稀有金属 2014,38(01),1-7 DOI:10.13373/j.cnki.cjrm.2014.01.001
电火花表面改性对AZ91D镁合金电弧喷涂铝涂层耐蚀性的影响
赵建华 王自红 盖锐
重庆大学材料科学与工程学院
国家镁合金材料工程技术研究中心
摘 要:
通过电弧喷涂/电火花沉积复合工艺在AZ91D镁合金表面制备了耐蚀性涂层。利用扫描电镜 (SEM) 、能谱分析仪 (EDS) 、电化学测试和浸泡实验等研究手段, 研究了电弧喷涂/电火花沉积复合涂层的结构及耐腐蚀性能, 并对涂层腐蚀机制进行了分析。结果表明:经电弧喷涂/电火花沉积复合处理后, E corr=-1.33 V, 较基体和喷涂铝涂层试样分别正移约280, 40 mV, 腐蚀倾向性有所降低;点蚀电位为-0.704 V, 较电弧喷涂铝涂层试样提高约60 mV, 点蚀敏感性有所降低;电弧喷涂铝涂层试样的钝化电流i pass=4.6×10-3A·cm-2, 电弧喷涂/电火花沉积处理试样的ipass=3.2×10-5A·cm-2, 经电火花表面改性后, 涂层钝化膜自修复能力大幅增强;在3.5%NaCl溶液中, 经36 h浸泡试验后, 电弧喷涂铝涂层试样表面出现直径达150μm的点蚀坑;而电弧喷涂/电火花沉积复合涂层表面仅出现直径约58μm的点蚀坑, 涂层发生的主要为亚稳态点蚀。
关键词:
电火花沉积;电弧喷涂;耐蚀性;镁合金;
中图分类号: TG174.44
作者简介:赵建华 (1962-) , 男, 湖北当阳人, 博士研究生, 教授, 研究方向:轻合金材料、表面工程;电话:13508361677;E-mail:zjh213@cqu.edu.cn;
收稿日期:2013-06-19
基金:重庆市科技攻关计划 (CSTC, 2008AA4029) 项目资助;
Effect of ESD Surface Modification on Corrosion Resistance of Electric Arc Spraying Aluminum Coating of AZ91D Magnesium Alloy
Zhao Jianhua Wang Zihong Gai Rui
College of Materials Science and Engineering, Chongqing University
National Engineering Research Center for Magnesium Alloys
Abstract:
Through the electric arc spraying ( EASP) /electric spark deposition ( ESD) compound process, the corrosion resistance coating was prepared on the surface of AZ91D magnesium alloy. The structure and the corrosion resistance of the composite coating were analyzed by means of scanning electron microscopy ( SEM) , energy dispersive spectrometer ( EDS) , electrochemical test and immersion test. The corrosion mechanism of the coating was also studied. The results showed that, compared with the substrate and EASP sample, after EASP / ESD compound process, the free corrosion potential E corr was- 1. 33 V, which was positively moved about 280, 40 mV, respectively, and the corrosion tendency was reduced. The pitting potential of the composite coating was- 0. 704 V, which enhanced about 60 mV by sprayed aluminum layer, and the pitting sensitivity was reduced. The passive current of the EASP sample and EASP / ESD sample was 4. 6 × 10- 3, 3. 2 ×10- 5A·cm- 2respectively. After ESD surface modification, the self-healing capabilities of the passive film were significantly enhanced. After 36 h immersion test in 3. 5% NaCl solution, the diameter of the pitting corrosion of sprayed aluminum coating could reach 150 μm, however, the diameter of the pitting corrosion of EASP / ESD composite coating was just about 5 ~ 8 μm, and the coating occurred mainly metastable pitting.
Keyword:
electric spark deposition; electric arc spraying; corrosion resistance; magnesium alloy;
Received: 2013-06-19
镁合金具有密度小, 比强度高等特点, 且具有良好的铸造性能和切削加工性能, 已受到汽车、航空航天、电子和通讯等行业广泛的关注[1 - 2]。然而, 由于镁合金的化学活性较高, 在大气中形成的氧化膜疏松多孔, 在潮湿的环境或硫化物和氯化物存在时都会发生严重的腐蚀, 因而在一定程度上制约了镁合金在工程领域的广泛应用[3 - 4]。
电弧喷涂是将熔融或半熔融状态的微粒以高速冲击到基体表面, 形成具有一定特性涂层的表面处理方法[5]。这种涂层是由相互叠加的微粒构成, 叠加的微粒之间必然存在孔隙。尤其是贯穿性孔隙的存在, 腐蚀介质就有可能通过穿孔到达被保护基体的表面, 使涂层与基体发生化学或电化学侵蚀[6]。电火花表面沉积技术是直接利用电能的高密度能量对金属表面进行涂覆的表面处理工艺[7]。它是通过电极材料与金属零件表面的火花放电作用, 把作为火花放电的导电材料熔渗进金属零件的表层, 从而形成含电极材料的表面涂覆层, 电火花沉积层与基材的结合强度高, 电火花沉积热输入小, 沉积过程在较低温度下进行, 对基材组织的影响小[8 - 9]。
本文采用电弧喷涂/电火花沉积复合工艺改善镁合金基材的耐腐蚀性能。通过电火花沉积工艺对电弧喷涂铝涂层进行“修复”, 并研究了电火花表面改性处理工艺对AZ91D镁合金电弧喷涂铝涂层耐蚀性的影响。
1 实验
实验以AZ91D铸造镁合金为基材。喷涂前采用粒度为30 μm的钢玉砂进行喷砂处理, 并用丙酮溶液清洗表面。采用高速电弧喷涂机进行喷涂, 喷涂电压为32 V, 电流为120 A, 空气压力为0. 6MPa, 喷涂距离为160 mm。喷涂材料选用纯度大于99. 7% 的高纯铝丝, 直径为1. 6 mm。喷涂后, 对喷铝的试样在430 ℃、氩气保护氛围下保温2 h, 进行热扩散处理, 随后随炉缓冷至室温。采用上海生造SZ-08 电火花堆焊修复机对经干燥处理的电弧喷涂铝涂层试样进行电火花沉积表面改性处理。实验电火花沉积电极材料为工业纯铝丝材, 电极直径为2 mm。电火花沉积工艺参数为: 工作电压为30 V、脉冲能量输出百分比为50% 、氩气流量6 L·min- 1、放电频率250 Hz。电火花沉积表面改性的示意图如图1 所示。
从经电弧喷涂和电弧喷涂/电火花沉积处理试样上分别切取尺寸为10 mm × 10 mm × 8 mm的试样, 将试样表面完全浸泡在质量分数为3. 5% Na Cl溶液中36 h, 其他面采用环氧树脂进行封闭。浸泡后观察涂层表面腐蚀形貌及进行腐蚀机制分析。为了降低腐蚀产物对试验的影响, 需要保证溶液的量和试样表面积的比例大于20 ml∶ 1 cm2[10]。
采用TESCAN VEGA Ⅱ LUM扫描电镜 ( 附带能谱仪 ( EDS) ) 分别对电弧喷涂铝涂层和电弧喷涂/电火花沉积改性涂层的表面和截面形貌以及浸泡实验后涂层的腐蚀形貌进行观察, 对涂层以及腐蚀产物进行元素分析。采用CHl660B Electro-chemistry Station ( 上海辰华仪器公司) 电化学工作站对AZ91D镁合金基材、电弧喷涂试样和电弧喷涂/电火花沉积改性试样进行动电位极化曲线测试。腐蚀介质为3. 5% Na Cl溶液, 测试温度为室温。采用标准三电极系统, 参比电极为饱和甘汞电极, 辅助电极为铂片, 工作电极为研究试样, 所有试样在相同测试面积下进行腐蚀试样, 测试面积为10 mm ×10 mm, 环氧树脂封闭, 扫描速度为1 m V·s- 1。
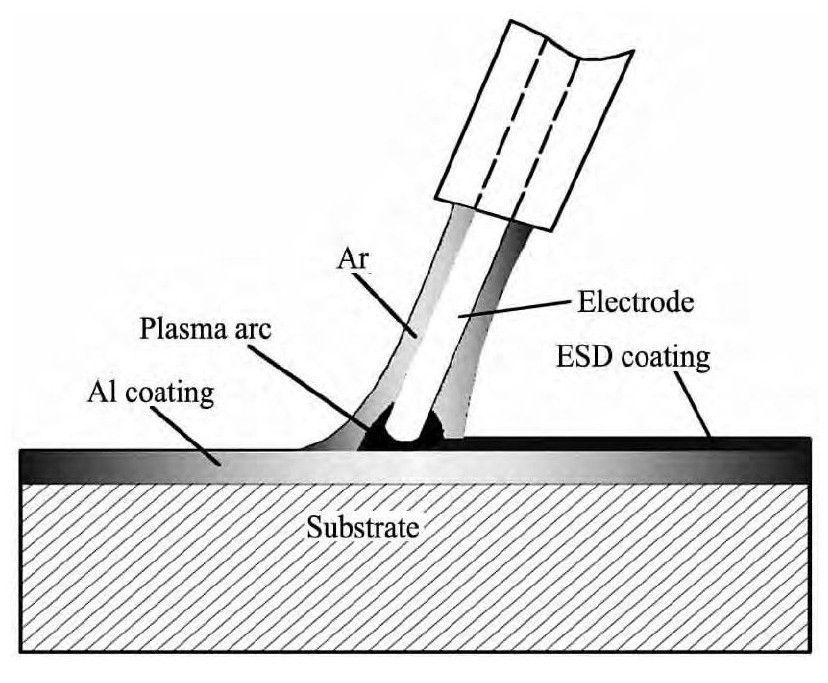
图1 电火花沉积表面改性示意图Fig. 1 ESD surface modification schematic diagram
2 涂层形貌及结构
2. 1 热扩散层形貌及元素分析
图2, 3 分别为电弧喷涂试样和经430 ℃ 热扩散处理2 h后试样基材与喷涂铝层间的界面形貌。马凯等[11]的研究表明: 在电弧喷涂过程中, 在镁合金基体与喷涂铝层之间产生Al-Mg二元相的过渡层。
图4 为热扩散层能谱分析图 ( EDS) , 其中Mg的含量约为58. 66% , Al的含量约为41. 34% ( 原子分数) 。
由图2, 3 和4 可见, 在随后的保温热扩散处理过程中, 在过渡层、基体和涂层之间发生镁铝元素的互扩散, 过渡层向两侧扩展, 过渡层与基体以及过渡层与涂层间的界面变得曲折, 形成了明显的热扩散层, 有效的改善了涂层跟基体之间的结合性能, 这为后续的电火花沉积表面改性处理过程中防止喷涂铝层因焊接应力开裂、脱落是十分必要的。
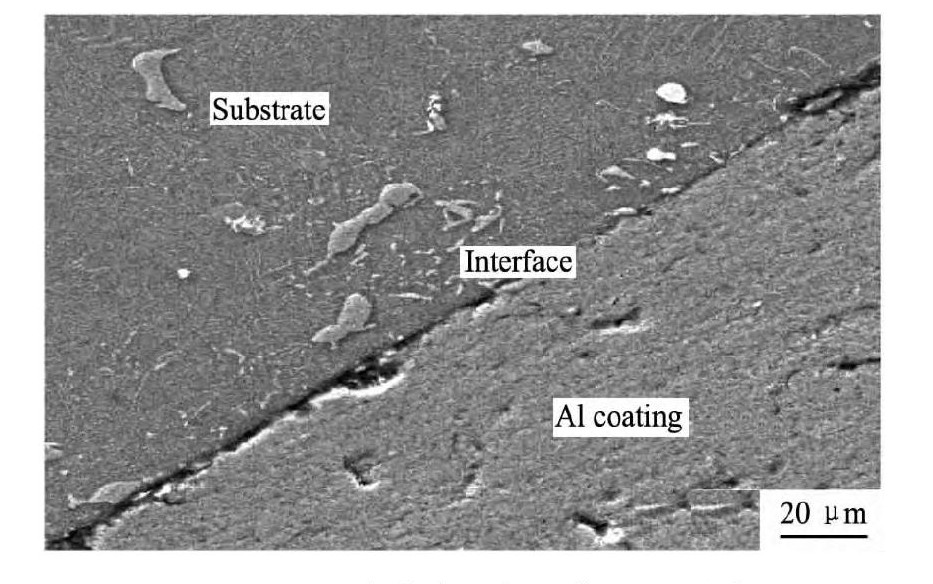
图2 电弧喷涂涂层与基体界面形貌Fig. 2Interface morphology between substrate and sprayed a-luminum layer
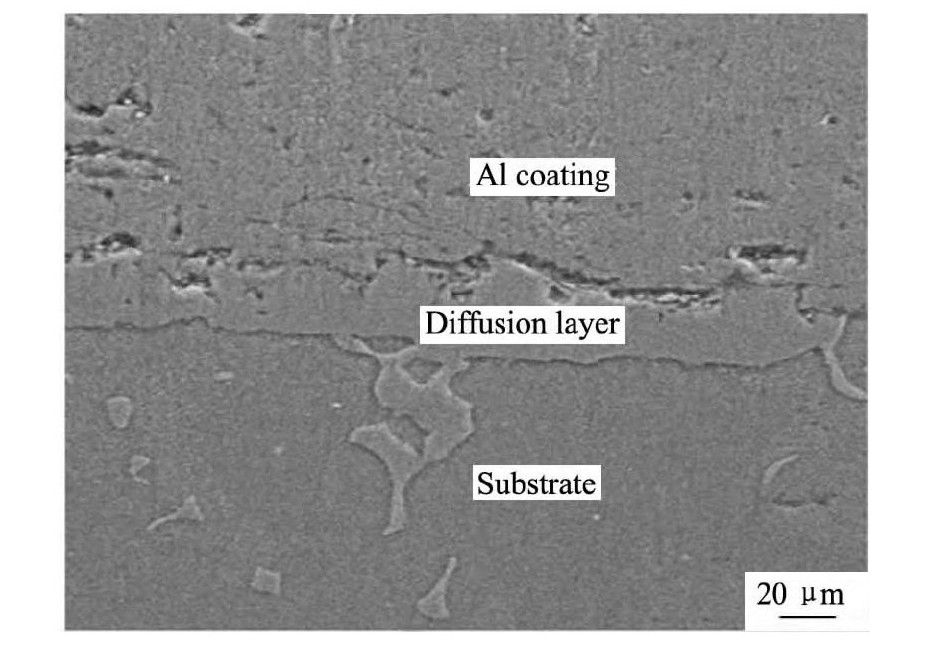
图3 热扩散处理后基体与涂层界面形貌Fig. 3 Interface morphology between substrate and coatings af-ter thermal diffusion treatment
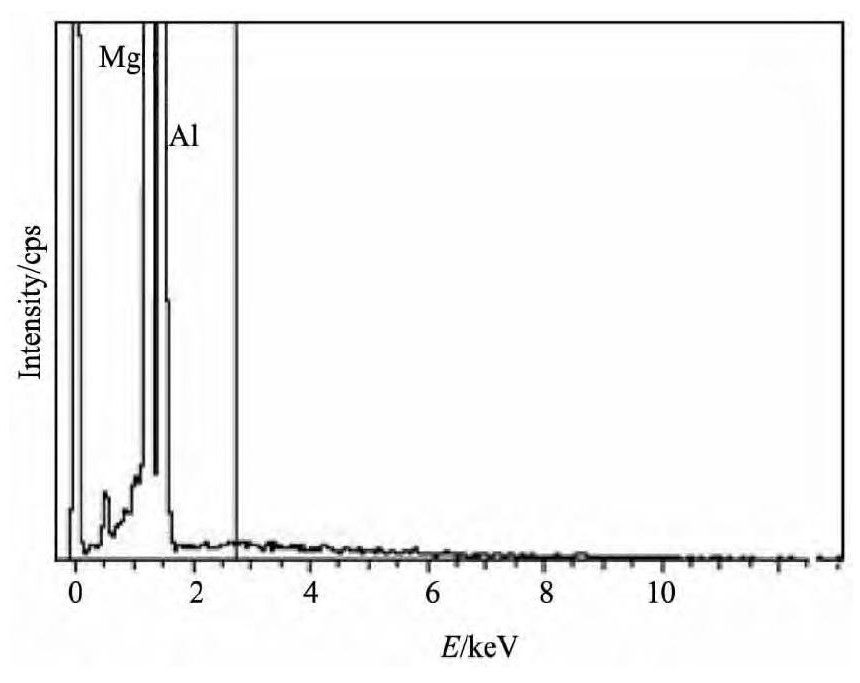
图4 热扩散层能谱分析 ( EDS) Fig. 4 EDS analysis of thermal diffusion layer
2. 2 电弧喷涂铝涂层表面及截面形貌
图5 为电弧喷涂铝涂层的表面形貌。由图5 可知, 电弧喷涂结束后喷涂铝涂层表面熔滴堆叠状明显, 熔滴呈脊状或岛状不均匀分布, 脊状和岛状组织之间形成互连, 导致喷涂后涂层表面在脊状和岛状组织之间存在喷涂凹坑及喷涂孔洞, 表面粗糙度大、致密度差、表面缺陷多。
图6 为经过热扩散处理后电弧喷涂铝涂层试样的横截面形貌。由图6 可见, 由下到上依次为基体、热扩散层和喷涂铝层。由于电弧喷涂工艺自身的喷涂工艺特点, 喷涂铝层为逐层堆叠形成, 这不可避免的导致喷涂铝层层中存在孔隙, 涂层致密性较差, 由喷涂铝层截面上部形貌, 也可以间接的看出喷涂涂层表面粗糙度较大, 存在较深的喷涂凹坑类缺陷。
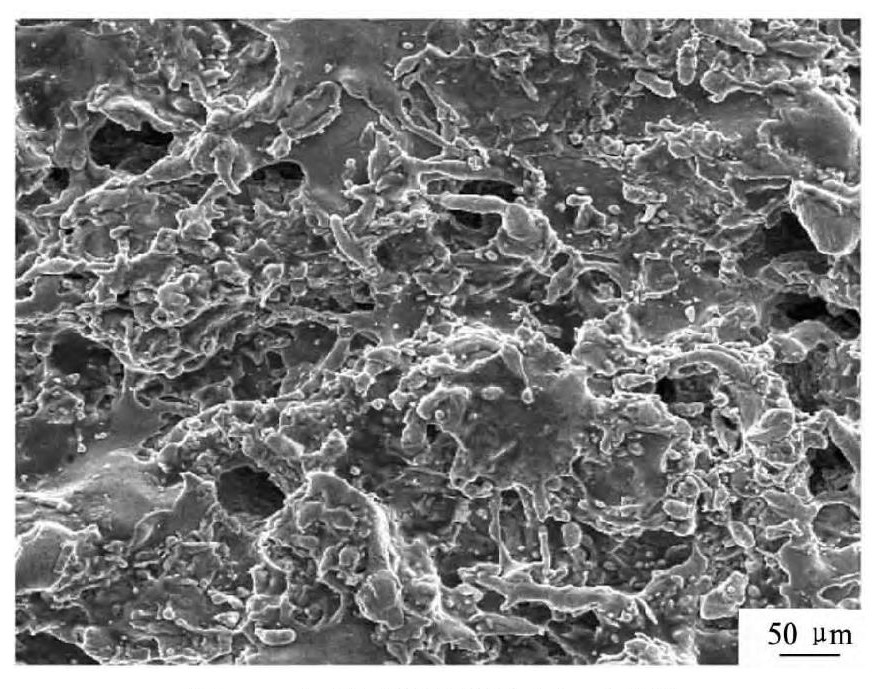
图5 电弧喷涂铝涂层表面形貌Fig. 5 Surface morphology of sprayed aluminum coating
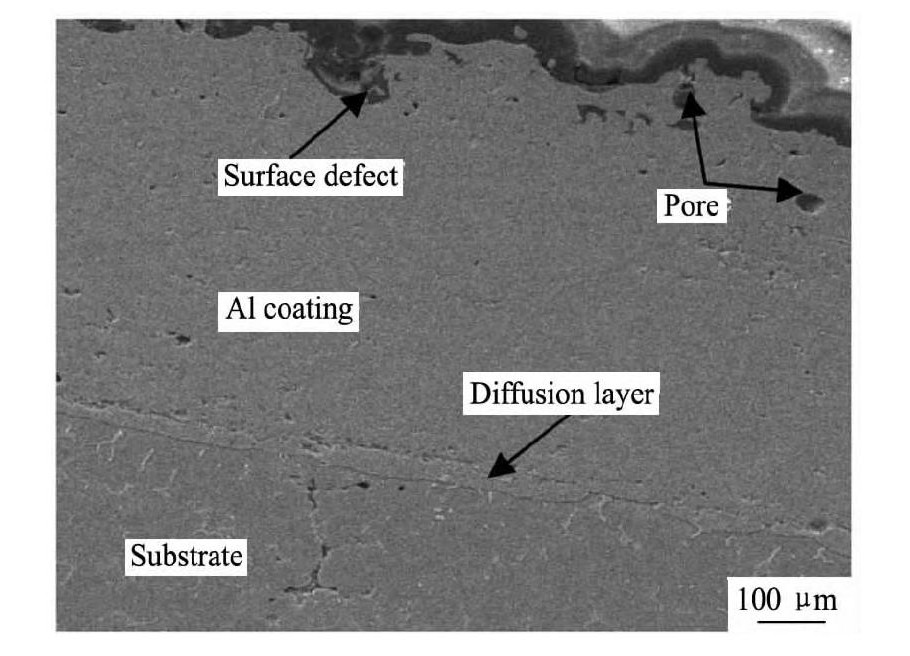
图6 电弧喷涂铝涂层截面形貌Fig. 6 Cross section morphology of sprayed aluminum coating
2. 3 电弧喷涂/ 电火花沉积复合涂层表面及截面形貌
图7 为电弧喷涂/电火花沉积复合涂层的表面形貌。由图7 可见, 电弧喷涂/电火花沉积复合涂层表面呈现出无数重叠的溅射状斑块形貌。由于沉积时电极与基体发生无数次脉冲放电, 基于脉冲放电的特性, 在脉冲间隔时间, 在基体的激冷作用下, 熔池熔滴涌溅后快速凝固, 形成溅射状斑点, 无数的溅射斑点在沉积过程中不断重熔、叠加, 最终形成图示的表面改性沉积层。与电弧喷涂铝涂层表面形貌进行对比可见, 电火花表面改性层孔隙率大幅降低, 致密性得到显著提高, 涂层表面粗糙度降低, 表面缺陷相对较少。
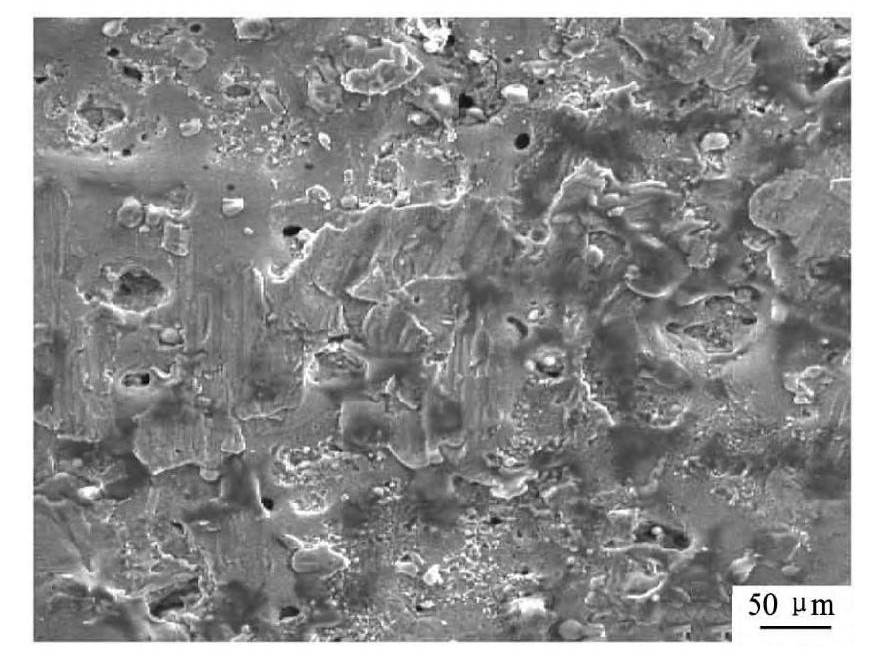
图7 电弧喷涂/电火花沉积复合涂层表面形貌Fig. 7 Surface morphology of EASP / ESD composite coating
图8 为热喷涂/电火花沉积复合涂层的横截面形貌。图8 中, 从下向上依次为AZ91D镁合金基体、热扩散层、喷涂铝层和电火花沉积层, 经电火花表面改性后, 在电弧喷涂铝涂层表面形成了约20 ~ 30 μm厚的表面改性层, 基于电火花沉积改性的特点, 电火花表面改性层与喷涂铝层间呈冶金结合, 层间结合紧密。
3 腐蚀性能及腐蚀机制分析
3. 1 极化曲线
图9 为在3. 5% Na Cl溶液中AZ91D基材、电弧喷涂铝涂层和电弧喷涂/电火花沉积试样的动电位极化曲线。对图9 中曲线A进行塔菲尔拟合得出: AZ91D镁合金基体的自腐蚀电位Ecorr= - 1. 61V, 自腐蚀电流密度icorr= 7. 6 × 10- 4A·cm- 2, 进入阳极极化以后, 腐蚀电流急剧增大, 实验过程中试样表面迅速产生气泡, 发生活性溶解。电弧喷涂铝涂层试样的自腐蚀电位Ecorr= - 1. 37 V, 较AZ91D镁合金基材正移了约240 m V左右, 腐蚀倾向性较基材有所降低。动电位扫描进入阳极区后, 喷涂铝层表面产生钝化, 钝化电流密度ipass= 4. 6 × 10- 3A·cm- 2, 由于电弧喷涂涂层表面缺陷较多, 层中也存在孔隙, 涂层致密度较差, 导致喷涂铝层表面钝化膜的均匀性较差, 钝化膜自修复能力差, 在连续的极化过程中, 铝涂层表面虽有钝化膜的产生, 钝化膜在较大的腐蚀速度下被破坏, 当电压达到- 0. 759 V是, 涂层开始发生点蚀, 腐蚀电流开始快速增大。电弧喷涂/电火花表面沉积改性试样的自腐蚀电位为- 1. 33 V, 较电弧喷涂铝涂层试样正移约40 m V, 腐蚀倾向性有所降低。当极化电压达到- 0. 704 V时出现点蚀, 点蚀电位较电弧喷涂正移约60 m V, 点蚀敏感性有所降低。在阳极极化区, 涂层表面产生钝化, ipass= 3. 2 × 10- 5A·cm- 2, 钝化膜的自修复能力较电弧喷涂试样大幅提高, 腐蚀速率大幅降低。
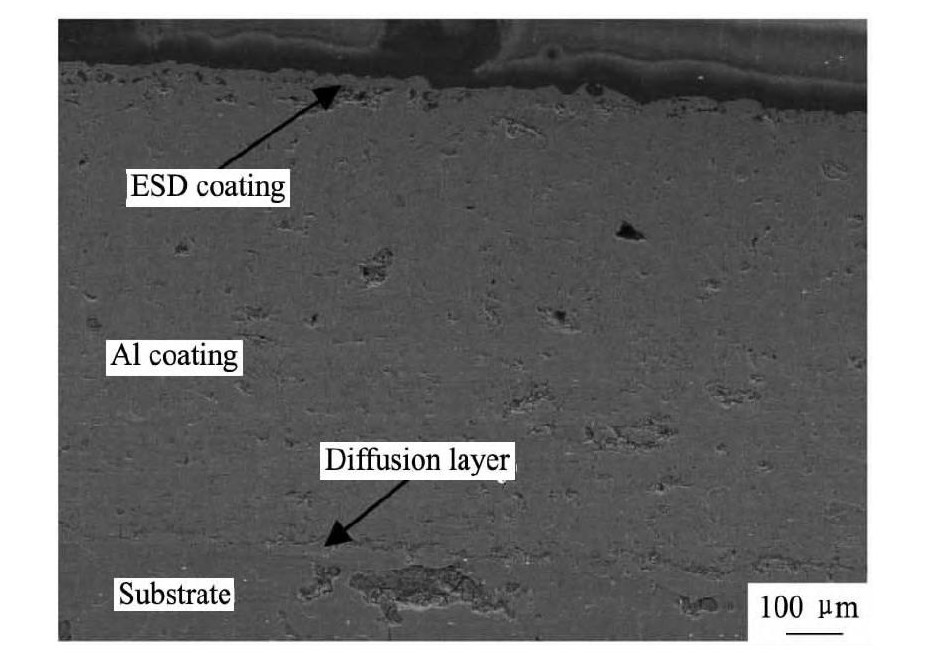
图8 电弧喷涂/电火花沉积复合涂层截面形貌Fig. 8 Cross section morphology of EASP / ESD composite coat-ing
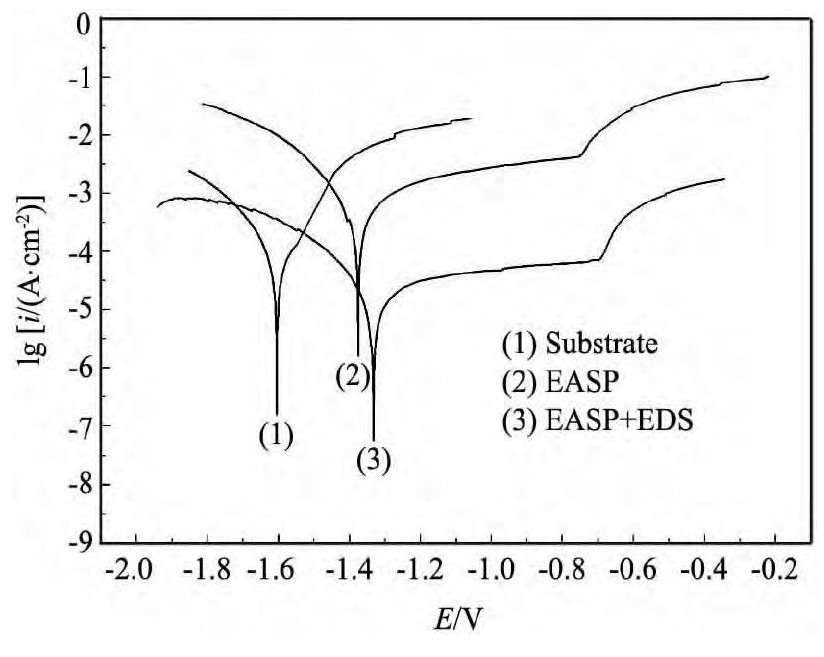
图9 基体及涂层极化曲线Fig. 9 Polarization curve of substrate and coating
3. 2 涂层腐蚀形貌及腐蚀产物元素分析
图10, 11 分别为电弧喷涂铝涂层和经电弧喷涂/电火花沉积复合工艺处理后的试样在3. 5%Na Cl溶液中浸泡36 h后的表面腐蚀形貌。
由图10, 11 可电弧喷涂铝涂层试样在3. 5%Na Cl溶液中浸泡36 h后发生了严重的点蚀, 涂层中出现大而深的腐蚀坑, 腐蚀坑直径可达150 μm左右。而电弧喷涂/电火花沉积复合处理后, 在3. 5% Na Cl溶液中经36 h浸泡试验后, 腐蚀坑直径在5 ~ 8 μm之间, 点蚀程度较电弧喷涂铝涂层试样显著降低。
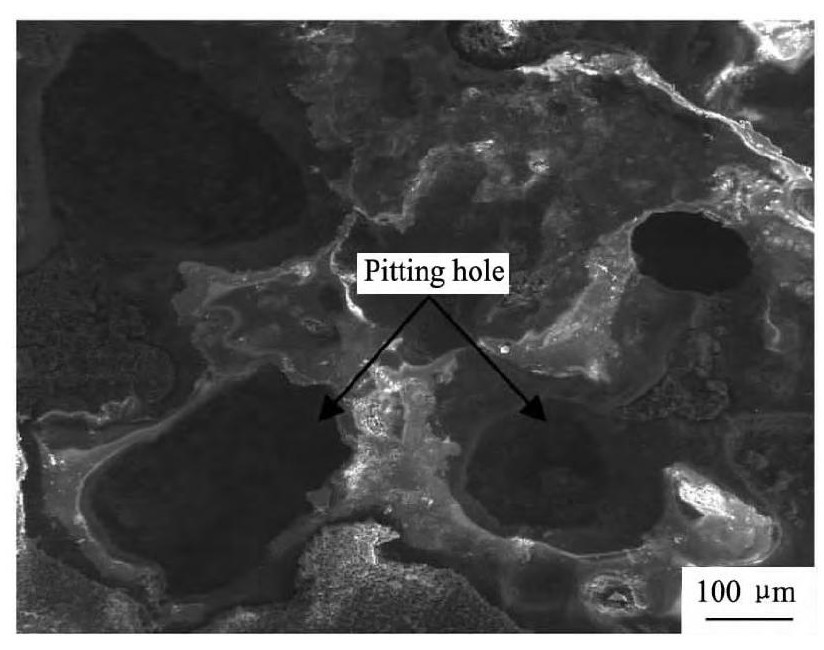
图10 电弧喷涂铝涂层腐蚀形貌Fig. 10 Surface corrosion morphology of EASP coating
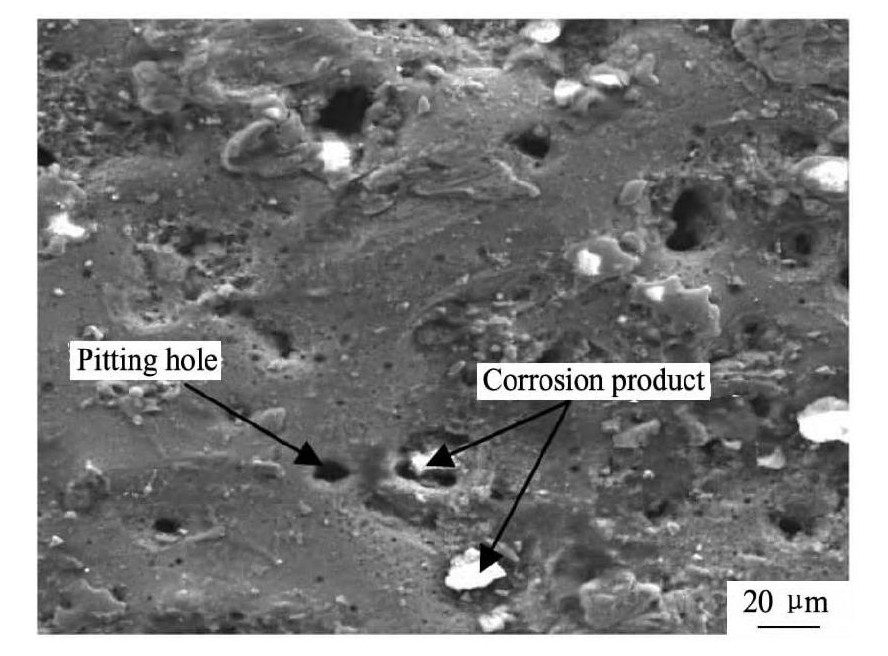
图11 电弧喷涂/电火花沉积复合涂层腐蚀形貌Fig. 11 Surface corrosion morphology of EASP / ESD coating
3. 3 腐蚀机制
根据成相膜理论, 当铝发生阳极溶解时, 可以在表面生成一层致密的氧化铝薄膜, 使其转入钝态[12]。在Na Cl溶液中, 铝涂层由于氯离子的存在而加速腐蚀, 氯离子的活度大, 氧化膜更容易把氯离子吸附在表面, 取代膜中的氧形成易溶于水的氯化物使得保护膜的结构遭到破坏。在临界点蚀电位以下, 存在亚稳点蚀阶段[13]。在钝态金属的表面上, 点蚀核优先在一些敏感位置上形成。活性阴离子在这些敏感位置上更加容易与阳离子结合形成可溶性氯化物, 从而形成孔蚀核。蚀核形成后, 可以继续生长, 也可以被迅速钝化。点蚀主要包括两个速度控制步骤: 点蚀孕育和点蚀生长[13]。金属的耐点蚀能力跟点蚀孕育速率和点蚀生长速率这两个因素密切相关。
由于喷涂铝涂层表面缺陷很多, 从而致使表面存在很多的腐蚀活性点, 涂层表面具有很高的点蚀孕育速率。喷涂铝层表面粗糙度较大、表面缺陷多, 致使铝涂层钝化膜出现缺陷, 完整性较差。同时, 由于涂层致密度较差, 层中存在喷涂孔隙, 半径小的氯离子容易侵入涂层内部, 导致其腐蚀速率大于钝化膜的形成速率, 表面膜自修复能力差, 孔蚀核有很高的生长速率, 当电位达到点蚀临界点蚀电位时, 达到临界核尺寸 ( 纯铝亚稳态点蚀坑最大直径约为10 μm[14]) 的孔蚀核发展成为蚀孔。蚀孔内的金属表面处于活态, 电位较负, 而蚀孔外的金属表面却处于钝态, 电位较正, 于是孔内和孔外构成一个活态-钝态微电偶腐蚀电池, 电池具有大阴极-小阳极的面积比结构, 阳极电流密度很大, 孔蚀加深很快, 最终发生严重的点蚀。
对于电弧喷涂/电火花表面改性铝涂层, 研究表明[15 - 16]: 电火花沉积铝涂层为细晶结构。细晶结构对纯铝的点蚀行为有两方面的影响, 一方面, 点蚀孕育速率增大, 另一方面微晶化后, 其表面膜的自修复性能增强, 点蚀生长速率降低。由于电火花改性表面为细晶结构, 虽然由于晶界的增多, 亚稳态点蚀的萌生位置较多, 但是, 由于电火花表面改性层致密度高, Cl-不易侵入涂层内部, 改性层表面形成的氧化铝膜的致密度高、自修复能力强, 表面形成的点蚀坑不易长大, 点蚀生成后立刻进行了再修复, 由图11 可见, 点蚀坑大多在5 ~ 8μm左右, 小于临界核尺寸, 腐蚀方式主要为亚稳态点蚀。
4 结论
1. 电弧喷涂/ 电火花沉积复合涂层试样的自腐蚀电位Ecorr= - 1. 33 V, 较AZ91D镁合金基体和电弧喷涂铝涂层试样分别正移约280, 40 m V, 腐蚀倾向性降低; 点蚀电位为- 0. 704 V, 较电弧喷涂铝涂层试样提高约60 m V, 点蚀敏感性降低;电弧喷涂铝涂层试样的ipass= 4. 6 × 10- 3A·cm- 2, 电弧喷涂/电火花沉积处理试样的ipass= 3. 2 × 10- 5A·cm- 2, 经电火花表面改性后, 涂层钝化膜自修复能力大幅增强。
2. 在3. 5% Na Cl溶液中, 喷涂铝层钝化膜的点蚀孕育速率跟点蚀生长速率都很大, 经36 h浸泡试验后, 电弧喷涂铝涂层试样表面出现直径达150 μm的点蚀坑; 电火花表面改性处理后, 电火花沉积层氧化铝膜自修复性能强、点蚀生长速率小, 复合涂层表面仅出现直径约5 ~ 8 μm的点蚀坑, 小于临界核尺寸, 涂层发生的主要为亚稳态点蚀。
参考文献
[1] Mordike B L, Ebert T.Magnesium properties-applications-potential[J].Material Science and Engineering A, 2001, 302:37.
[2] Shi W F, Zhou K.The present situation and prospects of the development and application of magnesium alloy in our country[J].Automobile Technology&Material, 2004, (6) :32. (史文芳, 周昆.我国镁合金的开发应用现状及展望[J].汽车工艺与材料, 2004, (6) :32.)
[3] Gray J E, Luan B.Protective coatings on magnesium and its alloys-a critical review[J].Journal of Alloys and Compounds, 2002, 336:88.
[4] Huang M H, Li X G, Zhang K, Li Y J, Ma M L, Zhang Y C.High-temperature diffusion dynamics of EW75magnesium alloy[J].Chinese Journal Rare Metals, 2012, 36 (1) :13. (黄未华, 李兴刚, 张奎, 李永军, 马鸣龙, 张玉春.EW75镁合金高温扩散动力学研究[J].稀有金属, 2012, 36 (1) :13.)
[5] Chao Y J, Liu S G, Dai Y B, Su M, Li J, Sang J P.The microstructure and abrasion resistance of high velocity arc spraying composite FeMnCrNiAl/Cr3C2coatings containing rare earth[J].Transactions of Materials and Heat Treatment, 2012, 33 (3) :137. (晁拥军, 刘少光, 戴炎彬, 苏茂, 郦剑, 桑劲鹏.高速电弧喷涂含稀土FeMnCrNiAl/Cr3C2复合涂层的组织与耐磨性能[J].材料热处理学报, 2012, 33 (3) :137.)
[6] Minnamari Vippol, Samppa Ahmaniemi.Aluminum phosphate sealed alumina coating:characterization of microstructure[J].Materials Science and Engnieering, 2002, A323:1.
[7] Chen C J.ESD Surface Processing Technology[M].Peking:Machinery Industry Press, 2011.1. (陈长军.电火花表面加工新技术[M].北京:机械工业出版社, 2011.1.)
[8] Su Y Z.The Research of ESD Surface Alloying of Magnesium Alloy[D].Wuhan:Wuhan University of Science and Technology, 2011.1. (苏衍战.镁合金电火花表面合金化研究[D].武汉:武汉科技大学, 2011.1.)
[9] Chen W W, Zhu Y, Kang H, Qu P.The research status of ESD deposition technology[J].Welding, 2006, (5) :21. (陈伟伟, 朱颖, 康慧, 曲平.电火花沉积技术国内外研究现状[J].焊接, 2006, (5) :21.)
[10] Zhang H R.The Corrosion Behavior of AZ91D in Solution[D].Lanzhou:Lanzhou University of Technology, 2004.13. (张汗茹.AZ91D在溶液中的腐蚀行为[D].兰州:兰州理工大学, 2004.13.)
[11] Ma K, Sun D Q, Xuan Z Z.The analysis of microstructure and interface of arc sprayed aluminum coating on magnesium alloy surface[J].Welding Journal, 2008, 29 (12) :89. (马凯, 孙大千, 宣兆志.镁合金表面电弧喷铝层的微观结构及界面分析[J].焊接学报, 2008, 29 (12) :89.)
[12] Liu D X.Corrosion and Protection of Material[M].Xi'an:Northwestern Polytechnical University Press, 2005.80. (刘道新.材料的腐蚀与防护[M].西安:西北工业大学出版社, 2005.80.)
[13] Xu L X, Hu J, Geng L, Yao Z K.The pitting corrosion behavior of aluminum[J].Aerospace Materials&Technology, 2002, (2) :21. (徐丽新, 胡津, 耿林, 姚忠凯.铝的点蚀行为[J].宇航材料工艺, 2002, (2) :21.)
[14] Gumbel E J.Statistics of Extremes[M].New York:Columbia University Press, 1957.218.
[15] Wang W F, Wang M C, Sun F J, Zheng Y G, Jiao J M.Microstructure and cavitation erosion characteristics of Al-Si alloy coating prepared by electrospark deposition[J].Surface and Coating Technology, 2008, 202 (21) :5116.
[16] Wei L Y, Meng G Z, Zhang T, Shao Y W, Wang F H.The affect of microcrystalline on aluminum pitting behavior[J].Corrosion Science and Protection Technology, 2009, (2) :155. (魏立艳, 孟国哲, 张涛, 邵亚薇, 王福会.微晶化对纯铝点蚀行为的影响[J].腐蚀科学与防护技术, 2009, (2) :155.)