
Fatigue properties of pack ply-rolling Ti-6Al-4V alloy sheets
HONG Quan(洪权), YANG Guan-jun(杨冠军), ZHAO Yong-qing(赵永庆),
QI Yun-lian(戚运莲), GUO Ping(郭萍)
Northwest Institute for Nonferrous Metal Research, Xi’an 710016, China
Received 15 July 2007; accepted 10 September 2007
Abstract: The influence of pack ply-rolling process and heat-treatment on the texture characteristics of Ti-6Al-4V alloy sheets was investigated applying the EBSD technique. The tensile properties and fatigue properties of the sheets possessing different type textures were measured. The results show that the alloy sheets possessing single type texture (B or T) exhibit lower fatigue strength compared with the mixed texture (B/T). The sheet possessing basal texture exhibits isotropy and its elastic modulus and yield strength are lower than those under other conditions.
Key words: Ti-6Al-4V alloy; pack ply-rolling; sheet; texture; fatigue properties
1 Introduction
Texture type can influence the sheet property strongly. Different rolling process brings different texture characteristics. The sheet possessing specifical texture characteristics and properties can be controlled through fit rolling process.
The pack ply-rolling process is an effective method to produce Ti-6Al-4V alloy thin sheet[1-2]. This method should lower the product cost and improve the mechanical properties of the alloy sheet. This paper introduces the effects of texture characteristics on the fatigue properties of Ti-6Al-4V alloy. The texture characteristics of sheets were studied by applying the EBSD technique. The texture of Ti-6Al-4V alloy sheet was strong by hot rolling process. In this study, unidirectional rolling at 930 ℃ brings about basal texture (B), the cross rolling at 930 ℃ leads to transverse texture (T), cross rolling at 980 ℃ results in fiber texture. In some cases (process Ⅱ and press Ⅳ, the sheet texture types are changed after annealing process. In the other case (process Ⅰ and process Ⅲ), the sheet texture types do not change after annealing process. The alloy sheet, which possesses mixed texture (B/T) exhibits higher fatigue strength compared with single type texture (B or T).
2 Experimental
2.1 Material
The material used in the present work was ply-rolled in different process (Table 1). The pack stack consisted of three layers Ti-6Al-4V sheet blank which was wrapped by 16MnR steel. The thickness of Ti-64 sheet blank and 16MnR steel sheet was 2 mm and 10 mm. The pack dimensions are 200 mm?140 mm?25 mm. The isolator was applied in the pack rolling process, which was sprayed on Ti-6Al-4V sheet surface and 16MnR steel surface. It can prevent sticking between the titanium sheets in rolling process. The beta transus temperature of Ti-6Al-4V was 990 ℃.
Table 1 Pack ply-rolling process of Ti-6Al-4V alloy sheets
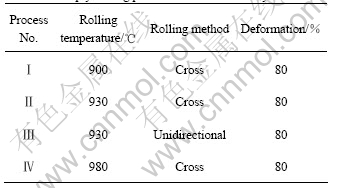
2.2 Hot rolling
Hot Rolling process is listed in Table 2. The general reduction of hot rolling is 80%, and the final thickness of pack is 5mm. The thickness of every layer of Ti-6Al-4V sheet is 0.3mm after hot rolling. The Ti-6Al-4V sheet were heat treated at 800 ℃ for 60 min after surface treatment of acid. The sizes of tensile sample and fatigue sample were 161 mm?20 mm and 100 mm?30 mm. Fatigue tests were run in 10% of the maximum load (R=0.1). The frequency of load cyclic was 45 Hz. The texture characteristics of sheets were investigated the EBSD technique.
3 Results and discussion
3.1 Texture feature of Ti-6Al-4V sheets
The texture feature of Ti-6Al-4V sheets rolled under different conditions are shown in Fig.1 In this study, the cross rolling at 900 ℃ brings about mixed texture (B/T). Unidirectionally rolling at 930 ℃ brings about basal texture(B), cross rolling at 930 ℃ leads to transverse texture(T), cross rolling at 980 ℃ results in fiber texture. It is shown that both rolling temperature and rolling method can affect the texture feature of Ti-6Al-4V sheet. When rolled at lower temperature (900-930 ℃) the rolling method is the main factor. However, when the rolling temperature is near transus point(β), the temperature is the main factor which influences the texture feature of Ti-6Al-4V sheet.
3.2 Influence of annealing on texture
Compared with the pole figure, we can find that, in some cases (process Ⅱ and process Ⅳ), the sheet texture types change after annealing process. In the other cases (process I and process Ⅲ), the sheet texture type does not change after annealing process (Fig.2).
3.3 Influence of texture on tensile strength
The tensile results are summarized in Tables 2 and 3. The sheet, which possesses basal texture (B), exhibits isotropy and its elastic module is lower than that under the other condition. The sample, which possesses transverse texture (T) and mixed texture (B/T), exhibits higher tensile strength values and elastic values when applying the stress on transverse direction.
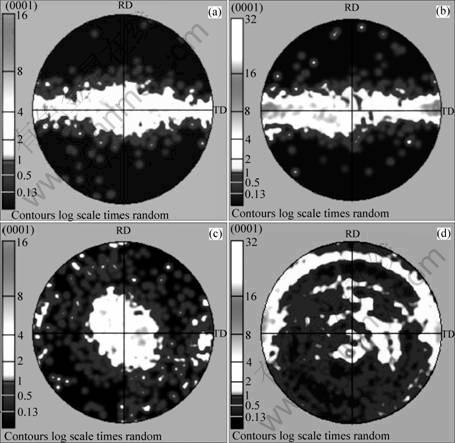
Fig.1 Texture characteristics of sheets after different rolling processes (0001 pole figure): (a) Cross rolled at 900 ℃ (Process Ⅰ); (b) Cross rolled at 930 ℃ (Process Ⅱ); (c) Unidirectionally rolled at 930 ℃ (Process Ⅲ); (d) Cross rolled at 980 ℃ (Process Ⅳ)
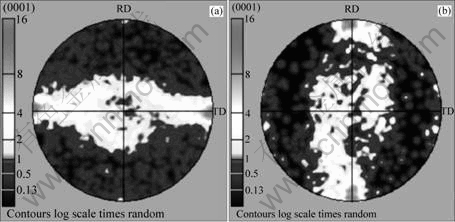
Fig.2 Texture characteristics of sheets after annealed at 800 ℃ for 1 h (0001 pole figure): (a) Cross rolled at 930 ℃ (Process Ⅱ); (b) Cross rolled at 980 ℃ (Process Ⅳ)
Table 2 Tensile properties for different texture types of sheets after hot rolling
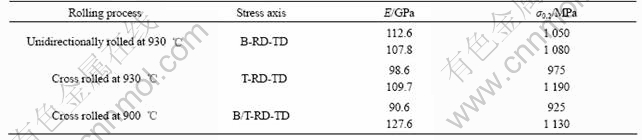
Table 3 Tensile properties for different texture types of sheets after annealed at 800 ℃ for 1 h
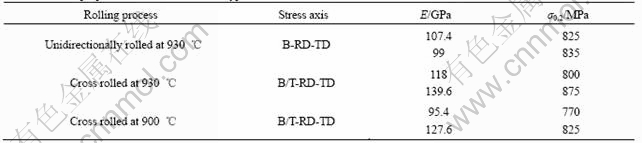
For the symmetry reason, whenever applying the stress in rolling direction or transverse direction on basal texture sample, stresses acting on hexagonal crystal were identical. So the basal texture sample is rather isotropic. The elastic values are mainly dependent on the crystal parameter. When the stresses are applied parallel to the C-axis direction of α phase crystal, then the highest elastic values are observed. For the same reason whenever loaded on basal texture sample in rolling direction or transverses direction, the stresses are perpendicular to C-axis of hexagonal crystal. So the sheet which possesses basal texture exhibits lower elastic values[3-5].
3.4 Influence of texture on fatigue properties
The fatigue strengths for different texture types of Ti-6Al-4V sheet are shown in Fig.3 and Table 4. The results show that the sheet which possesses mixed texture type exhibits the highest fatigue strength compared with the basal texture and transverse texture. The reason why the single type texture samples possess lower fatigue strength is that slip bands have similar direction in its crystal system, which leads to faster expanding of slip from one crystal to another. So the single type texture samples exhibit earlier crack nucleating and lower fatigue strength. The mixed texture sample brings about perpendicular slip bands in its crystal system. However, different slip bands direction will resist slip moving from one crystal to another, which leads to higher fatigue strength[6-11].
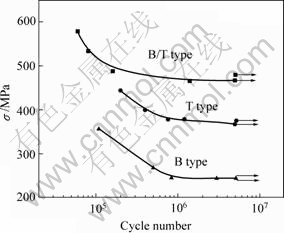
Fig.3 Influences of texture type on sheet fatigue strength
Table 4 Fatigue strengths of sheets in different texture types at 5×106 cycles
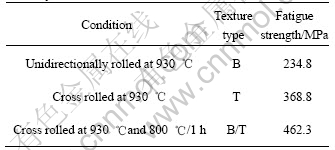
3.5 Fatigue crack propagation path and fracture surface
The fatigue crack propagation path and fracture surface in fatigue specimens are shown in Figs.4 and 5. Fig.4(a) shows that the crack propagation path possesses much flattens where the specimen is in unidriectionally rolling process. In Fig.4(b), the crack propagation path is more tortuous and the crack tip is inactived. This suggests that fatigue crack will consume more energy. On the other hand, we can observe striation in Fig.5(b) which is against to the direction of crack propagation. However, it suggests that a corresponding relationship between Fig.4 and Fig.5 exists in some sections. It can be concluded that the fatigue crack of cross rolling specimens is more tortuous and the fatigue strength also increases.
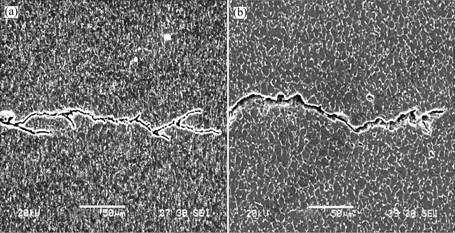
Fig.4 Microstructures showing fatigue crack propagation paths in fatigue specimens
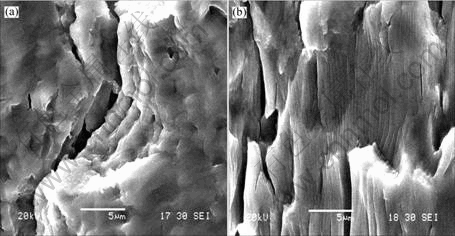
Fig.5 SEM microstructures of fractures surface (fatigue crack tip)
4 Conclusions
1) The texture of Ti-6Al-4V alloy sheet prepared by hot rolling process is strong.
2) The unidirectional rolling at 930 ℃ brings about basal texture (B), cross rolling at 930 ℃ leads to transverse texture (T), cross rolling at 980 ℃ results in fiber texture.
3) In processes Ⅱ and Ⅳ, the sheet texture types change after annealing process. In processes Ⅰ and Ⅲ, the sheet texture types do not change after annealing process.
4) The alloy sheet, which possesses mixed texture (B/T), exhibits higher fatigue strength compared with single type texture (B or T).
References
[1] LU Fu-sheng, JIA Hong, HE Yu, HAO Bin. Industrial present status and trend of development of titanium in the world[J]. Titanium Industry Progress, 2001(5): 1-5.
[2] HAO Bin. Market retrospective of titanium in the world in 1999[J]. World Nonferrous Metal, 2000(6): 1-5.
[3] ZHENG Jian-min, ZHANG Sao-zhi. Technology review of pack ply-rolling Ti-6Al-4V alloy sheets[C]//Eighth National Conference on Titanium, Shanghai: Titanium Science and Technology, 1993: 212-216. (in Chinese)
[4] REN Lian-bao, WANG Hong-wu, HU Qing-xiong, WANG Jian, CHEN Dong. Microstructure ans mechanical properties of TC4 sheets produced by sheath and ply-rolling technology[J]. Chinese Journal of Rare Metals, 2004, 28: 274-276. (in Chinese)
[5] PETERS M, LUEGUERING G. Control of Microstructure and texture in Ti-6Al-4V[J]. Ti Sci Technol, 1988: 926-935.
[6] KIYOSHI A, ANABE T, AKASHI T, SHIMURA N. The Formation of hot rolled texture in commercially pure titanium and Ti-6Al-4V alloy sheets[J]. Ti Sci Technol, 1988: 937-945.
[7] MURAYAMA Y. Texture hardening of Ti-6Al-4V alloy formation of basal plane texture by dentate rolling[J]. Ti Sci Technol, 1988: 967-971.
[8] ZENG Chun-hua. Fatigue[M]. Beijing: National Defense Industry Press, 1991: 214-218.
[9] SURESH S. Fatigue of material[M]. Beijing: National Defense Industry Press, 1999: 216-219.
[10] NAKA S, PENELLE R. Recrystallization texture development in a commercial purity titanium thin sheet[J]. Ti Sic Tec, 1988: 955-963.
[11] FUJISHIRO S, NADIR S. Effect of transformation on the texture of titanium[J]. Ti Sci Technol, 1988: 889-905.
Foundation item: Projects(2007CB613805) supported by the National Basic Research Program of China
Corresponding author: HONG Quan; Tel: +86-29-86231078; E-mail: hongquan@c-nin.com
(Edited by LONG Huai-zhong)