文章编号:1004-0609(2012)04-0991-09
镁合金板材的固体颗粒介质拉深工艺参数
赵长财1,曹秒艳1,肖 宏1,董国疆2,郝海滨1
(1. 燕山大学 机械工程学院,秦皇岛 066004;
2. 燕山大学 车辆与能源学院,秦皇岛 066004)
摘 要:提出基于固体颗粒介质成形(SGMF)工艺的镁合金板材差温拉深工艺,并展开试验研究。通过对AZ31B镁合金薄板进行差温拉深成形试验,研究了成形温度、拉深速度、压边力、压边间隙、凹模圆角和润滑条件对拉深性能的影响,确定AZ31B镁合金板料最佳成形工艺参数。结果表明:该工艺可显著提高镁合金板材的成形性能,成形温度及拉深速度对板料拉深性能影响较大,板料最佳成形温度区间为290~310 ℃,颗粒介质与板料理想温差为110~150 ℃;压边力和压边间隙对拉深性能产生联合影响;此外,凹模圆角和润滑条件也对拉深性能有一定的影响。当上述工艺参数达到最佳值时成功拉深出极限拉深比(LDR)为2.41的工件。
关键词:AZ31B镁合金;固体颗粒介质成形;差温;拉深性能
中图分类号:TG146.2 文献标志码:A
Solid granular medium drawing process parameters of magnesium alloy sheet
ZHAO Chang-cai1, CAO Miao-yan1, XIAO Hong1, DONG Guo-jiang2, HAO Hai-bin1
(1. College of Mechanical Engineering, Yanshan University, Qinhuangdao 066004, China;
2. College of Vehicles and Energy, Yanshan University, Qinhuangdao 066004, China)
Abstract: The non-isothermal drawing of the magnesium alloy sheet in solid granular medium forming (SGMF) technology was put forward. The non-isothermal drawing experiment of the AZ31B magnesium alloy sheet was conducted, through which, the impacts of the forming temperature, the drawing speed, the blank holder force and the blank holder gap as well as the female die fillet and lubrication condition on the drawing performance were studied, then the optimal process parameters were determined for AZ31B magnesium alloy sheet. The results show that this process is beneficial to significantly enhance the formability of the magnesium alloy sheet, the forming temperature and the drawing speed have great impact on the drawing performance of the sheet metal, whose optimal forming temperature is 290-310 ℃, and the ideal temperature difference between the granular medium and the sheet metal is supposed to be 110-150 ℃. The blank holder force and the blank holder gap combine to make effects on the drawing performance. Besides, the female die fillet and lubrication condition also have certain impact on the drawing performance. The workpiece with limit drawing ratio (LDR) of 2.41 is successfully obtained when the previous parameters achieve the corresponding optimal values.
Key words: AZ31B magnesium alloy; solid granules medium forming; non-isothermal; drawing performance
镁合金密度较低,是实际应用中最轻的金属结构材料,具有比强度和比刚度高、电磁屏蔽效果好、抗震减震能力强、易于加工成形和易于回收再利用等优点,在航空、航天、汽车、3G产品以及军工等领域具有广泛的应用前景和巨大的应用潜力[1-3]。目前,大部分镁合金零件都是通过压铸工艺生产,但由于压铸件的组织不够致密并存在一些微观空洞,因而在使用性能方面难以满足承力构件的强度要求。而与铸造镁合金相比,变形镁合金具有较高的强度、较好的塑性和更多样化的规格,因而在许多方面具有一定的竞争力。由于镁合金的结构为密排六方,在常温下变形时,只有基面滑移系参与,从而限制了其塑性变形能力。但在较高温度(≥200 ℃)时,镁合金可以通过动态再结晶(DRX)来改善其塑性变形性能[4-5],并在适当工艺条件下,变形镁合金板材具有良好的拉深成形性能,因此,镁合金板材拉深一般都在热态下进行。近年来,关于镁合金热拉深成形方面有很多学者进行了有益探索。YOSHIHARA等[6]通过对板材按温度划分3个区域设定相应的材料参数的方法,对温热拉延成形过程进行数值模拟,在此基础上进行了极限拉深比(LDR)试验,试验结果表明,采用合适的压边力和局部加热、冷却技术可以将镁合金板材的极限拉深比从2.1提高到5.0。张凯峰等[7]通过试验研究了镁合金温热拉延性能。苌群峰等[8]采用热力耦合技术对镁合金板材温热冲压过程中的温度场进行了数值模拟,研究冲压过程中温度场的分布规律,并对差温拉延工艺进行分析,其研究结果表明:差温拉延工艺可以提高镁合金板材的温热成形性能。目前也有一些学者采用橡胶、液体、气体等弹性材料来代替刚性凸模或凹模的软模成形工艺对铝镁合金板材进行拉深研究。刘晓晶等[9]对铝镁合金平底筒形件进行了双路径加载充液拉深成形模拟研究,模拟发现采用合理的液室加载曲线可以有效提高铝镁合金筒形件的成型极限。上述工艺的出现促进了板料成形技术的发展,但亦存在着模具复杂、对设备要求高、密封困难、难于热成形等不足。为适应板料成形的新发展,提出了既能克服刚性模成形和软模成形的缺点,又吸取了各自优点的新的成形工艺——固体颗粒介质成形(Solid granules medium forming, SGMF)工艺。
SGMF工艺是采用固体颗粒代替刚性凸模(或弹性体、液体)的作用对板管料进行软模成形的工艺,该工艺由赵长财首次提出并成功应用于板管材成形,取得了阶段性成果[10-11]。本研究工艺与其它软模成形工艺相比,具有制模简单、操作简便、低碳环保的优点,还可以大大提高板料的成形性能及产品尺寸精度;并克服充液成形工艺密封困难及难以适合在高温下工作的缺点。
由于镁合金独特的密排六方晶体结构,冲压成形工艺条件复杂,所以镁合金薄板成形技术是薄板塑性成形领域的一个研究难题。为此,本文作者首次提出将SGMF工艺应用于镁合金板料热成形,为镁合金板料的加工制备提供了新的方法和手段,对提高镁合金板料成形性能具有重要意义。
本文作者以AZ31B变形镁合金为例,使用固体颗粒介质成形工艺对AZ31B镁合金薄板进行差温拉深成形,研究了成形温度、拉深速度、压边力和压边间隙、凹模圆角、润滑条件等对拉深性能的影响。
1 实验
1.1 实验材料
实验材料选用AZ31B镁合金板材,板料厚度分别为0.6、1.0和1.1 mm,其成分如表1所列。镁合金板料毛坯直径为150~180 mm。
表1 AZ31B镁合金成分分析结果
Table 1 Component analysis results of AZ31B magnesium alloy (mass fraction, %)

1.2 试验装置及过程
为了研究各工艺参数对AZ31镁合金差温拉深性能的影响,在20~350 ℃的温度范围内,采用固体颗粒介质成形工艺对AZ31B镁合金薄板进行差温拉深试验。试验在3 150 kN液压机上进行,试验装置如图1所示。凹模直径为d 80 mm,冲头直径为d 70 mm,冲头底部为带有一定锥度的平面,加强颗粒介质的传力效果;在板料和冲头之间填充固体颗粒介质,实现软凸模拉深成形;试验中采用弹性压边,压边力可有压力传感器测出;试验中的压边间隙通过放置于凹模与压边圈之间的调整垫片来调整。
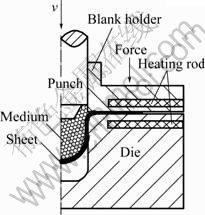
图1 AZ31B镁合金差温拉深试验装置
Fig. 1 Non-isothermal drawing test device of AZ31B magnesium alloy
通常情况下,镁合金的加热方式有外部加热法和内部加热法两种方式。本研究采用内部加热法,即在压边圈和凹模内分别均布多根电热棒进行加热。测温装置为便携式数字测温计,传感器采用E型热电偶,对压边圈及凹模表面温度进行精确测量。
试验过程中,先将润滑剂均匀涂抹于加工坯料的上下表面(中心留有直径d 60 mm左右的空白圆不涂抹润滑剂),再将板料放置于凹模之上,并用压边圈压紧,通过压力传感器测出压边力并对压边力大小进行调节。然后在料筒内倒入适量颗粒介质,以避免加热过程中加工坯料氧化。将压边圈及凹模加热至所需温度后倒入定量室温颗粒介质并放入冲头,然后保温5 min,以保证板料接触的颗粒介质、板料以及凹模的温度场均匀,颗粒介质温度由红外线测温仪测得。
试验中选取0.5、1和2 mm/s 3种不同的拉深速度,以考察不同拉深速度对拉深工艺的影响。试验还通过采用不同润滑剂及改变凹模圆角大小,研究不同凹模圆角和润滑条件对拉深性能影响。工件底部形状为球形底和平底。
2 结果与分析
2.1 成形温度对拉深成形性能的影响
将固体颗粒介质成形工艺应用于镁合金热拉深最大的优点在于,可以通过调节颗粒介质温度来实现被加工板料的差温控制。试验中发现,当坯料无温差拉深时,容易出现底部中心位置拉裂现象。从破裂部位可以很明显看出,工件出现桔皮现象,这主要是由于中心部位温度过高,抗拉强度降低,不能提供足够承载力将法兰继续拉深。
鉴于上述现象,采用差温成形工艺,使板料中心局部温度低于法兰部位温度,从而提高其承载力,试验发现,二者温差在110~150 ℃较为理想。颗粒介质总量除了对板料形成局部温差有影响外,在加工球形底工件时对成形高度和底部形状有较大影响。通过对加工过程中添加不同体积介质所成形的球形底工件进行对比(工件1与工件2颗粒介质加料总量分别为200 mL和320 mL),板料直径为160 mm,板厚1 mm,压边圈与凹模温度分别为310 ℃和290 ℃。结果发现,工件2底部为扁球,而工件1底部更趋向于球形且成形高度较高,法兰边较工件2更宽,这说明颗粒总量减少,使得冲头在板料中心部位所传递的压力衰减较少,局部应力较大,故顶部拉胀效果更为显著;相反地,随着颗粒高度的增加,颗粒介质对冲头所传递的压力衰减效果加强,板料与颗粒接触部位的应力相对均匀,因此工件底部形状为扁球。
由AZ31B镁合金在不同温度下的单向拉伸特 征[12]可知,随着温度的升高,由于镁合金的非基滑移系被激活,塑性变形能力显著增强,拉深性能明显提高;但与此同时,AZ31B镁合金的抗拉强度却随着温度的升高明显降低。若板料温度过高则将导致凹模入口板料的抗拉强度严重下降,就会降低镁合金的拉深性能。因此,应存在一最佳成形温度范围,AZ31B镁合金板材在此温度下具有良好的拉深性能。为了找出最佳成形温度范围,在150~350 ℃的范围内,拉深速度为1 mm/s时,得到1 mm板厚在不同温度下的极限拉深比LDR曲线(见图2(a))。由图2(a)可见,最佳成形温度为290~310 ℃,在300 ℃时,LDR达到最大值2.4。同时,测定直径为180 mm,板厚1 mm的板料在不同温度下拉深成形工件的高径比(h/d)曲线(见图2(b)),其成形工件实物如图2(c)所示,成形温度为300 ℃时,工件的成形高度达到101.6 mm。由以上试验结果可以看出,一方面,随着成形温度的升高,镁合金的塑性能力增强,拉深性能会得到一定的改善。另一方面,随着温度的上升,板料的屈服应力降低而且应变硬化能力明显减弱,这使得板料的屈强比(屈服强度与抗拉强度的比值,σs/σb)和均匀变形能力下降,极易使危险截面处金属发生局部流动,从而使拉深极限降低。因此,成形温度对成形极限的影响取决于以上两方面相互作用的结果。温度对镁合金变形能力施加影响的原因也能通过观察热拉伸实验后的试样断口形貌来得到解释。将AZ31B镁合金板料试样在Gleeble-3500热模拟实验机上以相同应变速率(1.0×10-3 s-1)不同温度下进行热拉伸试验后,进而运用KYKY-2800型扫描电子显微镜对拉伸试样的断口进行扫描,得到温度分别为100、200、300、350 ℃时的形貌,如图3所示。
由图3中可以看出,在变形温度100 ℃(图3(a))时,出现少量较浅的韧窝;当温度升至200 ℃(图3(b))时,出现等轴韧窝数量和深度明显增加,表现出典型韧窝聚合型延性断裂的特征,此时的断裂是由于位错运动在晶界处塞积造成应力集中的结果;当温度为300 ℃(图3(c))时,韧窝边缘出现明显的细小晶粒,说明开始出现沿晶断裂;温度达到350 ℃时,沿晶断裂现象更加明显,且晶界滑移引起的晶间微小空洞连接成较大的空洞而导致断裂的发生。由此可见,镁合金在温度较低时的变形主要受位错运动控制,当温度升高至300 ℃时,原子扩散能力增强,受扩散控制的晶界滑移逐渐取代了位错运动,使镁合金塑性明显改善,表现出良好的拉深性能[13]。
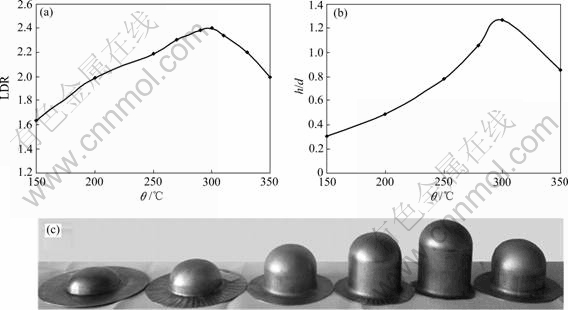
图2 不同温度下镁合金差温拉深LDR曲线、成形工件高径比和成形工件图
Fig. 2 LDR curve(a), ratio of height to diameter of work-pieces(b) and work-pieces(c) in non-isothermal drawing experiment of magnesium alloy at different temperatures
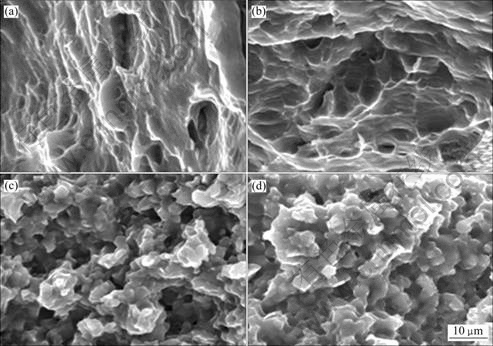
图3 应变速率1.0×10-3 s-1时不同温度下工件断口形貌
Fig. 3 Fracture morphologies of work-pieces at strain rate of 1.0×10-3 s-1 and different temperatures: (a) 100 ℃; (b) 200 ℃; (c) 300 ℃; (d) 350 ℃
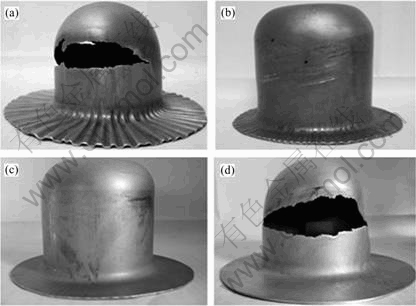
图4 不同压边力下AZ31B镁合金拉深成形工件
Fig. 4 AZ31B drawing work-pieces under different blank holder forces: (a) 5.6 kN; (b) 8.4 kN; (c) 11.3 kN; (d) 15 kN
2.2 压边力对拉深性能的影响
压边力控制对于镁合金板材的拉深成形性能具有重要影响[14-15]。压边力太大使坯料法兰处所受摩擦力增加从而导致危险断面的拉应力变大,致使坯料拉裂或者底部变薄严重;压边力太小则法兰起皱严重。为研究压边力对镁合金板料拉深性能的影响,以直径为d 175 mm,厚度1 mm的镁合金板料为研究对象,在间隙为1.3 mm、成形温度为300 ℃的条件下,压边力分别设为5.6、8.4、11.3、15 kN,得到的成形工件分别如图4(a)~(d)所示。压边力偏小时工件法兰起皱严重(图4(a)),阻碍法兰处板料继续向直筒部流动,造成工件底部和直壁过渡部分壁厚减薄严重、最终破裂;图4(b)中压边力较图4(a)中的有所增加,工件顺利成形,法兰处略微起皱;图4(c)中所示法兰平整,看不出明显褶皱现象,表面光滑,成形质量较好;图4(d)中压边力过大,工件法兰处平整,无任何起皱现象,但由于太大压应力造成法兰处所受摩擦力较大,从而导致拉应力急剧增大,工件在危险截面处壁厚减薄,最后被拉裂。
压边力的大小可根据下式进行计算[16]:
(1)
式中:Fp为压边力;D为毛坯外径;d为拉深件直径;rd为凹模圆角半径;p为单位压边力。
p由福开-吉田经验公式计算
(2)
式中:σs为屈服极限;σb为抗拉强度;R0为毛坯半径;r2为拉深圆筒半径;t为板厚。
将式(1)和(2)代入具体数值见表2,最后得到Fp=12.4 kN,该计算值比实验值11.3 kN稍大,这主要是由于在拉深过程中,冲头与压边圈之间的摩擦力F充当了压边力的功能,对压边力起到加强作用,故作用于板料上的压边力实际应为外部施加压边力与摩擦力F之和。
表2 拉深工件实际参数
Table 2 Actual parameters of deep drawing workpiece
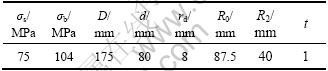
2.3 压边间隙和压边力联合控制对拉深性能的影响
在本研究中,压边间隙和压边力联合控制对板料成形施加影响,在拉深初期,由于变形小,板料法兰部位增厚不明显,此时由于压边间隙的存在,施加的压边力大部分由调整垫片承受,作用于板料上的压边力非常小,故压边圈和凹模对板料摩擦阻力也小,板料能够顺利继续拉深变形,此时由压边间隙起主要作用保证板料进一步拉深。由冲压原理可知,当拉深工件法兰外径Dw减至0.85倍左右坯料直径D时,板料处于拉深变形的一个关键阶段,此时拉深力将出现峰值,若板料法兰边缘部位失稳起皱而使整体板厚大于压边间隙时,就需要依靠压边力来控制板料法兰部位的过度起皱变形。由此可见,在整个板料拉深过程中,压边间隙和压边力分别在前后两个阶段起主导作用。但是,压边间隙太小时,间隙将失去意义,仅有压边力起作用;相反地,间隙过大时,板料起皱严重,压边力不能起到应有的作用。因此,这两个因素的组合存在一个最佳范围需要通过试验来确定。为测定二者的最佳值,以板厚为1 mm、直径为175 mm的板料为研究对象,在300 ℃温度下,分别测试压边间隙为1.1、1.2、1.3、1.4、1.5 mm,压边力为5.6、8.4、11.3、15 kN共计20种工况的板料拉深性能。结果发现,间隙为1.1 mm时,压边力不论大小,工件法兰处平整光滑,在拉深开始不久即被拉裂,见图5(a),这是由于在拉深过程中,法兰厚度会增加,间隙变小,摩擦力增加,阻碍板料向凹模内进一步流动;压边间隙为1.2 mm时,法兰质量较好,压边力为5.6 kN时可以成形,但极限成形高度只有68.3 mm(见图5(b)),压边力大于5.6 kN时,工件拉裂(见图5(c))。间隙为1.3 mm、压边力为11.3 kN时,成形性能及成形质量最好,如图5(d)所示;间隙为1.4~1.5 mm时,即便调大压边力也避免不了法兰处的起皱,部分工件可以成形(见图5(e)),但多数工件极易被拉裂(见图5(f))。因此,合理压边间隙为板厚的1.2~1.3倍。
2.4 拉深速度对拉深成形性能的影响
为确定拉深速度对AZ31B镁合金差温拉深工艺的影响,在板料温度为300 ℃,压边间隙1.3 mm,压边力为11.3 kN时,分别采用3种恒定的拉深速度0.5、1和2 mm/s对直径为175 mm的AZ31镁合金坯料进行了拉深试验。实验结果表明,以2 mm/s的速度拉深时,板料很快便在底部、直筒与底部过渡区发生断裂,见图6(a)和图6(b);在1 mm/s的速度时可成功拉深LDR为2.4的工件,见图6(c);而以较低的速度如 (0.5 mm/s)速度拉深时,坯料能完全成形,见图6(d)和图6(e)。
通过试验获得的镁合金板料不同拉深速度下的拉深力-冲头行程曲线可知,拉深速度从0.5 mm/s增加至1 mm/s,拉深力的增加不大;当拉深速度增至2 mm/s时,拉深力迅速增大,致使板料直壁或者底部被拉断。这是因为一方面随着变形速度的增加,镁合金的流动应力随之增大,而材料的断裂抗力受变形速度的影响很小,这使得板料较早到达断裂阶段[17];另一方面,在加热条件下拉深成形,增加变形速度将使镁合金没有足够的时间进行回复,造成镁合金软化不充分因而塑性明显下降。拉深速度对成形性能影响的原因也可通过观察不同应变速率下的拉伸试样组织变化来揭示。图7所示为300 ℃下不同应变速率下的试样断口显微组织。从图7中可以看出,应变速率较低时,在晶界处产生了大量的细小再结晶颗粒;而速率较大时,动态再结晶来不及充分进行即被破坏,晶界周围主要是晶界滑移和破碎的细晶组织。动态再结晶进行的越不充分,变形中的应力集中越难以松弛,大大降低了材料的变形协调能力,从而会使伸长率降低。这是因为动态再结晶是通过晶界扩散控制的晶界迁移进行的,是一个速率控制的过程,提高应变速率抑制了扩散过程的进行,从而限制了动态再结晶的发展。
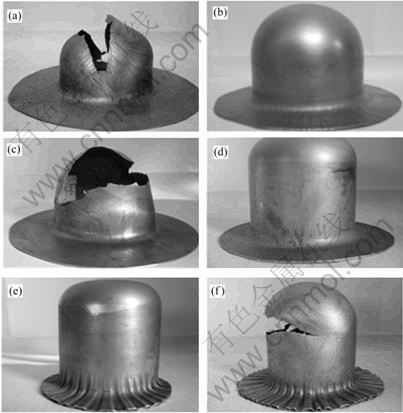
图5 不同间隙下AZ31B镁合金拉深成形工件
Fig. 5 AZ31B drawing work-pieces under different blank holder gaps: (a) 1.1 mm; (b) 1.2 mm, 5.6 kN; (c) 1.2 mm, >5.6 kN; (d) 1.3 mm, 11.3 kN; (e), (f) 1.4~1.5 mm
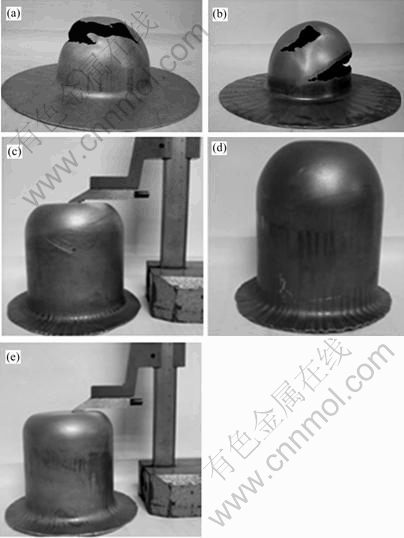
图6 不同拉深速度AZ31B镁合金拉深成形工件
Fig. 6 AZ31B drawing work- pieces under different drawing speeds: (a), (b) 2 mm; (c), (d) 1 mm; (e) 0.5 mm
上述试验结果表明,镁合金板材与铝合金和钢板等非密排六方晶格金属相比,其差温拉深成形对变形速度有很大的敏感性,因此,镁合金的差温拉深成形宜在工作速度较低的液压机上进行。
2.5 凹模圆角半径对拉深成形性能的影响
试验测试了厚度0.6 mm和1 mm的AZ31B镁合金板材在凹模圆角半径分别为2、3.5、5、6.5、8 mm的条件下极限成形高度曲线(见图8)。随着凹模圆角半径的增大,不同板厚的板料拉深高度均有所增加,且1 mm厚度的板材增加的趋势更为明显。
2.6 润滑条件对拉深成形性能的影响
为选择合适的润滑剂,在300 ℃成形温度下,采用厚度1 mm的AZ31B镁合金板料在无润滑、肥皂润滑、油基石墨润滑、水基石墨润滑和水基二硫化钼润滑的条件下分别进行拉深试验,研究润滑条件对拉深成形性能的影响。试验结果表明,无润滑剂的条件下,工件很快被拉裂;用肥皂润滑时,工件易被拉裂,但成形直壁高度较前者高,同时工件表面结有胶状物清洗比较困难;油基石墨润滑剂是由机油和石墨粉按照一定比例配置而成,该润滑剂可以在一定程度上提高拉深高度,但是加工过程中由于加热温度较高,出现较浓烟雾,并有刺激气味,作业环境较差,同时机油经高温后结成胶状物附着在工件表面,从而加大了法兰处的摩擦力,对工件拉深成形不利,同时工件清洗困难;水基石墨避免了油基石墨润滑剂出现烟雾和刺激气味的问题,水在高温下蒸发,剩下石墨粉末进行润滑,能有效提高了拉深高度,但是石墨清洗困难,并且对镁合金有腐蚀作用,一段时间后残留的石墨会在工件表面留下黑色腐蚀印迹;相对而言,水基二硫化钼是较为理想的润滑剂,克服了前述几种润滑剂的缺点,加工完毕后润滑剂会在工件表面形成光亮的二硫化钼粉末薄层,非常容易清洗,最终可以得到极限拉伸比为2.4的工件。因此,水基二硫化钼可以作为镁合金板材温热拉深成形的一种较理想的润滑剂。
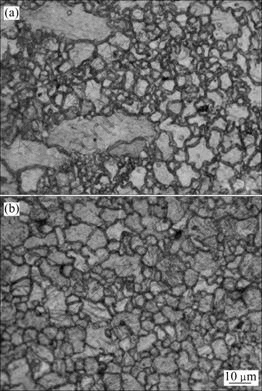
图7 不同应变速率下的AZ31B断口组织形貌(横向拉伸)
Fig. 7 Fracture morphologies of AZ31B magnesium alloy under different strain rates (lateral tension): (a) 10-1 s-1; (b) 10-3 s-1
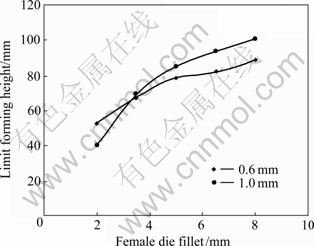
图8 不同凹模圆角半径下极限成形高度曲线
Fig. 8 Limit forming height curves under different female die radii
2.7 板厚对极限拉深比的影响
在最佳成形条件下,分别对厚度0.6、1和1.1 mm的AZ31B镁合金板材进行拉深试验,得到其极限拉深比LDR分别为2.12、2.4和2.41。可见,对于AZ31B镁合金薄板而言,随着板厚增加,极限拉深比LDR也能增加。
3 结论
1) 提出基于固体颗粒介质成形工艺的AZ31B镁合金板差温拉深工艺,该工艺可显著提高镁合金板的拉深性能。
2) 镁合金的差温拉深极限拉深比并非随板料温度单调增加而是在300 ℃左右达到最大值,温度继续升高,极限拉深比反而下降。
3) 压边间隙和压边力联合影响镁合金板的拉深性能。
4) AZ31B镁合金差温拉深工艺对变形速度有显著的敏感性,因此,拉深过程应在工作速度较慢的液压机上进行,并需严格控制拉深速度。
5) 适当增加凹模圆角可以提高拉深性能。
6) 在镁合金的差温拉深工艺中,选用合适的润滑剂是保证拉深成功的重要环节。
REFERENCES
[1] 余 琨, 黎文献, 王日初, 马正青. 变形镁合金的研究、开发及应用[J]. 中国有色金属学报, 2003, 13(2): 277-288.
YU Kun, LI Wen-xian, WANG Ri-chu, MA Zheng-qing. Research, development and application of wrought magnesium alloys[J]. The Chinese Journal of Nonferrous Metals, 2003, 13(2): 277-288.
[2] Slooff F A, ZHOU J, Duszczyk J, Katgerman L. Constitutive analysis of wrought magnesium alloy Mg-A14-Zn1[J]. Seripta Materialia, 2007, 57(8): 759-762.
[3] 陈振华, 刘俊伟, 陈 鼎, 严红革. 镁合金超塑性的变形机理、研究现状及发展趋势[J]. 中国有色金属学报, 2008, 18(2): 193-202.
CHEN Zhen-hua, LIU Jun-wei, CHEN Ding, YAN Hong-ge. Deformation mechanisms, current status and development direction of superplastic magnesium alloys[J]. The Chinese Journal of Nonferrous Metals, 2008, 18(2): 193-202.
[4] SPIGARELLI S, MEHTEDI M E, CABIBBO M, EVANGELISTA E, KANEKO J, J?GER A, GARTNEROVA V. Analysis of high-temperature deformation and microstructure of an AZ31 Magnesium alloy[J]. Mater Sci Eng A, 2007, 462(1/2): 197-201.
[5] VARZANEH S M F, HANZAKI A Z, BELADI H. Dynamic recrystallization in AZ31 magnesium alloy[J]. Mater Sci Eng A, 2007, 456(1/2): 52-57.
[6] Yoshihara S, Nishimura H, Yamamoto H, Manabe K. Formability enhancement in magnesium alloy stamping using a local heating and cooling technique: circular cup deep drawing process[J]. Journal of Materials Processing Technology, 2003, 142: 609-613.
[7] 张凯锋, 尹德良, 吴德忠, 蒋少松. AZ31镁合金板的热拉深性能[J]. 中国有色金属学报, 2003, 13(6): 1505-1509.
ZHANG Kai-feng, YIN De-liang, WU De-zhong, JIANG Shao-song. Deep drawability of AZ31 magnesium alloy sheets at elevated temperatures[J]. The Chinese Journal of Nonferrous Metals, 2003, 13(6): 1505-1509.
[8] 苌群峰, 李大永, 彭颖红, 曾小勤. 镁合金板材温热冲压成形热力耦合数值模拟[J]. 中国有色金属学报, 2007, 41(10): 1582-1585.
CHANG Qun-feng, LI Da-yong, PENG Ying-hong, ZENG Xiao-qi. Numerical simulation of warm stamping of magnesium alloy sheet based on thermo-mechanical coupled method[J]. The Chinese Journal of Nonferrous Metals, 2007, 41(10): 1582-1585.
[9] 刘晓晶, 闫 巍, 郭立伟. 铝镁合金双路径加载充液拉深成形的数值模拟[J]. 中国有色金属学报, 2008, 18(4): 698-702.
LIU Xiao-jin, YAN Wei, GUO Li-wei. Numerical simulation of aluminum-magnesium alloy cup’s forming by hydrodynamic deep drawing with double loading paths[J]. The Chinese Journal of Nonferrous Metals, 2008, 18(4): 698-702.
[10] 赵长财, 李晓丹, 董国疆, 王银思. 板料固体颗粒介质成形新工艺及其数值模拟[J]. 机械工程学报, 2009, 45(6): 211-215.
ZHAO Chang-cai, LI Xiao-dan, DONG Guo-jiang, WANG Yin-si. Solid granules medium forming technology and its numerical simulation[J]. Journal of Mechanical Engineering, 2009, 45(6): 211-215.
[11] 董国疆, 赵长财, 曹秒艳, 郝海滨. 管板材SGMF工艺传压介质的物理性能试验[J]. 塑性工程学报, 2010, 17(4): 71-75.
DONG Guo-jiang, ZHAO Chang-cai, CAO Miao-yan, HAO Hai-bin. Experimental research on physical properties of pressure-transfer medium in SGMF of plates and pipe[J]. Journal of Plasticity Engineering, 2010, 17(4): 71-75.
[12] 胡丽娟, 彭颖红, 唐伟琴, 李大永, 张少睿. AZ31镁合金薄板动态再结晶对其拉伸性能的影响[J]. 中国有色金属学报, 2008, 18(9): 1571-1576.
HU Li-juan, PENG Ying-hong, TANG Wei-qin, LI Da-yong, ZHANG Shao-rui. Effect of dynamic recrystallization on tensile properties of AZ31 magnesium alloy sheet[J]. The Chinese Journal of Nonferrous Metals, 2008, 18(9): 1571-1576.
[13] 刘满平, 马春江, 王渠东, 吴国华, 朱燕萍, 丁文江. 工业态AZ31镁合金的超塑性变形行为[J]. 中国有色金属学报, 2002, 12(4): 797-801.
LIU Man-ping, MA Chun-jiang, WANG Qu-dong, WU Guo-hua, ZHU Yan-ping, DING Wen-jiang. Superplastic deformation behavior of commercial magnesium alloy AZ31[J]. The Chinese Journal of Nonferrous Metals, 2002, 12(4): 797-801.
[14] chang Qun-feng, LI Da-yong, peng Ying-hong, zeng Xiao-qin. Experimental and numerical study of warm deep drawing of AZ31 magnesium alloy sheet[J]. International Journal of Machine Tools & Manufacture, 2007, 47: 436-443.
[15] Yoshihara S, Manabea K, Nishimura H. Effect of blank holder force control in deep-drawing process of magnesium alloy sheet[J]. Journal of Materials Processing Technology, 2005(1): 7-15.
[16] 肖景容, 姜奎华. 冲压工艺学[M]. 北京: 机械工业出版社, 1999: 72-126.
XIAO Jing-rong, JIANG Kui-hua. Stamping technology[M]. Beijing:China Machine Press, 1999: 72-126.
[17] 于彦东, 李彩霞. 镁合金AZ31B板材热拉深成形工艺参数优化[J]. 中国有色金属学报, 2006, 16(5): 786-792.
YU Yan-dong, LI Cai-xia. Optimization of processing parameters for magnesium alloy AZ31B sheets in thermal deep-drawing process[J]. The Chinese Journal of Nonferrous Metals, 2006, 16(5): 786-792.
(编辑 李艳红)
基金项目:国家自然科学基金资助项目(50775197)
收稿日期:2011-06-02;修订日期:2011-11-28
通信作者:赵长财,教授,博士;电话:0335-8057270;E-mail: jacmy@ysu.edu.cn