Trans. Nonferrous Met. Soc. China 20(2010) s832-s836
Semi-solid rheocasting of grain refined aluminum alloy 7075
U. A. CURLE, G. GOVENDER
Materials Science and Manufacturing, Council for Scientific and Industrial Research, Pretoria, South Africa
Received 13 May 2010; accepted 25 June 2010
Abstract: Near-net shape rheocasting with the Council for Scientific and Industrial Research Rheo casting system(CSIR–RCS) and a high pressure die casting machine was successfully performed on Al–5Ti–1B grain refined aluminum alloy 7075. Grain refinement levels used were 0.03% Ti, 0.13% Ti and 0.29% Ti (mass fraction). Tensile tests reveal that the ultimate tensile strengths, at all levels of grain refinement, are at least 97% of the specified minimum. Elongation at fracture increases with the increase of level of grain refinement although a maximum elongation is only 76% of the required minimum elongation in the case of 0.29% Ti. Incipient melting, during solution treatment, of the low melting point multinary eutectic causes porosity in the material and accounts for poor elongation results. 0.03% Ti has a coarse eutectic structure forming larger pores while 0.29% Ti has a fine structure forming fine pores in the multinary eutectic. The 0.2% offset yield strengths of all the grain refinement levels are at least equal to or above the specified minimum and a decrease is observed with the increase of grain refinement level. There is a clear reduction in grain size from 0.03% Ti to 0.29% Ti in the as-cast condition. An underlying grain structure develops in the T6 condition material which has an inverse size to the as-cast structure; coarse grained as-cast material results in fine grained T6 condition material after solution heat treatment. The decrease in the offset yield strength as grain refinement increases correlates very strongly with the T6 grain sizes according to a Hall–Petch type relationship.
Key words: CSIR–RCS; 7075; Al-5Ti-1B; high pressure die casting; F condition; T6 condition; incipient melting
1 Introduction
It is commonly known that wrought alloys are difficult to cast due to solidification properties causing hot tearing [1-3]. Attempts have been made previously to semi-solid process aluminum alloy 7075 but mainly by the thixo-processing route where a slug or billet of starting material is re-heated into the semi-solid state [4-10]. Rheo-processing as an alternative semi-solid process has also been used for this alloy [11-13] where the molten liquid is cooled into the semi-solid state before casting.
Grain refinement of wrought alloy microstructures can be achieved by inoculation with a grain refiner [7], increasing the cooling rate of the liquid metal or by controlling the alloy melt superheat [14]; vibration methods have also been successful [12, 14].
In this study, the semi-solid shape rheocasting of Al–5Ti–1B grain refined aluminum alloy 7075 was investigated. Microstructures of the as-cast (F) and T6 condition materials were examined and correlated with tensile properties.
2 Experimental
Wrought aluminum alloy 7075 was used for rheo-processing and high pressure die casting (HPDC) of plates containing different levels of Al–5% Ti–1% B(mass percentage) as a grain refiner. Dimension of the plates is 100 mm×55 mm×6 mm. Fig.1 shows the whole casting including the runner and the biscuit.
A batch of the 7075 alloy was melted in a 20 kg tilting furnace and degassed with argon. A sample was poured and cooled to analyze the starting chemical composition of the liquid metal by optical emission spectroscopy (Thermo Quantris OES). Thermodynamic properties of the starting alloy were then calculated (Scheil solidification model) with an aluminum thermodynamic database (ProCast 2009.1) using the OES composition of the alloy labeled alloy 1-3 given in Table 1.Table 2 summarizes the calculated thermodynamic properties and the deduced rheocasting parameters. A pouring temperature of approximately 40℃above the liquidus (the pouring temperature sensitivity has not yet been established) and a semi-solid metal(SSM) processing temperature corresponding to a solid fraction of 30% were used from experience with the processing system.
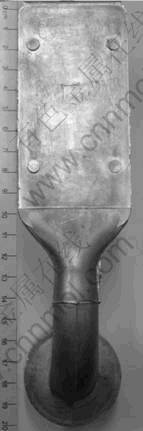
Fig.1 Example of rheocast plate including runner and biscuit
Table 1 Chemical composition of each 7075 grain refined casting interval as determined by OES and specification [15] (mass percentage,%)
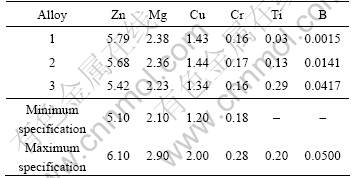
The liquid metal was poured from the tilting furnace into the stainless steel processing cup (about 400 g) which was then manually transferred to a single coil version of the CSIR-RCS (induction stirring with simultaneous forced air cooling [16]) where processing started when the cup entered the coil. The semi-solid temperature of the material in the cup was measured by a thermocouple, and the processing stopped after the thermocouple signal reached the preset SSM temperature. The cup was ejected from the coil and manually transferred to the HPDC machine (LK DCC130). The injection shot was manually triggered when the SSM billet was in the shot sleeve. The piston followed the preset computer controlled injection velocity profile which was kept the same for the different levels of grain refinement.
Table 2 Processing parameters for aluminum alloy 7075 (all levels of grain refinement)
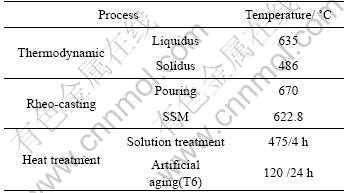
The different levels of grain refinement were achieved through adding rods of Al–5% Ti–1% B master alloy to the melt at two intervals. The first interval was after 12 castings were made from the starting alloy. the melt temperature then increased to approximately 700 ?C before a rod was stirred into the melt. This melt temperature was then reduced to the pouring temperature of the initial alloy. The process was repeated for the last interval. Samples for later OES analysis were solidified prior the specific casting interval. Table 1 shows the chemical composition obtained for each of the different grain refinement levels and indicates the Ti and B contents in each case.
Three plates from each grain refined 7075 alloy composition were selected and heat treated to the T6 condition with parameters shown in Table 2. Subsize rectangular tensile test specimens were machined according to ASTM standards [17] and the tensile properties were evaluated (Instron Model 1342).
An optical microscope (Leica DMI5000 M) equipped with a camera (Leica DFC480) and imaging software (Image–Pro MC v6.0) revealed the as-cast and heat treated microstructures after polishing and etching with 0.5 % HF. Image analysis software (ImageJ 1.38x) was used to measure grain sizes and the result is given as the average of 30 measurements.
3 Results and discussion
Fig.2 shows microstructures of successfully rheocast grain refined aluminum alloy 7075. It is apparent that progressive additions of Al–5Ti–1B achieve smaller grain sizes in the F condition. The proeutectic alpha aluminum(white) globules become finer and more spherical while the multinary eutectic(gray) also becomes finer with increased grain refinement. Fig.3 shows microstructures of the rheocast material in the T6 condition. The grain boundaries around the proeutectic globules have lost definition during the solution treatment process.

Fig.2 Optical micrographs of rheocast grain refined 7075 alloy at 0.03% Ti (a), 0.13% Ti (b) and 0.29% Ti (c) in F condition
The tensile tests results are given in Table 3. All the resulting ultimate tensile strengths (UTS) are at least 97% of the minimum specification. An option to increase the UTS is to use a higher solution treatment temperature and a longer soak time in order to dissolve more of the precipitation strengthening phase.
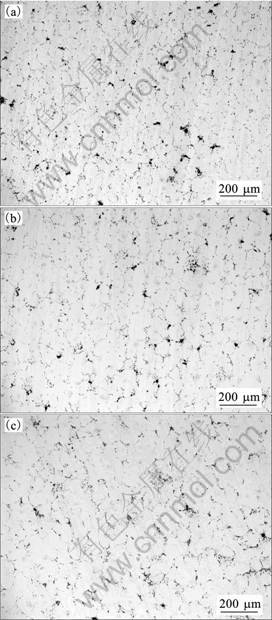
Fig.3 Optical micrographs of rheocast grain refined 7075 alloy at 0.03% Ti (a), 0.13% Ti (b) and 0.29% Ti (c) in T6 condition (Solution treated at 470 ?C for 4 h, quenched in water at room temperature and immediately artificially aged at 120 ?C for 24 h)
Table 3 Tensile properties of rheocast grain refined 7075 alloy in T6 condition and specifications[15]
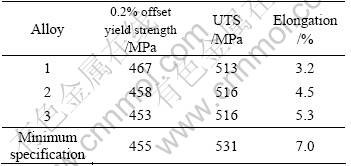
All of the elongation values fall short of the minimum specification, the best result being the 0.29% Ti which reaches 76% of the required minimum. At the other extreme is the 0.03% Ti result only reaching 46% of the minimum specification. These elongation results can be explained by looking closer in Fig.4 at the multinary eutectic areas; especially comparing the 0.03% Ti and 0.29% Ti microstructures in the T6 condition. Pores are clearly visible in both cases but the size difference is striking. Bigger pores cause a larger reduction in percentage elongation at fracture.
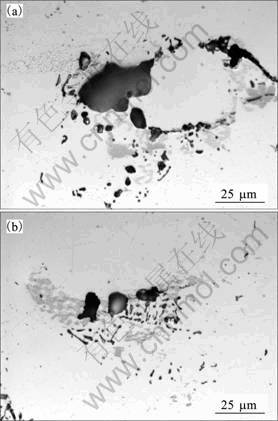
Fig.4 Optical micrographs of pores caused by incipient melting in multinary eutectic areas of 0.03% Ti (a) and 0.29% Ti (b) grain refined rheocastings in T6 condition
Fig.5 shows the source of pore formation caused by incipient melting during solution treatment, although shrinkage has been suggested before [10]. The eutectic microstructure of the 0.03% Ti is much coarser than that of the 0.29% Ti in the T6 condition. It is clear that 11 ?C below the calculated non-equilibrium solidus, as a first attempt, is not low enough for solution heat treatment. Differential scanning calorimetry (DSC) will be a better technique to determine the solidus of the multinary eutectic.
The offset yield strength values are above the required minimum except for 0.29% Ti of which is only just below the limit. There seems to be an inverse relationship between the level of grain refinement and the offset yield strength from inspecting Table 3. Table 4 indicates average grain sizes of each grain refinement level in the F condition as well as the T6 condition. Inspection of the microstructures in Fig.3 indicates an underlying grain structure in the T6 condition material and an attempt was made to also measure the average grain sizes as indicated in Table 4.
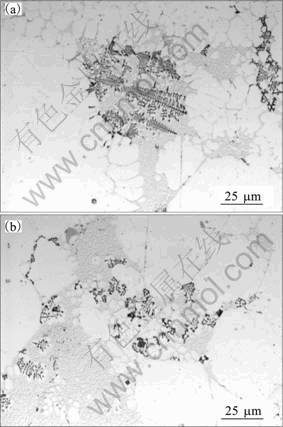
Fig.5 Optical micrographs of phases that solidified last during solidification in multinary eutectic areas of 0.03% Ti (a) and 0.29% Ti (b) grain refined rheocastings in F condition
Table 4 Average grain sizes of rheocast grain refined aluminum alloy 7075 in F and T6 conditions
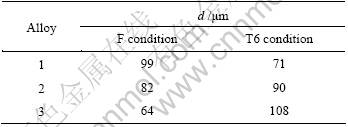
The relationships between the offset yield strengths and the grain sizes of the F condition and the T6 condition were calculated according to a Hall–Petch type relationship from Eqn.(1):
s 0.2∝d -1/2 (1)
where s0.2 is the 0.2% offset yield strength and d is the grain diameter.
Fig.6 shows that the yield strength is more strongly associated with the grain sizes of T6 condition than that of F condition. The F condition grain size is also inversely proportional to Eqn.(1). The results of T6 condition can be expected from the fact that the tensile properties are a function of the modified microstructures after solution heat treatment and artificial aging.
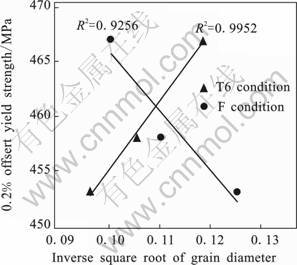
Fig.6 Relationship between 0.2% offset yield strength and grain diameter of grain refined 7075 in F condition and T6 condition
4 Conclusions
1) The CSIR–RCS with HPDC can successfully shape rheocast Al–5Ti–1B grain refined aluminum alloy 7075 with very spherical proeutectic alpha globules.
2) Ultimate tensile strengths at all levels of grain refinement are at least 97% of the specified minimum.
3) Elongation at fracture increases as the level of grain refinement increases although a maximum of only 76% of the required minimum elongation is reached in the case of 0.29% Ti.
4) Incipient melting, during solution treatment, of the low melting point multinary eutectic causes porosity in the material and accounts for elongation results. 0.03 % Ti has a coarse eutectic structure forming larger pores while 0.29% Ti has a fine structure forming fine pores.
5) The 0.2% offset yield strengths of all the grain refinement levels are at least equal to or above the specified minimum and a decrease is observed with increased grain refinement.
6) There is a clear reduction in grain size from the 0.03% Ti to 0.29% Ti in the F condition. An underlying grain structure develops in the T6 condition material which has an inverse size to the F condition structure; coarse grained F condition material results in fine grained T6 condition material after solution heat treatment.
7) The decrease in the offset yield strength as grain refinement increases correlates very strongly with the T6 grain sizes according to Hall–Petch type relationship.
References
[1] STALEY J R. J T, APELIAN D. Vacuum die-casting of wrought 7050 aluminum alloy[C]//Proceedings from Materials Conference 2001. Indianapolis: ASM International, 2001: 290-297.
[2] OH S I, KANG B M, LEE S Y. Defects, microstructures and mechanical properties of thixoformed aluminum suspension parts for electric vehicle [C]// 7th International Conference on Semi-Solid Processing of Alloys and Composites. Tsukuba, 2002: 725-730.
[3] LANGLAIS J, ANDRADE N, LEMIEUX A, CHEN X G, BUCHER L. The semi-solid forming of an improved AA6061 wrought aluminum alloy composition[J]. Diffusion and Defect Data. Part.B: Solid State Phenomena, 2008, 141/143: 511-516.
[4] VANEETVELD G, RASSILI A, PIERRET J C, LECOMTE-BECKERS J. Improvement in thixoforging of 7075 aluminium alloys at high solid fraction[J]. Diffusion and Defect Data Part B: Solid State Phenomena, 2008, 141/143: 707-712.
[5] VANEETVELD G, RASSILI A, LECOMTE-BECKERS J, ATKINSON H V. Thixoforging of 7075 aluminium alloys at high solid fraction[J]. Diffusion and Defect Data. Part B: Solid State Phenomena, 2006, 116/117: 762-765.
[6] JO H H, YOON Y O, LEE J K , KIM S K. Effect of partial remelting procedure on the microstructural evolution of 7075 Al wrought alloy for thixoextrusion[J]. Diffusion and Defect Data Part.B: Solid State Phenomena, 2006, 116-117: 336-339.
[7] GOVENDER G. Semi-solid forming of 7075 aluminum alloys [C]// 7th International Conference of Semi-Solid Processing of Alloys and Composites. Tsukuba, 2002: 179-184.
[8] CHAYONG S, KAPRANOS P, ATKINSON H V. Semi-solid processing of aluminium 7075 [C]// 6th International Conference on Semi-Solid Processing of Alloys and Composites. Turin, 2000: 649-654.
[9] CUI J, LU G, DONG J, XIA K. Microstructures after castings and reheating in a continuously cast aluminium alloy 7075 [C]// 6th International Conference on Semi-Solid Processing of Alloys and Composites. Turin, 2000: 701-704.
[10] JIRATTITICHAROEAN W, JONES H, ATKINSON H V, TODD I, KAPRANOS P. Thixoforming of aluminium 7xxx alloys produced using a cooling slope [C]// 8th International Conference on Semi-Solid Processing of Alloys and Composites. Limassol, 2004
[11] GUO H M, YANG X J. Rheoforging of wrought aluminum alloys[J]. Diffusion and Defect Data. Part.B: Solid State Phenomena, 2008, 141-143: 271/276.
[12] MOVAHEDI M, TAHERI A K , NIAMANESH H. Combined effect of cooling slope angle and mould vibration on semisolid microstructures of wrought aluminium alloy 7075 [J]. International Journal of Cast Metals Research, 2007, 20(4): 221-227.
[13] AZPILGAIN Z, HURTADO I, ORTUBAY R, LANDA I, ATXA J. Semisolid forging of 7000 series aluminum alloys[J]. Diffusion and Defect Data. Part B: Solid State Phenomena, 2006, 116/117: 758-761.
[14] STJOHN D H, EASTON M A, QIAN M. Controlling the semisolid grain size during solidification[J]. Diffusion and Defect Data. Part B: Solid State Phenomena, 2008, 141/143: 355-360.
[15] ALCOA. Alloy 7075[EB/OL]2010-03-18: http://www.alcoa.com/ gcfp/catalog/pdf/alcoa_alloy_7075.pdf.
[16] BRUWER R, WILKINS J D, IVANCHEV L H, ROSSOUW P, DAMM O F R A. Method of and apparatus for processing of semi-solid metal alloys: US7368690 [P]. 2008.
[17] ASTM E 8M-04: Standard test methods for tension testing of metallic materials[S].
(Edited by ZHAO Jun)
Corresponding author: U. A. CURLE; Tel: +27-12-8412132; E-mail: ucurle@csir.co.za