J. Cent. South Univ. Technol. (2010) 17: 732-737
DOI: 10.1007/s11771-010-0548-7
Influence of flux additives on iron ore oxidized pellets
FAN Xiao-hui(范晓慧), GAN Min(甘敏), JIANG Tao(姜涛), YUAN Li-shun(袁礼顺), CHEN Xu-ling(陈许玲)
School of Resources Processing and Bioengineering, Central South University, Changsha 410083, China
? Central South University Press and Springer-Verlag Berlin Heidelberg 2010
Abstract: Six additives, i.e., limestone, lime, magnesite, magnesia, dolomite and light-burned-dolomite, were added for investigating their influences on the pellet quality. For green balls, adding lime and light-burned-dolomite makes the wet drop strength decrease firstly, and then increase with further increase of additive dosage. Ca(OH)2 affects the bentonite properties at the beginning, but the binding property of Ca(OH)2 will be main when the dosage is higher. The other four additives decrease the drop strength for their disadvantageous physical properties. For preheated pellets, no mater what kind of additive is added, the compressive strength will be decreased because of unmineralized additives. For roasted pellets, calcium additives can form binding phase of calcium-ferrite, and suitable liquid phase will improve recrystallization of hematite, but excessive liquid will destroy the structure of pellets, so the compressive strength of pellet increases firstly and then drops. When adding magnesium additives, the strength will be decreased because of the oxidation of magnetite retarded by MgO.
Key words: iron ore; additives; oxidized pellets; compressive strength
1 Introduction
In order to satisfy the requirements of the blast furnace (BF) slag chemical compositions, fluxes such as limestone, magnesite, and dolomite should be added as furnace burdens [1-4]. Because it is unsuitable and unscientific to add fluxes into BF directly, they are usually added in the agglomerating process, which will heighten basicity (R) or MgO content of agglomerations. There are many reports about the influence of R and MgO on the sintering, and the results showed that suitable adding quantity of fluxes would improve the quality of sinter [5-9]. However, the research of fluxes applications in pelletizing is not as many as that in sintering, because the dominating production of pellet in China is acid at present.
With the rapid increase of the output of pellets in China, the proportion of pellets in BF burdens will be increased inevitably. In order to keep the balance of slag basicity, the sinter basicity should be heightened continuously if the pellets are acid. However, there are suitable ranges for sinter basicity and MgO contents, which means that the adding fluxes in sinters are limited. So, adding part of fluxes into pellets becomes an essential measure.
Metallurgical properties, such as softening and melting properties, and reduction characteristics of fluxed pellets were evaluated in Refs.[10-13], and suitable basicity and MgO content were also assured. Conclusions were established that limestone, dolomite, magnesia and so on could be used to make a fluxed pellet that had superior metallurgical properties relative to conventional acid pellets[14-16]. But there was lacking of research about the influences of flux additives on the quality of green ball, preheated pellet and roasted pellet. Therefore, it is very significant to find out the universal influence laws of flux additives with different basicities and MgO contents.
2 Materials and methods
2.1 Materials properties
The chemical compositions of the materials are shown in Table 1. In the experiment, the used concentrate had high Fe grade, with few impurities except for 5% SiO2. Bentonite was used as binder. Additionally, there were six additives used for increasing MgO content or basicity of the pellets. The particle size of concentrate and additives was in the “fine” category, with more than 90% passing sieve with pore diameter of 0.074 mm. The surface area surpassed 1 000 cm2/g. Bentonite used had a colloid index of 6.6 mL/g, a swelling index of 20.7 mL/g, water absorption rate of 500.3% per 2 h, montmorillonite content of 88.8%, and a proportion of particles with a size of smaller than 0.074 mm of 99.6%.
Table 1 Chemical compositions and physical properties of materials

2.2 Experimental methods
Micro-balling was done in a laboratory-scale balling disc with a diameter of 1.0 m, a rotational speed of 21 r/min, and 5 kg per batch. After adjusting the humidity of the concentrate, the binder and additives were introduced. The quantity of bentonite was fixed as 2% (mass fraction). The amounts of additives were assured by the requirements of basicity and MgO content. The mixture was first formed into green pellets. The green pellets were then sieved between 12 and 16 mm. Drying of the green pellets was carried out in a drier at 105 ℃ for 2 h. A horizontal tube furnace was used to fire the pellets in two stages: first a preheat cycle and then a roasting cycle. The temperature of preheating was set at 950 ℃, and the time was 10 min. The temperature of roasting was 1 250 ℃, and the time was 12 min.
3 Results analysis
3.1 Influence of additives on green balls
The effect of additives on the wet drop strength of green balls is shown in Fig.1. With no additives (R 0.03 and MgO 0.4%), the wet drop strength is 4.7 times. When limestone, dolomite, magnesite or magnesia is added separately, the wet drop strength decreases gradually with the increase of additives. But when lime or light-burned dolomite is added, the wet drop strength decreases at first and then increases with further increasing the dosage.
Dolomite, magnesite and limestone belong to carbonate minerals. There are no reactions between carbonate minerals and concentrate or water in green balls. Fig.2 shows the granule morphologies of concentrate and carbonate minerals. Compared with the figure of concentrate, limestone presents rectangle and rhombus more closely, which makes them more difficult to contact with other particles, and deteriorates the strength of green balls.
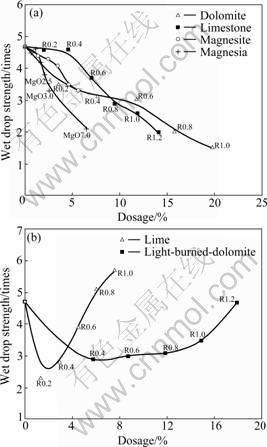
Fig.1 Effect of additives on wet drop strength of green balls: (a) Additives without ionized Ca2+; (b) Additives with ionized Ca2+
However, lime and light-burned-dolomite could be hydrated and produce Ca(OH)2. Compared with Na+, Ca2+ has more electric quantity and the electrostatic attraction between montmorillonite platelets and Ca2+ is larger, which cause Ca2+ easily to substitute Na+ in the interlayer of bentonite. The effects of Ca2+ on the water-absorbing ability of bentonite and the speed of absorbing water are shown in Table 2 and Fig.3, respectively. Table 2 indicates that Ca2+ has a notable influence on the ability of absorbing water, and absorbency (mass fraction of water per 2 h) decreases as the concentration of Ca2+ ascends. Fig.3 shows that Ca2+ will reduce the speed of bentonite absorbing water. So it can be concluded that adding lime or light-burned- dolomite will decrease the cohesive action of bentonite and reduce the wet drop strength. But Ca(OH)2 is also a binder, so the wet drop strength will increase with higher dosage of lime or light-burned-dolomite.

Fig.2 Granule morphologies of materials scanned by SEM: (a) Concentrate; (b) Limestone
Table 2 Effect of Ca2+ concentration in water on bentonite’s water absorbency
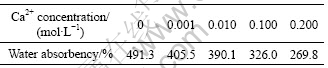
3.2 Influence of additives on preheated pellets
The influence of additives on preheated pellets is shown in Fig.4. The two charts of Fig.4 show that no mater adding calcium additives or magnesium additives, the strength decreases with the increase of additives, also with rising the basicity or MgO content.
The microstructures of preheated pellets are shown in Fig.5. With no additives (see Fig.5(a)), the main minerals are hematite and magnetite, whose mirco- crystallization will improve the strength of preheated pellets. However, when additives are added (see Figs.5(b) and (c)), there exist unmineralized additives in pellets because the preheating temperature is not high enough. The unmineralized additives will hinder the micro- crystallization of hematite and magnetite, which will decrease the compressive strength of preheated pellets.

Fig.3 Speed of bentonite absorbing water affected by Ca2+

Fig.4 Effect of additives on compressive strength of preheated pellets: (a) Additives containing calcium; (b) Additives containing magnesium
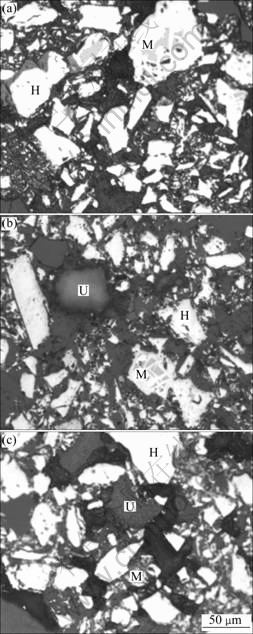
Fig.5 Microstructures of preheated pellets (H—Hematite, M—Magnetite, U—Unmineralized additives): (a) No additives; (b) Adding limestone; (c) Adding magnesite
On the other hand, at preheating temperature (generally 950-1 000 ℃), carbonate minerals will decompose and produce CO2, which will also influence the strength of preheated pellets.
3.3 Influence of additives on roasted pellets
The effect of additives on the compressive strength of roasted pellets is shown in Fig.6. Fig.6(a) shows that with the increase of basicity, the compressive strength increases firstly and then drops, and the maximum value is obtained when the basicity is between 0.4 and 0.6, and limestone, lime, dolomite, and light-burned-dolomite are added separately. Fig.6(b) shows that the compressive strength decreases when the content of MgO increases, no mater adding magnesite or magnesia.

Fig.6 Effect of additives on compressive strength of roasted pellets: (a) Additives containing calcium; (b) Additives containing magnesium
The microstructures of roasted pellets are shown in Fig.7. Fig.7(a) indicates that with no additives the main mineral of pellets is hematite, so the strength is determined by the recrystallization of hematite. Figs.7(b) and (c) show that with adding calcium additives, such as limestone and dolomite, CaO will react with Fe2O3 and SiO2, separately, and form calcium-ferrite and calcium-silicate, and then calcium-ferrite will become liquid phase at roasting temperature. A little liquid phase can improve the solid diffusion and enhance the recrystallization of hematite, but the structure of pellets will be destroyed if the liquid phase is excessive. That is why the strength of roasted pellets increases firstly and then decreases with the increase of basicity. Fig.7(d) indicates that when adding additives containing magnesium, such as magnesite, MgO will react with Fe2O3 and form magnesium ferrite, which cannot become liquid phase at the roasting temperature. Besides, MgO can also resolve in magnetite, and retard the oxidation of magnetite, which will holdback the recrystallization of hematite and cause the strength of roasted pellets to be decreased when increasing the content of MgO.
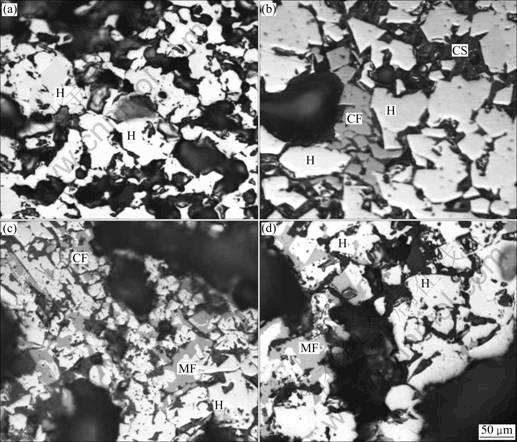
Fig.7 Microstructures of roasted pellets (H—Hematite; M—Magnetite; CF—Calcium ferrite; MF—Magnesium ferrite; CS— Calcium silicate): (a) No additives; (b) Basicity 0.8 with adding limestone; (c) Basicity 0.5 and MgO 2.3% with adding dolomite; (d) MgO 2.5% with adding magnesite
4 Conclusions
(1) When adding lime and light-burned-dolomite, the wet drop strength of green ball will decrease firstly, and then go up with the increase of dosage. The reason is that Ca2+ formed by lime and light-burned-dolomite will replace Na+ in the interlayer of bentonite and lower the quality of bentonite. But with high additives dosage, the binding of Ca(OH)2 can increase the wet drop strength. When adding limestone, magnesite, dolomite and magnesia, separately, the wet drop strength will be decreased because of their disadvantageous granule morphologies.
(2) No mater what kind of additives is added, there exist unmineralized ones in preheated pellets, which will hinder the micro-crystallization of hematite and make the compressive strength decreased.
(3) For roasted pellet, as additives contain calcium, the compressive strength increases firstly and then drops with the increase of basicity, and the maximum value is obtained at the basicity of 0.4-0.6. The reaction of CaO with Fe2O3 and SiO2 will form binding phase of calcium-ferrite, and the suitable liquid phase will improve the recrystallization of hematite, but the excessive liquid phase will destroy the structure of pellets.
(4) When adding magnesium additives, the compressive strength of roasted pellets decreases with the increase of MgO, not only because the magnesium- ferrite formed by MgO and Fe2O3 cannot become liquid phase at roasting temperature, but also because the dissolution of MgO in magnetite will retard the oxidation of magnetite and holdback the recrystallization of hematite.
References
[1] ZHANG Yu-zhu, CENG Ming-shan, XIANG Li, TAO Wen. The influence of MgO and basicity on the viscosity of BF slag [J]. Journal of Materials and Metallurgy, 2005, 4(4): 253-256. (in Chinese)
[2] EL-GEASSY A A, NASR M I, KHEDR M H, ABDEL-HALIM K S. Reduction behaviour of iron ore fluxed pellets under load at 1 023- 1 273 K [J]. ISIJ International, 2004, 44(3): 462-469.
[3] GUAN Xue-fang, HOU Hui-jun, OU Tao. The way of heightening MgO content of sintering and the effect of BF [J]. Sintering and Pelletizing, 2001, 26(2): 1-5. (in Chinese)
[4] FU Ju-ying, JIANG Tao, ZHU De-qing. Sintering and pelletizing [M]. Changsha: Central South University Press, 1995: 296-298.
[5] NUTTER S M, LI K. Effect of composition and structure on fluxed pellet reduction kinetics [J]. Transactions of the Iron and Steel Society of AIME, 1991, 12: 71-83.
[6] JIANG Xin, WU Gang-sheng. Effect of MgO on sintering process and metallurgical properties of sinter [J]. Iron and Steel, 2006, 41(3): 8-12. (in Chinese)
[7] SUN Jin-tuo. Investigation on rational basicity of sintering [J]. Iron and Steel, 2001, 36(8): 1-4. (in Chinese)
[8] YANG Yong-bin, HUANG Gui-xiang, JIANG Tao, HUANG Zhu-chong. Application of organic binder as substitutes for bentonite in pellet preparation [J]. Journal of Central South University: Science and Technology, 2007, 38(5): 851-857. (in Chinese)
[9] FENG Xiang-peng, ZHANG Yu-zhu, LI Zhen-guo. The effect of basicity on sintering strength in the condition of low-Si [J]. Sintering and Pelletizing, 2004, 29(2): 9-12. (in Chinese)
[10] ADRIAN I P, BORJE B. Experiences with dolomite fluxed pellets by Lkab [C]// Proceedings of Ironmaking. New York: AIME, 1977, 366-383.
[11] CHIZHIKOVA V M, VAINSHTEIN R M. Composition of iron-ore pellets with different types of additives [J]. Metallurgist, 2003, 47(9): 349-352.
[12] BLEIFUSS R L, GOETZMAN H E, LOPEZ R D, BECKMAN C A. Development of Minnesota taconite fluxed pellets as an improved blast-furnace material [C]// Proceedings of AIME 47th Annual Mining Symposium. New York: AIME, 1986: 1-31.
[13] OSAMU T, TAKESHI S, MAMORU O, ISAO F. Effect of MgO-component on various metallurgical properties of self-fluxed pellets [J]. Journal of the Iron and Steel Institute of Japan, 1980, 66(13): 1840-1849.
[14] FRIEL J J, ERICKSON E S Jr. Chemistry microstructure and reduction characteristics of dolomite-fluxed magnetite pellets [J]. Metallurgical Transactions B: Process Metallurgy, 1980, 11(2): 233- 243.
[15] TAKESHI S, SHOJI S, OSAMU T, MAMORU O, ISAO F. High temperature reduction and softening properties of pellets with magnesite [J]. Transactions of the Iron and Steel Institute of Japan, 1983, 23(2): 153-160.
[16] ZHANG Yong-ming. Characteristic and production practice of fluxed pellets contents MgO [J]. Sintering and Pelletizing, 1998, 23(2): 1-4. (in Chinese)
Foundation item: Project(2008BAB32B06) supported by the Key Projects in the National Science and Technology Pillar Program during the 11th Five-year Plan Period; Project(2009ybfz20) supported by the Program for Excellent Doctor’s Degree Paper in Central South University, China; Project(1343/74333001114) supported by the Postgraduate’s Paper Innovation Fund of Hunan Province, China
Received date: 2009-12-01; Accepted date: 2010-04-07
Corresponding author: GAN Min, Doctoral candidate; Tel: +86-731-88830542; E-mail: ganminhao@126.com
(Edited by CHEN Wei-ping)