J. Cent. South Univ. Technol. (2009) 16: 0892-0896
DOI: 10.1007/s11771-009-0148-6

Flexural strength of zirconia/stainless steel functionally graded materials
LI Jun(李 军), ZHAO Kang(赵 康), TANG Yu-fei(汤玉斐), LI Da-yu(李大玉)
(School of Materials and Engineering, Xi’an University of Technology, Xi’an 710048, China)
Abstract: Zirconia/stainless steel (ZrO2/SUS316L) functionally graded materials (FGMs) were fabricated by tape casting and laminating. Microstructures of FGMs were observed by optical microscope. Fracture behavior of FGMs in different loading modes and influences of different gradient changes on flexural strength were investigated. The results show that ZrO2/ SUS316L FGMs with graded components at interlayers are obtained after they are sintered in vacuum and pressureless condition at 1 350 ℃. TheⅠ-Ⅱ mixed mode crack creates in composite layer and grows to both sides zigzag while loading on ZrO2 layer. Flexural strengths are 496.4, 421.7 and 387.5 MPa when gradient changes are 10%, 15% and 20%, but flexural strengths of the corresponding fracture layers are 387.1, 334.6 and 282.3 MPa since cracks of FGMs are affected by three-dimensional stress, respectively. The cracks are generated in ZrO2 layer and extend to SUS316L layer while loading is added on SUS316L layer, flexural strength does not change with the graded components and keeps consistent basically.
Key words: ZrO2; functionally graded materials; flexural strength; fracture; tape casting
1 Introduction
Defensive quality of armors is facing a severe challenge with the development of counter-armor weapon technology[1]. Armor materials require not only excellent anti-penetration property but also lower density and high specific strength[2-3]. Ceramic/metal composites have recently become a research focus since they can satisfy the requirement of performances. Ceramic/metal armor composites[4-6] are adhesive composites fabricated with ceramic plate and metal plate. Stress concentration, as a result of poor wettability between metal and ceramic in interlayers, however, results in delamination fracture and spalling, and reduces the performances of armor materials. Ceramic/metal functionally graded materials (FGMs)[7-11] with graded components in the thickness direction cannot make failure of physical properties, which can avoid interlaminar stress or scale stress concentrate down. It was reported that the ceramic/metal FGMs displayed higher resistance to crack growth, and had good anti-penetration property as armor materials[12].
Strength and fracture mechanism of FGMs are some of new subjects involving material mechanics[13-14]. ZHANG et al[15-16] investigated fractures on mode Ⅰ crack and mode Ⅱ crack respectively in FGMs by theoretical analysis. NIKHIL et al[17] reported flexural properties of functionally graded syntactic foams. Interesting results were obtained from the referred studies and the flexural strength was testified to be a fine approach to evaluate mechanical properties of FGMs. However, fracture behaviors and flexural strength of metal/ceramic FGMs in different loading modes are seldom reported.
In this work, the zirconia/stainless steel (ZrO2/ SUS316L) FGMs were prepared by tape casting and laminating. Microstructures were observed. Fracture of FGMs in different loading modes and influences of various gradient changes on flexural strength were also investigated.
2 Experimental
2.1 Specimen preparation of FGMs
3%Y2O3-doped partially stabilized zirconia (PSZ, in mole fraction) powder from Nabo Corp., China, was used as ceramic raw material, and stainless steel 316L powder (SUS 316L), from Aisier Corp., China, was used as metal starting material. ACL-B01 organic binder as an additive was used for tape casting[18]. Specimens of FGMs were prepared via the changed component distributed from ZrO2 to SUS 316L, as shown in Fig.1.
The amounts of organic additives for slurries were calculated from those of ZrO2 and SUS316L slurries in proportion to ZrO2 volume fraction. The dispersed slurry was cast onto a base plate and dried slowly in a humid room to avoid generating cracks in the green sheet. Green sheets were stacked into a die and then pressed at 20 MPa and 70 ℃, resulting in a FGMs baked body after burned-out process in furnace (model GSL1600X, China) at 600 ℃. The baked FGMs body was sintered invacuum at about 1 350 ℃ for 3 h.
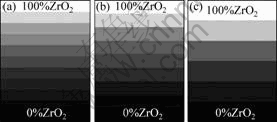
Fig.1 Various components changed of ZrO2: (a) 10%; (b) 15%; (c) 20%
2.2 Characterization
The microstructures and crack propagation paths of the prepared FGMs were examined with an optical microscope (GX71, OLYMPUS, Japan). The flexural strength was studied using three-point bending test by computer servo control material testing machine (HT-2402-100KN, Taiwan, China). The thickness of FGMs was 3 mm, the span was 20 mm and the punch rate was 0.2 mm/min. The flexural strength was tested by two fashions while loading on ZrO2 layer and SUS316L layer, respectively. Loading modes of flexural strength test are shown in Fig.2.
The flexural strength is calculated by the following formula:
(1)
where σf is the flexural strength; P is the maximum load; L is the span length; and h and b are thickness and width of FGMs, respectively.
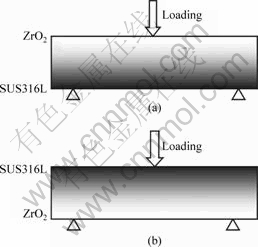
Fig.2 Loading modes of flexural strength test: (a) Loading mode A; (b) Loading mode B
3 Results and discussion
3.1 Microstructure
Microstructures of ZrO2/SUS316L FGMs with various gradient changes are shown in Fig.3. In Fig.3(a), gradient change of FGMs is 10% (volume fraction), and white region represents SUS316L and the black region represents ZrO2. The composition gradually changes from SUS316L layer to ZrO2 layer. The interfaces are eliminated by diffusing components from high concentration to low concentration although the component of ZrO2 or SUS316L with the change contrast of volume fraction of 10% exists in adjacent layers, and the microstructure between layers changes continually. The flaws are not observed in interlayer of FGMs with better bonding. There are some pores in the FGMs sintered under vacuum and pressureless condition. The pores can be removed by pressure sintering[19]. Other gradient changes of FGMs display the similar regularity, as shown in Figs.3(b) and (c). Discontinuity of physical properties at interface can be eliminated due to the diffusion of the component.
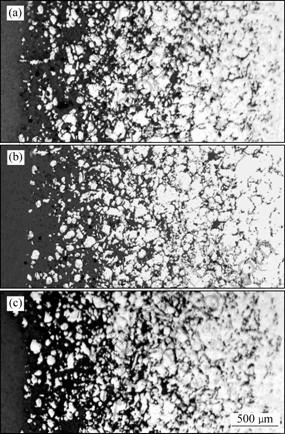
Fig.3 Microstructures of zirconia/SUS316L FGMs with various gradient changes (ZrO2): (a) 10%; (b) 15%; (c) 20%
3.2 Fractures of FGMs in different loading modes
Crack paths of ZrO2/SUS316L FGMs with 20% gradient change for three-point bending experiment are shown in Fig.4. The crack initiation and propagation path are various since graded layers of FGMs with different performances are acted on crack propagation. In Fig.4(a), the crack is created in 20%ZrO2/80%SUS316L composite layer and grows to both-sides in loading mode A. The crack isⅠ-Ⅱ mixed mode crack due to normal stress and shear stress effect. The crack path is polygonal line and the section of FGMs is staggering. It is further found from the observation of crack extension paths that crack deflections improve the fracture work. The destructibility of crack decreases and failure of FGMs is avoided. The result shows a better resistance to crack initiation.
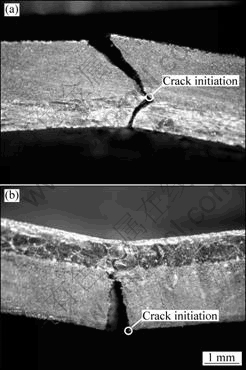
Fig.4 Crack paths of ZrO2/SUS316L FGMs for three-point bending experiment: (a) Loading mode A; (b) Loading mode B
In Fig.4(b), the crack is generated in 100% ZrO2 layer and grows to SUS316L layer. The crack is propagated rapidly, but some deflections are formed with the increase of SUS316L content. This suggests that the SUS316L can prevent the crack from propagating. The delamination fracture phenomenon in interlayer and the crack throughout FGMs along gradient direction like homogeneous materials cannot be observed. Moreover, flaking damaged is generated around crack path because of the joint of inner air hole and microcrack initiated by crack growth.
Diagrams of crack extension of ZrO2/SUS316L FGMs in different loading modes are shown in Fig.5. In Fig.5(a), the crack is created in interlayer in loading mode A. Generally, the crack should be created in SUS316L layer located at the maximum tensile stress. However, elastic deformation occurs in SUS316L layer because of its good ductility. ZrO2/SUS316L composite layer is fractured before SUS316L layer since the ductility of the composite layer is less than that of SUS316L layer while bears tensile stress. And then, crack extends through layers and is deflected in interlayer from crack initiation to ZrO2 and SUS316L, respectively.
The thickness h of FGMs should be modified. The formula of practical flexural strength is as follows:
(2)
where
is the practical flexural strength of FGMs in loading mode A; h′ is the distance from crack initiation to loading point measured by microscopic observation.
In Fig.5(b), on the contrary, the crack is generated in ZrO2 layer and extends to SUS316L layer in loading mode B. The brittle rupture occurs in ZrO2 layer located at the maximum tensile stress since ZrO2 is a typical brittle material. The fracture resistance increases with the crack extending to SUS316L layer that undergoes plastic deformation finally.
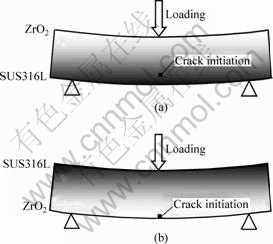
Fig.5 Diagrams of crack extension of ZrO2/SUS316L FGMs: (a) Loading mode A; (b) Loading mode B
3.3 Flexural strength of FGMs
Fig.6 shows the relative displacement with loading when three-point bending test of specimen with 20% graded change is carried out. In Fig.6(a), relative displacement increases with the increase of loading. In SUS316L layer elastic deformation firstly takes place due to its plastic property, and then plastic deformation occurs when relative displacement arrives at 0.235 mm, but no crack initiates. The crack is generated in 20%ZrO2/ 80%SUS316L composite layer when relative displacement arrives at 0.291 mm, and in the SUS316L layer plastic deformation occurs. The crack extends with the increase of loading. The failure of FGMs is accrued when relative displacement arrives at 0.707 mm.
In Fig.6(b), relative displacement increases rapidly with the increase of loading. Abrupt failure of FGMs is produced when relative displacement is 0.047 mm. Because ZrO2 is a typical brittle material the crack is generated in ZrO2 layer and the brittle fracture occurs. The regularity of fracture behaviors with other graded changes is similar to that with graded change of 20%.
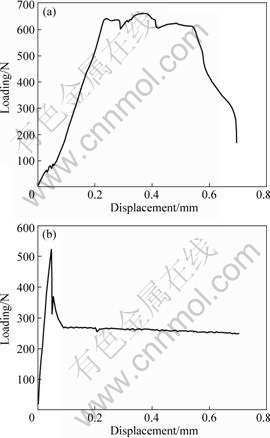
Fig.6 Trial curves of three-point bending test of ZrO2/SUS316L FGMs with 20% graded change: (a) Loading mode A; (b) Loading mode B
The flexural strength of FGMs in loading mode B is calculated according to Eq.(1). And flexural strength of FGMs in loading mode A is obtained by Eq.(2). As shown in Table 1, the flexural strength decreases with the increase of gradient component in loading mode A. The maximum of the flexural strength is 496.4 MPa at gradient component of 10% and the minimum is 387.5 MPa at gradient component of 20%. This is because when SUS316L content of position where crack is generated is higher the flexural strength will increase with the increase of the content of SUS316L and the minor difference in adjacent layers of FGMs. However, the flexural strength basically keeps a constant because all the initiations of cracks are located at ZrO2 layer with various gradient changes. In general, the flexural strength
Table 1 Flexural strength of FGMs when loading on zirconia layer (σ'f) and SUS316L layer (σf)
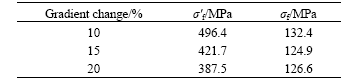
in loading mode B is less than that in loading mode A since strength of ZrO2/SUS316L composites is larger than that of ZrO2.
The position of crack initiation is calibrated by microscopic observation at various gradient changes in loading mode A. The flexural strength of ZrO2/SUS316L composite layer corresponding to the position of producing cracks is calculated according to Eq.(1), and finally the flexural strength of FGMs is compared. As shown in Table 2, the flexural strength of FGMs is larger than that of ZrO2/SUS316L composite layer with component corresponding to the position of crack initiation. The flexural strength of the corresponding fracture layer accounts for 73%-79% of that of FGMs. The crack propagation is affected by three-dimensional stresses: the tensile stress produced by bending test; the shear stress due to different components of gradient layers; and the compression stress of SUS316L layer. Compared with that of ZrO2/SUS316L composite layer, the flexural strength of FGMs is increased. Moreover, ZrO2/SUS316L FGMs have good mechanical properties since they have better wettability between ZrO2 and SUS316L[20].
Table 2 Flexural strength of FGMs when loading on ZrO2 layer (
) and corresponding fracture layer (σ)
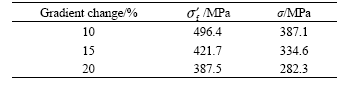
4 Conclusions
(1) Cracks are created in composite layers with volume fraction of ZrO2 being 10%, 15% and 20% respectively in loading mode A and extend to two sides in the form ofⅠ-Ⅱ mixed mode crack.
(2) Flexural strengths of FGMs in loading mode A determined by post-corrective thickness are 387.1, 334.6 and 282.3 MPa with various gradient changes of 10%, 15% and 20%, respectively. Flexural strengths of the corresponding fracture layer are less than those of FGMs since cracks of FGMs are affected by three-dimensional stress.
(3) Cracks are generated in ZrO2 layer and extend to SUS316L layer in loading mode B. Flexural strengths basically keep constant. It is possible to improve the flexural strength by process optimization in the future.
References
[1] MITTEAU R, MISSIAEN J M, BRUSTOLIN P, OZER O, DUROCHER A, RUSET C, LUNGU C P, COURTOIS X, DOMINICY C, MAIER H, GRISOLIA C, PIAZZA G, CHAPPUIS P. Recent developments toward the use of tungsten as armour material in plasma facing components[J]. Fusion Engineering and Design, 2007, 82(15/24): 1700-1705.
[2] SHOKRIEH M M, JAVADPOUR G H. Penetration analysis of a projectile in ceramic composite armor[J]. Composites Structure, 2008, 82(2): 269-276.
[3] MA Bei-yue, YU Jing-kun, LIU Tao, YAN Zheng-guo. Preparation of β-Sialon/ZrN bonded corundum composites from zircon by nitridation[J]. Journal of Central South University of Technology, 2009, 16(5): 725-729.
[4] ANNIKA P, PERNILLA M, PATRIK L, MATS N. Titanium-titanium diboride composites as part of a gradient amour material[J]. International Journal of Impact Engineering, 2005, 32 (1/4): 387-399.
[5] HAN Hui, LI Jun, JIAO Li-juan, LI Nan. Study on the application of ceramic-metal composite materials in bulletproof field[J]. Material Review, 2007, 21(2): 34-37. (in Chinese)
[6] AMIT K C, KIM J H. Interaction integrals for thermal fracture of functionally graded materials[J]. Engineering Fracture Mechanics, 2008, 75(8): 2542-2565.
[7] LOPEZ E S, BARTOLOME J F, PECHARROMAN C, MOYA J S. Zirconia/stainless-steel continuous functionally graded material[J]. Journal of European Ceramics Society, 2002, 22(16): 2799-2804.
[8] TETSURO O, YOSHIMI W, HISASHI S, KIM I, FUKUI Y. Theoretical study on fabrication of functionally graded material with density gradient by a centrifugal solid-particle method[J]. Composites: Part A, 2006, 37(12): 2194-2200.
[9] ZHOU Shi-wei, LI Qing. Micro structural design of connective base cells for functionally graded materials[J]. Materials Letter, 2008, 62(24): 4022-4024.
[10] Heian E M, Gibeling J C, Munir Z A. Synthesis and characterization of Nb5Si3/Nb functionally graded composites[J]. Materials Science and Engineering A, 2004, 368 (1): 168-174.
[11] Put S, Vleugels J, VANDER Biest O. Microstructural engineering of functionally graded materials by electrophoretic deposition[J]. Journal of Materials Processing Technology, 2003, 143(20): 572-577.
[12] LU Yun. Advance composites[M]. Beijing: China Machine Press, 2003. (in Chinese)
[13] GAO X W, ZHANG C, SLADEK J, SLADEK V. Fracture analysis of functionally graded materials by a BEM[J]. Composites Science and Technology, 2008, 68(5): 1209-1215.
[14] HUANG Zi-qian, HE Yue-hui, CAI Hai-tao, WU Cong-hai, XIAO Yi-feng, HUANG Bai-yun. Thermal residual stress analysis of diamond coating on graded cemented carbides[J]. Journal of Central South University of Technology, 2008, 15(2): 165-169.
[15] ZHANG Shao-qin, ZHANG Ke-wei, YANG Wei-yang. Fracture analysis of mode I crack in functional gradient materials[J]. Journal of Taiyuan University of Technology, 2005, 36(4): 173-176. (in Chinese)
[16] ZHANG Shao-qin, ZHANG Ke-wei, YANG Wei-yang. Fracture analysis of mode Ⅱ crack in functional gradient materials[J]. Journal of North University of China: Natural Science, 2006, 27(6): 644-648. (in Chinese)
[17] NIKHIL G, SANDEEP K G, BENJAMIN J M. Analysis of a functionally graded particulate composite under flexural loading conditions[J]. Materials Science and Engineering A, 2008, 485(1/2): 439-447.
[18] ZHAO Kang, LI Jun, TANG Yu-fei, XU Lei. Fabrication and properties of ZrO2/stainless steel functionally graded materials by tape casting[J]. Journal of the Chinese Ceramic Society, 2008, 36(8): 1042-1046. (in Chinese)
[19] ZHANG Wen-quan, XIE Jian-xin, WANG Cong-zeng. Properties of 316L/PSZ composites fabricated by means of extrusion forming and gas-pressure sintering[J]. Materials Science and Engineering A, 2004, 382(1/2): 387-394.
[20] ODEGARD C, BRONSON A. The reactive liquid processing of ceramic-metal composites[J]. Journal of Minerals, 1997, 49(6): 52-54.
(Edited by CHEN Wei-ping)
Foundation item: Project (2007K06-13) supported by the Science and Technique Research and Development Program of Shaanxi Province, China
Received date: 2009-01-22; Accepted date: 2009-06-19
Corresponding author: ZHAO Kang, Professor, PhD; Tel: +86-29-82312601; E-mail: kzhao.xaut@gmail.com