
J. Cent. South Univ. (2019) 26: 3410-3419
DOI: https://doi.org/10.1007/s11771-019-4263-8

Characterizing properties of magnesium oxychloride cement concrete pavement
ZHENG Wei-xin(郑卫新)1, 2, 3, XIAO Xue-ying(肖学英)1, 2, CHANG Cheng-gong(常成功)1, 2,DONG Jin-mei(董金美)1, 2, WEN Jing(文静)1, 2, HUANG Qing(黄青)1, 2, 3,ZHOU Yuan(周园)1, 2, LI Ying(李颖)1,2
1. Key Laboratory of Comprehensive and Highly Efficient Utilization of Salt Lake Resources, Qinghai Institute of Salt Lakes, Chinese Academy of Sciences, Xining 810008, China;
2. Key Laboratory of Salt Lake Resources Chemistry of Qinghai Province, Xining 810008, China;
3. University of Chinese Academy of Sciences, Beijing 100049, China
Central South University Press and Springer-Verlag GmbH Germany, part of Springer Nature 2019
Abstract: The performance of magnesium oxychloride cement concrete (MOCC) in road engineering in the arid region in northwest China was investigated over a two-year period. Two categories of MOCC pavement, light-burnt magnesia concrete road (Road-L) and dolomite concrete road (Road-D), were prepared with light-burnt magnesia and a mixture of light-burnt magnesia and caustic dolomite (1:3 by mass), respectively. Variations in the properties of the MOCC pavement, such as compressive and flexural strength, mineralogical phase, and microstructure, after being exposed to two rainy seasons in the field were monitored. The compressive strength of the cored samples were conducted after being aged for 28 d, and the compressive and flexural strength were tested at ages of 1, 2, 3, 28, 90, 180, 270, 360 and 720 d. The mineralogical phase and microstructure of the pavement were also analyzed by X-ray diffraction (XRD) and scanning electron microscopy (SEM). The results demonstrate that MOCC pavement obtained desirable compressive and flexural strengths after curing for 3 d for Road-L and 28 d for Road-D. Both of the compressive and flexural strength of Road-L and Road-D decreased slightly after experiencing two rainy seasons, with the major hydration products being 5Mg(OH)2·MgCl2·8H2O (Phase 5) and 3Mg(OH)2·MgCl2·8H2O (Phase 3). The decomposition of Phase 5 is mainly responsible for reducing the mechanical strength of the MOCC pavement.
Key words: magnesium oxychloride cement concrete (MOCC); pavement; mechanical strength; microstructure
Cite this article as: ZHENG Wei-xin, XIAO Xue-ying, CHANG Cheng-gong, DONG Jin-mei, WEN Jing, HUANG Qing, ZHOU Yuan, LI Ying. Characterizing properties of magnesium oxychloride cement concrete pavement [J]. Journal of Central South University, 2019, 26(12): 3410-3419. DOI: https://doi.org/10.1007/s11771-019-4263-8.
1 Introduction
Magnesium oxychloride cement (MOC) is formed by the addition of magnesium chloride solution to magnesia or caustic dolomite [1-3]. At room temperature and pressure, the chemical reactions may happen in the MgO-MgCl2-H2O system as the following equations:
5MgO+MgCl2+13H2O→5Mg(OH)2·MgCl2·8H2O (Phase 5) (1)
3MgO+MgCl2+11H2O→3Mg(OH)2·MgCl2·8H2O (Phase 3) (2)
MgO+H2O→Mg(OH)2 (3)
The above equations [4] show that the hydration product of MOC depends on the ratio of the constituents, including the molar ratios of MgO/MgCl2 and H2O/MgCl2. In addition, the active MgO affects the hydration product of MOC [5]. Hence, the hydration products in MOC could consist of Phase 5, Phase 3, Mg(OH)2, or any combination of them. Phase 5 and Phase 3 are responsible for the excellent mechanical properties of MOC [6].
Compared with Portland cement, MOC has many advantageous characteristics, such as lightweight, high strength, good abrasive resistance, and dry curing. Based on the above characteristics, MOC has been applied in many fields, such as door frames, fireproof materials, floor tiles, grinding wheels, and thermal insulation materials [7–11]. The versatility of magnesium-based cement materials has inspired many researchers to focus on characterizing its properties and developing its applications, including improving its water resistance abilities [12, 13], solidifying industrial waste [14], optimizing mixture proportions [15], and sequestrating carbon dioxide [16].
Compared with the properties of Portland cement, the merits of MOC may be suitable for use as pavement materials, especially in the arid area in Northwest China, where building traditional concrete pavement required costly amounts of water for curing. However, there are only a few reports available worldwide on magnesium oxychloride cement concrete (MOCC) [17, 18]. Moreover, as far as we know, there is insufficient research in the literature on MOCC applied to mass concrete like road pavement. In particular, its properties and variations are noteworthy issues.
Considering all of the aforementioned factors, this paper is dedicated to studying the mechanical strength, hydration product and microstructure of MOCC used as pavement in the open air. Two types of MOCC pavements were established, namely, light-burnt magnesia concrete road (Road-L) and dolomite concrete road (Road-D). The performance variation of the two road pavements with age were comparatively studied as well.
2 Materials and experiment
2.1 Materials
The constituents for preparing MOCC included light-burnt magnesia, caustic dolomite, bischofite, water resistance modifier, sand, and coarse and fine aggregates. The magnesium oxide used in this study was commercially available light-burnt magnesia with a content of active MgO of 50.51% by mass, which was obtained from Liaoning province in China. Caustic dolomite powder was in the form of calcined dolomite from a tunnel kiln, and the content of active MgO was 14.56% by mass. The direct hydration method was used to test the content of active MgO in the constituents [19]. The bischofite containing the magnesium chloride employed was in the form of hygroscopic hexahydrate (MgCl2·6H2O) crystals from Jiayoumeiye Ltd., Qinghai province, China. The chemical compositions of light-burnt magnesia, dolomite powder, and bischofite were analyzed by X-ray fluorescence spectrometry (XRF, Axios PW4400) and are listed in Tables 1 and 2. The water resistance additive in this study was the same as in Ref. [4]. The coarse aggregate was produced in the Haixi Prefecture, Qinghai province, China. Its sizes were 5-10 and 10-30 mm. Locally available sand that passed a 5-mm sieve was retained on a 0.35-mm sieve for utilization.
Table 1 Chemical composition of light-burnt magnesia, dolomite powder (mass fraction, %)
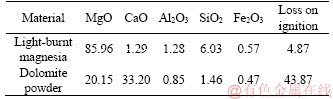
Table 2 Chemical composition of bischofite (mass fraction, %)

2.2 Brine preparation
The brine was prepared by dissolving bischofite in tap water. To dissolve a significant amount of bischofite and to precisely control the concentration of brine in freshly mixed concrete, two circulation systems were designed for the dissolution process of bischofite (see Figure 1). The first system was a dissolving tank (40 m×40 m×3 m) formed from two circulating pumps, labeled A and B. This system was mainly responsible for bischofite dissolution and impurities precipitation.
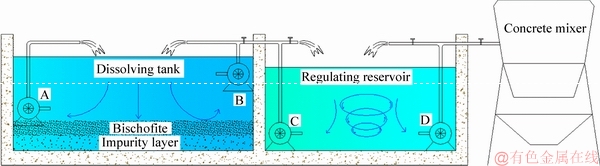
Figure 1 Bischofite solution system
The second system was a regulating reservoir, also installed with two circulating pumps, labeled C and D. This system was largely responsible for precisely controlling the brine concentration. The concentration of the solution is expressed in terms of the Baume degree (°Bé).
2.3 Pavement construction and specimen preparation
Two sections of MOCCs pavement were constructed a few kilometers north of Delingha city, Haixi Prefecture, Qinghai Province in northwestern China in August 2014. Light-burnt magnesia was used to mix MOC concrete for pavement, labeled as Road-L. The blended powder, used to keep the mass ratio of light-burnt magnesia to caustic dolomite at 1:3, was used to mix MOC concrete for another section of pavement labeled as Road-D. Road-L and Road-D had lengths of 1000 and 220 m, respectively. The design compressive strength and flexural strength of both sections of pavements were 25 and 4 MPa, respectively. Table 3 presents the mix proportions for each section of road. The content of water-resistance additives was 10% by mass for the light-burnt magnesia for Road-L or the blended power for Road-D. The molar ratio of active MgO to MgCl2 (MgOa/MgCl2) in the paste was about 5.0 for Road-L and about 5.4 for Road-D, both of which were prepared according to Table 3.
Table 3 Proportion of constituents in MOCC pavement
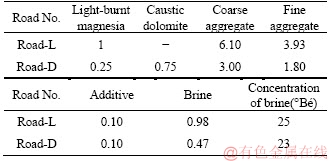
The powders and aggregate were first mixed thoroughly in a concrete mixer, and then brine was added to the blended mixture. This mixture was then mixed for a few minutes to produce MOCC. The well-mixed MOCC paste was transported and poured into the prefabricated formwork (the semi-side road size of 6 m×3.5 m×0.25 m), and a wood board with the thickness of 1.5 cm was set at the connection between the semi-side pavements to prevent any irregular cracking of the road surface.
Since MOCC is fast-hardening, and it is necessary to ensure the consistency of the workability, the transport time of the paste from the mixing station to the pouring site was limited to less than 20 min. After pouring the concrete into the model, four concrete vibrating tubes were adopted to synchronously vibrate from the periphery to the center for 10 min. Then manual operation was conducted for surface finishing.
At the same time, standard specimens were cast in the field and were used to characterize the mechanical properties of MOCC. The specimens were immediately buried in the roadside at locations A1, A2, B1, B2, C1, C2, D1 and D2 in the schematic diagram in Figure 2 after demolding. Standard specimens mixed with light-burnt magnesia (Specimen-L) were buried near Road-L, and the ones mixed with blended power (Specimen-D) were buried near Road-D. The constituents, production conditions, and curing environments of the standard specimens were maximally consistent with that of the pavement.
The monthly rainfall totals in the Delingha area in 2015 and 2016 [20] are listed in Table 4. Based on the data in Table 4, the MOCC pavements suffered from a rainy season from May to September each year. During the curing time, from about the 270th day to about 390th day, the MOCC pavements and specimens experienced the first rainy season.
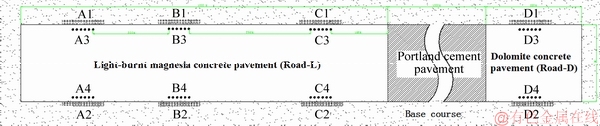
Figure 2 Diagrammatic sketch of road and specimen’s location
Table 4 Monthly rainfall (mm) in Delingha area
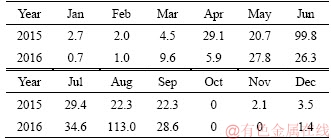
2.4 Testing method
The core samples were drilled around A3, A4, B3, B4, C3, C4, D3 and D4, as shown in Figure 2 with a core drilling machine (d=100 mm) at the age of 28 d. The cylindrical core specimens (d=100 mm, l=250 mm) and standard cube specimens (l=150 mm) were used to test compressive strength by a material testing system (SANYU, SYE-3000D) with a maximum load of 3000 kN at a loading rate of (0.5±0.1) MPa/s. The flexural strengths of the cured standard MOCC specimens (150 mm×150 mm×550 mm) were investigated with a universal testing machine (WDW-200Y, span of 150 mm, loading speed of (0.5±0.005) MPa/s).
The mineralogical compositions of the upper surface of the MOCC pavement were sampled and measured by X-ray diffraction (XRD, PANalytical X’pert Pro). The particles prepared for XRD were ground and screened to less than 75 μm. The micro-morphology of the fractured surface within 2 cm of the upper surface of the MOCC pavement was characterized by scanning electron microscopy (SEM, JSM-5610LV) with gold coating.
3 Results and discussion
3.1 Mechanical properties
3.1.1 Compressive strength of core specimen and cube specimen
The compressive strengths of the core samples and cube samples are shown in Table 5 at an age of 28 d. The average compressive strength of the cube samples for the light-burnt magnesia concrete specimens (Specimen-L) and dolomite concrete specimens (Specimen-D) is 29.2 and 27.3 MPa, while that of core samples is 30.3 and 28.3 MPa, respectively. The compressive strengths of the core samples are relatively close to those of the cube samples at the same sampling points. For the light-burnt magnesia concrete, the differentials of compressive strength between the core sample (Core-L) and the cube sample are just within the range of 0.1-2.3 MPa. For example, the maximum difference value (2.3 MPa) at C3 is 7.9% of the average strength of the cube specimen.
For dolomite concrete, the differentials of compressive strength between the core sample (Core-D) and the cube specimen are only within the range of 0.4-1.7 MPa, and the maximum difference value is 6.2% of the average strength of cube specimens. It can be said that the embedded cube specimens (standard specimen) excellently display the superior mechanical properties of the pavement. The long-term mechanical properties of the MOCC road in this study are all characterized by the embedded cube specimens.
3.1.2 Compressive strength at different curing ages
The compressive strengths of the MOCC cube specimens from 1 to 720 d of curing in the field are shown in Figure 3. The compressive strengths of both the Road-L and Road-D samples at early ages (first 3 d) grow quickly and keep increasing at first and then decreased inconsiderably at later ages (after 28 d). The average compressive strengths of Road-L and Road-D are 26.2 and 24.6 MPa at 3 d, which are 90.7% and 90.4% of their compressive strength at 28 d, respectively. The compressive strength of Road-L already reaches and Road-D almost reaches the designed strength of pavement in a short curing time. The maximum values of the compressive strength for Road-L and Road-D are 31.8 MPa at 90 d and 30.5 MPa at 180 d, respectively.
Table 5 Compressive strength of cube specimen (Specimen-L and Specimen-D) and core specimen (Core-L and Core-D)
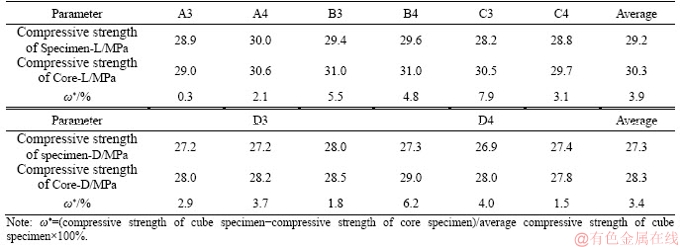
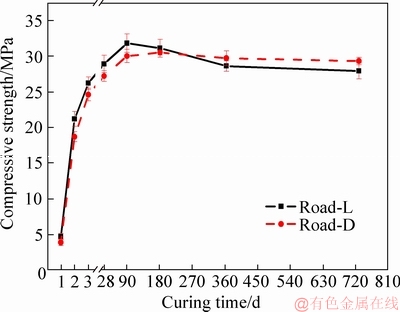
Figure 3 Compressive strength of MOCC specimens cured in air
After 180 d, compressive strengths of both Road-L and Road-D go down slightly. After undergoing a second rainy season (720 d), although the compressive strength of Road-L and Road-D is 12.3% and 3.9% lower than the maximum values, it is 11.6% and 17.2% higher than the designed value, respectively. The linear fitting equations between compressive strength and curing time for Road-L and Road-D after 180 d are y1=-0.0062x+32.36 (R2=0.86) and y2=-0.0021x+30.84 (R2=0.81), respectively. The slopes of equations y1 and y2 are very small, which means that the compressive strengths of Road-L and Road-D at later ages are relatively stable.
After pouring the molds, the pastes of both Road-L and Road-D sustained hydration for a period of several months, resulting in an increase of their compressive strengths. After 180 d, the pavements start to suffer the effects of rain, which gently decomposes the hydration product and washes against the filler in the matrix. Therefore, the compressive strengths of Road-L and Road-D reduce slightly.
3.1.3 Flexural strength at different curing ages
As shown in Figure 4, the variation tendency of the flexural strengths of Road-L and Road-D is similar to that of the compressive strengths from 1 to 720 d. The flexural strength of Road-L and Road-D is 3.74 and 3.51 MPa at 3 d, which is 91.0% (4.11 MPa) and 89.3% (3.93 MPa) of the flexural strength at 28 d, respectively. Upon increasing the curing time, the flexural strength of Road-L already and Road-D almost reaches the designed strength of the pavement at 28 d. The maximum flexural strength values of Road-L and Road-D appear at 90 and 180 d, respectively. After undergoing the second rainy season (720 d), the flexural strength of Road-L and Road-D is reduced to 3.87 and 4.19 MPa. The linear fitting equations between the flexural strength and curing time for Road-L and Road-D after 180 d are y3=-0.0012x+4.73 (R2=0.89) and y4=-0.0004x+ 4.48 (R2=0.83), respectively. The change in flexural strength of Road-L after suffering from two rainy seasons indicates that the water resistance of the MOCC pavement needs to be further improved, even when applied in arid zones.
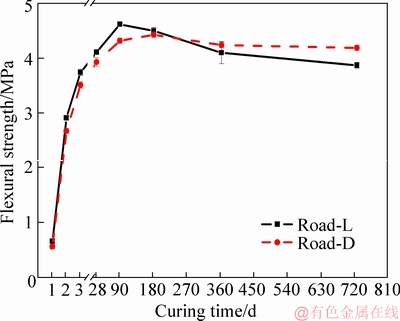
Figure 4 Flexural strength of MOCC specimens cured in air
Both the compressive and flexural strengths of Road-L are higher than those of Road-D in the earlier stage and become lower after reaching the highest point. For example, the compressive and flexural strengths of Road-L are 6.3% (28.9 MPa) and 4.6% (4.11 MPa) higher at 28 d but 4.8% (27.9 MPa) and 7.6% (3.87 MPa) lower at 720 d than that of Road-D, respectively.
These circumstances may be caused by the content of active MgO in caustic dolomite, the concentration of brine, and the mineralogical phase composition of the pavements. First, the content of active MgO in the mixture power of magnesia and caustic dolomite used for Road-D is lower than that of magnesia used for Road-L. The lower content of active MgO in the mixture power results in a slower hydration process [3]. Second, the lower the concentration of brine, the less the hydration process occurs in the MOC [17].
Both the content of active MgO and the concentration of brine used for Road-D lead to the slower formation rate of hydration products. Hence, the compressive and flexural strengths of Road-D are lower than those of Road-L at first, and Road-D needs more time to reach the maximum value. Other reasons for these phenomena are discussed in the next section.
3.2 Mineralogical composition
Figure 5 shows the XRD patterns of Road-L at different curing ages from 3 to 720 d. Figure 5 shows that the mineralogical phases in samples of Road-L change over time. From 3 to 180 d, the mineralogical phases are made up of major Phase 5, Phase 3, CaCO3, and trace amounts of MgCO3 and SiO2. However, the intensity of the characteristic diffraction peaks of Phase 3 reduces with increasing age, and the peaks of Phase 3 almost disappear after 180 d. Moreover, the characteristic diffraction peaks of Mg(OH)2 apparently emerge at 540 and 720 d. Except for Phase 5, Phase 3, and Mg(OH)2, other mineralogical phases originate from the light-burnt magnesia and aggregate.
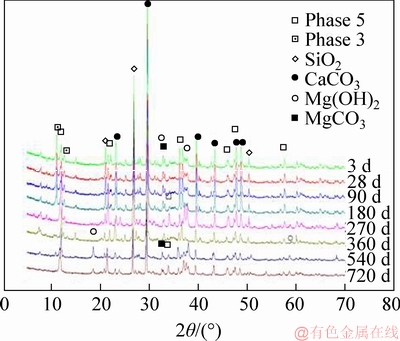
Figure 5 XRD patterns of Road-L (B3) with different ages
Unfortunately, due to the powder for XRD testing being blended with different contents of aggregate particles for each sampling at different ages, the quantitative composition of the mineralogical phases in MOCC analyzed by XRD is not representative enough to reflect the change tendencies of all kinds of phases with the increase of service time. However, the intensity variation of the characteristic peaks of Phase 5, Phase 3 and Mg(OH)2 with time indicates the transformation to a certain degree.
The initial abundance of Phase 5 and Phase 3 primarily depends on the MgOa/MgCl2 used to produce the MOCC. This circumstance is in line with how Phase 5 and Phase 3 are formed simultaneously in the MgO-MgCl2-H2O system when MgOa/MgCl2 is about or less than 5 [21]. However, the change trend of the intensity of characteristic diffraction peaks indicates that Phase 5 and Phase 3 gradually decompose into Mg2+, Cl-, and Mg(OH)2 in the open air by rain action, as shown in Eqs. (4) and (5) [22], after the first rainy season:
5Mg(OH)2·MgCl2·8H2O→5Mg(OH)2↓+Mg2++2Cl-+8H2O (4)
3Mg(OH)2·MgCl2·8H2O→3Mg(OH)2↓+Mg2++2Cl-+8H2O (5)
It can be seen from Figure 6 that Road-D has a similar hydration product to Road-L. For all the Road-D specimens, mineralogical phases are made up majorly of Phase 5, Phase 3, CaCO3, SiO2 and CaMg(CO3)2, and minorly of Mg(OH)2 and MgCO3 from 180 to 720 d. Compared with Road-L, the characteristic diffraction peaks of Mg(OH)2 are lower at the same curing age, which means less decomposition of the hydration product. Road-D contains more CaMg(CO3)2, which comes from dolomite raw ore. Although the MgOa/MgCl2 of Road-D is larger than 5, the low active MgO content of caustic dolomite results in the formation of Phase 3 [5]. In addition, a chlorartinite phase (see Figure 6) is found in one-year-old samples, which is yielded by the carbonation of Phase 5, Phase 3, and Mg(OH)2 with H2O and CO2 in the open air.
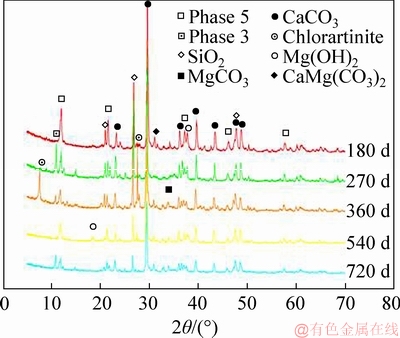
Figure 6 XRD patterns of Road-D (D3) with different ages
The impurities, such as MgCO3, SiO2 and CaCO3 in light-burnt magnesia and caustic dolomite, act as filler, which improves the mechanical strength of MOCC [23]. However, the filler in MOCC is washed away by rain as time proceeds. As shown in Figure 7, the peak intensities of SiO2 and CaCO3 decrease as time proceeds and significantly reduce after the first rainy season (540 d).
This circumstance is probably one of the reasons causing the reduction of mechanical properties with the increasing service time of the pavement. However, the influence on the reduction of mechanical strength by washing away the filler may be lower than by decomposing the hydration product. Hence, the mechanical strength of Road-D is higher than that of Road-L after 180 d.
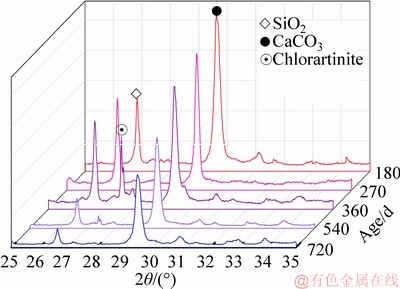
Figure 7 XRD interval graphs of Road-D (D3) with different ages
Research on the MgCl2-NaOH-H2O system conducted by MAZURANIC et al [24] indicated that the pH range of optimum basicity for Phase 3 formation was from 6.12 to 6.40, much lower than that of Phase 5 formation, which was pH=7.65± 0.05 or even higher. The fact that the MOCC pavement was built on salt-containing soil (soil pH>8.5) and the pH of the rain containing alkaline particles brought by the soil was more than 7.5 [25] possibly leads to ensure the formation and preservation of Phase 5 but the disappearance of Phase 3.
3.3 Microstructure
Figure 8 shows the SEM images of the fractured surface of Road-L from 28 to 720 d and Road-D at 720 d. Figure 8(a) shows that Phase 5 and Phase 3 form needle, rod-like crystals with large length-to-diameter ratios on the fractured surface of Road-L. The microstructure at 90 d is similar to the one at 28 d. The dense and spidery Phase 5 and Phase 3 needle, rod-like crystals interlacing with each other all lead to Road-L obtaining a high strength.
After 180 d (see Figure 8(c)), the needle, rod-like crystals convert into short, rod-like crystals, meaning that Phase 5 and Phase 3 slightly decompose into Mg(OH)2 [5]. The hydration product, decomposition product, and intergranular filler agglomerate into a flaky substance. The SEM image at 270 d is similar to that at 180 d.
At 360 d, the needle, rod-like crystals decreased in mass and proportion, and there is an increase in the amount of surface, flaky substance, the structure of which is looser than that of Phase 5 and Phase 3 needle, and rod-like crystal (see Figure 8(e)).
After undergoing the first rainy season (540 d; Figure 8(f)), very few of the needle, rod-like crystals are located in pores with a size of about 10 μm. Thus, a relatively loose structure forms, which acts against the mechanical strength of the pavement.
After two years, the SEM images indicate that Phase 5, needle, rod-like crystals transform into rod-like Mg(OH)2 crystal and disperse disorderly around the inner wall of large pores on the fractured surface. This leads to a looser structure of the MOCC pavement and a decrease in the mechanical strength. However, the XRD results show that the matrix mainly comprises Phase 5, which ensures the strength of Road-L. Hence, the compressive and flexural strengths of Road-L after two years of service are only slightly lower than the highest strength at 90 d.
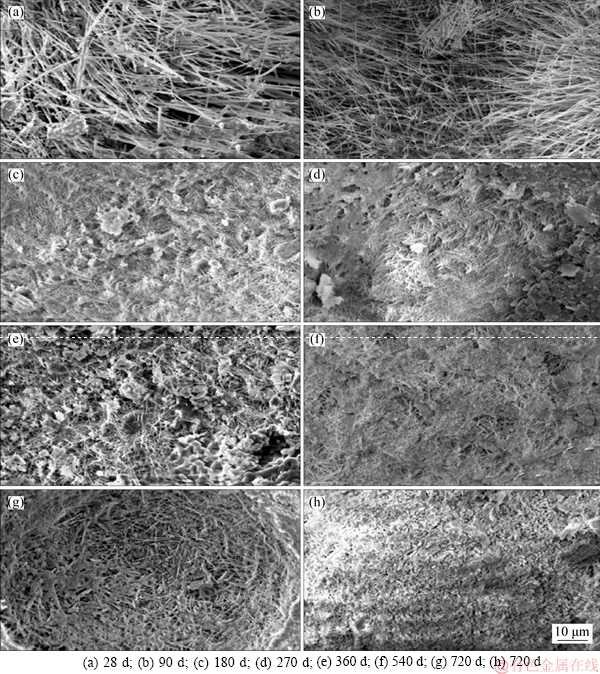
Figure 8 SEM images of Road-L (a-g) and Road-D (h) with different ages:
As for Road-D, there are neither many Phase 5, needle, rod-like crystals nor any loose pores or fissures after 720 d (Figure 8(h)). Thus, the seemingly dense structure on the whole also contributes to strength maintenance to some extent.
4 Conclusions
This work investigates the performance of magnesium oxychloride cement concrete in road engineering. A series of tests on the compressive and flexural strength, mineralogical composition, and microstructure of the MOCC have been carried out. Based on the experimental results, the conclusions can be drawn as follows:
1) The MOCC pavement prepared by light-burnt magnesia (Road-L) and the blended mix of light-burnt magnesia and calcined dolomite (Road-D) obtained high mechanical properties in the short term. Although the poor water resistance of the MOC material prevents it from serving in the outdoor environment for a long time [26], but the mechanical properties of Road-D and Road-L does not appear sharply lower. After undergoing two rainy seasons, compressive and flexural strengths of road-D can meet the requirements of the original design value (compressive strengths ≥25 MPa, flexural strength ≥4.0 MPa).
2) Phase 5 is mainly responsible for the mechanical strength of the MOCC pavement. The decomposition of Phase 5 leads to decreasing the mechanical strength of the MOCC pavement after undergoing a rainy season.
3) The MOCC pavement prepared with the mixture of magnesia and caustic dolomite gains strength slowly but has a better water resistance while undergoing rainy seasons than the one prepared with magnesia.
References
[1] MAHMUT A, MEHMET Y. Influence of filler on the properties of magnesium oxychloride cement prepared from dolomite [J]. Emerging Materials Research, 2017, 6(2): 417-421. DOI: 10.1680/jemmr.17.00012.
[2] WEN Jing, YU Hong-fa, LI Ying, WU Cheng-you, DONG Jin-mei, ZHENG Li-na. Effects of H3PO4 and Ca(H2PO4)2 on mechanical properties and water resistance of thermally decomposed magnesium oxychloride cement [J]. Journal of Central South University, 2013, 20(12): 3729-3735. DOI: 10.1007/s.11771-013-1901-4.
[3] HUANG Ting-jie, YUAN Qiang, DENG De-hua. The role of phosphoric acid in improving the sthrength of magnesium oxychloride cement pastes with large molar ratios of H2O/MgCl2 [J]. Cement and Concrete Composites, 2019, 97: 379-386. DOI: 10.1016/ j.cemconcomp.2019.01.013.
[4] LI Ying, LI Zong-jin, PEI Hua-fu, YU Hong-fa. The influence of FeSO4 and KH2PO4 on the performance of magnesium oxychloride cement [J]. Construction and Building Materials, 2016, 102: 233-238. DOI: 10.1016/ j.cobuildmat.2015.10.186.
[5] ZHANG Zheng-yu, DAI Chang-lu, ZHANG Quan-chang, GUO Bo-zhi, LIU Wei-ling. Study on the formation mechanism of Phase 5 and Phase 3 [J]. Sci China (Ser B), 1991, (1): 82-89. (in Chinese)
[6] DENG De-hua, ZHANG Chuan-mei. The formation mechanism of the hydrate phases in magnesium oxychloride cement [J]. Cement and Concrete Research, 1999, 29(9): 1365-1371. DOI: 10.1016/S0008-8846(98)00247-6.
[7] ZHOU Xiang-ming, LI Zong-jin. Light-weight wood- magnesium oxychloride cement composite building products made by extrusion [J]. Construction and Building Materials, 2012, 27(1): 382-389. DOI: 10.1016/j.conbuildmat. 2011.07.033.
[8] MONTLE J, MAYHAN K. The role of magnesium oxychloride as a fire-resistive material [J]. Fire Technology, 1974, 10(3): 201-210.
[9] WANG Yi-chao, WEI Lin-zhuo, YU Jiang-tao, YU Ke-quan. Mechanical properties of high ductile magnesium oxychloride cement-based composites after water soaking [J]. Cement and Concrete Composites, 2019, 97: 248-258. DOI: 10.1016/ j.cemconcomp.2018.12.028.
[10] LI Guo-zhong, YU Yan-zhen, LI Jian-quan, WANG Ying-zi, LIU Hua-shi. Experimental study on urban refuse/ magnesium oxychloride cement compound floor tile [J]. Cement and Concrete Research, 2003, 33(10): 1663-1668. DOI: 10.1016/S0008-8846(03)00136-4.
[11] KARIMI Y, MONSHI A. Effect of magnesium chloride concentrations on the properties of magnesium oxychloride cement for nano SiC composite purposes [J]. Ceramics International, 2011, 37(7): 2405-2410. DOI: 10.1016/ j.ceramint.2011.05.082.
[12] HE Ping-ping, POON C S, TSANG D C W. Effect of pulverized fuel ash and CO2 curing on the water resistance of magnesium oxychloride cement (MOC) [J]. Cement and Concrete Research, 2017, 97: 115-122. DOI: 10.1016/ j.cemconres.2017.03.005.
[13] HE Ping-ping, POON C S, TSANG D C W. Comparison of glass powder and pulverized fuel ash for improving the water resistance of magnesium oxychloride cement [J]. Cement and Concrete Composites, 2018, 86: 98-109. DOI: 10.1016/j.cemconcomp.2017.11.010.
[14] CHAU C K, CHAN J, LI Zong-jin. Influences of fly ash on magnesium oxychloride mortar [J]. Cement and Concrete Composites, 2009, 31(4): 250-254. DOI: 10.1016/ j.cemconcomp.2009.02.011.
[15] LI Zong-jin, CHAU C K. Influence of molar ratios on properties of magnesium oxychloride cement [J]. Cement and Concrete Research, 2007, 37: 866-870. DOI: 10.1016/j.cemconres.2007.03.015.
[16] POWER I M, DIPPLI G M, FRANCIS P S. Francis, assessing the carbon sequestration potential of magnesium oxychloride cement building materials [J]. Cement and Concrete Composites, 2017, 78: 97-107. DOI: 10.1016/ j.cemconcomp.2017.01.003.
[17] QIAO Hong-xia, GONG Wei, SHI Ying-ying, ELIZABETH M, WAN Ji-ru, DONG Jin-mei. Experimental study on magnesium oxychloride cement concrete [J]. Emerging Materials Research, 2016, 5(2): 248-255. DOI: 10.1680/ jemmr.16.00012.
[18] MISRA A K, MATHUR R. Magnesium oxychloride cement concrete [J]. Bull Mater Sci, 2007, 30(3): 239-246.
[19] WB/T 1019-2002. Caustic burned magnesia for magnesium oxychloride cement products [S]. (in Chinese)
[20] China meteorological data interchange platform [EB/OL]. [2017-04-24]. http://data. cma.cn/.
[21] BILINSKI H, MATKOVIC B, MAZURANIC C, ZUNIC T. B. The formation of magnesium oxychloride phases in systems MgO-MgCl2-H2O and NaOH-MgCl2-H2O [J]. Journal of the American Ceramic Society, 1984, 67(4): 266-269. DOI: 10.1111/j.1151-2916.1984.tb18844.x.
[22] DENG De-hua. The mechanism for soluble phosphates to improve the water resistance of magnesium oxychloride cement [J]. Cement and Concrete Research, 2003, 33(9): 1311-1317. DOI: 10.1016/S0008-8846(03)00043-7.
[23] LI Ying, YU Hong-fa, ZHENG Li-na, WEN Jin, WU Cheng- you, TAN Yong-shan. Compressive strength of fly ash magnesium oxychloride cement containing granite wastes [J]. Construction and Building Materials, 2013, 38: 1-7. DOI: 10.1016/j.conbuildmat.2012.06.016.
[24] MAZURANIC C, BILINSKI H, MATKOVIC B. Reaction products in the system MgCl2-NaOH-H2O [J]. Journal of the American Ceramic Society, 1982, 10: 523-526. DOI: 10.1111/j.1151-2916.1982.tb10346.x.
[25] ZHOU Chang-jin, DONG Suo-cheng. Water quality of main rivers in the qaidam basin and water environmental protection [J]. Resources Science, 2002, 24(2): 37-41. (in Chinese)
[26] HUANG Qing, XIAO Xue-ying, LI Ying, AN Shen-Xia, CHANG Cheng-gong, Wen Jing, ZHENG Wei-xin, DONG Jin-mei. Research on the properties of magnesium oxychloride cement prepared with simulated seawater [J]. Advances in Cement Research, 2018, 30(7): 277-284. DOI: 10.1680/jadcr.17.00127.
(Edited by FANG Jing-hua)
中文导读
氯氧镁水泥混凝土路面性能表征
摘要:本文用轻烧氧化镁和轻烧氧化镁与苛性白云石的混合物(质量比为1:3)制备了氯氧镁水泥混凝土(MOCC),并将其应用于西北干旱地区道路工程中,分别修建了Road-L和Road-D两种MOCC路面。通过抗压强度、抗折强度、物相组成及微观结构等性能测试,研究了MOCC路面材料在两年龄期内的性能变化规律。测试了28 d龄期时试样的抗压强度,以及1、2、3、28、90、180、270、360和720 d龄期时预埋试件的抗压强度和抗折强度。采用X射线衍射和扫描电镜对路面的矿物组成和微观结构进行了分析。结果表明,养护3 d龄期时Road-L路段的抗压强度和抗折强度达到设计要求,而Road-D路段养护28 d时达到设计要求,主要水化产物为5Mg(OH)2·MgCl2·8H2O(5相)和3Mg(OH)2·MgCl2·8H2O(3相)。经历两个雨季后,路段Road-L和Road-D的抗压强度和抗折强度均略有下降,服役过程中5相被雨水分解是导致MOCC路面机械强度降低的主要原因。
关键词:氯氧镁水泥混凝土;路面;机械强度;微观结构
Foundation item: Project(2014–GX-A2A) supported by Major Science and Technology Projects of Qinghai Province, China; Projects(2018-NN-152, 2019-GX-165) supported by Science and Technology Achievements Transformation Project of Qinghai Province, China; Projects(2018467, 2019423) supported by the Youth Innovation Promotion Association of Chinese Academy of Sciences project supported by the High-end innovative talents Thousand talents Plan of Qinghai Province, China
Received date: 2018-12-24; Accepted date: 2019-03-18
Corresponding author: ZHOU Yuan, PhD, Professor; Tel: +86-13639716009; E-mail: zhouy6009@163.com; ORCID: 0000-0001-9908- 0466; LI Ying, PhD, Associate professor; Tel: +86-18997049460; E-mail: liying@isl.ac.cn; ORCID: 0000-0001-8182-5749