DOI: 10.11817/j.issn.1672-7207.2020.09.007

编织纤维金属层板成形性能及充液成形工艺分析
李磊1,郎利辉1,HAMZA Blala1,王洪锋2,曹兴龙2
(1. 北京航空航天大学 机械工程及自动化学院,北京,100191;
2. 中国人民解放军93175部队,吉林 长春,130000)
摘要:为了解半固化工艺下不同编织方式的纤维金属层板力学及成形性能,进一步优化半固化纤维金属层板充液成形工艺,通过拉伸试验,对半固化、固化工艺下不同铺层角度的平纹和破斜纹编织纤维金属层板进行力学性能测试,并通过充液成形试验验证工艺的可行性。研究结果表明:半固化工艺可以使编织纤维金属层板在与纤维成45°方向上具有最佳的成形性能,而在0°方向上成形性能提升有限。固化后的编织纤维金属层板具有更高的强度,半固化纤维金属层板的最优压边间隙选用与纤维金属层板板厚一致较为合理,这可能是由于中间层预浸料弹性性质原因。当压边间隙为1.2 mm,液室压力为10 MPa时,可以得到无缺陷的筒形件。
关键词:编织纤维金属层板;充液成形;拉伸性能;压边间隙;液室压力;可行性分析
中图分类号:TG394 文献标志码:A 开放科学(资源服务)标识码(OSID)
文章编号:1672-7207(2020)09-2422-08
Analysis of forming properties and hydroforming process of braided fiber metal laminates
LI Lei1, LANG Lihui1, HAMZA Blala1, WANG Hongfeng2, CAO Xinglong2
(1. School of Mechanical Engineering and Automation, Beihang University, Beijing 100191, China;
2. Unit 93175, People's Liberation Army, Changchun 130000, China)
Abstract: In order to understand the mechanics and forming properties of fiber metal laminates (FMLs) with different weaving pattern fiber during semi-cured process, and further optimize the hydroforming process of semi-cured FMLs, the mechanical properties of plain and twill braided FMLs with different layer angles during semi-cured and cured processes were tested through tensile tests. The feasibility was verified by the hydroforming experiment. The results show that the semi-cured process can make different braided FMLs to have better formability in the 45° direction with the fiber, while the formability in the 0° direction is limited. And the cured laminates have higher strength. It is reasonable to choose the optimal blank-holding clearance of the semi-cured process consistent with the same thickness of the FMLs, which may be due to the elastic nature of the intermediate layer prepreg. When the blank holder clearance is 1.2 mm and the cavity pressure is 10 MPa, the non-defective cup parts can be obtained during the semi-cured process.
Key words: braided fiber metal laminate; hydroforming; tensile test; blank-holder clearance; cavity pressure; feasibility analysis
近几十年来,随着航天技术和电动汽车工业的不断发展,结构材料要求轻量化、高强度、耐冲击、抗疲劳和低成本。纤维金属层板(fiber metal laminates, FMLs)是一种由金属与纤维增强树脂组成的超混杂材料,结合了金属的抗冲击与纤维增强材料的高强度的优点。与单层金属材料相比,FMLs具有高比强度、抗疲劳、抗冲击、高断裂韧性、耐火性好和易制造与维修等优点[1-4]。到目前为止,纤维金属层板已经发展出4代,包括凯夫拉纤维增强铝合金层板(ARALL),玻璃纤维增强铝合金层板(GLARE),碳纤维增强铝合金层板(CARALL)和碳纤维增强钛合金层板(TIGR)。由于铝合金与凯夫拉纤维的热膨胀系数不同,第一代ARALL纤维的层间应力较大,容易发生层间破坏。荷兰Fokker公司开发了第二代GLARE层板,凭借优异的抗疲劳性能、较高的损伤容限和抗冲击性能,一跃发展成为使用最为广泛的一类纤维金属层板,并在空客A380飞机上大范围应用[2]。为了进一步提高FMLs的性能,研究人员开发了高强度碳纤维代替玻璃纤维的CARALL层板。然而,铝和碳之间的电化学腐蚀影响了这些层合板的广泛应用。TIGR层板没有腐蚀问题,并能进一步提高综合性能,已应用于B787的机翼前缘和机身蒙皮,但由于钛合金与树脂的胶接问题,很难控制其良品率。目前的纤维金属层板主要应用于大型航空航天大型覆盖件,如机翼前缘和机身蒙皮件,但小尺寸和复杂形状零件的应用还比较少。这是因为真空罐工艺和人工铺层的成本较高,而且真空罐的压力不足以成形小型复杂结构件[5]。为了减少制造成本,国外许多研究者对纤维金属层板的热拉深成形进行研究。MOSSE等[6-7]研究了温度和冲压工艺参数对聚丙基FMLs成形性的影响,发现FMLs相比单层金属板具有潜在的成形优势;还分析了影响FMLs冲压成形中产生形状误差和分层的因素,压边力、进给速度和刀具半径均会影响FMLs的回弹。GRESHAM等[8]发现FMLs成形过程中温度和压边力对起皱和断裂的影响不同,提高温度对FMLs成形有积极影响。ZAFAR等[9-10]通过开发一种三层板同时成形工艺,然后再进行铺贴固化制备成形FMLs层板零件,缩短了制备板料时间,但是还需要手工铺贴。国内对于纤维金属层板的成形性研究主要针对单曲率大面积零件研究较多,如:华小歌等[11]通过研究玻璃纤维铝锂合金复合层板的自成形工艺发现层板可以成形贴模度较高的大曲率零件;陆一等[12]进行了热塑性纤维金属层板喷丸成形的残余应力研究;陶杰等[13]综合介绍了新型纤维金属层板、失效理论和成形技术等。本文作者对半固化与固化不同编织方式制备的纤维金属层板进行拉伸试验,分析不同制备工艺纤维金属层板在不同方向上的失效形式和成形性能,并选用不同工艺参数进行半固化充液成形对比试验,对压边间隙和液室压力工艺参数进行分析,验证半固化编织纤维金属层板充液成形的可行性,为进一步研究半固化纤维金属层板充液成形工艺提供依据。
1 试验材料及方法
1.1 试验材料
制备纤维金属层板选用的铝合金为2024-T3,厚度为0.5 mm,标称化学成分如表1所示。根据ASTM E8试验标准测得力学性能如表2所示。
表1 2024-T3铝合金化学成分(质量分数)
Table 1 Chemical composition of aluminum alloy 2024-T3 %

表2 2024-T3铝合金材料力学性能
Table 2 Mechanical properties of aluminum alloy 2024-T3
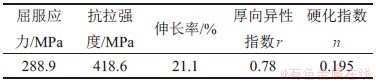
选用山东光威公司生产的玻璃纤维预浸料。型号分别为WP-9011的平纹预浸料和 218号的破斜纹预浸料,厚度分别为0.20 mm和0.29 mm,树脂质量分数为40%和36%,纤维单位面积质量为204 g/m2和220 g/m2。平纹:经向8根/cm,纬向7根/cm;斜纹:经向20根/cm,纬向10根/cm。表3所示为厂商提供预浸料性能参数。由于平纹和破斜纹预浸料的编织方式不同,2种预浸料的变形能力有较大区别,所以,选用平纹和破斜纹2种编织方式。
表3 预浸料力学性能
Table 3 Mechanical properties of prepreg
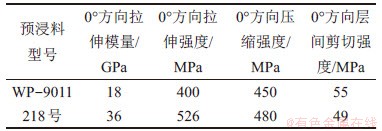
1.2 试验方法
所有试验件都采用固化和半固化2种工艺进行制备。固化工艺是将铝合金板进行表面处理后,将预浸料铺贴在两层铝合金板厚度方向中央,然后在真空袋中以0.1 Pa的真空度以一定的升温曲线进行固化[14],如图1所示。半固化工艺是在层板进行铺贴后,在真空袋中加压0.5 h直接进行试验。半固化工艺条件下的测试旨在探究纤维金属层板在此种工艺条件下成形的可能性。
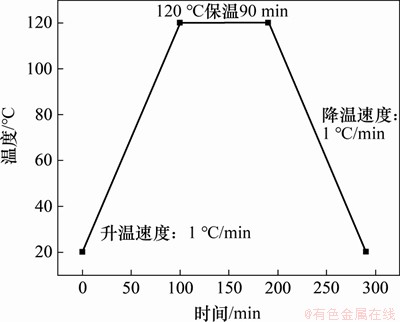
图1 真空固化工艺时间-温度曲线
Fig. 1 Vacuum curing process time-temperature curve
1.2.1 拉伸试件
根据ASTM D3039(2000)测试标准,采用长×宽为175 mm×25 mm的矩形试样进行不同中间层纤维预浸料FMLs的拉伸试验。铝层的轧制方向沿试件长度方向。不同种类纤维预浸料的铺设方向都参考铝层的轧制方向,如0°表示预浸料的经纱纤维方向与轧制方向相同,90°表示预浸料的纤维方向与轧制方向垂直(如图2所示)。试样均采用2/1结构,中层为玻璃纤维预浸料,分别沿不同方向进行拉伸试验。试验设置如表4所示。试验在CTM 100G通用试验机上进行,测试十字头速度设定为2 mm/min。在试验过程中,测定了拉伸强度、弹性模量和断裂伸长率。
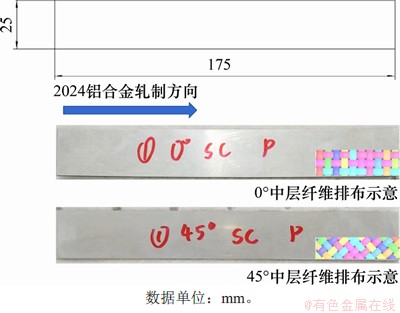
图2 拉伸试验试件
Fig. 2 Facilities of vacuum curing process
表4 拉伸试样设置
Table 4 Tensile specimen setup
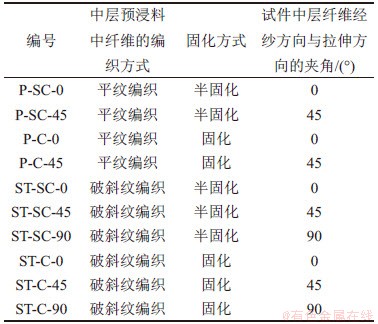
1.2.2 充液成形试验
选用半固化平纹和破斜纹FMLs进行被动式充液拉深试验。试验原理如图3(a)所示,凸模形状为圆柱形,如图3(b)所示。圆柱形凸模半径为40 mm;圆柱形凸模圆角为8 mm;凹模圆角半径为10 mm;凹模半径为42.5 mm。选用直径为140 mm的圆形板料进行试验。试验条件如表5所示。目标成形深度为25 mm。液室压力分别为0,5,10和15 MPa时进行试验。
表5 充液拉深试验条件
Table 5 Experimental conditions for hydroforming
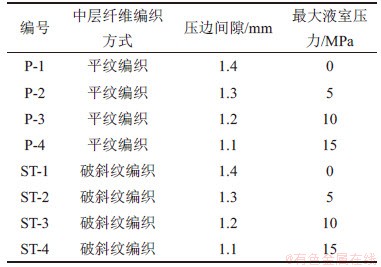
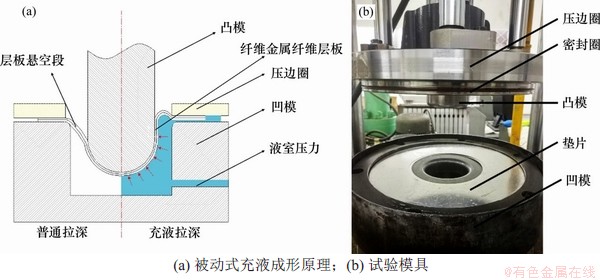
图3 充液成形试验
Fig. 3 Hydroforming experiment
2 结果和讨论
2.1 编织纤维金属层板半固化条件下的性能试验
图4所示为半固化和固化2种条件下制备的平纹FMLs的应力-应变曲线。由于平纹编织为正交各向异性材料,其在0°方向和90°方向的性能相同,所以选取0°方向和45°方向进行拉伸试验。从图4可以明显地观察到在弹性段半固化和固化的FMLs斜率基本一致,比2024-T3的小。这是因为无论是半固化还是固化FMLs,其中都加入了预浸料,而预浸料的弹性模量(18 GPa)要低于2024-T3铝合金的弹性模量(试验测得弹性模量为65 GPa),这符合混合率[15]的计算结果。从图4(a)可以清楚地观察到在塑性段半固化平纹FMLs相比铝合金发生了明显的应力下降,但是伸长率有少量增大。值得注意的是0°半固化平纹FMLs曲线在6.04%应变处发生了明显的下降,然后与45°方向的曲线基本重合。这说明在此时0°纤维发生了断裂,随后只由半固化树脂与外层铝板承担载荷并继续发生塑形变形。45°半固化平纹FMLs的中层编织纤维由于编织结构的原因而发生偏转,在到达最大剪切角之前只能承担少部分载荷[16],这也解释了45°方向拉伸应力相比于0°方向拉伸应力略高的原因,这是纤维之间的扭转造成的。在图4(b)中,观察到与半固化平纹FMLs拉伸曲线类似,但是0°方向和45°方向的抗拉强度都有明显增强,分别高于半固化抗拉强度的14.5%与13.7%。半固化工艺条件下45°FMLs的伸长率提升明显,固化条件下伸长率:0°方向时为6.8%,45°方向时为13.8%;而半固化状态下伸长率:0°方向时为6.3%,45°方向时为22.2%。可见,半固化工艺在45°方向上有利于纤维金属层板的成形,而固化工艺层板的强度更高。
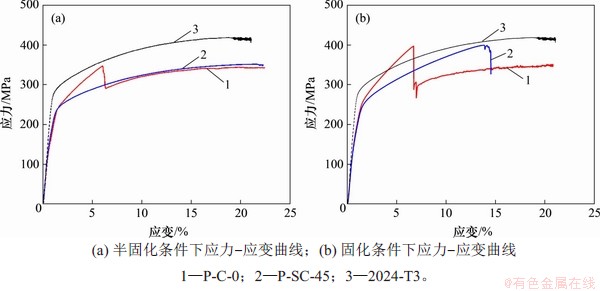
图4 平纹纤维金属层板半固化与固化应力-应变曲线
Fig. 4 Stress-strain curves of plain FMLs under semi-cured and cured condition
图5所示为半固化和固化2种条件下制备的破斜纹FMLs的应力-应变曲线。由于破斜纹编织方式的原因,0°方向和90°方向的性能不同,所以,选取0°方向,45°方向和90°方向进行拉伸试验。从图5(a)可以看到破斜纹的曲线的规律与平纹曲线相似,但是值得注意的是0°方向的伸长率相比于平纹FMLs的伸长率有所降低。这是因为与平纹预浸料不同,在0°方向上相比90°方向的纤维束更多,更加不易变形。而在45°方向,半固化条件下的破斜纹FMLs抗拉强度比平纹的有所下降,这是因为斜纹编织方式更有利于纤维束的剪切形变,最大剪切角更大。另外,在90°方向纤维束的数量只有0°方向的一半,半固化的树脂与铝合金承担载荷的比例增大,所以,与45°方向的曲线基本重合。在45°和90°这2个方向,伸长率达到21.9%和23.0%,这与平纹预浸料45°方向的伸长率基本相同。图5(b)所示为固化后的破斜纹FMLs的应力-应变曲线,0°,45°和90°方向的抗拉强度比半固化层板的分别提高30.2%,15.1%和4.4%。固化条件下伸长率如下:0°方向时为5.2%,45°方向时为10.8%,90°方向时为20.7%。半固化状态下伸长率如下:0°方向时为3.6%,45°方向时为21.9%,90°方向时为23.0%。破斜纹预浸料与平纹预浸料在固化和半固化拉伸曲线在0°和45°方向表现相似,但是在90°方向有较大不同,拉伸性能与45°方向时相似。
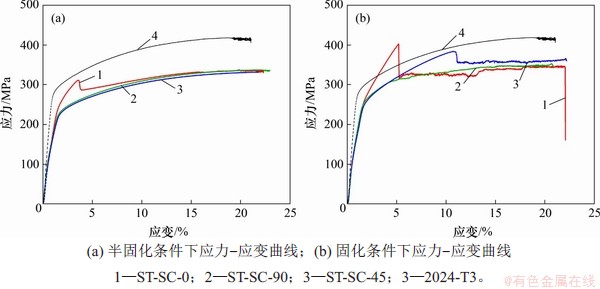
图5 破斜纹纤维金属层板固化与半固化应力-应变曲线
Fig. 5 Stress-strain curves of satin FMLs under semi-cured and cured condition
根据拉伸试验结果,半固化工艺条件下的编织纤维金属层板在与纤维成45°方向上伸长率相比固化工艺提高显著,在0°方向上与固化后的伸长率相似。所以,半固化工艺可以根据预浸料铺层方向提高FMLs的成形性能,成形后再进行固化以提高成形性和零件强度。通过充液成形试验进一步验证其成形性能。
2.2 半固化充液成形
图6所示为在不同工艺参数下,半固化平纹纤维金属层板充液成形试件对比。在图6(a)和图6(b)中观察到明显起皱现象。从下方的放大图可以看出,无液室压力的试件除法兰区域外直壁区也明显发生了起皱现象。由于起皱严重,层板发生分层破裂,如图6(a)中黄色箭头所示。而在图6(b)中,P-2试件只有在法兰区域观察到起皱现象,但是在直壁区域并未发生明显的起皱现象,这说明液室压力对于纤维金属层板的分层和起皱有一定的抑制作用。在图6(c)和(d)中,起皱现象明显减少,试件凸模圆角处均发生破裂,如黄色箭头所示。这种变化可以归因于压边间隙减小,但是值得注意的是图6(c)所示P-3的压边间隙为1.2 mm,试件层板的厚度同为1.2 mm,压边间隙与板厚的一致。而P-3的成形深度为21.2 mm,P-4为18.3 mm。压边间隙为1.2 mm,液室压力10 MPa为这组充液成形试验的最优工艺参数。最优压边间隙与板料厚度一致,不同于传统充液成形工艺中最优压边间隙为1.1~1.2倍的板料厚度这一规律。这是由于中间层预浸料有一定的弹性形变空间,在液室压力的作用下,板料的厚度根据液室压力发生动态变化,因此造成了这种现象。如图6下方放大图红圈所示,从P-1到P-4试件,中间层凸耳由大变小,这是层板各向异性所致。在无液室压力或液室压力较小时,各层之间的黏结作用不够承载变形力,所以,金属层与纤维层变化不一致。随着压边力和液室压力增大,金属层与预浸料之间的内聚力增大,使变形更协调。在10 MPa左右的液室压力下,纤维层板的内外层材料应变分布更加均匀,使不同方向的预浸料与铝层变形更加协调,也避免了分层情况的发生。
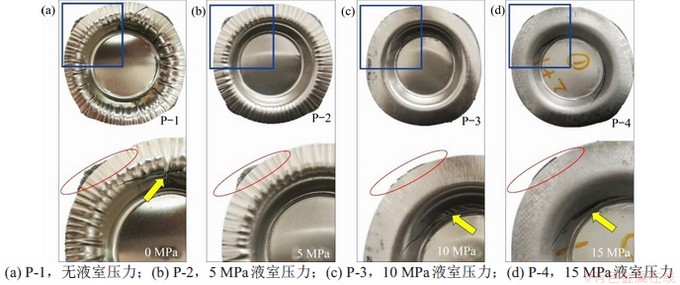
图6 半固化平纹纤维金属层板不同液室压力下的充液成形试件
Fig. 6 Hydroforming specimens of semi-cured plain FMLs under different cavity pressures
图7所示为在不同液室压力下,半固化破斜纹纤维金属层板充液成形试件对比。与平纹预浸料不同的是,层板只在无液室压力条件下发生了法兰起皱现象,此时的压边间隙为1.4 mm;而随着液室压力增大和压边间隙减小,法兰区起皱现象消失,特别是在压边间隙为1.2 mm,压力为10 MPa时,成形深度达到25 mm并未发生起皱破裂现象,破斜纹纤维金属层板厚度为1.29 mm。当压边间隙为1.1 mm,液室压力增大到15 MPa时,直壁区发生破裂。破斜纹的凸耳现象也不如平纹预浸料明显,这可能是压边间隙相对于层板厚度比较小造成的。
根据上述2组半固化平纹预浸料充液成形试验结果可以看出:压边间隙选用等于或略小于纤维金属层板的实际厚度可以得到较为理想的成形零件,最优液室压力为10 MPa。
2.3 固化充液成形
为了对比半固化工艺与固化工艺,图8所示为固化后的破斜纹纤维金属层板在ST-3试验条件下成形试验件。分别成形2次,深度分别为10 mm和20 mm,并查看固化层板成形情况。在试件成形至10 mm深时(如图8(a)所示),试件凹模圆角处发现已经开始起皱,并且部分法兰已经分层;当成形至14.8 mm时(如图8(b)所示),试件发生破裂。由于分层严重,内层铝合金法向贴模力不足,导致发生严重起皱,凸模圆角处发生破裂。由此可见,固化后的层板无法有效进行充液成形。
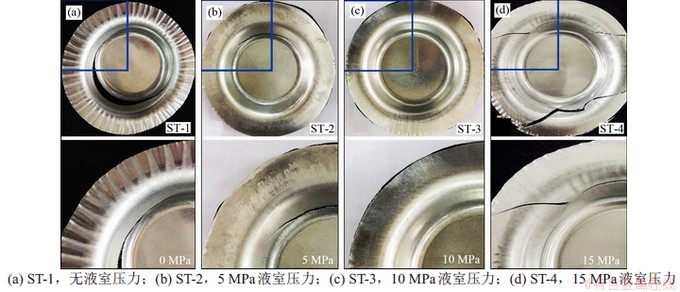
图7 半固化破斜纹纤维金属层板不同液室压力下的充液成形试件
Fig. 7 Hydroforming specimens of semi-cured satin FMLs under different cavity pressures
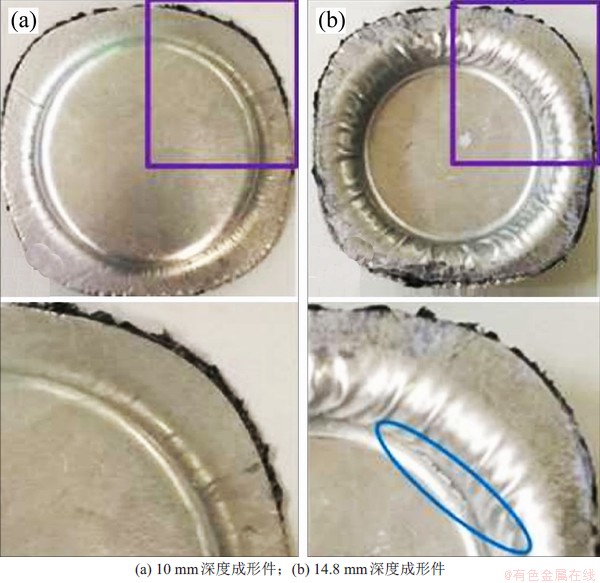
图8 固化破斜纹纤维金属层板充液成形试件
Fig. 8 Hydroforming specimens of cured satin FMLs
3 结论
1) 编织纤维金属层板不同方向的拉伸性能有较大差异,是明显的各向异性材料。通过拉伸试验对比半固化与固化后的试件,证明了半固化工艺制备的纤维金属层板在特定方向有更好的成形性能。
2) 固化后的纤维金属层板抗拉强度明显增强,可以通过成形后再固化的方式得到性能更好的零件。
3) 半固化编织纤维金属层板充液成形制造多曲率小型零件是可行的。最优压边间隙选用等于或略小于层板厚度,最大液室压力为10 MPa,可以成形无缺陷零件。
4) 固化的编织纤维金属层板难以成形合格零件。
参考文献:
[1] SINMAZCELIK T, AVCU E, BORA M O, et al. A review: fibre metal laminates, background, bonding types and applied test methods[J]. Materials & Design, 2011, 32(7): 3671-3685.
[2] 王永贵, 梁宪珠. 纤维金属层板技术与大型飞机[C]// 第十八届玻璃钢/复合材料学术年会论文集. 北京, 2010: 146-150.
WANG Yonggui, LANG Xianzhu. Fiber metal laminates and large airplane[C]// Proceedings of the 18th annual conference on fiberglass/composites. Beijing, 2010: 146-150.
[3] 刘建光, 张嘉振, 岳广全, 等. 纤维金属层板曲面零件成形技术研究[J]. 航空制造技术, 2019, 62(16): 46-52.
LIU Jianguang, ZHANG Jiazhen, YUE Guangquan, et al. Research on forming technology of fiber metal laminate curved parts[J]. Aeronautical Manufacturing Technology, 2019, 62(16): 46-52.
[4] 郑兴伟, 卢佳, 庄欣, 等. 航空用玻璃纤维铝合金层板成形技术研究进展[J]. 材料导报, 2018, 32(S2): 413-418.
ZHENG Xingwei, LU Jia, ZHUANG Xin, et al. A review on the forming technology of aerospace glass-reinforced aluminum laminates[J]. Materials Review, 2018, 32(S2): 413-418.
[5] 曾一畔, 郎利辉, 刘世琛, 等. 半固化GLARE层板橡皮垫成形工艺过程及其数值模拟研究[J]. 锻压技术, 2018, 43(11): 66-71.
ZENG Yipan, LANG Lihui, LIU Shichen, et al. Investigation on rubber pad forming process and its numerical simulation for semi-cured GLARE laminates[J]. Forging & Stamping Technology, 2018, 43(11): 66-71.
[6] MOSSE L, COMPSTON P, CANTWELL W J, et al. The effect of process temperature on the formability of polypropylene based fibre-metal laminates[J]. Composites Part A: Applied Science and Manufacturing, 2005, 36(8): 1158-1166.
[7] MOSSE L, COMPSTON P, CANTWELL W J, et al. Stamp forming of polypropylene based fibre-metal laminates: the effect of process variables on formability[J]. Journal of Materials Processing Technology, 2006, 172(2): 163-168.
[8] GRESHAM J, CANTWELL W, CARDEW-HALL M J, et al. Drawing behaviour of metal-composite sandwich structures[J]. Composite Structures, 2006, 75(1/2/3/4): 305-312.
[9] ZAFAR R, LANG Lihui, ZHANG Rongjing. Analysis of hydro-mechanical deep drawing and the effects of cavity pressure on quality of simultaneously formed three-layer Al alloy parts[J]. The International Journal of Advanced Manufacturing Technology, 2015, 80(9/10/11/12): 2117-2128.
[10] ZHANG Rongjing, LANG Lihui, ZAFAR R, et al. Investigation into thinning and spring back of multilayer metal forming using hydro-mechanical deep drawing (HMDD) for lightweight parts[J]. The International Journal of Advanced Manufacturing Technology, 2016, 82(5/6/7/8): 817-826.
[11] 华小歌, 李华冠, 陆一, 等. 玻璃纤维-铝锂合金层板机翼前缘结构的成型工艺研究[J]. 航空制造技术, 2017, 60(16): 58-63.
HUA Xiaoge, LI Huaguan, LU Yi, et al. Forming process of glass fiber/aluminum-lithium laminates leading edge structure[J]. Aeronautical Manufacturing Technology, 2017, 60(16): 58-63.
[12] 陆一. GFRP/Al-Li层板喷丸成形及其在交变热场下的残余应力研究[D]. 南京:南京航空航天大学材料科学与技术学院, 2019: 36-69.
LU Yi. Residual stresses of GFRP/Al-Li laminates after shot-peening forming and during alternating thermal field[D]. Nanjing: Nanjing University of Aeronautics and Astronautics. College of Materials Science and Technology, 2019: 36-69.
[13] 陶杰, 李华冠, 潘蕾, 等. 纤维金属层板的研究与发展趋势[J]. 南京航空航天大学学报, 2015, 47(5): 626-636.
TAO Jie, LI Huaguan, PAN Lei, et al. Review on research and development of fiber metal laminates[J]. Journal of Nanjing University of Aeronautics & Astronautics, 2015, 47(5): 626-636.
[14] 介苏朋. 纤维金属层板(FMLs)结构制造方法研究[D]. 西安: 西北工业大学材料学院, 2006: 5-14.
JIE Supeng. Investigation on fabrication method of fiber metal laminates(FMLs)[D]. Xi′an: Northwestern Polytechnical University. College of Materials, 2006: 5-14.
[15] STARIKOV R. Assessment of impact response of fiber metal laminates[J]. International Journal of Impact Engineering, 2013, 59: 38-45.
[16] ZHANG Q, CAI J, GAO Q. Simulation and experimental study on thermal deep drawing of carbon fiber woven composites[J]. Journal of Materials Processing Technology, 2014, 214(4): 802-810.
(编辑 杨幼平)
收稿日期: 2020 -04 -01; 修回日期: 2020 -04 -30
基金项目(Foundation item):国家自然科学基金资助项目(51675029) (Project(51675029) supported by the National Natural Science Foundation of China)
通信作者:郎利辉,博士(后),教授,从事高温高压充液成形研究;E-mail:lang@buaa.edu.cn