
Preparation and properties of borate glass coatings on Ti-based alloy substrates
ZHU Dong-mei(朱冬梅), LOU Xia(娄 霞), LUO Fa(罗 发),
XIONG Liang-ming(熊良明), ZHOU Wan-cheng(周万城)
State Key Laboratory of Solidification Processing, Northwestern Polytechnical University, Xi’an 710072, China
Received 15 July 2007; accepted 10 September 2007
Abstract: A series of BaO-La2O3-B2O3 (BLB) glass coats on the Ti-based alloy substrates were developed at different temperatures for different times. The BLB glasses were analyzed by differential thermal analysis (DTA) and thermal mechanical analysis (TMA) to determine the crystallization temperature and coefficients of thermal expansion (CETs) of the glass. The tensile strength and microstructure of the glass coats were analyzed and the effects of the coating condition on the tensile strength and microstructure were discussed. The results show that the CETs of the borate glass at different temperatures match with those of Ti-based alloy, and the difference between the borate glass and Ti-based alloy at each temperature is below 5%. The spreading area in N2 atmosphere is much larger than that in air atmosphere, indicating that N2 atmosphere is helpful for the wetting of borate glass to Ti-based alloy. The tensile strength of the glass coats can reach as high as 28.42 MPa, meeting the requirements for the coat binder. With the increase of coating time, the tensile strength of coats increases firstly while then decreases. The coat prepared at 730 ℃ for 30 min is fairly smooth and complete, while the other coats contain lots of defects such as large or small uncoated region. It is believed that the coating temperature of 730 ℃ and coating time of 30 min are the proper coating conditions to prepare BLB glass coats.
Key words: BaO-La2O3-B2O3 glass; coating condition; Ti-based alloy; tensile strength
1 Introduction
Glasses have been most widely used to make metal-ceramic seals because they can be modified to have a very close match of thermal expansion with metal materials. Except that, the glass seals show good hermeticity along with good thermal and environmental stability[1-5]. Owing to the inherent brittleness of the glass seal, however, the cracks will appear in the seal during thermal cycling or shock, leading to the degradation of the glass-metal joints. Fortunately, there are already some ways found to minimize this problem.
Borate glasses have the promising application for the metal-ceramic seals for their lowing melting temperature and high thermal expansion coefficient matching with those of metals[6-8]. In such applications, it is found that the glass does not bond directly to the metal, but to an oxide that is conventionally formed by a thermal treatment on the metal prior to bonding. The resulting oxide acts as a bonding agent in that it is bonded to the underlying metal and the glass material[9-10].
For the same sealing purpose, the glasses in BaO-La2O3-B2O3 system (BLB glass), which possess the obvious advantages such as good high-temperature performance and good water durability, were explored for many years[11-12]. In this study, the characteristics of the BLB glass were determined and the BLB coats were prepared under different coating conditions. The effects of coating conditions on the mechanical properties of the coats were investigated.
2 Experimental
2.1 Preparation of coating
The BLB glasses were prepared through melting- quenching method according to the batch formula listed in Table 1. The obtained glasses were crushed into powder and put into the mould in furnace to prepare the coat on Ti-based alloy plate. After coating, turn off the power and leave the coated plates in the furnace to cool down. All the coats were annealed at 560 ℃ for 10 h.
Table 1 Composition and appearance of BLB glass

2.2 Properties measurements
The characteristic temperatures of the as-obtained glass were determined by differential thermal analysis (DTA) at a heating rate of 10 ℃/min. The coefficient of thermal expand (CTE) of the glass at different temperatures were determined by thermal mechanical analysis (TMA).
The tensile strength of the coats was determined through the tensile experiment conducted using a 0.1 MN electrical pulling machine at speed of 1mm/min. The tensile strength was calculated from the measured load F measured for the tensile fracture using the equation as

where σb is the tensile strength of coat, F is the maximum load when the coat is broken, and S is the fracture surface area.
The microstructures of the fracture for different coats were observed by scanning electron microscopy (SEM).
3 Results
3.1 Properties of BaO-La2O3-B2O3 glasses
Differential thermal analysis (DTA) was conducted to determine several characteristic temperatures of the borate glass in BaO-La2O3-B2O3 system. Fig.1 shows the DTA curve and the characteristic temperature determined from the DTA curve of the borate glass at heating rate of 10 ℃/min. The glass transition temperature (tg), the onset temperature of crystallization, and the peak temperature of crystallization are 556, 794 and 839 ℃, respectively.
The CTE (coefficient of thermal expansion) of the borated glass were measured by TMA and listed in Table 2 together with those of Ti-based alloy at the corresponding temperature. The CTE of the borate glass at 100 ℃ is about 8.00×10-6 ℃-1. With the increase of temperature, the CTE of the glass increases slowly and reaches 9.8×10-6 ℃-1 when the temperature is around 600 ℃.
Also, it is found that the difference between borate glass and Ti-based alloy at each temperature is below 5%, indicating that the CTEs of the borate glass match with those of Ti-based alloy at the corresponding temperature.
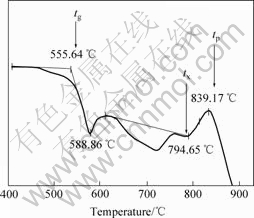
Fig.1 DTA curve and characteristic temperature determined for borate glass at heating rate of 10 ℃/min
Table 2 CETs of borate glass and Ti-based alloy at different temperatures (10-6 ℃-1)

The wet abilities of the borate glass to the Ti-based alloy substrate in different atmospheres including air and N2 were studied by comparing the spreading areas of the glass on the substrate at high temperature measured through wetting experiment. Fig.2 shows the spreading areas of the borate glass to the Ti-based alloy in air atmosphere and N2 atmosphere, respectively. The spreading area in N2 atmosphere is much larger than that in air atmosphere, indicating that N2 atmosphere is helpful for the wetting of borate glass to Ti-based alloy.
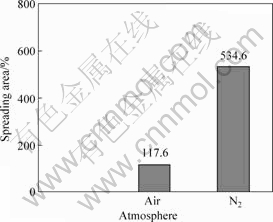
Fig.2 Spreading area of borate glass on Ti-based alloy at 730 ℃ in air and N2 atmosphere
3.2 BaO-La2O3-B2O3 coats on Ti-based alloy substrate
Three temperatures (680 ℃, 730 ℃, and 780 ℃) were selected in this study for the coating according to the thermal analysis results. For one certain coating temperature, the coating times of different coats are 15, 30 and 45 min, respectively. Table 2 lists the tensile strength of different coats at different temperatures for different times. It is clear that the tensile strengths of all the coats are much higher that the value of the requirement for the tensile strength of the coat, 10 MPa. It is shown that the tensile strengths of the coats prepared at 680 ℃ and 780 ℃ are much lower than those coated at 730 ℃, which are above 20 MPa no matter the coating time is long or not. We know that the viscosity of soften glass at low coating temperature is high, resulting in the low surface tension and large wetting angle of glass to Ti-based alloy substrate. Therefore the wettability of the glass to substrate, and the bonding of the glass and substrate are weak. With the increase of coating temperature, the fluidity of the soften glass is improved and the wetting angle become small, leading to the improvement of the wettability of glass to substrate and strengthening of the bonding between glass and substrate.
The tensile strength of the glass coat prepared at 780 ℃ is much lower than that at 730 ℃, the reason may
be that the 780 ℃ is too close to the onset temperature of crystallization, resulting in that the coats partly crystallized and then the tensile strength of glass coat is lowered.
It can be found from Table 3 that the tensile strengths of the coats for 30 min are much higher than those for 15 min or 45 min no matter the coating temperature is high or not. The coat prepared at 730 ℃ for 30 min possesses the highest tensile strength, indicating that the coating temperature of 730 ℃ and coating time of 30 min are the proper conditions to prepare the BLB coats on the Ti-based alloy substrate.
Table 3 Tensile strengths of different coats prepared under different conditions

Fig.3 shows the micrographs of the fracture of coats from different coating temperature for different time. It is clear that the coat prepared at 730 ℃ for 30 min is fairly smooth and complete, while the other coats contain lots of defects such as large or small uncoated regions. It is also evident that the the coating temperature of 730 ℃ and coating time of 30 min are the proper coating conditions for the BLB glass.
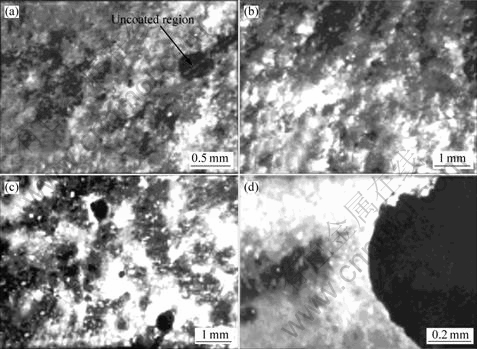
Fig.3 Micrographs of coats prepared at different temperatures for different time: (a) 680 ℃ for 30 min; (b) 730 ℃ for 30 min; (c) 780 ℃ for 30 min; (d) 730 ℃ for 45 min
4 Conclusions
1) The CETs of the borate glass at different temperatures match with those of Ti-based alloy very well. The spreading area in N2 atmosphere is much larger than that in air atmosphere, indicating that N2 atmosphere is helpful for the wetting of borate glass to Ti-based alloy.
2) The tensile strength of the glass coats can reach as high as 28.42 MPa, meeting the requirements for the coat binder.
3) With the increase of the coating time, the tensile strengths of coats increase firstly, then decrease.
4) The coat prepared at 730 ℃ for 30 min is fairly smooth and complete, while the coats prepared under other condition contain lots of defects. The coating temperature of 730 ℃ and coating time of 30 min are believed to be the proper coating conditions for the preparation of BLB glass coats.
References
[1] SOHN S B, CHOI S Y, KIM G H, SONG H S, KIM G D. Stable sealing glass for planar solid oxide fuel cell[J]. J Non-Cryst Solids, 2002, 297: 103-112.
[2] ZHABREV V A, EFIMENKO L P, KAYALOVA S S. Mechanism of the formation of coatings on metallic substrates from separated glass-metal composites[J].Glass Physics and Chemistry, 2005, 31(2): 229-235.
[3] SINGH R N. High temperature seals for solid oxide fuel cells[C]// Proceedings of 29th International Conference on Advanced Ceramics and Composites, 2004, 25(3), 299-307.
[4] GOMEZ-VEGA J M, SAIZ E, TOMSIA A P. Glass-based coatings for, titanium implant alloys[J]. J Biomed Mater Res, 1999, 46: 549-59.
[5] PAZO A, SAIZ E, TOMSIA A P. Silicate glass coatings on Ti-based implants[J]. Acta Mater, 1998, 46: 2551-8.
[6] BOBKOV N M, KHOT'KO S A. Low-melting glasses based on borate systems[J]. Lass and Ceramics, 2004, 61 (5/6): 175-177.
[7] KHANNA A, SAWHNEY K J S, TIWARI M K. Effects of melt ageing on the density, elastic modulus and glass transition temperature of bismuth borate glasses[J]. Journal of Physics—Condensed Matter, 2003, 15(40): 6659-6670.
[8] HOVHANNISYAN R M. Rafaelites-new kinds of glass ceramics with low thermal expansion and low melting temperatures on the basis of alkaline earth aluminium borates[J]. Glass Technology, 2003, 44(2): 96-100.
[9] YANG Z, XIA G, KERRY D, MEINHARDT K, STEVENSON J W. Chemical stability of glass seal interface in intermediate temperature solid oxide fuel cell[J]. J Mat Eng Perform, 2004, 13: 327-334.
[10] MANTEL M. Effect of double oxide layer on metal±glass sealing[J]. J Non-Cryst Solids, 2000, 273: 294-301.
[11] BROW R K, SAHA S K, GOLDSTEIN J I. Interfacial reactions between titanium and borate glass[C]//Materials Research Society Symposium Proceedings, 1993, 314: 77-81.
[12] ZHU D, LUO F, XIONG L. Preparation and properties of glass coats containing SiCN nano powder as filler[J]. Mater Sci Eng A, 2006, 431(1/2): 311-314.
(Edited by LONG Huai-zhong)
Foundation item: Project(50572090) supported by the National Natural Science Foundation of China
Corresponding author: ZHU Dong-mei; Tel: +86-29-88494574; E-mail: dzhunwpu@nwpu.edu.cn