文章编号: 1004-0609(2005)07-1131-08
喷射共沉积7075/SiCp复合材料薄板的轧制成形
张福全, 陈振华, 严红革, 袁武华, 唐绍裘, 傅杰兴
(湖南大学 材料科学与工程学院, 长沙 410082)
摘 要: 研究了轧制方式、 轧制温度等对喷射共沉积7075/SiCp复合材料挤压板材成形性能、 显微组织和力学性能的影响。 结果表明: 挤压变形可以提高7075/SiCp喷射共沉积坯的轧制变形性能, 平行于挤压方向取样并进行交叉轧制可以制备出高质量、 高性能的薄板; 轧制变形对挤压过程中形成的SiC颗粒条带状不均匀分布有显著的改善作用, 随着轧制变形量的增加, SiC颗粒分布趋于均匀; 轧制过程中, SiC颗粒破碎, 尺寸明显变小, 形貌呈钝化趋势; 7075/SiCp复合材料薄板(T6态)的力学性能为: σs=536.2MPa, σb=670.2MPa, δ=4.8%。
关键词: 7075/SiCp复合材料; 喷射共沉积; 轧制; 薄板 中图分类号: TG335.8; TG113.25
文献标识码: A
Rolling processing of spray co-deposition 7075/SiCp composite
ZHANG Fu-quan, CHEN Zhen-hua, YAN Hong-ge, YUAN Wu-hua, TANG Shao-qiu, FU Jie-xing
(School of Materials Science and Engineering, Hunan University, Changsha 410082, China)
Abstract: The effects of rolling processing on the formability, microstructure and mechanical properties of the as-extruded spray co-deposited 7075/SiCp composite were investigated. The results show that the extruded thick sheet exhibits excellent formability along the extrusion direction. Cross rolling processing can enhance the formability and mechanical properties of the 7075/SiCp sheet. The rolling processing leads to the refinement of SiC particles and the distribution state. Furthermore, the optimal properties of the sheet are: yield strength 536.2MPa, ultimate tensile strength 670.2MPa, and elongation 4.8%, respectively.
Key words: 7075/SiCp composite; spray co-deposition; rolling process; sheet
陶瓷颗粒增强铝基复合材料薄板因具有密度低、 比强度及比模量高、 抗蠕变、 耐磨损、 可控膨胀系数等一系列优点, 被广泛应用在航天、 航空、 汽车、 兵器、 体育等重要领域, 且成本较纤维增强铝基复合材料低廉, 成为近年来高技术新材料研究开发的重要领域[1-4]。
目前颗粒增强铝基复合材料的研究主要集中在材料制备、 力学性能、 微观组织结构等方面, 且所研究使用的材料多为挤压态, 而对轧制态复合材料薄板的研究较少, 因此, 开展颗粒增强铝基复合材料薄板制备工艺的研究具有很重要的理论意义和实际应用价值。 但复合材料薄板的制备难度很大[5-9], 首先需要制备晶粒组织微细、 SiC颗粒分布均匀的复合材料坯料, 其次轧制工艺对复合材料薄板的成形性能和组织、 力学性能有重要影响。 目前颗粒增强铝基复合材料坯料的制备方法主要有搅拌铸造法、 粉末冶金法、 喷射共沉积法等。 若采用搅拌铸造法制备复合材料坯料, 则存在基体合金晶粒组织粗大、 成分偏析严重、 陶瓷颗粒与基体之间容易发生有害界面反应等缺点; 采用粉末冶金技术制备复合材料坯料则成本过高, 且难以制备大尺寸坯料。 采用喷射共沉积技术制备此类复合材料则具有沉积坯冷速高、 合金晶粒组织微细、 组织成分均匀、 无成分偏析、 容易制备大尺寸坯料等优点, 近年来的研究表明该方法是制备高性能金属基复合材料的理想方法之一[10]。 本文作者采用自行研制的坩埚移动式喷射共沉积装置制备了d650mm×800mm的复合材料圆柱锭坯, 再轧制成厚度为1.0~1.2mm的薄板。 研究轧制工艺对复合材料薄板成形性及其组织、 力学性能的影响。
1 实验
实验材料采用7075/SiCp复合材料, 基体合金成分组成列于表1。 增强相为15%(质量分数)的SiC颗粒, 颗粒尺寸大小为1~10μm。 采用本研究所自行研制的坩埚移动式喷射共沉积装置制备复合材料, 工艺参数见表2。
表1 7075铝合金的化学成分
Table 1 Chemical composition of 7075 aluminium alloy(mass fraction, %)
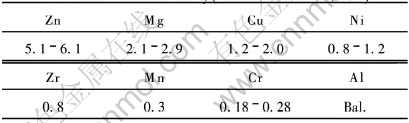
表2 喷射共沉积工艺参数
Table 2 Processing parameters of spray co-deposition
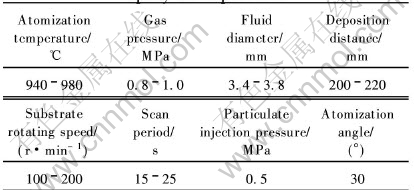
圆柱锭坯的直径为d650mm, 高500~800mm。 挤压前车削成直径d630mm的坯料。 热挤压实验在西南铝加工厂的1250MN挤压机上进行, 挤压筒内径为d650 mm。 挤压模具内尺寸为330mm×125mm, 挤压比λ=8.0。 挤压时锭坯的加热温度为420~440℃, 保温时间为8h; 挤压筒加热温度为430℃, 挤压速度为0.2~0.5m/min, 并视挤压情况进行调节。
薄板轧制实验在d360mm×600mm双辊热轧机上进行。 从挤压厚板上取样, 在刨床上刨成厚度为10mm的小块进行多道次热轧。 按照双辊热轧机上板材轧制方向与挤压方向的关系, 自行定义了3种轧制方式, 即平行于挤压方向送料为纵轧方式, 垂直于挤压方向送料为横轧方式, 在平行和垂直于挤压方向上交替进行的轧制方式为交叉轧制方式。
热轧总变形量ε控制在80%左右。 道次压下量的合理控制是热轧工艺顺利进行的关键。 在前2~3道次中, 道次压下量应控制在10%以下, 7%~8%较为合适。 当ε>30%后, 道次压下量可达10%~20%, 以尽量减少热轧道次及道次间的退火时间。 当ε>80%后, 可进行冷轧。 由于材料的强度较大, 塑性较小, 故冷轧道次压下量控制在5%~10%之间, 每压下一定厚度, 应反复轧制多次以实现压下。 可视具体工艺过程确定是否进行冷轧间的退火, 以消除加工硬化提高材料的塑性。 轧速为0.43m/s(实验过程中轧制速度为恒定值), 热轧前加热温度为350~470℃, 保温时间为120min。 道次间退火温度为415℃, 保温时间为30min。 热轧采用乳液润滑, 冷轧采用煤油添加油酸润滑。
在Leitz MM6卧式金相显微镜和H-800电镜上进行微观组织结构观察, 在WDW-200微机控制电子万能试验机上进行拉伸实验, 拉伸速度为1mm/min。
2 结果与讨论
2.1 喷射共沉积坯及挤压板材的组织特点
图1所示为喷射共沉积7075/SiCp复合材料锭坯的照片, 图2所示为沉积坯的金相组织照片。 由图2可见, 沉积坯中晶粒组织微细、 SiC颗粒分布均匀, 无明显的团聚现象, 但在大的SiC颗粒与基 [CM(22]体结合处存在一定数量的孔洞。 由于沉积时SiC颗粒的捕获既有液相捕获, 也有固相捕获, 导致部分[CM)] SiC颗粒与基体的界面是机械结合界面。 该复合材料沉积坯的相对密度为88.9%。
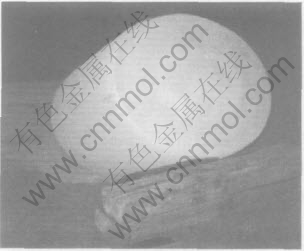
图1 7075/SiCp沉积坯的照片
Fig.1 Photograph of 7075/SiCp composite
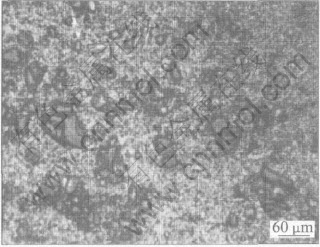
图2 7075/SiCp沉积坯的显微组织照片
Fig.2 Optical microstructure of as-deposited 7075/SiCp composite
图3所示为沉积坯挤压厚板材及其典型显微组织照片, 可见挤压态材料基本保持了喷射共沉积坯细小的晶粒组织, 最明显的组织特征是SiC颗粒沿挤压流线分布, SiC颗粒仍未发生团聚现象, 挤压流变应力不足以使SiC发生断裂。 沉积坯挤压变形基本上可以分为两个阶段: 致密化阶段和塑性变形阶段。 多孔坯的致密化包括: 增加SiC颗粒与基体合金之间的接触面积, 孔隙压缩变形破裂, 材料挤入孔隙。 在挤压变形区, 孔隙同时受到静水压力和剪切应力的作用, 静水压力使孔洞压缩, 剪切变形作用使孔隙拉长和闭合, 孔隙体积可通过弹性变形和塑性变形方式减小[11]。 变形区的这种应力应变状态对沉积坯中孔洞的愈合非常有利, 经过密度测试, 挤压后材料致密度达到97.5%。 挤压实验表明喷射共沉积复合材料坯经过挤压加工后, 沉积坯件中的孔洞基本消失。
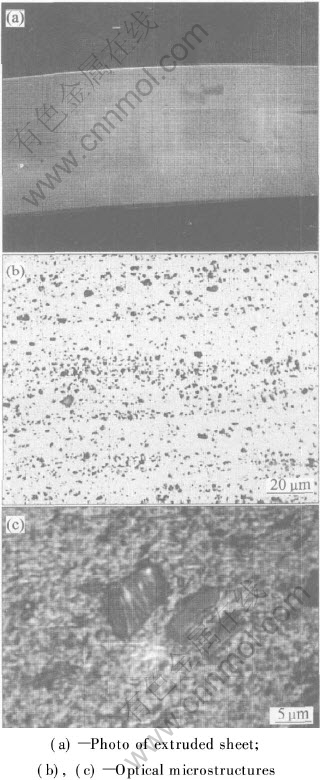
图3 7075/SiCp挤压板料照片及其典型显微组织
Fig.3 Photo of 7075/SiCp composite extruded sheet and typically optical microstructures
喷射沉积圆锭坯经过挤压可以获得良好的冶金结合, 一个原因是挤压时具有的三向压应力状态; 另一原因则为热挤压过程中的摩擦力分解出一个剪应力分力, 使SiC颗粒与基体合金晶粒发生剪切, 破坏颗粒和晶粒表面存在的微弱氧化膜, 促进SiC颗粒与基体合金晶粒之间的粘结。 由此可见, 剪应力对于复合材料沉积坯获得良好的冶金结合有着积极作用[11]。
2.2 喷射共沉积坯直接轧制时材料的成形性能
实验研究了从沉积坯上取样直接轧制板材的成形性能。 实验发现, 尽管道次压下量仅5%, 但板材表面开裂现象非常严重。 这主要是由于喷射共沉积7075/SiCp复合材料属于多孔体, 沉积坯中存在孔洞, 颗粒和晶粒表面存在微弱的氧化膜, 颗粒与基体合金之间没有达到冶金结合, 故塑性变形性能很差。 这种沉积坯料若直接进行轧制, 虽然轧制时坯料受到三向压应力, 但沿轧制方向压应力很小, 容易产生裂纹。 由此可见, 对喷射沉积坯直接采用轧制加工, 成形过程具有很大的难度。
沉积坯挤压变形后再进行轧制, 实验研究发现: 挤压厚板材的轧制成形性能大幅度提高。 实验还发现平行于挤压方向取样进行轧制有利于板料的成形, 且材料的成形率较高。 这是由于挤压变形后, 材料致密度大幅度提高, SiC颗粒与基体合金之间的结合状况明显改善, 因此, 挤压厚板材的塑性变形性能显著提高。 此外, 采用挤压方法制备的复合材料厚板存在明显的方向性, 即材料在平行于挤压方向和垂直于挤压方向上的组织和性能差别很大, 导致不同方向材料的轧制成形性能存在明显差异。
2.3 轧制方式对材料成形性能和力学性能的影响
采用不同轧制方式轧制的板材如图4所示。 实验发现, 横轧与纵轧板材在各道次均存在不同程度的边裂现象, 但采用交叉轧制时, 总变形量达到51.5%也没有出现明显的边裂和表面裂纹, 这表明交叉轧制方式可以显著提高复合材料的塑性成形性能。
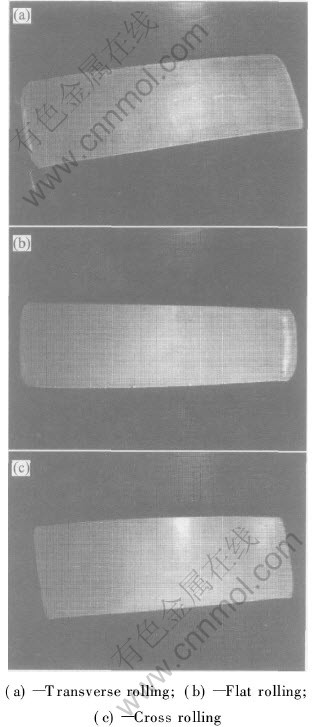
图4 采用不同轧制方式轧制的板材
Fig.4 7075/SiCp composite rolled sheets under different rolling methods
表3所列为410℃时, 采用不同轧制方式轧制的薄板经T6热处理后(460℃、 20min淬火+120℃、 20h)的力学性能实验结果。 由表可见, 纵向轧制板材的力学性能明显优于横向轧制板材的, 而采用交叉轧制方法制备的板材的力学性能最高, 这表明交叉轧制工艺可以显著提高复合材料薄板的力学性能。
表3 不同轧制方式轧制板材的力学性能
Table 3 Mechanical properties of 7075/SiCp composite sheets under different rolling methods
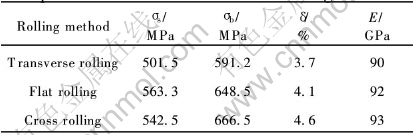
如前所述, 挤压后材料致密度为97.5%, 轧制加工时, 材料变形过程大致可分为致密化与塑性变形两个阶段。 在致密化阶段由于存在孔隙, 材料对拉应力敏感极易出现表面横裂。 板坯在热轧的前几个道次中, 由于材料存在孔隙, SiC颗粒与基体合金之间的冶金结合状态不够理想, 而轧制过程的三向压应力在纵向上相对较小、 材料在纵向上的流动较大, 因此垂直于轧制方向的横向成为相对的弱结合面, 轧制过程中板坯易形成表面横向裂纹。 如果在微裂纹扩展之前改变轧制方向即采用交叉轧制, 则可有效地抑制裂纹的进一步长大与宏观扩展。 交叉轧制的作用可归纳如下: 1)轧制过程中, 在轧制压应力及颗粒(晶粒)流动时相互间存在的摩擦剪切应力作用下, SiC颗粒和基体合金晶粒表面的氧化膜发生破碎并重新分布。 交叉轧制可以使氧化膜在两个垂直的方向得到充分破碎, 而不是只沿一个方向破碎并排列, 从而减小了氧化物破碎与碎片分布的方向性, 也可促使SiC颗粒与基体合金在各个方向均获得良好的冶金结合; 2) 交叉轧制使塑性变形过程容易实现; 3)交叉轧制使颗粒(晶粒)均匀化和等轴化, 降低各向异性、 改善板材性能。 此外, 交叉轧制后板材的SiC颗粒分布情况较好, 也有利于改善板材的成形性能, 提高板材的力学性能。
在轧制过程中, 影响板材成形性及其组织性能的工艺参数有轧制道次变形量、 轧制温度、 轧制速度等, 其中道次变形量是关键参数[12]。 本实验中7075/SiCp复合材料的相对密度为97.5%, 对于这种非致密材料, 在轧制过程中宜采用小变形量、 多道次轧制工艺, 特别是要控制第一到第三道次的压下量, 才可有效的避免材料开裂, 提高板材的成形性能。
2.4 轧制温度对材料成形性能和力学性能的影响
实验选择了350、 390、 410、 430、 470℃等5个轧制温度进行交叉轧制, 轧速为0.43m/s, 采用基本相同的道次变形量轧制成厚度为1.0~1.2mm的薄板。 实验研究发现: 在350~470℃温度之间, 板材的轧制成形性能没有明显的差异。 对薄板进行T6热处理, 其室温拉伸性能如表4所示。 结果表明, 轧制温度为410~430℃时板材的力学性能明显高于其它温度下的数据。
表4 轧制温度对板材力学性能的影响
Table 4 Mechanical properties of 7075/SiCp composite sheets under different rolling temperatures

轧制能否顺利进行, 关键在于轧制温度的确定。 开轧温度对金属的塑性变形性能有较大影响, 而终轧温度直接影响产品的组织与性能。 因此轧制温度的选择十分重要。 要确定合理的温度制度, 通常需综合考虑合金相图、 塑性图、 变形抗力图及再结晶图等。 根据合金状态图可以确定轧制温度范围; 而合金的塑性图可以作为轧制温度选择的主要依据; 变形抗力图及再结晶图作为控制轧制品的组织和性能的参考[12]。
7075合金的最佳塑性变形温度范围为350~470℃, 因此在该温度范围进行轧制, 材料的成形性能没有明显的差异。 材料的力学性能是由其微观组织特征决定的。 具体来说, 轧制后7075合金板材的力学性能主要受合金晶粒度、 晶粒尺寸分布、 晶粒取向等的综合影响。 轧制温度对板材性能的影响, 其实质是通过轧制时的塑性变形机制和动态再结晶过程来左右板材的最终组织, 并成为决定板材性能最重要的因素。 当轧制温度过低时, 不能通过动态再结晶细化晶粒, 粗大晶粒组织中会存在大量的孪晶; 在再结晶温度以上进行热轧时, 可通过形成细小的新晶粒而使平均晶粒尺寸下降, 提高其综合力学性能; 而当轧制温度过高时, 有可能发生二次再结晶导致晶粒长大, 使材料的综合力学性能下降。 尤其在较高轧制速度条件下, 材料内部会形成局部剪切变形带而促使裂纹的萌生和扩展。
7075/SiCp复合材料板材的力学性能除与基体合金的塑性变形机制和动态再结晶过程有关之外, 还与SiC颗粒在轧制过程中的变化有关。 复合材料中增强体颗粒的质量分数、 形状、 大小、 特别是增强体颗粒的分布及其与基体的结合状况等对材料内载荷的传递、 应力应变分布以及其物理、 力学性能都有着极为重要的作用和影响[6, 13, 14]。 因此, 塑性加工过程中, 增强体颗粒的分布及其与基体的结合情况等是影响基体和增强体性能能否充分发挥、 形成最佳复合效果的关键。
轧制加工过程中, SiC颗粒破碎, SiC颗粒形貌及其分布状态的变化必然影响材料的力学性能。 在本实验中, 经过各道次轧制后SiC颗粒尺寸明显减小, 形貌钝化、 圆角化, 随着轧制变形量的增加, SiC颗粒的不均匀分布现象有所改善, 这些因素都有利于提高复合材料板材的力学性能。 但是, 在SiC颗粒破碎的同时, 如果没有基体金属填充SiC颗粒破碎形成的孔隙间, 则会在材料中形成内部缺陷, 使材料强度下降。 轧制温度较高时, 基体金属流动性好, 能够充填到SiC颗粒破碎形成的间隙中去, 改善SiC颗粒与基体的结合状况, 使材料的力学性能提高, 而当轧制温度进一步升高时, 基体合金晶粒尺寸明显长大, 反而使板材的力学性能下降。
2.5 轧制加工对7075/SiCp复合材料组织的影响
2.5.1 SiC颗粒的分布特征
图5所示为垂直于板面方向取样、 不同轧制压下量时SiC颗粒的分布状态。 由图发现, 随着轧制变形量的增加, 挤压时形成的明暗相间的SiC颗粒条带逐渐变窄, 即SiC颗粒密集层与SiC颗粒较少层之间的层间距逐渐减小, SiC颗粒分布趋于均匀, 明暗条带区域的界面不明显。
轧制对挤压过程形成的SiC颗粒的不均匀分布具有一定的改善作用。 随着变形量的增加, SiC颗粒层状分布现象有所改善, 但轧制并不能完全改变挤压时形成的SiC颗粒的条带分布状态。
2.5.2 轧制变形对SiC颗粒尺寸的影响
图6所示为7075/SiCp复合材料中SiC颗粒的微观形貌。 由于目前工业使用的SiC颗粒均为机械破碎方法制备, SiC颗粒带有明显的尖角, 这从图6(a)的喷射共沉积复合材料坯组织可以清楚看到; 而从图6(b)可以发现, 经过挤压后, SiC颗粒形貌有一定的钝化、 圆角化倾向; 经过大变形量的轧制后, 大SiC颗粒破碎变成多个小的SiC颗粒, SiC颗粒的平均粒度明显变小, 同时SiC颗粒形貌已经明显圆角化, 没有条状、 尖角状SiC颗粒存在。 在剪切应力作用下, 大颗粒发生破裂。
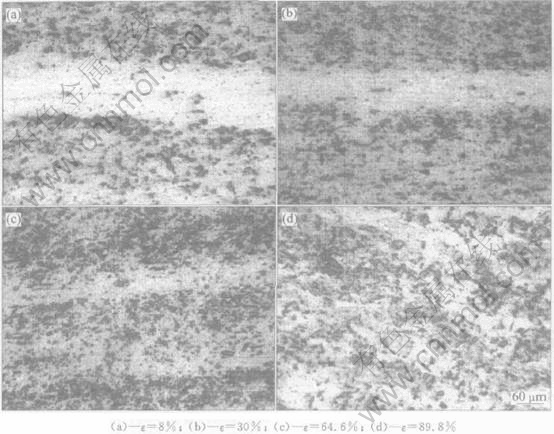
图5 变形程度对颗粒分布的影响
Fig.5 Effect of deformation levels on SiC particles distribution

图6 7075/SiCp复合材料中SiC颗粒的微观形貌
Fig.6 SEM images of SiC particles in 7075/SiCp composite
复合材料的高温塑性变形是通过基体的塑性变形来实现的。 SiC颗粒对基体的变形有明显的阻碍作用, 那些严重阻碍基体滑移的SiC颗粒, 即长径比较大且排列方向与基体滑移方向不一致的SiC颗粒受到基体变形产生的垂直于SiC颗粒长轴方向剪切力的作用。 如果剪应力足够大时引起SiC颗粒的断裂, 同时SiC颗粒也可随基体变形作相应的流动, 并适当调整自己的方位, 以利于基体材料的塑性变形。 塑性成形特别是高温轧制成形可以细化SiC颗粒, 减小或消除材料内部存在的孔洞缺陷, 使增强体分布均匀[9, 15]。
如果轧制温度选择合适, 基体金属流动性好, 能够充填到大的SiC颗粒破碎形成的间隙中去, 并改善SiC颗粒与基体的结合状况, 则会使复合材料板材的力学性能提高。
3 结论
1) 挤压变形可以提高7075/SiCp喷射共沉积坯的轧制变形性能, 平行于挤压方向取样并进行交叉轧制可以制备出高质量、 高性能的薄板。
2) 轧制变形对挤压过程中形成的SiC颗粒条带状不均匀分布有显著的改善作用。 随着轧制变形量的增加, SiC颗粒分布趋于均匀; 轧制加工过程中, SiC颗粒破碎, 尺寸明显变小, 形貌有钝化趋势。
3) 7075/SiCp复合材料薄板(T6态)的最佳力学性能为: σs=536.2MPa, σb=670.2MPa, δ=4.8%。
REFERENCES
[1] 崔 岩. 碳化硅颗粒增强铝基复合材料的航空航天应用[J]. 材料工程, 2002, 6: 3-6.
CUI Yan. Aerospace application of silicon carbide particulate reinforced aluminium matrix composites[J].Material Engineering, 2002, 6: 3-6.
[2] Miller W S, Zhuang L, Bottenm J, et al. Recent development in aluminum alloy for the automotive industry[J]. Mater Sci Eng A, 2000, 280(1): 37-49.
[3] Rakand H J, Hiskanen P W. Deformation structures and flow stress in aluniminum containing short whisker[J]. Light Metal Age, 1984(2): 223-226.
[4]Ibrahim I A, Mohamed F A, Lavernia E J, et al. Particulate reinforced metal matrix composites—a review[J]. J of Mater Sci, 1991, 26: 1137-1155.
[5] 胡 明, 费维栋, 姚忠凯, 等. 非连续增强金属基复合材料的变形形为[J]. 宇航材料工艺, 2001, 1: 10-14.
HU Ming, FEI Wei-dong, YAO Zhong-kai, et al. Deformation behavior of discontinuous reinforced metal matrix composite[J]. Space Material Technics, 2001, 1: 10-14.
[6] 胡代忠, 陈礼清, 赵明久, 等. SiC颗粒增强铝基复合材料薄板的力学性能[J]. 中国有色金属学报, 2000, 10(6): 827-831.
HU Dai-zhong, CHEN Li-qing, ZHAO Ming-jiu, et al. Mechanical properties of SiC particulate-reinforced aluminium matrix composite sheets[J]. The Chinese Journal of Nonferrous Metals, 2000, 10(6): 827-831.
[7] 赵明久, 肖伯律, 刘 越, 等. 碳化硅颗粒增强铝基复合材料(SiCp/2024Al)的热变形行为[J]. 中国有色金属学报, 2002, 12(S1): 137-140.
ZHAO Ming-jin, XIAO Bo-lu, LIU Yue, et al. Hot deformation behavior of silicon carbon particulate reinforced 2024 aluminium composite[J]. The Chinese Journal of Nonferrous Metals, 2002, 12(S1): 137-140.
[8] 陈礼清, 吕毓雄, 毕 敬. SiCp增强铝基复合板材力学性能与晶粒取向分布[J].金属学报, 1998, 34(11): 1183-1187.
CHEN LI-qing, L Yu-xiong, BI jing. Mechanical properties and crystallite orientation distribution SiCp reinforced aluminium matrix composite sheets[J]. Acta Matall Sin, 1998, 34(11): 1183-1187.
[9] 郭 成, 程 宇, 尚春阳, 等. SiC颗粒增强铝合金基复合材料断裂与强化机理[J].复合材料学报, 2001, 18(4): 54-57.
GUO Cheng, CHENG Yu, SHANG Chun-yang, et al. Mechanism on fracture and strengthening of aluminium alloy matrix composites reinforced with SiC particles[J]. Acta Materiae Composites Sinica, 2001, 18(4): 54-57.
[10] 陈振华, 陈 鼎, 康智涛, 等. 坩埚移动式喷射共沉积制取铝基复合材料的技术[J]. 湖南大学学报, 2002, 29(6): 22-30.
CHEN Zhen-hua, CHEN Ding, KANG Zhi-tao, et al. Preparation technology of aluminium alloy matrix composites by spray co-deposition with moving crucible[J]. Journal of Hunan University, 2002, 29(6): 22-30.
[11] 詹美燕, 匡 勇, 周 明, 等. 多孔金属及合金成形过程中的致密化与变形理论研究[J]. 稀有金属与硬质合金, 2002, 30(4): 42-47.
ZHAN Mei-yan, KUANG Yong, ZHOU Ming, et al. Research on density and deformation mechanism of porous metal and alloy during processing[J]. Rare Metals and Cemented Carbides, 2002, 30(4): 42-47.
[12] 王祝堂, 田荣璋. 铝及铝合金加工手册[M]. 长沙: 中南工业大学出版社, 2000. 68-79, 454-457.
WANG Zhu-tang, TIAN Rong-zhang. Handbook of Aluminium Alloy and Machine[M]. Changsha: Central South University of Technology Press, 2000. 68-79, 454-457.
[13] Manoharan M, Lewandowski J J. Effect of reinforcement size and matrix microstructure on the fracture properties of an Al metal matrix composite[J]. Mater Sci and Eng A, 1992, A150: 179-186.
[14] Lee K B, Kwon H. Strength of Al-Zn-Mg-Cu Matrix composite reinforced with SiCp[J]. Metal and Mater Trans A, 2002, 33A(2): 455-465.
[15] Semiatin S L, Seetharaman V. Deformation and microstructure development during hot- pack rolling of a near gamma titanium aluminum alloy[J]. Metall Mater Trans A, 1995, A26(2): 371-381.
基金项目: 湖南省杰出青年基金资助项目(02JJYB006)
收稿日期: 2005-01-07; 修订日期: 2005-05-09
作者简介: 张福全(1962-), 男, 副教授.
通讯作者: 张福全, 副教授; 电话: 0731-8821648; 传真: 0731-8821483; E-mail: Zhangfq@hnu.cn
(编辑 龙怀中)