
Microstructure and texture evolution of AZ31 magnesium alloy during rolling
HUANG Guang-jie(黄光杰)1, 2, LIU Qing(刘 庆)1, 2, WANG Ling-yun(汪凌云)1, 2,
XIN Ren-long(辛任龙)1, CHEN Xing-pin(陈兴品)1, PAN Fu-sheng(潘复生)1, 2
1. College of Materials Science and Engineering, Chongqing University, Chongqing 400044, China;
2. National Engineering Research Center for Magnesium Alloys, Chongqing University,
Chongqing 400044, China
Received 12 June 2008; accepted 5 September 2008
Abstract: The production of magnesium alloy sheets normally involves several processing stages including hot rolling, cold rolling and intermediate annealing. The microstructure and texture evolution of AZ31 magnesium alloy sheets in different processing states were investigated by optical microscopy and X-ray diffraction technique. It is found that the microstructure of hot-rolled sheets is dominated by recrystallized equiaxed grains, while that of cold-rolled sheets is dominated by deformation twins. With final annealing applied on the cold-rolled sheets, fine recrystallization grains are obtained and ductility of the samples is increased. It is also found that the texture of magnesium alloy sheets prefers the basal texture, and other compositions of texture are relatively weak. Moreover, final annealing does not significantly affect texture distribution. The results of this study provide useful guidelines for optimizing the processing of magnesium alloys.
Key words: AZ31 magnesium alloy; rolling; microstructure; texture
1 Introduction
Magnesium alloys draw more and more international attention and are regarded as the 21st century metal materials. Compared with casting magnesium alloys, wrought magnesium alloys possess many excellent over-all properties, and are widely used in many areas, such as vehicle, aviation and spaceflight, and electronic communication.
Among the structure parts of engineering, the proportion of the sheets is very high. Especially, a large number of thin-wall covering parts are produced by means of pressing. In order to obtain the high quality pressing products, sheets with excellent mechanical properties and surface quality should be produced first. Unfortunately, being one of hexagonal close-packed (HCP) crystal structure metals, the plasticity of magnesium alloys is so limited at room temperature. Secondly, magnesium alloys have the lowest volume heat capacity[1-2]. Consequently, the velocities of heating and cooling are much quicker than those of other metals. Thirdly, magnesium and its alloys have a narrow range of heat working temperatures. All above brings many difficulties to the processing of magnesium alloy sheets, and restricts the development of processing industry as well as the application of magnesium sheets. For the purpose of improving the deformation properties of AZ31 magnesium alloys and the mechanical properties of the sheets, in this work, the rolling and annealing of the AZ31 magnesium alloys were studied, the optimized rolling and annealing parameters of the alloy sheets were obtained and the mechanical properties of the products were improved, in order to satisfy the application in the structure parts of engineering.
2 Experimental
The samples with dimensions of 40 mm×200 mm ×400 mm were cut from the AZ31 magnesium alloy billets. In order to get homogeneous structures and eliminate microsegregation, the AZ31 magnesium alloy billets were homogenized at 400 ℃ for 15 h, then hot-rolled, warm-rolled and cold-rolled subsequently with pass reduction of 5%-20%. The end products werefinally rolled to 1.0 mm by controlling the reduction of each pass suitably. The sheets were annealed at 260-350℃ for 10-120 min. The mechanical properties of sheets were tested on a WE-1000B universal testing machine. Microstructures of the rolled AZ31 sheets were investigated by optical microscopy. Texture measurements were carried out on a Dmax1400 X-ray diffractometer. Pole figures were constructed using diffracted X-ray intensities measured on {0002},
and
reflections. The main components and sharpness of the textures were evaluated by examining the pole figures.
3 Results and discussion
3.1 Effect of rolling processes on microstructures and mechanical properties of AZ31 alloy sheets
The hot rolling parameters of AZ31 magnesium alloy, including starting temperature 450-460 ℃ of hot rolling, reductions 15%-20% in each pass and finishing rolling temperature 300 ℃, are determined by phase identification, dynamic materials model(DMM), processing maps[3-7] as well as the results of experiments. According to processing parameters mentioned above, the small edge crack and fine surface finishing quality were obtained. However, serious edge cracks, even crazing in the middle of the sheets will appear when the finishing temperature is below 300 ℃ and the pass reduction is above 15%. The microstructure after hot rolling of magnesium alloy sheets is shown in Fig.1(a), from which it can be seen that the recrystallized structures are much more homogeneous and their average grain sizes are 36 μm. It is discovered that there are a great number of twins existing in grains of magnesium alloy sheets (Fig.1(b)), which are deformed at 200-300 ℃ and warm-rolled by 15%, though rolling temperature is not too low. As listed in Table 1, the strength of hot-rolled sheets is lower while the ductility is higher, and the strength is improved by warm rolling at the expense of the decline of the ductility (Table 1).
Although AZ31 magnesium alloys have poor ability of cold rolling, by properly controlling the degree of deformation, using about 5% reduction in each pass, total 25% cold reduction, edge and middle cracks can be avoided. The structure of AZ31 magnesium alloy is “breaking”, especially there is a large deformation at the grain boundary. Therefore, it is easy to have rotting effect and thus cause gullies, meanwhile many twins can be founded at the grain boundary (Fig.1(c)). Cold rolling usually produces work-hardening, high density of dislocation, as a result, the strength increases while ductility decreases obviously (Table 1).
In order to achieve optimal mechanical property, a proper annealing process is needed to eliminate deforma-
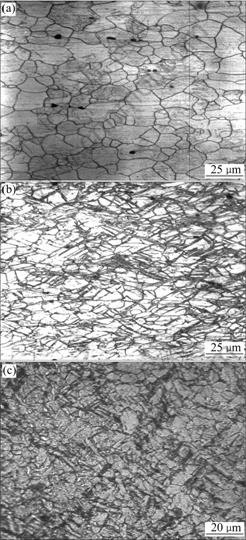
Fig.1 Microstructures of rolled AZ31 sheets under different conditions: (a) Hot rolling; (b) Warm rolling; (c) Cold rolling
Table 1 Representative mechanical properties of AZ31 magnesium alloy sheets
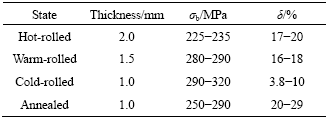
tion structure, and to improve the mechanical properties. Research indicates that when annealing at 260 ℃, the distorted structure increasingly disappears with the time going on. After 60 min, all the distorted structures disappear. The grains are uniformly distributed equiaxed grains with average diameter of 14 μm (Fig.2(a)) and with high mechanical properties. As the annealing time increases, the mean grain size becomes larger. After the annealing time prolongs to 120 min some grains grow
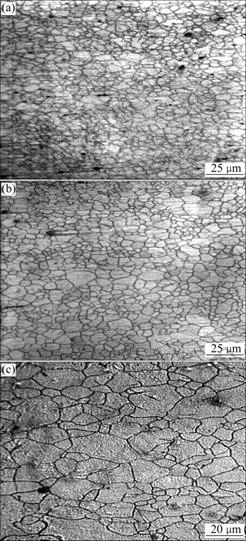
Fig.2 Microstructures and fracture pattern of cold-rolling sheet annealed under different conditions: (a) 260 ℃, 60 min; (b) 260 ℃, 120 min; (c) 350 ℃, 60 min
bigger (Fig.2(b)). When annealing at 350 ℃ for 30 min, all grains are equiaxed, but with different size distributions. If the annealing time increases, some grains grow bigger. After 60 min, the growing becomes faster (Fig.2(c)). After 120 min, the average diameter of grains is 27 μm. The properties decrease a little.
3.2 Texture characteristics of sheet
Fig.3 presents obvious basal plane texture. The {0001} basal plane is aligned with the sheet surface and the peak value direction of pole density is consistent with normal direction(ND). In addition, the ND of basal planes are rotated by approximately 35? toward the ND of sheet surface, while the texture is weak on
and
planes. Fig.4 indicates that the hot-rolled AZ31 magnesium after cold-rolling appears in basal plane texture. In this case the double peaks in the basal
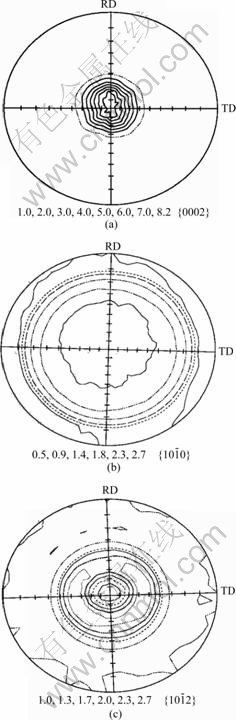
Fig.3 Pole figures of hot-rolled AZ31 sheet
poles are observed. The pole density is in the RD rotated by 18? towards the ND of sheet surface. The ND of basal planes in the RD is rotated by 40? towards the ND of basal planes. While the basal poles are rotated by approximately 35? towards the ND, the texture components in other two crystal planes are a little weak. Heat treatment at 300 ℃ has no significant influence on distribution of texture, and it simply lowers the pole density of basal planes (Fig.5).
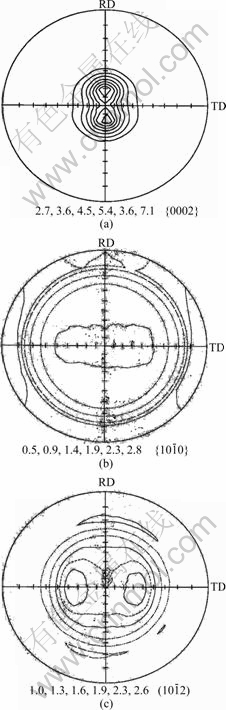
Fig.4 Pole figures of cold-rolled AZ31 sheet
Different textures reflect different deformation mechanisms[8-12]. According to the principle of crystal deformation, the basal plane slip is the reason of basal plane texture in close-packed metal, and the basal plane slip makes the deformed crystal grain rotate in the applied compression stress field and gradually turns the basal plane vertically toward the compressive stress direction, as shown in Fig 3.
HELIS et al[13] and HUANG et al[14] believe that,
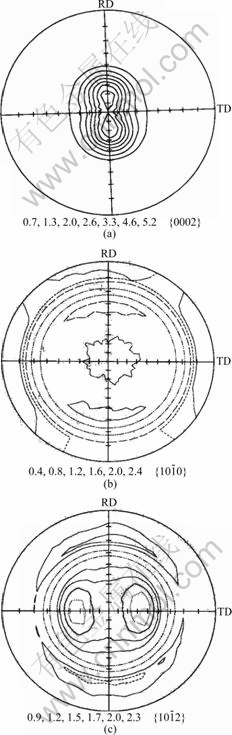
Fig.5 Pole figures of AZ31 sheet heat treated at 300 ℃ for 120 min after cold-rolling
the secondary twinning of
and the basal plane slip occurring in the primary
compressive twins result in the double peak texture in rolling direction. By mathematical simulation, AGNEW et al[15-16] concluded that the texture of double-peak type in rolling direction was obtained by lowering the critical shear stress of slip deformation mode, and the pole density center of its basal plane turned around the sheet transversely toward the rolling direction, so its pole figure was similar to that of the cold rolled sheet. AGNEW et al believed that it was the slip deformation mode that caused the texture characteristics. As shown in Fig.1(c), large quantity of twins play an important role in cold rolling of magnesium alloy.
Generally, it is believed that, at room temperature, the basal plane slip and pyramidal plane
twinning are the main deformation mechanisms of magnesium, while the slip of primatic plane and pyramidal plane is difficult to activate. Therefore, the basal plane slip and twinning of pyramidal plane
are main causes for the basal texture and double-peak pole density of the cold rolled sheet. In the co-effect of the two deformation modes, the pole density turns toward the rolling direction, and the pole figure reflects the double-peak of the pole density, which also proves that twinning contributes greatly in the cold deformation of magnesium alloy.
It is obvious that, during the high temperature and room temperature rolling, there are apparent differences of deformation mechanism, and different texture characteristics are formed under different deformation modes.
4 Conclusions
1) The microstructures of hot-rolled AZ31 sheets are dominated by the uniformly distributed equiaxed grains with diameter of 36 μm, while those of cold-rolled sheets are dominated by twins.
2) With the proper final annealing applied on the cold-rolled AZ31 sheets, fine recrystallization grains are obtained and mechanical properties of σb=250-290 MPa and δ=20%-29% are obtained.
3) The texture of AZ31 sheets prefers basal texture, and other compositions of texture are relatively weak.
4) During hot rolling, the basal plane slip is the main deformation mechanism of magnesium alloy, thus forming a single-peak texture characteristic. However, under cold rolling, both basal plane slip and pyramidal plane
twining are the deformation mechanisms, thus forming a double-peak texture characteristic with its basal plane inclined towards the rolling direction.
References
[1] AVEDESIAN M M, BAKER H. Magnesium and magnesium alloys—ASM speciality handbook [M]. Ohio: ASM International, 1999.
[2] MORDIKE B L, EBERT T. Magnesium properties—applications— potential [J]. Mater Sci Eng A, 2001, A302: 37-45.
[3] PRASAD Y V R K, RAO K P. Processing maps for hot deformation of rolled AZ31 magnesium alloy plate: Anisotropy of hot workability [J]. Mater Sci Eng A,2008, A487: 316-327.
[4] KIM W J, AN C W, KIM Y S, HONG S I. Mechanical properties and microstructures of an AZ61 Mg alloy produced by equal channel angular pressing [J]. Scripta Materialia, 2002, 47: 39-44.
[5] GALIYEV A, KAIBYSHEV R, GOTTSTEIN G. Correlation of plastic deformation and dynamic recrystallization in magnesium alloy ZK60 [J]. Acta Materialia,2001, 49(7): 1199-1207.
[6] BEER A G, BARNETT M R. Microstructure evolution in hot worked and annealed magnesium alloy AZ31 [J]. Mater Sci Eng A, 2008, A485: 318-324.
[7] VESPA G, MACKENZIE L W F, VERMA R, ZARANDI F, ESSADIQI E, YUE S. The influence of the as-hot rolled microstructure on the elevated temperature mechanical properties of magnesium AZ31 sheet [J]. Mater Sci Eng A, 2008, A487: 243-250.
[8] DEL VALLE J A, P?REZ-PRADO M T, RUANO O A. Texture evolution during large-strain hot rolling of the Mg AZ61 alloy [J]. Mater Sci Eng A,2003, A355: 68-78.
[9] JIANG J, GODFREY A, LIU W, LIU Q. Microtexture evolution via deformation twinning and slip during compression of magnesium alloy AZ31 [J]. Mater Sci Eng A, 2008, A 483/484: 576-579.
[10] BARNETT M R, NAVE M D, BETTLES C J. Deformation microstructures and textures of some cold rolled Mg alloys [J]. Mater Sci Eng A, 2004, A386: 205-211.
[11] BOHLEN J, YI S B, SWIOSTEK J, LETZIG D, BRORMFIER H G, KAINER K U. Microstructure and texture development during hydrostatic extrusion of magnesium alloy AZ31 [J]. Scripta Materialia, 2005, 53: 259-264.
[12] AL-SAMMAN T, GOTTSTEIN G. Room temperature formability of a magnesium AZ31 alloy: Examining the role of texture on the deformation mechanisms [J]. Mater Sci Eng A, 2008, A488: 406-414.
[13] HELIS L, OKAYASU K, FUKUTOMI H. Microstructure evolution and texture development during high-temperature uniaxial compression of magnesium alloy AZ31 [J]. Mater Sci Eng A, 2006, A430: 98-103.
[14] HUANG X S, SUZUKI K, WATAZU A, SHIGEMATSU I, SAITO N. Microstructure and texture of Mg-Al-Zn alloy processed by differential speed rolling [J]. Journal of Alloys and Compounds, 2008, 457: 408-412.
[15] AGNEW S R, YOO M H, TOM? C N. Application of texture simulation to understanding mechanical behavior of Mg and solid solution alloys containing Li or Y [J]. Acta Materialia,2001, 49(20): 4277-4289.
[16] JAIN A, AGNEW S R. Modeling the temperature dependent effect of twinning on the behavior of magnesium alloy AZ31B sheet [J]. Mater Sci Eng A, 2007, A462: 29-36.
(Edited by CHEN Wei-ping)
Foundation item: Project(2006BAE04B09-1) supported by the National Key Project of Scientific and Technical Supporting Programs Funded by Ministry of Science and Technology of China
Corresponding author: LIU Qing; Tel: +86-23-65111295; E-mail: qingliu@cqu.edu.cn