文章编号:1004-0609(2008)03-0394-06
流变压铸YL112铝合金的热处理与力学性能
郭洪民1,杨湘杰2
(1. 南昌大学 材料科学与工程学院,南昌 330031;
2. 南昌大学 机电工程学院,南昌 330031)
摘 要:采用具有自主知识产权的流变铸造工艺,研究了流变压铸YL112合金铸件中的气孔、流变压铸件的热处理和力学性能。结果表明:采用低固相率半固态浆料的直接压铸工艺可提高压铸件的致密性和力学性能,尤其伸长率提高更为显著,可采用热处理可进一步提高YL112合金的力学性能。在500 ℃固溶处理3 min后,YL112合金的共晶Si已经破碎并球化,固熔处理30 min 的T6热处理工艺可使YL112合金的强度和塑性达到比较好的匹配。
关键词:流变成形;压铸;微观组织;力学性能;热处理
中图分类号:TG 146.2; TG 166 文献标识码:A
Heat treatments and mechanical properties of YL112 aluminum alloy produced by rheo-diecasting process
GUO Hong-min1, YANG Xiang-jie2
(1. School of Materials Science and Engineering, Nanchang University, Nanchang 330031, China;
2. School of Mechanical and Electronic Engineering, Nanchang University, Nanchang 330031, China)
Abstract: Based on the independently developed rheocasting process named as low superheat pouring with a shear field (LSPSF), a new one-step semi-solid processing technique, the rheo-diecasting (RDC) process, was exploited. The porosity in RDC YL112 secondary aluminum alloy castings, heat treatments and mechanical properties were investigated. The results show that RDC can improve the integrity and mechanical properties, particularly elongation of YL112 alloy, and the heat treatment can further enhance the mechanical properties. The spheroidization process of eutectic silicon in YL112 alloy is already finished after solution treatment at 500 ℃ for 3 min. A suitable combination of strength and ductility can be obtained under an exploited T6 heat treatment process, solution treated at 500 ℃ for 30 min followed by water quenching at 80 ℃ and then artificial aged at 160 ℃ for 6 h.
Key words: rheoforming; diecasting; microstructure; mechanical properties; heat treatment
目前,限制压铸技术应用的主要问题是压铸件的多孔性以及由此带来的强度问题。多孔性导致压铸件力学性能下降,通常无法进行热处理,从而限制了压铸件应用范围的扩大[1]。为了提高压铸件的致密度,目前主要有两大技术:以真空压铸为代表的直接消除型腔气体法和以半固态压铸为代表的层流压铸法。其中半固态压铸(包括流变压铸和触变压铸),由于成形件的性能、质量、经济性等方面都具有极强的竞争力,受到学术界和工业界的广泛关注[2-4]。性价比是决定半固态成形技术工业应用的决定性因素,因此,工艺流程长、生产成本高的触变压铸工艺并不能充分展现半固态成形技术的优点,其应用受到限制。自20世纪末至今,国内外学术界和企业界将研究重点重新转移至流变压铸工艺,并相继开发了两种模式:以压射室制浆压铸[5]和流变射铸[6-7]为代表的制浆和成形一体化技术,虽然避免了半固态浆料转移,但浆料制备设备复杂昂贵,并且须对压铸机进行较大改动;另一种是以New Rheocasting (NRCTM)[8]、Semi-solid Reocasting (SSRTM)[9]等为代表的浆料制备系统和成形系统相分离的模式,可通过多工位的手段提高生产效率,这是目前比较简单、工业上容易接受的方式,但具体技术细节尚未公开。另外,关于流变压铸的研究主要集中于半固态浆料制备、工艺参数确定和优化,应用的合金主要集中于A356、A357和AZ91D等铸造类合金。而在流变压铸件热处理和扩大应用合金范围方面的研究还很少。
本文作者开发了LSPSF(low superheat heat pouring with a shear field)优质半固态浆料制备技术,成功制备了A356铸造铝合金、201高强铸造铝合金、2024变形铝合金、YL112压铸专用合金的半固态浆料[10-11]。并将LSPSF工艺与压铸工艺衔接开发了流变压铸工艺,研究了流变压铸YL112合金的微观组织特征[12]。本文作者在此继续研究流变压铸YL112合金铸件中的气孔、流变压铸件的热处理和力学性能。
1 实验
1.1 实验材料
压铸专用铝合金具有较大的硬度和强度、较好的流动性能和铸造性能,广泛应用于压铸产业,但对该类合金在半固态成形领域的研究非常有限。实验合金为工业用压铸专用铝合金YL112,属AlSiCu系,是一种高强度压铸铝合金,合金锭由江西洪都航空工业集团铸造分厂提供,合金成分(质量分数,%)见表1。
表1 YL112压铸专用合金的化学成分
Table 1 Chemical compositions of YL112 alloy (mass fraction, %)
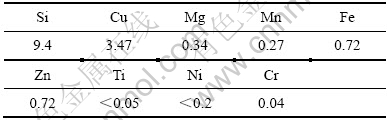
1.2 实验过程
实验中采用LSPSF法制备YL112合金半固态浆料。前期研究[12]表明,获得优质YL112合金半固态浆料的最佳工艺参数范围是:浇注温度620~630 ℃;输送管倾角20?~35?;输送管转速90~150 r/min。在此工艺范围内,YL112合金中初生α(Al)的平均等效圆直径为70 μm,平均形状因子为0.93,初生α(Al)内没有夹裹液相。本研究采用的浆料制备参数为浇注温度625 ℃,输送管倾角20?,输送管转速90 r/min,浆料蓄积器预热温度560 ℃。浆料制备时间为15~20 s,其中合金熔体流经输送管约历时2 s,其余时间用于浆料在缓慢冷却过程中调整固相率。
浆料成形设备为DCC280型280 t卧式冷室压铸机。压铸过程中,模具温度保持在200 ℃,增压压力为180 MPa,半固态浆料成形温度为580 ℃。常规压铸时,YL112合金的成形温度为660 ℃,具体的实验流程见文献[12]。流变压铸零件为支架,如图1所示。矩形力学性能试样按照ASTM B557M-02a 标准从支架上截取,采用CSS-44200型电子万能机测定拉伸试样的抗拉强度、屈服强度和伸长率。将流变压铸成形的支架零件进行热处理:T5热处理,160 ℃人工时效6 h;T6热处理,固溶(500 ℃,3 min~4 h)+80 ℃热水淬+160 ℃人工时效6 h。金相试样用混合酸浸蚀,通过SEM的二次电子成像获得固溶处理前后共晶硅的形貌。
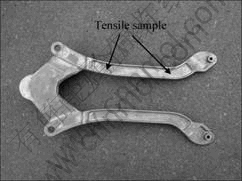
图1 YL112合金流变压铸支架及拉伸试样取样位置
Fig.1 RDC bracket and sample positions for tensile test
2 结果与分析
2.1 压铸件中的气孔
密度在一定程度上体现着铸件的致密程度。为此,本文作者采用密度作为压铸件气孔率的衡量标准,并以密度的理论计算值作为气孔率为零的参考值。合金的理论密度按照组成化学元素的密度及其所占的质量分数计算,压铸件的密度根据阿基米德定律测定[13]。计算所需的各元素的密度见表2,每个试样测量3次,取其平均值为该试样的密度。
合金的理论密度为2.756 g/cm3。流变压铸件密度与传统压铸件密度、理论密度的比较如图2所示。虽然采用阿基米德定律测量密度在操作上有一定误差,但从图2仍然可以看出,与传统压铸相比,流变压铸件的密度较高,并且密度分布比较集中。但与理论密度相比,流变压铸件的致密性还有一定差距。
`表2 YL112合金中各元素的密度
Table 2 Densities of elements contained in YL112 alloy (g/cm3)

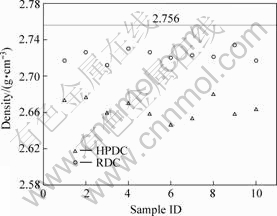
图2 流变压铸件密度与传统压铸件密度、理论密度的比较
Fig.2 Densities of YL112 alloys under RDC, HPDC and theoretical calculation
气孔是压铸件中最重要的缺陷,气体主要来源于熔炼过程中吸入的气体和充型过程中卷入的气体。与传统压铸相比,流变压铸的原料不是具有一定过热度的高温合金液,而是半固态浆料,由于浆料的温度较低,气体的溶解度降低,这是流变压铸件气孔率低的原因之一。另外,半固态浆料具有较高的表观粘度、低的雷诺数,可实现平稳充型,减少甚至消除了充型中的包裹气,提高铸件的致密性。然而,图2说明YL112合金流变压铸件的致密性还是有一定限度的。在浆料制备阶段,合金熔体流经输送管的过程中,由于液面的波动,会卷入气体,增加了吸氢的可能。因此,必须预防二次污染,这是工业用LSPSF浆料制备机必须解决的问题。YL112合金的热分析表明,该合金半固态浆料含有近70%的液相[12],在半固态浆料充型过程中,如果充型速度过快,就会卷入一些气体。因此,保持低固相率半固态浆料的平稳充型,是减少YL112合金流变压铸件中气孔的有效措施,是后续工作的重点之一。在压铸工艺方面,流变压铸所考虑的压射工艺因素与液态压铸基本相似,但对压铸机压射性能的要求更高,如慢压射与快压射的转换时间、填充阶段的压力稳定以及增压减压的反应时间等。在压铸模具方面,必须按照半固态浆的力学性能和流变行为进行模具设计,重点是浇道、内浇口、排气和溢流部件的设计。
2.2 流变压铸件的固溶处理
低气孔率为流变压铸件的可热处理性提供了先决条件。实验中,当固溶处理温度为500 ℃时,流变压铸件也不会出现气泡,而传统压铸在480 ℃便出现大量气泡。选择的固溶处理规范为:500 ℃,3 min~4 h,重点研究固溶处理时间对流变压铸微观组织的影响。
图3所示为流变压铸YL112合金的共晶Si在 500 ℃固溶处理3 min~4 h过程中的演变特征。由图3(a)可见,共晶Si在铸态下,呈纤维状。这些形态的共晶Si在500 ℃时迅速破碎,并在保温3 min后基本全部球化,如图3(b)所示。根据瑞利失稳[14-15],流变压铸YL112合金中的共晶Si通过界面失稳,在降低界面能的驱动作用下,发生破碎而球化。流变压铸的二次凝固过程具有非常高的冷却速度[12],共晶Si变得非常细小,并且形状变得不规则,如图3(a)所示,这些因素加快了瑞利失稳过程。
如图3所示,共晶硅在固溶处理中的演变包括破碎、球化和粗化3个过程。Si颗粒的粗化是通过小颗粒的消失及大颗粒的生长来实现的,符合Owstwald粗化机理。由于Si的生长各向异性很强,因此,Si颗粒形态在保温处理2 h后变差。
2.3 流变压铸YL112合金的力学性能
表3总结了传统压铸、流变压铸及Sub Liquidus Casting(SLCTM)[16]条件下,YL112合金的铸态力学性能。与传统压铸相比,流变压铸件的抗拉强度较低,但屈服强度和伸长率得到提高,尤其伸长率提高了53.6%;与SLCTM流变成形相比,RDC铸件的抗拉强度比SLCTM铸件的高,屈服强度与之相当,而伸长率偏低。
表3 YL112合金在不同条件下的力学性能
Table 3 Mechanical properties of YL112 alloy under different conditions
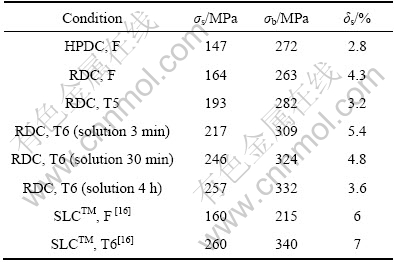
根据YL112合金在RDC中的凝固行为可知[12]:1) LSPSF工艺利用转动输送管提供的激冷和搅拌混合作用,再配以适当的浇注温度实现特殊的浇注过程,可有效地激发熔体形核,促进晶粒游离,提高游离晶的存活率,使得流变压铸YL112合金获得晶粒尺寸41 μm的细小初生α1(Al)。2) 半固态浆料二次凝固的主要特征是极高的冷却速度(数量级为103 ℃/s[8]):整个半固态浆料中的剩余液相将爆发形核,形成的初生α2(Al)呈细小的颗粒状,均匀地分布在基体中,其平均尺寸为13 μm;产生非常细小的共晶Si,层片间距约1 μm;金属间化合物形态被改善;充满模具型腔的半固态浆料将发生整体式凝固,而不会发生逐层凝固,因此,流变压铸件在纵断面和横断面上的微观组织都非常均匀。另外,由于流变压铸件的致密性很高,所以流变压铸YL112合金的力学性能优于传统压铸。
图3 500 ℃时固溶处理时间对共晶Si形态和尺寸的影响
Fig.3 Effects of solution treatment time at 500 ℃ on size and morphology of eutectic Si in RDC YL112 alloy: (a) As-cast; (b) 3 min; (c) 30 min; (d) 2 h; (e) 4 h
在传统压铸条件下,模具型壁的激冷使合金液在压力下发生逐层凝固,沿型壁面生长的晶粒迅速相连形成激冷层[12],激冷层有利于提高铸件的抗拉强度。SLCTM是利用挤压铸造工艺实现半固态浆料的直接成形,由于挤压铸造的优势[17],SLCTM铸件的致密性非常高,伸长率很高。RDC铸件的抗拉强度比SLCTM铸件的高,可能原因是RDC铸件的组织很细小。
YL112合金热处理后的力学性能见表3。低温人工时效(T5)能够提高RDC铸件的屈服强度和抗拉强度,但伸长率有所降低。T6热处理可有效地提高RDC铸件的力学性能,并且T6(固熔处理3 min)处理后,铸件的伸长率达到最高点5.4%,T6(固熔处理30 min)使得强度和塑性达到比较好的匹配。但总体而言,流变压铸的力学性能比SLCTM的低。但与触变压铸Y112合金相比[18],RDC的优势非常明显,微观组织和力学性能均明显优于触变压铸,因此,Y112合金比较适合于低固相率流变压铸。
T6(固熔处理3 min)和T5的区别是:T6有3 min的500 ℃固溶处理。这使得铸态下的纤维或杆状的共晶Si转变成球形,因此T6(固熔处理3 min)状态下的RDC铸件的伸长率比T5状态下的提高了约65%。在相同的人工时效条件下,随着固溶时间的延长,屈服强度和抗拉强度增大,而伸长率下降。固溶时间越长,Si和Mg等元素溶解得越充分,更多的CuAl2从过饱和的固溶体中脱溶沉淀,因此T6处理后铸件的强度提高。但随着固溶时间的延长,Si颗粒变得粗大,初生α(Al)长大,尤其是初生α2(Al),如图4所示。
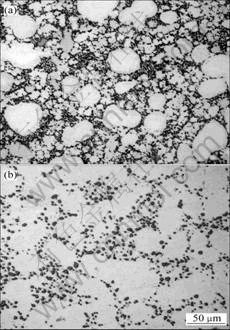
图4 500 ℃固溶处理30 min(a)和4 h(b)后,流变压铸YL112合金的微观组织
Fig.4 Microstructures of RDC YL112 alloy solution treated at 500 ℃ for 30 min(a) and 4 h(b)
固溶处理30 min时,Si颗粒还很细小,初生α1(Al)尚基本保持铸态尺寸,但初生α2(Al)已经开始合并生长(尚能辨识出)。当固溶处理4 h时,Si颗粒已经很粗大,初生α2(Al)已经和初生α1(Al)连成一片结合成粗大的初生α(Al),塑性下降。
3 结论
1) 流变压铸可实现YL112合金低固相率半固态浆料的低气孔率压铸。与HPDC相比,RDC可提高铸件的致密性和力学性能,尤其伸长率提高明显。但流变压铸工艺和流变压铸模具还具有极大的改善和优化空间。
2) 可采用热处理进一步提高YL112合金的力学性能。500 ℃固溶处理3 min,共晶Si已经破碎并球化。T6(固溶处理30 min)使得强度和塑性达到比较好的结合。
REFERENCES
[1] 潘宪曾. 压铸工艺与模具[M]. 北京: 电子工业出版社, 2006.
PAN Xian-zeng. Die casting technology and its moulds[M]. Beijing: Electronic Industry Press, 2006.
[2] FAN Z. Semisolid metal processing[J]. International Materials Reviews. 2002, 47 (2): 1-37.
[3] MIDSON S P. Rheocasting processes for semi-solid casting of aluminum alloy[J]. Die Casting Engineer, 2006, 50(1): 48-51.
[4] DASGUPTA R. Industrial application-the present status and challenges we face[C]//APELIAN D, ALEXANDROU A, GEORGIOU G, et al. Proceedings of 8th International Conference on Semi-Solid Processing of Alloys and Composites. Limassol: The Worcester Polytechnic Institute and The Metals Processing Institute, 2004: 1-14.
[5] SHIBATA R, KANEUCHI T, SOUDA T, YAMANE H. Formation of spherical solid phase in die casting shot sleeve without any agitation[C]//BHASIN A K, MOORE J J, YOUNG K P, et al. Proceedings of the 5th International Conference on Semi-Solid Processing of Alloys and Composites. Golden, Colorado: Colorado School of Mines, 1998: 465-470.
[6] FAN Z. Development of the rheo-diecasting process for magnesium alloys[J]. Mater Sci Eng A, 2005, 413/414: 72-78.
[7] KANG Yong-lin, XU Yue, WANG Zhao-hui. Study on microstructure and mechanical properies of rheo-die casting semi-solid A356 aluminum alloy[J]. Solid State Phenomena, 2006, 116/117: 453-456.
[8] KAUFMANN H, WABUSSEG H, UGGOWITZER P J. Metallurgical and processing aspects of the NRC semi-solid casting technology[J]. Aluminum, 2000, 76(1/2): 70-75.
[9] YURKO J A, FLEMINGS M C, MARTINEZ R A. Semisolid rheocasting (SSR)-increasing the capabilites of die casting[J]. Die Casting Engineering, 2004(1): 50-52.
[10] GUO Hong-min, YANG Xiang-jie. Preparation of semi-solid slurry containing fine and globular particles for wrought aluminum alloy 2024[J]. Transactions of Nonferrous Metals Society of China, 2007, 17(4): 799-804.
[11] GUO H M, YANG X J. Efficient refinement of spherical grain by LSPSF rheocasting process[J]. Materials Science and Technology, 2008, 24(1): 55-63.
[12] 郭洪民, 杨湘杰. 流变压铸YL112铝合金的微观组织特征[J]. 中国有色金属学报, 2008, 18(3): 400-408.
GUO Hong-min, YANG Xiang-jie. Microstructure characteristics of YL112 aluminum alloy produced by rheo- diecasting process[J]. The Chinese Journal of Nonferrous Metals, 2008, 18(3): 400-408.
[13] RAMADAN M, NOMURA H, TAKITA M. Semi-solid processing of thin section gray cast iron in sand mold[C]// APELIAN D, ALEXANDROU A, GEORGIOU G, et al. Proceedings of 8th International Conference on Semi-Solid Processing of Alloys and Composites. Limassol: The Worcester Polytechnic Institute and The Metals Processing Institute, 2004: 625-637.
[14] RAYLEIGH L. On the instability of jets[J]. Pro London Math Soc, 1978, 10: 4-13.
[15] NICHOLS F A, MULLINS W W. Surface (-interface-) and volume-diffusion contributions to morphological changes driven by capillarity[J]. Transaction of the Metallurgical Society of AIME, 1965, 233: 1840-1847.
[16] JORSTAD J L, THIEMAN M, KAMM R. Sub liquidus casting (SLC): Process concept and product properties[J]. Transactions of the American Foundry Society, 2003, 111: 399-405.
[17] 罗守敬, 陈炳光, 齐丕骧. 液态模锻与挤压铸造技术[M]. 北京: 化学工业出版社, 2006.
LUO Shou-jing, CHEN Bing-guang, QI Pi-xiang. Liquid forging and squeeze casting[M]. Beijing: Chemical Industry Press, 2006.
[18] 左宏志, 刘昌明, 邹茂华, 谷忠明, 范 增, 李德全, 吴 均. ZL112Y压铸铝合金摩托车零件的半固态高压铸造成形[J]. 中国有色金属学报, 2003, 13(4): 949-955.
ZUO Hong-zhi, LIU Chang-ming, ZOU Mao-hua, GU Zhong-ming, FAN Zeng, LI De-quan, WU Jun. Semi-solid die casting process of motorcycle parts of ZL112Y die cast alloy[J]. The Chinese Journal of Nonferrous Metals, 2003, 13(4): 949-955.
基金项目:国家自然科学基金资助项目(50474007);江西省教育厅科技计划资助项目(GJJ08006);江西省科技支撑计划资助项目
收稿日期:2007-05-20;修订日期:2007-12-24
通讯作者:郭洪民,博士;电话:0791-3969611;E-mail: hmguo_email@163.com
(编辑 何学锋)