
Sound absorption and insulation property of closed-cell aluminum foam
YU Hai-jun(尉海军)1, LI Bing(李 兵)1, YAO Guang-chun(姚广春)1,
WANG Xiao-lin(王晓林)2, LUO Hong-jie(罗洪杰)1, LIU Yi-han(刘宜汉)1
1. School of Materials and Metallurgy, Northeastern University, Shenyang 110004, China
2. Institute of Acoustics, Chinese Academy of Sciences, Beijing 100080, China
Received 28 July 2006; accepted 15 September 2006
Abstract: The closed-cell aluminum foams (specimen ρ=0.31 g/cm3, diameter of 100 mm, and thickness of 20 mm for sound absorption testing; specimen ρ=0.51 g/cm3, length of 1 240 mm, width of 1 100 mm, and thickness of 30 mm for sound insulation testing) were prepared by the method of molten body transitional foaming process. Its sound absorption property under frequency of 160-2 000 Hz and the sound insulation property under frequency of 100-4 000 Hz were tested. The sound absorption results show that the sound absorption property is much better under middle frequencies than that under low and high frequencies. The sound absorption coefficient climbs when frequency increases from 160 Hz to 800 Hz and then drops when frequency is increased from 800 Hz to 2 000 Hz. The function of the sound absorption mainly depends on the Helmholtz resonator, the microphone as well as cracks of closed-cell aluminum foam. The sound insulation experiments show that the sound reduction index (R) is small under low frequencies, and large under high frequencies; the weighted sound reduction index (Rw) and the highest sound reduction index (R) can reach around 30.8 dB and 43 dB, respectively.
Key words: closed-cell aluminum foam; sound absorption; sound insulation; mechanism
1 Introduction
The research and development of metal foams have started since 1940s. The earliest was the patent technology of SOSNICK[1] who prepared metal foams through the gasification of low melting point substance in the metal. In 1956, Borksten Research Laboratory Inc. first successfully prepared aluminum foam through molten body direct foaming process[2]. Then Foamalum Corp. and Italy Corp. put this technology into practice[3]. Besides, IFAM in Germany[4] and Alcan International Limited in Canada[5] both made great progress in the production technology of metal foam materials.
Compared with the traditional materials, aluminum foam materials have the advantages of low density, high stiffness, high impact resistance, low thermal conductivity, low magnetic conductivity, and fine damping, so they have become one of the fields in high technology material research all over the world[6-9]. Owing to the limitation of preparing large specimen, the researches in the past focused only on the mechanics and energy absorption of aluminum foam material[10-11] and rarely on the acoustics especially sound insulation property. Because of its special structure, aluminum foam has great potential application in fields such as noise reduction and sound insulation[12]. In this paper, the authors research the sound absorption property and sound insulation property of closed-cell aluminum foam prepared by molten body transitional foaming process in Northeastern University, China[13], and provides some information for its application in such fields as sound insulation and noise reduction.
2 Experimental
2.1 Preparation of closed-cell aluminum foam
For making the foams, two different metals and one powder were employed: 99.9% high purity binary eutectic Al-Si alloy, the high purity metal Ca and the powder of TiH2 (with granularity of 47 μm). Closed-cell aluminum foams are produced by molten body transitional foaming process in Northeastern University, China[13]. Fig.1 shows the schematic map of preparing closed-cell aluminum foam. The process has five step techniques: 1) Melting alloy of aluminum-silicon and calcium (3%, mass fraction) in furnace at 850 ℃; 2) adding titanium hydride (45 μm; 1.5%, mass fraction) to the molten body at 680 ℃ and stirring at a speed of 2 000 r/min; 3) transferring the molten mixture to the bubbly case; 4) pushing bubbly case to the maintaining furnace (650 ℃) and foaming in it for 6 min; 5) aluminum foam post processing[13].
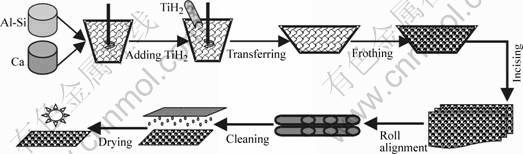
Fig.1 Sketch map of preparing closed-cell aluminum foam bare board by molten body transitional foaming process
Preparing one specimen (ρ=0.31 g/cm3, diameter 100 mm, thickness 20 mm) for sound absorption testing and another specimen (ρ=0.51 g/cm3, length 1 240 mm, width 1 100 mm, thickness 30 mm) for sound insulation testing by utilizing the saw machine, flattener, cleaning machine, etc.
Fig.2 shows the specimen for sound absorption testing, from which it can be seen that the cell modality of specimen is uniform, the wall of cells is joined by ‘Y’ type, and the angles are basically 120?.
Fig.3 shows the specimen for sound insulation testing. The essential parameters of specimens were systematically recorded before experiments, including the density of specimen, cell diameter, and wall thickness of cell etc (see Table 1). The densities of the closed-cell aluminum foams were calculated by weighing the machined test specimens on a balance and measuring their dimensions using a digital caliper. The cell and wall of cell for each specimen were measured using the method of arithmetic average.
2.2 Test of sound absorption and insulation property
The sound absorption property of closed-cell aluminum foam was tested by standing wave tube at Institute of Acoustics, Chinese Academy of Sciences, and the sound absorption coefficient of aluminum foam was also tested[14]. When sound wave meets the surface of closed-cell aluminum foam vertically, the traveling direction of reflected wave is against the direction of incidence wave, forming standing wave superposing one another. Measuring the maximal and minimal value of sound pressure can figure out normal incidence sound absorption coefficient. The measuring temperature and humidity were 24 ℃ and 66% respectively, and the range of frequency was controlled between 160 Hz to 2 000 Hz.
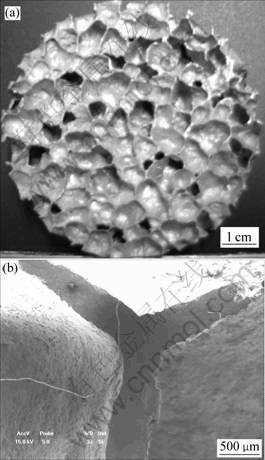
Fig.2 Macroscopic(a) and microcosmic(b) pictures of specimen for sound absorption testing
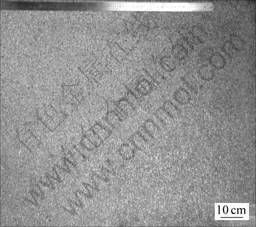
Fig.3 Specimen of sound insulation testing
Table 1 Parameters of specimens of closed-cell aluminum foam for sound absorption and insulation testing

The sound insulation property of specimen was also tested at Institute of Acoustics, Chinese Academy of Sciences. The shape and the volume of the Lab test room were in agreement with the constraints of GBJ 75/84[15]. Clamping the specimen on testing frame, the actual testing area of specimen was only 1 100 mm×1 100 mm. The sound pressure signals of emitting room and receiving room were collected by Real Time Analyzer 840 sound pressure analytical apparatus. Microphones were set at five different positions, and for each position the sound reveration time was analyzed at least twice.
3 Results and discussion
3.1 Sound absorption property of aluminum foam
As the structure of aluminum foam is quite special, while the specimen is incised, different cell shapes appear on the surface of specimen, one of which is called Helmholtz resonator (see Fig.4(b)) when the cell is incised only by a small hole[16]. As a result there are many Helmholtz resonators in parallel. While sound is imposed on the pipe orifices of Helmholtz resonators, the dimensions of pipe orifices are much smaller than the wavelength, and each section of air in pipe orifices belongs to a small region within wavelength of λ. So the vibration behavior of them is considered uniform, that is to say, the air in pipe orifices as a whole vibrates just like a piston and frictionizes with the wall faces to consume sound energy.
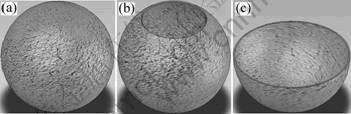
Fig.4 Surface pore modality of closed-cell aluminum foam
As for the air in cavity, when air column moves into the cavity, the air and the pressure in cavity will be compressed and increased because there is no way to go for the air, which will cause the vibration of air and congregation of sound energy in cavity. The interior surface of aluminum foam is rough (see Fig.5), the sound in which will be reflected and refracted many times owing to the resistance of flexural cell wall, resulting in large damping. That causes the friction between air and cell faces, therefore the cavity isn’t suitable for storing sound energy and the sound energy will transfer to heat energy to expand.
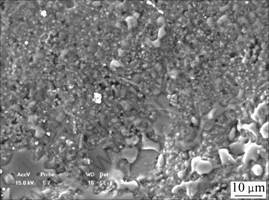
Fig.5 Internal surface of closed-cell aluminum foam
In addition, owing to the high temperature of preparing closed-cell aluminum foam and cooling out of time, the cracks and micropores are inevitable (see Fig.6), so another main path to expand sound energy is through the cracks and micropores of aluminum foam. The damping characteristic of aluminum is not very good, but the loss coefficient value of aluminum foam is higher than that of aluminum by one order of magnitude at least[17]. The consumption of sound energy by aluminum foam is mainly through the friction between crack faces in the structure, i.e. transmitting vibration energy to thermal energy and pushes air in or pushes it out of micropore, causing viscous consumption then dispersing into the surrounding environment.
The sound absorption property of closed-cell aluminum foam is shown in Fig.7, which indicates that the sound absorption property is much better under middle frequencies than that under low and high frequencies. The sound absorption coefficient climbs when frequency increases from 160 Hz to 800 Hz and then drops when frequency is increased from 800 Hz to 2 000 Hz. The highest sound absorption coefficient is 79%.
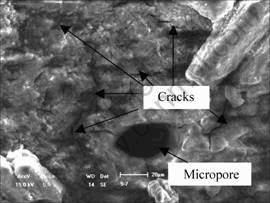
Fig.6 Micropore and crack of closed-cell aluminum foam
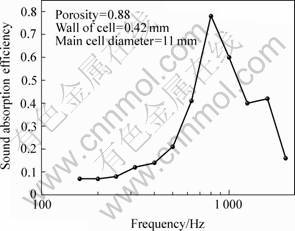
Fig.7 Sound absorption characteristic curve of closed-cell aluminum foam
3.2 Sound insulation property of aluminum foam
For the given material, the sound reduction index (R) is controlled by different mechanisms in different frequency ranges[18] (Fig.8). When the frequency is lower than f1, the sound reduction index (R) is mainly controlled by the stiffness of the board [18]. Among this section, sound reduction index (R) is proportional to the stiffness of the board wall (for certain frequency, the higher the stiffness, the larger the sound reduction index (R)). For the same board, sound reduction index (R) gradually drops when the frequency increases. Fig.9 shows the sound insulation property of closed-cell aluminum foam with density of 0.51 g/cm3. Through calculating, the first resonant frequency of closed-cell aluminum foam is lower than 100 dB, so there isn’t the stiffness control section in Fig.9. Aluminum foams have fine mass ratio rigidity, as a result, they have fine attraction for application in low frequency range [18].
When the frequency is higher than f1, sound reduction index (R) mainly relies on natural resonance, board size and fix condition of the board[18]. Compared with entity material, aluminum foams have good damping effect. As a result the fluctuations of curves in Fig.9 within this section are smooth, which can be well predicated by the theoretical curve with large damping.
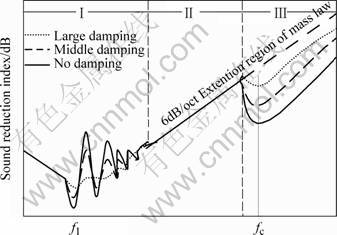
Fig.8 Characteristic curve between sound reduction index and frequency of monolayer board (f1, first resonance frequency; fc, critical frequency; Ⅰ Stiffness and damping control section; Ⅱ Mass control section; Ⅲ Coincidence effect section)
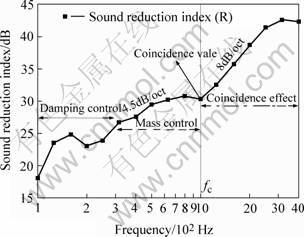
Fig.9 Sound insulation property of closed-cell aluminum foam bare board with ρ=0.51 g/cm3, thickness of 30 mm, length of 1 240 mm and width of 1 100 mm
After the damping control comes the mass control (see Fig.9), the sound reduction index (R) in this section climbs straightly when the frequency increases, and the slope coefficient is 4.5dB/oct, which is close to the theoretical value (6dB/oct). While the projection of incident sound wave’s wavelength on the board is equal to the wavelength of board doing flexural vibration, the sound wave of this frequency can completely transfer to the opposite side of the board, and generate a valley, which is called coincidence effect, and the frequency is called critical frequency [19]. The result in Fig.9 indicates that the coincident valley of closed-cell aluminum foam bare board is not obvious. The sound reduction index (R) also climbs straightly when the frequency is larger than fc, and the slope coefficient is 8 dB/oct approaching to 10 dB/oct. The single sound reduction index (Rw) is gotten to be about 43 dB according to international evaluation criterion of sound insulation material [20].
4 Conclusions
1) The sound absorption property of closed-cell aluminum foam is much better under middle frequencies than that under low and high frequencies. The sound absorption coefficient climbs when frequency increases from 160 Hz to 800 Hz and then drops when frequency is increased from 800 Hz to 2 000 Hz. The highest sound absorption coefficient is 79%. The function of the sound absorption mainly depends on the Helmholtz resonator, the microphone as well as cracks of closed-cell aluminum foam.
2) The sound reduction index (R) is small under low frequencies, and large under high frequencies; the weighted sound reduction index (Rw) and the highest sound reduction index (R) could reach around 30.8 dB and 43 dB respectively. The sound insulation property of closed-cell aluminum foam basically conforms to the monolayer board sound insulation theory, which has three control sections: damping control section, mass control section and coincidence effect section, and there are no obvious coincidence effect owing to the good damping property of aluminum foam.
References
[1] SOSNICK B. Process for Making Foam-like Mass of Metal [P]. US Patent 2434775, 1948.
[2] ELLIOTT J C. Method of Producing Metal Foam [P]. US Patent 2751289, 1956.
[3] HAN Fu-sheng. A kind of new-style physics functional material—Aluminum foam [J]. Int Sci Tech, 1996, 6: 3-6. (in Chinese)
[4] BAUMG?RTNER F, DUARTE I, BANHART J. Industrialization of powder compact foaming process [J]. Adv Eng Mater, 2000, 2(4): 168-174.
[5] BEALS J T, THOMPSON M S. Density gradient effects on aluminum foam compression behavior [J]. J Mater Sci, 1997, 32: 3595-3600.
[6] BANHART J. Manufacture, characterization and application of cellular metals and metal foams [J]. Progr Mater Sci, 2001, 46: 559-632.
[7] BASTAWROS A F, BARTSMITH H, EVANS A G. Experimental analysis of deformation mechanisms in a closed-cell aluminum alloy foam [J]. J Mech Phy Solids, 2000, 47: 2235-2272.
[8] ROBERTS A P, GARBOCZI F J. Elastic moduli of model random three-dimensional closed-cell cellular solids [J]. Acta Materialia, 2001, 49(2): 189-197.
[9] LU T J, HESS A, ASHBY M F. Sound absorption in metallic foams [J]. J Appl Phys, 1999, 85: 7528-7539.
[10] ZHOU J, SHROTRIYA P, SOBOYEJO W O. Mechanisms and mechanics of compressive deformation in open-cell Al foams [J]. Mech Mater, 2004, 36: 781-797.
[11] ANDREWS E W, GIBSON L J. On notch-strengthening and crack tip deformation in cellular metals [J]. Mater Lett, 2002, 57: 532-536.
[12] YU Hai-jun, YAO Guang-chun, LIU Yi-han. Tensile property of Al-Si closed-cell aluminum foam [J]. Trans Nonferrous Met Soc China, 2006, 16(6): 1335-1340.
[13] YU Hai-jun, YAO Guang-chun, LI Bing, GUO Zhi-qiang. Electromagnetic shielding effectiveness of Al-Si closed-cell aluminum foam[J]. J Functional Mater, 2006, 37(8): 1239-1241. (in Chinese)
[14] GBJ88-85. Testing Standard of Sound Absorption Coefficient by Standing Wave Tube Method[S]. 1985.
[15] GBJ75/84. Testing Standard of Sound Insulation in Building[S]. 1984.
[16] MA Da-you. Theoretic Basis of Modern Acoustic[M]. Beijing: Science Press, 2003: 254-255. (in Chinese)
[17] KOVACIK J, BUSSE P, SIMANCIK F. Metal Foams and Porous Metal Structures [M]. UK: MIT Verlag Press, 1999: 165-168.
[18] LI Yao-zhong. The Technology of Sound Insulation Controlling [M]. Beijing: Chemical Industry Press, 2004: 22-23. (in Chinese)
[19] DEGISCHER H P, KRISZT B. Handbook of Cellular Metals: Production, Processing, Applications [M]. Austria: Wiley-VCH Press, 2002: 191-192.
[20] ISO 717-1/97. Rating of Sound Insulation in Buildings and of Buildings Elements–Airborne Sound Insulation[S]. International standard, 1997.
(Edited by YUAN Sai-qian)
Foundation item: Project (2002AA334060) supported by the Hi-tech Research and Development Program of China
Corresponding author: YU Hai-jun; Tel: +86-24-83686462; E-mail: yuhaijunneu@163.com