Trans. Nonferrous Met. Soc. China 25(2015) 1865-1871
Effects of solution-aging treatment on microstructures and properties of Ti-55.06%Ni-0.3%Cr alloy
Li-zhou ZENG, Bing-hui LUO, Bin LI, Zhen-hai BAI, Sheng OUYANG, Wen-li FAN
School of Materials Science and Engineering, Central South University, Changsha 410083, China
Received 13 July 2014; accepted 16 December 2014
Abstract: The effects of solution-aging treatment on the microstructures, mechanical properties and internal friction of Ti- 55.06%Ni-0.3%Cr (mole fraction) alloy were investigated by means of tensile test, dynamic mechanical analysis (DMA) and spherical aberration electron microscopy (SAEM). The results show that the aged alloys with Cr3Ni2 phase always exhibit higher tensile strength and hardness than those of solution-treated alloy without Cr3Ni2 phase, and the aging peak temperature presents at 375 °C. It is also found that the internal friction peak (tan δ) value decreases with increasing the frequency. There are two internal friction peaks corresponding to the B2(austenite)→R and R→M(martensite) transformations upon cooling, but only one corresponding to the reverse M→B2 transformation upon heating in both solution-treated and 375 °C-aged alloys, due to the superposition of M and R phase transformation. Besides, the position of internal friction peaks in the alloy after aging at 375 °C shifts to higher temperature. This is attributed to the decrease of Cr and Ni content, and the decline of lattice deformation and transformation resistance, all of which are related to the precipitation of Cr3Ni2 phase in the solution-aged alloys.
Key words: Ti-Ni-Cr alloy; mechanical properties; martensite transformation; internal friction
1 Introduction
Shape memory alloys (SMAs) that undergo a thermoelastic martensitic transformation show unique properties such as shape memory effect and super- elasticity [1,2]. Numerous studies have revealed that SMAs also exhibit high-damping properties during the martensitic transformation, and accordingly meet the dramatically increasing needs for energy dissipation materials. TiNi-based alloys are confirmed to be one of the most popular SMAs because of their excellent wear-resistance, high damping capacity and mechanical properties [3-5]. Up to now, various factors that affect the mechanical properties and internal friction of TiNi binary alloys have been well established, such as compositional changes [6,7], aging treatment and external parameter [8-10].
To our knowledge, considerable efforts have been focused on studying the effect of the third element on the mechanical and phase transformation properties of Ni-Ti-X ternary alloy systems. It has been observed that the addition of Fe or Nb to Ni-Ti alloys improves their super-elastic property by lowing the transformation temperature [11-13]. HSIEH et al [14], UCHIL et al [15], JEOM and SIA [16] studied the transformation behavior of Ti-Ni-Cr alloys with different Cr contents and annealing temperatures. They reported that the transfor- mation temperatures of Ti-Ni-Cr alloys decrease with increasing the Cr addition, while the transition stress for stress-induced martensite formation and super-elasticity are improved, therefore, Ti-Ni-Cr alloys can be used in vibration damping devices and wear-resisting parts. However, there is no study that addresses the mechanical properties and the internal friction of Ti-Ni-Cr alloys at various solution-aging temperatures. In this study, the evolution of mechanical properties and the precipitated second phases of Ti-Ni-Cr alloys with respect to solution-aging treatment are discussed. After determining the optimum aging condition, the internal friction of the corresponding aged Ti-Ni-Cr is investigated.
2 Experimental
The Ti-Ni-Cr alloy was provided by Xi’an Saite Metal Materials Development Co., Ltd. The chemical composition given in Table 1 is determined by inductively coupled plasma (ICP) spectral analysis. The ingots were forged and hot-rolled to alloy bars with 8.5 mm in diameter, and then hot-rolled at 700 °C into 1.8-mm-thick plates. After that, the sheets were solution-treated at 800 °C for 1 h, and subsequently quenched in water. Finally, the solution-treated samples were aged at 300, 375, 450 and 525 °C for 1 h, respectively, followed by water quenching.
Table 1 Chemical components of Ti-Ni-Cr alloy (mole fraction, %)

The phase constitution was identified by a D/max-2550 X-ray diffractometer with Cu Kα radiation obtained from a tube operated at 40 mA and 40 kV. The scanning speed was 8 (°)/min, and the scanning angle was between 10° and 80°. The microstructure observations were performed using an FEI Titan 80-300 spherical aberration electron microscope operated at 200 kV. The foils for TEM observation were mechanically ground to 50 μm and then thinned by twin-jet polishing in an electrolyte consisting of 8% HClO4 and 92% C2H5OH (volume fraction). The specimens of 7.5 mm × 1.8 mm × 100 mm for tensile test were cut from the samples after different heat treatments by electro-discharge machining (EDM). The tensile properties of Ti-Ni-Cr alloys were performed at a strain rate of 1 mm/min using a CSS-41100 electronic tensile machine. For the internal friction measurements, each sample was cut into bulks with dimensions of 35 mm × 12 mm × 1.8 mm, with the internal friction peaks (tan δ) value and the storage modulus were determined using a TaQ800 dynamic mechanical analyzer at temperatures ranging from -100 to 100 °C at a constant heating/cooling rate of 3 °C/min. The strain amplitude was controlled at 2×10-5, and the oscillation frequency was set at 1, 2 and 4 Hz, respectively.
3 Results and discussion
3.1 XRD patterns of Ti-Ni-Cr alloys
Figure 1 shows the X-ray diffraction (XRD) spectra of solution-treated and aged Ti-Ni-Cr alloys at room temperature. The XRD spectrum in Fig. 1(a) mainly indicates that the solution-treated alloy exhibits the B2(austenite)+R phases at room temperature. After aging treatment, there are Cr3Ni2 diffraction peaks besides B2+R diffraction peaks, which imply that the aging treatment after solid solution treatment can promote the precipitation of Cr3Ni2 phase. The strongest peak belongs to the B2 phase which represents the matrix.
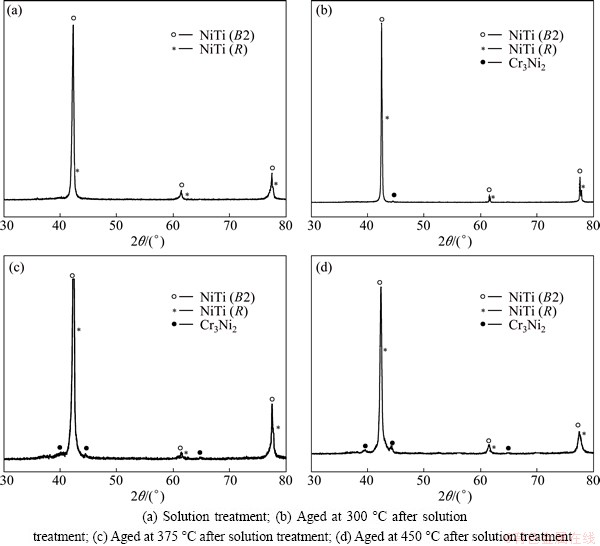
Fig. 1 XRD patterns of Ti-Ni-Cr alloys after different heat treatments
It can be seen from Figs. 1(b)-(d) that, the Cr3Ni2 particles cannot precipitate completely in the alloy aged at 300 °C as the Cr3Ni2 diffraction peaks are less evident than others. Meanwhile, the height of R diffraction peaks rises with aging treatment, indicating that the relative amount of R to B2 increases through aging treatment. The precipitation of Cr3Ni2 phase in alloys after aging treatment decreases the Cr and Ni contents of the matrix, leading to the decline of the Ni and Cr atomic oversaturation, lattice deformation and transformation resistance, and the rise of phase transformation temperature [5,6].
3.2 Microstructures of Ti-Ni-Cr alloys
The detail information of morphologies including Cr3Ni2 precipitate in Ti-Ni-Cr alloys after different heat treatments was studied by spherical aberration electron microscopy (SAEM) and the corresponding selected area electron diffraction(SAED).
Figure 2(a) shows the grain boundary photographs of the solution-treated alloy. The microstructures and the corresponding [111]B2 selected area electron diffraction pattern of the sample aged at 375 °C after solution treatment are illustrated in Figs. 2(b)-(d), respectively. From Fig. 2(a), flat grain boundary and clean grain without the second particles can be seen, but very fine precipitates distinctly occur in Fig. 2(b). The Cr3Ni2 particles (marked by arrows in Fig. 2(c)) with an average size of 20 nm can be easily observed in dark-field image of 375 °C-aged alloy. The precipitation of Cr3Ni2 phase in alloy aged at 375 °C after solution treatment decreases the Ni content of the matrix, which can lead to the increase of the transformation temperature [10]. In Fig. 2(d), the electron diffraction pattern represents the B2 parent matrix, corresponding to the XRD spectrum in Fig. 1(c), and the 1/3[111]B2 super-lattice spot [17] can be also observed.
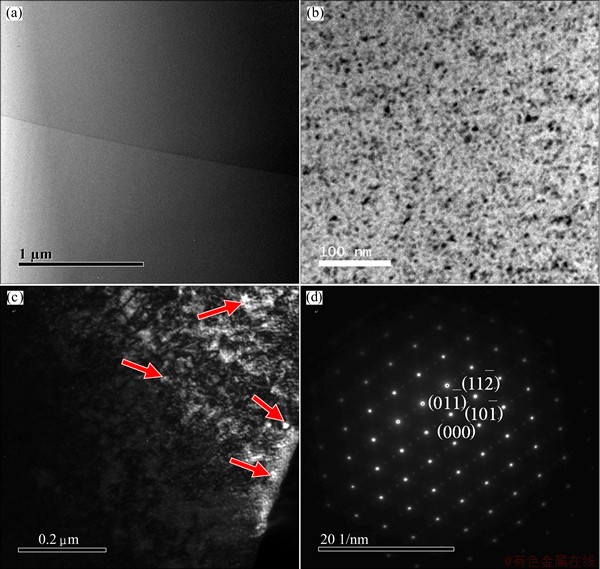
Fig. 2 SAEM image of solution-treated alloy (a), bright-field image (b) and dark-field image (c) of 375 °C-aged alloy, and SAED pattern (d) of 375 °C-aged alloy
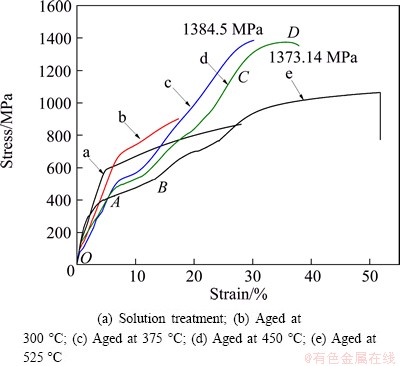
Fig. 3 Tensile curves of Ti-55.06%Ni-0.3%Cr alloys after different heat treatments
3.3 Mechanical properties of Ti-Ni-Cr alloys
To investigate the overall mechanical properties of Ti-Ni-Cr alloy, the specimens were aged at various temperatures for 1 h and then quenched in water. Figure 3 shows the stress-strain curves of Ti-Ni-Cr alloy aged at various temperatures, and the mechanical properties are shown in Table 2. It can be seen from Fig. 3 that, the typical stress platforms are clearly observed in solution treated alloys which aged at 375, 450 and 525 °C, respectively, while not appearing in solution treated alloy and 300 °C-aged alloy. The curves can be divided into four stages: OA stage represents the elastic deformation of austenite, platform in AB stage indicates the transformation of austenite into martensite, BC is the elastic deformation of martensite, and CD stage stands for the hardening and fracture procedure of martensite.
Table 2 Mechanical properties of Ti-Ni-Cr alloys
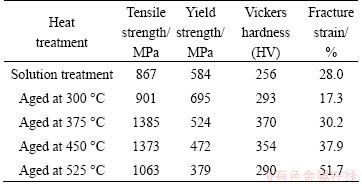
In addition, the solution-treated alloys aged at 375, 450 and 525 °C, respectively, exhibit lower yield strength (Table 2) than that of solution-treated alloy, because the precipitation of Cr3Ni2 particles (shown in Fig. 1 and Fig. 2(c)) in aged alloy decreases the Cr and Ni contents of the matrix, leading to the rise of phase transformation temperature and the decline of the amount of B2 parent phase. Moreover, the yield strength of aged alloys decreases evidently as the aging temperature rises, because the strengthening effect of B2 parent phase fades, which is related to the decline of dislocation density at relatively high aging temperature.
Table 2 exhibits that the tensile strength and hardness of aged alloys are always higher than those of solution treated alloy, expressing that aging treatment following solid solution treatment can enhance the strength and hardness remarkably. This phenomenon would be attributed to the fine Cr3Ni2 precipitates formed by aging treatment. In the tensile test, the Cr3Ni2 precipitates which can strengthen the B2 matrix could act as the pinning sites against the movement of dislocations, and create energy barrier for the motion of dislocations [10,17], resulting in the increase of tensile strength. Meanwhile, the highest strength and hardness occur in solution treated alloy aged at 375 °C, as the finest Cr3Ni2 particles are participated completely. In addition, the plasticity is significantly improved as the aging temperature increases.
3.4 DMA results of Ti-Ni-Cr alloys
Figure 4 shows the dynamic mechanical analysis (DMA) curves measured at different frequencies for solution-treated Ti-Ni-Cr alloy aged at 375 °C. It can be seen from Fig. 4 that, the temperatures of the internal friction peaks corresponding to the minimum storage modulus are independent of the measuring frequency, and the heights of the internal friction peaks increase with decreasing the measuring frequency. It is well known that the internal friction peak of TiNi-based alloy only appears during the forward/reverse martensite transformation, which is due to the moving of austenite/martensite coherent interfaces, twin boundaries between martensite variants and mutual merging of martensite variants [8]. Moreover, when the measuring frequency decreases, the measuring period will increase. Therefore, as the forward/reverse martensite transformation is performed further, the corresponding tan δ value would be larger.
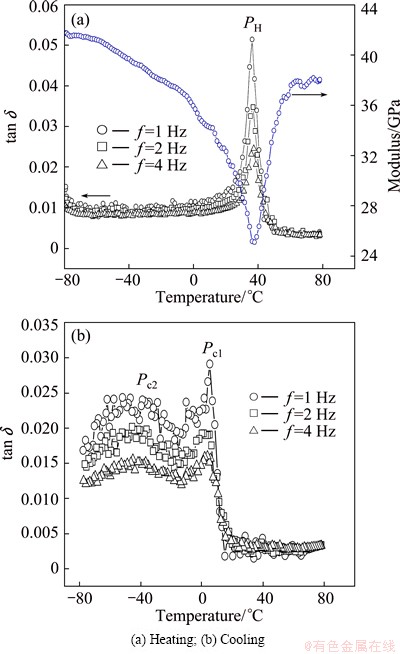
Fig. 4 tan δ and storage modulus vs temperature curves measured at different frequencies for solution-treated sample aged at 375 °C
Comparing Figs. 4(a) with (b), there are two internal friction peaks PC1 and PC2 related to the B2→R and R→M transformations measured at different frequencies upon cooling, while only one internal friction peak PH corresponding to the reverse M→B2 transformation appears in Ti-Ni-Cr alloy aged at 375 °C upon heating. It indicates that the reverse M→R phase transformation and the subsequent reverse R→B2 martensite transformation overlap together [17], because the interaction of the complex structure containing M phase and the grain decorated with Cr3Ni2 particles (shown in Fig. 2(b)) makes the M→R transformation covered. During the cooling process, B2→M transformation is very difficult to take place, since the addition of Cr to B2 matrix increases the lattice deformation and the transformation resistance of B2→M, that is to say, the one-stage phase transformation requires more energy. However, the multiple phase transformation would nucleate through the intermediate R phase transformation, namely, B2→R→M, which needs less energy. Additionally, the presence of Cr3Ni2 in the B2 matrix favors the formation of R phase in some ways.
From Fig. 4, the tan δ value in heating process is always higher than that in cooling process. As far as we known, the motion of M phase and lots of phase interfaces can produce very high tan δ value under very low temperature, therefore, the relatively higher tan δ value occurs during the reverse phase transformation. Besides, the tan δ value in M or R phase is much higher than that in B2 phase. The B2 matrix exhibits a rather small tan δ value because it comes only from the dynamic/static hysteresis of lattice defects such as vacancies and dislocations. On the other hand, the M and R phases exhibit extremely high tan δ values due to their abundant twin boundaries between 24 kinds of M variants and 4 kinds of R variants which can be easily moved by the external stress to accommodate the applied strain [5].
The DMA test of solution-treated Ti-Ni-Cr alloy was conducted at a constant cooling/heating rate of 3 °C/min and an oscillation frequency of 1 Hz, and the results are shown in Fig. 5. The DMA curves of alloy aged at 375 °C after solid solution treatment shown in Fig. 4 are also plotted in Fig. 5 for comparison. In Fig. 5, there is only one reverse M→B2 phase transformation internal friction peak PH upon heating. Upon cooling, two internal friction peaks PC1 and PC2 corresponding to the B2→R and R→M transformations exist in both alloys.
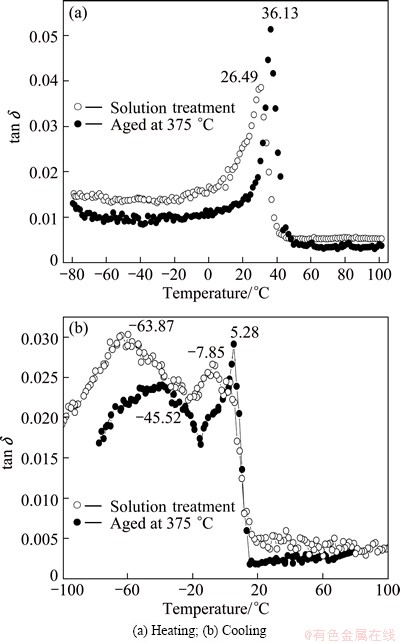
Fig. 5 tan δ vs temperature curves for solution-treated alloy and 375 °C-aged alloy
In Fig. 5(a), the peak temperatures of solution- treated alloy and solution-aged alloy are 26.49 and 36.13 °C, respectively. In Fig. 5(b), the peak temperatures are -63.87, -7.85 and -45.52, 5.28 °C for solution treated alloy and solution-aged alloy, respectively. It is not difficult to find out that the alloy after aging treatment exhibits higher internal friction peak temperatures than those of solution treated alloy. From the XRD spectra in Fig. 1 and the micrographs in Fig. 2, the existence of Cr3Ni2 precipitate in the solution-treated alloy aged at 375 °C decreases the Ni and Cr contents of the matrix, which could lead to the rise of phase transformation temperature. Meanwhile, the fine and dispersed precipitate keeps coherent with the matrix and forms a quite strong coherent stress field. The combined action of coherent stress field and applied stress field makes the transformation of some local region easier [18]. At the same time, the precipitation of Cr3Ni2 phase would serve as the nucleation site of the martensite phase transformation. Across the whole test, the tan δ value can reach 0.051 which is regarded as a high-damping value. Thus, the solution-treated alloy aged at 375 °C is a potential material for energy absorbing and vibration damping applications.
4 Conclusions
1) B2 and R phases coexist in the solution treated alloy, while the solution-aged alloy also contains Cr3Ni2precipitate besides B2 and R phases at room temperature.
2) Ti-Ni-Cr alloy with Cr3Ni2 particles after solution and aging treatment always owns higher tensile strength and hardness than those of solution-treated alloy without Cr3Ni2 precipitate. The solution-treated alloy aged at 375 °C gets the maximum strength (1385 MPa) and hardness (HV 370).
3) There is only one reverse M→B2 phase transformation internal friction peak in both solution treated and 375 °C-aged alloys; upon cooling, there are two internal friction peaks PC1 and PC2 corresponding to the B2→R and R→M transformations, respectively.
4) Upon heating, the internal friction peak temperatures of solution-treated alloy and 375 °C-aged alloy are 26.49 and 36.13 °C, respectively; upon cooling, the internal friction peak temperatures are -63.87, -7.85 and -45.52, 5.62 °C for the solution-treated alloy and the 375 °C-aged alloy, respectively. Namely, the internal friction peak temperatures of Ti-Ni-Cr alloy aged at 375 °C after solution treatment are higher than those of solution treated alloy.
References
[1] JIANG Shu-yong, ZHAO Ya-nan, ZHANG Yan-qiu. Effect of solution treatment and aging on microstructural evolution and mechanical behavior of NiTi shape memory alloy [J]. Transaction of Nonferrous Metals Society of China, 2013, 23(12): 3658-3667.
[2] GONG Wei-huai, CHEN Yu-hua, KE Li-ming. Microstructure and properties of laser micro welded joint of TiNi shape memory alloy [J]. Transaction of Nonferrous Metals Society of China, 2011, 21(9): 2044-2048.
[3] CHANG S H, HSIAO S H. Inherent internal friction of Ti50Ni50-xCux shape memory alloys measured under isothermal conditions [J]. Journal of Alloys and Compounds, 2014, 586(2): 69-73.
[4] OTSUA K, REN X. Physical metallurgy of Ti-Ni based shape memory alloys [J]. Progress in Materials Science, 2005, 50: 511-678.
[5] CHANG S H, WU S L. Internal friction of B2→B19′ martensitic transformation of Ti50Ni50 shape memory alloy under isothermal conditions [J]. Materials Science and Engineering, 2007, 454-455: 379-383.
[6] FRENZEL J, GEORGE E P,
A, SOMSEN C, WAGNER M F X, EGGELER G. Influence of Ni on martensitic phase transformations in NiTi shape memory alloys [J]. Acta Materialia, 2010, 58(9): 3444-3458.
[7] ZHAO H, LIANG C Q, LIU J T, TONG Y X, ZHENG Y F. Effect of aging treatment on superelasticity of a Ti48.8Ni50.8V0.4 alloy [J]. Journal of Materials Engineering and Performance, 2012, 21: 2566-2571.
[8] XING Ting-yong, ZHENG Yan-jun, CUI Li-shan, MI Xu-jun. Influence of aging on damping behavior of TiNi/TiNi alloys synthesized by explosive welding [J]. Transaction of Nonferrous Metals Society of China, 2009, 19(6): 1470-1473.
[9] WANG Xie-bin, LI Kai, SCHRYVERS D, VERLINDEN B, HUMBEECK J V. R-phase transition and related mechanical properties controlled by low-temperature aging treatment in a Ti-50.8at% Ni thin wire[J]. Scripta Materialia, 2014, 72-73: 21-24.
[10] SONG Jie, WANG Li-ming, Zhang Xiao-ning, SUN Xiao-gang. Effects of second phase on mechanical properties and martensitic transformations of ECAPed TiNi and Ti-Mo based shape memory alloys [J]. Transaction of Nonferrous Metals Society of China, 2012, 22(8): 1839-1848.
[11] BOZZLO G, NOEBE R D, MOSCA H O. Site preference of ternary alloying additions to NiTi: Fe, Pt, Pd, Au, Al, Cu, Zr and Hf [J]. Journal of Alloys and Compounds, 2005, 389: 80-85.
[12] LI Yan-feng, KANG Xiao-yu, YIN Xiang-qian. Microstructure and mechanical properties of cold-rolled Ti50Ni47Fe3 shape memory alloy [J]. Transaction of Nonferrous Metals Society of China, 2014, 24(9): 2890-2895.
[13] XIAO Pu, ZHAO Xin-qing, XU Hui-bin. Damping capacity and mechanical property of NiTiNb shape memory alloys [J]. Acta Metallurgica Sinica, 2009, 45(1): 18-24.
[14] HSIEH S F, CHEN S L, LIN H C, LIN M H, HUANG J H, LIN M C. A study of TiNiCr ternary shape memory alloys [J]. Journal of Alloys and Compounds, 2010, 494(1): 155-160.
[15] UCHIL J, GANESH KUMARA K, MAHESH K K. Effects of heat treatment temperature and thermal cycling on phase transformations in Ni–Ti–Cr alloy[J]. Journal of Alloys and Compounds, 2001, 325(2): 210-214.
[16] JEOM Y C, SIA N N. Effect of annealing and initial temperature on mechanical response of a Ni-Ti-Cr shape-memory alloy [J]. Materials Science and Engineering A, 2006, 432: 100-107.
[17] ZHANG Xiao-ning, XIA Bao-yu, SONG Jie. Effects of equal channel angular extrusion and aging treatment on R phase transformation behaviors and Ti3Ni4 precipitates of Ni-rich TiNi alloys [J]. Journal of Alloys and Compounds, 2011, 509: 6296-6031.
[18] TONG Yun-xiang, LIU Jun-ting, CHEN Feng. Effect of aging on martensitic transformtion and superelasticity of TiNiCr shape memory alloy [J]. Transaction of Nonferrous Metals Society of China, 2014, 24(8): 2598-2605.
固溶时效处理对Ti-55.06%Ni-0.3%Cr合金组织和性能的影响
曾丽舟,罗兵辉,李 彬,柏振海,欧阳盛,范文丽
中南大学 材料科学与工程学院,长沙 410083
摘 要:通过拉伸试验、动态力学分析(DAM)和球差电镜研究固溶时效处理对 Ti-55.06%Ni-0.3%Cr(摩尔分数)合金的显微组织、力学性能和内耗性能的影响。结果表明:析出Cr3Ni2相粒子的时效态合金的抗拉强度和硬度总大于无Cr3Ni2析出的固溶态合金,时效峰温度为375 °C。固溶态和375 °C时效合金的内耗峰值(tan δ)均随频率的增加而降低,降温过程出现奥氏体(B2)→预马氏体相(R)和R→马氏体(M)两个相变内耗峰;升温过程中由于R和M相变的叠加,两种状态合金均只出现一个M→B2相变内耗峰。此外,由375 °C时效态合金析出的Cr3Ni2相粒子导致的基体中Cr、Ni含量降低,晶格畸变程度减弱,相变阻力减小,使得375 °C时效态合金的内耗峰峰温向高温方向移动。
关键词:Ti-Ni-Cr合金;力学性能;马氏体相变;内耗
(Edited by Mu-lan QIN)
Foundation item: Project (LH201236) supported by Pre-research
Corresponding author: Bing-hui LUO; Tel: +86-731-88830333; E-mail: lbh@mail.csu.edu.cn
DOI: 10.1016/S1003-6326(15)63793-1