J. Cent. South Univ. Technol. (2008) 15(s1): 021-024
DOI: 10.1007/s11771-008-306-2

Rate dependent rheological stress-strain behavior of porous nanocrystalline materials
LI Hui(李 慧), ZHOU Jian-qiu(周剑秋)
(School of Mechanical and Power Engineering, Nanjing University of Technology, Nanjing 210009, China)
Abstract: To completely understand the rate-dependent stress-strain behavior of the porous nanocrystalline materials, it is necessary to formulate a constitutive model that can reflect the complicated experimentally observed stress-strain relations of nanocrystalline materials. The nanocrystalline materials consisting grain interior and grain boundary are considered as viscoplastic and porous materials for the reasons that their mechanical deformation is commonly governed by both dislocation glide and diffusion, and pores commonly exist in the nanocrystalline materials. A constitutive law of the unified theory reflecting the stress-strain relations was established and verified by experimental data of bulk nanocrystalline Ni prepared by hydrogen direct current arc plasma evaporation method and hot compression. The effect of the evolution of porosity on stress-strain relations was taken into account to make that the predicted results can keep good agreements with the corresponding experimental results.
Key words: stress-strain; porous; nanocrystalline materials; rate dependent; porosity
1 Introduction
Ultrafine grained materials with average grain size in the range from 1 nm to 100 nm are referred to as nanocrystalline(NC) materials which have attracted intensive attentions from researchers[1-3] for the potential mechanical characteristics they may offer. Compared to their microcrystalline counterparts with grain size typically larger than 1 μm, the NC materials possess some attractive properties including high strength and ductility[4-10]. It is well accepted that the mechanical properties of NC materials are evidently affected by the evolution of the microstructure of NC materials. Meanwhile relevant aspects of porous NC materials including the pore space and the value of porosity should be taken into account to make a comprehensive research for the mechanical properties of NC materials. Thus, to systematically understand the porosity dependent plastic deformation, it is necessary to analyze the evolution of microstructure and related stress-strain relations for NC materials quantitatively.
There are several constitutive models for NC materials which have been established by some researchers[11-14]. For example, the NC materials are seen as a mixture of crystalline phase, intercrystalline phases including grain boundary and triple line junction, as well as quadratic node, and pores[11]. They have considered the pores, but they ignored the evolution of porosity. JIANG and WENG[12-13] suggested a generalized self-consistent polycrystal model that took each oriented grain and its immediate grain boundary to form a pair to study the transition of rate independent yield strength of polycrystalline metals with decreasing grain size from the traditional coarse grain to the nanometer scale. LI and WENG[14] presented the composite model including grain-interior phase and grain-boundary affected zone (GBAZ) to predict the strain rate and grain size dependent stress-strain relations. Although the models mentioned above are successful, they have to use a mass of complicated iteration during the constitutive law of grain of NC materials. For the purpose of analyzing the real hypostasis and the mechanical deformation of NC materials in a simple way, the energy principle will be employed to develop a constitutive model predicting not only strain rate and grain size dependent but also porosity dependent stress-strain behavior.
2 Constitutive model
NC materials in this paper are considered as two-phase composites: grain interior governed by dislocation and diffusion mechanisms and grain boundary controlled by a boundary diffusion mechanism. In order to study the strain rate and grain size dependent mechanical deformation of porous NC materials, it is necessary to set up a constitutive law of NC materials including the constitutive equations of the grain interior and the grain boundary respectively.
The mechanical properties of grain interior are described using unified viscoplastic constitutive relations that reflect the dislocation glide and diffusion controlled mechanisms. It has been proved previously that the effect of dislocation glide (contributing the plastic strain rate
) on the mechanical deformation decreases with reducing of the grain size and holds up until that the grain size decreases to a critical dimension dc where diffusion creep mechanism(contributing the plastic strain rate
and
) begins to make a major action on the mechanical deformation of NC materials. Hence, when the grain size falls below the critical size dc, the plastic flow is controlled by diffusion mechanism with no dislocation glide, and the corresponding plastic strain rate of the inclusion phase is given[15] by
(1)
where
(2)
(3)
(4)
In Eqn.(1),
is viscoplastic strain rate of grain interior,
is strain rate controlled by dislocation glide,
and
are strain rates controlled by coble and N-H diffusions respectively. In Eqn.(2),
is material constant, ρ0 is initial dislocation density and σ0 is initial stress corresponding with the initial dislocation density ρ0. In Eqns.(3)-(4),
and
are coble and N-H diffusion coefficients. σI is compressive stress of grain interior, Ω is atomic volume, T is absolute temperature, k is the Boltzemann constant. The dislocation density ρ in Eqn.(2) is considered as internal variable associated with storage and vanish of the dislocation. The evolution equation for the dislocation density can be given[16] by
(5)
where
(6)
and C1, C20 and
are material constants, the exponents m in Eqn.(2) and n in Eqn.(6) are inversely proportional to the absolute temperature T, they can be seen as constants for a given temperature.
The constitutive description of the deformation behavior is provided by the phase mixture model. In Ref.[17], the grain boundary phase was described as a viscous pseudo-amorphous phase. In a more recent version of the model[18], diffusion-controlled plastic flow of the grain boundary phase was considered. The corresponding plastic strain rate is given by
(7)
where σGB is the stress acting in the grain boundary phase, DGB is the self-diffusion coefficient for grain boundary diffusion, and A is numerical coefficient.
To establish the overall mechanical behaviors of porous NC materials, we adopt the energy principle to build the constitutive law of the grain including grain interior and grain boundary where the effect of evolutional porosity will also be included. It can be written as:
(8)
where UI and UM are the work of grain interior and grain boundary respectively, Up is the work of the pores that do not apply work (Up=0). CI, CM and Cp are the volume fractions of grain interior, grain boundary and the pores respectively. CI and CM can be given by
(9)
Eqn.(8) can be written as:
(10)
where
is the overall stress of the materials and E is the overall strain of the materials. It is assumed that the overall strain rate is same with the strain rate of each phase in small plastic strain range, we can get that
(11)
It should be noted that the iso-strain assumption is approximately reasonable for the small deformation of NC materials. Overall, the stress-strain relations of NC materials can be determined by varying the level of the total strain.
3 Results and discussion
To verify the model established in this paper, numerical simulations for our prepared porous NC Ni are carried out based on the developed method in this paper. The following parameters are used during the numerical calculation: C1=52.86, C20=18.5, α=0.33, β=0.256 nm, M=3.06, m=230, n=21.25,
= 0.005/s, σ0=195 MPa, G=51.7 GPa, Ω=1.09×10-29 m3,
T=290 K, τp=117.6 MPa, ηi=2 MPa?s.
Figs.1 and 2 show that the calculated stress—strain curves of the porous NC Ni are compared with the experimental stress-strain curves of the porous NC Ni at different grain sizes and strain rates under the unaxial compression. It is obvious that stress—strain curves of the calculated results fit well with the experimental results in the small plastic range whereas the difference increases gradually with the increasing of strain. This should be related with no consideration of the evolution of porosity with the increasing of strain.
WEETMAN et al[19-21] have taken NC materials with the inert gas condensation technique to investigate the effect of porosity on the mechanical behavior of NC materials, but they do not take the evolution of porosity into account for that the porosity changes with the
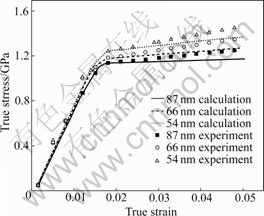
Fig.1 Comparison between calculated and experimental stress—strain curves at different strain rates
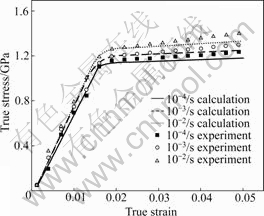
Fig.2 Comparison between calculated and experimental stress—strain curves with different grain sizes
variety of strain. For the purpose of studying the evolution of porosity with the increase of strain, we took a group of five samples previously prepared in one batch (with same grain size and initial porosity) to be compressed and downloaded at the strain of 2%, 4%, 6%, 8%, 10% respectively at a constant strain rate. The porosity values of those five downloaded samples were determined before and after compression, and the results are listed in Table 1.
Table 1 Porosity values of five samples before and after compression

Table 1 shows that the evolutional porosity decreases from 10% to 0.53% with the increasing strain from 0 to 0.1. It is obvious that the porosity decreases and the evolution become important with the increase of strain. This result suggests that the evolution of porosity does exist and has an impact on the stress-strain relations at different grain sizes and strain rates. With the increase of strain, the porosity will decrease and lead to the increase of relevant true stress. Therefore, if we take the evolution of porosity into account to calculate, the values of calculated true stress will fit better with the experimental values over a wide range of plastic strain.
Since the evolution of porosity exists and affects the stress-strain relations, investigations on the evolution of porosity and the effect of the evolution of porosity on the stress-strain relations need to be studied more completely for constitutive modeling of NC materials in the future.
4 Conclusions
A composite constitutive model consisting grain interior and grain boundary was proposed to investigate the plastic deformation of the porous NC materials. First, Constitutive equations of grain interior driven by dislocation glide and diffusion and grain boundary controlled by a boundary diffusion are established respectively. The energy principle approach is used to establish the mechanical calculation model for the plastic deformation of the porous NC materials. Comparison results between the experimental data and the model predictions show that the developed model in this paper appears to be capable of reflecting the plastic deformation of porous NC materials. Further analysis on the effect of the evolution of porosity on stress-strain relations should be studied.
References
[1] GLEITER H. Nanocrystalline materials [J]. Progress in Materials Science, 1989, 33(4): 223-315.
[2] SURYANARAYANA C. Nanocrystalline materials [J]. International Materials Reviews, 1995, 40(2): 41-64.
[3] CHIANG Y M. Introduction and overview: Physical properties of nanostructured materials [J]. Journal of Electroceramics, 1997, 1(3): 205-209.
[4] SANDERS P G, FOUGERE G E, THOMPSON L J, EASTMAN J A, WEERTMAN J R. Improvements in the synthesis and compaction of nanocrystalline materials [J]. Nanostructed Materials, 1997, 8(3): 243-252.
[5] TELLKAMP V L, MELMED A, LAVERNIA E J. Mechanical behavior and microstructure of a thermally stable bulk nanostructured Al alloy [J]. Metallurgical and Materials Transactions A, 2001, 32(9): 2335-2343.
[6] VALIEV R Z, ISLAMGALIEV R K, ALEXANDROV I V. Bulk nanostructured materials from severe plastic deformation [J]. Progress in Materials Science, 2000, 45(2): 103-189.
[7] ERB U. Electrodeposited nanocrystals: Synthesis, properties and industrial applications [J]. Nanostructured Materials, 1995, 6(5/8): 533-538.
[8] EBRAHIMI F, ZHAI Q, KONG D. Deformation and fracture of electrodeposited copper [J]. Scripta Materialia, 1998, 39(3): 315-321.
[9] WANG Y M, WANG K, PAN D, LU K, HEMKER K J, MA E. Microsample tensile testing of nanocrystalline copper [J]. Scripta Materialia, 2003, 48(12): 1581-1586.
[10] LU L, LI S X, LU K. An abnormal strain rate effect on tensile behavior in nanocrystalline copper [J]. Scripta Mater, 2001, 45(10): 1163-1169.
[11] KIM H S, BUSH M B. The effect of grain size and porosity on the elastic modulus of nanosrystalline materials [J]. Nanostructured Materials, 1999, 11(3): 361-367.
[12] JIANG B, WENG G J. A generalized self-consistent polycrystal model for the yield strength of nanocrystalline materials [J]. Journal of the Mechanics and Physics of Solids, 2004, 52(5): 1125-1149.
[13] JIANG B, WENG G J. A theory of compressive yield strength of nano-grained ceramics [J]. International Journal of Plasticity, 2004, 20(11): 2007-2026.
[14] LI J, WENG G J. A secant-viscosity composite model for the strain-rate sensitivity of nanocrystalline materials [J]. International Journal of Plasticity, 2007, 23(12): 2115-2133.
[15] KIM H S, ESTRIN Y. Phase mixture modeling of strain rate dependent mechanical behavior of nanostructured materials [J]. Acta Materialia, 2005, 53(3): 765-772.
[16] KIM H S, ESTRIN Y, GUTMANAS E Y, RHEE C K. A constitutive model for densification of metal compacts: the case of copper [J]. Materials Science and Engineering A, 2001, 307 (1/2): 67-73.
[17] KIM H S, BUSH M B, ESTRIN Y. A phase mixture model of a particle reinforced composite with fine microstructure [J]. Materials Science & Engineering A, 2000, 276(1/2): 175-185.
[18] KIM H S, ESTRIN Y, BUSH M B. Plastic deformation behaviour of fine-grained materials [J]. Acta Materialia, 2000, 48(2): 493-504.
[19] NIEMANN G W, WEERTMAN J R, SIEGEL R W. Tensile strength and creep properties of nanocrystalline palladium [J]. Scripta Metall Mater, 1990, 24(1): 145-150.
[20] NIEMANN G W, WEERTMAN J R, SIEGEL R W. Mechanical behavior of nanocrystalline Cu and Pd [J]. Materials Research Society, 1991, 6(5): 1012-1027.
[21] NIEMANN G W, WEERTMAN J R, SIEGEL R W. Mechanical behavior nanocrystalline metals [J]. Nanostructured Materials, 1992, 1(2): 185-190.
(Edited by YANG You-ping)
Foundation item: Project(10502025) supported by the National Natural Science Foundation of China; Project(101005) supported by the Fok Ying Tong Education Foundation; Project(BK2007528) supported by the Natural Science Foundation of Jiangsu Province, China
Received date: 2008-06-25; Accepted date: 2008-08-05
Corresponding author: ZHOU Jian-qiu, Professor; Tel: +86-25-83587299; E-mail: zhouj@njut.edu.cn