
Influence of pH value on chromate-free conversion coating for magnesium alloys
WENG Wen-ping(翁文凭), CHEN Qi(陈 琦), ZHANG Hui(张 慧),
ZHONG Hao(钟 皓), YAN Yun-qi(闫蕴琪)
Suzhou Institute for Nonferrous Metals Processing Technology, Suzhou 215026, China
Received 28 July 2006; accepted 15 September 2006
Abstract: Many factors were found to have effects on the conversion coatings for AZ31 alloy, alloy the most important one in producing high quality conversion coatings is found to be the control of the pH value. The influence of pH value on the conversion coating including color, thickness, adhesion and surface morphology was studied. The performance of conversion coating was examined by cross cut test, SEM method and salt immersion. The results show that the variation of pH value causes surface treatment process unstably. The conversion coating can obtain as pH value ranging from 3.0 to 5.0, while it presents dark, thick and bad adhesion under lower pH value. The conversion coatings have good combination of thickness and adhesion when pH value ranging from 4.0 to 4.5, and it exhibits a good corrosion resistance.
Key words: magnesium alloys; AZ31 alloy; conversion coating; pH value; phosphate-permanganate
1 Introduction
As a green engineering material, magnesium alloys have many advantages and are widely used as structural materials for automobiles and aircrafts[1]. However, the poor corrosion resistance restricts the industrial applications of magnesium alloys[2-3]. The existing surface treatment technology of magnesium alloys is divided into many groups such as organic coating, metal coating, chemical converting coating and anodic oxidation. Unsatisfactorily, these methods are complicated and costly,especially the conventional conversion coatings for magnesium alloys are based on chromium compounds, which are highly toxic carcinogens[4-5]. Researchers’ awareness of chromium-free conversion coating has been made more acute by increasing popularity of environmental issues[6-7]. One of the effective alternatives is phosphate-permanganate conversion technology for magnesium alloys.
HAWK et al[8] studied the phosphate-permang
anates conversion coatings for AM60 alloy, the conversation coatings that they achieved as pH ranging from 3.9-4.3 present good corrosion resistance and adhesion ability. Up to now, researches on the surface treatments for magnesium alloys are focused on the casting alloys, and the researches on the efficient surface treatments for wrought alloys are inadequate. In this paper, the influence of pH value on the performance of the conversion coating for AZ31 alloy was analyzed by phosphate-permanganate treatment, and the relationship between conversion coating and pH value was established.
2 Experimental
Hot extrusion AZ31 alloy plates (25 mm×10 mm×3 mm) were used as specimens with compositions of 3.0%Al, 1.0%Zn, 0.20%Mn, and balance magnesium (mass fraction, %). Firstly, the specimens were mechanically polished and then washed with an alkaline detergent, degreased in a sodium hydroxide/sodium phosphate/sodium silicate (NaOH/Na3OP4/ Na2O?nSiO2?xH2O) solution. The specimens were rinsed in stirred water at each step. Immersing specimen in a bath solution formed the conversion coatings; the solution compositions and operating conditions for the phosphate-permanganate treatment are given in Table 1[9].
Table 1 Parameters of phosphate-permanganate bath for AZ31 magnesium alloy
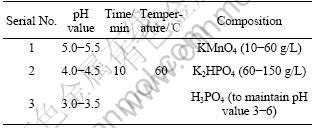
The cross-cut method was conducted to test the adhesion ability based on Japanese Industrial Standard testing methods[10]. The morphology and the compositions of conversion coating were observed by SEM method used with JSM6480 system. The cross sections of the specimens were polished by sand paper until exposing the base of magnesium alloy, and then the thickness of the conversion coating was measured by scanning electron microscopy. The corrosion resistance of the specimens after conversion treatment bath by salt solution (5%) immersing was compared, and then the rust area percentage of the specimen surface was calculated.
3 Results and discussion
3.1 Morphology of conversion coating
Fig.1 shows the transverse section of conversion coating treated with solution contains various concentration of phosphoric acid. According to Fig.1, the thickness of the conversion coatings treated in solution whose pH values are 5.0, 4.2, 3.1, are approximately by 2.0-3.0, 5.0-7.0, 20-24 μm, respectively. Obviously, the conversion-coating thickness increases with the increase of phosphoric acid content, while the coating uniformity is just reversed. Fig.2 shows the morphology of the conversion coating. Network-like cracks are obviously distributed all over the surface of the conversion layer. This type of network-like crack is generally in agreement with the observation results of KOUISNIet al[11-12]. When the phosphate-permanganate treatment solution’s pH value is 5.0, there are two different areas A and B in the conversion coating as shown in Fig.2(a), which indicates that the conversion coating is neither uniform nor integrated in area A compared with area B. There is no area A in the conversion coating as long as its solution’s pH value is 4.2. Moreover, the size of crack area decreases as shown in Fig.2 (b). As shown in Fig.2(c) the A area reduces and the number of area B decreases when the treatment solution’s pH value is 3.1. In other words, the conversion coating of AZ31 magnesium alloy is quite coarse with the decrease of phosphoric acid content in the treatment solution. The uniformity of conversion coating is improved with the increase of phosphoric acid content.
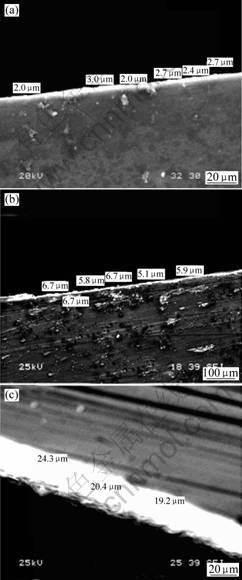
Fig.1 Transverse sections of conversion coating treated with solution containing various concentrations of phosphoric acid: (a) pH=5.0; (b) pH=4.2; (c) pH=3.1
3.2 Compositions of conversion coating
Fig.3 gives the typical concentration profiles of O, Mg, P and Mn in AZ31 magnesium alloy along the lines shown in the micrographs that measured using EDS analysis. It’s evident that magnesium concentration near to crack area is high and decreases with the increase of the distance from the crack. The magnesium content in crack area is more than 60% mass of the coating layer. Contrarily, the content of O, P and Mn near crack is low and increases with the increase of the distance from the crack area. The results confirm that the crack in the coating does not penetrate through the coating though the coating layer in those areas is very thin.
3.3 Adhesion and corrosion resistance of conversion coating
There are many factors in the process that are found to have effects on the adhesive ability of the final coatings. The most important one in producing best quality conversion coatings is found to be the control of the pH value. Adhesion of the coating and matrix will be good enough to meet many needs if pH value of treatment bath is above 3.While pH value is below 3, not only the surface of the coating layer is incompact but also adhesion is unsatisfactory. The results of cross-cut test which is based on Japanese Industrial Standard[6] show that the coating layer of the specimen is almost peeled off, though the thickness of coating is more than 20 ?m.
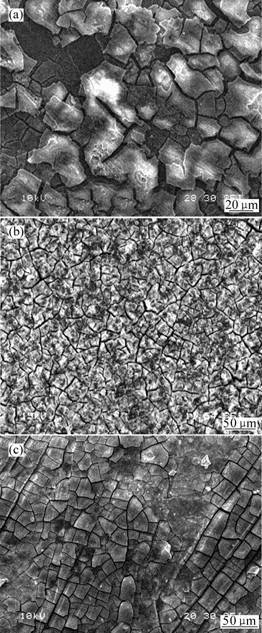
Fig.2 Morphologies of conversion coating treated with solution containing various concentrations of phosphoric acid: (a) pH=5.0; (b) pH=4.2; (c) pH=3.1
The coated specimen was immersed in salt solution with 5% NaCl for 24 h. The percent of rusted area of the specimen surface determines the corrosion resistance of the conversion coating. It is known from Table 2 that the corrosion resistance, thickness, adhesion and color of the coating are sensitive to the pH value of the treatment solution. The conversion coating presents better performance under the conditions that the treatment solution’s pH value ranging between 4.0 and 4.5.
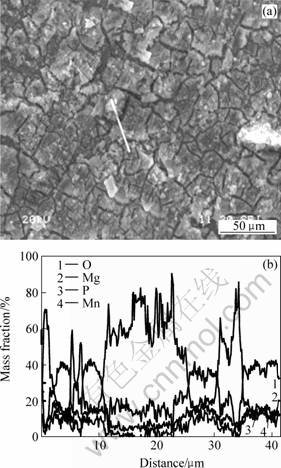
Fig.3 SEM image of conversion coating after(a) and phosphate-permanganate treatment corresponding elemental line scanning analysis of O, Mg, P,Mn elements (b)
Table 2 Performance of conversion coating specimens
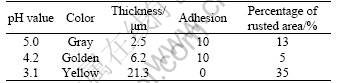
4 Conclusions
1) The reaction in phosphate-permanganate solutions with phosphoric acid is sensitive to the pH value of the treatment solution. The color, thickness, adhesion and corrosion resistance of the conversion coating are notable related to the pH value of treatment solution. The conversion coating, which has good performance, is obtained under the conditions that pH value of treatment solution ranging from 4.0 to 4.5.
2) Network-like cracks are obviously distributed all over the surface of the conversion layer, the size of crack area decreases with the high concentration of phosphoric acid in treatment solution, and the cracks on the surface of conversion coatings do not penetrate through the coatings.
3) The conversion coatings of AZ31 alloy are quite coarse when pH value of the treatment solution is 5.0. The conversion-coating thickness increases with the increase of phosphoric acid content, while the coating uniformity and adhesion are just the reverse.
References
[1] MORDIKE B L, EBERT T. Magnesium properties-applications-
potential[J]. Mater Sci Eng A,2001, A302: 37-45.
[2] SONG Guang-ling, ANDREJ A,MATTHEW D. Influence of microstructure on the corrosion of die-cast AZ91D[J]. Corrosion Science, 1998, 41(2): 249-273.
[3] GHALI E, DIETZEL W, KAINER K U. General and localized corrosion of magnesium alloys:Acritical review[J]. Journal of materials engineering and performance, 2004, 13(1): 1203-1211.
[4] JAIME V M,HALADA G P, CLAYTON C R. The application of synchrotron-based spectroscopic techniques to the study of chromate conversion coatings[J]. Electrochimica Acta, 2002, 47(19): 3105-3115.
[5] VANDER K J, SCHMIDT W, HASSEL A W, STRATMANN M. The role of chromate in filiform corrosion inhibition[J]. Electrochimica Acta, 2004, 49(9/10): 1675-1685.
[6] NIU LY, JIANG Z H, LI G Y, GU C D, LIAN J S. A study and application of zinc phosphate coating on AZ91D magnesium alloy[J]. Surface and Coatings Technology, 2006, 200(9): 3021-3026.
[7] GONZALEZ-NUNEZ M A, NUNEZ-LOPEZ C A. A Non-chromate conversion coating for magnesium alloys and magnesium-based metal matrix composites[J]. Corrosion Science, 1995, 37(11): 1763-1772.
[8] HAWK D, ALBRIGHT D L. A phosphate-permanganate conversion coating for magnesium[J]. Metal Finishing, 1995, 11: 34-38.
[9] ZHAO Ming, WU Shu-sen, LUO Ji-rong, FUKUDA B Y, NAKAE H A chromium-free conversion coating of magnesium alloy by a phosphate–permanganate solution[J]. Surface and Coatings Technology, 2006, 200: 5407-5412.
[10] Japanese Industrial Standard Testing Methods for Paints JIS K5400[S]. Japanese Standards Association, 1990.
[11] KOUISNI L, AZZI M, ZERTOUBI M, DALARD F, MAXIMOVITCH S. Phosphate coatings on magnesium alloy AM60 (part 1): Study of the formation and the growth of zinc phosphate films[J]. Surface and Coatings Technology, 2004, 185(1): 58-67.
[12] KOUISNI L, AZZI M, ZERTOUBI M, DALARD F, MAXIMOVITCH S. Phosphate coatings on magnesium alloy AM60 (part 2): Study of the formation and the growth of zinc phosphate films[J]. Surface and Coatings Technology. 2005, 192(2/3): 239-246.
(Edited by LI Xiang-qun)
Foundation item: Project(BK2006543) supported by the Nature Science Foundation of Jiangsu Province, China; project (2005KJA13) supported by the CHALCO S&T Foundation
Corresponding author: WENG Wen-ping; Tel: +86-512-62585622; E-mail: wwphorse@126.com