Trans. Nonferrous Met. Soc. China 22(2012) s775-s780
Machining performance on hybrid process of abrasive jet machining and electrical discharge machining
Yan-cherng LIN 1, Yuan-feng CHEN 1, A-cheng WANG 2, Wan-lin SEI 1
1. Department of Mechanical Engineering, Nan Kai University of Technology, Nantou County 54243;
2. Department of Mechanical Engineering, Chien Hsin University of Science and Technology, Taoyuan County 32097
Received 21 May 2012; accepted 1 November 2012
Abstract: To develop a hybrid process of abrasive jet machining (AJM) and electrical discharge machining (EDM), the effects of the hybrid process parameters on machining performance were comprehensively investigated to confirm the benefits of this hybrid process. The appropriate abrasives delivered by high speed gas media were incorporated with an EDM in gas system to construct the hybrid process of AJM and EDM, and then the high speed abrasives could impinge on the machined surface to remove the recast layer caused by EDM process to increase the efficiency of material removal and reduce the surface roughness. In this study, the benefits of the hybrid process were determined as the machining performance of hybrid process was compared with that of the EDM in gas system. The main process parameters were varied to explore their effects on material removal rate, surface roughness and surface integrities. The experimental results show that the hybrid process of AJM and EDM can enhance the machining efficiency and improve the surface quality. Consequently, the developed hybrid process can fit the requirements of modern manufacturing applications.
Key words: hybrid process; electrical discharge machining; abrasive jet machining; EDM in gas; surface roughness
1 Introduction
Electrical discharge machining (EDM) process is greatly adequate to shape difficult-to-machine materials, such as mold steels, ceramics, and composites [1]. The EDM process is generally considered as an attractive candidate to fabricate complex, precision, and miniature components [2,3]. The sophisticated EDM process also emerged as a promising approach to fabricate the components of a micro electromechanical system (MEMS)[4].
The concept of EDM performed in gas media (dry EDM) was proposed by KUNEIDA and YOSHIDA [5] in 1997. The molten materials generated in EDM process was ejected from machining area by a gas jet with high pressure. The benefits to EDM associated with jetting and intake modes of gas supply have been studied [6]. Their experimental results reported that the air supplied in intake mode presented a better machining precision. The technique of EDM in gas media has also been used to explore the machining feasibility in wire electrical discharge machining (WEDM) [7]. YU et al [8] studied the potential of EDM in gas media for machining tungsten carbides; the experimental results confirmed that the tungsten carbides could be machined by EDM milling in gas media using uniform tiny electrodes. CURODEAU et al [9] investigated the effects of EDM in gas media on surface modification and surface finishing by using a thermoplastic composite electrode for mold manufactures. In addition, ZHANG et al [10] incorporated ultrasonic vibration with EDM to build a hybrid process of EDM with ultrasonic machining (USM), and the ejection efficiency of machining debris could be facilitated for EDM in gas media by using such a hybrid machining system. KAO et al [11] studied the machining performance of EDM using liquid-gas as the dielectric media. The unique properties of the EDM dielectric media could be tailored to achieve the desired features. SAHA et al [12] conducted an experimental study using gaseous medium as the dielectric to develop the empirical model. According to the previous investigation [13], the compressed gas jet can be regarded as the machining media to maintain the stabilization of discharge sparks consecutively generating in the machining gap and to expel the molten material in the EDM process.
Abrasive jet machining (AJM) is suitable to be used for hard and brittle materials with excellent performance, it is the most frequently used in the surface finishing, cleaning, deburring, for the materials such as mold steels, glass, and ceramics. There are several researchers investigating the machining performance of AJM to fabricate micro hole, micro slit, micro device and micro array structure on hard and brittle materials. The capability of the AJM process used for specific materials with high efficiency, accuracy and low cost was conducted to meet the requirement of modern industrial applications. QU et al. [14] and TSAI et al. [15] adopted AJM technique to improve the machined surface quality of tungsten carbide and SKD 61 steel obtained from EDM. As the experimental results indicated that the surface roughness (Ra) could be reduced from 1.3 to 0.7 m a within a very short period, and the thickness of the recast layer could also be diminished. SHAFIEI et al [16] developed a numerical model to simulate the effects of AJM parameter on machined surface integrity.
This investigation developed the hybrid process of AJM and EDM initially, and then explored this novel process to evaluate the benefits of the hybrid process on machining characteristics such as material removal rate (MRR) and surface roughness (SR), and surface integrities. The main process parameters such as peak current, pulse duration, abrasive grain size, abrasive type, and air pressure were chosen to elucidate their effects on machining performance. Moreover, the relationships between machining parameters and machining characteristics of the developed hybrid process were established to exploit their potential for modern industrial applications.
2 Experimental
2.1 Materials
The workpiece material adopted in this study was SKD 61 steel, which is widely employed in mold and die industries, with dimensions of 30 mm×10 mm× 10 mm. The specimens were milled and ground firstly to ensure their parallelism before each experiment. Cylindrical electrolytic copper drilled with a through hole in the center was served as electrode material. The outer and inner diameters of the electrode are 8 mm and 5 mm, as well as 50 mm in length, respectively. The end face of electrode against to workpiece was ground by the emery papers on a granite flat plate in the sequence of 600#, 800#, and 1200#. Therefore, the electrode surface roughness and parallelism was ensured at an identical situation. The abrasive grains supplied into the machining zone were Al2O3 and SiC, whose grain sizes were 80# and 220# mesh. The essential properties of Al2O3 and SiC depict in Table 1. The compressed and dehumidified air was used as the dielectric media. Therefore, the machining media consisted of abrasives and gas media, which were adjusted by a pressure control valve and delivered through a tube electrode into the machining zone during the process.
Table 1 Essential properties of Al2O3 and SiC
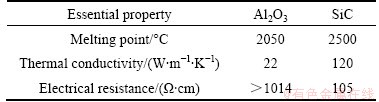
2.2 Equipment and procedure
A novel hybrid process combined material removal mechanisms of AJM and EDM was developed initially, and then a series of experiments were performed to determine the effects of the machining parameters on the machining characteristics for machining SKD 61 steels. The AJM was incorporated with the EDM in gas system to build an effective hybrid process that would promote the machining performance. The dielectric media adopted compressed air that was dehumidified before passing to the machining gap between workpiece and tool electrode. A self-designed abrasive grain mixture and delivery system was evolved and utilized. The added abrasive could be adjusted to control the amount of mixed abrasive into the compressed air. The compressed air pressure with specific abrasives was regulated by a precision pressure valve to keep the pressure of machining media. The machining media was supplied to the machining gap through the hollow electrode at the setting conditions for each trial run. Consequently, the consecutive electrical sparks were generated and EDM progress was maintained. The melting and vaporizing material caused by EDM was ejected as fast as possible by high compressed machining media. Moreover, the melted materials and recast layer, formed by EDM would be splashed and impinged by the high speed abrasive grains. Therefore, the surplus material was removed and surface finishing would be enhanced. Figure 1 demonstrates the actions within the machining gap associated with the hybrid process of AJM and EDM.
2.3 Conditions
The essential machining parameters such as peak current (Ip), pulse duration (tp), abrasive grain size, abrasive type, and air pressure (pA) were varied to explore their effects on the machining characteristics associated with the hybrid process of AJM and EDM. The machining elapsed time was set at 30 min for each experiment. The detail experimental conditions are listed in Table 2.
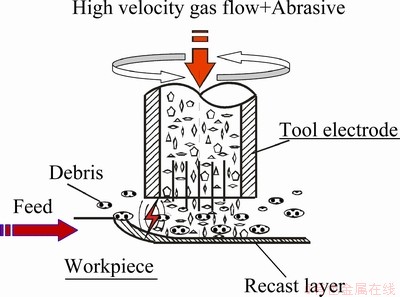
Fig. 1 Details of actions within machining gap of hybrid process of AJM and EDM
Table 2 Experimental conditions
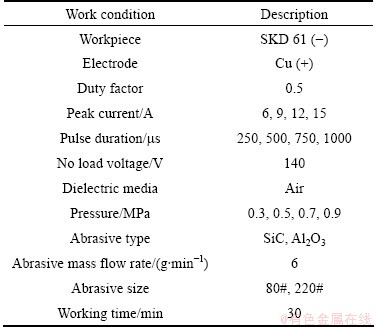
3 Results and discussion
3.1 Benefits of hybrid process
Figure 2 shows the comparisons of MRR and SR obtained by the hybrid process and dry EDM. The experimental results show that the hybrid process is superior to the dry EDM both in MRR and SR. The MRRs increase by 46% and 32% at the peak currents of 6 A and 9 A, individually. Moreover, the SR also improves at a conspicuous range that is reduced by 18% and 40% at the peak currents of 6 A and 9 A, respectively. The experimental results indicate that the hybrid process of AJM and EDM incorporated the effects of abrasive impact on the machined surface to promote the material removal and improve the surface finishing obviously. It can obtain the machining benefits with higher MRR and finer surface finishing. Thus, the hybrid process possesses the potential to ameliorate the machining performance to fit the requirement of modern manufacturing applications.
Figure 3 depicts the comparison of surface integrities associated with the hybrid process and the dry EDM. From the SEM micrograph, the scraped traces are observed on the machined surface with the hybrid process. When the high speed abrasive grain impinged on the machined surface, the material removal actions caused by the abrasive grain not only splashed the melted materials but also scraped the recast layer to further facilitate the material removal during the process. Thus, the hybrid process received the improvement of material removal efficiency and reduction of surface roughness to attain the goal of the process with high machining efficiency and high surface quality.
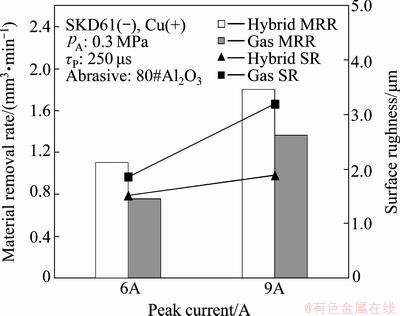
Fig. 2 Comparisons of MRR and SR obtained by hybrid process and dry EDM
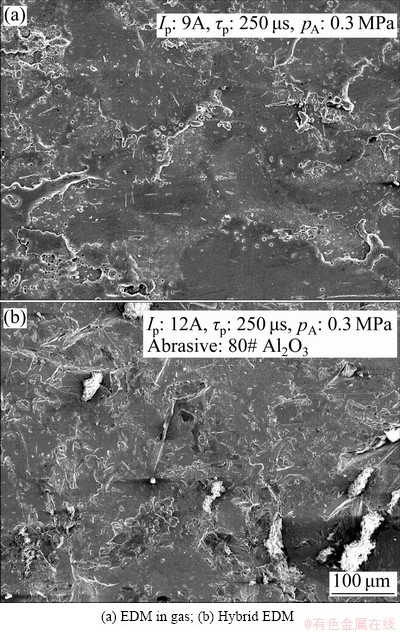
Fig. 3 Comparison of surface integrities associated with hybrid process and dry EDM
3.2 Material removal rate of hybrid process
Figure 4 shows the relationships of pulse duration and MRR under various peak currents using the developed hybrid process of AJM and EDM. As the experimental results shown, the MRR increases with the peak current. Indeed, a higher peak current would deliver more discharge energy into the machining zone, and then the melting and evaporation effects were more obvious to obtain a higher MRR. Moreover, the MRR substantially increased with pulse duration before 500 s. When the pulse duration further prolonged, the MRR exhibited a reducing trend at the pulse duration over 500 s. In general, the discharge channel expanded as the pulse duration lengthened. As a result, the material removal actions such as melting and evaporation would be enhanced at the initial period with increasing the pulse duration. Thus, the MRR increased as the pulse duration lengthened initially. However, the discharge energy density would be reduced when the pulse duration further prolonged due to expanding the diameter of discharge channel. Consequently, the MRR would be reduced as the discharge energy density diminished. Therefore, exceeding long pulse duration demonstrated a reverse effect on material removal during the process.
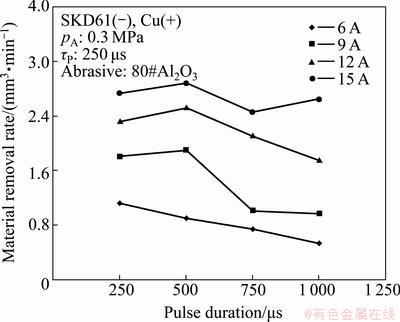
Fig. 4 Relationships between pulse duration and MRR under various peak currents using developed hybrid process of AJM and EDM
Figure 5 depicts the effects of grain size on the MRR for the hybrid process of AJM and EDM. The experimental data show that the small grain size abrasive (mesh 220#) would receive a higher MRR. This result can be attributed to that the larger grain size abrasive (mesh 80#) delivered to the machining gap would disturb the progress of EDM, and an appropriate grain size would exist and be used in the hybrid process of AJM and EDM. Figure 6 depicts the effects of abrasive types on the MRR for the hybrid process of AJM and EDM. As the experimental result shown, the SiC with higher hardness and better electrical conductivity was suitable for AJM to impinge on the machined surface and for EDM to generate sparks within the machining gap to remove the surplus materials. Therefore, using SiC could obtain a higher MRR for the hybrid process of AJM and EDM. Figure 7 shows the effects of air pressure on the MRR for the hybrid process of AJM and EDM. It was observed that higher MRR occurred as a higher air pressure was supplied to the machining area. It can be attributed to the fact that a higher air pressure would facilitate the melted materials caused by EDM to be expelled from the machining zone more completely. Therefore, a higher air pressure would obtain a larger MRR in the hybrid process of AJM and EDM.
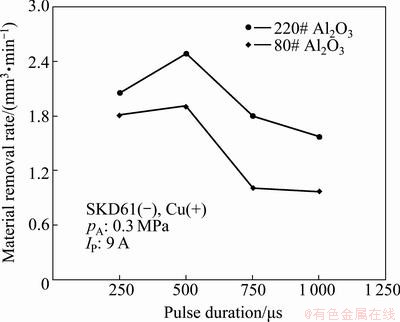
Fig. 5 Effects of grain size on MRR for hybrid process of AJM and EDM
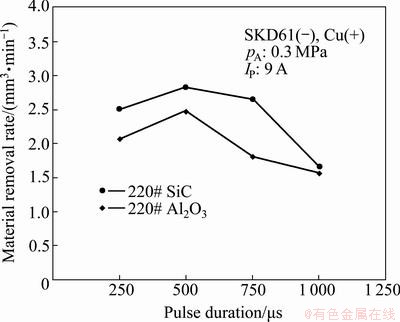
Fig. 6 Effects of abrasive types on MRR for hybrid process of AJM and EDM
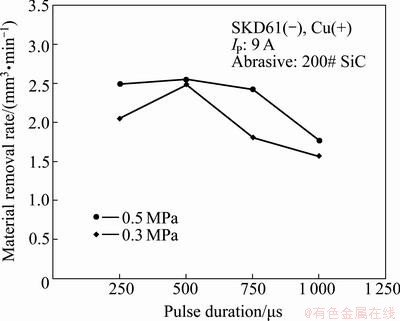
Fig.7 Effects of air pressure on MRR for hybrid process of AJM and EDM
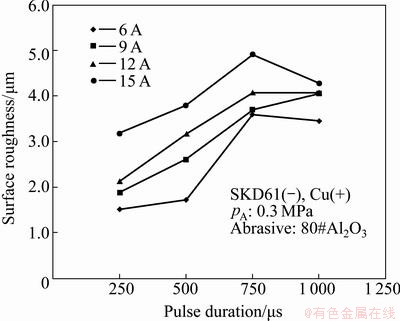
Fig. 8 Relationships between pulse duration and SR under various peak currents using developed hybrid process of AJM and EDM
3.3 Surface integrities of hybrid process
Figure 8 shows the relationships between pulse duration and SR under various peak currents using the developed hybrid process of AJM and EDM. As the experimental results shown, the SR increased with the pulse duration and peak current, and then the SR illustrated a declined SR value at an exceeding long pulse duration (more than750 ms). Indeed, the more discharge energy would be delivered to the machining zone when large peak currents and long duration pulses were chosen in the machining process. The machined surface would generate deeper and wider craters caused by the apparent material removal. Therefore, the surface integrities became coarser as the peak current and pulse duration were set at high levels. Figure 9 shows the effects of abrasive grain size on the SR for the hybrid process of AJM and EDM. The experimental results show that the large grain size abrasive adopted in the hybrid process would result in coarser surface integrities. The big abrasive impinged on the machined surface would produce apparently impacting and scraping actions to abrade more surplus materials from the machined surface. Consequently, the larger SR would be generated when the big abrasive grains were used in the hybrid process of AJM and EDM. Figure 10 shows the effects of abrasive types on the SR employed in the hybrid process of AJM and EDM. The experimental results show that using SiC resulted in larger SR than that by using Al2O3. This can be attributed to the fact that the SiC with good hardness would generate obviously scraping traces on the machined surface, so the SR would be occurred at high level using the SiC abrasive. Figure 11 shows the effects of air pressure on the SR for the hybrid process of AJM and EDM. As the experimental results indicate that high air pressure would generate large SR on the machined surface. When the air pressure set at high level, the material removal behavior was aggressive. Therefore, the machined surface integrities became coarser as the high air pressure was set for the hybrid process.
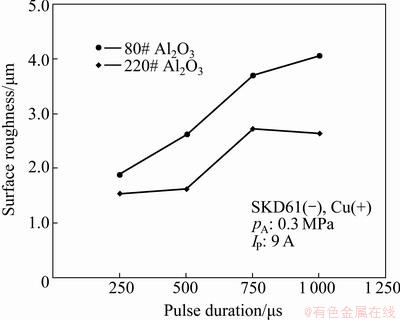
Fig. 9 Effects of abrasive grain size on SR for hybrid process of AJM and EDM
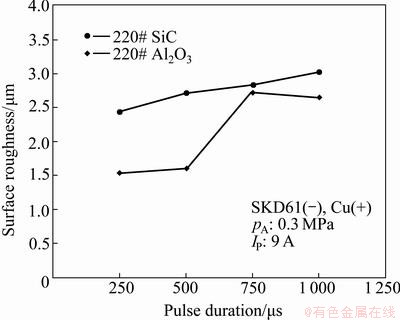
Fig. 10 Effects of abrasive types on SR employed for hybrid process of AJM and EDM
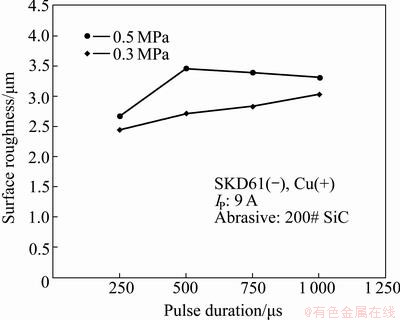
Fig. 11 Effects of air pressure on SR for hybrid process of AJM and EDM
4 Conclusions
1) The hybrid process of AJM and EDM can enhance the material removal. The abrasive grain generated mechanical plowing not only increased the MRR but also generated fine surface integrities.
2) The MRR of the hybrid process of AJM and EDM increased with the peak current. Moreover, the MRR increased with the pulse duration initially when the value reached the peak; then the MRR declined with further increased the pulse duration. Moreover, using small grain size of SiC abrasive and higher air pressure would promote the material removal effects to obtain a larger MRR.
3) The SR of the hybrid process of AJM and EDM increased with peak current. Beside, the SR increased with the pulse duration first, and then the SR would reduce with the further extended the pulse duration.
References
[1] LIN Y C, CHEN Y F, LIN C T, TZENG H J. Electrical discharge machining (EDM) characteristics associated with electrical discharge energy on machining of cemented tungsten carbide [J]. Materials and Manufacturing Processes, 2008, 23: 391-399.
[2] Lin Y C, Cheng C H, Su P L, Hwang L R. Machining characteristics and optimization of machining parameters of SKH 57 HSS using EDM based on Taguchi method [J]. Materials and Manufacturing Processes, 2006, 21: 922-929.
[3] Kuo C L, Huang J D. Fabrication of series-pattern micro-disk electrode and its application in machining micro-slit of less than 10 mm [J]. International Journal of Machine Tools and Manufacture, 2004, 44: 545-553.
[4] Fleischer J, Masuzawa T, Schmidt J, Knoll M. New applications for micro-EDM [J]. Journal of Materials Processing Technology, 2004, 149: 246-249.
[5] Kunieda M, Yoshida M. Electrical discharge machining in gas [J]. Annals of the CIRP, 1997, 46(1): 143-146.
[6] Kunieda M, Miyoshi Y, Takaya T, Nakajima N, Zhanbo Y, Yoshida M. High speed 3D milling by dry EDM [J]. Annals of the CIRP, 2003, 52(1): 147-150.
[7] Kuneida M, Furudate C. High precision finish cutting by dry WEDM [J]. Annals of the CIRP, 2001, 50(1): 121-124.
[8] Yu Z, Jun T, Masanori K. Dry electrical discharge machining of cemented carbide [J]. Journal of Materials Processing Technology, 2004, 149: 353-357.
[9] Curodeau A, Richard M, Frohn-Villeneuve L. Molds surface finishing with new EDM process in air with thermoplastic composite electrodes [J]. Journal of Materials Processing Technology, 2004, 149: 278-283.
[10] Zhang Q H, Du R, Zhang J H, Zhang Q B. An investigation of ultrasonic-assisted electrical discharge machining in gas [J]. International Journal of Machine Tools and Manufacture, 2006, 46: 1582-1588.
[11] Kao C C, Tao J, Shih A J. Near dry electrical discharge machining [J]. International Journal of Machine Tools and Manufacture, 2008, 48: 2273-2281.
[12] Saha S K, Choudhury S K. Experimental investigation and empirical model of the dry electric discharge machining process [J]. International Journal of Machine Tools and Manufacture, 2009, 49: 297-308.
[13] Lin Y J, Lin Y C, Wang A C, Chen Y F, Chow H M. Machining characteristics of EDM using gas media. [J]. Advanced Materials Research, 2011,189-193: 3132-3130.
[14] Qu J, Shih, A J. Scattergood R O, Luo J. Abrasive micro-blasting to improve surface integrity of electrical discharge machining WC-Co composite [J]. Journal of Materials Processing Technology, 2005, 166: 440-448.
[15] Tsai F C, Yan B H, Kuan C Y, Huang F Y. A Taguchi and experimental investigation into the optimal processing conditions for the abrasive jet polishing of SKD61 mold steel [J]. International Journal of Machine Tools and Manufacture, 2008, 48: 932-945.
[16] Shafiei N, Getu H, Sadeghian A, Papini M. Computer simulation of developing abrasive jet machined profiles including particle interface [J]. Journal of Materials Processing Technology, 2009, 209: 4366-4378.
(Edited by ZHAO Jun)
Foundation item: Project (NSC 99-2212-E-252-006-MY3) Supported by National Science Council
Corresponding author: Yan-cherng LIN; Tel: +886-49-2563489; E-mail: ycline@nkut.edu.tw
DOI: 10.1016/S1003-6326(12)61803-2