DOI:10.19476/j.ysxb.1004.0609.2017.06.04
板坯头/尾部平面形状对铝合金厚板粗轧头尾切除量的影响
燕 猛1,黄华贵1,张彩云1,杜凤山1,张尚斌2
(1. 燕山大学国家冷轧板带装备及工艺工程技术研究中心,秦皇岛 066004;
2. 中国第二重型机械集团公司重型机械设计研究院,成都 610052)
摘 要:为降低铝合金厚板粗轧头尾切除量,提高热轧铝板成材率,以5052铝合金材料为对象,基于DEFORM商用软件,利用刚塑性有限元方法模拟板厚和压下量对头尾鼓形深度的影响规律,建立头尾切除量定量预测模型。以此为基础,开展多道次可逆轧制过程中头/尾部普通平面、圆弧平面、梯形平面下的轧件头尾切除量演变规律探究,结果表明:圆弧平面与梯形平面能减少头尾切损约18%~20%。普通平面的头尾切除量预测模型已应用于实际轧制规程,预测结果和现场实测情况吻合,验证了有限元模拟结果的正确性。综合考虑铸锭的端面铣削工艺,梯形平面更有利于现有铝合金厚板热轧生产。
关键词:铝合金厚板;头尾切除量;头/尾部平面形状;刚塑性有限元方法
文章编号:1004-0609(2017)-06-1102-07 中图分类号:TG339 文献标志码:A
铝及铝合金板带具有质量轻、比强度高、耐蚀可焊、易加工、表面美观等优点,在航空航天、汽车、机械制造、船舶及化工等国民经济重要领域都有广泛应用[1-3]。铝合金热轧板坯,因大压下量轧制消除了铸造组织缺陷,将铸造组织转变为形变组织,其延续产品在深冲性能、表面质量和精度控制方面具有很大的优势[1, 4-5]。然而,铝合金热轧初始板坯初始厚度大(500~800 mm),轧制压下量无法渗透到心部,累积变形在厚度和侧边上形成了明显的双鼓形缺陷,轧制流程中切头尾工艺的粗放式控制形式,造成了板坯的巨大浪费,大大降低了成材率[6-8]。
对钢材热轧板坯的双鼓形缺陷形成机理和控制策略,国内外学者已开展了大量研究。王爱丽等[9]采用有限元ANSYS-DYNA分析了热轧板坯头尾鱼尾形状的演变规律,并通过短行程控制曲线模型改善了头尾形状。李学通等[10]采用刚塑性有限元法开展了热轧带钢鱼尾变形过程的基理研究,并建立了相应的短行程控制模型应用于实际生产。田野等[11]建立了热轧带钢头尾短行程控制的自学习策略。胡彬等[12]研究了中厚钢板轧制过程的平面形状控制。但是中厚钢板连铸坯最大厚度仅300 mm,而铝板坯厚度达500~800 mm,且铝合金变形抗力小、导热系数高,使其轧制过程存在着初始压下量小、立辊轧边量小、头尾易出现叠轧等独特现象[1, 6]。综上可知,铝合金轧制无法直接采用中厚钢板的研究成果,亟待开展铝合金热轧过程中头尾变形的定量化预测及减少切除量的研究。
本文作者以5052铝合金材料为对象,在精确研究头尾切除量预测模型的基础上,提出一种铝合金板坯粗轧头/尾部平面形状控制策略。利用刚塑性有限元方法对比分析了头/尾部普通平面、圆弧平面和梯形平面下多道次连续可逆轧制过程中的轧件头尾切除量演变规律,并给出最优头/尾平面形状控制方案,为进一步降低铝合金厚板粗轧可逆道次中头尾的切除量提供了新的可选方案。
1 铝合金厚板粗轧有限元建模
1.1 轧制压下规程及材料本构模型的建立
为保证模拟结果的准确性,轧制规程参考国内某厂的实际规程,工作辊直径为1000 mm,初始板坯厚度为530 mm,初始温度为480 ℃;粗轧可逆轧制规程如表1所列。材料的流变应力曲线和其相关的热物性参数对模拟结果影响重大,是准确分析头尾变形的必备条件。国内大量学者已在5系铝合金流变应力与其他热物性参数测试方面已做了深入研究,详见参考文献[13-16]。
表1 5052铝合金厚板轧制规程
Table 1 Rolling schedule of 5052 aluminum alloy plate
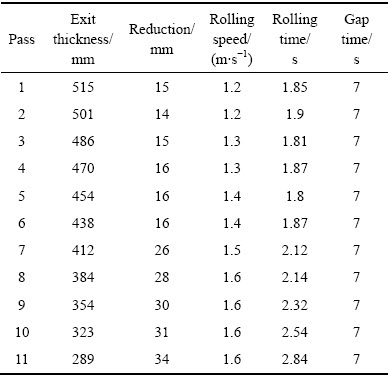
1.2 有限元建模及边界设置
鉴于铝合金热轧立辊轧制压下量小,立辊轧制对头尾变形的影响仅限于板坯两侧局部区域,本研究采用二维平面应变模型对轧制头尾变形过程进行定量分析。其建模效果如图1所示,轧辊为刚体,轧件为塑性体,参考轧制现场工况设置乳化液与轧件的接触换热等热力边界。定义鼓形最高点和最低点的距离为鼓形区深度L1,用以分析头尾切除量的变化。
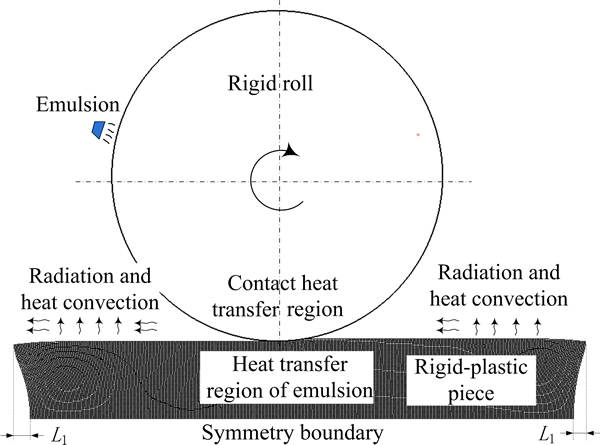
图1 铝合金轧制模拟模型
Fig. 1 Rolling simulation model for aluminum alloy
相关参数具体计算公式如下:轧件与轧辊的摩擦因数μ采用文献[13]中的公式进行计算:

(1)
式中:v为轧制速度,m/s;T为轧件表面温度,K。轧件与周围空气的换热边界采用混合对流换热,取值6.90 W/(m2·K);辐射率设定为0.8。乳化液冷却换热系数hy参照文献[16]计算公式,根据实际工况取值5837.6 W/(m2·K):
(2)
1.3 板坯头/尾部平面形状控制模型
参考现有实际生产的铣削铸锭断面[4],提出了一种新型铝合金厚板热轧平面形状控制模型。如图2所示,板坯头/尾平面形状分为圆弧和梯形两种方案,是基于普通矩形头/尾平面铣削加工而成。其中,圆弧平面参数为圆弧半径R与过度圆弧r,梯形平面参数为梯形高度B和梯形上底h。参考现有铣削铸锭断面尺寸,圆弧平面参数R=1050 mm,r=35 mm;梯形平面参数B=54 mm,h=155 mm。

图2 板坯头/尾部平面形状方案
Fig. 2 Head and end plane shape
2 普通粗轧头尾切除量的预测模型研究
2.1 轧件轧制过程的鼓形缺陷原因分析
图3所示为头/尾部普通平面板坯粗轧第5道次的等效应变云图和头部的X方向速度云图。由图3(a)可知,轧件表面等效应变为0.9,心部等效应变为0,轧制变形只能渗透到1/8~1/4的板坯深度,剧烈的表面形变引起了轧件头部X方向金属的明显不均匀流动;由图3(b)可知表层金属流动速度高出心部达6.7%。具体分析可知,中厚板轧制过程中板坯的头尾为自由端,变形不受约束,容易引起轧件的不均匀变形。同时,铝合金初始板坯厚度大,延展性好,轧制难以渗透到心部的表面变形,使板坯向自由端的金属流动更加剧烈,导致头尾出现了明显强于钢的鼓形特征。综合轧制工艺考虑,铝合金粗轧为可逆轧制,立辊的作用为轧边,侧边压下量小,不会引起“舌头”和“鱼尾”现象。鼓形缺陷引起的难以咬入和叠轧现象成为铝合金粗轧头尾切除的主要原因。
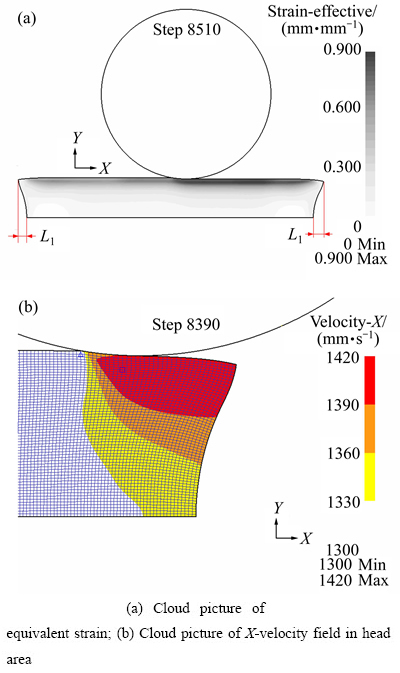
图3 轧制模拟结果
Fig. 3 Rolling simulation results
2.2 板坯厚度对头尾变形的影响
参照实际工况(见表1),分别取板坯厚度H为600、550、500、450和400 mm,压下量20 mm,进行模拟分析。分别提取各模型的鼓形轮廓和对厚度进行归一化处理,其头部变形结果和鼓形深度L1与板坯厚度的关系如图4(a)和图4(c)的N1曲线所示。由图4(a)可知,随着轧件厚度的增大,轧件的头部变形逐渐增大,在相对厚度0.46~0.48区域时发生突变,其外部区域轧件变形量呈现线性分布;其内部区域的心部鼓形呈现二次曲线分布。由曲线N1可知鼓形深度L1与板坯厚度呈线性关系,拟合求得的相对变形结果如下:
(3)
式中:L1为鼓形区深度,mm;H为板坯厚度,mm。
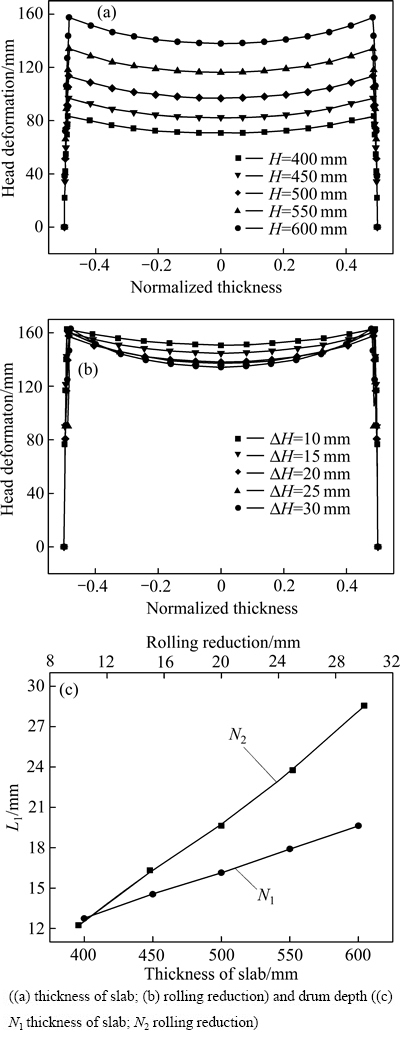
图4 轧制参数对头部变形的影响及与鼓形深度的关系曲线
Fig. 4 Influence of rolling parameter to end face deformation
2.3 道次压下量对头尾变形的影响
同上,分别选择单道次压下量ΔH为10、15、20、25和30 mm,板坯厚度600 mm,进行对比分析。其中,图4(b)所示为各轧件轧后头部变形结果,图4(c)所示为变形曲线N2为鼓形深度L1与道次压下量的关系。由图4(b)可知,不同压下量下的变形趋势与板坯厚度研究结果一致,且随着压下量的增大,轧件头部的心部变形逐渐增大,呈现线性分布趋势。由曲线N2可知鼓形深度与道次压下量的关系如下:
(4)
式中:L1为鼓形区深度,mm;ΔH为道次压下量,mm。
综合上述分析可知,鼓形深度L1受到板坯压下量和板坯厚度的综合影响,并呈现出单变量下的线性变化。如果忽略轧制各道次间的遗传特性,各道次鼓形区深度L1与板坯厚度H、单道次压下量ΔH的关系如式(5)所示。综合式(5)及轧制工艺表1即可预测各道次轧制后的头尾鼓形深度,进而确定各道次的切除量。
(5)
3 铝合金粗轧平面形状控制模型的连续可逆轧制模拟及预测模型研究
上述切除量预测公式可以提高铝合金厚板切头尾工序的精准度,但不能实质降低切除量。为进一步降低板坯头尾切除量,提出了板坯头/尾部平面形状控制方案,并采用表1的轧制工艺进行了可逆道次的连续轧制模拟,得出了平面形状对头尾切除量的影响规律及其切除量预测模型。
3.1 铝合金平面控制下的轧制模拟研究
图5所示为不同头/尾部平面形式下各道次的变形结果。由图5可知,梯形和圆弧平面板坯在第3~5道次时才出现略微的向后凹陷现象,在6~11道次中逐渐出现轻微双鼓形区域,且凹陷程度明显低于普通头/尾部平面,其11道次时鼓形深度减少18%~20%。对比可知,头/尾部平面控制方式能够抵消部分双鼓变形,降低头尾切除量。
其次,对比梯形平面板坯和圆弧平面板坯在11道次的变形效果知:此时的圆弧板坯心部变形区域仍为圆润过渡,而梯形板坯心部即将出现类似普通板坯11道次的尖角重叠形式。分析原因为梯形板坯上底区域在变形后期(7~11道次)近似于普通板坯轧制变形,大压下量引起心部的局部变形贴合。从防止出现叠轧角度分析,圆弧板坯略微优于梯形板坯。但综合考虑圆弧平面铣削工艺耗费量远大于梯形平面,且9~11道次时梯形平面和圆弧平面的双鼓变形深度几乎一致,总体结论为梯形平面板坯头/尾控制方式更适应于现有实际铝合金厚板热轧生产工艺。

图5 各头/尾部平面下不同道次的头部变形程度对比
Fig. 5 Head deformation comparison of each rolling passes under different head and end plane shape
3.2 平面形状控制下的鼓形深度预测模型研究
图6所示为普通平面和梯形/圆弧平面下各轧制道次的鼓形区深度L1的对比结果。由图6可知,梯形平面、圆弧平面的结果与普通平面趋势完全一致。分析可知不同平面形式下的鼓形区深度L1与轧制过程无关,只受初始板坯的影响。综合两种头/尾部平面形式引入端部深度值M(梯形平面为梯形高度B,圆弧平面为圆弧深度),则梯形平面的双鼓变形深度预测公式如下:

(6)
式中:L1为鼓形区深度,mm;H为板坯厚度值,mm;ΔH为单道次压下量,mm;M为梯形平面高度;0.67为深度值M的修正系数。
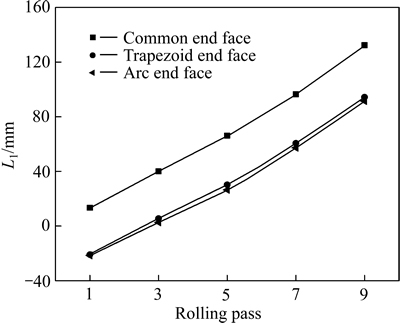
图6 各平面形状下变形量对比
Fig. 6 Deformation comparison on each plane shape
4 预测模型修正及工业现场对比
如图7所示,为保证预测模型的准确性,首先将单道次叠加的鼓形深度预测结果和连轧模拟结果进行了对比。由图7可知,预测结果与连轧模拟结果相近,最大误差值9.2%,且预测结果全部小于实际连轧模拟结果。分析原因为预测模型中未考虑轧制过程中道次的叠加效果。将预测模型加入修正系数K=1.1,修正公式与连轧预测结果完全一致,表明修正后的轧件头尾预测模型具有很好的实用性。后续的工业现场进一步验证了此结论。
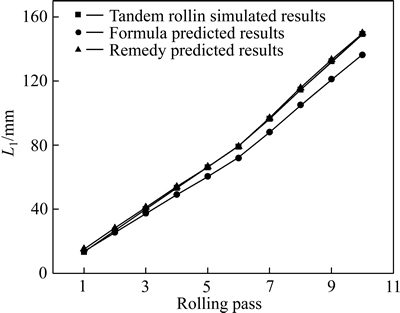
图7 变形量预测结果的对比与修正
Fig. 7 Comparison and correction of deformation prediction results
图8所示分别给出了普通头/尾部平面粗轧模拟第11道次和实际轧制现场同道次的头部变形结果。对比变形轮廓可知,现场双鼓变形与模拟预测结果在鼓形心部稍微差异,现场板坯心部出现了圆弧凹陷闭合区域(红色圆圈区域)。分析原因为实际轧制中铝合金表面氧化、温降等引起表面难以贴合。同时,对比分析轧制模拟的头尾鼓形深度预测结果(148.5 mm)与现场板坯测量结果(152 mm)相近,表明了预测模型的准确性。
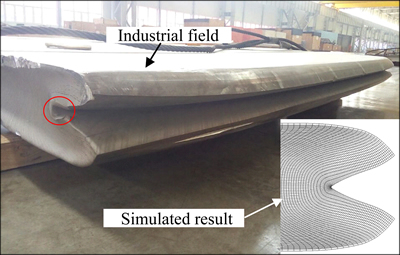
图8 工业现场结果验证
Fig. 8 Industrial on-site validation
5 结论
1) 定义铝合金厚板鼓形区深度L1,并分析了普通板坯的鼓形区深度与各道次板坯厚度H、压下量ΔH的关系,给出了普通板坯鼓形区深度L1的预测模型。
2) 在普通板坯研究基础上开展了头/尾部平面形状控制下轧制过程的头尾切除量演变规律和头尾切除量模型研究,给出了头/尾部平面下鼓形区深度L1的预测模型。但现有预测公式是基于本研究工况的结论,工况变化还需进行相应的系数修正。
3) 将普通头/尾部平面形状的头尾切除量预测模型与现场实际铝合金厚板轧制效果进行了对比验证,验证了有限元模型的正确性。
4) 结合头/尾部平面形状控制及铣削加工工艺综合分析,梯形头/尾部平面形状控制方案更加适合现有铝合金厚板热轧生产。
REFERENCES
[1] 张新明. 铝热连轧原理与技术[M]. 长沙: 中南大学出版社, 2010: 1-5.
ZHANG Xin-ming. Principle and technology on hot tandem rolling of aluminium and aluminium alloys[M]. Changsha: Central South University Press, 2010: 1-5.
[2] 刘 兵, 彭超群, 王日初, 王小锋, 李婷婷. 大飞机用铝合金的研究现状及展望[J]. 中国有色金属学报, 2010, 20(9): 1705-1707.
LIU Bing, PENG Chao-qun, WANG Ri-chu, WANG Xiao-feng, LI Ting-ting. Recent development and prospects for giant plane aluminium alloys[J]. The Chinese Journal of Nonferrous Metals, 2010, 20(9): 1705-1707.
[3] 李 翔, 唐建国, 张新明, 凌利月, 刘文辉, 廖志宇, 杨 涛, 邓运来. 温变形对汽车车身用6061铝合金自然时效及力学性能的影响[J]. 中国有色金属学报, 2016, 26(1): 1-2.
LI Xiang, TANG Jian-guo, ZHANG Xin-ming, LING Li-yue, LIU Wen-hui, LIAO Zhi-yu, YANG Tao, DENG Yun-lai. Effect of warm deformation on natural ageing and mechanical property of aluminium alloy 6061 sheets for automotive body[J]. The Chinese Journal of Nonferrous Metals, 2016, 26(1): 1-2.
[4] 赵世庆, 王华春, 郭金龙, 潘 祯. 铝合金热轧及热连轧技术[M]. 北京: 冶金工业出版社, 2010: 5-12.
ZHAO Shi-qing, WANG Hua-chun, GUO Jin-long, PAN Zhen. Hot rolling and hot tandem rolling technology of aluminium alloy[M]. Beijing: Metallurgical Industry Press, 2010: 5-12.
[5] 李多, 徐贺年, 王祝堂. 轧制及铸造铝厚板产业[J]. 轻合金加工工艺, 2015, 43(4): 11-13.
LI Duo, XU He-nian, WANG Zhu-tang. Casting and rolling industry of aluminium thick plates[J]. Light Alloy Fabrication Technology, 2015, 43(4): 11-13.
[6] 谢水生, 刘相华. 有色金属材料的控制加工[M]. 长沙: 中南大学出版社, 2013: 384-386.
XIE Shui-sheng, LIU Xiang-hua. Control processing for non-ferrous material[M]. Changsha: Central South University Press, 2013: 384-386.
[7] 张 林, 赵德文, 王根矶, 李春智. 特厚钢板轧制缺陷压合和双鼓形有限元分析[J]. 轧钢, 2011, 28(4): 1-3.
ZHANG Lin, ZHAO De-wen, WANG Gen-ji, LI Chun-zhi. Analysis of defects closing and double drum in ultra-heavy plate rolling by FEM[J]. Steel Rolling, 2011, 28(4): 1-3.
[8] 冯 迪, 张新明, 刘胜胆, 吴泽政, 郭奕文, 余翠娟. 7A55铝合金厚板的微观组织和性能不均匀性[J]. 中南大学学报(自然科学版), 2015, 46(8): 2824-2830.
FENG Di, ZHANG Xin-ming, LIU Sheng-dan, WU Ze-zheng, GUO Yi-wen, YU Cui-juan. Inhomogeneity of microstructure and properties of 7A55 aluminium alloy thick plate[J]. Journal of Central South University (Science and Technology), 2015, 46(8): 2824-2830.
[9] 王爱丽, 杨 荃, 刘华强; 杜晓钟. 热连轧带钢头尾鱼尾形状模拟控制研究与应用[J]. 塑性工程学报, 2009, 16(2): 101-103.
WANG Ai-li, YANG Quan, Liu Hua-qiang, DU Xiao-zhong. Analog control research and application of hot rolling strip head and tail shape[J]. Journal of Plasticity Engineering, 2009, 16(2): 101-103.
[10] 李学通, 杜凤山, 孙登月, 吴建峰. 热轧带钢头尾形状短行程控制研究[J]. 钢铁, 2005, 40(2): 51-53.
LI Xue-tong, DU Feng-shan, SUN Deng-yue, WU Jian-feng. Study of SSC for strip head and tail shape on hot strip mill[J]. Iron and Steel, 2005, 40(2): 51-53.
[11] 田 野, 胡贤磊, 刘相华. 热轧带钢头尾短行程控制自学习策略[J]. 钢铁研究学报, 2010, 22(4): 55-58.
TIAN Ye, HU Xian-lei, LIU Xiang-hua. Self-learning strategy of short stroke control for head and tail of hot strip[J]. Journal of Iron and Steel Research, 2010, 22(4): 55-58.
[12] 胡 彬. 中厚板轧制平面变形控制物理模拟[D]. 秦皇岛: 燕山大学, 2006: 33-40.
HU Bing. Physical simulation of plan view pattern control during plate rolling process[D]. Qinhuangdao: Yanshan University, 2006: 33-40.
[13] 何玉辉. 板带多道次热轧过程温度场数值模拟与温降模型研究[D]. 长沙: 中南大学, 2010: 63-68.
HE Yu-hui. Research on thermal field numerical simulation and temperature fall model of strip during multi-pass hot rolling process[D]. Changsha: Central South University, 2010: 63-68.
[14] 王卫卫. 5052铝板带热连轧全流程温度计算模型研究[D]. 长沙: 中南大学, 2012: 25-33.
WANG Wei-wei. The study on the temperature calculation model of 5052 A1 plate in hot continuous rolling[D]. Changsha: Central South University, 2012: 25-33.
[15] 陈 婕. 5052 铝合金热粗轧建模与轧制力预测研究[D]. 长沙: 湖南大学, 2009: 18-26.
Chen Jie. Study on modelling and rolling force prediction model for hot rough rolling of 5052 aluminium alloy[D]. Changsha: Hunan University, 2009: 18-26.
[16] 彭 建, 王永建, 钟丽萍, 孙 勇, 彭龙飞. 5052铝合金板材热轧过程塑性变形及应力分布的三维热力耦合模拟[J]. 材料热处理学报, 2015, 36(3): 209-212.
PENG Jian, WANG Yong-Jian, ZHONG Li-ping, SUN Yong, PENG Long-fei. Three dimensional thermal mechanical coupled simulation of plastic deformation and stress distribution during hot rolling of 5052 aluminium sheet[J]. Transactions of Materials and Heat Treatment. 2015, 36(3): 209-212.
Effects of head and end plane shape of slab on metal removal of head and tail in aluminum alloy plate rough rolling
YAN Meng1, HUANG Hua-gui1, ZHANG Cai-yun1, DU Feng-shan1, ZHANG Shang-bin2
(1. National Engineering Research Center for Equipment and Technology of Cold Strip Rolling, Yanshan University, Qinhuangdao 066004, China;
2. Heavy Machinery Research Institute, China National Erzhong Group Company, Chengdu 610052, China)
Abstract: In order to reduce the metal removal of head and tail and improve the hot rolled aluminum plate yield, taking 5052 aluminum alloy as an object, the effects of strip thickness and rolling reduction on metal removal of head and tail were simulated and the prediction model of head and tail was precisely established. Then the head and tail evolution rules were studied under the conditions of general plane shape, circular plane shape and trapezoidal plane shape of the slab head and end in the process of multi pass reversing rolling. The results show that the cropping is reduced by 18%-20% under the condition of circular and trapezoidal cross-section. In order to testify the correctness of finite element simulation results, the prediction model of head and tail under the condition of general plane shape is applied to the actual rolling schedule, and the prediction results are consistent with the in-site measurement data. Considering the milling process of ingot end face, the trapezoidal plane shape is more suitable for the hot rolling production of aluminum alloy thick plate at this stage.
Key words: aluminum alloy plate; metal removal of head and tail; head and end plane shape; rigid-plastic finite element method
Foundation item: Project(U1560206) supported by the State Key Program of National Natural Science Foundation of China; Project(51474189) supported by the General Programs of National Natural Science Foundation of China
Received date: 2016-05-03; Accepted date: 2016-08-05
Corresponding author: HUANG Hua-gui; Tel: +86-335-8077352; E-mail: hhg@ysu.edu.cn
(编辑 何学锋)
基金项目:国家自然科学基金重点资助项目(U1560206);国家自然科学基金面上项目(51474189)
收稿日期:2016-05-03;修订日期:2016-08-05
通信作者:黄华贵,教授,博士;电话:0335-8077352;E-mail: hhg@ysu.edu.cn