
Microstructure and mechanical properties of Ti6Al4V
powder compacts prepared by magnetic pulse compaction
LI Min(李 敏), YU Hai-ping(于海平), LI Chun-feng(李春峰)
School of Materials Science and Engineering, Harbin Institute of Technology, Harbin 150001, China
Received 23 March 2009; accepted 28 July 2009
Abstract: Ti6Al4V powder compaction was performed by using magnetic pulse compaction in air at 200 ℃. Effects of process parameters such as voltage, capacitance, discharge times on the microstructure, compressive strength, hardness and relative density of compacts were investigated. The experimental results show that the relative density, hardness and compressive strength of compacted specimens increase with increasing voltage. In addition, the relative density and compressive strength of compacted specimens increase with the augmentation of capacitance in the range investigated. The relative density increases, the hardness firstly increases and then tends to be a fixed value; and the compressive strength firstly increases and then decreases from one to five times compaction. Both values of the hardness and compressive strength reach the maxima of HRA 69.1 and 1 062.31 MPa, at three times compaction, respectively. There are pores in and between particles.
Key words: powder metallurgy; Ti6Al4V powder compaction; magnetic pulse compaction; relative density; electromagnetic forming
1 Introduction
Ti6Al4V alloy is one of the most widely used titanium alloys[1-2]. Owing to its excellent properties, it has been widely used in aerospace[1], marine, power generation and offshore industries. However, its high yield ratio and large spring back make it difficult to occur plastic deformation[3-4]. It is easy for Ti6Al4V to generate hard and brittle compounds with oxygen, hydrogen, nitrogen and other elements in air in the process of cutting, thus it is difficult to be machined[5]. The above factors restrict the extensive application range. Powder metallurgy is an effective way to produce a variety of high performance structure materials[6], materials under extreme conditions and special function materials; and it can also achieve near-net-shape powder products[7]. It is effective to produce high relative density powder products by using high strength impact loading[8], one of which is dynamic magnetic compaction (DMC, namely magnetic pulse compaction). DMC is a high-energy rate method; and it can be used to manufacture metal[9], ceramic[10] and composite powder, etc.[11]. It is superior to other powder compaction methods in energy control and forming efficiency. DMC not only can get high-density compact products but also can decrease composition segregation and inhibit grain growth. Therefore, it can be widely used to compact ultrafine powder such as nanopowder[9, 12]. The scholars of the United States, Russia, Japan and South Korea have carried out intensive research in ultra-fine powder forming and the properties of compacts by magnetic pulse compaction[13-15]. Under the pressure of more than 1 GPa, the particles move at the rate of 10-100 m/s. Hence, the kinetic energy can overcome the energy barrier and achieve the combination of particles[13, 16].
In order to get fine grain and high density compacts, a series of compaction experiments of Ti6Al4V powder in air at 200 ℃ were carried out by magnetic pulse compaction. The effects of voltage, capacitance and discharge times on the relative density, hardness, compressive strength and microstructure of compact specimens were investigated. The results can provide experimental foundation for the research on sintering of compacts at middle or low temperature.
2 Experimental
2.1 Experimental equipment
The compaction experiments were performed by using magnetic pulse forming machine. The parameters of the machine are as follows: the maximum discharge energy is 33.6 kJ and the highest discharge voltage is 5.0 kV. Fig.1 shows the schematic diagram of experimental setup, where the internal diameter of cavity die is 20.0 mm. Magnetic pulse compaction involves passing an electrical current pulse through an inductor (such as flat coil) placed in proximity to the driver. The electric pulse flowing through the inductor generates a high magnetic field around that an eddy current is induced in the driver as well as an associated secondary magnetic field. The two fields are repulsive and the forces between them push the driver together with the amplifier and punch moving down to the powder body. Then, the power body is compacted by the punches. The coil is made up of rectangular section copper wire, whose dimensions are as follows: outer diameter 260 mm, coil height 30 mm, wire width 2 mm, wire height 9 mm, interval of turns 0.5 mm, and 34 turns.
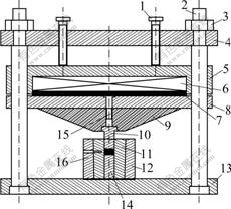
Fig.1 Schematic diagram of magnetic pulse forming setup: 1—Screw; 2—Guide pillar; 3—Nut; 4—Upper template; 5—Coil sleeve; 6—Coil; 7—Driver; 8—Backing plate; 9—Amplifier; 10—Punch; 11—Cavity die; 12—Die sleeve; 13—Lower template; 14—Pad; 15—Screw; 16—Heating sleeve
2.2 Materials and measurements
The distribution of particle size of Ti6Al4V powder was analyzed by Horiba laser scattering particle size distribution analyzer (LA-920), and the average size of particles is 43.23 μm. 5.0 g Ti6Al4V powder was pressed into cylindrical disk by magnetic pulse compaction at 200 ℃. The microstructure of compacted specimen was observed by scanning electron microscope (SEM, Hitachi S-570); and the hardness (HRA) was measured by automatic Rockwell hardness tester (CSS-144). The compacts were cut to cylinder with a size of d 3 mm×3.2 mm by wire cutting; and the compressive strength was tested on electronic universal testing machine (CSS-88050) with a crosshead speed of 0.05 mm/min.
Because the shape of compacts is very regular, the mass of compacts was measured by electronic balance (accuracy 0.001 g); the thickness and diameter of compacts were measured by using vernier caliper on four different position (accurate to 0.02 mm); and then the average value of them was calculated. Finally, the volume and density of the compacted specimens were counted.
3 Results and discussion
3.1 Effects of discharge energy
As discharge energy for the magnetic pulse compaction depends on the discharge voltage (constant capacitance) and the peak of magnetic pressure acting on the driver is directly proportional to the square of discharge voltage, the parameters selected are as follows: capacitance of 12×192 ?F, and discharge voltage of 2.75, 3.0, 3.25 and 3.5 kV.
It can be seen from Fig.2 that increasing discharge voltage contributes to the increase of the relative density and compressive strength of compacts. Because the capacitance is fixed, the increase of discharge voltage enhances the discharge energy, which improves the combination strength of particles. Therefore, the relative density and compressive strength of compacts increase owing to the intensified kinetic energy acting on the powder body.
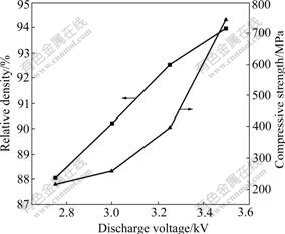
Fig.2 Dependences of relative density and compressive strength of Ti6Al4V compacts on discharge voltage
Compact samples were cut along the central axis, then grinded, polished and eroded. In order to analyze the influence regularity of DMC process parameters on the microstructure of powder compacts, the processed section of compact was observed by SEM. Fig.3 presents the close combination of particles and increasing fraction of fine particles. It is the brittle fracture of particles caused by the increasing voltage that lead to producing fine particles. The fine particles are easy to fill into the gaps among coarse particles.
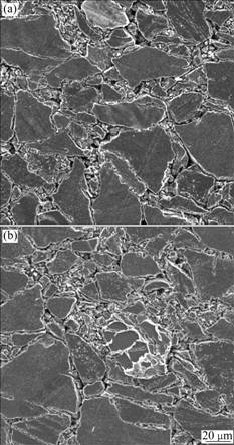
Fig.3 SEM micrographs of Ti6Al4V compacts by DMC with different discharge voltages: (a) 2.75 kV; (b) 3.25 kV
The density distribution of compacts can be analyzed by the hardness distribution of compacts. The hardness of compacts was tested in four different positions. As shown in Fig.4, the arrow direction presents compact direction.
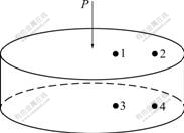
Fig.4 Schematic view of Rockwell hardness measurement positions
As shown in Fig.5, the average hardness of compacts increases as discharge voltage rises and it is consistent with that of relative density. The increasing voltage leads to the difference of hardness values at varied positions of compacts, which indicates that the relative density of compacts tends to be more uniform with increasing discharge voltage from 3.0 to 3.5 kV.
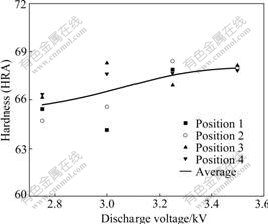
Fig.5 Dependence of hardness of Ti6Al4V compacts on discharge voltage
3.2 Effects of discharge capacitance
In order to explore better parameters in order to get high relative density compacts, effects of different parameters on the relative density of compacts were studied. In view of discharge energy of magnetic pulse forming machine, discharge voltage and capacitance are key process parameters. The effects of voltage on compacts have been discussed in the above section. In this section, the capacitance of capacitor bank of the machine is adjusted to be 8×192, 10×192, 12×192 and 14×192 μF, in the condition that discharge energy of 14.112 kJ keeps constant. Correspondingly, Ti6Al4V powder was compacted in discharge voltage of 4.29, 3.83, 3.50 and 3.24 kV.
As shown in Fig.6, the relative density and compressive strength of compacts increase with the augment of capacitance. The following two aspects can be concluded for the increase of relative density. On one hand, the discharge frequency reduces with increasing capacitance, which indicates an increasing discharge period. Because the compaction was carried out at a constant temperature of 200 ℃, it is equal to increase the time of heat and pressure preservation on compacts. On the other hand, increasing capacitance is favorable to releasing gas among particles. Since both factors contribute to the combination of particles and the failure resistance ability of compacts, the compressive strength increases with the increase of capacitance. The compressive strength of compacts can be increased by using large capacitance when the energy of the machine is fixed.
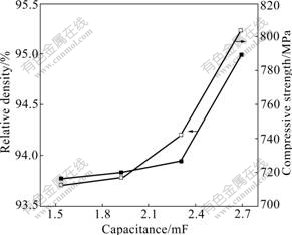
Fig.6 Dependences of relative density and compressive strength of Ti6Al4V compacts on discharge capacitance
3.3 Effects of discharge times
Repeated discharge compaction is another way to reinforce the relative density of compacts. In order to analyze the influence of discharge times on Ti6Al4V powder compacts, the experimental parameters are given as follows: discharge capacitance 12×92 μF, discharge voltage 3.50 kV and repeat discharge from one to five times. From Fig.7, it can be found that the relative density of compacts increases with discharge times. The multi-times discharge causes the accumulation of energy. Although the total energy consumption for compaction increases with discharge times, multi-times discharge compaction is an effective method for some powders that need high energy to be compacted when the rated energy of equipment is limited.
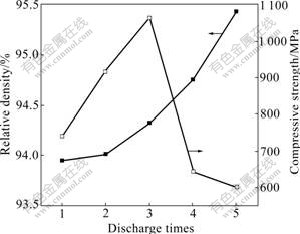
Fig.7 Dependences of relative density and compressive strength of Ti6Al4V compacts on discharge times
Magnetic pulse compaction works by using the impact effects of powerful magnetic pulse load on compact powder. The initial powder is in a loose state and is easy to deform than die, so it is easy to obtain the impact energy. And the compacting process is too fast to work harden the compaction obviously. Therefore, most of mechanical energy changes into the deformation energy of powder, and the dies bear smaller elastic deformation energy. For the further magnetic pulse compaction process, as long as the relative density of compacts is less than 100% and its anti-deformation ability is less than die, the relative density of compacts can be still enhanced.
As Fig.7 shows that, the compressive strength of compacts first increases and then decreases with increasing discharge times. With three times discharge, the compressive strength of compacts reaches the maximum value of 1 062.31 MPa. Although the relative density of compacts increases with discharge times, the brittle fracture of particles constantly happens. The following discharge compaction destroys the compacted structure of previous one and the residual stress in compacts increases after three times discharge. Because the partial welding points among particles are destroyed after three times discharge, the connection strength among particles reduces. The factors mentioned above lead to the dramatic decrease of compressive strength of compacts after three times discharge.
As shown in Fig.8, there are many holes and pores among particles in compacts. A few of pores pass through some particles. Multiple discharge compactions contribute to making more gas discharge from compacts and more holes among large particles become smaller, which results in the increasing relative density of compacts. Moreover, it does not cause obvious plastic deformation and growing up of particles, which indicates that the grains of particles do not deform plastically and grow up obviously.
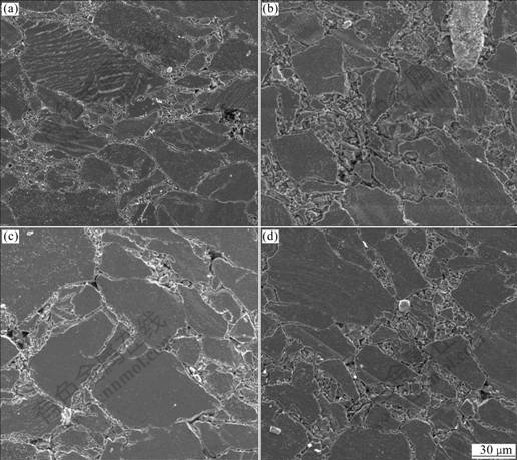
Fig.8 SEM micrographs of Ti6Al4V compacts by DMC with different discharge times: (a) Twice; (b) Three times; (c) Four times; (d) Five times
In Fig.9, we can see that the average hardness of compacts first increases and then tend to be a fixed value with increasing discharge times. Its value reaches the maximum value of HRA 69.1 at three times discharge. The augmentation of average hardness of the compacts is the largest from one to two times discharge. The hardness difference in different positions of the compact prepared under one time discharge compaction is the least, which indicates the relative density of the compact is nearly uniform. The hardness difference in different positions of compact pressed under two times discharge is the largest. Since the hardness difference is relatively small, the relative density of the compact is comparatively uniform. The relative density of compact pressed for three and four times discharge is more uniform than the one pressed for two times discharge, which is mainly related to the particles composition and internal residual stress of compacts. Arch bridges among particles produce holes and pores in compact; and the closer combination of particles can be obtained at two times discharge. The work hardening of the compact is marked and the stress state is different from that of compacted by one time, which causes uneven relative density and obvious hardness difference in different positions of compact. The number of particles occurring brittle fracture further increases at three times discharge. Most of discharge energy is transmitted into the parts with lower relative density; so, the relative density of compacts becomes more uniform and the hardness difference at different positions of compacts decreases. Although the relative density of compacts further increases after three times discharge, there are more particles occurring brittle fracture and the particles produced by brittle fracture are larger with increasing internal cracks. The particles produce work hardening after multiple discharges, which makes the deformation resistance of particles increase. When it reaches a certain value, the hardness of compacts tends to be constant.
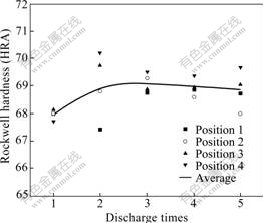
Fig.9 Dependences of hardness of Ti6Al4V compacts on discharge times
4 Conclusions
1) Magnetic pulse compaction is an efficient method to form Ti6Al4V powder compacts with high relative density, hardness and compressive strength.
2) The relative density, hardness and compressive strength of compacts constantly increase with increasing discharge energy.
3) With increasing discharge times, the relative density of compacts constantly increases, which reaches the maximum value of 95.43% under five times discharge; the compressive strength of compacts firstly increases and then decreases; and the hardness of compacts firstly increases and then tends to be a fixed value. Their values reach the maximum of 1 062.31 MPa and HRA 69.1 at three times discharge, respectively.
References
[1] DING R, GUO Z X, WILSON A. Microstructural evolution of a Ti-6Al-4V alloy during thermomechanical processing [J]. Materials Science and Engineering A, 2002, 327(2): 233-245.
[2] LEE W S, LIN C F. High-temperature deformation behaviour of Ti6Al4V alloy evaluated by high strain-rate compression tests [J]. Journal of Materials Processing Technology, 1998, 75(1): 127-136.
[3] GONG P, SUN D L. Effect of hydrogen on the microstructure of Ti-6Al-4V alloy by hot deformation [J]. Materials for Mechanical Engineering, 2007, 31(6): 69-72.
[4] KE Ying-lin, DONG Hui-yue, LIU Gang, ZHANG Ming. Use of nitrogen gas in high-speed milling of Ti-6Al-4V [J]. Transactions of Nonferrous Metals Society of China, 2009, 19(3): 530-534.
[5] HOU Hong-liang, LI Zhi-qiang, WANG Ya-jun, GUAN Qiao. Technology of hydrogen treatment for titanium alloy and its application prospect [J]. The Chinese Journal of Nonferrous Metals, 2003, 13(3): 533-549. (in Chinese)
[6] FROES F H, MASHL S J, MOXSON V S, HEBEISEN J C, DUZ V A. The technologies of titanium powder metallurgy [J]. JOM, 2004, 56(11): 46-48.
[7] HUANG Shang-yu, CHANG Zhi-hua, TIAN Zhen-wu, SHU Xing-jun, CHEN Yan-bo, LI You-chen. Experimental research on low–voltage electromagnetic compaction of powder materials [J]. Journal of Plasticity Engineering, 2001, 8(3): 10-13. (in Chinese)
[8] YU H P, LI C F. Dynamic compaction of pure copper powder using pulsed magnetic force [J]. Acta Metallurgica Sinica (English Letters), 2007, 20(4): 277-283.
[9] CHELLURI B, BARBER J P. Full-density, net-shape powder consolidation using dynamic magnetic pulse pressure [J]. JOM, 1999, 51(7): 36-37.
[10] JAK M J G, OOMS F G B, KELDER E M, LEGERSTEE W J, SCHOONMAN J, WEISENBURGER A. Dynamically compacted all-ceramic lithium-ion batteries [J]. Journal of Power Sources, 1999, 80(1/2): 83-89.
[11] MENG Z H, HUANG S Y, SUN W. Low-voltage electromagnetic compaction of metal and ceramic powders [J]. Journal of Wuhan University of Technology: Materials Science Edition, 2007, 22(4): 714-717.
[12] LI Jin-ping. Low-temperature sintering research on mechanical alloying CuCr contact materials compacted by explosion [D]. Harbin: Harbin Institute of Technology, 2002: 13-15. (in Chinese)
[13] LEE G H, RHEE C K R, LEE M K, KIM W W, IVANOV V V. Nanostructures and mechanical properties of copper compacts prepared by magnetic pulsed compaction method [J]. Materials Science and Engineering A, 2004, 375/377: 604-608.
[14] HONG S J, LEE G H, RHEE C K, KIM W W, LEE K S. Magnetic pulsed compaction of ferromagnetic nano-powders for soft-magnetic core [J]. Materials Science and Engineering A, 2007, 449/451: 401-406.
[15] IVANOV V V, LIPILIN A S, KOTOV Y A, KHRUSTOV V R, SHKERIN S N, PARANIN S N, SPIRIN A V, KAYGORODOV A S. Formation of a thin-layer electrolyte for SOFC by magnetic pulse compaction of tapes cast of nanopowders [J]. Journal of Power Sources, 2006, 159(1): 605-612.
[16] ANDO S, MINE Y, TAKASHIMA K, ITOH S, TONDA H. Explosive compaction of Nd-Fe-B powder [J]. Journal of Materials Processing Technology, 1999, 85(1/3): 142-147.
Corresponding author: LI Min; Tel: +86-451-86413970; E-mail: limin_com@163.com
DOI: 10.1016/S1003-6326(09)60177-1
(Edited by FANG Jing-hua)