
Corrosion behavior of CuCrNiAl alloy in HCl solutions
YU Cui-yan(于翠艳)1, CHANG Li-min (常立民)2, ZHOU Li-min(周利敏)3, LIN Hong-yan(林红岩)1
1. Department of Applied Technology, Daqing Petroleum Institute, Daqing 163318, China;
2. Analysis and Measure Center, Jilin Normal University, Siping 136000, China;
3. College of Electric Engineering, Yanshan University, Qinhuangdao 066004, China
Received 22 April 2005; accepted 26 September 2005
Abstract: The corrosion behavior of a CuCrNiAl alloy in HCl solutions was studied by means of metallograph, XRD, SEM/EDX and TEM methods. The results show that in low concentration of HCl solutions, Cu of CuCrNiAl alloy is more easily subject to corrsion than Cr; the dechromisation of the CuCrNiAl alloy occurs at a certain concentration of HCl solutions, at the same time Al of CuCrNiAl alloy is subject to corrosion also. The dechromisation corrosion occurs initially at the interface between Cr phase and Cu phase, then it gradually extends Cr phase until Cr phase is dissolved completely. It is also revealed that the tendency of dechromisaion of the CuCrNiAl alloy increases with the increase in concentration and temperature of HCl solutions.
Key words: CuCrNiAl alloy; HCl solutions; corrosion behavior
1 Introduction
Cu alloy has become a kind of important materials for ocean construction as its excellent anti-corrosion performance. Though this kind of alloy has been applied for a long time, it often undertakes serious corrosion, low strength and leakage in the early stage during its service[1]. So it needs to develop a kind of Cu alloy with high strength and excellent anti-corrosion performance. The CuCr alloy has been applied widely in vacuum circuit breaker with its high strength, excellent electric conductivity and heat conductivity. There are also some reports about preparation, mechanical performance and electric performance of this CuCr alloy[2-8]. Recently CHIANG[9] reported that CuCr coating successfully protected NARLOY-Z from corrosion under flowing corrosive gas at high temperature. WALTER and CHIANG[10] reported that CuCr coating prolonged the creep rupture life of matrix at 482-704℃, which indicated that CuCr alloy can be applied at high temperature. Hence, many researches on the high temperature corrosion of CuCr alloy under different conditions were done[11-13]. However study on its corrosion behavior in solutions has scarcely been reported. The authors have studied the corrosion behavior of a CuCr alloy in HCl solutions and discovered serious dechromisation behavior in HCl solutions. Therefore, we added a little Ni and Al to CuCr alloy and studied the corrosion behavior of CuCrNiAl alloy in HCl solutions. The experimental results showed that there were two obvious corrosion characteristics of CuCr alloy in HCl solutions. When the concentration and temperature of HCl solution were compatible, it occurred dechromisation phenomenon. Some results about Cu alloys’ dealloying have been reported [14, 15], but mainly concentrated on brass’s dezincification and aluminum bronze’s dealuminization, and few reports were about Cu-Cr alloys’ dechromisation. Therefore, research on the dechromisation of CuCr alloy is significant for understanding of CuCrNiAl alloy’s corrosion behavior in HCl solutions and increasing the probability of CuCrNiAl alloy’s application.
2 Experimental
The raw materials were oxygen-free copper, chromium powder(99.9%), nickel powder(99.95%) and aluminium powder(97%). The raw materials were melted in a crucible which was fixed in a vacuum furnace, after completely melting, the melt was cooled in the furnace to room temperature, and the CuCrNiAl alloy containing Cu 47.48%, Cr 50.54%, Al 1.34%, Ni 0.42% and others 0.22%(mass fraction) was obtained.
The specimens with the size of 5 mm×5 mm×10 mm were prepared from the alloy ingot. The specimens were rubbed to 1 200# grit abrasive paper, then polished, washed with water and degreased with alcohol, and then were immersed in HCl solutions with different concentrations and temperatures. Tests were carried out on a HHS-12 type electric thermostatic water container. The phenomenon of the experiment was observed and the rate of dechromisation was calculated according to the following equation: V=h/t, where h is the thickness of dechromisation layer, t is the dechromisation time recorded from the beginning of bubble evolution. The corrosion morphology, the characteristics of dechromisation, and the composition of phase and micro-zone were observed and analyzed by means of ADVANTPXP-381 X-ray fluorescence spectrometer, XP-2TM profilometer, Neophot21 metallomicroscope, H800 TEM, KYKY-2800 SEM (with EXD) and D/MAX-rB XRD(with graphite monochromator, Kα radiation).
3 Result
There were two corrosion phenomena when the CuCrNiAl alloy was immersed in HCl solutions through macroscopical observation as listed Table 1. When the concentration of HCl solutions was low, the surface of the sample immersed in HCl solutions displayed light grey and silvery white grains can be found at the surface along with increase in the immersion time of the sample. The results shown in Fig.1 reveal that some of the samples are seriously corrupted. The experimental results (Table 2 and Fig.2) show that on the surface of sample the content of Cu decreases and the content of Cr increases respectively. However the contents of Al and Ni do not change a lot. Fig.3 shows the microstructure of the CuCrNiAl alloy. It can be seen that the CuCrNiAl alloy is composed of Cu phase and Cr phase with the articulated Cr phase scattering into the Cu phase substrate. The results in Fig.4 show that there exists serious corrosion at the interface between Cu phase and Cr phase, and Cr phase is in the front of Cu phase, this means that the corrosion under the experimental condition is selective, Cu phase is easier subject to corrupt than Cr phase, the corrosion occurs initially at the surface between Cu phase and Cr phase.
Table 1 Phenomenon of CuCrNiAl alloy in HCl solutions
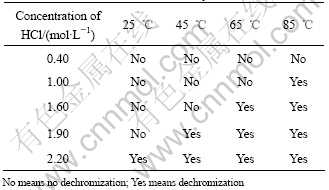
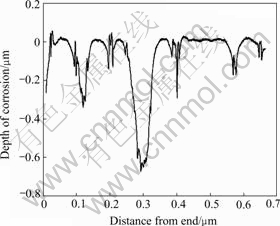
Fig.1 Smoothness of un-dechromised samples’ surface in HCl solutions
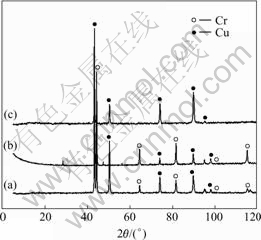
Fig.2 XRD patterns of samples: (a) Original; (b) Undechromised; (c) Dechromised
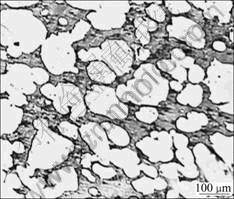
Fig.3 Original microstructure of CuCrNiAl alloy
Table 2 Composition of surface of samples under different conditions (mass fraction, %)

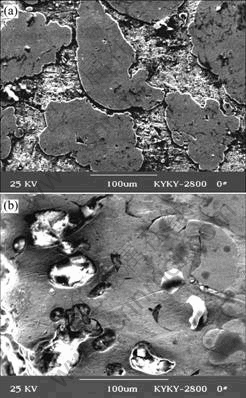
Fig.4 Corrosion characteristics of CuCrNiAl alloy in HCl solutions: (a) Un-dechromisation; (b) Dechromisation
As the concentration and temperature of HCl solutions increase, the corrosion of the alloy becomes more serious. When the concentration and temperature of HCl solutions increase to a certain value, the surface of sample is seriously corroded and it gradually becomes pure copper color, with solutions turning into blackish green and plenty of gases. Experiments on sample’s surface through fluorescence spectrometer and XRD show that: the content of Cr is much lower, the content of Ni increases a little and the content of Al decreases. It is concluded that this kind of phenomenon should result from the dechromisation behavior, and Al is corroded. The results listed in Table 2 show that the concentration of Cl- on the sample’s surface is high at the beginning of the dechromisation, indicating that Cl- participates in the corrosion course. The surface of dechromisation sample was scraped up to the interface between the dechromisation zone and original substrate zone, and observed by Neophot21 microscope. The results show that in the zone of dechromisation the substrate of Cu phase contains a lot of holes (Fig.5) and the size of holes is smaller than that of Cr phase. SEM analysis show that the Cr content in the white and bright zone is 31.25% (mass fraction, %), much lower than that in Cr phase (99.82%). This means that the dechromisation of CuCrNiAl alloy occurs at the interface between Cu phase and Cr phase initially, and then extends into the Cr phase until Cr phases are dissolved completely. In order to further observe the microphenomenon of corrosion, TEM analysis was conducted on dechromisation sample. The results (Fig.6) show that in Cr substrate, dechromisation takes place in the Cr phases with the size of 10-100 nm, and the corrosion characteristics are the same as that from SEM observation.
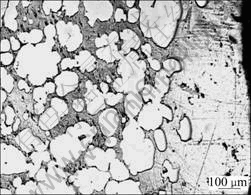
Fig.5 Morphology of CuCrNiAl alloy dechromisation layer
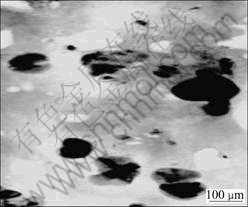
Fig.6 TEM micrograph of dechromisation zone
It can also be found that after being immersed in HCl solution for a certain time (incubation time), the specimen dechromisates, once dechromisation happens, it goes rapidly, increasing solutions concentration and temperature is favorable to shortening incubation time and speed the dechromisation, as listed in Table 3.
Table 3 Incubation time and dechromisation rates of CuCrNiAl alloy in HCl solutions
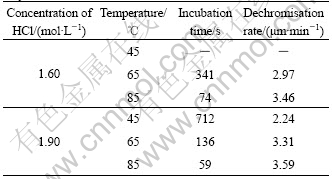
4 Discussion
It can be known from potential(
)-pH diagrams that there is a potential difference between Cr and Cu phase in acid solutions, that is to say, CuCrNiAl alloy shows a strong tendency of selective corrosion in acid solutions theoretically. In fact, when CuCrNiAl alloy is immersed in low concentration of HCl solutions, the corrosion of Cu phase is much easier than that of Cr phase. This is probably due to the passivation of Cr. After the passivation the electrode potential of Cr becomes more positive, so the tendency of dechromisation of CuCrNiAl alloys becomes much lower. While, in solution Cl- and Cu can form a kind of ion CuCl2-[16], leading to the continuous dissolution of Cu. So the dechromisation rate is higher, and much more CuCl2- is formed when the temperature as well as the number of Cl- increases.
When the Cl- concentration reaches a certain value, because of its small radius, strong penetrability, high polarity, and easy distortion, it can destroy the passivation film on Cr surface. The activation of Cr is higher when the temperature is high and it enhances this kind of destruction on Cr surface. Therefore when the concentration of Cl- and the temperature are suitable, the passivation film on Cr phase is superior to Cu phase, the corrosion behavior of CuCrNiAl changes, the corrosion of Cr phase is prior to that of Cu phase. It can be concluded that Cu and Cr in the solutions compose a corrosion battery with Cr being the anode and Cu being the cathode, and the gas produced on the sample is H2. It can be described simply as
Anodic reaction: Cr→Cr3++3e (1)
Cathodic reaction: 2H++2e→H2 (2)
It is concluded from the above experimental results that the dechromisation initially occurs at the interface between Cu and Cr phase and then extends into the Cr phase inside. The reason is that CuCrNiAl alloys are composed of Cu phase and Cr phase, and these two phases can not almost dissolve each other. The atom diameters and crystal structure of Cu phase and Cr phase are different form each other, so at the interface between the two phases the atom arrangement is not continuous, and there exist many holes, leading to lower density and lower diffusion resistance for atoms.
Through microscopic observation it can be found that the size of holes on the substrate of Cr phase in dechromisation area is much less than the size of Cr phase in original organization. This means that the vacancy that Cr atoms left is occupied by Cu atoms and the mechanism will be further discussed.
5 Conclusions
1)Cu in CuCrNiAl alloy is more easily subject to corrosion than Cr in low concentration of HCl solution. When the concentration of HCl is at a certain value, the dechromisation of CuCrNiAl alloys occurs, and Al is corroded also. The tendency of dechromisation is higher when the concentration of HCl as well as the temperature increases.
2)The dechromisation of CuCrNiAl alloys initially occurs at the interface between Cu phase and Cr phase, then extends to the Cr phase until Cr phase is dissolved completely, and the size of holes on the substrate of Cr phase in dechromisation area is much less than that of Cr phase in original organization.
3)The corrosion behavior of CuCrNiAl alloys in HCl solutions is selective. We can change the corrosion behavior of CuCrNiAl by controlling the temperature as well as the concentration of HCl solutions.

References
[1] ZHU Xiao-long, LEI Ting-quan, XU Jie. The effects of deformation on corrosion behavior of 70Cu-30Ni alloy[J]. The Chinese Jounal of Nonferrous Metals, 1997, 7(2): 79-81.(in Chinese)
[2] Statya Prasad V V, Rama Krishma RAO U, MISRA R D K. Electroslag crucible melting of age hardening copper-chromium alloy[J]. Material Science and Technology, 1995, 11: 1306-1309.
[3] RIEDER W F, Schussk M, Glatzle W, KNY E. Influence of composition and Cr particle size of Cu/Cr contacts on chopping current, contact resistance and breakdown voltage in vacuum interrupters[J]. IEEE Trans Comp Hydrids Manufact Technol, 1989, 12(2): 273-283.
[4] LI Jin-ping, LUO Shou-jing, JI Song. Characteristics of CuCr contact materials made by explosivesintering[J]. The Chinese Journal of Nonferrous Metals, 2001, 11(S1): 98-101.(in Chinese)
[5] WANG Li-bin, ZHANG Cheng-yu, DING Bin-gju. Influence of W or C adding on the microstructure of CuCr25 alloys[J]. Rare Metal Materials and Engineering, 2003, 32(1): 41-44. (in Chinese)
[6] WANG Jiang, ZHANG Cheng-yu, DING Bing-jun. Microstructures and properties of CuCr25 alloys melted by vacuum induction[J]. Rare Metal Materials and Engineering, 2001, 30(4): 290-294. (in Chinese)
[7] JIN Y, Adachi k, Takeuchi T. Correlation between the colding-working and aging treatment in a Cu-15wt pct Cr in situ composite[J]. Matellurgical and Materials Transactions, 1998, 29A(8): 2195-2204.
[8] COOPER K P, AYERS J D, Malzahnkampe J C. Microstruatural evolution and thermal stabilitly in rapidly solidified high-chromium-containg coppers[J]. Materials Science and Engineerings, 1991, A142: 221-233.
[9] CHIANG K T. Hot gas erosion resistance of a vapor-deposited Cu-Cr coating[J]. Surface and Coating Technology, 1999, 114: 1-6.
[10] WALTER R J, CHIANG K T. Creep of uncoated and Cu-Cr coated NARloy-Z[J]. Materials Science and Engineering, 1999, A263: 8-14.
[11] FU Guang-yan, NIU Yan, WU Wei-tao, GUAN Hong-rong. Oxidation of two-phase Cu-Cr alloys with different microstructures[J]. Trans Nonferrous Met Soc China, 2001, 11(3): 333-336.
[12] CAO Zhong-qiu, NIU Yan. Effect of grain size on the oxidation behavior of Cu-20Ni-20Cr alloy[J]. Rare Metal Materials and Engineering, 2003, 32(12): 1016-1020. (in Chinese)
[13] ZHANG Cheng-yu, WANG Jiang, ZHANG Hui. Deoxidization of CuCr25 alloys prepared by vacuum induction melting[J]. Trans Nonferrous Met Soc China, 2001, 11(3): 237-239.
[14] HAN Zhong, ZHAO Hui. Study on dealloying corrosion of QA-9-2 alloy in 3.5%NaCl solution[J]. Acta Metallurgica Sinica, 2000, 36(5): 521-524. (in Chinese)
[15] WANG Ji-hui, JIANG Xiao-xia, LI Shi-zhuo. Advances of researches on the dezincification mechanism of brass[J]. Chinese Journal of Materials Research, 1999, 13(1): 1-7. (in Chinese)
[16] FU Li-ying, CHEN Zhong-xing, CAI Lan-kun. Effect of pH and chloride on corrosion of beonze[J]. Corrosion & Protection. 2000, 21(7): 294-296.
Corresponding author: YU Cui-yan; Tel: +86-13703234535; E-mail: xt4535@yahoo.com.cn
(Edited by YUAN Sai-qian)