J. Cent. South Univ. Technol. (2008) 15(s1): 284-287
DOI: 10.1007/s11771-008-364-5

Experiments and analysis for rheological properties of MRF
WANG Hai-xia(王海霞), RUAN Yu-ming(阮予明), KONG Sun(孔 笋), WANG Jie(王 捷)
(Fujian Electric Vocational and Technical College, Department of Mechanical and Electric Engineering
Quanzhou 362000, China)
Abstract: The work principle of flat-plate structure under shearing mode is expounded based on a vertical type rheometer for MRF which combined data acquisition with treatment and result display. The formula to calculate shearing stress is deduced. Based on different recipe for MRF, experiments under different working gap length were done by altering the intensity of magnetic field. The rheological model for MRF was established and the relationships between shearing stress, viscosity and magnetic field intensity were deduced. Experiments indicate that MRF has the flowing characters: with an increase of the magnetic induction and the nominal shear rate, the shear stress of MRF increases. However, as the working gap decreases, the shear stress increases. MRF has shear thinning property under magnetic field.
Key words: magneto-rheological fluid; constitutive equation; rheometer; experiment
1 Introduction
Magnetorheological fluids(MRF) belong to the newly class of smart materials which are composed of dispersed phase, discontinuous phase and stabilizer[1-3]. In this paper MRFs are manufactured with micron-sized, reduction hydroxyl irons particles(DT-50), grade A silicon oil and nanometer-sized spherical silica.
Normally, in the absence of magnetic field, MRF behaves as Newtonian fluid. With exposure to a magnetic field, the iron particles acquire a dipole moment aligned with the external field which causes particles to form linear chains parallel to the field[4]. Such phenomenon is called magnetorheological effect. Instantaneously the rheological properties are dramatically changed under external magnetic field such as apparent viscosity increases, the fluid turns into solid and reverts to fluid when the applied magnetic field vanishes[4].The transition has such characters: the transition is reversible and controllable; the time scale for the transition is of the order of a millisecond; the transition requires a much lower voltage[5].
Rheological characteristic of MRF is influenced by lots of factors, so studying rheological properties, the application of rheological properties and designing MRF element must carry out an experiment on MRF and build mechanical model of MRF.
Based on the experiment of MRF, the equation for nominal shear rate is defined. Effects of magnetic
induction strength, mass fraction of iron particles, the shear rate etc on the shear stress of MRF are discussed. Finally, the Bingham model, generalized Bingham model and nonlinear model were built to describe the shear stress of MRF[6].
2 Experimental
2.1 Principle of rheological properties experiment
Experimental arrangement shown in Fig.1 consisted of driving plate which is forced to rotate by a stepping motor and a fixed. The gap between the driving plate and the fixed one is defined as h. In the experiments, the gap is filled with MRF. The shear stress under different shear rates can be measured by testing system using LabVIEW platform affiliated with this magnetorheological arrangement. When the active disk rotates with angular velocity Ω, MRF will flow with the mode of torsion and haul under the action of active disk. The analysis assumes that MRF is incompressible, homothermal and laminar when test is going into stability condition. Cylindrical coordinate system is adopted for this analysis and the forward of z as Fig.1, the component of the shearing stress τzθ acting on the plane is perpendicular to z. The tangential direction of the twist flow is defined as the direction of θ. Among the twist motion vθ(z)=0, vz=vr=0, assume that ω=0 at z=0, ω=Ω at z=h. Circumferential velocity vθ(z) is the function of distribution density function is the function of variable z as Eqn.(1)
(1)
By application of the velocity distribution and the equation of shearing stress for parallel plate reported earlier[4] , the shearing rate of the twist motion
is given by:
(2)
The integration of Eqns.(1) and (2),
is given by:
(3)
2 mm is the maximum working gap which is allowed by the measurement of magnetorheological rheometer. As shown in Fig.1, in the middle of the disk, there is a groove, R2 in radius, over 2 mm in working gap, so its effective operating range is the ring part between R1 and R2. The analysis takes average radius R0 as a measure standard of shear rate.
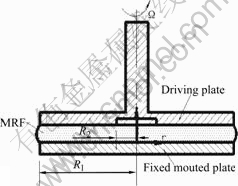
Fig.1 Magnetorheological arrangement
(4)
So integrating Eqn.(3) to Eqn.(4), nominal shearing rate
is given by:
(5)
In the test the shearing rate
is calculated using Eqn.(5). Under the twist motion the shearing stress τzθ is given by:
(6)
where
is defined as nominal viscosity. By the application of the theory about dynamical characters for parallel plate[7], the relationship between torque and viscosity is not proportional and the equation of viscosity must be deduced by means of Robinowitsh as Eqn.(7):
(7)
where T is torque, defined
=
,
=n.
Parameters n and T are determined by experiment. So nominal viscosity ηa is given by:
(8)
2.2 Results and analysis
The rated torque of the stepping motor used in this experiment is 5 N?m, so this magnetorheological rheometer mainly measures rheological properties in the condition of low shear rates. According to results of groups of experiment data, gap, magnetic intensity, shear rates and recipes all have huge effect on rheological properties of MRF.
In the following section the mass percent of iron particles is defined as φ, shear stress as τ, magnetic induction as B, n as rotational speed, shear rate as symbol
, and nominal viscosity as ηa.
Figs.2-3 illustrate B—τ curves when φ=74% and φ=78% at the gap of 2 mm. As shown in Figs.2-3, τ
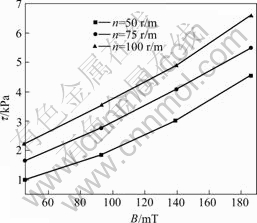
Fig.2 Relationships between B and τ at φ=74%
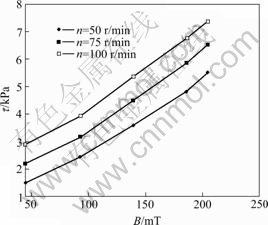
Fig.3 Relationships between B and τ at φ=78%
increases with φ and B increasing. It can be seen that MRF has an approximately linear property when the applied magnetic field is small.
A type of MRF at φ=78% is shown in Fig.4. And Fig.4 presents the curve of
—τ under different magnetic inductions when the gap is given. As shown in Fig.4 the relationship between
and τ is nonlinear and MRF exhibits a significant shear thinning effect. Furthermore, Fig.5 indicates that shear stress increases with
and B increasing.
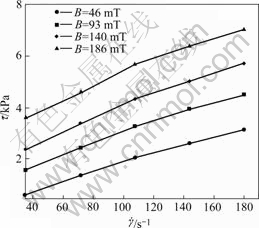
Fig.4 Relationships between
and τ
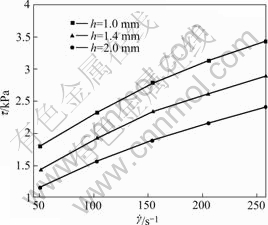
Fig.5 Relationships between gap h and τ at B=93 mT and φ=74%
Fig.6 illustrates that when B and φ are given, shear stress increases with shear rate increasing and with the gap increasing it decreases.
Fig.6 presents the curve ηa—
when φ=78%, B=0 mT and room-temperature of 27 ℃. The curve indicates the viscosity of MRF is not a constant and it decreases with the nominal shear rate increasing. Further more the curve certificates the conclusion that MRF using in the experiment is non-Newton fluid and the result that MRF have shear thinning property.
The relationship between ηa and
or B is shown in Fig.7 with φ=78%. Compared with Fig.6 such
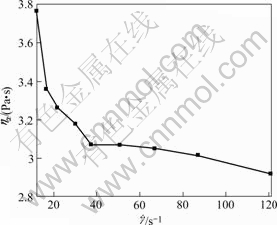
Fig.6 Relationships between
and η when B=0 and φ=78%
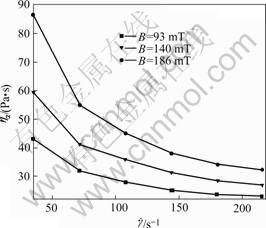
Fig.7 Curves of
—ηa at φ=78%
conclusion is obtained that magnetic field intensity has dramatically effect on the viscosity of MRF and the nominal viscosity is one order of magnitude higher than the one under no-magnetic field. Furthermore, Fig.7 illustrates that the nominal viscosity of MRF becomes sharply higher as the magnetic induction increases. In the same way, MRF also has shear thinning property under influence of magnetic field.
3 MRF models
3.1 Bingham model
Bingham model (Philips 1969) is effective to describe the essential field-dependent fluid characteristics. In this model, the equation of shear stress τ is given by
(9)
where Kb is defined as Bingham viscosity. When the value of magnetic induction is 140 mT or 186 mT, experimental data are fitted by means of least squares. Then the relationship between shear stress and shear rate is acquired as follows
, B1=140 mT (10)
or
, B2=186 mT (11)
The variances for Eqns.(10) and (11) are respectively σ1=0.05 and σ2=0.09. The results indicate that MRF is non-Newton flow and has yield stress τy.
Bingham model cannot reflect shear thinning property, so generalized Bingham model and nonlinear model are employed.
3.2 Generalized Bingham model
Generalized Bingham model can be employed to accommodate the shearing thinning phenomenon and the equation is given by
(12)
where kp is defined as consistence factor and index number n reflects the degree of shear thinning. The two group of data are fitted and Eqns. (13) and (14) are acquired:
B1=140 mT (13)
or
B2=186 mT (14)
The variances for Eqns.(13) and (14) are respectively σ1=0.037 1, σ2=0.06.
3.3 Nonlinear model
(15)
where μ is a dimensionless factor, kn is a consistence factor for nonlinear model which reflects the degree of shear thinning. The equations fitted from the test data are shown as follows:
(16)
or
(17)
The variances for Eqns.(16) and (17) are respectively σ1=0.23, σ2=0.35.
4 Conclusions
1) With an increase of the magnetic induction and the nominal shear rate, the shear stress of MRF increases. However, as the working gap decreases, the shear stress increases.
2) The trend that the shear stress increases with the nominal shear rate increasing under lower shear rates is sharper than the speed under high shear rate. And when the shear rate is high enough the shear stress will decease with the shear rate increasing. Then this phenomenon proves MRF has shear thinning property under magnetic field.
3) The viscosity of MRF is one order of magnitude higher than that of the zero field in a magnetic field.
References
[1] JIANG Wan-quan, ZHU Chun-ling, CHEN Zu-yao, ZHOU Gang-yi, ZHANG Pei-qiang. The enhanced MR effect of dense magnetic particles suspensions consisting of superfine α-Fe particles [J]. Chinese Journal of Chemical Physics, 2001, 14(5): 629-632.
[2] JIANG Wan-quan, ZHU Chun-ling, HE Pei. The enhanced MR effect of concentrated magnetic microns suspensions consisting of non-magnetic nanosize particles [J]. Journal of Functional Materials, 2001, 32(3): 243-244, 247.
[3] JIANG Wan-quan, ZHU Chun-ling, CHEN Zu-yao, ZHANG Pei-qiang. Preparation of micron polymer-Fe capsulized composites by mechanic milling and MR effect of concentrated [J]. 2001, 14(5): 543-547.
[4] CHEN K C, YEH C S. A mixture model for magneto-rheological materials [J]. Continuum Mech Thermodyn, 2002, 15: 485-510.
[5] GINDER J M, DAVIS L C, ELIE L D. Rheology of magnetorheological fluids: Models and measurements [C]// Proceedings of the fifth International Conference on ER Fluids and MR Suspensions. Sheffield, UK, 1996.
[6] JOLLY M R, CARLSON J D. Controllable squeeze film damping using magnetorheological fluid [C]// ACTUATOR 96, Fifth International Conference on New Actuators. Bremen, 1996: 333-336.
[7] XU Pei-xuan. Polymer rheology and its application[M]. Beijing: Chemical Industry Press, 2003: 92-98.
(Edited by CHEN Ai-hua)
Foundation item: Projects(10472134, 50490274) supported by the National Natural Science Foundation of China
Received date: 2008-06-25; Accepted date: 2008-08-05
Corresponding author: WANG Hai-xia, Master; Tel: +86-15980020850; E-mail: snqailmm@126.com