J. Cent. South Univ. Technol. (2010) 17: 425-430
DOI: 10.1007/s11771-010-0501-9 
Hot-compression behavior of Al-1Mn-1Mg alloy
ZHANG Xin-ming(张新明), XU Min(徐敏), TANG Jian-guo(唐建国), OU Jun(欧军)
School of Materials Science and Engineering, Central South University, Changsha 410083, China
? Central South University Press and Springer-Verlag Berlin Heidelberg 2010
Abstract: The hot-compression of Al-1Mn-1Mg (mass fraction, %) alloy sample was carried out on a Gleeble-1500 thermo-simulator at deformation temperatures from 320 to 400 ℃ and strain rates from 0.1 to 10 s-1 by total strain of 1.4. Microstructure and texture evolution of the hot-compressed alloy were investigated by optical microscopy and X-ray diffraction analysis, respectively. The results show that the relationship among flow stress σ, deformation temperature T and strain rate
can be expressed in the form of
ln A. The threshold value of ln Z (Z is Zener-Hollomon parameter) characterizing the dynamic recrystallization (DRX) is 46, below which the DRX takes place. A strong P orientation {011}á455? associated with a weak cube orientation {100}á001? is found in the recrystallized sample during hot-compression.
Key words: Al-1Mn-1Mg alloy; hot-compression; dynamic recovery; dynamic recrystallization; texture
1 Introduction
The major problem in the manufacture of Al-1Mn-1Mg alloy sheets used in beverage can body is the occurrence of earing, and its solution is focused on how to obtain a strong cube texture in the hot-rolled strip. During the process of producing Al sheets through modern high-speed hot tandem mill, full recrystallization is expected to take place during coiling of the hot-rolled strip, i.e., the so-called self annealing, so as to develop a favorable amount of the cube texture.
However, the extent of the recrystallization during self-annealing is largely influenced by the recrystallization during hot tandem rolling, which includes inter-stand recrystallization and dynamic recrystallization (DRX). According to ENGLER et al [1], because of the high strains and strain rates with short inter-stand time, the high-speed tandem mills can be run in a process window by which the inter-stand recrystallization can be controlled and thus the recrystallization can be obtained during self-annealing. DRX is known to be controlled by the deformation parameters [2], which can prevent the reduction of the stored energy before self-annealing. A number of research groups have studied the hot deformation process of materials. For example, FANG et al [3] studied the hot compression behavior of Mg-Al-Y-Zn magnesium alloy, directing a reasonable hot working process of this alloy. However, few studies have been reported about Al-1Mg-1Mn alloy concerning the influence of hot compression behavior for guiding its manufacture process. Therefore, it is necessary to have understanding of hot compression behavior of Al-1Mn-1Mg alloy, so as to optimize the deforming parameters for controlling the manufacture procedure and the final properties of the products.
This work is to explore the deformation conditions under which the DRX takes place during hot- compression. The constitutive equation of Al-1Mn-1Mg alloy deformed at elevated temperatures is established and the microstructure and texture evolution during hot deformation are investigated as well.
2 Experimental
2.1 Materials processing
The as-cast material used in this work is Al-1Mn-1Mg produced by laboratory casting. The chemical composition is given in Table 1.
Table 1 Main chemical composition of Al-1Mn-1Mg alloy (mass fraction, %)
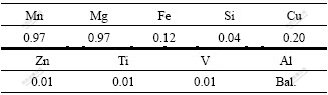
Plain strain compression (PSC) specimens of 25 mm in length, 15 mm in width and 8 mm in thickness were machined from the homogenized material. The PSC
tests were performed on a Gleeble-1500 thermo- simulator in different deformation conditions, i.e., deformation temperatures from 320 to 400 ℃, strain rates from 0.1 to 10 s-1 by the total strain of 1.4. A thermocouple was affixed at the middle of the specimen to measure the instantaneous temperature during compression. Lubricated with graphite in the deformation zone, all specimens were heated to each deformation temperature at the rate of 10 ℃/s, and held for 3 min at the temperature prior to compression. Then, the specimens were water-quenched within 1-2 s after compression, so as to maintain the deformed microstructure at the end of deformation.
2.2 Analysis of microstructure and texture
The microstructure evolution was investigated by using the polarized light in an optical microscope on the hot deformed samples which were underwent electropolishing and anodic oxidation. Micrograph was taken from the longitudinal section, i.e., the elongation direction (ED) and the normal direction (ND) of the samples.
Crystallographic texture measurement was performed on the cross-sectional plane (the elongation direction (ED) and the transverse direction (TD)) of samples by means of X-ray diffractometry, with the applied voltage and current of 40 kV and 40 mA, respectively. Four incomplete pole figures {111}, {200}, {220} and {311} were measured by the Schulz reflection method using Cu Kα radiation, followed by the corrections of defocusing. Orientation distribution functions (ODFs) were subsequently computed with series expansion method from these incomplete pole figures. And two- dimensional ODFs were plotted in the constant φ2 sections with the method proposed by TANG et al [4]. Fig.1 shows the schematic of the deformed sample of PSC.
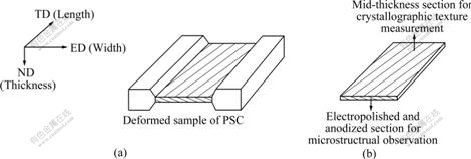
Fig.1 Schematic diagram of deformed sample of PSC (a) and sections used for microstructural observation as well as crystallographic texture measurement (b)
3 Results and discussion
3.1 Constitutive analysis of hot-compression of Al- 1Mn-1Mg alloy
Fig.2 shows the true stress-strain curves of hot compression of Al-1Mn-1Mg alloy at different strain rates and deformation temperatures. It is the typical stress-strain curve of dynamic recovery (DRV) of the plastic metallic material, which is characterized by three stages involving work hardening (WH), transition stage and steady flow stage (see Fig.2(d)). Therefore, conclusions could be drawn that the main softening mechanism in the investigated Al-1Mn-1Mg alloy is DRV. This is consistent with the common understanding of aluminum alloys with high stacking fault energy, in which, both the climb and cross slip of dislocations can be easily developed.
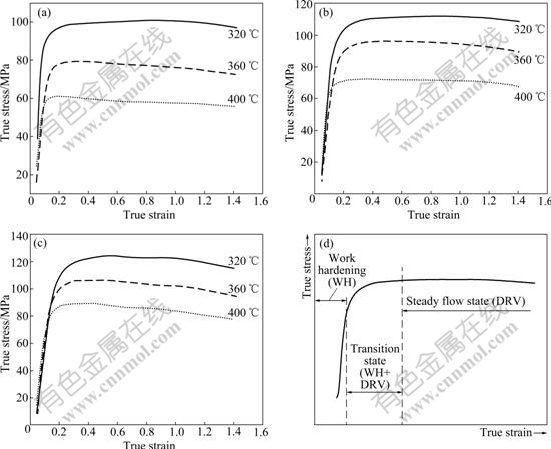
Fig.2 True stress-strain curves of hot-compression of Al-1Mn-1Mg alloy at different strain rates: (a) 0.1 s-1; (b) 1 s-1; (c) 10 s-1; (d) Typical stress-strain curve of DRV
It can be seen from Fig.2 that both deformation temperature and strain rate exert an essential influence on flow stress. The maximum flow stress level decreases with enhancing deformation temperature and decreasing strain rate, because dislocation annihilation and rearrangement are accelerated at high temperature as well as a prolonged time period. This is a prevailing law in hot-deformation of the metallic alloys. For instance, some researchers reached the consistent conclusion by investigating the flow stress behavior of AZ31 magnesium alloy, 7050 aluminum alloy and 42CrMo steel, respectively [5-7].
The constitutive relationship widely used to depict the flow stress behavior at elevated temperatures can be classified into two main types [8]: One is applied to the low stress level with the power law equation,
(1)
The other is applicable to the high stress level which can be given in an exponent type equation,
(2)
where Z is Zener-Hollomon parameter [9],
(3)
where Q is the apparent activation energy for hot- deformation; R is the universal gas constant;
σ and T are strain rate, stress and deformation temperature, respectively; A1, A2, n and β are the material constants.
Substituting Z of Eqs.(1) and (2) with Eq.(3), and taking logarithm of both sides of the developed equations, give
(4)
(5)
The values of n and β are the slopes of the lines for
and
plots, respectively (Fig.3). By means of linear regression analysis, the average values 16.185 and 0.173 MPa-1 of n and β can be obtained (see Table 2) with the relative standard deviation of 39.3% and 9.4%, respectively. Therefore, the constitutive relationship for high stress level describes the flow stress behavior of the hot-compression of Al-1Mn-1Mg alloy more accurately, which is in conformity with the result studied on aluminum alloy by SAMANTA [10].
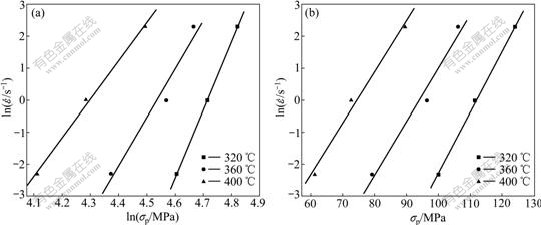
Fig.3 Variation of flow stress of hot compression of Al-1Mn-1Mg alloy with strain rates at true strain of 1.4 and different temperatures: (a) ln
- lnσp; (b) ln
-σp
Table 2 Comparison of values of steady state flow stress (σp) between experimental and calculated results
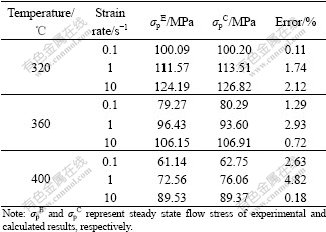
The apparent activation energy Q=268.77 kJ/mol and the material constant A2=1.402×1015 can be derived from the slope and intercept of σp-1/T plots (Fig.4), respectively. Consequently, the constitutive equation of hot-compression of Al-1Mn-1Mg alloy is σ=[ln
+268 770/(RT)-34.877]/0.173.
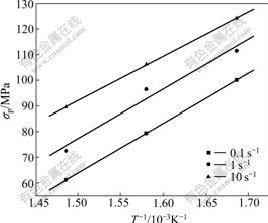
Fig.4 Variation of flow stress of hot-compression of Al-1Mn-1Mg alloy with reciprocal of deformation temperature at different strain rates
3.2 Microstructure and macrotexture evolution of hot-compressed Al-1Mn-1Mg alloy
Fig.5 exhibits the representative microstructures of the hot compressed Al-1Mn-1Mg alloy under different deformed conditions. Typical fibrous microstructure of the hot compressed, characterized by banded structure is observed in all micrographs. As can be seen from Figs.5(a)-(e), no new grains are visualized in the microstructure, indicating that only DRV took place. However, it is interesting that a few new grains appeared in some localized area sandwiched between the deformed bands in Fig.5(f). This suggests that dynamic recrystallization (DRX), in addition to DRV, occurs at deformation temperature of 400 ℃ and strain rate of 0.1 s-1 (T400
0.1). Note that the true stress-strain curve above (Fig.2(a)) demonstrates no clear signs of DRX under the condition of T400
0.1. This can be attributed to the fact that the localized DRX just made a slight contribution to softening during hot deformation, while DRV is still the main softening process.
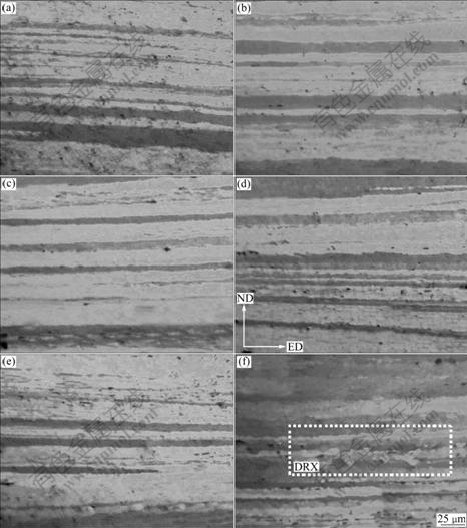
Fig.5 Polarized optical microstructures of Al-1Mn-1Mg alloy under different hot deformation conditions: (a) 320 ℃, 10 s-1; (b) 360 ℃, 10 s-1; (c) 360 ℃, 1 s-1; (d) 360 ℃, 0.1 s-1; (e) 400 ℃, 10 s-1; (f) 400 ℃, 0.1 s-1
Fig.6 shows the ODFs of the Al-1Mn-1Mg alloy sample hot compressed at 400 ℃ with the strain rates of 10 s-1 and 0.1 s-1, respectively. Fig.6(a) represents a prevailing orientation distribution under the deformation conditions corresponding to that in Figs.5(a)-(e). It can be seen from Fig.6(a) that along β fiber, the brass (Bs) {011}á211?, the copper (Cu) {112}á111? and the S {123}á634? components are developed with the peaks located at all those main texture centers. However, the scattering of the Bs orientation along α fiber is observed in Fig.6(b), and the densities of the orientations along β fiber drop obviously by comparing with that of Fig.6(a). Besides, it should be noted that the P orientation {011}á455? and the cube orientation {100}á001? are found in Fig.6(b). It is widely accepted that the cube orientation is a typical recrystallization texture. The P orientation is also considered as a recrystallization texture component during hot deformation of aluminum alloys [11-12]. Therefore, it provides an indication of the occurrence of DRX under T400
0.1, which corresponds with the result observed from the microstructure in Fig.5(f). What is more, it has been reported by LIU et al [11] that the P orientation leads to 30?/60? earing, exhibiting the same earing behavior as deformation textures. It is widely known that the cube orientation with development of 0?/90? earing is the ideal recrystallization texture to balance deformation textures and depress the plane anisotropy in materials, and in turn, improve the property of the final product. In terms of this fact, the P orientation with the characteristic of deformation texture may increase the anisotropy and exert an adverse effect on the reduction of earing.
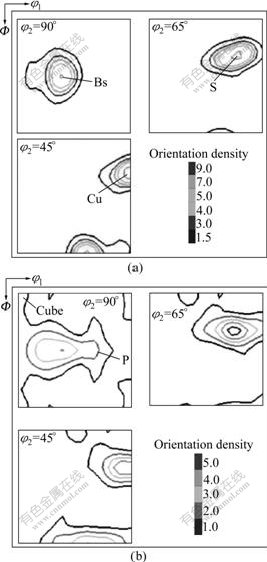
Fig.6 Crystallographic textures of Al-1Mn-1Mg alloy sample under hot-compression at 400 ℃ with different strain rates: (a) 10 s-1; (b) 0.1 s-1
Of particular concern here is that through the microstructure observation and texture analysis, it can be found that at a constant strain rate of 10 s-1, the microstructure hardly varies with the change of deformation temperature. Likewise, at the medium deformation temperature of 360 ℃, no obvious change in microstructure takes place when the strain rate is decreased. Nevertheless, when the temperature goes up to 400 ℃ and the strain rate declines to 0.1 s-1, the occurrence of recrystallization texture is observed. According to this fact, the occurrence of DRX must be related to both the deformation temperature and strain rate, i.e., it connects with the Zener-Hollomon parameter. WANG et al [13] reported that the low Zener-Hollomon condition can accelerate the nucleation and development of DRX grains during hot deformation. With the derived activation energy, it can be calculated from Eq.(3) that the value of ln Z under T400
0.1 is 46, which indicates that the process of DRX occurs during hot compression of Al-1Mn-1Mg alloy when ln Z≤46.
Fig.7 shows the orientation density f(g) along α fiber and β fiber at different deformation temperatures and strain rates, respectively. It is seen on α fiber (Fig.7(a)) that the T400V0.1 produces a much higher density of the P orientation than the other deformation conditions. In addition, it is interesting to note that a slight shift in the density level of the Goss orientation (G) {011}á100? was observed through the occurrence of DRX. This can be explained by the fact that the grains near the G orientation receive a small amount of strain during deformation, leading to a low dislocation density which is not sufficient to drive the process of recrystallization; instead, the process of recovery is apt to occur around the G orientation [14]. As can be seen from Fig.7(b), the maximum density along β fiber is located at an orientation near the S position, and the density of Cu component is higher than that of the Bs component. Furthermore, the orientation densities along β fiber decrease with enhancing deformation temperature as well as decreasing strain rate. This can be considered as another proof that the effect of softening enhances with increasing compression temperature and decreasing compression strain rate.
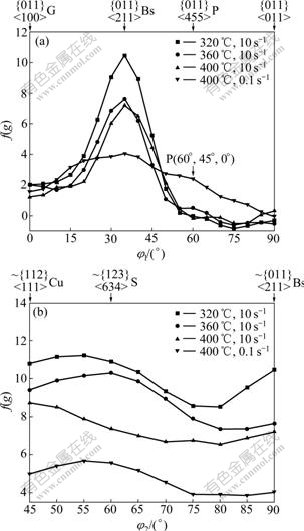
Fig.7 Orientation density along fibers for hot-compression of Al-1Mn-1Mg alloy at different temperatures and strain rates: (a) α fiber; (b) β fiber
4 Conclusions
(1) The constitutive relationship for high stress level can describe well the flow stress behavior of hot-compression of Al-1Mn-1Mg alloy sample, and the constitutive equation σ=
+268 770/(RT)-34.877]/ 0.173 is derived.
(2) The process of DRX takes place when the value of ln Z≤46.
(3) The hot-compression textures are distributed along β fiber with the strongest orientation density located nearly at S position. The occurrence of a high orientation density of P orientation and a weak cube texture are observed in the sample underwent DRX during hot-compression.
References
[1] ENGLER O, LOCHTE L, HIRSCH J. Through-process simulation of texture and properties during the thermomechanical processing of aluminium sheets [J]. Acta Mater, 2007, 55(16): 5449-5463.
[2] HU Zhu-chao, ZHANG De-fen, HUANG Tao, ZUO Liang, WANG Fu. Flow stress behavior and dynamic recrystallization of 3104 aluminum alloy [J]. Mater Mech Eng, 2005, 29(2): 6-9, 20. (in Chinese)
[3] FANG Xi-ya, YI Dan-qing, WANG Bin, WU Chun-ping, ZHANG Hong. Hot compression deformation behavior of the Mg-Al-Y-Zn magnesium alloy [J]. Rare Metals, 2008, 27(2): 121-126.
[4] TANG Jian-guo, ZHANG Xin-ming, DENG Yun-lai, DU Yu-xuan, CHEN Zhi-yong. Texture decomposition with particle swarm optimization method [J]. Comp Mater Sci, 2006, 38(2): 395-399.
[5] CHENG Yong-qi, ZHANG Hui, CHEN Zhen-hua, XIAN Kui-feng. Flow stress equation of AZ31 magnesium alloy sheet during warm tensile deformation [J]. J Mater Process Tech, 2008, 208(1/3): 29- 34.
[6] HU H E, ZHEN L, YANG L, SHAO W Z, ZHANG B Y. Deformation behavior and microstructure evolution of 7050 aluminum alloy during high temperature deformation [J]. Mater Sci Eng A, 2008, 488(1/2): 64-71.
[7] LIN Y C, CHEN M S, ZHONG J. Effect of temperature and strain rate on the compressive deformation behavior of 42CrMo steel [J]. J Mater Process Tech, 2008, 205(1/3): 308-315.
[8] MCQUEEN H J, RYAN N D. Constitutive analysis in hot working [J]. Mater Sci Eng A, 2002, 322(1/2): 43-63.
[9] ZENER C, HOLLOMON J H. Effect of strain-rate upon the plastic flow of steel [J]. J Appl Phys, 1944, 15(1): 22-27.
[10] SAMANTA S K. Dynamic deformation of aluminium and copper at elevated temperatures [J]. J Mech Phys Solids, 1971, 19(3): 117- 135.
[11] LIU J, DICK R E, FRIDY J M, ROUNS T N. Crystallographic texture evolution of continuous cast Al-Mn-Mg alloy sheet during cold rolling and annealing [J]. Mater Sci Eng A, 2007, 458(1/2): 73- 87.
[12] DAALAND O, NES E. Recrystallization texture development in commercial Al-Mn-Mg alloys [J]. Acta Mater, 1996, 44(4): 1413- 1435.
[13] WANG Y, SHAO W Z, ZHEN L, YANG L, ZHANG X M. Flow behavior and microstructures of superalloy 718 during high temperature deformation [J]. Mater Sci Eng A, 2008, 497(1/2): 479- 486.
[14] MAO Wei-min, ZHANG Xin-ming. Quantitative texture analysis of crystalline materials [M]. Beijing: Metallurgical Industry Press, 1995: 127-131 .
Foundation item: Project(2007BAE38B01) supported by National Science and Technology Pillar Program
Received date: 2009-09-07; Accepted date: 2009-12-03
Corresponding author: ZHANG Xin-ming, Professor; Tel: +86-731-88830265; E-mail: xmzhang_cn@yahoo.cn
(Edited by YANG You-ping)