Trans. Nonferrous Met. Soc. China 22(2012) s735-s739
Growth of BaTiO3-Ag hybrid composite films at room temperature by aerosol deposition
Young Joon YOON1, Sung Hwan CHO1, Jihoon KIM2, Hyo Tae KIM1, Hong Koo BAIK3, Jong-Hee KIM1
1. Nano-Convergence Intelligence Material Team, Korea Institute of Ceramic Engineering and Technology, 233-5 Gasan-dong, Guemcheon-gu, Seoul 153-801, Korea;
2. Division of Advanced Materials Engineering, Kongju National University, Cheonan, Chungchurgnam-do 331-717, Korea;
3. Department of Materials Science and Engineering, Yonsei University, 134 Shinchon-dong, Seodamun-gu, Seoul 120-749, Korea
Received 21 May 2012; accepted 28 September 2012
Abstract: Barium titanate (BaTiO3) and silver (Ag) composite film with high dielectric constant was grown at room temperature by an aerosol deposition method. The dielectric constant increases by 0.5 times after adding Ag to the BaTiO3 matrix, compared with pure BaTiO3. The high dielectric constant can be attributed to the percolation effect of Ag inclusions in the BaTiO3 matrix. The Ag was present in the form of discrete layer in the BaTiO3 film. The dielectric properties of BaTiO3-Ag were discussed in detail taking into account the changes in microstructures.
Key words: composites; percolation; aerosol deposition; BaTiO3; Ag
1 Introduction
BaTiO3 is a dielectric ceramic with a perovskite crystal structure. Because of its unique ferroelectric property, it is commonly used in various types of passive components in electronic devices, including multi-layer capacitors, transducers, thermistors and electro optic devices [1,2]. In conventional electronic package devices and passive components, including capacitors, resistors and inductors account for approximately 80% of electronic components and the ratio of passive to active components continues to increase. Therefore, the process used for embedding passive components is becoming a new paradigm in the area of electronic device fabrication, in attempts to achieve system miniaturization and high performance[3,4]. However, there are several technical issues that remain to be solved in the area of embedded passive technology, including the materials used, the processes involved in their fabrication, and system designs. Considering the integration schemes associated with conventional printed circuit board (PCB) processes, the processing temperature should be kept below 200 °C to prevent the degradation of the polymer resin and epoxy materials. In addition, a low cost process is essential in producing various passive components with a wide range of film thicknesses which meet the specifications required for dielectric constant, dielectric loss and leakage current with long-term reliability [5-7].
The aerosol deposition method (ADM) proposed by Akedo is a potentially promising process as a substitute for conventional thin film techniques, such as vacuum evaporation, DC and RF sputtering, chemical vapor deposition, sol-gel process and anodization, etc [8,9]. As published elsewhere, high density dielectric films well crystallized could be obtained through the impact consolidation of starting ceramic powders on substrates at room temperature using the ADM process [9-11].
The findings reported herein indicate that the ADM can be used in an embedded passive fabrication process using BaTiO3. Due to the unique nanocrystalline microstructure of the aerosol deposited film, there are limitations to achieving a high dielectric constant from a ferroelectric BaTiO3 film. Therefore, the percolation concept of incorporating Ag into a BaTiO3 film was employed to increase the dielectric constant [12]. In order to investigate the effect of Ag addition on the BaTiO3 matrix on the dielectric properties of a composite film, the changes of the internal microstructure of the product were monitored in detail.
2 Experimental
BaTiO3 and BaTiO3-Ag composite films were produced using aerosol deposition (AD) systems at room temperature. The aerosol deposition system is composed of two parts, an aerosol generation system and a film deposition chamber. An aerosol from raw powders is formed by mechanical vibration and mixing with a carrier gas in the aerosol generation system. A film is produced as the result of the continuous impacts of powders in an aerosol state, which is transported by the carrier gas to the substrate, which is located in a deposition chamber. The experimental details for this process were described in a previous report [9,13].
The raw powder used in this study was commercial, as-received BaTiO3 (Ferro, USA). In order to form a composite film, powdered Ag (Mitsui, SPQ05S, Japan) was mixed with powdered BaTiO3 by ball-milling. The quantity of Ag in the starting powders was controlled from 0.5% to 2% (mass fraction). In the film deposition process, the oxygen carrier gas flow was 4 L/min and the base pressure of the chamber was maintained at under 1 kPa. A polished Cu plate was used as the substrate to characterize the dielectric properties of the thick films.
The surface morphology and crystallinity of the raw powders and as-deposited films were characterized by field emission scanning electron microscopy (FE-SEM) and transmission electron microscopy (200 kV, Jeol JEM-2000EX), respectively. A cross-sectional TEM sample was prepared using a focused ion beam (FEI company helios 2000E) after applying a coating of carbon and platinum as a protective layer. Dielectric properties were measured after completing a microstructure analysis of the BaTiO3 thick film and the BaTiO3-Ag composite thick film. A circular upper electrode with diameter of 1.5 mm was formed with an Au sputter, using a mask, on the thick film grown on the Cu substrate. Leakage current measurements were also applied to evaluate the electric properties of the films. Dielectric property evaluation was done by means of an impedance analyzer (Agilent, 4294A), and leakage current measurements were made using a sourcemeter (Keithley, 2636 system sourcemeter).
3 Results and discussion
SEM images of the raw BaTiO3 and Ag powders used are shown in Figs. 1(a) and (b), respectively. The as-received BaTiO3 powders have irregular shapes with an average particle size of 0.5 μm. The Ag powders are spherical shaped with an estimated average size of 0.2-0.5 μm. Ag is chosen for use in growing a ceramic-metal hybrid composite film due to its high resistance to oxidation in the low vacuum conditions used in the aerosol deposition [9]. The amount of Ag in the starting powders varies from 0 to 2% (mass fraction). When 2% Ag powder is added to the starting powders, the composite film fails to maintain its dielectric properties, due to electrical breakdown.

Fig. 1 SEM images of as-received BaTiO3 (a) and Ag (b) powders
Given the above findings, BaTiO3-1.5% (mass fraction) Ag powders were used in the aerosol deposition for growing composite films on polished Cu substrates at room temperature. Scanning electron microscopy (SEM) analysis was done to observe the surface morphology of the product, as shown in Fig. 2(b), compared with the pure BaTiO3 film in Fig. 2(a). The thicknesses of the BaTiO3 and BaTiO3-Ag composite films are 10.4 and 13.9 μm, respectively. The morphology of the BaTiO3- Ag composite film is similar to that of BaTiO3 thick film. The surface roughnesses (Ra) of BaTiO3 and BaTiO3-Ag composite film are about 0.12 and 0.83 μm, respectively. However, in the cross-sectional focused ion beam (FIB) image of the BaTiO3-Ag composite film (Fig. 2(c)), the Ag is clearly present in the form of discrete layers with depth of 1-3 μm.
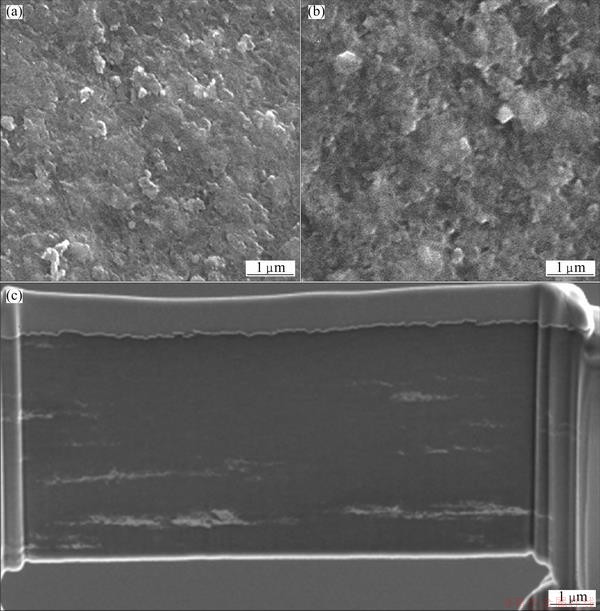
Fig. 2 SEM images of pure BaTiO3 (a) and BaTiO3-1.5%Ag (b) powders and cross-sectional FIB image of BaTiO3-Ag composite film (c)

Fig. 3 Optical images of BaTiO3 based thick film grown by using mixture of starting powders with different Ag
The change of microstructure in the BaTiO3-Ag composite film as a function of the amount of Ag in the starting powders can be readily monitored by optical microscopy. The optical image of the BaTiO3-Ag composite film shown in Fig. 3 reveals that the isolated Ag particles are very homogeneously distributed on the surface with a bright contrast. The Ag distribution increases when the amount of Ag in the starting powders increase from 0.5% to 2.0%.
Figure 4 shows the dependence of the dielectric constant on the Ag content of the starting powders. The BaTiO3 film has a dielectric constant of around 68.4, and the composite film grown using a BaTiO3-1.8%Ag (mass fraction) starting powder has a dielectric constant of 101.8, which is an increase of 0.5 times. When amounts in excess of 2% Ag is used in the starting powders, the BaTiO3-Ag composite thick film becomes a conductor, which prevents measurement of the dielectric properties. It can be concluded that the inclusion of Ag has a significant effect on the dielectric properties of the BaTiO3 films. However, no substantial enhancement in dielectric constant in the vicinity of percolation thresholds is observed in our system in contrast to previous reports [14,15]. This might be due to the different microstructure of Ag in the BaTiO3 film, when it is grown by aerosol deposition.
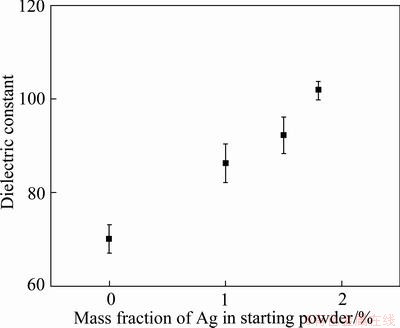
Fig. 4 Various curve of dielectric constant with Ag content in starting powders
Figure 5 shows cross-sectional transmission electron microscopy (TEM) images of BaTiO3 and BaTiO3-Ag composite films. As shown in Fig. 5(a), a highly dense BaTiO3 film is formed at room temperature, when aerosol deposition is used. The ring type diffraction pattern of the BaTiO3 film including a diffused center beam spot shown in the inset of Fig. 5(a) indicates that its microstructure is nanocrystalline in nature with crystal sizes of 10-20 nm. On the other hand, Ag is present in the form of discrete layers in the BaTiO3-Ag composite film as shown in Fig. 5(b). No voids or cracks are detected at the interface between the Ag layered structure and BaTiO3. This suggests that no heterojunction reaction occurs between BaTiO3 and Ag during the growth of the composite film. However, strong physical bond formation is found at the interface due to the impaction caused by the highly accelerated BaTiO3 and Ag powders. It should be noted that the effective dielectric field developed around the conducting Ag layers resulted in an increase of the dielectric constant of BaTiO3-Ag composite film.
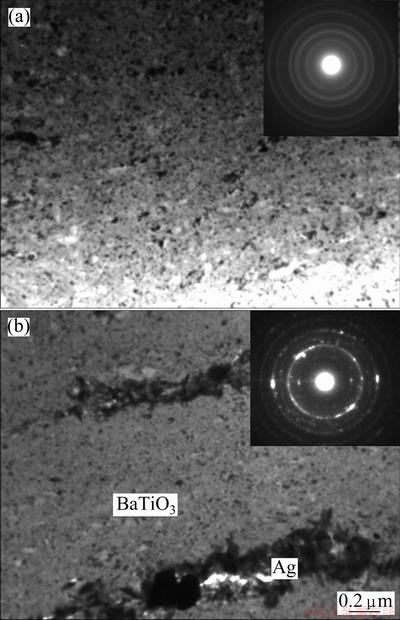
Fig. 5 Cross-sectional TEM images of BaTiO3 (a) and BaTiO3-Ag (b) composite films
The growth mechanism of the BaTiO3-Ag composite thick film can be explained by the micro- structure analysis, as previously discussed. The Ag powder used in the process is a solid powder with particles sizes of 200-500 nm. As shown in Fig. 5(b), the Ag layered structure in the photograph is 0.1 μm thick, and 0.6-3.6 μm long, and is distributed perpendicular to the growth direction of the BaTiO3-Ag composite film. It is assumed that the Ag powder will be compressed without being fragmented, due to its high ductility. Dimension measurements based on this assumption results in identical figures, as shown in the TEM images of the Ag layered structure. In other words, the BaTiO3 powder breaks down on impact with the substrate, and contributes mainly to the thick film growth. In addition, the Ag powder does not break down, and instead, is compressed, contributing to the thick film growth as well. The distribution of the Ag layered structure increases with the increase of the amount of Ag of BaTiO3-Ag composite in the starting mixture.
When a powder mixture of BaTiO3 and Ag is used,a composite film with a higher dielectric constant could be grown by aerosol deposition. Moreover, this composite with low dielectric loss of about 0.01 supports the conclusion that a high quality of the dielectrics is achieved, as described in Table 1.
Table 1 Dielectric and electric properties of BaTiO3 film and composite film grown with BaTiO3-1.8% Ag (mass fraction) starting powder

4 Conclusions
1) BaTiO3-Ag hybrid composite films are successfully grown at room temperature by aerosol deposition, which is achieved by a physical consolidation process caused by the mixed powders impacted the substrate at a high velocity.
2) Ag is present in the form of discrete layers due to its ductile properties compared to BaTiO3.
3) The dielectric constant of a composite film grown with BaTiO3-1.8% (mass fraction) Ag starting powders is 101.8 at 1 MHz, which is 1.5 times higher that of a pure BaTiO3 film.
4) The dielectric loss of the BaTiO3-Ag composite film (tan δ= 0.01) is also sufficiently low to permit it being an embedded capacitor.
Acknowledgements
This research was supported by a grant from the Fundamental R&D Program for Core Technology of Materials funded by the Ministry of Knowledge Economy, Korea.
References
[1] HAYASHI T, OJI N, MAIWA H. Film thickness dependence of dielectric properties of BaTiO3 thin films prepared by sol-gel method [J]. Japanese Journal of Applied Physics, 1994, 33: 5277-5280.
[2] CHIEN A T, SPECK J S, LANGE F F, DAYKIN A C, LEVIC G. Low temperature/low pressure hydrothermal synthesis of barium titanate: Powder and heteroepitaxial thin films [J]. Journal of Materials Research, 1995, 10: 1784-1789.
[3] TUMMALA R. Fundamentals of microsystems packaging [J]. New-york: McGrow-Hill, 2001: 10-25.
[4] ULRICH R K, SCHAPER L W. Intergrated passive component technology [J]. Hoboken: Wiley-Interscience Press, 2003: 1-30.
[5] RAO Y, WONG C P. Material characterization of a high-dielectric-constant polymer–ceramic composite for embedded capacitor for RF applications [J]. Journal of Applied Polymer Science, 2004, 92: 2228-2231.
[6] POTHUKUCHI S, LI Y, WONG C P. Development of a novel polymer–metal nanocomposite obtained through the route of in situ reduction for integral capacitor application [J]. Journal of Applied Polymer Science, 2004, 93: 1531-1538.
[7] QI L, LEE B I, CHEN S, SAMUELS W D, EXARHOS G J. High-dielectric-constant silver-epoxy composite as embedded dielectrics [J]. Advanced Materials, 2005, 17: 1777-1781.
[8] AKEDO J, LEBEDEV M. Influence of carrier gas conditions on electrical and optical properties of Pb(Zr, Ti)O3 thin films prepared by aerosol deposition method [J]. Japanese Journal of Applied Physics, 2001, 40: 5528-5532.
[9] AKEDO J. Aerosol deposition of ceramic thick films at room temperature: Densification mechanism of ceramic layers [J]. Journal of the American Ceramic Society, 2006, 89: 1834-1839.
[10] IMANAKA Y, HAYASHI N, TAKENOUCHI M, AKEDO J. Aerosol deposition for post-LTCC [J]. Journal of the European Ceramic Society, 2007, 27: 2789-2795.
[11] NAM S M, MORI N, KAKEMOTO H, WADA S, AKEDO J, TSURUMI T. Alumina thick films as intertral substrates using aerosol deposition method [J]. Japanese Journal of Applied Physics, 2004, 43: 5414-5418.
[12] CHEN C Y, TUAN W H. Mechanical and dielectric properties of BaTiO3/Ag composites [J]. Journal of Materials Science Letters, 1999, 18: 353-354.
[13] HATONO H, ITO T, MATSUMURA A. Application of BaTiO3 film deposited by aerosol deposition to decoupling capacitor [J]. Japanese Journal Applied Physics, 2007, 46: 6915-6919.
[14]
C, ESTEBAN-BETEGON F, BARTOLOME J F, LOPEZ-ESTEBAN S, MOYA J S. New percolative BaTiO3-Ni composites with a high and frequency-independent dielectric contant [J]. Advanced Materials, 2001, 13: 1541-1544.
[15] TUAN Wei-hsing, HUANG Yung-ching. High percolative BaTiO3-Ni nanocomposites [J]. Mater Chem & Phys, 2009, 118: 187-190.
(Edited by LI Yan-hong)
Corresponding author: Young Joon YOON; Tel: +82-2-32827854; Fax: +82-2-32827838; E-mail: yjyoon@kicet.re.kr
DOI: 10.1016/S1003-6326(12)61796-8