
Rapid chemical vapor infiltration of C/C composites
ZHANG Ming-yu(张明瑜)1, 2, WANG Li-ping(王丽平)3, HUANG Qi-zhong(黄启忠)2, CHAI Li-yuan(柴立元)1
1. School of Metallurgical Science and Engineering, Central South University, Changsha 410083, China;
2. State Key Laboratory of Powder Metallurgy, Central South University, Changsha 410083, China;
3. Department of Biological Engineering and Environmental Science, Changsha College, Changsha 410003, China
Received 10 August 2009; accepted 15 September 2009
Abstract: With liquid petrol gas (LPG) as carbon source, carbon felt as porous perform and hydrogen as diluent, C/C composites were fast fabricated by using a multi-physics field chemical vapor infiltration (MFCVI) process in a self-made furnace. A set of orthogonal experiments were carried out to optimize parameters in terms of indices of density and graphitization degree. The results show the optimal indices can be achieved under the conditions of temperature 650 ℃, LPG concentration 80%, gas flux 60 mL/s, total pressure 20 kPa, infiltration time 15 h. The verification experiment proves the effectiveness of the orthogonal experiments. Under the optimal conditions, the graphitization degree of 75% and bulk density of 1.69 g/cm are achieved with a uniform density distribution. At the same time, a new structure is obtained.
Key words: C/C composites; chemical vapor infiltration(CVI); graphitization degree; bulk density; orthogonal experiment
1 Introduction
Carbon fiber-reinforced carbon matrix composites, carbon-carbon (C/C) composites, typically made by chemical vapor infiltration (CVI), are attractive materials to be used at elevated temperatures in inert atmosphere and ablative environments for aviation and aerospace applications. But the high manufacture cost of C/C composites restrains applications. At present, thousands of hours are needed for the C/C composites manufacture of full cycle large-scale isothermal chemical vapor infiltration(ICVI). Nevertheless, by the rapid densification technologies, the cost can be greatly lowered[1-3]. Therefore, many countries have been focusing their studies on rapid CVI technology[3-7] including an improved ICVI[8-10]. A rapid densification technology, multi-physics field CVI (MFCVI) was developed[11]. In this work, orthogonal experiments were designed and carried out to evaluate the novel technique for scale production. High density and high graphitization degree are the most important for high temperature applications. These two parameters were employed as orthogonal indices to weigh the performance of C/C composites[12].
2 Experimental
C/C composites were fast fabricated by MFCVI in a self-made furnace[11]. Schematic diagram of infiltration is presented in Fig.1 with liqnid petrol gas (LPG) as carbon source, polyacrylonitrile-based carbon felt with dimensional sizes of 280 mm×40 mm×20 mm and an initial density of about 0.2 g/cm3 as porous preform and hydrogen as diluent gas. A set of orthogonal experiments L16(45) were designed to optimize the density and graphitization degree[13-14]. The temperature varied between 650 ℃ and 950 ℃, LPG concentration changed from 50% to 80%, gas flux was in the range of 40-100 mL/s and consequently total pressure increased from 5 kPa to 20 kPa. The factor-level configuration is shown in Table 1.
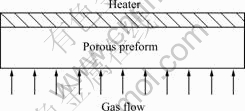
Fig.1 Schematic diagram of CVI process in cold-wall reactor
Table 1 L16(45) factor-level configuration
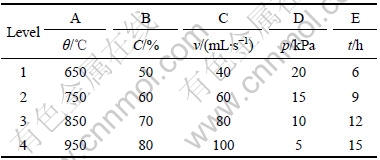
The density of C/C composites was measured by Archimedes principle. The graphitization degree of C/C composites was obtained after high temperature treatment at 2 300 ℃ for 2 h. The Rigaku-D/2550VB X-ray diffractometer was employed to scan the (002) peak of the composites. According to Franklin model, the diffraction angle corresponding to (002) peak, gravity center and median value of full width at half maximum (FWHM) were collected to calculate the graphitization degree (g). g value of the C/C composites in the present work was the average of the three calculated values. Polarized optical microscopy (PLM) was used to characterize the texture of the different pyrolytic carbons on a Leica MeF3A microscope. Scanning electron microscopy (SEM) was performed on JSM6360LV microscope.
3 Results and discussion
Table 2 shows the results of the orthogonal experiments.
Table 2 Results of L16(45) LPG-hydrogen experiments
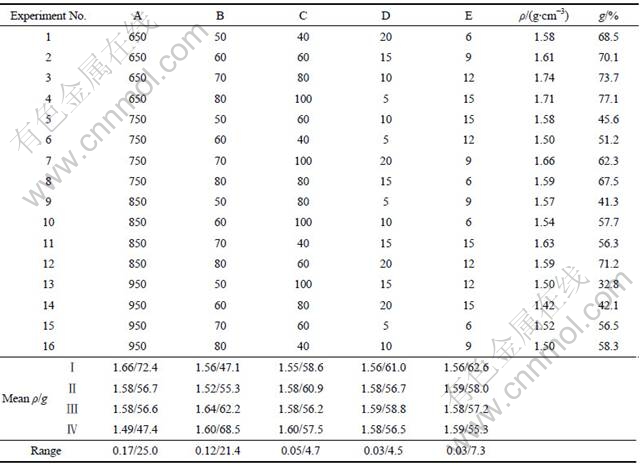
3.1 Density
As shown in Table 2, the mean optimal parameters for density are 650 ℃, 70%, 100 mL/s, 10 kPa and 15 h. It is clear that a wider range of one factor leads to a greater influence on indices while the level of the factor is varied reversely. The factors are in the order RA>RB>RC>RD=RE, indicating an increasing effect on indices. The variance analysis was carried out to evaluate the influence of factor and the obtained data are listed in Table 3. The F-test results show FA>F99(3, 6)=9.78, indicating that both A and B are predominant at level of 0.01. The best level should be accessible if the level can be selected on the basis of low cost and easy operation. Therefore, the best level combination is A1B3C4D3E4 according to above analysis.
Table 3 Results of variance analysis on density
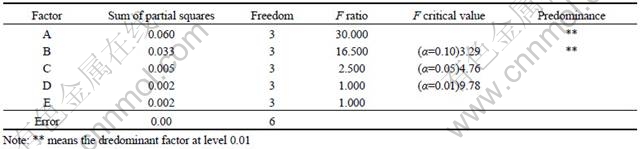
3.2 Graphitization degree
The mean optimal condition for graphitization degree is 650 ℃, 80%, 60 mL/s, 20 kPa and 6 h. The factor is in the order of RA>RB>RE>RC>RD.
Variance analysis results are listed in Table 4. The F-test results show FA>F99(3, 6)=9.78, demonstrating that both A and B are predominant at level 0.01. Thus, the best level combination is A1B4C2D1E1.
Table 4 Results of variance analysis on graphitization degree
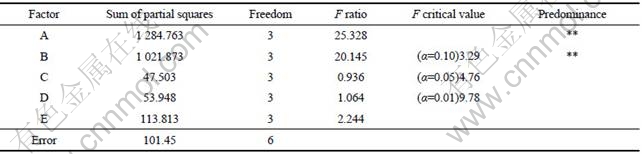
3.3 Integrative comparison of cross table
In order to find the conditions that meet the relevant parameters of density and graphitization degree, an integrative comparison of cross table was undertaken and shown in Table 5.
Table 5 Integrative comparison
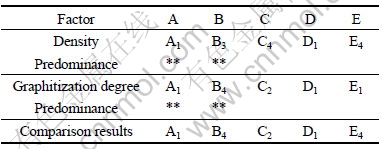
Form the cross table analysis (Table 5), A1B4C2D1E4 is the optimum condition; and based on the experiment results, it can be seen that the five characteristic values in the experiments do not conflict with each other. After analysis, the optimum conditions do not appear in orthogonal experiments. Therefore, it is necessary to carry out the verification experiments.
3.4 Verification experiment
The verification experiment was performed under the conditions shown in Table 5, temperature 650 ℃, LPG concentration 80%, gas flux 60 mL/s, total pressure 20 kPa and infiltration time 15 h. The corresponding density and graphitization degree are 1.69 g/cm3 and 75%, respectively, which conform the analysis and the availability of the experiments.
3.5 Density distribution
In order to measure the density distribution of the C/C composites fabricated by MFCVI, the obtained sample was cut into small pieces (30 mm×30 mm×20 mm) along the thermal gradient direction. After polishing every 500 μm of the thickness of pieces, the mass of the remained piece was measured. The cycle was repeated until the piece was used up. The density distribution along the thickness direction was calculated according to the mass, as shown in Fig.2. It is clear that the density distribution of the C/C composites fabricated by MFCVI is quite uniform. The middle part has a lower density, which is attributed to the gas diffusion limitation. It is supposed that the low gradients of thermal diffusion and magnetic field, and the cooling effect of the fast flowing gas all cause the temperature of the exterior part substantially lower than that of the hot surface. As a result, the open pores on surface can further be infiltrated. The results indicate that the density distribution of the fabricated materials can meet the requirement of most applications.
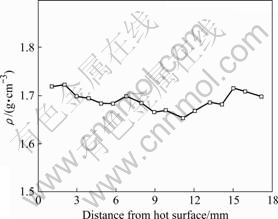
Fig.2 Density distribution of C/C composites
3.6 Microstructure analysis
PLM performed on the matrix exhibits a novel structure of pyrolytic carbon(Fig.3(a)). There are no obvious Maltese-cross and extinction angle with deep blue and orange colors. Meanwhile, it is noticeable that a lot of huge cones grow from the matrix.
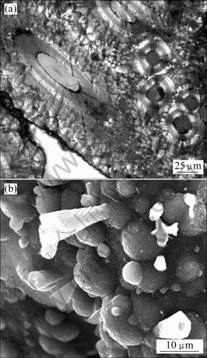
Fig.3 Microstructure of pyrocarbon of C/C composites: (a) PLM image; (b) SEM image
SEM measurements show there are a large amount of nodular textures and hollow cones on the surface of this pyrolytic carbon up and down while the fracture surface is RL-like layers with a certain angles. Energy disperse spectrum (EDS) results show that no catalytic element exists in the materials except carbon. The XRD pattern also displays the presence of identical structures. At the same time, its graphitization degree is higher. This pyrolytic carbon has a new structure.
4 Conclusions
1) Orthogonal experiments demonstrate that the optimal parameters for C/C composites via MFCVI are temperature 650 ℃, LPG concentration 80%, gas flux 60 mL/s and total pressure 20 kPa within 15 h.
2) The density is 1.69 g/cm and graphite degree is 75% under optimal conditions. and the density distribution is uniform.
3) PLM and SEM images show the possibility of the existence of a novel pyrocarbon structure with a high graphitization degree.
References
[1] GOLECKI I, MORRIS R C, NARASIMHAN D. Method of rapidly densifying a porous structure: US5348774[P]. 1994-09-20.
[2] BRUNETON E, NARCY B, OBERLIN A. Carbon-carbon composites prepared by a rapid densification process II: Structural and textural characterizations [J]. Carbon, 1997, 35(10/11): 1599-1611.
[3] DELHA?S P. Chemical vapor deposition and infiltration processes of carbon materials [J]. Carbon, 2002, 40(5): 641-657.
[4] HOUDAYER M, SPITZ J, TRAN-VAN D. Process for the densification of a porous structure: US4472454[P]. 1984-09-18.
[5] SUN W C, LI H J, HAN H M. Microstructure of the pyrocarbon matrix prepared by the CLVI process [J]. Mater Sci Eng A,2004, 369(1/2): 245-249.
[6] JOHN O Y, STRATIS V S. Investigation of the potential of forced-flow chemical vapor infiltration [J]. Electrochem Soc, 1997, 144(1): 264-269.
[7] TANG Su-fang, ZHOU Xing-ming, DENG Jing-yi, DU Hai-feng, LIU Wen-chuan. The preparation of 2D C/C composites by chemical vapor infiltration [J]. New Carbon Materials, 2005, 20(2): 139-143. (in Chinese)
[8] CHEN T F, GONG W P, LIU G S, ZHANG F Q. Influence of graphite foils on I-CVI densification rate and microstructure of obtained pyrolytic carbon of carbon-carbon composites [J]. Composites Part A: Applied Science and Manufacturing, 2005, 36(11): 1494-1498.
[9] NORINAGA K, DEUTSCHMANN O, H?TTINGER K J. Analysis of gas phase compounds in chemical vapor deposition of carbon from light hydrocarbons [J]. Carbon, 2006, 44(9): 1790-1800.
[10] ZHANG W G, H?TTINGER K J. Densification of a 2D carbon fiber preform by isothermal isobaric CVI: Kinetics and carbon microstructure [J]. Carbon, 2003, 41(12): 2325-2337.
[11] ZHANG Ming-yu, HUANG Qi-zhong, SU Zhe-an, XIE Zhi-yong. Preparation and microstructure analysis of C/C composites with multi-coupling fields CVI [J]. Journal of Inorganic Materials, 2006, 21(6): 1373-1377. (in Chinese)
[12] OBERLIN A. Pyrocarbons [J]. Carbon, 2002, 40(1): 7-24.
[13] CHEN Ai-liang, SUN Pei-mei, ZHAO Zhong-wei, LI Hong-gui, CHEN Xing-yu. Study of decomposing carbonyl slag [J]. Trans Nonferrous Met Soc China,2006, 16(2): 477-482.
[14] WANG Tong-min, SU Yan-qing, GUO Jing-jie, OHNAKA I, YASUDA H. Structure simulation in unidirectionally solidified turbine blade by dendrite envelope tracking model (II): Model validation and defects prediction [J]. Trans Nonferrous Met Soc China, 2006, 16(4): 753-759.
Foundation item: Projects(50802115; 50721003) supported by the National Natural Science Foundation of China; Project(2006CB600901) supported by the National Basic Research Program of China
Corresponding author: ZHANG Ming-yu; Tel: +86-731-88877671; E-mail: mingyu@mail.csu.edu.cn
DOI: 10.1016/S1003-6326(09)60046-7
(Edited by YANG Hua)