
Fabrication and thermo-physical properties of TiB2p/Cu composites for electronic packaging applications
CHEN Guo-qin(陈国钦)1, XIU Zi-yang(修子扬)2, MENG Song-he(孟松鹤)3,
WU Gao-hui(武高辉)1, ZHU De-zhi(朱德志)1
1. School of Materials Science and Engineering, Harbin Institute of Technology, Harbin 150001, China;
2. Academy of Fundamental and Interdisciplinary Sciences, Harbin Institute of Technology,
Harbin 150001, China;
3. Center for Composite Materials, Harbin Institute of Technology, Harbin 150001, China
Received 10 June 2009; accepted 15 August 2009
Abstract: TiB2p/Cu composites with high reinforcement content (φp=50%, 58% and 65%) for electronic packaging applications were fabricated by squeeze casting technology. The microstructures and thermo-physical properties of the TiB2p/Cu composites were investigated. The results show that TiB2 particles are homogeneous and distribute uniformly, and the TiB2-Cu interfaces are clean and free-from interfacial reaction products and amorphous layers, the densifications of the TiB2p/Cu composites are higher than 98.2%. The mean linear coefficients of thermal expansion at 20-100 ℃ for TiB2p/Cu composites range from 8.3×10-6 to 10.8×10-6/K and decrease with increasing volume fraction of TiB2. The experimental coefficients of thermal expansion agree well with the predicted values based on Turner’s model. The thermal conductivities of TiB2p/Cu composites range from 167.3 to 215.4 W/(m?K), decreasing with increasing volume fraction TiB2.
Key words: TiB2p/Cu composites; densification; coefficient of thermal expansion; thermal conductivity
1 Introduction
The development of packaging technology has resulted in need for new materials with superior properties[1]. Firstly, packaging materials should have coefficient of thermal expansion(CTE) matching the ceramic substrates such as alumina, beryllia or aluminum nitride or semiconductors such as silicon or gallium arsenide to avoid thermally induced stresses that often cause eventual device failure. Additionally, since the reliability of semiconductors drops dramatically as temperature rises, higher thermal conductivity is demanded to remove excess heat and keep operating temperature low. Further, large mechanical properties and low density are desirable in applications that require maximal performance at low mass[2-3].
Particulate reinforced copper matrix composite combines the benefits of compatible and tailorable CTE, high thermal conductivity, lightmass, enhanced specific strength and stiffness[4-5]. So, it has been identified as an ideal candidate material for power module baseplates, printed wiring board cores, microprocessor lids and heat spreaders. Titanium diboride (TiB2) is well known for its high thermal and electrical conductivities, good chemical stability and good thermal shock stability[6-7]. Thus, the addition of TiB2 to copper matrix greatly decreases its coefficient of thermal expansion, while reducing the electrical and thermal conductivities much less than the addition of most other ceramic reinforcements[8-9]. Therefore, TiB2 reinforced metal matrix composites have received a great attention recently. The previous researches about the TiB2p/Cu composites were mostly focused on the thermal shock resistance properties and fabrication methods[10-12].
In the present study, high particle content TiB2p/Cu composites with particle volume fraction of 50%, 58% and 65% were fabricated by the patent squeeze casting technology, the densification of which was higher than 98.2%, with their microstructures, thermo-physical properties were tested and analyzed.
2 Experimental
The reinforcements used in this work were titanium diboride, TiB2, particles with nominal diameters of 2-3 μm, and the reinforcements volume fraction were 50%- 65%. The copper matrix was commercially available pure copper (w(Cu)≥99.7%). This pure copper was chosen for the purpose of high thermal conductivity and low cost. Table1 lists the typical parameters of TiB2.
Table 1 Typical parameters of TiB2 particle reinforcements
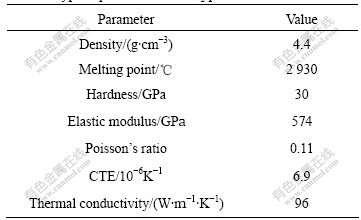
The TiB2p/Cu composites were fabricated by squeeze casting technology. The TiB2 preform was first fabricated and preheated. At the same time, copper alloy was melted, after which the molten copper was infiltrated into TiB2 preform under the pressure and held for some time. And then, TiB2p/Cu composite was solidified. A flow chart of the above process is shown in Fig.1. The composites were annealed in vacuum at 700 ℃ for 1.5 h and furnace cooled in order to release residual stress within the composites.
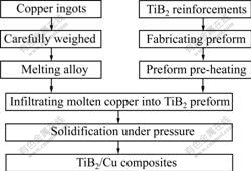
Fig.1 Flow chart of squeeze casting technology used for fabricating TiB2p/Cu composites
An S-570 scanning electron microscope(SEM) was used to examine the microstructure of as-fabricated TiB2p/Cu composites. The measured density was obtained using the Archimedes method and compared with the theoretical density to obtain various degree of densification. The CTE was measured on a DIL 402C (NETZSCH Corp.) with a heating rate of 5 ℃/min. The thermal conductivity was measured by the laser flash method with the NETZSCH LFA427 thermal constant measuring equipment. The testing sample was cylindrical, 12.7 mm in diameter and 3 mm in thickness.
3 Results and discussion
3.1 Densification
The effect of TiB2 volume fraction on the densification for TiB2p/Cu composites is shown in Fig.2. The densification of the TiB2p/Cu composites decreases with increasing TiB2p volume fraction under the same processing conditions. The densification of three composites is in the range of 98.2%-99.3%, which can completely meet the high dense requests for the electronic package materials.
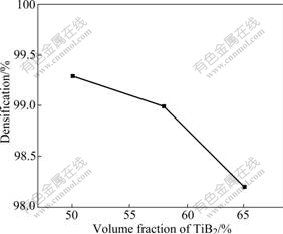
Fig.2 Dependence of TiB2 volume fraction on densification for TiB2p/Cu composites
3.2 Microstructure observation
Fig.3 reveals the microstructure of as-cast TiB2p/Cu composites. The TiB2 particles are observed to be homogeneously distributed in the copper matrix. And the composites are free from common cast defects such as porosity and shrinking cavities because pressure was applied during the solidification of TiB2p/Cu composite.
The interface and the existing of interface effect are the important factors which can affect the properties of the composite. Fig.4 illustrates the typical TEM micrographs of the interfaces in TiB2p/Cu composites. A large a mount of observations indicate that the TiB2-Cu interfaces are clean, smooth and free from interfacial reaction products and amorphous layers, and no TiB2 particles dissolved are observed.
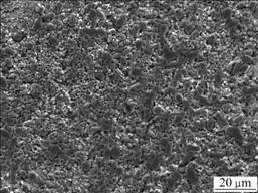
Fig.3 Microstructure of TiB2p/Cu composite
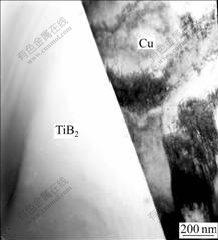
Fig.4 TEM micrographs of TiB2-Cu interfaces
3.3 Thermal expansion analysis
The measured CTEs of TiB2p/Cu composites are 8.9×10-6, 9.5×10-6 and 10.4×10-6 K-1 for the composites with volume fraction of TiB2 of 65%, 58% and 50%, respectively. The CTEs reduce with increasing volume fraction of TiB2. In a TiB2p/Cu composite, the thermal expansion behavior is influenced by the thermal expansion of copper matrix and the tightened restriction of TiB2 particles. Several theoretical models were proposed to predict the CTE of particulate composite [13-14]. If the matrix modulus is much smaller than that of reinforcement, the CTE of a composite is expressed as rule-of-mixture(Rom):
αc=αmφm+αpφp (1)
where α is the CTE, φ is the volume fraction; and subscripts c, m, p refer to the composite, matrix and particle, respectively.
Turner’s model considers the uniform hydrostatic stresses and gives the CTE of a composite as
(2)
where K is the bulk modulus.
Both the normal and shear stress are taken into account in Kerner’s model, and the CTE of a composite is expressed as

(3)
where G is shear modulus.
Fig.5 shows the comparison between the above theoretical predictions and experimental data. It can be seen that the experimental data are in good agreement with the predicted values based on Turner’s model, but deviate from ROM and Kerner’s model. This may be attributed to the fact that the uniform hydrostatic stresses are included in Turner’s.
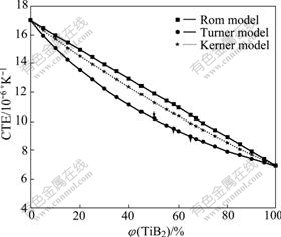
Fig.5 Comparison between theoretical predictions and experimental CTEs
3.4 Thermal conductivity
The measured thermal conductivities of TiB2p/Cu composites are 215.4, 180.5 and 167.3 W/(m·K) for the 50%, 58% and 65% composites, respectively, which are enough to satisfy the high thermal conductivity requests for electronic package materials. The thermal conductivities of TiB2p/Cu composites increased with increasing volume fraction of Cu. It is attributed to the thermal conductivity of TiB2 which is lower so far than that of copper.
Although the thermal conductivity of PMMCs is mainly decided by the thermal conductivity and content of constituent components, it connects with the densification of materials, interface condition, the figures and distribution of particles[15-17]. There are two ways for heat transfer in TiB2p/Cu composites: free electron in Cu matrix and phonon in TiB2 particles. Both the movement would be scattered by interface. Therefore, heat conduction in TiB2p/Cu composite depends on the Cu matrix, TiB2 particles and their interface. Fortunately, the interface between Cu and TiB2 particles are smooth without any reactant (see Fig.4), which is beneficial to heat transfer.
Accurate prediction of the composite properties is one important goal for researchers on materials, and two widely used models for prediction of PMMCs thermal conductivity are as the following[18-19]:
1) For Rom model
λc=λmφm+λpφp (3)
2) For Maxwell model
According to the conductance and the thermal conductivity property of biphase and multiphase, the expression of the thermal conductivity is deduced:
(4)
where λ is thermal conductivity; φ is volume fraction; x equals λm/λp; and subscripts c, p and m refer to composite, reinforcement particle and matrix, respectively.
Generally, the thermal conductivity of matrix Cu is 398 W/(m·K), the thermal conductivity of TiB2 is 96 W/(m·K). The calculated thermal conductivity is obtained from the above models, and the comparison between predictions and experimental data is listed in Table 2.
Table 2 Predicted and experimental thermal conductivities of TiB2p/Cu composite
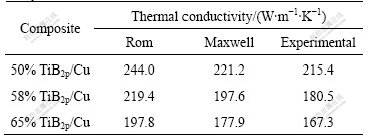
The comparison of those with experimental data indicates that the calculated thermal conductivity of Maxwell models is close to that of TiB2p/Cu composites. The achievement of higher thermal conduction is attributed the high dense composite fabricated by the patent squeeze casting technology, and the TiB2-Cu interfaces are clean, smooth and free-from interfacial reaction products and amorphous layers.
4 Conclusions
1) The full densities of the TiB2p/Cu composites with volume fractions of TiB2 of 50%-65% were fabricated. The composites are full dense and porosity-free macroscopically. TEM observations indicate the TiB2-Cu interfaces are clean, smooth and free from interfacial reaction products and amorphous layers.
2) The linear CTEs of TiB2p/Cu composites range from 8.9×10-6 to 10.4×10-6/K, depending on the volume fraction of TiB2. The experimental CTEs are in good agreement with the predicted values based on Turner’s model.
3) The thermal conductivities of TiB2p/Cu composites at ambient temperature range from 167.3 to 215.4 W/(m?K) and decrease with increasing volume fraction of TiB2, which agrees with the calculated values of Maxwell model.
References
[1] HE H, FU R L, SHEN Y. Preparation and properties of Si3N4/PS composites used for electronic packaging [J]. Composites Science and Technology, 2007, 67(11/12): 2493-2499.
[2] RASHID E S A, ARIFFIN K, KOOI C C, AKIL H M. Preparation and properties of POSS/epoxy composites for electronic packaging applications [J]. Materials & Design, 2009, 30: 1-8.
[3] ZHANG L, QU X H, HE X B. Thermo-physical and mechanical properties of high volume fraction SiCp/Cu composites prepared by pressureless infiltration [J]. Mater Sci Eng A, 2008, 489: 285-293.
[4] ZHANG L, QU X H, DUAN B H. Preparation of SiCp/Cu composites by Ti-activated pressureless infiltration [J]. Trans Nonferrous Met Soc China, 2008, 18(4): 872-878.
[5] HIDEAKI Y, MORIGAMI K. Thermal properties of diamond/copper composite material [J]. Microelectronics & Reliability, 2004, 44(2): 303-308.
[6] SHEN P, ZOU B L, JIN S B. Reaction mechanism in self-propagating high temperature synthesis of TiC-TiB2/Al composites from an Al-Ti-B4C system [J]. Mater Sci Eng A, 2007, 454/455: 300-309.
[7] TU J P, WANG N Y, YANG Y Z. Preparation and properties of TiB2 nanoparticle reinforced copper matrix composites by in situ processing [J]. Materials Letters, 2002, 52(6): 448-452.
[8] TIONG S C, LAU K C. Abrasive wear behavior of TiB2 particle-reinforced copper matrix composites [J]. Mater Sci Eng A, 2000, 282(1/2): 183-186.
[9] KIM J H, YUN J H , PARK Y H. Manufacturing of Cu-TiB2 composites by turbulent in situ mixing process [J]. Mater Sci Eng A. 2007, 449/451: 1018-1021.
[10] ZHANG X H, YAN C, YU Z Z. In-situ combustion synthesis of ultrafine TiB2 particles reinforced Cu matrix composite [J]. Journal of Materials Science, 2004, 39(14): 4683-4685.
[11] HONG C Q, HAN J C. Influence of hot pressing on microstructure and mechanical properties of combustion synthesized TiB2-Cu-Ni composite [J]. Journal of Materials Processing Technology, 2007, 183: 445-449.
[12] KWON Y S. Solid-state synthesis of titanium diboride in copper matrix [J]. Journal of Metastable and Nanocrystalline Materials, 2003, 15/16: 253-258.
[13] ZHAO L Z, ZHAO M J, CAO X M. Thermal expansion of a novel hybrid SiC foam-SiC particles-Al composites [J]. Composites Science and Technology, 2007, 67(15/16): 3404-3408
[14] HSIEH C L, TUAN W H. Thermal expansion behavior of a model ceramic–metal composite [J]. Mater Sci Eng A, 2007, 460/461: 453-458.
[15] TEKCE H S. Effect of particle shape on thermal conductivity of copper reinforced polymer composites [J]. Journal of Reinforced Plastics and Composites, 2007, 26(1): 113-121.
[16] MOLINA J M, NARCISO J, WEBER L. Thermal conductivity of Al-SiC composites with monomodal and bimodal particle size distribution [J]. Mater Sci Eng A, 2008, 480(1/2): 483-488
[17] WEBER L, TAVANGAR R. On the influence of active element content on the thermal conductivity and thermal expansion of Cu-X (X=Cr, B) diamond composites [J]. Scripta Materialia, 2007, 57(11): 988-991.
[18] Hasselman D P H, Lloyd F J. Effective thermal conductivity of composites with interfacial thermal barrier resistance [J]. Journal of Composites, 1987, 21(6): 508-515.
[19] HE J, ZHAO N Q, SHI C S. Reinforcing copper matrix composites through molecular-level mixing of functionalized nanodiamond by co-deposition route [J]. Mater Sci Eng A, 2008, 490(1/2): 293-299.
(Edited by LONG Huai-zhong)
Foundation item: Project(20080430895) supported by China Postdoctoral Science Foundation; Project(2008RFQXG045) supported by the Special Fund of Technological Innovation of Harbin, China
Corresponding author: CHEN Guo-qin; Tel: +86-451-86402372-5058; E-mail: chenguoqin@hit.edu.cn