
Improvement of flotation behavior of Mengzi lead-silver-zinc ore by pulp potential control flotation
QING Wen-qin(覃文庆), HE Ming-fei(何名飞), CHEN Yu-ping(陈玉平)
School of Minerals Processing and Bio-engineering, Central South University, Changsha 410083, China
Received 18 April 2007; accepted 22 November 2007
Abstract: The electrochemical behavior of Mengzi lead-silver-zinc ore flotation system was studied. Based on the electrochemical characteristics of sulfide mineral flotation system, a stage potential control flotation was developed with the main parameters of pulp potential(φp), pH value and collector dosage. Using N,N’ diphenylamino-dithiolphosphoric acid(NNDDC) as a collector, which has good selectivity for galena flotation at pH 8.8 and pulp potential 330 mV, DDTC is used as secondary collector to improve both the grade and recovery of Pb and Ag. The pulp potential values significantly influence the floatability of practical minerals and single minerals when using NNDDC as the collector. The flotation recovery of galena reaches 85% at about 0.3 V and pH8.8. With the usage of pulp potential control during grinding and flotation, the new pulp electrochemical technology for Mengzi lead-silver-zinc ore flotation was developed. The results show that the grades of Pb and Ag of galena concentrate are 55% and 1 800 g/t, respectively, while the recoveries of Pb and Ag are 86.5% and 65%, respectively, the grade of Zn of marmatite concentrate is 42.5%, and the recovery of Zn is 91.25%.
Key words: flotation; pulp potential; N,N’ diphenylamino-dithiolphosphoric acid; lead-silver-zinc ores
1 Introduction
In the past decade, much progress has been made in understanding the reactions of sulfide minerals with xanthates. Many electrochemical techniques have been employed to study the reaction mechanism of minerals (such as pyrite, galena and chalcopyrite) with xanthate reagents and played an important role in sulfide mineral flotation[1-6].
However, the application of electrochemical control technology in mineral processing industry is slow[7-8]. Now, two types of control methods have been developed to adjust the pulp potential: one is the addition of oxidants and reductants, the other is an outside polarized electrode, and both of them have some disadvantages, such as difficulty to stabilize potential and low efficiency of polarized potential. Developed by Central South University, China, Potential Control Flotation(PCF) technology[7,9-10] has been applied successfully in galena flotation of complex lead-zinc-iron sulfide ores. Under appropriate pulp potential in PCF process, the flotation speed is fast and the flotation flowsheet is simpler than commonly used ones. The key factor of PCF is the redox reactions in the system, and according to the mixed potential theory, in the grinding-flotation system, redox reactions of sulfide minerals in pulp had two situations: local cell and galvanic interaction. However, the high dosage of lime was used to modify pH and φp, and it’s common sense that silver is sensitive to lime. It can be seen from Table 1 that, the concentrate and recovery of lead are increased greatly, while silver recovery is decreased remarkably.
Table 1 Flotation performance before and after adoption of PCF flotation strategy

This paper presents a Pulp Potential Control Flotation by Stages technique to improve the flotation performance of the lead-silver-zinc ores, especially enhance the grade and recovery of silver. The performance of the control system is given for the flotation of a complex lead-silver-zinc sulfide ore from Mengzi Mining and Metallurgy Group, Yunan Province, China.
2 Experimental
2.1 Materials
The single mineral and complex ore were provided by Mengzi Mining and Metallurgy Group, Yunnan Province, China. Mengzi ore body has two lodes, which contains the valuable minerals, such as galena, marmatite, cassiterite, pyrite, pyrrhotite, and precious metals silver and indium.
The lump sample was crushed and dry screened to 1 mm. 600 g of the crushed ore was ground in a steel mill with 360 g water, and the grinding time was 5 min to get a sample 68% passing 0.074 mm. The mineralogy of the ore sample shows that the main metal minerals are galena, marmatite, cassiterite, pyrite and pyrrhotite and the main gangue are quartz, feldspar and calcite. The chemical composition of the complex lead-silver-zinc sulfide ore sample is listed in Table 2. The oxidation rate of lead minerals is about 15.32%. In this deposit, the value of associated silver is almost as much as that of the lead and zinc. Electron microprobe investigations indicate that the majority of silver in the ore was disseminated finely in galena, part of which comparatively aggregated into small granule, while only a small portion of silver was in marmatite and pyrite.
Table 2 Chemical composition of complex Pb-Ag-Zn sulfide ore sample (mass fraction, %)
1) g/t.
2.2 Flotation experiments
The flotation tests of the pure mineral were conducted in 40 mL small cells under atmosphere. A sample of 2.0 g for each experiment was weighted before its surface was cleaned by ultrasonic generator for 5 min to remove the oxidation film. The flotation experiments of crude ores were carried out with 600 g samples in a 1.5 L cell using the XDF machine for flotation. N,N’ diphenylamino-dithiolphosphoric acid, sodium diethyl dithiocarbamate and sodium butyl xanthate were used for the complex ore flotation. And ZnSO4 and Na2SO3 were used as depressant. Lime was used to modify pH and φp. The products from the flotation experiments of the complex ore sample were analyzed. All potentials reported are versus the standard hydrogen electrode(SHE) assuming that the standard electrode potential of the calomel electrode is 0.245 V.
3 Results and discussion
Mengzi Mining and Metallurgy Corporation has two concentrators. The flow sheet is shown in Fig.1, and the processing capacity of each concentrator is 2 000 t/d. Since July 2004, the improvement achieved by the adoption of the Potential Control Flotation technology, is compared with the traditional technology.

Fig.1 PCF process in concentrator of Mengzi lead-silver-zinc ore
It can be seen from Table 3 that Pb, Zn flotation recovery and the grade of the concentrate are improved obviously by PCF technology; on the contrary, the flotation recovery and concentrate of Ag are decreased clearly. The result is similar to other report in the Nanjing concentrate (listed in Table 1).
Table 3 Comparisons of OPCF and traditional flotation in concentrator of Mengzi lead-silver-zinc ore

Recently, in order to improve the silver flotation performance in the lead-silver-zinc ores, Central South University developed a new technology, Pulp Potential Control Flotation by Stages.
3.1 Effects of pH, collector type and pulp potential on flotation
Three types of collector were studied, namely sodium butyl xanthate, sodium diethyl dithiocarbamate (DDTC) and N,N’ diphenylamino-dithiolphosphoric acid (NNDDC). All the collector concentrations were kept constant at 45 g/t, and pH was adjusted to be 9.0.
Fig.2 shows that the maximum lead recovery (86%) was obtained with xanthate then DDTC followed with 83.1% lead recovery. Low recovery of 80% was obtained with NNDDC but grade of lead was in the maximum at 23.5%. Fig.3 shows that the maximum silver recovery (72%) was obtained with NNDDC or DDTC+NNDDC. NNDDC was developed by Beijing General Research Institute of Mining & Metallurgy, China[11]. The molecular formula is (C6H5NH)2PSSH, and its relative molecular mass is 280. It was widely used as a collector for lead-zinc complex ores flotation in China. LI et al[11] reported that NNDDC had good selectivity for galena and silver flotation.
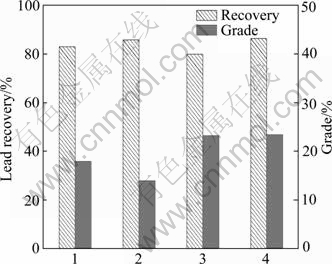
Fig.2 Lead recovery and grade for Mengzi lead-zinc-silver ore with different collectors at pH 9.0: 1—DDTC; 2—BX; 3—NNDDC; 4—DDTC and NNDDC

Fig.3 Silver recovery and grade for Mengzi lead-zinc-silver ore with different collectors at pH 9.0: 1—DDTC; 2—BX; 3—NNDDC; 4—DDTC and NNDDC
The flotation behaviors of galena, marmatite, pyrrhotite and pyrite in the presence of NNDDC are shown in Fig.4. The galena exhibits high floatability when the pH is below 9.0, and the recovery of galena is larger than 90%. It deceases obviously at high alkaline solution, for example, the recovery is only 43% at pH 12.5. NNDDC is easily decomposed to C6H6NH2, Na2S and Na3PO4 in high alkaline solution, as shown below:
(C6H6NH)2PSSH+7H2O→2C6H6NH2+Na3PO4+2Na2S+3H2O (1)
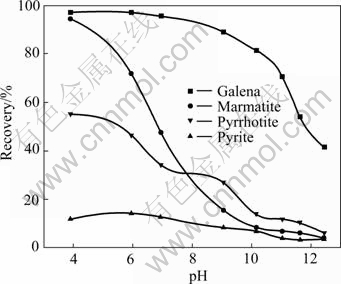
Fig.4 Effect of pH on recovery of sulfide minerals ([NNDDC]= 104 mol/L)
In the whole pH range, the recovery of marmatite decreases significantly, from 95% (pH 4) to 8% (pH 12.5). The recovery of pyrrhotite also decreases quickly. Pyrite nearly could not be floated. When pH is about 9.0, NNDDC exhibits not only high selectivity for galena, but also for silver in complex ore flotation, as shown in Fig.3. So NNDDC is more favorable than xanthate and DDTC both in the regard of recovery and grad.
Using dithiocarbamates or xanthates alone, the metal recovery is found to be cow. Therefore, dithiocarbamates are used as secondary collector with xanthates to improve both grade and recovery[12]. In this study, as shown in Fig.2, NNDDC and DDTC (2?1) were used together to increase the recovery and grade of galena significantly, while the flotation behavior of silver does not change much compared with using NNDDC alone (Fig.3).
The adsorption of collectors onto sulfide minerals is recognized to occur through an electrochemical mechanism. Electrochemical potential is considered an important parameter in controlling the recovery and selectivity of sulphide minerals during flotation. It is shown that the high floatability of galena with NNDDC as a collector is ascribed to anode oxidizing products. The range of optimum electrode potential in the flotation system was from the beginning of NNDDC anode oxidation to the end of galena anode oxidation.
It can be seen from Fig.5 that the flotation behavior of galena has a remarkable difference compared with pyrite, pyrrhotite and marmatite. Galena exhibits higher floatability in wider potential region using NNDDC as a collector at pH 8.8. The flotation recovery of galena reaches maximum at 0.3 V, but the recovery falls when the potential is higher than 0.45 V. The recoveries of pyrrhotite and pyrite are marginal, and the recovery of marmatite is about 20%.
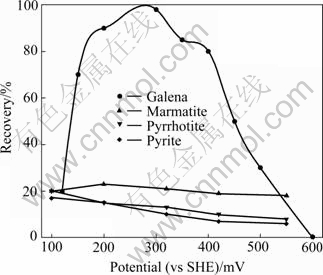
Fig.5 Effect of potential on flotation of sulfide minerals in presence of NNDDC at pH 8.8 ([NNDDC]=10-4 mol/L)
The flotation of Mengzi lead-silver-zinc ore demonstrates a marked dependency on φp when using NNDDC as a collector (Fig.6). The current changes of lead and silver are the same, and the φp of lead and silver in the maximum recovery is in the region of 280-320 mV. At φp values not in this range, there is a significant decrease in recovery. In the whole φp range, the recoveries of Zn and Fe are very low.
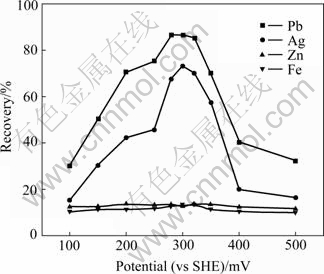
Fig.6 Effect of potential on recovery of elements from Mengzi lead-zinc-silver ore (NNDDC 40 g/t, pH 8.8)
The pulp potential is related to pH value of the flotation (Fig.7), and it decreases with increasing pH value. When pulp pH value reaches 12.5, the pulp potential decreases to 0.145 V. The flotation behavior of lead and silver minerals in the Mengzi lead-silver-zinc ore is greatly affected by the pH value. Both lead and silver recoveries decease at high alkaline values. At the pH value of 12.5, the recovery of lead is only 65%, and that of silver is only 46%. Importantly, lead and silver recoveries do not change much at pH values in the range of 7-9 using NNDDC as collector, at high recovery level.
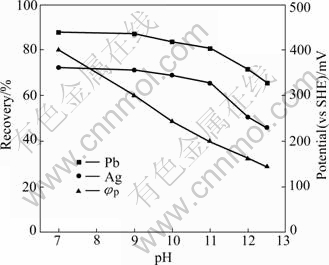
Fig.7 Effect of pH and pulp potential(φp) on recovery of lead and silver of Mengzi lead-zinc-silver ore (NNDDC 40 g/t, pH 8.8)
3.2 New electrochemical control technology
Galena flotation is fast with NNDDC and DDTC (2?1) as collectors (Fig.8). In the first 1 min, the recovery of galena is about 68% and the selectivity of galena flotation against marmatite, pyrrhotite and pyrite is high. The flotation speed of minerals containing silver is fast too, due to the fact that silver is mainly locked in galena minerals. The recovery of Ag is about 58%, whereas the recoveries of Zn (11%) and Fe (10%) are relatively low. Under such conditions, the flotation rates of lead and silver minerals are obviously much higher than those of mamartite and pyrite. In 1-5 min, the recoveries of galena and silver increase to 87.2% and 72%, respectively form a high recovery, while the recoveries of Zn and Fe increase greatly from a low recovery. During this period, the selectivity of galena flotation against marmatite, pyrrhotite and pyrite is decreased markedly. The recovery of galena and silver minerals levels off at 5-12 min, Zn recovery increases from 42% to 58%, and the recovery of Fe also increases slightly.
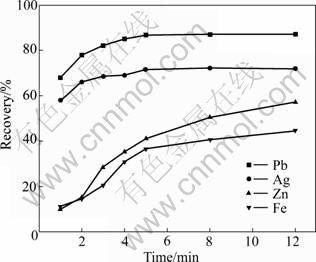
Fig.8 Effect of time on recovery of minerals from Mengzi lead-silver-zinc ore (NNDDC 30 g/t, DDTC 15 g/t, pH 8.8, φp 0.30 V)
It can be seen from the results above that for galena flotation, 5 min is enough, and the rougher flotation could be divided into two stages. At the first rougher flotation, using NNDDC (30 g/t) and DDTC (15 g/t) as collectors, the flotation is fast (only 1 min) at high pulp potential (0.3 V) and low pH value (8.8). At the second rougher flotation, using xanthate (30 g/t) and DDTC (30 g/t) as collectors, the flotation time is about 4 min, at low pulp potential (0.15 V) and high pH value (12.5). The galena oxidation rate of the Mengzi lead-silver-zinc ore is relatively high. The flotation process relies on exploiting differences in the surface chemistry between sulfide and non-sulfide minerals, and this difference becomes increasingly marginal as the sulfide mineral surfaces become oxidized. The flotation recovery decreases rapidly with increasing oxidation. At the second rougher flotation, in order to improve the recovery of lead, 200 g/t Na2S is added. The flotation flowsheet can be seen in Fig.9.
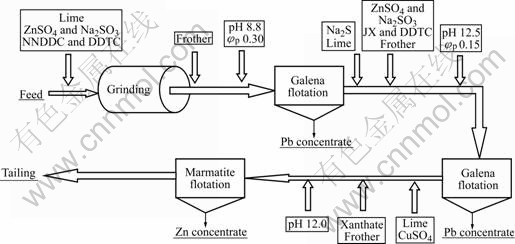
Fig.9 Flotation flowsheet of Mengzi lead-silver-zinc ore
According to the results above, the lead rougher flotation is divided into two stages (Fig.10). The first rougher concentrates are cleaned once, and the tailing’s and the second rougher concentrates are reground and cleaned. The first cleaner concentrates are cleaned once more to produce a product of over 55% lead, and the recovery of lead is 86.5% (Table 4). Regrinding of the middling products is a common practice in most flotation plants. In many mills, grinding is carried out in two or more stages. The purpose of primary grinding is to promote the maximum recovery. In the second grinding or regrinding, the major consideration is the grade of the concentrate. The first tailings and the second rougher product contain unliberated marmatite, which influence the grade of lead concentrate and decrease the recovery of zinc, so the coarse product should be reground.
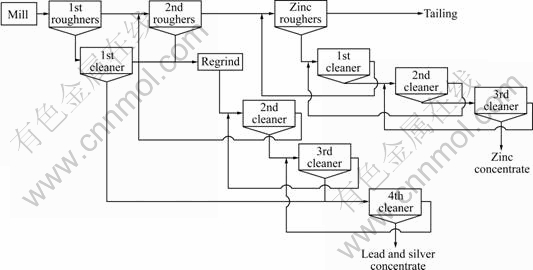
Fig.10 Flotation circuit of Meingzi lead -silver-zinc sulfide ores
Table 4 Flotation results of Mengzi ore using staged potential control flotation technology

After flotation of the galena, the tailings are treated with copper sulphate, which reactivates the surface of the zinc mineral(marmatite), allowing them to be floated off. Lime is used in the zinc flotation to depress pyrite and pyrrhotite, but it has great depressing effect on the activated marmatite at high pH. Rougher zinc concentrate are triple cleaned to produce a product of 42.5% zinc.
4 Conclusions
1) NNDDC has a good selectivity for galena flotation. The flotation recovery of galena reaches maximum at pH 8.8 and potential of 0.3 V with NNDDC as a collector. Using DDTC and NNDDC as mixed collectors, both the recovery and grade of Pb and Ag are increased.
2) The flotation behavior of lead and silver minerals in the Mengzi lead-silver-zinc ore complex ores is greatly affected by the pH and φp. Both Pb and Ag recoveries decease with the increase of pH and the decrease of φp.
3) Galena flotation is fast with NNDDC and DDTC as collectors. In the first minute, the recovery of galena is about 68% and the selectivity of galena flotation against Zn and Fe minerals is high. The selectivity in the flotation of galena and silver minerals from the complex ore is significantly improved under conditions of Pulp Potential Controlled by Stages compared with Potential Control Flotation.
References
[1] RALSTON J. Eh and its consequences in sulfide mineral flotation [J]. Minerals Engineering, 1994, 4: 859-878.
[2] HINTIKKA V V. Potential control in flotation of sulfide minerals and precious metals [J]. Minerals Engineering, 1995, 8: 1151-1158.
[3] QIN Wen-qing, LI Quan, QIU Guan-zhou, XU Ben-jun. Elecro- chemical oxidation of pyrrhotite in aqueous solution [J]. Trans Nonferrous Met Soc China, 2005, 15(5): 1279-1290.
[4] WOODS R. Electrochemical potential controlling flotation [J]. Mineral Engineering, 2003, 2: 152-162.
[5] QIN Wen-qing, QIU Guan-zhou, HU Yue-hua, XU Jing. Kinetics of electrochemical process of galena electrode in diethyldithiocar- bamate solution [J]. Trans Nonferrous Met Soc China, 2001, 11(4): 587-590.
[6] BUSWELL A M, BRADSHAW D J, HARRIS P J, EKMEKCI Z. The use of electrochemical measurements in the flotation of a platinum group minerals(PGM) bearing ore [J]. Minerals Engineering, 2002, 15: 395-404.
[7] GU Guo-hua, HU Yue-hua, WANG Hui. Original potential flotation of galena and its industrial application [J]. Cent South Univ Technol J, 2002, 9: 91-94.
[8] QIN Wen-qing, QIU Guan-zhou, HU Yue-hua. Dynamics of eletrodeposition of tetraethylthioram disulphide(TETD) on pyrite surface [J]. Journal of Central South University of Technology, 2001, 8(3): 164-167.
[9] GU Guo-hua, HU Yue-hua, WANG Hui. Potential control flotation of galena in strong alkaline media [J]. Journal of Central South University of Technology, 2002, 9(1): 61-64.
[10] WANG D Z, QIN W Q, GU G H. Electrochemistry of flotation-the potential control flotation technology of sulfide minerals [C]// CIM 23th International Mineral Processing Congress, Turkey, 2006: 665-674.
[11] WANG Fu-liang, LI Feng-lou. Electrochemical study on N,N’ diphenylamino-dithiolphosphoric acid-galena flotation system [J]. Nonferrous Metals J, 1998, 50: 13-23. (in Chinese)
[12] BULATOVIC S M, WYSLOUZIL D M. Selection of reagent scheme to treat massive sulphide ores [C]// CIM 14th International Mineral Processing Congress, Canada, 1982: 17-23.
Corresponding author: HE Ming-fei; Tel: +86-15887733998; E-mail: hemingfei@126.com
(Edited by YANG Bing)