J. Cent. South Univ. Technol. (2008) 15: 54-58
DOI: 10.1007/s11771-008-0012-0

Synthesis of P(St-BA-MAA-SPAA) nano-latex and its application in high anti-corrisive coating
LIU Hai-feng(刘海峰), SHENG Ming-shuang(盛明爽), PAN Zhao-ji(潘肇基),
QIU Da-jian(邱大健), GUO Zhi-hua(郭志华), GAN Fu-xing(甘复兴)
(College of Resources and Environmental Science, Wuhan University, Wuhan 430072, China)
Abstract:A novel zinc-rich pigment based on P(St-BA-MAA-SPAA) nano-latex was obtained, which is suitable for the use in hot alkali liquid medium. The nano-latex was synthesized by active emulsifier latex polymerization method with monomers of styrene (St), butylacrylate (BA), methylacrylic acid(MAA) in the presence of active emulsifier 3-sulfopropylacrylate(SPAA). The synthesis condition and properties of the latex were investigated. And the anti-corrosive property of the resultant zinc-rich coating was studied. The results show that the nano-latex is self-stabilized and has a narrow particle diameter distribution, the average diameter of the latex particles is 71 nm. Zinc powders can be evenly dispersed in the nano-latex, which indicates that the P(St-BA-MAA-SPAA) nano latex can be used as the binder of zinc-rich coating. The resultant zinc-rich coating is able to resist the invasion of hot alkali solution(the temperature is 95 ℃ and the pH value is 14) for 480 h and the exposure time in salt spray is 1 200 h. Moreover, the coating shows good thermal conductivity and static electricity properties, its thermal conductivity and electric resistivity are 21-37 W/(m·K) and 6.7×105-3.5×106 Ω·cm, respectively.
Key words: latex polymerization; active emulsifier; nano latex; anti-corrosive coating
1 Introduction
In recent years, anti-corrosive coatings made by nano-latex have attracted much attention for their excellent properties[1-3]. It is well known that in traditional latex polymerization method, some low molecular emulsifier should be added to stabilize the latex. However, these emulsifiers may be unfavourable for the anti-corrosive ability of coating, especially the waterproof property of the coatings will become worse. Studies of electron spectroscopy for chemical analysis(ESCA) electron spectrum[4-5] show that about 50% of the emulsifier will emerge at the interfaces between metallic substrates and the cured coatings. These emulsifiers greatly influence the adhesion of the coatings[6-7]. The research of the wet-adhesion of coatings shows that the emulsifier molecule will combine with water molecule firstly when it reaches the interface by permeation, then the adhesion between coating and substrate is lost for the existence of water. As a result, the coating will peel off, and the corrosion of substrate will occur. In order to avoid these shortcomings, the traditional emulsifiers should be modified. Among the methods reported, active emulsifier latex polymerization is of good prospect in the synthesis of high anti-corrosive coating binder[8-9]. Active emulsifiers (or polymerized emulsifier) can crosslink with
polymer chain, which prohibits the emulsifier molecules from moving during the cure process[4,10-11]. Furthermore, the active emulsifier also favors stabilizing latex and producing nano latex particles.
Hot alkali liquid medium is a kind of severely corrosive environment in industry process, the protective coatings of equipments used for hot alkali liquid transport should have high anti-corrosive ability, good thermal conductivity and static conductivity. In order to achieve this purpose, a novel zinc-rich coating was made, in which the nano-latex was synthesized by active emulsifier latex polymerization method. The nano-latex P(St-BA-MAA-SPAA) is polymerized mainly by monomers of styrene (St)[11-12], butylacrylate(BA), methylacrylic acid(MAA) in the presence of active emulsifier 3-sulfopropylacrylate(SPAA). And the properties of the zinc-rich coating based on the prepared nano latex were investigated.
2 Experimental
2.1 Materials
Chemical purity reagents used in the experiments included styrene (St), 1, 2-epoxypropane(EP), acrylic acid(AA), methylacrylic acid(MAA), butylacrylate(BA), sodium bisulfite (NaHSO3), ammonium persulfate (APS), sodium pyrosulfite (SMS), ferrous sulfate (FeSO4·7H2O),sodium lauryl sulfate (SLS), OP-10. All of them were purchased from Shanghai Guoyao Reagent Limited.
2.2 Synthesis of SPAA
The synthetic process of SPAA includes the following two steps[13]:
(1)
(2)
2.2.1 Synthesis of sodium 2-hydroxy propanesulfate
The starting materials were EP (0.82 mol), NaHSO3 (0.50 mol) and water (3.89 mol). In a 500 mL reactive flask with a stirrer, thermometer and condenser, NaHSO3 was added into water and the solution was stirred till the solid NaHSO3 dissolved, EP was then added by drops at a controlling speed, the reaction temperature was kept below 30 ℃. The reaction was maintained for 1 h. When EP dropping was finished, condenser was removed, the temperature was then raised to 75 ℃ in order to distil the unreacted EP from the solution. The flask was cooled down to room temperature and then put into ice-water bath. At last, the pure sodium 2-hydroxy propanesulfate was obtained after the product was pump-filtered and recrystallized in water .
2.2.2 Synthesis of SPAA
The prepared sodium 2-hydroxy propanesulfate and AA (the molar ratio was 1?1) were put into flask with a stirrer, thermometer and oil/water separator. Certain inhibitor(hydroquinone) was added, the reaction temperature was kept at 90 ℃. The reaction degree was tested by measuring the amount of water in oil/water separator. After the reaction finished, the rough product SPAA was obtained and purified by recrystallization. According to analysis, the mass fraction of sulphur in SPAA was 16.7%(theoretical value is 16.5%) and the melting point of SPAA was 256-258 ℃.
2.3 Preparation of P(St-BA-MAA-SPAA) nano-latex
The total mass of the mixed monomers (mass ratio of St to BA to MAA was 60?35?5) was 40 g, the mass ratio of initiator was m(APS)/m(SMS)/m(FeSO4·7H2O)= 1?1?1. Firstly, 60 g water, 0.1 g SLS and 0.2 g OP-10 were added into the reactor with a magnetic stirrer, thermometer and condenser under the condition of purging nitrogen. Then about 30% (mass fraction) of total mixed monomers and about 80%(mass fraction) of the total initiator were added. The reaction temperature was kept at 15-25 ℃. Approximately 20 min later, the seed latex became pale blue and the rest monomers and initiator mixture were added. The drop time of the rest was controlled in 2 h, then the reaction maintained for 2 h after all monomers and initiator mixture were added. At last, some ammonia water (volume ratio of ammonia to water was 1:3) was added to adjust the pH value of latex to 7-9 under quickly stirring. The final bluish transparent nano-latex was obtained and the total polymerization reaction lasted for 7 h.
2.4 Preparation of zinc-rich coating
The prepared nano latex of P(St-BA-MAA-SPAA) and zinc powder were mixed by mass ratio of 1.00?2.33. Then some pigment assistants were added. After the nano latex was agitated enough to guarantee the dispersion of zinc powder and assistants, the preparation of zinc-rich coating was finished. The coating was cured on steel board with a thickness of 35 nm in order to measure its properties.
2.5 Measurement method
Polymeric conversion rate (to total monomers ) was calculated from the following formula by measuring mass fraction of solid of latex:
η= maws/mm×100% (3)
where η is polymer conversion rate, %; ma is the mass of the total added materials, g; ws is the mass fraction of solid, %; mm is the total mass of monomer, g. Sample was taken from latex and certain inhibitor(hydroquinone) was added immediately, its solid content was measured by mass.
The emulsion particle diameter was determined by the equipment of Spectrex Laser Particle MalvernZetasizer3000[14]. The IR spectrum was measured by Fourier transform IR spectrometer (Nicolet, USA), the samples were mixed with KBr and pressed into a pellet. The morphology of the particles was examined by scanning electron microscope(SEM) (FEI, USA). The investigation of latex conventional properties was referred to Ref.[15].
3 Results and discussion
3.1 IR characterization of active emulsifier SPAA
Fig.1 shows the FT-IR spectrum of SPAA and the characteristic absorption peaks. 3 455 cm-1 is the wave- number of water absorption. 2 975 cm-1 is the wave- number of C-H stretching vibration of -CH2 and -CH3, 1 451 and 786 cm-1 are the wavenumbers of C-H stretching vibration of -CH2. 1 405 and 1 384 cm-1 are the wavenumbers of C-H stretching vibrations of -CH. 1 188, 1 045 and 614 cm-1 are the wavenumbers of S=O stretching vibration. 842 and 942 cm-1 are the wavenumbers of C-S-O stretching vibration. 1 707 cm-1 is the wavenumber of C=O stretching vibration. 1 635 cm-1 is the wavenumber of C=C stretching vibration. 1 263 cm-1 is the wave- number of C-O-C asymmetric stretching vibration of α and β unsaturated esters. From Fig.1, it can be inferred that the characteristic absorption peaks and melting point of the prepared sample is in accordance with those of SPAA.
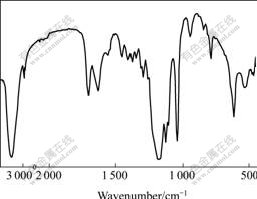
Fig.1 FT-IR spectrum of SPAA
3.2 Influence of reaction time and SPAA amount on nano-emulsion conversion rate
Conversion rate of nano-emulsion in different reaction times is presented in Fig.2. It shows that the conversion rate has a linear relation with reaction time during initial period. After 6 h, the change of conversion rate becomes slow. The reaction will stop when the reaction time goes beyond 7 h, so the best reaction time should be 7 h.
Conversion rate also changes with the change of the amount of SPAA, as shown in Fig.3. It shows that when c(SPAA)<15 mmol/L, emulsion conversion rate is very low. It is most likely due to the low content of emulsifier, which causes the lack of micelle formation and the motive power for polymerization; the other reason is that the monomers of St, BA and MAA have low activities at low temperature, and the initiation of polymerization at low concentration of SPAA is difficult.
When the concentration of SPAA increases and reaches a certain level, SPAA will be of higher polymeric activity, and the polymerization of the system will become possible and react completely. In this experiment, it is found when c(SPAA)≥90 mmol/L, agglomeration can be observed and continous adding of SPAA is adverse to the stabilizing of latex.
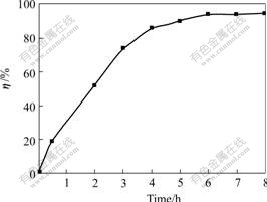
Fig.2 Relation between conversion rate and reaction time
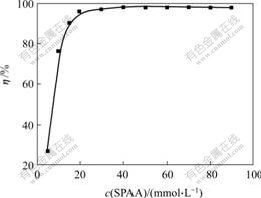
Fig.3 Effect of concentration of SPAA on conversion rate
3.3 Determination of P(St-BA-MAA-SPAA) latex particle size and latex performance
The particle diameter distribution of P(St-BA- MAA-SPAA) latex is given in Fig.4, which shows that the distribution of latex particles is narrow and the average of size is about 72 nm.
The basic performance of P(St-BA-MAA-SPAA) emulsion is listed in Table 1, which shows that the latex has good storage stability and the minimum film forming temperature(MFT) is 16.5 ℃. It can easily form film at room temperature.
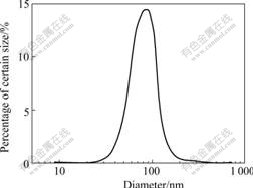
Fig.4 Particle diameter distribution of prepared nano-latex
Table 1 Performance of prepared nano-latex
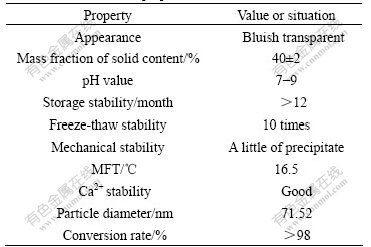
3.4 Properties of P(St-BA-MAA-SPAA) nano latex zinc-rich coating
The properties of the zinc-rich coating were tested. The results are shown in Table 2. It shows that zinc-rich coating made from P(St-BA-MAA-SPAA) nano-latex has excellent anti-corrosive performance and can bear corrosion in hot alkali solution for 480 h and resist to salt spray for 1 200 h. The electric resistivity of the coating is 6.7×105-3.5×106 Ω·cm, which is lower than that of the common organic coatings by 2-3 orders of magnitude. The coating owns better static conductivity and its thermal conductivity is 21-37 W/(m·K), which is higher than that of the common organic polymer (polyamide1010, 0.16-0.46 W/(m·K); polyimide, 0.36 W/(m·K); polyoxymethlene, 0.23 W/(m·K)) by 2 orders of magnitude[16].
Table 2 Properties of P(St-BA-MAA-SPAA) nano latex zinc- rich coating
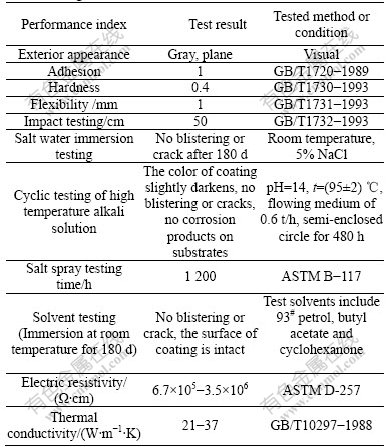
Fig.5 shows that zinc powder disperses equably in the basic material of P(St-BA-MAA-SPAA) nano-latex, indicating that the dispersion of metal zinc powder in polymer is improved as the induction of SPAA. Because there is a high content and equal dispersion of metal zinc powder in modified coating, it lowers the electric resistivity notably and improves thermal conductivity of this coating.
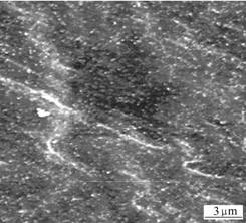
Fig.5 SEM image of P(St-BA-MAA-SPAA) nano latex zinc- rich coating
4 Conclusions
1) Using 1, 2-epoxypropane as the raw material, the active emulsifier 3-sulfopropylacrylate(SPAA) is synthesized by two steps. The product is analyzed and characterized by melting point measurement and FT-IR spectrum.
2) P(St-BA-MAA-SPAA) nano-latex is polymerized with active emulsifier latex polymerization method. At low temperature, a novel nano-latex is obtained and the distribution of particle diameter is narrow, which also has good storage stability. The influence of reaction time and SPAA amount on emulsion polymerization are studied. The results show that the reaction is completed when reaction time is over 7 h; the concentration of active emulsifier should be higher than 15 mmol/L and a high polymeric conversion rate of nano-latex can be obtained.
3) The zinc-rich coating is produced from P(St- BA-MAA-SPAA) nano-latex. Zinc powder can be equably dispersed in polymer and the coatings prepared have excellent corrosion resistance, which can bear invasion of high hot alkali solution for 480 h and salt spray over 1 200 h. Its electric resistivity is 6.7×105- 3.5×106 Ω·cm and its thermal conductivity coefficient is 21-37 W/(m·K). So it is suitable for the protection of equipment worked in the hot alkali solution.
References
[1] XU Bin-shi, LIANG Xiu-bing, DONG Shi-yun, MA Song. Progress of nano-surface engineering[J]. International Journal of Materials and Product Technology, 2003, 18(4): 338-343.
[2] ZHANG Xiao-yan, SUN Zheng-guang, HUANG Shi-qiang. The progress of preparing polymer nanocomposites by emulsion polymerization[J]. Chinese Journal of Colloid and Polymer, 2004, 22(2): 27-29. (in Chinese)
[3] ZHANG Xin-ya, SUN Zhi-juan, HUANG Hong, LI Yong-jin, LAN Ren-hua, CHEN Huan-qin. Synthesis and properties of acrylate latex modified by vinyl alkoxy siloxane[J]. Journal of Central South University of Technology, 2007, 14(5): 666-672.
[4] TORSTENSSON M, RANBY B, HULT A. The emulsifier moving during the course of coatings cured[J]. Macromolecules, 1990, 23(1): 23-31.
[5] PAN Zhao-ji, FUNKE W. A study of surface/interface properties of organic coatings by contact angle and MIR measurements[C]// 7th Asian-Pacific Corrosion Control Conference. Beijing, 1991: 645-651.
[6] FUNKE W. Protection of metals by organic coatings against corrosion to wet adhesion[C]// 7th Asian-Pacific Corrosion Control Conference. Beijing, 1991: 16-28.
[7] PAN Zhao-ji. A study of wet adhesion for organic coating[J]. Materials Protection, 1994, 27(2): 9-12. (in Chinese)
[8] CHEN Da-jun, LI Na. Synthesis of reactive emulsifiers and their emulsion copolymerization with acrylic monomers[J]. Chemical World, 2004, 45(4): 186-188. (in Chinese)
[9] ZHANG Chao-can, DU Hong-yan. Study of nano-SiO2/MMA emulsifier-free emulsion polymerization and application[J]. Chinese Journal of Colloid and Polymer, 2004, 22(4): 5-10. (in Chinese)
[10] ZHANG Li, XIE Zhi-ming, LI Zhuo-mei. Study on the room temperature curing of soap-free water-solubilized polyacrylic coating[J]. Polymeric Materials Science and Engineering, 1997, 13(3): 84-88.
[11] LORIMER J P, MASON T J, KERSHAW D, LIVSEY I, TEMPLETON-KNIGHT R. Effect of ultrasound on the encapsulation of titanium dioxide pigement[J]. Colloid Polym Sci, 1991, 269(4): 392-397.
[12] MICHALE D, WIM P J, BERND T. Copolymerization behavior and structure of styrene and polymerizable surfactants in three-component cationic microemulsion[J]. Macromolecules, 1998, 31(2): 272-280.
[13] CHEN Zheng-guo, QIAN Yong, GAO Qing, LU Sheng-jun, WANG Hai-ping. Synthesis of sodium 3-chloro-2-hydroxy propanesulfate[J]. Chinese Journal of Colloid and Polymer, 2003, 21(2): 17-18.
[14] XU Xin-lan, HU Xiao-ying, LU Nai-di. The preparation of nano-emulsion for transmitting electron microscopy and image analysis[J]. Journal of Chinese Electron Microscopy Society, 2002, 21(5): 786-787.
[15] ZHI Wei-sun. A microscopic approach to studying colloidal stability[J]. Journal of Chemical Physics, 2003, 22(119): 2399-2405.
[16] SHI An-fu, GONG Yun-biao. Engineering plastics-properties, shaping, application[M]. Shanghai: Shanghai Science and Technology Press, 1989: 68-69.
(Edited by CHEN Wei-ping)
Received date: 2007-07-10; Accepted date: 2007-08-27
Corresponding author: LIU Hai-feng, PhD; Tel: +86-27-83611279; E-mail: lhfhbxg@tom.com