J. Cent. South Univ. Technol. (2011) 18: 932-939
DOI: 10.1007/s11771-011-0783-6
Flexural response of reinforced concrete beams strengthened with post-poured ultra high toughness cementitious composites layer
WANG Nan(王楠)1, 2, XU Shi-lang(徐世烺)1
1. State Key Laboratory of Coastal and Offshore Engineering, Dalian University of Technology, Dalian 116024, China;
2. Dalian Institute of Building Scientific Research & Design Stock Co., Ltd., Dalian 116021, China
? Central South University Press and Springer-Verlag Berlin Heidelberg 2011
Abstract: Four-point bending tests were conducted up to failure on eleven reinforced concrete (RC) beams and strengthening beams to study the effectiveness of externally pouring ultra high toughness cementitious composites (UHTCC) on improving the flexural behavior of existing RC beams. The strengthening materials included UHTCC and high strength grade concrete. The parameters, such as thickness and length of strengthening layer and reinforcement in post-poured layer, were analyzed. The flexural behavior, failure mode and crack propagation of composite beams were investigated. The test results show that the strengthening layer improves the cracking and ultimate load by increasing the cross section area. Introducing UHTCC material into strengthening not only improves the bearing capacity of the original specimens, but also disperses larger cracks in upper concrete into multiple tightly-spaced fine cracks, thus prolonging the appearance of harm surface cracks and increasing the durability of existing structures. Compared with post-poured concrete, UHTCC is more suitable for working together with reinforcement. The load-deflection plots obtained from three-dimensional finite-element model (FEM) analyses are compared with those obtained from the experimental results, and show close correlation.
Key words: ultra high toughness; cementitious composities; strengthening beams; flexural behavior; post-poured layer
1 Introduction
Plain concrete was a brittle material characterized by an extremely weak tensile strength, which had been a problem of a primary concern for structural applications. So the crack in the structure appeared early under the service. It allowed water and other chemical agents, such as chloride ions, oxygen, carbon dioxide, to go through the cover layer and come into contact with the reinforcements, leading to the reinforcement corrosion and rupture. Deterioration of conventional steel reinforcement due to corrosion reduced the service life of reinforced concrete member. Repairing or strengthening was an effective and economical way to prolong the working life of existing structures. With the development and application of new material and technology, the method has achieved great progress in various countries.
Recently, a kind of new fiber reinforced cement matrix composite has raised some relevant researchers’ interests owing to its remarkable tensile performance and excellent crack limit behavior. This type of material was named ultra high toughness cementitious composites (UHTCC). The material was proposed by LI and LEUNG and named engineered cementitious composites (ECC) in their research [1]. In material design, the interaction among fiber, matrix and interface was emphasized and linked by a micromechanics model such that a couple of criteria for tension strain hardening, i.e. first cracking stress criterion and steady-state cracking criterion, were satisfied in the case of low fiber (mainly PVA or PE fiber) volume fraction of no more than 2% [1-3]. As the UHTCC cracked, the load was transferred by fiber bridging from this crack plane back into brittle matrix and caused the formation of another crack, which might initiate from another matrix defect site. Repetition of this process created the well-known phenomenon of multiple cracking. The material had significant tensile strain capacity of normally up to 3% and performed tension strain hardening after first cracking. It avoided the strain localization and macro single crack pattern of traditional cement-based materials. And the material had superior impermeability, freeze-thaw and corrosion resistance [4-7]. It had also been found that the cracked UHTCC exhibited nearly the same permeability as sound concrete, even when strained in tension [8].
By using the principle and method of composite structure, pouring UHTCC on the external surface to limit crack and improve load capacity offered a new way of strengthening the existing concrete structure. A number of full-scale applications of UHTCC had been carried out in some countries. The notable repair applications included the Mitaka Dam in Japan, Shinkansen Viauct in Japan, runway and parking of Zurich Airport in Switzerland and deck of simply supported steel beam bridge in Michigan [9-11]. However, the recent researches mainly concentrated on material properties of UHTCC and engineering effect of full-scale experiment. There were few related reports on the mechanical performance of composite members, especially with existing concrete members. In this work, the flexural behaviors of reinforced concrete (RC) beam strengthened with UHTCC were investigated, which was different from the traditional strengthening materials. The influences of different strengthening layer thickness, length and addition of reinforcement in post-poured layer on the flexural behaviors were considered. The flexural behavior, failure mode and crack propagation of composite beams were also investigated.
2 Experimental program
2.1 Specimen geometry and test setup
A total of eleven beams were cast and cured under laboratory conditions, which included one reinforced concrete (RC) control beam, six RC beams strengthened with post-poured UHTCC and four RC beams strengthened with post-poured high strength grade concrete. All RC beams were of the same dimensions (1 400 mm × 120 mm × 200 mm), and had the same concrete grade and reinforcement arrangement. Each concrete beam was reinforced with three 8 mm-diameter steel bars for tension and two 6.5 mm-diameter steel bars for compression along 6.5 mm-diameter bars at spacing of 60 mm center-to-center for shear reinforcement. The longitudinal tensile reinforcing bars were hooked at the ends. The clear concrete covers of 20 mm for tensile and compressive reinforcement were provided. The details of the test specimen are shown in Fig.1.
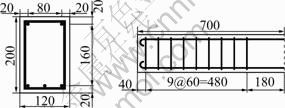
Fig.1 Main dimensions of RC beam (Unit: mm)
When the reinforced concrete beam attained, approximately, 28 days of age, the tension face of the concrete surface was made rough to expose the coarse aggregate by artificial chiseling with a toothed grinder and cleaned with an air compressor to remove all dirt and debris. The average unevenness measured with sand replacement was about 2 mm. Before pouring UHTCC material, it was important to keep the rough face of concrete naturally saturated.
Cubic concrete specimens of 150 mm high were cast at the same time as the beams. The average cube strength in compression was 32.3 MPa, which was evaluated by tests on three cubic specimens. The yield strength of steel bars used as tensile reinforcement was determined by standard tensile test; the average values were 427 MPa for d8 mm steel bars, and 400 MPa for d6 mm steel bars. The proportioning of UHTCC was from group N2 in Ref.[12], and the material properties of it are reported in Table 1. The average cube strength of high strength grade concrete was 45.5 MPa in compression. The RC beam was designated as Con. The RC beams strengthened with UHTCC or reinforced UHTCC were fabricated (CON-CB 1-4 and UH-CB 1-6). The details of the beams fabricated for testing are presented in Table 2.
Table 1 Properties of UHTCC
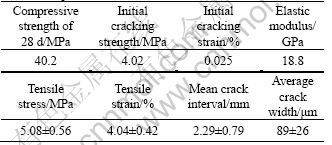
Table 2 Test parameters of beam specimens
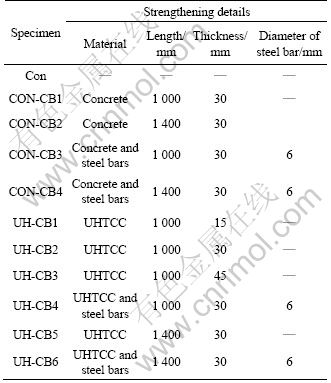
2.2 Testing procedures and test results
The test setup is shown in Figs.2(a) and (b). The hydraulic testing machine with a capacity of 5 000 kN was used, and the applied load was transmitted continuously through a spreader beam with two 400 mm- spaced rollers. Load was from zero to failure, and multi-stage loading was employed. The applied load was measured by the load cell. The mid-point deflections were measured using linear variable differential transducers (LVDTs). The strain gauges were pasted on the lateral and tensile faces of specimens. The load cell, LVDTs, and train gauges were connected through a data acquisition system, Integrated Measurement & Control (IMC), to a computer and the data were recorded and stored in the computer.
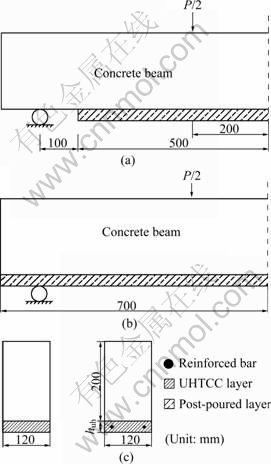
Fig.2 Strengthening method and test set-up: (a) Locally strengthening beam; (b) Entirely strengthening beam; (c) Cross- section after strengthening
2.3 Strain distribution along beam depth
Figure 3 presents the measured strain distribution along the beam depth at various load levels, taking the beams UH-CB2, UH-CB4 and UH-CB6 as examples. The strain distribution in concrete and reinforcement layer was nearly proportional to the distance from the neutral axis, and the other test results were also the same. This indicated that the assumption of plane cross section was valid for the RC beams strengthened with post- poured UHTCC and reinforced UHTCC materials. And there was also continuous strain kept at the interface between concrete and post-poured layer.
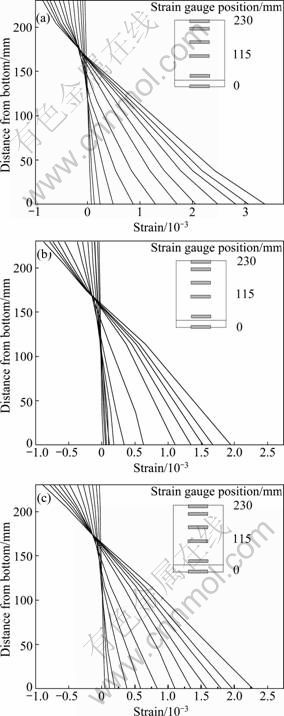
Fig.3 Strain distributions along beam depth: (a) UH-CB2; (c) UH-CB4; (c) UH-CB6
3 Test results and discussion
3.1 Flexural behavior and strengthening effect
The control beam (Con) exhibited a typical flexural failure similar to that of conventional RC beam. The tension steel in concrete beam reached its yield strength before the compressive strain in concrete reached 0.003 and the beams failed by crushing of concrete.
All beams strengthened with post-poured layer had better work performance than control beam. The RC beams strengthened with high strength grade concrete improved the initial rigidity, as the cross section of composite beams increased. Due to the shortage of concrete, the failure patterns of locally and entirely strengthening beams (CON-CB1 and CON-CB2) presented brittle characteristics after the tensile surface had cracked. The beams (UH-CB1, UH-CB2 and UH-CB3) locally strengthened with different depth UHTCC layers also had flexural failure, as shown in Fig.4(a). Flexural cracks were observed between the loading points in the above mentioned beams. With the load increasing, the visual flexural cracks became wider and more. Reinforced layer of UHTCC restricted the crack propagation in the concrete beam. As the UHTCC layer thickness increased, the average crack width at the same load level decreased correspondingly. The single crack in concrete beam, which extended to UHTCC layer, would disperse into multiple tightly-spaced cracks. When the concrete crack width was up to 0.7-1.5 mm, the UHTCC cracks in tension remained around 0.07 mm wide. Then the strain of tensile reinforcement was close to the yield value. Meanwhile, UHTCC crack width grew rapidly until the flexural failure occurred. The results showed that UHTCC improved the structural durability by restricting the cover layer cracking obviously, and the load capacity of specimens composed of RC beam and UHTCC increased slightly, about 110%, 113% and 116% of the control beam. No inclined cracks were observed in the ends of strengthened beams (UH-CB1 and UH-CB2). Flexural cracks appeared firstly in the loading process of strengthening beam (UH-CB3), which had 45 mm-deep UHTCC layer. With increasing the load, the concrete crack occurred near the end of the UHTCC layer and extended toward the same side support. However, the inclined cracks propagated more slowly compared with the flexural cracks. The flexural crack remained the main failure cause as the strengthening beams.
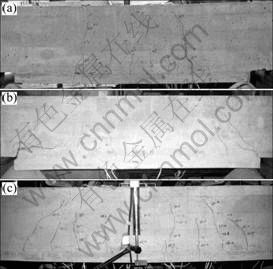
Fig.4 Failure mode of composite specimen
The reinforced layer of the locally strengthening beams (CON-CB3 and UH-CB4) composed of concrete or UHTCC as the matrix and longitudinal reinforcement added. In the test, it was found that the reinforced layer restricted the original structure more effectively and increased the load capacity significantly. Compared with the beams strengthened with concrete or UHTCC materials, the cracking width and space reduced obviously. From the load-deflection curves, it was shown that the strengthening effect of reinforced UHTCC layer was fairly close to that of reinforced concrete. The reinforced bars were still the main bearing body. When there was crack appearing on the tension surface, the corresponding load value of UH-CB4 was more than that of the CON-CB3. Initial cracking along the vertical direction occurred in the mid-span firstly. Due to the addition of tension bars, the rigidity of the reinforcement layer increased correspondingly. At some service load, there were some cracks around the ends of the reinforcement layer. The inclined cracks transferred from the end to the support. The beam strengthened with reinforced UHTCC failed by local debonding the concrete covers of original beam due to the concentrated stress of the layer ends, as shown in Fig.4(b).
The observed failure modes of the globally strengthening beams except CON-CB2 were also flexural failure, as shown in Fig.4(c). The above mentioned specimens failed due to the crushing of the concrete in the compressive zone after the steel bars yielded or the stress of the UHTCC layer reached its ultimate value. The appearance and propagation of the cracks were similar to those of the locally strengthening beams. And there were no interfacial debonding found during the loading. From the comparison of results, it was concluded that UHTCC was more suitable to work together with the reinforced bars than the concrete.
3.2 Crack propagation
The average crack width in the UHTCC was not less than 60 μm until the material reached its ultimate strain under direct tension. So, the visual cracks on the concrete tension zone of the strengthening beams might be found firstly by naked eyes in tests, not in the UHTCC layer. When the concrete cracks extended to the interface between concrete and UHTCC, they were dispersed into a number of finer ones. As shown in Fig.5(a), when the concrete crack width was more than 0.15 mm under the service load, the crack on the bottom face of the strengthening layer remained at 0.02 mm. In addition to the cracks observed by naked eyes, there were still multiple fine cracks which had not been detected on the bottom of the UHTCC layer. After painting the display fluid, it could be shown in Fig.5(b). The crack width was measured with a DJCK-2 measurement instrument, as shown in Fig.5(c). Table 3 lists the maximum crack widths of the concrete and UHTCC and their corresponding loads at different stages of loading history. The results showed that the UHTCC layer restricted the propagation of the strengthening beam cracks effectively to improve the overall working performance. It transformed the major cracks of the concrete beam into multiple harmless fine cracks, and prolonged the appearance of the outer surface harmful cracks.
4 Finite element analyses
4.1 Finite element model
To study the flexural response of all the composite beams, three-dimensional (3D) finite-element models (FEMs) were established to calculate and analyze using a commercial general-purpose FEA software ABAQUS [13-15]. In order to improve the computational efficiency, a half of the composite beam was taken for practical modeling and calculating. The overall diagram of the typical composite beam is shown in Fig.6, taking UH-CB1 as example.

Fig.5 Photos of crack observation: (a) Front view of cracking area; (b) Bottom view of strengthening beam; (c) Enlarged view of UHTCC cracks
Table 3 Test results of beam specimens
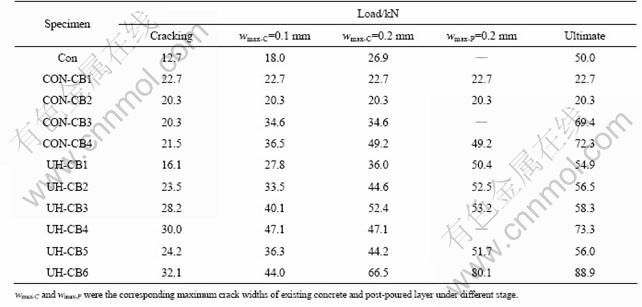
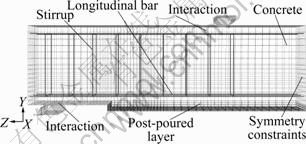
Fig.6 Geometry model of nonlinear analysis
The concrete and UHTCC materials in the beams were generated using three-dimensional eight-node solid brick elements with one-point integration. The steel reinforcement in the beams was modeled by truss elements connected to the nodes of adjacent concrete or UHTCC elements. The embedded element technique was used to specify the steel elements embedded in the concrete or UHTCC elements. ABAQUS searched for the geometric relationships between the nodes of the embedded elements and the host elements. If a node of the embedded element lay within the host element, the translational degrees of freedom at the node were eliminated and the node became an “embedded node”. The translational degrees of freedom of the embedded node were constrained to the interpolated values of the corresponding degrees of freedom of the host element [15].
Loading method and boundary condition in the model were the same as the experiment scheme, as shown in Fig.6. Symmetrical constraints were imposed on the two symmetrical planes of the quarter. Surface-to- surface contact definition between two-way slab, loading plate and supports was divided to two directions for simulating the separation and interaction of the contact surfaces. Normal contact used hard contact, in which the pressure vertical to the contact surface could transfer at the interface completely. And assuming that the surface was frictionless, the tangential force was neglected. The change of specimen thickness caused by artificial chiseling was not considered. The main failure mode in this test of composite beams was bending failure. Therefore, a perfect bond between materials was assumed. Nonlinear iterative solutions were performed until the convergence of force equilibrium and displacement compatibility could be satisfied to obtain the solved results.
4.2 Material parameters
It was important to select an appropriate material model that could closely represent the actual behavior of the physical entity under consideration. ABAQUS/ standard contained a large library of material models, and the ones that represented the material’s behavior within the constraints of the available material property data. The concrete material was assigned the Concrete Damage plasticity model. The model assumed that the uniaxial tensile and compressive response of concrete was characterized by damaged plasticity. The elasto-plastic material property with isotropic strain hardening was selected to simulate the material behaviors of steel reinforcement. And the UHTCC material was assigned the Cast Iron Plasticity model. ABAQUS/standard made use of a composite yield surface to describe the different behaviors in tension and compression. In tension, yielding is assumed to be governed by the maximum principal stress; while in compression, yielding is assumed to be pressure independent and governed by the deviatoric stresses alone (Mises yield condition).
A typical stress-strain curve of concrete is shown in Fig.7(a). It is assumed to be linear up to
where
is the cylinder compressive strength of concrete. The curved part is represented by Eqs.(1) and (2):
(1)
(2)
where
is the concrete strain corresponding to its compressive strength
The ultimate tensile stress of concrete
is equal to one tenth of the compressive strength. The rebar reinforcements are assumed to be an elasto-plastic material with strain hardening in both tension and compression, as shown in Fig.7(b). The yield stress and ultimate strength of the steel bars are fsy and fsu, both of which were measured by tensile tests. According to the measured stress-strain curves of UHTCC, they are simplified as double broken line models, respectively, under compression stress and tensile stress [12], as shown in Fig.7(c). σtc and σtu are the cracking and ultimate stresses of UHTCC in tension. σcc and σcu are the equivalent yield and ultimate stress in compression.
4.3 Comparison of results
The load-deflection relationships, which were calculated by the above mentioned FEM, are compared with the test results. When the mid-span was 5 mm, the maximum crack width of UHTCC layer reached about 0.2 mm. The width which ranged from 0.2 to 0.4 was described as the serviceability limit width of engineering structure. So, the range of deflection was from 0 to 5.5 mm. Figure 8 shows that numerical calculations are in good agreement with the test ones. The results show that the numerical models and material parameters are able to provide a better simulation to the loading situation and mechanical state of composite beams.
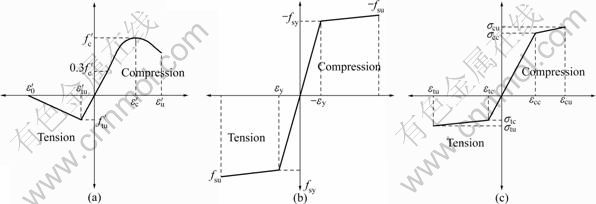
Fig.7 Stress-strain curves: (a) Concrete; (b) Steel; (c) UHTCC
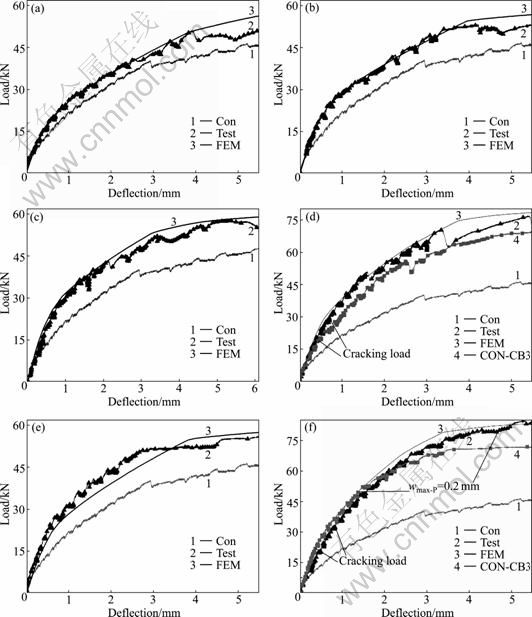
Fig.8 Load-deflection curves: (a) UH-CB1; (b) UH-CB2; (c) UH-CB3; (d) UH-CB4; (e) UH-CB5; (f) UB-CB6
5 Conclusions
1) The UHTCC as retrofit material is more feasible and effective to apply in strengthening existing concrete members than high strength grade concrete. Although the protective layer thickness increases, no brittle failure appears during the loading.
2) The addition of reinforced bars to the UHTCC layer improves the overall stiffness and the carrying capacity of the strengthening beam significantly. Compared with concrete, UHTCC is more suitable to work together with the reinforced bars. With the strengthening ratio and overall stiffness increasing, there are some cracks found around the end zone of post-poured layer of locally strengthening beam.
3) The application of the UHTCC material in the beam tension zone prevents the development of macro cracks in the upper concrete beam, and disperses them into a number of finer cracks to prolong the appearance of harm cracks on the bending face.
4) The load-deflection plots obtained from three- dimensional finite-element models (FEMs) analyses are basically consistent with those obtained from the experimental results. The reasonableness and practicality of the proposed models are also verified.
References
[1] LI V C, LEUNG C K Y. Theory of steady state and multiple cracking of random discontinuous fiber reinforced brittle matrix composites [J]. Journal of Engineering Mechanics, 1992, 118(11): 2246-2264.
[2] LI V C, WANG S, WU C. Tensile strain hardening behavior of polyvinyl alcohol engineered cementitious composites (PVA-ECC) [J]. ACI Mater J, 2001, 98(6): 483-492.
[3] LI V C. On engineered cementitious composites (ECC)—A review of the material and its applications [J]. J Adv Concr Technol, 2003, 1(3): 215-230.
[4] XU Shi-lang, ZHANG Xiu-fang. Theoretical analysis and experimental investigation on flexural performance of steel reinforced ultrahigh toughness cementitious composite (RUHTCC) beams [J]. Science in China Series E: Technological Sciences, 2009, 52(4): 1068-1089.
[5] XU Shi-lang, LI He-dong. A review on the development of research and application of ultra high toughness cementitious composites [J]. China Civil Engineering Journal, 2008, 41(6): 72-87. (in Chinese)
[6] XU Shi-lang, CAI Xin-hua, Li He-dong. Experimental study of the durability properties of ultra-high toughness cementitious composites under freezing and thawing cycles [J]. China Civil Engineering Journal, 2009, 42(9): 42-46. (in Chinese)
[7] SHAIKH F U A, HIROZO M. A review on durability properties of strain hardening ?ber reinforced cementitious composites [J]. Cement & Concrete Composites, 2007. 29(5): 365-376.
[8] LEPECH M D, LI V C. Water permeability of cracked cementitious composites [C]// Compendium of Papers, ICF 11, Turin, Italy, 2005. CD-ROM.
[9] KIM Y Y, FISCHER G, LI V C. Performance of Bridge Deck Link Slabs Designed with Ductile ECC [J]. ACI Structural J, 2004, 101(6): 792-801.
[10] KOJIMA S, SAKAT N, KANDA T, HIRAISHI T. Application of direct sprayed ecc for retrofitting dam structure surface-application for Mitaka-Dam [J]. Concrete Journal, 2004, 42(5): 135-139.
[11] KUNIEDA M, ROKUGO K. Recent progress on HPFRCC in Japan—Required performance and applications [J]. J Advanced Concrete Technology, 2006, 4(1): 19-33.
[12] LI He-dong. Experimental research on ultra high toughness cementitious composites [D]. Dalian: Dalian University of Technology, 2008. (in Chinese)
[13] ISENBERG J. Finite element analysis of reinforced concrete structures II: Proceedings of the international workshop [M]. New York: ASCE, 1993: 1-35.
[14] WANG Xu-cheng. Finite element method [M]. Beijing: Tsinghua University Press, 2003: 545-660. (in Chinese)
[15] HIBBITT, KARLSSON, SORENSON, INC. ABAQUS/Standard User’s Manual [M]. Pawtucket: Hibbitt, Karlsson, Sorenson, Inc, 2002.
[16] ABAQUS Inc. Abaqus Analysis User’s Manual [M]. Volume V. Providence: ABAQUS Inc, 2007.
(Edited by PENG Chao-qun)
Foundation item: Project(50438010) supported by the National Natural Science Foundation of China
Received date: 2010-06-29; Accepted date: 2010-10-20
Corresponding author: XU Shi-lang, Professor, PhD; Tel: +86-411-84707937; E-mail: shilangxu@126.com