
Synthesis and behavior of Al-stabilized α-Ni(OH)2
WANG Hong(王 虹), TANG Zhi-yuan(唐致远), LIU Yuan-gang(刘元刚), LEE Chang-sheng(李昌盛)
Department of Applied Chemistry, School of Chemical Engineering and Technology, Tianjin University,
Tianjin 300072, China
Received 2 January 2008; accepted 21 August 2008
Abstract: Nano-fibrous Al-stabilized α-Ni(OH)2 was synthesized by the urea thermal decomposition method. The grain morphology, crystal structure, thermal stability, chemical composition and electrochemical performance of the Al-stabilized α-Ni(OH)2 were investigated. It is found that the urea thermal decomposition is an appropriate way to precipitate the Al-stabilized α-Ni(OH)2 with excellent performance. The fiber cluster TEM pattern shows that the synthesized α-Ni(OH)2 powder is composed of agglomerates of much smaller primary particles. The stabilized α-Ni(OH)2 powder with a 7.67 ? c-axis distance and low thermal stabilities is obtained. The FTIR spectrum shows that the materials contain absorbed water molecules, and intercalated CO32- and SO42- anions. The experimental α-Ni(OH)2 electrode exhibits excellent electrochemical redox reversibility, high special capacity, good rate discharging performance and perfect cyclic stability. Moreover, the synthesized α-Ni(OH)2 electrode also shows high discharge capacity and cyclic stability at high temperature. The electrode specific capacity remains 290 mA?h/g at 60 ℃, which is only 15 mA?h/g lower than its ambient value, and the capacity loss is 0.9 mA?h/g per charge-discharge cycle.
Key words: urea thermal decomposition; Al-stabilized α-Ni(OH)2; electrochemical performance
1 Introduction
Nickel hydroxide is widely used as the positive material in nickel-based alkaline secondary batteries such as Ni-Fe, Ni-Zn, Ni-Cd and Ni-MH rechargeable systems[1-2]. There are two polymorphs for Ni(OH)2 known as α- and β-phase, both of which have the same hexagonal structure. The difference is that the β-Ni(OH)2 exhibits well ordered brucite type hydroxide layers with an interlayer distance of 4.6 ?, whereas the α-Ni(OH)2 is known as hydrated nickel hydroxide with an interlayer separation of almost 8.0 ?, which depends on the type and extent of intercalated anions and water molecules bonded to the hydroxyl groups by hydrogen bonds[3-4]. Moreover, the α-Ni(OH)2 exhibits turbostratic character, for example, though the interlayer separation remains constant, the orientation of the layers is completely random. It is generally believed that the α-Ni(OH)2 shows superior electrochemical properties to the β-Ni(OH)2 with a much higher discharge capacity and no mechanical swelling deformation when reversibly converted to γ-Ni(OH)2[5-6]. However, the α-Ni(OH)2 is metastable and would transform automatically into β-Ni(OH)2 in strong alkaline solutions used for battery electrolyte[7-11]. Aluminium is considered to be the most effective element to stabilize α-Ni(OH)2. A number of investigations have been made on the preparation and characterization of Al-stabilized α-Ni(OH)2 powders since the aluminium addition could increase the positive charge of hydroxide layers and enhance the strength of anion binding to the layers [12-14]. The main purpose of the present work was to synthesize Al-stabilized α-Ni(OH)2 powders with a novel urea thermal decomposition method by programmed heating process. The physicochemical characterizations of prepared α-Ni(OH)2 powders were carried out by scanning electronic micrograph(SEM), X-ray diffraction (XRD), thermogravimetric analysis(TGA) and Fourier transform infrared spectroscopy(FTIR). Cyclic voltammetry, rate dischargeability and cycle life of batteries were tested at room temperature. The charge-discharge curves and cyclic properties were also conducted at a high temperature of 60 ℃.
2 Experimental
2.1 Synthesis of Al-stabilized α-Ni(OH)2
The Al-stabilized α-Ni(OH)2 was synthesized by the method as follows. 200 mL deionized water was used to prepare the source solution. An agate pot was used as the solution container, which was filled with 72 g urea (1.2 mol), 10.52 g NiSO4?6H2O (0.04 mol) and 2.67 g Al2(SO4)3?18H2O (0.004 mol). Then, 0.5 mL of Tween-80 was added as reaction surfactant. With a muffle stove as the programmed heater, the reaction solution was heated to 120 ℃ within 1 h and kept for 3 h, and then naturally cooled to 60 ℃ and preserved for 1 h. When cooled to ambient temperature, the reaction precipitate was separated from the solution by filtration, washed twice with deionized water, centrifugalized and dried in vacuum at 80 ℃ for 12 h.
2.2 Characterization of Al-stabilized α-Ni(OH)2
The surface morphology of Al-stabilized α-Ni(OH)2 particles was observed by SEM (JSM-6460LV) and the TEM morphology of samples was measured by a JEM-100CX-II transmission electron microscope. The phase structure was analyzed by an X-ray diffractometer (X’Pert PANalytica) with Co Kα1 radiation. Thermo- gravimetric analysis of the synthesized product was performed with NETZSCH STA409PC thermal analyzer at a heating rate of 20 ℃/min. A PEPKIN-E Fourier transform infrared spectrophotometer was used to study the infrared spectroscopy of synthesized Ni(OH)2 powders.
2.3 Preparation of nickel electrode and electro- chemical testing
The pasted nickel electrodes were prepared by the following methods. 86% Ni(OH)2, 4% cobalt powder and 9% nickel powder were thoroughly mixed with a certain amount of 60% polytetrafluoroethylene solution. The paste obtained was incorporated into a nickel foam (2.5 cm×2.5 cm×1.1 mm) using a spatula and then pressed to a thickness of 0.5 mm. Two pieces of MmNi3.55Co0.75Mn0.4Al0.3 plates were used as counter electrodes. The 7.8 mol/L KOH alkaline solution was used as the electrolyte. Galvanostatic charge-discharge and electrochemical cyclic performance tests at ambient environment and high temperature were conducted using a BS9300 battery tester. The electrochemical workstation (GAMARY PCI4-750) was used to measure the cyclic voltammetric performance with a three-electrode system. The powder microelectrode was used as working electrode, the Hg/HgO (7.8 mol/L KOH) electrode as the reference electrode and the platinum as counter electrode.
3 Results and discussion
The thermal decomposition of urea occurs rapidly when the urea is heated to 120 ℃. The decomposition reaction produces a lot of ammonia, which results in the increase of the pH value of the source solution. The NH3 and CO2 are formed according to the reaction (1). And then the NH3 and CO2 are hydrolyzed to NH4OH and H2CO3, respectively[15] as shown in reactions (2) and (3). The Al-stabilized α-Ni(OH)2 precipitation is synthesized according to the reaction (4), which contains the hydrotalcite-like compound of formula Ni1-2xAl2x- (OH)2(CO3)x(SO4)x·(H2O)n (i.e. α-Ni(OH)2) with aluminium substitution for nickel in the lattice of nickel hydroxide. It has been reported that those compositions (x≥0.1) in the compounds could increase the electrochemical stability strongly in alkaline medium.
NH2-CO-NH2+H2O→2NH3+CO2 (1)
CO2+H2O→H2CO3 (2)
NH3+H2O→NH4OH (3)
2NH4OH+(1-2x)NiSO4+xAl2(SO4)3+xH2CO3→
Ni1-2xAl2x(OH)2(CO3)x(SO4)x·(H2O)n+(NH4)2SO4 (4)
The SEM image of Al-stabilized α-Ni(OH)2 is given in Fig.1(a). It can be observed that the prepared particles are in sub-micron size and they agglomerate greatly and adhere with each other to form large ones. Fig.1(b) shows the TEM micrograph of synthesized Al-stabilized α-Ni(OH)2. It can be seen that the crystal grain of the nanocrystalline α-Ni(OH)2 is not in spherical-shape, but shows a nanometer fiber cluster. The diameter of the fiber is about 5-10 nm and its length is 40-70 nm. The EDS analysis result of the fiber is listed in Table 1, which indicates that all the elemental components of the source reagents were detected on the surface of the product except nitrogen, which is contained in excess extent of reaction solution as (NH4)2SO4. The mole fraction of Ni is approximately 40.5% in the experimental Al-stabilized α-Ni(OH)2. This value is a little lower than that of earlier studies.
Table 1 EDS composition of Al-stabilized α-Ni(OH)2 (mole fraction, %)
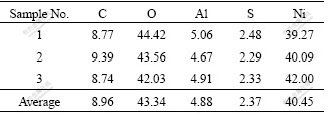
The XRD pattern of the synthesized Al-stabilized α-Ni(OH)2 is shown in Fig.2. The general features of all diffraction peaks are consistent with the patterns for reported α-Ni(OH)2 and its derivatives[16]. The two peaks at around 13? and 27? corresponding to (001) and (002) planes are characteristic peaks of α-Ni(OH)2. The broad asymmetric band at 40? is assigned to (101) reflec tion, which is attributed to turbostratic structures of α-Ni(OH)2[17]. No characteristic peak of the Al or Al(OH)3 is found in this pattern, which indicates that Al is co-precipitated with Ni into the lattice of α-Ni(OH)2. According to the Bragg formula 2dsinθ=λ, the c-axis distance of the synthesized Al-substituted α-Ni(OH)2 is 7.67 ?. The value is well consistent with that of the ideal α-Ni(OH)2.
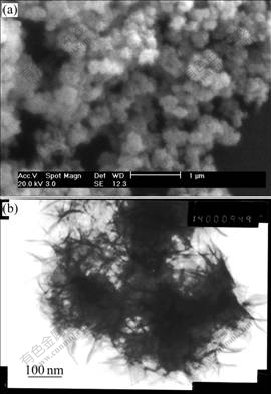
Fig.1 SEM (a) and TEM (b) micrographs of synthesized Al- stabilized α-Ni(OH)2
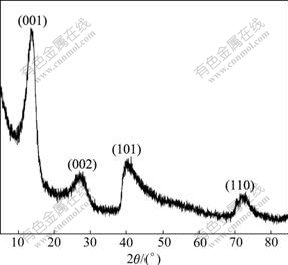
Fig.2 XRD pattern of Al-substituted α-Ni(OH)2
The thermal-gravimetric pattern of the synthesized Ni(OH)2 powders is shown in Fig.3. It can be observed that the mass of samples decreases gradually from 50 to 300 ℃ and decreases sharply between 300 and 400 ℃. A mass loss of about 10% is observed from 50 to 300 ℃; another mass loss of about 20% is shown between 300 and 400 ℃. Accordingly, two categories of chemical reactions were postulated[18]. The initial mass loss is attributed to dehydration process (reaction (5)), which is resulted from the loss of water molecules absorbed on the grains of synthesized α-Ni(OH)2. Another mass loss is attributed to the α-Ni(OH)2 decomposition (reaction (6)).
α-Ni(OH)2?XadsH2O→α-Ni(OH)2+XH2O (5)
α-Ni(OH)2→NiO+Al2O3+H2O (6)
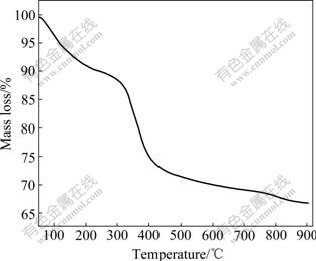
Fig.3 Thermo-gravimetric pattern of Al-stabilized α-Ni(OH)2
Fig.4 shows the FTIR spectrum of Al-stabilized α-Ni(OH)2. The characteristics of α-phase obtained from this spectrum are as follows[19-20]: 1) the largest absorption band centered at about 3 450 cm-1 is ascribed to the stretching vibration of hydroxyl group of absorbed water; 2) the absorption peak at about 1 630 cm-1 corresponds to the angular deformation of the water molecules intercalated in the interslab space or absorbed on the grain surface; 3) the band at 1 364 cm-1 is attributed to the stretching vibration of CO32- ions inserted in the α-Ni(OH)2 spaces, which are introduced to compensate for the excess of positive charge caused by the Al3+ substitution for Ni2+ site; 4) the vibration bands at 1 115 cm-1 and 619 cm-1 indicate the presence of a small amount of SO42- ions, which come from the precipitation medium; 5) a weak band around 460 cm-1 is resulted from the Ni-O lattice vibration ν(Ni-O).
Fig.5 shows the typical cyclic voltammogram of Al-substituted α-Ni(OH)2 with a scan rate of 0.5 mV/s. In the range of scanning potentials (0 V to 0.6 V vs Hg/HgO), one main anodic oxidation peak appears at about 525 mV and another sharp anodic oxidation peak appears at about 600 mV. The two anodic oxidation peaks correspond to the oxidation reaction α-Ni(OH)2→γ-NiOOH+H++e and parasitic oxygen evolution, respectively. In the reverse scan, it can be observed that the oxyhydroxide reaction of γ-NiOOH to α-Ni(OH)2 occurs at 384 mV. The second reduction current peak at 294 mV is probably due to the part-overlapped peaks of the reduction of γ*-NiOOH to α*-Ni(OH)2[21], which indicates that the experimental Al-stabilized α-Ni(OH)2 electrode can discharge at a wide range of current to deliver most of the capacity and show good kinetic characteristics.
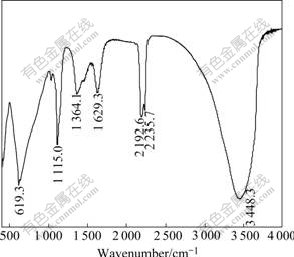
Fig.4 FTIR spectrum of Al-stabilized α-Ni(OH)2
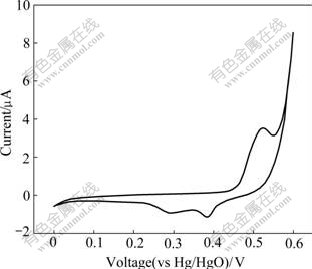
Fig.5 Cyclic voltammogram of Al-stabilized α-Ni(OH)2
Fig.6 shows the discharge curves of Al-stabilized α-Ni(OH)2. It is clearly observed from Fig.6 that the experimental α-Ni(OH)2 electrode exhibits excellent discharging capabilities at various rates. The special discharge capacities for discharge rates of 0.5C, 1.0C and 2.0C are 305, 280, and 250 mA?h/g, respectively, and the discharge curves exhibit high discharge voltage platforms. This is mainly due to the phase composition. The discharge capacity for electrodes containing γ-NiOOH is higher, which is caused by a higher nickel oxidation state. The value of nickel oxidation state in the γ-NiOOH can reach about 3.7, while that of β-NiOOH is around 3.0. The phase transformation during charge- discharge process of Al-stabilized α-Ni(OH)2 is from α-Ni(OH)2 to γ-NiOOH. The exchange electrons for per nickel atom are more than one. Thus, the electrode exhibits greater discharge capacity.
The structure of α-Ni(OH)2 is unstable and easily converted to that of β-Ni(OH)2 in alkali solution. Fig.7 presents the cycling performance for the synthesized Al-stabilized α-Ni(OH)2. The discharge capacity after 230 cycles is about 255 mA?h/g, which is 83.3% of the highest discharge capacity. Thus, it can be concluded that the structure of the synthesized Al-stabilized α-Ni(OH)2 obtained by urea thermal decomposition is stable during charge-discharge cycling. This might be attributed to the aluminium stabilization for the α-Ni(OH)2, which forms a double hydroxide containing Al3+ substitution for Ni2+ in the Ni(OH)2 lattice[22].
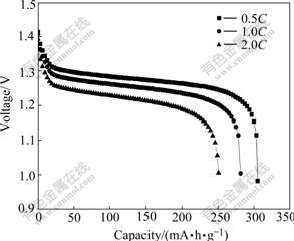
Fig.6 Discharge curves of Al-stabilized α-Ni(OH)2
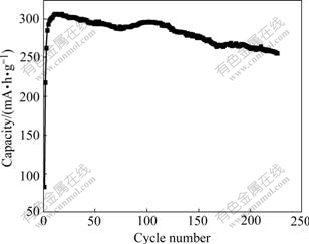
Fig.7 Cycling performance of Al-stabilized α-Ni(OH)2
Fig.8 shows the charge-discharge comparison of the synthesized Al-stabilized α-Ni(OH)2 at temperatures of 25 and 60 ℃. The charge and discharge potentials of the electrode at 60 ℃ are lower than those at 25 ℃. The special charge capacity reaches about 100 mA?h/g at high temperature, when the charge potential increases sharply to about 50 mV, which might result from the occurrence of parasitic oxygen evolution, and the side reaction coexists with the oxidation of α-Ni(OH)2 till the charging process ends. However, for the α-Ni(OH)2 electrode tested at 25 ℃, the oxygen evolution occurs when the special charge capacity arrives at 335 mA?h/g. From that time, the oxygen evolution acts as main reaction in the following charge process. The special discharge capacities at 25 and 60 ℃ are 305 mA?h/g and 290 mA?h/g, respectively. The discharge potential platforms at both 25 and 60℃ do not show obvious difference at the initial discharge stage, whereas the potential platform at 60 ℃ decreases greatly than that at 25 ℃ at the later discharge stage. Since the Al-stabilized α-Ni(OH)2 shows excellent properties at high temperature, its cycle life at 60 ℃ was further tested.
Fig.9 shows the cycling performance of Al- stabilized α-Ni(OH)2 with rate of 0.5C at 60 ℃. It is observed that the capacity of the experimental electrode decreases by about 30% after 95 cycles at 0.5C rate. The average capacity fading is about 0.9 mA?h/g per cycle, which indicates a high stability of the Al-stabilizedα-Ni(OH)2 electrode at 60 ℃.
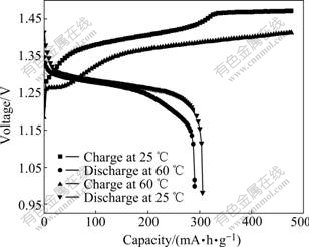
Fig.8 Charge-discharge curves of Al-stabilized α-Ni(OH)2 with rate of 0.5C at 25 ℃ and 60 ℃
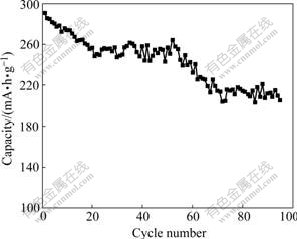
Fig.9 Cycling performance of Al-stabilized α-Ni(OH)2 with rate of 0.5C at 60 ℃
4 Conclusions
1) The urea thermal decomposition method was applied to synthesize Al-stabilized α-Ni(OH)2, which is composed of agglomerates of much smaller primary particles. It is confirmed that the crystal c-axis distance of prepared powders is 7.67 ?, corresponding to the characteristic of turbostratic α -Ni(OH)2.
2) According to thermogravimetric curves, two categories of chemical reactions can be proposed for the heating decomposition process of the synthesized α-Ni(OH)2. One is the loss of absorbed water on the grain boundary and the other is the formation of nickel oxide. The characteristic absorption bands of water molecules, inserted anions such as CO32- and SO42- in α-Ni(OH)2 lattice are also detected by FTIR spectrum. The redox potential variation of the as-prepared α-Ni(OH)2 is only 110 mV, indicating a higher electrochemical reversibility.
3) At 0.5C, 1.0C and 2.0C rate, the specific discharge capacities of experimental α-Ni(OH)2 electrode are 305, 280 and 250 mA?h/g, respectively.
4) The α-Ni(OH)2 electrode exhibits an excellent cyclic stability in alkaline medium at ambient and high temperature. For example, the discharge capacity after 200 cycles at room temperature is 83.3% of the highest discharge capacity. The discharge capacity after 90 cycles at 60 ℃ is 70% of the initial discharge capacity.
References
[1] SHUKLA A K, VENUGOPALAN S, HARIPRAKASH B. Nickel-based rechargeable batteries [J]. Journal of Power Sources, 2001, 100: 125-148.
[2] FREITAS M B J G. Nickel hydroxide powder for NiO·OH/Ni(OH)2 electrodes of the alkaline batteries [J]. Journal of Power Sources, 2001, 93: 163-173.
[3] INDIRA L, MRIDULA D, VISHNU, KAMATH P. Electrosynthesis of layered double hydroxides of nickel with trivalent cations [J]. Journal of Power Sources, 1994, 52: 93-97.
[4] JAYASHREE R S, VISHNU, KAMATH P. Factors governing the electrochemical synthesis of α-nickel (II) hydroxide [J]. Journal Appl Electrochem, 1999, 29: 449-454.
[5] WANG X Y, LUO H A, PARKHUTIK P V, MILLAN A C, MATVEEVA E. Studies of the performance of nanostructural multiphase nickel hydroxide [J]. Journal of Power Sources, 2003, 115: 153-160.
[6] JAYASHREE R S, VISHNU, KAMATH P. Layered double hydroxides of Ni with Cr and Mn as candidate electrode materials for alkaline secondary cells [J]. Journal of Power Sources, 2002, 107: 120-124.
[7] DAI J X, SAM, LI F Y, XIAO T D, WANG D M, REISNER D E. Structural stability of aluminum stabilized alpha nickel hydroxide as a positive electrode material for alkaline secondary batteries [J]. Journal of Power Sources, 2000, 89: 40-45.
[8] RAMESH N, JAYASHREE R S, VISHNU KAMATH P. The effect of the moisture content on the reversible discharge capacity of nickel hydroxide [J]. Journal of Electrochemistry Society, 2003, 150: A520-524
[9] CHEN H, WANG J M, PAN T, ZHAOY L, ZHANG J Q, CAO C N. The structure and electrochemical performance of spherical Al-substituted α-Ni(OH)2 for alkaline rechargeable batteries [J]. Journal of Power Sources, 2005, 143(1/2): 243-255.
[10] HU Kang, GAO Xue-ping, DAG N, BURCHARDT T, NAKSTAD N K. Evaluation of nano-crystal sized α-nickel hydroxide as an electrode material for alkaline rechargeable cells [J]. Journal of Power Sources, 2006, 160: 704-710.
[11] SHANG C X, BOUOUDINA M, SONG Y, GUO Z X. Mechanical alloying and electronic simulations of (MgH2+M) systems (M=Al, Ti, Fe, Ni, Cu and Nb) for hydrogen storage [J]. International Journal of Hydrogen Energy, 2004, 29: 73-80.
[12] SONG C H, CHIU S L, CHAN I. Effects of ball milling on the physical and electrochemical characteristics of nickel hydroxide powder [J]. J Appl Electrochem, 2005, 35(2): 157-162.
[13] LIU B, WANG X Y, YUAN H T, ZHANG Y S, SONG D Y, ZHOU Z X. Physical and electrochemical characteristics of aluminium- substituted nickel hydroxide [J]. J Appl Electrochem, 1999, 29: 855-860.
[14] ACHARYA R, SUBBAIAH T, ANAND S, DAS R P. Effect of preparation parameters on electrolytic behaviour of turbostratic nickel hydroxide [J]. Mater Chem Phys, 2003, 81: 45-49.
[15] AKINC M, JONGEN N, LEMAITRE J, HOFMANN H. Synthesis of nickel hydroxide powders by urea decomposition [J]. Journal Euro Ceram Soc, 1998, 18: 1559-1564.
[16] WANG C Y, ZHONG S, KONSTANTINOV K, WALTER G, LIU H K. Structural study of Al-substituted nickel hydroxide [J]. Solid State Ion, 2002, 148: 503-508.
[17] ACHARYA R, SUBBAIAH T, ANAND S, DAS R P. Effect of precipitating agents on the physicochemical and electrolytic characteristics of nickel hydroxide [J]. Mater Lett, 2003, 57: 3089-3095.
[18] KUMAR V G, MUNICHANDRAIAH N, KAMATH P V, SHUKLA A K. On the performance of stabilized α-nickel hydroxide as a nickel-positive electrode in alkaline storage batteries [J]. Journal of Power Sources, 1995, 56: 111-114.
[19] LIU B, YUAN H T, ZHANG Y S, ZHOU Z X, SONG D Y. Cyclic voltammetric studies of stabilized α-nickel hydroxide electrode [J]. Journal of Power Sources, 1999, 79: 277-280.
[20] JAYALAKSHMI M, VENUGOPAL N, RAMACHANDRA REDDY B, MOHAN RAO M. Optimum conditions to prepare high yield, phase pure α-Ni(OH)2 nanoparticles by urea hydrolysis and electrochemical ageing in alkali solutions [J]. Journal of Power Sources, 2005, 150: 272-275.
[21] ZHOU H B, ZHOU Z T. Structures and cyclic voltammetric performances of high Al-component Ni/Al-layered double hydroxide [J]. Chemistry, 2006, 69(1): 31-35.
[22] LIU B, YUAN H T, ZHANG Y S. Impedance of Al-substituted α-nickel hydroxide electrodes [J]. International Journal of Hydrogen Energy, 2004, 29: 453-458.
Corresponding author: WANG Hong, Tel: +86-769-83015364; E-mail: waho7808@163.com
DOI: 10.1016/S1003-6326(08)60247-2
(Edited by LI Xiang-qun)