Trans. Nonferrous Met. Soc. China 23(2013) 3568-3574
Microstructural evolution of Al-Zn-Mg-Zr alloy with trace amount of Sc during homogenization treatment
Bo LI 1, Qing-lin PAN1,2, Yun-jia SHI1, Chen LI1, Zhi-min YIN1
1. School of Materials Science and Engineering, Central South University, Changsha 410083, China;
2. Key Laboratory of Nonferrous Materials Science and Engineering of Ministry of Education, Central South University, Changsha 410083, China
Received 20 July 2013; accepted 25 October 2013
Abstract: The microstructural evolution of Al-Zn-Mg-Zr alloy with trace amount of Sc during homogenization treatment was studied by means of metallographic analysis, scanning electron microscopy (SEM), energy dispersive X-ray (EDX) and differential scanning calorimetry (DSC). The results show that serious dendritic segregation exists in studied alloy ingot. There are many eutectic phases with low melting-point at grain boundary and the distribution of main elements along interdendritic region varies periodically. Elements Zn, Mg and Cu distribute unevenly from grain boundary to the inside of alloy. With increasing the homogenization temperature or prolonging the holding time, the residual phases are dissolved into matrix α(Al) gradually during homogenization treatment, all elements become more homogenized. The overburnt temperature of studied alloy is 476.7 °C. When homogenization temperature increases to 480 °C, some spherical phases and redissolved triangular constituents at grain boundaries can be easily observed. Combined with microstructural evolution and differential scanning calorimeter, the optimum homogenization parameter is at 470 °C for 24 h.
Key words: Al-Zn-Mg-Sc-Zr alloy; dendritic segregation; homogenization; residual phases; overburnt temperature; microstructural evolution
1 Introduction
The Al-Zn-Mg alloys with trace amounts of Sc and Zr are extremely attractive structural materials for application in aerospace, nuclear energy and ship industry because of their high strength, good corrosion resistance and welding performance [1-3]. In the past several decades, a number of research groups have paid attention to microstructural evolution and mechanical properties of Al-Zn-Mg alloy with trace amounts of Sc and Zr. These researches showed that adding minor Sc, Zr in aluminum alloys can refine grain and increase tensile strength, which is attributed to the presence of coherent, L12-ordered Al3(Sc,Zr) particles [4-6].
As is well known, microstructural evolution and mechanical properties of Al-Zn-Mg alloys are sensitive to the structure of alloy ingot, heat treatment and subsequent deformation conditions, etc. A considerable amount of massive un-dissolved secondary phases and dendritic segregation are inevitable in the as-cast microstructure. In order to obtain good processing properties and service performance, the as-cast alloys should be homogenized before subsequent processing [7,8]. Thus, the homogenization temperature and holding time play a very important role in the dissolution of the residual phases during homogenization treatment. DENG et al [9] investigated the intermetallic phase evolution of 7050 aluminum alloy during homogenization. TAMARA et al [10] studied the microstructure evolution of a modified AA5083 aluminum alloy during a multi-stage homogenization treatment. TOTIK and GAVGALI [11] researched the effect of homogenization treatment on the hot workability between the surface and center of AA 2014 ingots.
The purpose of the present study is to investigate the microstructural evolution of Al-Zn-Mg-Zr alloy with trace amount of Sc during homogenization treatment. The effects of homogenization temperature and holding time on the microstructural evolution are also studied, from which optimum homogenization treatment parameter can be concluded.
2 Experimental
The nominal composition of Al-Zn-Mg-Zr alloy with trace amount of Sc is given in Table 1. The cast ingot was prepared with pure Al, pure Zn, pure Mg and Al-Mn, Al-Cu, Al-Sc, Al-Zr master alloys, by semi-continuous casting in a crucible furnace. Specimens with dimensions of 12 mm × 12 mm × 15 mm were wire- cut from the center of ingot. The specimens were homogenized at 450, 460, 465, 470, 475 and 480 °C for 24 h, respectively. And then at the optimized temperature, the specimens were homogenized for 8, 16, 24 and 32 h. All the homogenized specimens were air-cooled to room temperature.
Table 1 Nominal composition of studied alloy (mass fraction, %)

The microstructures of studied alloy were analyzed by optical microscopy (OM), scanning electron microscopy (SEM), and energy dispersive X-ray (EDX) spectrometry. The SEM specimens were prepared through a conventional mechanical grinding and polishing, followed by etching with Keller reagent (2 mL HF + 3 mL HCl + 5 mL HNO3 + 190 mL H2O) for OM observation. The analyses of SEM and EDX were carried out on a Philips Sirion 20 and a Finder-1000, respectively. And DSC analysis was carried out on a SDT-Q600 differential scanning calorimeter.
3 Results and discussion
3.1 As-cast microstructure
Figure 1 shows the microstructures of as-cast alloy. It has a typical ingot structure consisting of dendritic α(Al) phase (Fig. 1(a)). Serious dendritic segregation exists in the alloy ingot. Table 2 lists the results of EDX analysis. It can be seen that a large number of residual phases exist at grain boundaries. The white secondary phase shown in point A of Fig. 1(b) was identified as Zn- and Mg-rich non-equilibrium aluminides, which may be the mixture of supersaturated solid solution α(Al), h-MgZn2, and T-Mg32(Al, Zn)49. The grey phase is the impurity phase (point B), and it may be the matrix α(Al) with solute of elements Zn, Mg, Fe [12-15].
Figure 2 shows the SEM image and the element distribution maps of Zn, Mg, and Cu (brightness is proportional to elemental concentration) in as-cast alloy.

Fig. 1 Microstructures of as-cast alloy
Table 2 Chemical composition of secondary phases in Fig. 1(b) for studied alloy
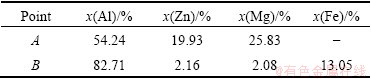
It can be found that the distribution maps exhibit the relative Zn, Mg, and Cu concentrations, and the segregation degrees of Zn, Mg and Cu at grain boundaries are different. The concentration of the elements decreases from grain boundary to inside of the studied alloy. Therefore, a homogenization treatment is necessary to eliminate severe dendritic segregation in as-cast alloy. Generally, the relationship between the diffusion coefficient and the temperature can be described as follows:
(1)
where D0 is the diffusion coefficient; Q is the diffusion activation energy; T is the thermodynamic temperature; and R is the mole gas constant. It can be seen from Eq. (1) that the higher the temperature is, the larger the diffusion coefficient will be, which makes it easier to eliminate the dendritic segregation in the as-cast alloy. Meanwhile, the temperature cannot surpass the overburnt temperature of the studied alloy, so it is very important for practical application to optimize homogenization temperature.

Fig. 2 SEM image (a) and elements distribution of Zn (b), Mg (c) and Cu (d) in as-cast alloy
3.2 DSC analysis of as-cast and homogenized alloys
The DSC curves of as-cast ingot and specimens homogenized at different temperatures for 24 h are shown in Fig. 3. The endothermic peak can be observed in the as-cast alloy, sited at 476.7 °C. With increasing the homogenization temperature, the endothermic peak at 476.7 °C disappears gradually after homogenization treatment. It may be corresponding to the dissolution of some non-equilibrium phases during homogenization treatment. It can be included that the homogenization temperature of studied alloy should not surpass the temperature of 476.7 °C, which is generally called the overburnt temperature of studied alloy.

Fig. 3 DSC curves of as-cast ingot and specimens homogenized at different temperatures
3.3 Microstructure of homogenized alloy
3.3.1 Effect of homogenization temperature on microstructures
Figure 4 shows BSE SEM microstructures of as-cast ingot and specimens homogenized at different temperatures for 24 h. It suggests that microstructural evolution of the alloy is determined significantly by homogenization temperature. With increasing the homogenization temperature, the volume fraction of residual phases is significantly decreased, and the grain boundaries become more thin and clear. The continuous residual phases along grain boundaries have turned to be uncontinuous ones, as shown in Figs. 4(c) and (d). When the specimen is homogenized at 470 °C, the dendritic- network structure reduces and most residual phases are spread homogeneously in matrix α(Al) (Fig. 4(d)). But when homogenization temperature was increased to 480 °C, the melting compounds both at grain boundaries and in triple conjunctions can be observed, and the specimen is overburnt [16-18] (Fig. 4(f)). According to the microstructure evolution, it can be included that the suitable temperature for homogenization treatment is 470 °C.
3.3.2 Effect of homogenization time on microstructures
The BSE SEM and optical images of specimens homogenized at 470 °C for different time are shown in Fig. 5. With prolonging homogenization time, the volume fraction of the dendritic-network structure is reduced gradually, and the non-equilibrium phases at the grain boundaries dissolve gradually. The residual phases become small and sparse. When the homogenization time increased, to 32 h, no obvious dissolution of residual constituents is observed (Figs. 5(g) and (h)), and the microstructure has no significant change compared with that homogenized for 24 h [19-21]. As a result, the reasonable homogenization time at 470 °C can be determined to be 24 h.

Fig. 4 BSE SEM images of studied alloy homogenized at different temperatures for 24 h
3.4 Line scanning analysis of homogenized alloy
The line scanning traces of as-cast and homogenized alloys are shown in Fig. 6. Elements Zn, Mg and Cu distribute unevenly from grain boundary to the inside of alloy. After homogenization treatment, it can be found that the segregation of the main elements Zn, Mg and Cu is almost eliminated, and the elements distribution is homogeneous from grain boundary to the inside of the studied alloy [22-25]. Thus, the optimum homogenization parameter is at 470 °C for 24 h.

Fig. 5 BSE (a, c, e, g) and optical (b, d, f, h) microstructures of studied alloy homogenized at 470 °C for different time

Fig. 6 Line scanning analysis of studied alloy
4 Conclusions
1) Severe dendritic segregation exists in the studied alloy ingot. The main residual phases are h-MgZn2 and T-Mg32(Al, Zn)49 phases, which precipitate along grain boundaries. The main elements Zn, Mg and Cu distribute unevenly from grain boundary to the inside of as-cast alloy.
2) By increasing homogenization temperature and/ or prolonging holding time of homogenization, the residual phases are dissolved into matrix α(Al) gradually, and the grain boundaries become sparse and the distribution of all the elements becomes more homogenized.
3) The overburnt temperature of Al-Zn-Mg-Zr alloy with trace amount of Sc is 476.7 °C. The optimum homogenization treatment is at 470 °C for 24 h.
References
[1] ZOU Liang, PAN Qing-lin, HE Yun-bin, WANG Chang-zhen, LIANG Wen-jie. Effect of minor Sc and Zr addition on microstructures and mechanical properties of Al-Zn-Mg-Cu alloys [J]. Transactions of Nonferrous Metals Society of China, 2007, 17: 340-345.
[2] LI Bo, PAN Qing-lin, ZHANG Zhi-ye, LI Chen. Characterization of flow behavior and microstructural evolution of Al-Zn-Mg-Sc-Zr alloy using processing maps [J]. Materials Science and Engineering A, 2012, 556: 844-848.
[3] KIM J H, KIM J H, YEOM J T, LEE D G, LIM S G, PARK N K. Effect of scandium content on the hot extrusion of Al-Zn-Mg-(Sc) alloy [J]. Journal of Materials Processing Technology, 2007, 187-188: 635-639.
[4] DENG Ying, YIN Zhi-min, DUAN Jia-qi, ZHAO Kai, TANG Bei, HE Zhen-bo. Evolution of microstructure and properties in a new type 2 mm Al-Zn-Mg-Sc-Zr alloy sheet [J]. Journal of Alloys and Compounds, 2012, 517: 118-126.
[5] DEV S, ARCHIBALD STUART A, RAVI DEV KUMAAR R C, MURTY B S, PRASAD RAO K. Effect of scandium additions on microstructure and mechanical properties of Al-Zn-Mg alloy welds [J]. Materials Science and Engineering A, 2007, 467: 132-138.
[6] LIU Bing, PENG Chao-qun, WANG Ri-chu, WANG Xiao-feng, LI Ting-ting. Recent development and prospects for giant plane aluminum alloys [J]. The Chinese Journal of Nonferrous Metals, 2010, 20(9): 1705-1715. (in Chinese)
[7] ZHONG Z G, ZUO X R, WENG Y G, SONG T F, WANG M X, LIU Z X, YANG S. The application situation and the study development of the wrought aluminum alloy’s homogenization [J]. Light Alloy Fabrication Technology, 2006, 34(1): 10-13. (in Chinese)
[8] Foroozmehr A, Kermanpur A, Ashrafizadeh F, Kabiri Y. Investigating microstructural evolution during homogenization of the equiatomic NiTi shape memory alloy produced by vacuum arc remelting [J]. Materials Science and Engineering A, 2011, 528: 7952-7955.
[9] DENG Ying, YIN Zhi-min, CONG Fu-guan. Intermetallic phase evolution of 7050 aluminum alloy during homogenization [J]. Intermetallics, 2012, 26: 114-121.
[10] TAMARA R, MILJANA P, ENDRE R. Microstructure evolution of a modified AA5083 aluminum alloy during a multistage homogenization treatment [J]. Materials Characterization, 2012, 65: 16-27.
[11] Totik Y, Gavgali M. The effect of homogenization treatment on the hot workability between the surface and the center of AA 2014 ingots [J]. Materials Characterization, 2003, 49: 261-268.
[12] FAN X G, JIANG D M, MENG Q C, LI Z. The microstructural evolution of an Al-Zn-Mg-Cu alloy during homogenization [J]. Materials Letters, 2006, 60: 1475-1479.
[13] XU Guo-fu, MOU Shen-zhou, YANG Jun-jun, JIN Tou-nan, NIE Zuo-ren, YIN Zhi-min. Effect of trace rare earth element Er on Al-Zn-Mg alloy [J]. Transactions of Nonferrous Metals Society of China, 2006, 16(3): 598-603.
[14] WU L M, WANG W H, HSU Y F, TRONG S. Effects of homogenization treatment on recrystallization behavior and dispersoid distribution in an Al-Zn-Mg-Sc-Zr alloy [J]. Journal of Alloys and Compounds, 2008, 456: 163-169.
[15] MAO Jian-wei, JIN Tou-nan, XU Guo-fu, NIE Zuo-ren. As-cast microstructure of Al-Zn-Mg and Al-Zn-Mg-Cu alloys added erbium [J]. Transactions of Nonferrous Metals Society of China, 2005, 15(6): 1341-1345.
[16] WANG Tao, YIN Zhi-min, SUN Qiang. Effect of homogenization treatment on microstructure and hot workability of high strength 7B04 aluminium alloy [J]. Transactions of Nonferrous Metals Society of China, 2007, 17(2): 335-339.
[17] LIU Xiao-yan, PAN Qing-lin, FAN Xi, HE Yun-bin, LI Wen-bin, LIANG Wen-jie. Microstructural evolution of Al-Cu-Mg-Ag alloy during homogenization [J]. Journal of Alloys and Compounds, 2009, 484(1-2): 790-794.
[18] ZHANG Xin-ming, HAN Nian-mei, LIU Sheng-dan, SONG Feng-xuan, ZENG Rui-lin, HUANG Le-yu. Inhomogeneity of texture, tensile property and fracture toughness of 7050 aluminum alloy thick plate [J]. The Chinese Journal of Nonferrous Metals, 2010, 20(2): 202-209. (in Chinese)
[19] DENG Yun-lai, WAN Li, WU Li-hui, ZHANG Yun-ya, ZHANG Xin-ming. Microstructural evolution of Al-Zn-Mg-Cu alloy during homogenization [J]. Journal of Materials Science, 2011, 46: 875-881.
[20] WANG Shao-hua, MENG Ling-gang, YANG Shou-jie, FANG Can-feng, HAO Hai, DAI Sheng-long, ZHANG Xing-guo. Microstructure of Al-Zn-Mg-Cu-Zr-0.5Er alloy under as-cast and homogenization conditions [J]. Transactions of Nonferrous Metals Society of China, 2011, 21: 1449-1454.
[21] LI Nian-kui, CUI Jian-zhong. Microstructural evolution of high strength 7B04 ingot during homogenization treatment [J]. Transactions of Nonferrous Metals Society of China, 2008, 18: 769-773.
[22] MONDAL C, MUKHOPADHYAY A K. On the nature of T (Al2Mg3Zn3) and S(Al2CuMg) phases present in as-cast and annealed 7055 aluminum alloy [J]. Materials Science and Engineering A, 2005, 391: 367-376.
[23] FAN X G, JIANG D M, MENG Q C, ZHANG B Y, WANG T. Evolution of eutectic structures in Al-Zn-Mg-Cu alloys during heat treatment [J]. Transactions of Nonferrous Metals Society of China, 2006, 16: 577-581.
[24] LI Wen-bin, PAN Qing-lin, XIAO Yan-ping, HE Yun-bin, LIU Xiao-yan. Microstructural evolution of ultra-high strength Al-Zn-Cu-Mg-Zr alloy containing Sc during homogenization [J]. Transactions of Nonferrous Metals Society of China, 2011, 21: 2127-2133.
[25] Xu C, Zheng M Y, Xu S W, Wu K, Wang E D, Kamado S, Wang G J, Lv X Y. Microstructure and mechanical properties of rolled sheets of Mg-Gd-Y-Zn-Zr alloy: As-cast versus as-homogenized [J]. Journal of Alloys and Compounds, 2012, 528: 40-44.
均匀化处理对含钪Al-Zn-Mg-Zr合金组织的影响
李 波1,潘清林1,2,史运嘉1,李 晨1,尹志民1
1. 中南大学 材料科学与工程学院,长沙 410083;
2. 中南大学 有色金属材料科学与工程教育部重点实验室,长沙 410083
摘 要:采用金相分析、扫描电镜、能谱分析、DSC等手段研究含钪Al-Zn-Mg-Zr合金均匀化态显微组织的演变。结果表明:在合金铸态组织中存在大量的枝晶偏析,在晶界处存在很多低熔点共晶相,主要元素在枝晶内部区域呈周期性变化;合金中元素Zn、Mg和Cu在晶内及晶界分布不均匀;在均匀化过程中,随着均匀化温度的升高或时间的延长,残留相逐渐溶入基体,元素分布逐渐均匀。合金的过烧温度为476.7 °C。当均匀化温度升高到480 °C时,合金中开始出现复熔球和三角晶界。综合考虑:合金的最佳均匀化制度为470 °C,24 h。
关键词:Al-Zn-Mg-Sc-Zr合金;枝晶偏析;均匀化;残留相;过烧温度;组织演变
(Edited by Hua YANG)
Foundation item: Project (2012CB619503) supported by the National Basic Research Program of China
Corresponding author: Bo LI; Tel: +86-731-88830933; E-mail: liboiec@sohu.com
DOI: 10.1016/S1003-6326(13)62902-7