-yu(李新宇)1, CHEN Wen-yao(陈文耀)2, CHEN Wei-min(陈炜旻)1
1. Hydrochina Huadong Engineering Corporartion, Hangzhou 310014, China;
2. China Three Gorges Project Corporation, Yichang 430002, China
Received 10 August 2009; accepted 15 September 2009
Abstract: Based on the fluidity, strength, heat of hydration and loop crack resistance experiment of multi-powder paste, the components and proportion of multi-powder were optimized and the concrete properties were studied. The multi-powder consists of limestone powder, slag, fly ash and moderate heat Portland cement (PMH cement). The results show that the compressive strength of the multi-powder paste and mortar is close to those of PMH cement, fly ash paste and mortar currently used in dam concrete, yet the flexural strength is relatively higher. The multi-powder paste is featured by larger fluidity, lower heat of hydration and delayed cracking time. In comparison, less unit water consumption and cement is used in multi-powder concrete, and under premise of equal mechanical performance, deformation, thermal performance and durability, the adiabatic temperature rise at 28 d is reduced by 2 ℃. In this way, the crack resistance is improved and it is feasible both technically and economically to produce HPC for dam concrete.
Key words: multi-powder paste; dam concrete; high performance concrete; crack resistance; adiabatic temperature rise
1 Introduction
High performance concrete(HPC), put forward firstly in USA, is a new concept based on durability design of concrete structure. Durability of HPC is the primary technical performance, and it aims to enhance the durability and reliability by improving various performances before and after concrete setting and hardening[1]. It is different from convention concrete. Because of big difference in concrete structure position and environment and research purpose, so far no recognized definition of HPC has been formed. Yet, good durability is undoubtedly acknowledged the basic characteristic of HPC. As for mass concrete, in order to fulfill better durability, lower hydration heat and better crack resistance performance are indispensable. For arch dams higher than 300 m, high strength should be fulfilled because of high stress level inside the high arch dams. For example, the design of mass concrete for Ertan high arch dam (240 m) was required to follow the principle of high strength, medium elastic modulus and low heat[2]. The design of mass concrete for Xiaowan high arch dam (294.5 m) adds another principle, higher tensile strain capacity and no autogenous shrinkage, to acquire better crack resistance capability[3]. The design of Laxiwa high arch dam (250 m) follows the principle of high strength, moderate elastic modulus, good crack resistance performance, minor expansion and good durability[4]. Hence, PMH cement, other supplementary materials and admixtures are currently used to meet the requirements mentioned above. Fly ash is widely used as supplementary cementitious material in mass concrete for high arch dams in China.
The adiabatic temperature rise of mass concrete with PMH cement and fly ash for high arch dams is relatively high. Generally, in terms of mass concrete in the heel of high arch dams with strength grade of C18040, adiabatic temperature rise in the lab at 28d is higher than 26 ℃. For example, the results of Xiaowan high arch dam concrete is 26.05 ℃[3]. However, the real-time adiabatic temperature rise is usually higher than the lab result and hard to control. A triple-powder mixed by PMH cement(50%)- fly ash(30%)-slag(20%) was used to produce dam concrete by CHEN and his team, its adiabatic temperature rise is lower in the early stage, yet it grows higher after 20 d than conventional concrete mixed by PMH cement(70%)-fly ash(30%)[5]. Limestone powder of sound fineness can fill in the gap of cement paste and improve gradation then make paste tightly compacted[6]. In the recent years, it has been applied to RCC and self-compacting concrete as a new admixture. For example, dual mineral admixture of limestone powder and slag has been successfully used in Jinghong Roller Compacted Concrete (RCC) dam[7].
The multi-powder here under study consists of slag, fly ash, limestone powder and PMH cement. It aims to use limestone powder to improve the multi-powder particle size distribution and use particle effect of fly ash and low heat of hydration of slag to produce pluralistic synergy. And then the selected multi-powder can be used to produce HPC of low adiabatic temperature rise, better deformation capability and crack resistance performance.
2 Optimization of multi-powder
Slag and fly ash used finished products in this study directly. Optimization of multi-powder mainly includes the fineness (measured by specific surface area) and content of limestone powder, the content and proportion of slag and fly ash.
2.1 Raw materials
PMH cement of 42.5 MPa, fly ash of class-I, slag and limestone powder of different specific surface areas were used in this study. The specific surface area of cement is 342 m2/kg and the compressive strength at 28 d is 51.3 MPa. The specific surface area of class-I fly ash is 416 m2/kg, which has a fineness of 11.1% and water requirement ratio of 92% and ignition loss of 1.06%. The specific surface area of slag is 398 m2/kg. The particle size distribution and eigenvalue of cement and other powder materials are listed in Table 1.
As shown in Table 1, the average particle size, D50 and specific surface area of cement and fly ash are close, in which the average particle size is larger than 18 μm and D50 larger than 12μm. However, the average particle size and D50 of slag are smaller than those of the cement and fly ash, but the specific surface area is close to that of the fly ash. With increasing specific surface area, the average particle size and D50 of limestone powder decrease, and the content of large particles dramatically reduces. Under given specific surface area of 978 m2/kg, D50 of limestone powder is 2.18 μm, less than that of the cement, fly ash and slag, so the gap in the cement could be effectively filled and the cementitious materials grade be obviously improved.
2.2 Fineness optimization of limestone powder
Paste cone penetration test was used to optimize the fineness of limestone powder. According to GB/T134-2001, the paste was cast in Vicat needle tester and the cone sinking depth was recorded.
Four kinds of limestone powder with the specific surface area of 591,777, 978 and 1 133 m2/kg were used in the paste cone penetration test. In the multi-powder, the proportion of cement keeps 50% and the ratio of slag to fly ash keeps 6?4, but the content of limestone powder was changed to make various multi-powder. The water-binder ratio of multi-powder paste with addition of a certain kind of carboxylic acid superplasticizer is 0.23. The results are shown in Table 2 and Fig.1.
As shown in Table 2 and Fig. 1, the particle size distribution of multi-powder is improved effectively
Table 1 Particle size distribution and eigenvalue of powders
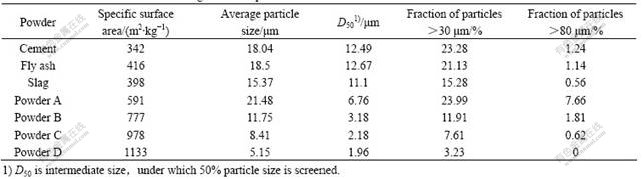
Table 2 Effects of content of limestone powder on paste cone penetration
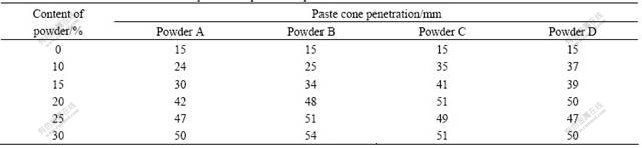
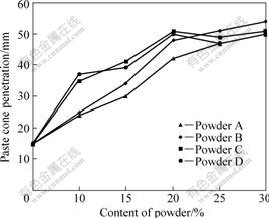
Fig.1 Effects of fineness and content of limestone powder on paste cone penetration
when the content of limestone powder is less than 20% and the paste cone penetration increases with the increasing of specific surface area of limestone powder; when the content of limestone powder is over 20%, the number of ultra-fine powder is surplus and the paste cone penetration no longer increases with specific surface area, which means that paste cone penetration of limestone powder with different fineness is basically close. So, the limestone with specific surface area of 1 000 m2/kg is chosen to continue the following tests, due to the fact that when the specific surface area is further increased, the fluidness is little improved and more energy is consumed.
2.3 Proportional optimization of multi-powder
Based on the selection of limestone powder with specific surface area of 1 000 m2/kg, paste cone penetration and strength are tested to optimize multi-powder proportion. Three factors including the ratio of slag to fly ash, the proportion of cement in cementitious materials and the content of limestone powder are identified in this L9(34) orthogonal test. The water-binder ratio of paste is 0.23 and 0.4% carboxylic acid superplasticizer is added. The results of paste cone penetration and strength are listed in Table 3, and the variance analysis is listed in Table 4 and Table 5.
As shown in Table 4, the paste cone penetration increases in step with limestone content which justifies limestone powder improving the fluidity of multi-powder paste and accords with results mentioned above. Ratio of slag to fly ash ranging between 7?3 and 5?5, has no effect on cone penetration and so does the proportion of cement ranging between 40% and 60%.
As shown in Table 5, the compressive strength at 7 d is obviously influenced by all three factors, especially cement proportion and limestone powder content. The early strength is contributed primarily by cement hydration and so increases with cement amount used in concrete. It is similar with limestone powder content which is closely related with improved cement hydration by grinding limestone powder. With aging, the influence of three factors is diminished, of which the ratio of slag to fly ash and content of limestone powder show no influence on the compressive strength at 28 d, and cement proportion has more obvious effect. It implies that the early compressive strength (28 d and earlier) is mainly contributed by the cement hydration.
Table 3 Cone penetration and strength of multi-powder paste
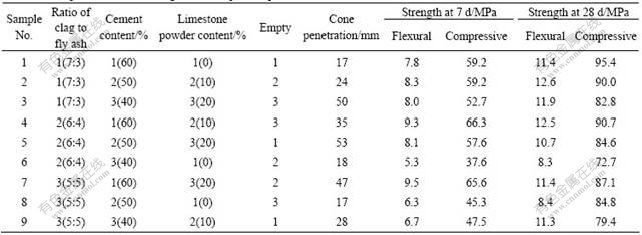
Table 4 Variance analysis of each factor on cone penetration

It can be seen from Table 5 that the ratio of slag to fly ash has no influence on the flexural strength at 7 d, but the influence grows obviously at 28d, which implies that the slag has partly hydrated between 7 d and 28 d and the slag is favorable to flexural strength develop- ment. The cement proportion and limestone powder content have positive effect on the concrete flexural strength at 7 d, yet, the effect diminishes dramatically at 28 d. Limestone is favorable to flexural strength development, and the strength is increased by 30% and 21%, respectively, when 10% and 20% limestone powders are added accordingly. Crack resistance can be improved by adding a proportionate limestone powder under premise of equal compressive strength.
2.4 Hydration heat and crack resistance of multi- powder
Hydration heat of multi-powder is tested according to GB/T12959-2008. Under the given tested consistency, multi-powder cementitious materials are mixed and cast. The results of hydration heat are shown in Table 6 and Fig.2.
The results in Table 6 and Fig.2 show that the hydration heat is decreased by about 12% when 30% fly ash or slag is added. The hydration heat is also decreased by adding 20% limestone powder. The hydration heat is decreased by only 5.6% when adding 30% multi-powder (the ratio of limestone powder, slag and fly ash is 5?3?2) and early activity of multi-powder is justified. The hydration heat is decreased with proportion increase of multi-powder in cementitious materials, when 70% multi-powder is added the hydration heat is decreased by 38.7%.
The crack resistance performance of multi-powder materials is tested by loop crack resistance method, in accordance with recommended cement and cement- based cementitious materials crack resistance test method in appendix a in “Guide to Durable Concrete Structure Design and construction(CECS01-2004)” edited by Division of Civil, Hydraulic and Architecture Engineering of China Engineering Academy[8]. Outer diameter and inner diameter of the loop specimen with height of 50 mm are 170 mm and 120 mm, respectively. With W/C of 0.23, the paste is cast and cured, then demoulded after 24 h and put under the condition of (20±2) ℃ and relative humidity of (60±5)%. Three samples are cast in one group and crack time is determined by the gap between the first crack appearance time and demoulding time, the average of which is the crack time of such group. When the difference between average and each single data is more than 4 h, it should be retested. The crack time of different multi-powders is listed in Table 6 and Fig.3.
Table 5 Variance analysis of each factor on strength
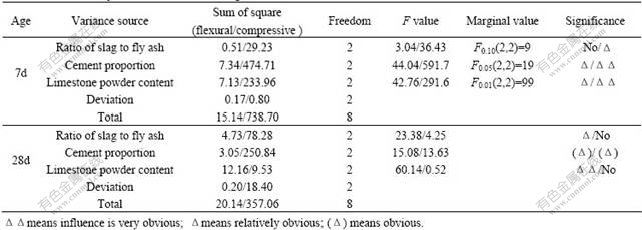
Table 6 Hydration heat and crack time of multi-powder paste
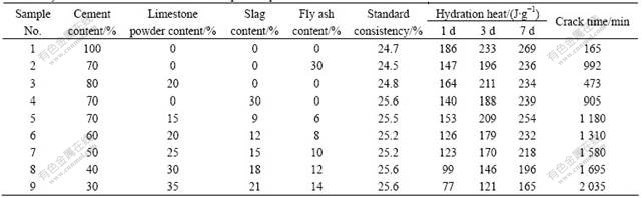
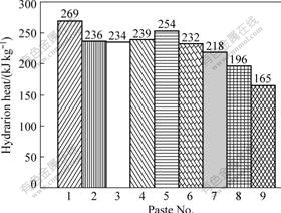
Fig.2 Hydration heat of different multi-powder pastes: 1—Cement; 2—Cement+30% fly ash; 3—Cement+20% limestone powder; 4—Cement+30% slag; 5—Cement+30% multi- powder; 6—Cement+40% multi-powder; 7—Cement+50% multi-powder; 8—Cement+60% multi-powder; 9—Cement+ 70% multi-powder
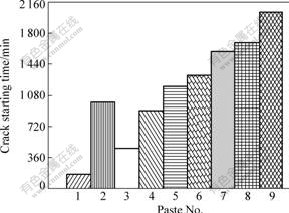
Fig.3 Crack starting time of different multi-powder pastes: 1—Cement; 2—Cement+30% fly ash; 3—Cement+20% limestone powder; 4—Cement+30% slag; 5—Cement+30% multi- powder; 6—Cement+40% multi-powder; 7—Cement+50% multi-powder; 8—Cement+60% multi-powder; 9—Cement+ 70% multi-powder
The results in Fig.3 show that when the slag, fly ash and limestone powder are added singly the crack time of fly ash paste is the longest, 16 h and 32 min, followed by slag paste and limestone powder paste. And the crack time of paste with some powder materials surpasses the cement paste. It can be deduced that the powder materials are favorable to the crack resistance performance of cementitious materials. Under 30% multi-powder content, the crack time of multi-powder paste is 19 h and 40 min, longer than fly ash paste, which demonstrates that the multi-powder consisting of slag, fly ash and limestone powder, has better crack resistance performance, and the crack time is delayed in line with multi-powder content.
3 Properties of multi-powder concrete
According to the result of the optimization of multi-powder, the specific surface area of limestone powder is 1 000 m2/kg, the ratio of the limestone powder to the slag and fly ash is 5?3?2. The paste mixed by multi-powder and cement is featured by deeper cone penetration, lower hydration heat and delayed cracking time. Dam concrete, made from PMH cement +50% multi-powder and PMH cement +35% fly ash, which is currently used in high arch dams, is tested in terms of mechanical, deformation and thermal properties. And the aggregate with maximum size of 150 mm is used in this paper.
3.1 Mixing proportion
Slump is controlled between 3 cm and 5 cm and the air content is between 4% and 6%. The mixing proportion of the concrete is listed in Table 7.
It can be seen from Table 7 that PMH cement +50% multi-powder concrete can reduce the unit water consumption under given mixing proportion and decrease the cement consumption despite the increment of the total amount of cementitious materials. This is caused by less water/cementitious material ratio. Compared with PMH cement +35% fly ash convention concrete, the unit cement consumption of PMH cement +50% multi-powder is approximately reduced by 17.1 kg in concrete of C18040.
Table 7 Mixing proportion of concrete
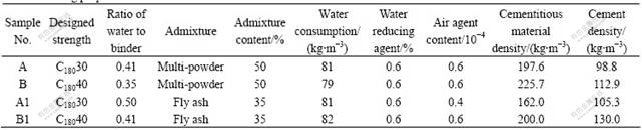
3.2 Mechanical properties
The compressive and splitting tensile strength, ultimate tensile strain and compressive elastic modulus of concrete at different ages are listed in Table 8.
It can be seen from Table 8, the compressive strength of multi-powder concrete at 28 d is higher than that of the concrete with conventional cementitious materials, and the increments of C18040 and C18030 are 2.5 MPa and 6.3 MPa, respectively, which is probably closely related with ultra-fine limestone powder improving hydration of cementitious materials at early stage. The splitting tensile strength at 28 d is relatively higher too, yet there is little difference in the tensile/compressive strength ratio. The tensile/compressive strength ratios of C18040 concrete are 0.079 and 0.077 with C18030 concretes of 0.081 and 0.084 at 28 d. The compressive strength of concrete with multi-powder at 180 d is higher than that of conventional concrete, with increments of C18040 and C18030 by 4.7 MPa and 11.7 MPa, respectively. With regard to higher increment at 180 d, it is due to more cementitious materials used and activity development of slag and fly ash at later stage. At 180 d, the tensile/compressive strength ratios of C18040 are 0.069 and 0.072, while those of C18030 are 0.080 and 0.084.
It also demonstrates that the ultimate tensile strain of C18030 at 28 d and 180 d are higher than 90×10-6 and 110×10-6, respectively, while that of C18040 at 28d and 180 d are higher than 100×10-6 and 120×10-6, respectively. Higher compressive elastic modulus of concrete with multi-powder is closely related with high compressive strength.
Overall, both multi-powder and conventional materials of PMH cement and fly ash are able to get high strength concrete, and a little more cementitious materials are used in multi-powder concrete yet less cement used.
3.3 Adiabatic temperature rise
Test results show that, at 28 d, the adiabatic temperature rise of conventional concrete C18040 is about 20.0 ℃ while that of the multi-powder concrete C18040 is about 18.0 ℃. The reduction is attributed to less cement and less active materials used. In the light of multi-powder concrete C18040, the cement amount is approximately 113 kg and active cementitious materials amount, including cement, fly ash and slag, is 168 kg. As for conventional concrete, cement amount is 130 kg and active materials amount including cement and fly ash is 200 kg. The test results show that lower adiabatic temperature rise can be obtained with multi-powder used in concrete. In comparison, because of less cement and other active materials used in multi-powder concrete, adiabatic temperature rise is lower, yet the fact that more heat is released from hydration of fly ash and slag after 28 d calls more attention to avoid thermal crack.
4 Discussion
Multi-powder is composed of slag, fly ash, limestone powder and PMH cement. Limestone powder can improves the gradation of multi-powder. Fly ash with particle effect and slag with low early hydration heat and strength development effect are favorable to synergy effect of cement and multi-powder. In this way, the concrete of high strength and low adiabatic temperature rise can be produced which can meet the requirements of high arch dams concrete. However, autogenous volume deformation of multi-powder concrete is greater than that of the conventional concrete made by PMH cement and fly ash.
Because of higher stress levels and lower capability of adjustment to concrete cracks, high arch dams require their dam concrete with higher crack resistance. A lot of numerical analysis on thermal stress of high arch dams shows that slower early hydration heat and lower adiabatic temperature rise benefit to the concrete temperature control for high arch dams but autogenous shrinkage is unfavorable. Multi-powder concrete has larger autogenous shrinkage that does not reduce with increasing concrete age. It is very unfavorable to concrete temperature control for high arch dams. Larger autogenous shrinkage of multi-powder concrete may be contribute to limestone powder accelerate cement early hydration, so that the shrinkage is produced ahead of schedule. While in the latter of hydration, multi-powder concrete has higher strength and elastic modulus and stronger constraint that leads to concrete has little expansion from the maximum shrinkage.
Table 8 Mechanical performances of concrete at different ages
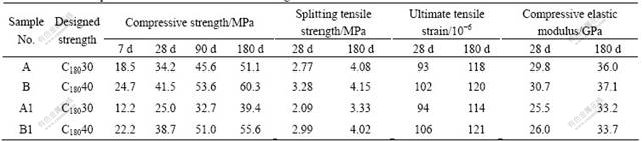
Whether multi-powder concrete has larger autogenous volume deformation is a result of limestone powder to accelerate the early hydration of cement? How to optimize the components of multi-powder so as to reduce the autogenous volume deformation of multi-powder concrete? These problems are worthy of further study to meet the requirements of high arch dams on concrete.
5 Conclusions
1) The fineness and content of limestone powder have obvious effect on fluidity of multi-powder paste. When the specific surface area of limestone powder is about 1 000 m2/kg and content ranges between 20% and 25%, the fluidity of multi-powder paste is relatively high.
2) Multi-powder paste has better toughness and crack resistance performance. Under premise of equal compressive strength, the flexural strength of multi-powder paste compared with conventional cement and fly ash paste is increased by approximately 20% and the circle cracking time is obviously delayed.
3) Featured by lower unit cement consumption and lower adiabatic temperature rise, multi-powder concrete is able to produce HPC for high arch dams. In comparison with conventional concrete produced by PMH cement and fly ash, unit water consumption is little reduced yet the cement is reduced by 6.5-17.1 kg. Adiabatic temperature rise at 28 d can be reduced by about 2 ℃ and less heat is released in the later period. And it is easier to control the temperature rise of mass concrete for high arch dams.
References
[1] WU Zhong-wei, LIAN Hui-zhen. High performance concrete [M]. Beijing: China Railway Publishing House, 1999. (in Chinese)
[2] LI Jia-jin. Raw materials and mix design of arch dam concrete for ertan hydrostation [J]. Guizhou Water Power, 2004, 18(2): 46-49. (in Chinese)
[3] XIE Min, XU Wen-tao. Research of concrete raw materials and temperature control in xiaowan arch dam [J]. Waterpower, 2006, 32(11): 48-50. (in Chinese)
[4] REN Zong-she, WANG Shi-kun, ZHANG Hua-chen. Optimization of concrete raw materials and its mix proportion of the arch dam for laxiwa hydropower station [J]. Waterpower, 2007, 33(11): 11-15. (in Chinese)
[5] CHEN Gai-xin, JI Guo-jin, LEI Ai-zhong, TIAN Jun-tao. Study on synergistic effects of multi-component cementitious material [J]. Journal of the Chinese Ceramic Society, 2004,32(3): 351-357. (in Chinese)
[6] LIU Shu-hua, YAN Pei-yu. Influence of limestone powder on filling effect of cement paste and pore structure of sand grout [J]. Journal of the Chinese Ceramic Society, 2008, 36(1): 69-72. (in Chinese)
[7] JI Guo-jin, Kong Xiang-zhi, Chen Gai-xi. Influence of fineness and curing temperature on the activity of bi-component admixture [J]. Waterpower, 2008, 34(4): 37-40. (in Chinese)
[8] CHEN Zao-yuan, ZHAO Guo-fan. Guide to durable concrete structure design and construction [M]. Beijing: China Architecture & Building Press, 2004. (in Chinese)
(Edited by LONG Huai-zhong)
Foundation item: Project(50879095) supported by the National Natural Science Foundation of China
Corresponding author: LI Xin-yu; Tel: +86-571-56738858(O), +86-015868816602(M); E-mail: li_xy@ecidi.com