
Influence of Mg21Ga5Hg3 compound on electrochemical properties of Mg-5%Hg-5%Ga alloy
FENG Yan(冯 艳), WANG Ri-chu(王日初), PENG Chao-qun(彭超群), WANG Nai-guang(王乃光)
School of Materials Science and Engineering, Central South University, Changsha 410083, China
Received 15 October 2008; accepted 10 December 2008
Abstract: The Mg-Hg-Ga alloys are widely used in high power the seawater batteries. Mg-5%Hg-5%Ga alloy was melted and heat treatments at 573-773 K were performed for different times. The electrochemical and corrosion behaviors of the Mg-5%Hg-5%Ga alloy were studied by means of potentiodynamic, galvanostatic and electrochemical impedance spectroscopy(EIS). Scanning electron microscopy(SEM), energy dispersive spectrometry(EDS) and X-ray diffractometry(XRD) were employed to characterize the microstructures of the alloy. The results demonstrate that the best electrochemical activity occurs in the Mg-5%Hg-5%Ga alloy with homogeneously dispersed Mg21Ga5Hg3 compound in α-Mg matrix. The most negative mean potential at 100 mA/cm2 polarization current density can reach -1.928 V. The largest corrosion current density 19.37 mA/cm2 of the Mg-5%Hg-5%Ga alloy appears in the Mg-5%Hg-5%Ga alloy with intergranular eutectic α-Mg and Mg21Ga5Hg3.
Key words: Mg-Hg-Ga alloys; Mg anodes; seawater battery; electrochemical activity; corrosion resistance
1 Introduction
The Mg anodes are widely used in the seawater batteries and cathodic protection(CP) technology due to their excellent properties, such as rapid activation, low density, low electrode potential and high current capacity [1-4]. The developed magnesium anode materials with high cell voltage are AP65 (Mg-6%Al- 5%Pb), Mg-7%Tl-5%Al[1] and Mg-Hg alloys. The specific energy of the seawater battery using Mg-Hg alloy as anode can reach 150 W·h/kg[5-6], compared with the 30 W·h/kg of lead acid battery. However, the good results of Mg anodes obtained in high power seawater battery still meet with problems such as bad deformability, large self-corrosion velocity and low current efficiency[7-8]. In order to solve these problems, the influences of alloying elements such as aluminium, zinc, lead and mercury on the magnesium anodes have been investigated in recent years[9-12]. But there is not any report about the influence of the second phases on the electrochemical and corrosion properties of the Mg anodes.
According to Refs.[13-14], Ga can activate Mg and Al anodes due to the dissolution-redeposition mechanism. Ga can also enhance the corrosion resistance of the dental amalgams[18]. But the influence of the compounds containing Ga on the electrochemical activation and corrosion resistance of the Mg and Al anodes was not reported. In this work, Ga was selected to substitute part of Hg in the Mg-Hg anodes and the morphology of the intermetallic compound Mg21Ga5Hg3 in the α-Mg matrix has been studied as a key factor in achieving good surface activation and corrosion resistance of the Mg-Hg-Ga anodes.
2 Experimental
The Mg-5%Hg-5%Ga alloy was prepared using metals with 99.99% purity in order to avoid contamination by other elements. The alloy was melted in a sealed iron tube filled with argon, as described in a previous work[19]. After heat treatment at 573-773 K for 1-200 h, the samples were removed from the iron tube. The chemical composition of the alloy (in Table 1) was determined by EDS and atomic absorption spectrum analysis.
Potentiodynamic and galvanostatic experiments were performed with a Potentiostat-Galvanostat (Model 263A) in a 3.5% (mass fraction) NaCl solution. The scanning rate of potentiodynamic test was 5 mV/s and the anodic current density in galvanostatic test was 100 mA/cm2. The EIS measurements were performed to study the kinetics of the electrode reactions using a Potentiostat-Galvanostat (Model 263A) and a 1255 Solartron Frequency Response Analyzer. The impedance measurements were made over a frequency range of 0.005-100 kHz (15 points per decade) with a 10 mV alternative current signal and interpreted in terms of equivalent circuit(EC) with frequency dependent components. The samples were polished with emery paper and buffed to a mirror finish. Each of them was sealed with epoxy resin except for an exposed surface of 10 mm×10 mm submitted to the electrochemical tests in a three-electrode cell. A platinum sheet was used as the auxiliary electrode and a saturated calomel electrode (SCE) was used as the reference electrode.
Table 1 Chemical composition of Mg-5%Hg-5%Ga alloy (mole fraction, %)

The microstructure of the corrosion morphology of each sample was determined by SEM. The phases of the samples were determined by EDS and XRD.
3 Results and discussion
3.1 Microstructure of Mg-5%Hg-5%Ga alloy
Fig.1 shows the SEM micrographs of Mg-5%Hg- 5%Ga alloy with different aging times. Combined with the EDS and XRD results (as seen in Figs.2 and 3), the samples aged for 1 h and 24 h show the presence of matrix which is α-Mg solid solution and eutectic at the grain boundary, characterized by “islands” of eutectic α-Mg within Mg21Ga5Hg3 compound. In the Mg-Hg-Ga ternary phase diagram, Mg21Ga5Hg3 is a new compound with Ge8Pd21 structure type (space group I41/a, a=14.539 1(5) ?, c=11.595 5(4) ?, Z=4), which was determined by XRD measurement and Rietveld method. When the aging time is prolonged from 1 h to 24 h, the grain becomes larger and the amount of eutectic obviously decreases. When the aging time is prolonged to 200 h, the intergranular eutectic disappears and the Mg21Ga5Hg3 particles with 2-30 μm size distribute homogeneously in the α-Mg matrix.
3.2 Influence of Mg21Ga5Hg3 compound on electro- chemical and corrosion behaviors of Mg-5%Hg- 5%Ga alloy
3.2.1 Potentiodynamic and galvanostatic measurements
To obtain information about the influence of Mg21Ga5Hg3 compound on the corrosion behavior of the Mg-5%Hg-5%Ga alloy, potentiodynamic polarization curves were tested on the Mg-5%Hg-5%Ga alloy in a 3.5% NaCl solution (Fig.4).
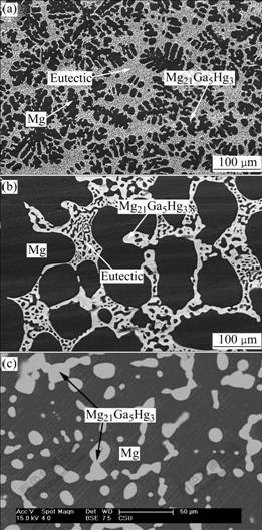
Fig.1 SEM images Mg-5%Hg-5%Ga alloy after aging for different times: (a) 1 h; (b) 24 h; (c) 200 h
As seen in Fig.4, during the potentiodynamic scanning, a steady state current is attained for each applied potential step. Starting from the rest potential, the anode polarization curves show a remarkable increase in the anodic current density. When the scanning potential is more positive than -1.95 V, the concentration polarization occurs more easily in the sample aged for 1 h because of the steeper anodic curves and the larger anodic Tafel rate of slope. The black corrosion products flake off continuously in the process of polarization, which is consistent with the electrochemical reaction of an amalgam with moisture[20-21].
The corrosion current densities and corrosion potentials of the Mg-5%Hg-5%Ga alloy were calculated by Tafel linear extrapolation and listed in Table 2. The corrosion current density of the alloy decreases from 19.37 mA/cm2 to 1.19 mA/cm2 when the aging time increases from 1 h to 200 h. The best corrosion resistance appears in the sample aged for 200 h.
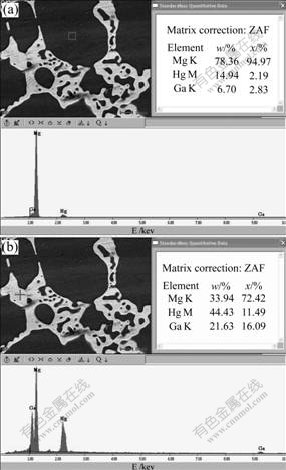
Fig.2 EDS results of Mg-5%Hg-5%Ga alloy after aging for 24 h: (a) α-Mg, (b) Mg21Ga5Hg3
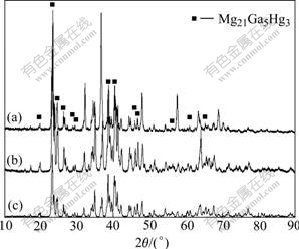
Fig.3 XRD spectra of Mg-5%Hg-5%Ga alloy after aging for different times: (a) 1 h; (b) 24 h; (c) 200 h
Table 2 Electrochemical corrosion parameters of Mg-5%Hg- 5%Ga alloy after aging for different times
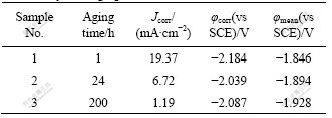
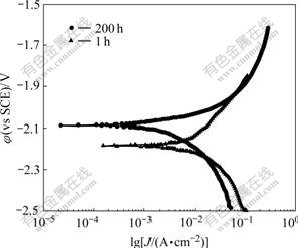
Fig.4 Potentiodynamical curves of Mg-5%Hg-5%Ga alloy after aging for 1 h and 200 h
The corrosion resistance of Mg-5%Hg-5%Ga alloy depends on the amount and distribution of the Mg21Ga5Hg3 compound. The samples aged for 1 h and 24 h have eutectic (α-Mg+Mg21Ga5Hg3) at the grain boundaries. Fig.5 shows the optical micrograph of the sample after aging for 24 h and exposure in air for 15 min. It can be seen that corrosion occurs in the intergranular eutectic. This is related to the different electronegativities of α-Mg and Mg21Ga5Hg3 in the intergranular eutectic. The intergranular corrosion has large ratio of cathodic area compared with anodic area, which increases the corrosion driving force. Moreover, the closest distance and largest contact area between the anodic and cathodic in the eutectic accelerate the corrosion rate. So the sample aged for 1 h has the largest corrosion current density and lowest corrosion resistance because of the largest amount of eutectic.
The sample aged for 200 h has dispersed Mg21Ga5Hg3 particles in the α-Mg matrix. Due to the homogeneity of electrochemical properties, the sample aged for 200 h preserves a general and homogeneous corrosion. Its corrosion resistance is better than that of the samples with intergranular eutectic.
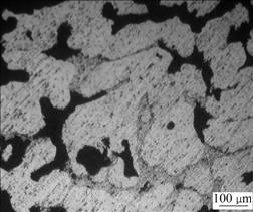
Fig.5 Corroded surface of Mg-5%Hg-1%Ga alloy after aging for 24 h and exposure in air for 15 min
Fig.6 shows the galvanostatic curves of Mg-5%Hg- 5%Ga alloy after aging for different times. The anodic current density is 100 mA/cm2. The specimen aged for 1 h shows obvious polarization behavior with the test time prolonging. When the aging time increases from 1 h to 200 h, the mean potentials of the samples move negatively. Table 2 shows the mean potentials of the samples measured from the galvanostatic curves. The sample aged for 200 h has the most negative mean potential of -1.928 V, which leads to the least anodic polarization and the best electrochemical activity. The sample aged for 1 h shows the most positive mean potential of -1.846 V and the worst electrochemical activity.
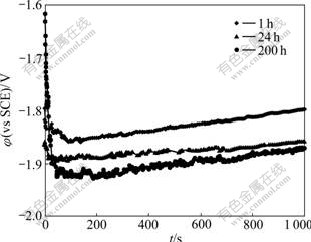
Fig.6 Galvanostatic curves of Mg-5%Hg-5%Ga alloy after aging for different times
The electrochemical activities of the samples are also relevant to the amount and distribution of the Mg21Ga5Hg3 compounds. The activation reaction of the surface begins from the interfacial zone between α-Mg and Mg21Ga5Hg3. The corrosion of the interfacial zone leads to the dissolution of the anodes, which agrees with the previous work[21-22]. The sample with dispersed Mg21Ga5Hg3 particles in the α-Mg matrix leads to homogeneous generalized dissolution of matrix, which enlarges the area of the activation reaction and enhances the electrochemical activity. While the activation reactions of the samples with intergranular eutectic only focus on the grain boundaries. Moreover, the larger corrosion current densities of the intergranular corrosion in these samples increase the activation polarization and decrease the electrochemical activity.
3.2.2 EIS measurement
The electrochemical impedance spectra for Mg- 5%Hg-5%Ga alloy at φcorr in a 3.5% NaCl solution are shown in Fig.7. Nyquist plots were characterized by two capacitive loops at high and medium frequencies and one Warburg diffusion line at low frequency.
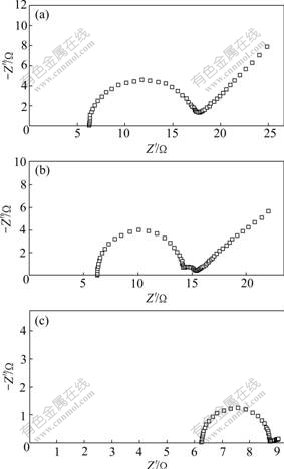
Fig.7 Electrochemical impedance spectra of Mg-5%Hg-5%Ga alloys after aging for different times at φcorr in 3.5% NaCl solution: (a) 1 h; (b) 24 h; (c) 200 h
On the basis of the reaction models of the Mg-Hg-Ga alloys discussed by FENG et al[17] and the EIS results in Fig.7, the EC could be attained (Fig.8). R0 is the electrolyte resistance, Cox is the capacitance of the corrosion products film and Rox is film resistance (Mg(OH)2 film resistance), Rp is the resistance of the electrolytic solution within the pit, Cdlt and Rct refer to the capacitances of the double layer and the charge transfer resistance in the faradaic reaction, and W is the value of the Warburg impedance. A method of parameter adjustment based on the equivalent circuit in Fig.8 was applied and the results are listed in Table 3.
The comparison of the values of the Mg-5%Hg- 5%Ga alloy after aging for different times in Table 3 shows a considerable decrease of Cdlt, Rct and W values with the aging time prolonging. Lower Cdlt and Rct values lead to lower charge transfer resistance in the faradaic reaction. Lower W value leads to smaller concentration polarization. Based on the above results, the sample after aging for 200 h has the best electrochemical activity, which is consistent with the galvanostatic results. It can be ascribed to the dispersed Mg21Ga5Hg3 particles in the α-Mg matrix. The largest Rct and Cdlt values in the sample after aging for 1 h lead to the largest faradaic impedance. Moreover, the largest W value of this sample leads to the largest concentration polarization. Based on the above results, the sample after aging for 1 h has the worst electrochemical activity, which depends on the intergranular eutectic of the α-Mg and Mg21Ga5Hg3.
Table 3 Electrochemical parameters obtained by fitting analysis of Nyquist diagrams of Mg-5%Hg-5%Ga alloy


Fig.8 Equivalent circuits of Mg-5%Hg-5%Ga alloy/3.5% NaCl solution interfaces
The largest Rp occurs in the sample aged for 200 h, which impedes the self-corrosion and leads to the least corrosion current density. The largest corrosion current density and the worst corrosion resistance occurs in the sample aged for 1 h, confirmed by the smallest Rp and potentiodynamic test results. The sample aged for 1 h has the highest corrosion film capacitive loop Cox and film resistance Rox, which suggests the largest coverage ratio of the corrosion products film and the least exposure ratio of α-Mg matrix. The corrosion products impede the mass diffusion rate of the electrode reaction. The impeded diffusion rate of mass further leads to the largest W value. So the concentration polarization of the sample with intergranular eutectic increases and the electrochemical activity decreases.
4 Conclusions
1) A sufficient annealing time during heat treatment has a positive influence on the microstructure of the Mg-5%Hg-5%Ga alloy. When the aging time increases from 1 h to 200 h, the intergranular eutectic (α-Mg+ Mg21Ga5Hg3) disappears and the Mg21Ga5Hg3 particles disperse homogeneously in the α-Mg matrix.
2) The amount and distribution of the Mg21Ga5Hg3 compound are relevant to the electrochemical activity and corrosion resistance of the Mg-5%Hg-5%Ga alloy. Homogenous dispersion of the Mg21Ga5Hg3 particles in the α-Mg matrix produces the least charge transfer resistance in the faradaic reaction and the least coverage ratio of the corrosion products film, which leads to the best electrochemical activity. Its mean potential at 100 mA/cm2 polarization current density is -1.928 V, the most negative potential in the Mg-5%Hg- 5%Ga alloy.
3) The intergranular eutectic of α-Mg and Mg21Ga5Hg3 in the Mg-5%Hg-5%Ga alloy produce the largest corrosion current density of 19.37 mA/cm2, which leads to the largest coverage of corrosion products in the electrode surface and the least exposure ratio of the α-Mg. The largest concentration polarization due to the thick corrosion film and the largest charge transfer resistance in the faradaic reaction produce the worst electrochemical activity of the Mg-5%Hg-5%Ga alloy.
References
[1] DORON A, GURUKAR S S, ELENA L, ARIEL M, OREN M, ORIT C, MICHELA B. Progress in rechargeable magnesium battery technology [J]. Advanced Materials, 2007, 19: 4260-4267.
[2] RENUKA R. Influence of allotropic modifications of surphur on the cell voltage in Mg-CuI(S) seawater activated battery [J]. Materials Chemistry Physics, 1999, 59(1): 42-48.
[3] JEROME G, DANIEL C, KATIA G, MARC D, AXEL H, FRANCIS M, ANDRE H. Magnesium batteries: Towards a first use of graphite fluorides [J]. Journal of Power Sources, 2007, 173: 592-598.
[4] RENUKA R. AgCl and Ag2S as additives to CuI in Mg-CuI seawater activated batteries [J]. Journal of Applied Electrochemistry, 1997, 27(12): 1394-1397.
[5] BAGSHAW N E, WARRELL S. Anodic dissolution of magnesium alloys related to lead chloride-mganesium seawater batteries [C]// THOMPSON J. Power Sources: Research and Development in Non-Mechanical Electrical Power Sources. London: E-Publishing Inc., 1981:117-139.
[6] FIRA S S, KIBL L, LIW L W. Water-activated disposable and long shelf-life microbatteries [J]. Sensors and Actuators A-Physical, 2004, 111(1): 79-86.
[7] VENKATESARA R K. Performance evaluation of Mg-AgCl batteries for under water propulsion [J]. Denfence Science Journal, 2001, 5(2): 161-170.
[8] GUANG L S, ANDREJ A. Corrosion mechanisms of magnesium alloys [J]. Advanced Engineering Materials, 1999, 1(1): 11-33.
[9] XI Bei-hua, XIA Tian. Survey of power battery for torpedo propulsion [J]. Torpedo Technology, 2005, 13(2): 7-12.
[10] FONT S, DESCROIX J P, SARRE G. Advanced reserve batteries for torpedoes proplsion [C]// CHERRY H. Proceedings of the 31st Power Sources Symposium. Penniton: Electrochemical Soc, 1984: 362-368.
[11] KIM J G, JOO J H, KOO S J. Development of high-driving potential and high-dfficiency Mg-based sacrificial anodes for cathodic protection [J]. Journal of Materials Science Letters, 2000, 19(6): 477-479.
[12] MA Zhen-qing, LI Wen-xian, YU Kun. Electrochemical characteristics of magnesium alloys in synthetic seawater [J]. Materials Protection, 2002, 35(12): 16-18.
[13] FLAMINI D O, SAIDMAN S B, BESSONE J B. Aluminium activation produced by gallium [J]. Corrosion Science, 2006, 48(6): 1413-1425.
[14] DENG Shu-hao, YI Dan-qing, ZHAO Li-hong, ZHOU Ling-ling, WANG Bin, JI Cheng-nian, LAN Bo. Study on Mg alloy anode material for seawater battery [J]. Battery Technology, 2007, 131(5): 402-405.
[15] SHAYEB H A E, WAHAB F A E, ABEDIN S Z E. Effect of gallium ions on the electrochemical behaviour of Al, Al-Sn, Al-Zn and Al-Zn-Sn alloys in chloride solutions [J]. Corrosion Science, 2001, 43: 643-645.
[16] MARIA N, DEREK P, ROBERT J K W, SHUNCAI W, RICHARD L J, KEIT R S, IAN W. The study of aluminium anodes for high power density Al/air batteries with brine electrolytes [J]. Journal of Power Sources, 2008, 178: 445-455.
[17] FENG Yan, WANG Ri-chu, YU Kun, PENG Chao-qun, LI Wen-xian. Influence of Ga content on electrochemical behavior of Mg-5at%Hg anode materials [J]. Materials Transaction, 2008, 49(5): 1077-1080.
[18] PINSSCO M R, ANGELINI E, CORDANO E, PRSALBINO F. Structural characterisation and corrosion resistance of Ga-precious metal alloys formed by liquid-solid reaction at room temperature [J]. Journal of Alloys and Compounds, 2001, 317/318: 411-418.
[19] FENG Yan, WANG Ri-chu, YU Kun, LI Wen-xian. Influence of heat treatment on electrochemical behavior of the Mg anode materials [J]. Journal of Central South University of Technology, 2007, 14(2): 12-15.
[20] BESSONE J B. The activation of aluminium by mercury ions in non-aggressive media [J]. Corrosion Science, 2006, 48: 4243-4256.
[21] KHEDR M G A, LASHIEN A M S. The role of metal cations in the corrosion and corrosion inhibition of aluminium in aqueous solutions [J]. Corrosion Science, 1992, 33(1): 137-151.
[22] CABOT P L, GARRIDO G A, PEREZ E, MOREIRA A H, SUMODIO P T A, PROUD W. EIS study of heat-treated Al-Zn-Mg alloys in the passive and transpassive potential regions [J]. Electrochimca Acta, 1995, 40(4): 447-454.
Corresponding author: PENG Chao-qun; Tel: +86-731-8877197; Fax: +86-731-8877197; E-mail: pcq2005@163.com
DOI: 10.1016/S1003-6326(08)60244-7
(Edited by YUAN Sai-qian)