文章编号:1004-0609(2009)11-1934-08
胞状AlCu5Mn合金泡沫的压缩性能和能量吸收特性
杨东辉1,何德坪2,杨上闰3
(1. 河海大学 材料科学与工程学院,南京 210098;
2. 东南大学 材料科学与工程学院,南京 210096;
3. 南京大学 化学化工学院,南京 210093)
摘 要:用熔体发泡法制备孔隙率为51.5%~90.5%、孔结构均匀的胞状铝合金(AlCu5Mn),研究其孔结构、压缩性能、能量吸收能力、能量吸收效率和吸能性能。结果表明:胞状铝合金孔结构由高孔隙率(88.8%)时的大孔径、多边形孔向低孔隙率(62.5%)时的小孔径、球形孔孔结构过渡,其压缩应力(σ)—应变(ε)曲线具有线性变形阶段、屈服平台阶段和致密化阶段三个部分,由线性变形阶段进入屈服平台阶段所对应的εs值介于2%~9%之间;屈服强度σs*随着孔隙率的增大而下降,在孔隙率相同的条件下,胞状铝合金的力学性能优于胞状铝和多孔铝合金,其比刚度高于钢;当应变为定值时,胞状铝合金单位体积和单位质量的压缩吸能能力(C和Cm)都随着孔隙率的升高而降低,但是孔隙率在73.5%~82.1%范围内时,其Cm与ε的关系几乎不随孔隙率的改变而改变;对于孔隙率为51.5%~90.5%的胞状铝合金,它们的吸能效率的峰值都大于80%。胞状铝合金的C—σ和Cm—σ关系可以表征其吸能性能,从而可以根据实际工况选择作为减振吸能材料的胞状铝合金的最佳孔结构。
关键词:胞状铝合金;压缩形变;能量吸收能力;能量吸收效率
中图分类号:TG 146.2 文献标识码:A
Compressive and energy absorption properties of cellular AlCu5Mn alloy foams
YANG Dong-hui1, HE De-ping2, YANG Shang-run3
(1. College of Materials Science and Engineering, HoHai University, Nanjing 210098, China;
2. School of Materials Science and Engineering, Southeast University, Nanjing 210096, China;
3. School of Chemistry and Chemical Engineering, Nanjing University, Nanjing 210093, China)
Abstract: Cellular Al alloy (AlCu5Mn) foams with wide porosity range (51.5%-90.5%) and homogeneous pore structures were fabricated successfully by melting foaming method. The pore structure, compressive property, energy absorption capacity, energy absorption efficiency and the judgment of energy absorption property were investigated. The results show that the pore structure varies from large diameter and polygonal pores for high porosity (88.8%) samples to small diameter and globular pores for low porosity (62.5%) samples. A typical compressive stress(σ)—strain(ε) curve consists of three parts (linear deformation stage, yielding plateau stage and densification stage). The εs values at yielding points are within the range of 2%-9%, and the value of yielding stress σs* decreases with increasing porosity. For a given porosity, the compressive properties are better than those of cellular Al and other Al based foams, and the specific stiffness are higher than those of steel. Both energy absorption capacity per unit volume C and per unit mass Cm decrease with increasing porosity, but the Cm—ε curves for cellular AlCu5Mn foams with porosity of 73.5%-82.1% almost do not alter with increasing porosity. The peak values of the energy absorption efficiencies of cellular AlCu5Mn foams with porosity of 51.5%-90.5% are all greater than 80%. The relationships of C—σ curves and Cm—σ curves can be used to characterize the energy absorption properties, which imply that they can be used as a criterion to choose the pore structure of cellular AlCu5Mn foam as energy absorption material in application.
Key words: cellular Al alloy; compressive deformation; energy absorption capacity; energy absorption efficiency
以孔隙为特征的超轻型金属实现了结构材料的轻质多功能化,其表观密度小,具有高比强度、高比刚度、好的能量吸收、吸声、隔热、电磁屏蔽及多功能兼容性能,在建筑、汽车、船舶、航空航天等民用和军用领域有着广阔的应用前景,因而成为当今的研究热点之一[1-2]。按孔洞的结构分类,超轻型结构金属分为具有闭孔结构的胞状金属(cellular metal) 和具有通孔结构的多孔金属(porous metal)两类。
熔体发泡法[1]具有制备成本低、易操控等优点,因此已成为制备胞状铝/铝合金的主要方法之一。在相同孔结构条件下,胞状铝合金的力学性能优于胞状纯铝,因此,对胞状铝合金的研究已成为当今的研究热点之一。胞状铝合金在受压时,由于其内部含有大量孔洞,所以它具有很大的变形空间和良好的吸能性能。因此,胞状铝合金可以作为防撞击的缓冲材料应用于汽车、航天器、兵器等领域[1-4]。迄今为止,关于高孔隙率(孔隙率>85%)胞状铝和胞状铝合金压缩性能的研究报道较多[5-7],但关于低孔隙率(孔隙率为50%~ 75%)胞状铝合金压缩变形特性的研究报道尚不多见。为此,本文作者采用熔体发泡法,通过调控制备参数,制备了孔隙率范围为50%~90%、孔结构均匀的胞状铝合金[8-12],就孔隙率对胞状铝合金的压缩性能、压缩吸能能力和能量吸收效率的影响以及胞状铝合金吸能性能的综合评判方法进行了研究,为胞状铝合金在实际应用中选择其最佳孔结构提供了依据。
1 实验
1.1 试样制备与实验方法
选用AlCu5Mn铝合金((质量分数)Cu 4.5%~ 5.3%, Mn 0.6~1.0%, Ti 0.15~0.35%, 余量Al)作为基体材料,以氢化钛粉末(40 μm,纯度>99.2%)为发泡 剂,用熔体发泡法[8-12]制备胞状铝合金试样(下文如无特指,铝合金均为AlCu5Mn)。前期的研究工作表 明[8, 10-12]:根据发泡剂氢化钛的热分解特性,通过调控金属熔体的粘度、搅拌发泡和保温发泡时间可以制备出孔结构均匀、孔隙率50%~90%的胞状铝合金。
将胞状铝合金样品线切割成d20 mm×40 mm的压缩试样,试样尺寸需要比孔径大7倍以上,以避免孔洞效应对胞状金属压缩性能的影响[13]。用长春试验机研究所生产的SS-202型电子万能机进行压缩试验,压头下降速率为2 mm/min,由计算机自动绘制出加载压力—位移关系曲线,据此绘制出压缩应力—应变关系曲线。由于压缩试样中的孔洞不能承受压力,基体金属受到的真实应力要比测量到的数值大得多,故将施加于样品上的压力与宏观面积之比称为表观应力,记为σ(以下简称应力)。试样的原始长度为L,压缩时长度方向上的形变量ΔL与L之比称为表观应变,记为ε(以下简称应变)。
1.2 孔结构描述
孔隙率和孔径(D)是描述胞状金属的两个重要参数。所谓孔隙率(P)是胞状材料中气泡所占体积的比例,如式(1)所示:
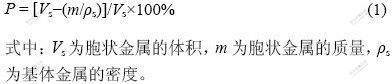
对于孔结构均匀的胞状铝合金,采用图像测量 法[12, 14]获取胞状金属截面的孔洞个数和相对应的孔径大小,计算出所测截面的平均孔径,并以此来表征胞状铝合金的孔径大小。
2 结果与讨论
2.1 胞状铝合金样品
图1所示为胞状铝合金试样和压缩试样的截面形貌,图2所示为对应的胞状铝合金试样的体视显微组织。由图1和2可知,用熔体发泡法可以制备出孔结构均匀的胞状铝合金,且孔隙率高的样品具有大孔径 (D>1 mm)、多边形孔(图1(a),图2(a))的孔结构,孔隙率低的样品具有小孔径(D<1 mm)、球形孔(图1(b),图2(b))的孔结构。
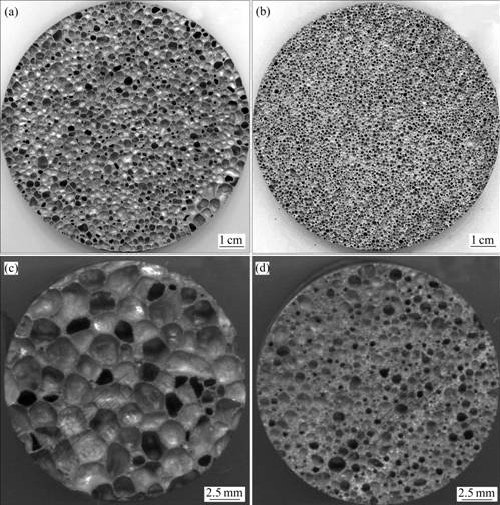
图1 胞状铝合金样品和压缩试样的截面形貌
Fig.1 Section images of cellular AlCu5Mn foam samples: (a) Cellular AlCu5Mn with porosity of 88.8%; (b) Cellular AlCu5Mn with porosity of 62.5%; (c) Sample used for compressive tests with porosity of 87.9%; (d) Sample used for compressive tests with porosity of 72.5%
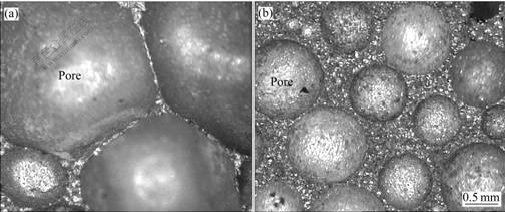
图2 胞状铝合金体视显微形貌
Fig.2 Stereo micrographs of cellular AlCu5Mn foams: (a) Foam sample shown in Fig.1(a); (b) Foam sample shown in Fig.1(b)
2.2 胞状铝合金的σ—ε曲线
图3(a)所示为以2 mm/min的速度对孔隙率为87.9%的胞状铝合金施压时得到的应力(σ)—应变(ε)关系线,该σ—ε关系线可以分为线性变形、屈服平台和致密化3个阶段。图3(a)中的σs*、εs和σD、εD分别表示进入屈服平台阶段和进入致密化阶段时的应力、应变,点(εs, σs*)和点(εD, σD)分别称为屈服点和致密化点。
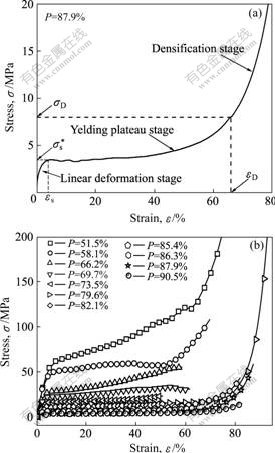
图3 胞状铝合金的压缩应力(σ)—应变(ε)曲线
Fig.3 Compressive stress—strain curves of cellular AlCu5Mn foams at strain rate of 2 mm/min: (a) Typical stress—strain curve; (b) Stress—strain curves with porosity of 51.5%-90.5%
1) 线性变形阶段:在σ—ε曲线上,从原点开始有一段呈直线关系,然后以曲线状向水平方向过渡至屈服点(σs*, εs),一般εs<9%,在此阶段中胞壁承受了所施的压力。
2) 屈服平台阶段:当ε≥εs时,随着应变的增加,应力的增大非常缓慢,σ—ε曲线呈现一个屈服平台,在此阶段气泡孔被压缩变小。
3) 致密化阶段:当ε≥εD时,胞状铝合金的部分胞壁相互接触,压缩曲线进入致密化阶段,应力随着应变的增加而快速增大。
图3(b)所示为P=51.5%~90.5%时胞状铝合金的压缩应力—应变曲线。由图3(b)可知,P不同的胞状铝合金的εs各不相同,相应的σs*也各不相同。
在胞状铝合金的压缩过程中,由线性变形阶段进入屈服平台阶段所对应的εs值和进入致密化阶段所对应的应变εD值可根据图3先求得dσ/dε,然后由dσ/dε—ε曲线确定。图4所示为P=85.4%时胞状铝合金样品的dσ/dε—ε关系曲线。由图4可知,dσ/dε值刚降至0时的ε值为εs,εs所对应的应力即为屈服应力σs*。dσ/dε—ε曲线中的水平线与上升斜线延长线的交点所对应的ε值即为致密化点的应变值εD。
2.3 胞状铝合金的强度和比刚度
用图4所述方法可以确定不同孔隙率胞状铝合金的εs和σs*值,结果如图5所示。由图5可知,胞状铝合金的εs介于2%~9%之间,σs*值随着P的增大总体上呈下降趋势。
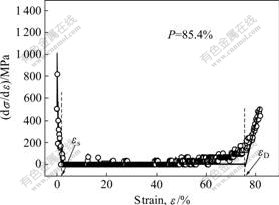
图4 P=85.4%时胞状铝合金样品的dσ/dε与ε的关系
Fig.4 Relationship between dσ/dε and ε for cellular AlCu5Mn foam sample with P=85.4%
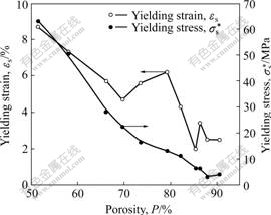
图5 胞状铝合金的εs和σs*值与孔隙率的关系
Fig.5 Relationships of εs—P and σs*—P for cellular AlCu5Mn foams
根据Ashby-Gibson经验公式[13],胞状材料的
和相对密度(ρ/ρs)之间应有如下关系:
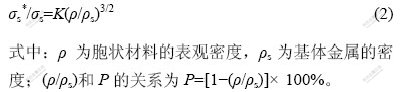
由式(2)可知,σs*与(ρ/ρs)3/2应呈线性关系,根据图5中的数据作胞状铝合金的σs*—(ρ/ρs)3/2直线,其线性相关度为0.986,如图6所示。这表明Ashby-Gibson经验公式对于P=51.5%~90.5%的胞状铝合金均适用。
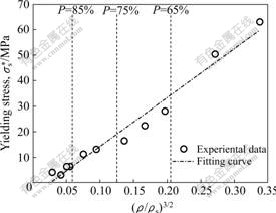
图6 胞状铝合金的σs*与(ρ/ρs)3/2的关系
Fig.6 Relationship between σs* and (ρ/ρs)3/2 for cellular AlCu5Mn foams
图7所示为7种闭孔/通孔结构的泡沫铝/铝合金的σs*—ρ/ρs关系曲线。在图7中除了完整地标出了胞状铝合金泡沫的σs*—ρ/ρs关系外,还标出了胞状铝、多孔铝、多孔铝合金、多孔ZL101铝合金(Si 6.5%~7.5%, Mg 0.25%~0.45%, 余量Al)、多孔ZL111铝合金(Si 8.0%~10.0%, Cu 1.3%~1.8%, Mg 0.4%~ 0.6%, Mn 0.10%~0.35%, Ti 0.10%~0.35%, 余量Al)和多孔ZL205铝合金(Cu 4.6%~5.3%, Mn 0.3%~0.5%, Ti 0.15%~0.35%, Cd 0.15%~0.25%, V 0.05%~0.3%, Zr 0.05%~0.2%, B 0.005%~0.06%, 余量Al)等6种泡沫材料的σs*—ρ/ρs关系曲线。由图7可知,当ρ/ρs一定时,胞状铝合金的强度(σs*)最大,这表明,在P相同的情况下,胞状铝合金具有比胞状铝和其它多孔铝合金更好的力学性能。
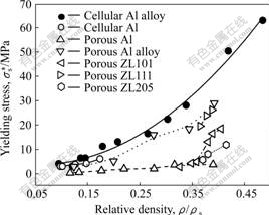
图7 7种闭孔/通孔的泡沫铝/铝合金的σs*与ρ/ρs的关系
Fig.7 Relationships between yielding strength σs* and relative densities ρ/ρs for seven Al alloy foams
对于承受弯曲负载的装置,拟采用比刚度较高的材料,即要求σs2/3/ρ(对梁构件)或σs1/2/ρ(对板构件)的比值较高。表1所列为根据图3和图7中的数据计算获得的胞状铝合金的σs2/3/ρ和σs1/2/ρ值。由表1可知,胞状铝合金的比刚度高,P为51.5%~90.5%时的胞状铝合金的比刚度甚至比钢的还高。
表1 钢和P=51.5%~90.5%的胞状铝合金的比刚度
Table 1 Specific strength of steel and cellular AlCu5Mn foams with P=51.5%-90.5%
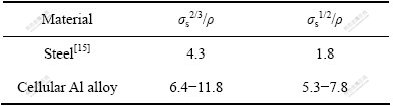
2.4 胞状铝合金的压缩吸能特性
胞状材料的吸能特性通常用单位体积或单位质量吸收的能量(即C或Cm)和吸能效率(e)来表征,它们的计算公式分别为[16-18]
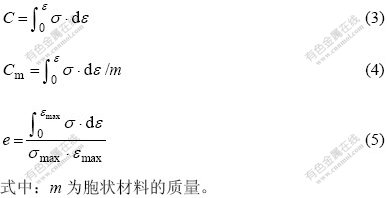
由式(3)可知,吸能能力C等于胞状铝合金压缩应力—应变曲线下的面积;由式(4)可知,Cm等于单位质量胞状铝合金的吸能能力;由式(5)可知,吸能效率e等于真实材料与理想材料压缩到相同应变时,两者吸能本领的比值。C、Cm和e的数值大小可表征胞状金属吸能的优劣。
对图3中的σ—ε曲线进行逐点积分可以获得如图8(a)所示的胞状铝合金的C—ε曲线。由图8(a)可知,当ε为定值时,胞状铝合金的C值随着P的升高而降低。由图8(b)可知,P对Cm—ε有很大影响,当ε为定值时,随着P值的增大,Cm值总体上呈下降趋势;但在P=73.5%~82.1%的范围内,胞状铝合金的Cm—ε关系几乎不随P的改变而改变。

图8 单位体积和单位质量胞状铝合金的能量吸收能力C和Cm与应变ε的关系
Fig.8 Relationships between C(a), Cm(b) and ε for cellular AlCu5Mn foams
图9所示为根据式(5)、图3和图8(a)得出的胞状铝合金的能量吸收效率e与ε的关系。由图9可知,胞状铝合金的吸能效率的峰值都很高,对于P=51.5%~90.5%的胞状铝合金,它们的e的峰值都大于80%。
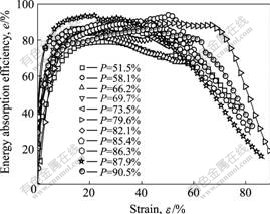
图9 胞状铝合金的能量吸收效率e与应变ε的关系
Fig.9 Relationships between energy absorption efficiency e and strain ε for cellular AlCu5Mn foams
2.5 胞状铝合金吸能性能的综合评判方法
在实际工程应用中,在胞状铝合金作为减振吸能材料时,其任务是通过自身的塑性变形吸收能量,从而使直接作用于被保护对象上的应力衰减到某一个允许的阈值σth之下。此时,胞状铝合金的孔隙率有一个与工况相适应的最佳值。P过大,其吸能能力C过小,外加的能量未被完全吸收,使作用到被保护对象上的应力超过阈值σth,从而导致保护失败;P过小,压缩能量来不及被充分吸收,使作用于被保护对象上的应力超过阈值σth,同样会导致保护失败。一般来说,胞状铝合金作为减振吸能材料时,应力—应变曲线上塑变屈服阶段的应力值应略小于σth,所以胞状铝合金在压缩过程中的吸能能力C随着应力σ的变化曲线,即能量吸收图,是实际工程应用中对不同孔结构的胞状铝合金的吸能性能进行综合评判的重要依据。
图10(a)所示为不同P值的胞状铝合金试样单位体积的吸能能力C与σ的关系。从图10(a)可见,随着应力σ的增大,胞状铝合金的吸能能力C先快速增大,至一肩值(Csh,σsh)后增大速度明显减慢。C—σ曲线用于表征单位体积胞状铝合金在一定应力状态下的能量吸收水平,当被保护对象所能承受的最大应力(阈值σth)大于胞状铝合金的肩值σsh时,被保护对象就能得到有效的减振吸能保护。根据图10(a),将不同孔隙率的胞状铝合金的Csh和σsh值列于表2,由表2可知,σsh和相应的Csh值是随着孔隙率P的增大而减小的。
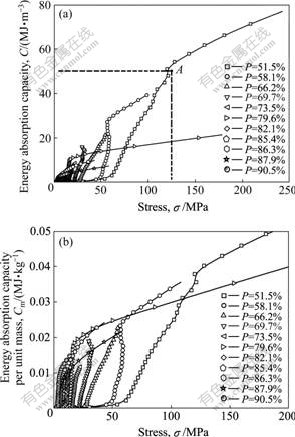
图10 胞状铝合金的吸能能力C、Cm与应力σ的关系
Fig.10 Relationships between C(a), Cm(b) and σ for cellular AlCu5Mn foams
表2 胞状铝合金的的σsh、σm,sh和相应吸能能力Csh、Cm,sh与孔隙率P的关系
Table 2 Relationship among σsh, σm,sh, energy absorption capacity Csh, Cm,sh and porosity P for cellular AlCu5Mn foams
`
图10(b)所示为不同孔隙率P的胞状铝合金试样单位质量的吸能能力Cm与应力σ的关系。从10(b)可见,随着应力σ的增大,胞状铝合金的吸能能力Cm先快速增大,至一定肩值(Cm,sh, σm,sh)后增大速度明显减慢。同样,Cm—σ曲线用于表征单位质量的胞状铝合金在一定应力状态下的能量吸收水平。根据图10(b),将不同孔隙率的胞状铝合金的Cm,sh、σm,sh值列于表2,由表2可知,σm,sh和相应的Cm,sh值是随着孔隙率的增大而减小的。
需要指出的是,表2中孔隙率为90.5%的胞状铝合金的Csh和Cm,sh值高于孔隙率为87.9%的,这可能是由于孔隙率过高的胞状铝合金样品的胞状结构的缺损度有所涨落造成的。
在实际应用中,可以根据实际工况采用上述方法选择作为减振吸能材料的胞状铝合金的最佳孔结构。例如,当被保护对象的状态处于图10(a)中点A处时,其CA=50 MJ/m3, σth=125 MPa。根据上述原则,可以选择孔隙率P=51.5%的胞状铝合金作为减振吸能材料。因为如表1所列,胞状铝合金σsh=119.5 MPa,略小于σth,而Csh=50.85 MJ/m3,略大于CA,所以该胞状铝合金在吸收外加的全部能量后,使到达被保护对象上的应力仍略小于其应力阈值,于是起到了保护作用。
3 结论
1) 用熔体发泡法制备了孔结构均匀、孔隙率P=51.5%~90.5%的胞状铝合金;孔隙率高的胞状铝合金具有大孔径、多边形孔孔结构,而孔隙率低的胞状铝合金具有小孔径、球形孔孔结构。
2) 胞状铝合金的压缩应力—应变曲线具有线性变形阶段、屈服平台阶段和致密化阶段3个部分;对于孔隙率P=51.5%~90.5%的胞状铝合金,εs介于2%~9%之间。
3) 胞状铝合金的屈服强度
随着孔隙率的增大而下降;在孔隙率相同的条件下,胞状铝合金的力学性能优于胞状铝和多孔铝合金;胞状铝合金的比刚度高于钢。
4) 当应变为定值时,单位体积和单位质量的胞状铝合金的压缩吸能能力都随着孔隙率的升高而降低,但是在P=73.5%~82.1%的范围内,胞状铝合金的Cm—ε关系几乎不随孔隙率的改变而改变;对于P=51.5%~90.5%的胞状铝合金,它们的吸能效率的峰值都大于80%。
5) C—σ和Cm—σ关系可以表征胞状铝合金的吸能性能,在根据实际工况选择作为减振吸能材料的胞状铝合金的最佳孔结构时,可以使用它们作为综合评判的依据。
REFERENCES
[1] BANHART J. Manufacture, characterization and application of cellular metals and metal foams[J]. Progress in Materials Science, 2002, 46(6): 559-632.
[2] ASHBY M F, LU Tian-jian. Metal foams: A survey[J]. Science in China Ser B Chemistry, 2003, 46(6): 521-532.
[3] BANHART J. Aluminum foams for lighter vehicles[J]. Int J Vehicle Design, 2005, 37(2/3): 114-125.
[4] 郑 伟, 孙悦年. 泡沫铝在航天工程中的应用展望[J]. 航天器工程, 2001, 10(3): 24-29.
ZHENG Wei, SUN Yue-nian. Al foam application outlook in spacecraft engineering[J]. Spacecraft Engineering, 2001, 10(3): 24-29.
[5] 吴照金, 何德坪. 胞状铝的压缩形变和吸能性能研究[J]. 应用科学学报, 2001, 19(4): 357-361.
WU Zhao-jin, HE De-ping. Research on the deformation and the energy absorption of cellular aluminum under compression[J]. Journal of Applied Science, 2001, 19(4): 357-361.
[6] 郑明军, 何德坪. 新型高比强胞状铝合金的压缩及能量吸收性能[J]. 材料研究学报, 2002, 16(5): 473-478.
ZHENG Min-jun, HE De-ping. Deformation and energy absorption characteristic of high strength cellular Al alloy[J]. Chinese Journal of Materials Research, 2002, 16(5): 473-478.
[7] BANHART J, BAUMEISTER J. Deformation characteristic of metal foams[J]. Journal of Materials Science, 1998, 33(6): 1431-1440.
[8] YANG Dong-hui, HE De-ping, YANG Shang-run. Thermal decomposition kinetics of titanium hydride and Al alloy melt foaming process[J]. Science in China Ser B Chemistry, 2004, 47(6): 512-520.
[9] ZOU Yi, HE De-ping, JIANG Jia-qiao. New type of spherical pore Al alloy foam with low porosity and high strength[J]. Science in China Ser B Chemistry, 2004, 47(5): 407-413.
[10] 杨东辉, 何德坪. 氢化钛热分解特性与小孔径低孔隙率泡沫铝合金[J]. 中国有色金属学报, 2004, 14(12): 2021-2028.
YANG Dong-hui, HE De-ping. Thermal decomposition properties of titanium hydride and Al alloy foam with low porosity and small pore diameter[J]. The Chinese Journal of Nonferrous Metals, 2004, 14(12): 2021-2028.
[11] YANG Dong-hui, HUR Bo-young. The relationship between thermal decomposition properties of titanium hydride and the Al alloy melt foaming process[J]. Materials Letters, 2006, 60: 3635-3641.
[12] YANG Dong-hui, HUR Bo-young, HE De-ping, YANG Shang-run. Effect of decomposition properties of titanium hydride on the foaming process and pore structures of Al alloy melt foam[J]. Mater Sci Eng A, 2007, 445/446: 415-426.
[13] ASHBY M F, EVANS A G, FLECK N A, GIBSON L J, HUTCHINSON J W, WADLEY H N G.. Metal foam: A design guide[M]. Boston: Bhtterworth-Heinemann, 2000.
[14] SONG Zhen-lun, ZHU Jin-song, MA Li-qun, HE De-ping. Evolution of foamed aluminum structure in foaming process[J]. Mater Sci Eng A, 2000, 298(1/2): 137-143.
[15] GIBSON L J, ASHBY M F. Cellular solids: Structure and properties[M]. Oxford: Pergamon Press, 1999: 330.
[16] MILTZ J, GRUENBAUM G. Evaluation of cushion properties of plastic foams compressive measurements[J]. Polymer Engineering Science, 1981, 21(15): 1010-1014.
[17] EVANS A G, HUTCHINSOM J W, ASHBY M F. Multifunctionality of cellular metal systems[J]. Progress in Materials Science, 1998, 43(3): 171-221.
[18] 杨东辉. 氢化钛热分解反应动力学与铝合金熔体泡沫化过程研究[D]. 南京: 东南大学, 2005: 85.
YANG Dong-hui. Thermal decomposition kinetics of titanium hydride and aluminum alloy melt foaming process[D]. Nanjing: Southeast University, 2005: 85.
基金项目:高等学校博士学科点专项研究基金资助项目(新教师基金)(200802941010);河海大学引进高层次人才科研启动基金资助项目(2084140801109);河海大学自然科学基金资助项目(2008428011);国家自然科学重点基金资助项目(50231010);国家自然科学重大基金资助项目(90205005);国家自然科学基金资助项目(50081002,19982001)
收稿日期:2008-11-28;修订日期:2009-04-20
通信作者:杨东辉,副教授,博士;电话:025-83786046;E-mail: donghuiyang@hhu.edu.cn
(编辑 李向群)