Article ID: 1003-6326(2005)06-1253-05
Superplasticity and diffusion bonding of
magnesium alloy ZK60
YU Yan-dong(于彦东)1, 2, JIANG Hai-yan(蒋海燕)2,
LI Qiang(李 强)2, ZAI Chun-quan(翟春泉)2, DING Wen-jiang(丁文江)2
(1. School of Materials Science and Engineering,
Harbin University of Science and Technology, Harbin 150040, China;
2. Light Alloy Net Forming National Engineering Research Center,
Shanghai Jiaotong University, Shanghai 200030, China)
Abstract: Superplasticity of as-rolled ZK60 magnesium alloy sheets, with the average grain size of 8.2μm, was investigated at a strain rate of 5.56×10-4-5.56×10-2 s-1 at 573-673K. The microstructure evolution during the superplastic deformation shows that the alloy deforms in a superplastic manner at the temperature from 573K to 673K. Diffusion bonding tests were carried out on the Gleeble-1500 testing machine and the specimens were successfully diffusion bonded at the superplastic temperature. The maximum specific strength is 0.82 at a bonding pressure of 10MPa for holding time 1h at 673K. The microstructures of the joints were observed through OM and SEM. There is no bond line visible in the original interfaces of sound joint with high specific strength.
Key words: ZK60 magnesium alloy; lap bonding; superplasticity; specific strength CLC
number: TG146.22 Document code: A
1 INTRODUCTION
Recently, the use of magnesium alloys as structural materials has significantly increased, for its good damping capacity, dimension stability, machinability and low casting costs. But magnesium alloys normally exhibit low ductility near room temperature because of their HCP structure. Therefore, it is necessary to improve the ductility of these alloys for their use as structural components[1-3].
In manufacturing, superplastic forming is often combined with diffusion bonding, which is known as SPF/DB(superplastic forming/diffusion bonding). As a kind of advanced manufacturing method, which can produce metallic parts with hollow structures, SPF/DB is time saving, material saving, efficiency improving and mass saving, and widely applied in aerospace fields[4-10]. Diffusion bonding is one of the joining techniques, and it is a solid state joining process, in which two clean metallic surfaces are contacted closely at elevated temperatures of 〈0.7 Tm at low pressure. The high-quality joints through diffusion bonding process need little or no post-welding machining, but it is important to optimize the conditions of diffusion bonding. Many factors affect the quality of diffusion bonds, including bonding temperature, bonding pressure and holding time. The optimized diffusion bonding conditions to produce high quality joints have already been reported for aluminum alloys, titanium alloys and steels[1]. SPF/DB technology has been developed in titanium and aluminum superplastic materials[8-15], and especially the SPF/DB processing titanium alloy superplastic materials have been widely used in aerospace industry[8, 9]. However, investigations of the possibility of SPF/DB processing magnesium alloy superplastic materials are still in progress.
In this paper, the superplastic behavior of as-rolled magnesium alloy sheets was investigated at first. Successively, diffusion bonding tests were carried out in superplastic conditions, and the mechanical properties of joints were tested for the possibility of joining magnesium alloys by diffusion bonding. As a result, the optimized diffusion bonding was obtained through a series of bonding tests carried out in a wide range of bonding temperature, bonding pressure and holding time.
2 EXPERIMENTAL
A commercial ZK60 magnesium alloy was employed in as-cast ingots, with a chemical composition of Mg-6%Zn-0.35%Zr(mass fraction). The ingots were extruded into sheets of 20mm in thickness. The sheets were rolled with a reduction ratio of 15% per one pass to a final thickness of 1.0mm, with an average grain size of 8.2μm. The specimens to be diffusion bonded were directly cut from the as-rolled sheet. The length was 30mm and the width was 12mm, respectively. And the lap length of bonding was 3-5mm.
In order to investigate the superplastic forming behavior, the tensile tests and metallograph analyses were carried out, after the superplastic forming was performed with a strain rate of 5.56×10-4-5.56×10-2s-1 at 573-673K .
Diffusion bonding tests were carried out on the Gleeble-1500 testing machine under a condition similar to superplastic characteristics. Before diffusion bonding, the bonding surfaces were cleaned in order to remove the oxides. The solution of bonding surfaces cleaning mainly included: acetone and chrome-anhydride. At 673K the bonding pressure varied from 3 to 15MPa and the bonding time was between 0.5h and 5h. The joint quality was investigated through shear strength tests and scanning electron microscope(SEM) observations.
3 RESULTS AND DISCUSSION
3.1 Superplasticity
Fig.1 shows the double logarithm relation of the flow stress and the strain rate sensitivity exponent with strain rate at 573K to 673K, indicating that the flow stress increases with the increase of strain rate. In the low strain rate range, at 573-673K, the strain rate sensitivity exponent m varies between 0.4 and 0.5, and the materials possess superplasticity. While in the high strain rate range, at 573-673K, m varies between 0.3 and 0.9 for most of materials. Generally it is accepted that the m values of 0.2 and 0.5 are predicted for climb-controlled dislocation creep and slip-accommodated grain boundary sliding, respectively. At a low temperature of 473K the climb-controlled dislocation creep is suggested to be the dominant deformation mechanism. With the increase of temperature, the grain boundary sliding dominates the deformation behavior[16]. The relation of elongation-to-failure with strain rate is shown in Fig.2. The elongation decreases with the increase of strain rate, showing strong strain rate sensitivity. The maximum elongation obtained is 1106% at a strain rate of 5.56×10-4s-1 at 673K.
3.2 Microstructure
Fig.3 shows the microstructures of fractured specimens deformed with the strain rate of 5.56×10-4s-1 at 573-673K (the tensile direction is horizontal). It is shown that the average grain size slightly increases after larger superplastic
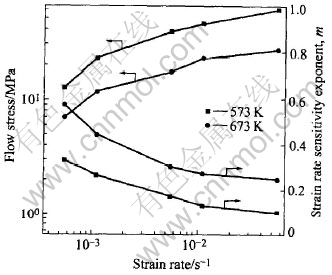
Fig.1 Flow stress and strain rate sensitivity exponent vs strain rate

Fig.2 Relation between strain rate and elongation
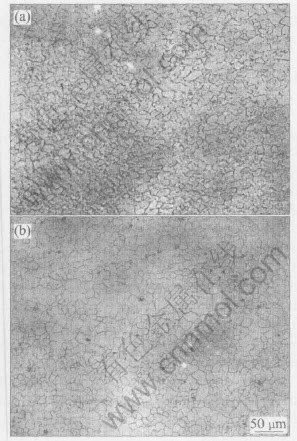
Fig.3 Microstructures of fractured specimens deformed at 573K(a) and 673K(b)
deformation. The grains are slightly elongated along the tensile direction, but the grain shapes remain close to equiaxial, indicating the dominant superplastic deformation mechanism is grain boundary slide for ZK60 magnesium alloy in the temperature range of 573-673K. Meanwhile the slight elongation of grains along the tensile direction suggests the occurrence of intragranular slip during the superplastic deformation of ZK60 magnesium alloy.
3.3 Diffusion bonding
Because ZK60 magnesium alloy possesses outstanding superplasticity at in temperature range of 573-673K, diffusion bonding can be carried out through composite technique of SPF/DB at this temperature range. In order to compare the joint with the base metal, the specific strength is calculated, which is the ratio of the shear strength of the joint and that of the base metal. In the present ZK60 alloy the shear strength is 86.5 MPa. The results of the shear strength tests for the joints after diffusion bonding are listed in Table 1. It is shown that the diffusion bonding strength depends on bonding pressure and time, and it tends to increase with the increase of bonding time and pressure.
Table 1 Shear strengths of joints bonded at 673K
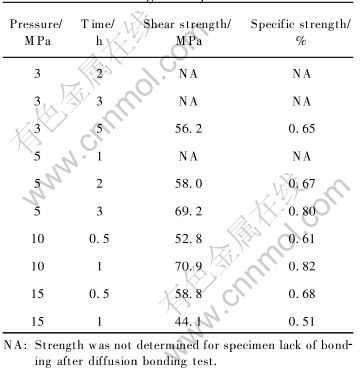
The maximum specific strength of 0.82 is obtained at the bonding pressure of 10MPa for 1h holding time. Fig.4 shows the SEM micrographs of the cross section of the interfaces bonding for different holding time under a pressure of 10MPa at 673K, the specimens were cooled rapidly to room temperature after bonding.

Fig.4 SEM micrographs of cross sections for different holding times
Fig.4(a) shows the SEM micrograph of the specimen held for 1h, which possesses the high specific strength of 0.8. Fig.4(b) shows the SEM micrograph of the specimen held for 0.5h. When the specific strength is high, the bond line is invisible. On the contrary, when the specific strength is low, the bond line is observed clearly. It appears that the original separate interface forms voids, which gradually disappear during the diffusion bonding process. So the low bonding strength is suggested to concern with the presence of voids, since the stress within the interfaces would cause a plastic flow through conventional creep or superplasticity, and would diffuse from the interfaces to the void surface and bonding surface. When the grain size is smaller than the void size in the case of superplastic materials, the mass transfer through the grain boundaries would significantly influence the bonding behavior, for the numerous grain boundaries intersect the void surfaces[16]. In order to obtain high specific strength, a higher bonding pressure or a longer holding time is required to make the visible bond line disappear and improve the joints quality.
Since the superplasticity depends on the grain size, the diffusion bonding process would also be grain size dependent[16].For the diffusion bonding of light metals, sound joining is marked by the disappearance of the original interfaces. According to the characteristics of diffusion bonding of ZK60 superplastic materials, the disappearance of the original interfaces is greatly attributed to the diffusion of interface atoms.
On the other hand, there is obvious variation in the grain size before and after diffusion bonding. As shown in Fig.5, the average grain size of specimens grows from 8.2μm (Fig.5(a)) to 17.9μm (Fig.5(b)) at 673K, which leads to the slide of original boundaries, and the residue of slide is shown in Fig.5(b). For grain growth is also

Fig.5 Microstructures of diffusion bonding
attributed to the diffusion of atoms, it is concluded that the mechanism of diffusion bonding of superplastic ZK60 is atom diffusion and original grain boundaries slide caused by grain growth[17].
4 CONCLUSIONS
1) ZK60 magnesium alloy exhibits superplasticity at the temperatures from 573K to 673K. The elongation significantly increases when increasing temperature and decreasing strain rate. A maximum elongation of 1106% is obtained at a strain rate of 5.56×10-4s-1 at 673K.
2) The grain shapes of ZK60 magnesium alloy remain equiaxial after superplastic deformation, indicating the dominant mechanism in superplastic deformation of ZK60 magnesium alloy is grain boundary slide. Meanwhile the slight elongation of grains along the tensile direction suggests the occurrence of intragranular slip during superplastic deformation.
3) The maximum specific strength of 0.82 is obtained at the bonding pressure of 10MPa for 1h holding time. There is no bond line visible in the original interfaces.
4) The mechanism of diffusion bonding of superplastic ZK60 is the slide of original grain boundaries caused by atom diffusion and grain growth, and sound joints with high specific strength are obtained through sufficient diffusion of the interface atoms.
REFERENCES
[1]Somekawa H, Hosokawa H, Watanabe H, et al. Diffusion bonding in superplastic magnesium alloys [J]. Materials Science and Engineering A, 2003, 339: 328-333.
[2]ZHAO Hong-liang, GUAN Shao-kang, ZHENG Fei-yan, et al. Microstructure and properties of AZ31 magnesium alloy with rapid solidification [J]. Trans Nonferrous Met Soc China, 2005,15(1): 144-149.
[3]Carrino L, Giuliano G, Napolitano G. A posteriori optimisation of the forming pressure in superplastic forming processes by the finite element method [J]. Finite Elements in Analysis and Design, 2003, 39: 1083-1093.
[4]Xun Y W, Tan M J. Applications of superplastic forming and diffusion bonding to hollow engine blades [J]. Journal of Materials Processing Technology, 2000, 99: 80-85.
[5]Weisert E D. Advanced structural component by SPF/DB processing [J]. Ti Sci and Techn, 1984(2): 1221-1228.
[6]Zuruzi A S, Li H, Dong G. Diffusion bonding of aluminium alloy 6061 in air using an interface treatment technique [J]. Materials Science and Engineering A, 1999, 259: 145-148.
[7]Huang J C, Chuang T H. Progress on superplasticity and superplastic forming in Taiwan during 1987-1997 [J]. Materials Chemistry and Physics, 1999, 57: 195-206.
[8]Watanabe H, Mukai T. Effect of temperature and grain size on the dominant diffusion process for superplastic flow in an AZ61 magnesium alloy [J]. Acta Mater, 1999, 147(14): 3753-3758.
[9]Huang Y, Ridley N, Humphreys F J, et al. Diffusion bonding of superplastic 7075 aluminium alloy [J] .Materials Science and Engineering A, 1999, 266: 295-302.
[10]Bussiba A, Ben A A. Grain refinement of AZ31 and ZK60 Mg alloys—towards superplasticity studies [J]. Materials Science and Engineering A, 2001, 302: 56-62.
[11]Li G Y, Tan M J, Liew K M. Three-dimensional modeling and simulation of superplastic forming [J]. Journal of Materials Processing Technology, 2004, 150: 76-83.
[12]Hu B H, Tong K K, Niu X P, et al. Design and optimisation of runner and gating systems for the die casting of thin-walled magnesium telecommunication parts through numerical simulation [J]. Journal of Materials Processing Technology, 2000, 105: 128-133.
[13]Mordike B L, Ebert T. Magnesium properties-applications-potential [J]. Materials Science and Engineering A, 2001, 302: 37-45.
[14]JIANG Chao, JIN Zhan-peng. Computer program for equilibrium calculation and diffusion simulation [J]. Trans Nonferrous Met Soc China, 2000,10(2): 156-161.
[15]Chung L C, Cheng J H. Fracture criterion and forming pressure design for superplastic bulging [J]. Materials Science and Engineering A, 2002, 333: 146-154.
[16]Somekawa H, Watanabe H, Mukai T, et al. Low temperature diffusion bonding in a superplastic AZ31 magnesium alloy [J]. Scripta Materialia, 2003, 48: 1249-1254.
[17]YU Yan-dong, LI Qiang. Diffusion bonding in superplastic ZK60 magnesium alloy [J]. Materials Science Forum, 2005, 488-489: 227-230.
(Edited by YUAN Sai-qian)
Foundation item: Project (E3080) supported by Natural Science Foundation of Heilongjiang Province; Project(10541046) supported by Scientific Item of Education Office of Heilongjiang Province
Received date: 2005-06-26; Accepted date: 2005-09-19
Correspondence: YU Yan-dong, Professor, PhD; Tel: +86-451-86392573; E-mail: yandongyu@yahoo.com.cn