铁路车辆动态偏移量的在线检测
韩伯领1, 2,陈治亚1,鲁寨军1
(1. 中南大学 交通运输工程学院,湖南 长沙,410075;
2. 铁道部运输局,北京,100844)
摘 要:提出基于机器视觉的车辆动态偏移量检测方案,即在被测车辆非共线的4个点上安装高速电荷耦合器件(CCD),随着车辆的运动,CCD高速扫描钢轨,实时分析钢轨相对CCD的运动图像序列,得到各测点相对于钢轨的横向位移和垂向位移,综合各测点的相对偏移量得到整个车体的运行姿态,经进一步分析得到任意点的动态偏移量;研究检测原理,建立由各测点的动态偏移量计算描述车体运行姿态的5个变量和计算任意点动态偏移量的公式,研制模拟车体振动的平台,将所研发的系统与第3方地面测试设备对模拟平台动态偏移量的测试结果进行比较。研究结果表明,采用这2种方法测得相同位置的偏移量波形完全相似,对应幅值相差在-2~2 mm以内。
关键词:机器视觉;动态偏移量;车辆运行姿态;在线检测
中图分类号:U270.1 文献标识码:A 文章编号:1672-7207(2008)04-0787-06
On--line detection of offset generated by vibration of
rolling stock based on machine visionthe ision
HAN Bo-ling1, 2, CHEN Zhi-ya1, LU Zhai-jun1
(1. School of Traffic and Transportation Engineering, Central South University, Changsha 410075, China;
2. Transportation Bureau, Ministration of Railway, Beijing 100844, China)
Abstract: The scheme based on theoffset was put forward. The scheme is as follows: four high-speed charge couple devices are anon-collinearly mounted on car-body; with the movement of car-body, CCDs scans the the rails,and image is areanalyzed in real time to get four locations’ lateral and vertical displacement relative to rail; attitude ttitude of the whole car is obtained by analyzing displacement of those locations introduced, and some formulae to calculate five variables describing car-bodyattitude and random location’s offset are built. A test-rig-rig platform which can simulate vehicle’s vibration was developed. Test results obtained respectively respectively by this this system and other test instrument fixed on ground were compared. The results show that waveforms obtained by those two system are similar and corresponding amplitudes only differs within 2 mm.
Key words: machine vision; offset generated by vibration; attitude of vehicle; on-line detection
在保证运行安全的前提下,合理利用限界空间运输超限货物,必须制定符合当前实际情况的超限车运行条件,包括超限车通过建筑物或设备的运行条件和超限车与邻线列车交会时的运行条件[1],这取决于超限车与建筑限界之间的距离以及超限车与邻线列车间的距离,这2种距离与货物外形尺寸、机车车辆限界、建筑限界、线间距以及车辆在运行过程中的横向偏移量密切相关。车辆在线路上运行时,由于轮轨之间的相互作用,在各种垂向力和横向力的作用下,车辆系统会产生垂向和横向振动[2]。因此,研究车辆系统各种振动型式下的偏移量是合理确定超限车运行条件的基础[3-4]。影响动态偏移量的因素多且复杂,难以通过理论分析或仿真计算得到,必须通过实车试验测得。
目前,国内外研发的各种铁路货车装载超限检测或横向偏移量检测装置,都只能对机车车辆(包括装载的货物)进行静态检测或通过固定点时的超限情况进行检测,不能随机车车辆运动实时监控其运行姿 态,如:采用激光测距技术检测装载的货物是否超限、检测列车动态横向偏移量[5];利用双光幕拼接与图像处理技术对货车端部超限进行实时自动检测[6];采用激光偏振光反射及具有背景屏蔽功能的激光漫反射检测相结合的组合方式对超限货物进行检测;采用红外技术或CCD摄像和图像处理技术检测超限情况[7-12];采用结构光与CCD摄像相结合的方式进行铁路货车超限检测[13]。以上方法都是在铁路上选取某一截面架设龙门架安装检测设备,当列车通过龙门架时,检测其是否超限。而影响动态偏移量的因素很复杂,必须在机车车辆运行过程中实时监控、检测其动态偏移量,才能获得有规律性的数据。为此,本文作者提出一种以轨面和轨道中心线为基准的基于机器视觉的机车车辆动态偏移量检测系统,并研制完整的测试系统和能模拟车体振动的试验平台,进行验证性试验。
1 检测方案
要判断机车车辆在运行过程中是否会因动态偏移量过大而与邻线车辆发生刮碰现象或超限,所测得的动态偏移量的基准必须与限界基准一致。相关国家标准[14-15]中限界是相对于轨面及轨道中心线定义的,因弯道上外轨超高及坡度等问题,偏移量的测量也只能是相对于轨面的。同时,为保证机车车辆的运行安全,任何测试系统绝对不允许超出机车车辆限界,更不允许接触轨道,因此,测试系统必须是非接触式的。
由于车体在运行过程中由动载荷引起的弹性变形很小,监测车体的运行姿态时,可将车体视为刚体考虑。在某一点建立坐标系,车体的动态偏移量由沿3个坐标轴方向的平动和绕3根轴的转动引起的位移叠加得到。车体运行方向是沿铁路长度方向,而限界是一垂直于轨面和轨道中心线的横断面,因此,纵向平动可以不用考虑,只需考虑横移?y、浮沉?z、点头θ、摇头φ和测滚ψ这5种振动参数对车体动态偏移量的贡献。
根据上述要求,本文作者研制了基于机器视觉的高速CCD检测系统,系统结构如图1所示。该系统在被测车体非共线的4个点(不能安装在垂直钢轨顶面的同一平面内)上分别安装2 000帧/s的高速CCD,随着车辆的运动,分别记录钢轨相对该测点CCD(也就是车体)的运动图像序列,运用图像处理技术,可分析出每个测点相对于钢轨的横向位移和垂向位移。4个测点上的高速CCD受时间同步装置控制,同步采集数据,计算机对测得的数据进行整理、显示、存储和对外实时通信。综合3个测点上的3个横向位移和3个垂向位移,可以确定车体相对于2条钢轨的空间姿态和偏移量,得到车体的运行姿态后,即可通过刚体运动学相关公式得到车体上任意点(或固连于车体上的货物)的动态偏移量。在第4个测点所测得的偏移量可用于对结果进行验证。为叙述方便,称这一高速CCD及相应数字信号处理系统为动态偏移量传感器,由4套动态偏移量传感器组成车辆运动姿态检测系统。在车辆运动过程中,通过车速信号采集,得到测试车的运行速度和里程信息。
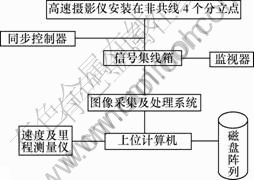
图1 车辆动态偏移量检测系统结构图
Fig.1 Structure of the rdynamic offset detection system
2 测试原理
2.1 计算坐标系
根据检测目的,建立轨面坐标系,以描述车体的运行姿态。任意时刻轨面坐标系如图2所示,原点O′ 一直位于右侧钢轨顶面的中点且沿钢轨随车辆前进方向作同步运动;X′ 轴位于轨面内指向车辆运行方向;Z′ 轴垂直轨面向下;Y′ 轴与轨面在同一平面,且垂直X′ 轴和Z′ 轴,指向由右手螺旋定则确定。
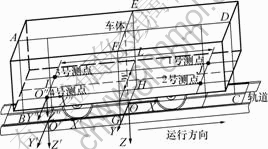
图2 车辆动态偏移量检测系统的测点布置及坐标系
Fig.2 Distribution of measuring points and definition of coordinate system of rdynamic offset detection system
为叙述方便,取纵横对称的车体进行讨论,并将车体相对于轨道的空间位置定义为正位置和实际位置。如图2所示,当车体纵向对称面ABCD内分别过2个上心盘中心I点和J点,且垂直于2个心盘中心连线IJ的2条直线与轨面上的交点为轨道中心线上的点,同时,车体相对轨道的空间状态沿其横向对称面EFGH对称时,该位置称为正位置;车体实际所处的位置称为实际位置(由于振动,一般相对正位置有所偏移)。为分析计算方便,计算坐标系O″X″Y″Z″由轨面坐标系O′X′Y′Z′平移至当车体处于正位置时的4号测点处得到(不是4号测点的实际位置);为便于分析使用输出结果,描述运动姿态的5个参数最后都以车体处于正位置时纵、横对称面的交线与轨面相交的1点为原点,各坐标轴与轨面坐标系对应轴平行的坐标系(图2中的OXYZ坐标系)为基准输出。直线上OXYZ坐标系即为限界的基准坐标系。
2.2 测点偏移量的检测
车体运行姿态的获得是以各测点测得的动态偏移量为基础。为提高测试精度,尽可能降低由于轨头形状变化带来的误差,本文采用双目立体视觉方案。下面以车体产生横向平移和垂向平移2种振动为例,简述检测原理。实际计算时,要考虑车体摇头、侧滚或点头运动对各测点平移量检测的影响。
如图3所示,O1′ 和O2′ 2点分别为2个摄像头的光心,设备安装后,O1′ 和O2′ 之间的距离b就已确定。在同一时刻,2个CCD对钢轨同一位置扫描各得到1幅图像,将2幅图像拼合起来予以分析。坐标系原点位于轨顶中点O,方位与前述的轨面坐标系O′X′Y′Z′完全一样,即Y0=0,轨面离光心的垂向距离为Z0。在初始时刻,轨顶面中点O在2个CCD中的位置分别为D点和E点,经标定可得到Z0和焦距f;在t时刻,车体相对轨道产生横向和垂向位移,O1′,O2′,D和E分别移到O1′t,O2′t,Dt和Et,轨顶图像中点离CCD成像面中点O1″和O2″的距离由初始时刻的YP10和YP20变为t时刻的YP1t和YP2t。因此,在t时刻镜头光心(固连于车体上)的动态偏移量为
,
。

(a) 单个测点双目立体视觉计算原理图 ;(b) 同一测点2个CCD实测的轨顶图像;
(c) 通过同一测点2个轨顶图像的宽度等信息相关性
图3 单个测点双目立体视觉测量偏移量
Fig.3 Detection of offset by binocular stereovisionof
由三角关系可以得到:
。
所以,,
。
其中:
,
(在图示情况下,YP20,YP1t和YP2t为正值,而YP10为负值)。则:

所以,
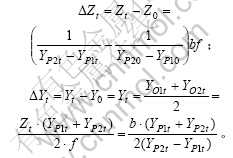
轨顶图像中点Dt和Et是通过分析同一时刻的2张相片的相关性得到的,由于采用了优化的自动阀值,中点查找的准确度高,稳定性好。如图3(c)所示,相关系数最大的2个尖峰分别对应2个轨顶图像的中点。可见,动态偏移量与轨面宽度没有关联。因此,采用双目检测方式可以避免因轨头磨损带来的误差。
2.3 车体姿态的计算
4个测点除了不能安装在垂直钢轨顶面的同一平面内外,可以分布在车体上其他便于安装和测量的位置,都可以检测并分解出车体的浮沉、横摆、点头、摇头和侧滚振动。根据大部分车辆的实际情况,以下分析按4个测点均布置于车体底架以下同一平面、各测点顺序连线能形成矩形的情况考虑,采用图2所示的轨面坐标系O′X′Y′Z′。设某检测点在静态时为点Pi0 (i=1, 2, 3, 4),t时刻对应位置为Pit (i=1, 2, 3, 4)。以下各图中,虚线为各测点没有偏移量时的结果,实线为t时刻车体的姿态。
由于不必考虑纵向振动的影响,因此,只需分析车体的横摆?Yt、浮沉?Zt、侧滚ψt、点头θt和摇头
,任一测点的垂向位移主要由车体的浮沉、侧滚和点头振动引起,横向位移由车体的横摆、侧滚和摇头振动引起。由于在实际情况中,点头、摇头和测滚角都很小,因此,可分以下几种情况独立求解各转角。
2.3.1 摇头角
的计算
如图4所示(图示摇头角为负值),有:

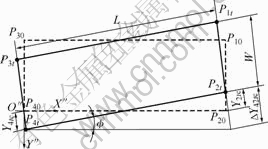
图4 车体摇头角
的计算(俯视图)
Fig.4 Yaw’s calculation of car-body (top view)
2.3.2 点头角θ的计算
如图5所示(车体侧面视图)(车体侧面视图),有:
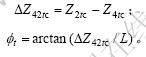

图5 车体点头角θ的计算(侧视图)
Fig.5 Pitch’s calculation of car-body (side view)
2.3.3 侧滚角ψ的计算
如图6所示(图示侧滚角为负),设P40与P30在Y方向的距离为W,则


图6 车体侧滚角ψ的计算(前视图)
Fig.6 Rolling’s calculation of car-body (front view)
2.3.4 平移量的确定
在任意时刻t,各测点检测到Yitc和Zitc。根据成像原理,考虑摇头角、点头角和测滚角的影响,在Y方向的变化量为:

在Z方向的变化量为:

若以4号测点为基准点,则车体的平移分量为
和
。
上述各式中都没有用到1号测点的数据,因此,第1号测点的数据可用于检验另3个测点所测数据的正确性。
2.4 任意点动态偏移量的计算
得到车体的运行姿态后,即可通过刚体的运动学分析得到任意P点的动态偏移量。设P点初始时刻相对轨面坐标系的坐标P0为(x0, y0, z0),t时刻的坐标 Pt为(xt, yt, zt)。
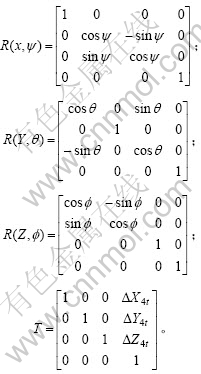
则
,动态偏移量
为:
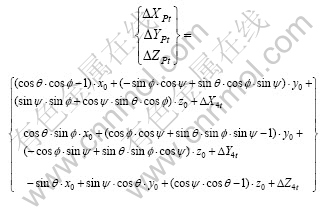
由于车体的点头、摇头和测滚角(θ,φ,ψ)都很小,同时不考虑纵向偏移量,故上式可简化为:
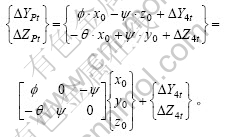
上式以4号测点为基准,分离出各种振动对横向和垂向振动偏移量的贡献。实际上,可以任意选取感兴趣的基准点进行分离。
3 试验验证
按照上述方案,研制了完整的测试系统。为验证系统测试方法的正确性和精确度,研制了能模拟车辆6种振动的试验台。在地面安装高精度测试系统与本系统同时检测该平台的振动偏移量,对比测试结果如图7所示,其中,虚线代表采用地面检测系统所得测试结果,实线代表采用本文研制的检测系统所得测试结果。通过比较分析各波形和对应位置的幅值发现,基于机器视觉的动态偏移量检测系统与地面测试系统测试结果相差在-2~2 mm以内,采用这2种方法测得的偏移量波形完全相似。
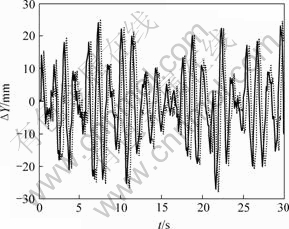
实线表示采用本文方法所得结果;
虚线表示采用地面激光仪所得结果
图7 基于机器视觉的动态偏移量检测系统与
地面测试系统测试结果比较
Fig.7 Comparison of test results obtained by detection system of dynamic offset based machine vision and fixed on ground
4 结 论
a. 基于机器视觉的车辆动态偏移量检测方案,以轨面和轨道中心线为测量基准,便于判断运行中的车辆是否超限,满足测试要求。
b. 能够由各测点的动态偏移量计算描述车体运行姿态的5个变量,进而计算任意点的动态偏移量。
c. 采用双目立体视觉检测测点的动态偏移量,可以有效降低轨顶侧面磨损带来的误差。
d. 研制了基于机器视觉的车辆动态偏移量检测系统和模拟车体振动的平台,并进行了验证性试验。所研发的系统与第3方地面测试设备测得的相同位置的偏移量波形完全相似,对应幅值相差在-2~2 mm以内。
参考文献:
[1] 中华人民共和国铁道部. 铁路超限货物运输规则[M]. 北京: 中国铁道出版社, 2005.
Railways Ministry of People’s Republic of China. Transportation regulation of railway out-of-gauge freight[M]. Beijing: China Railway Press, 2005.
[2] 王福天. 车辆系统动力学[M]. 北京: 中国铁道出版社, 1994.
WANG Fu-tian. Vehicle system dynamics[M]. Beijing: China Railway Press, 1994.
[3] 鞠殿铭, 王久梗, 郭维鸿. 超限车横向振动最大偏移量计算的方法[J]. 北方交通大学学报, 1999, 23(3): 48-52.
JU Dian-ming, WANG Jiu-geng, GUO Wei-hong. Calculating method on maximum offset generated by lateral vibration of vehicle loaded with out-of-gauge goods[J]. Journal of Northern Jiaotong University, 1999, 23(3): 48-52.
[4] 鞠殿铭, 韩 梅, 郭维鸿. 超限车侧滚振动偏移量的确定方法及影响因素分析[J]. 铁道学报, 1996, 18(6): 63-68.
JU Dian-ming, HAN Mei, GUO Wei-hong. Determination and analysis of affecting factors on the offset generated by rolling vibration of vehicle loaded with out-of-gauge goods[J]. Journal of the China Railway Society, 1996, 18(6): 63-68.
[5] 谢锦妹, 杨凤春, 冯毅杰, 等. 激光测距技术在列车动态横向振动偏移量测试中的应用[J]. 铁道机车车辆, 2007, 27(5): 31-32.
XIE Jin-mei, YANG Feng-chun, FENG Yi-jie, et al. Application of laser ranging technique in the measurement of train dynamic transversal vibrations offset[J]. Railway Locomotive & Car, 2007, 27(5): 31-32.
[6] 熊 军, 仲思东, 毛庆洲. 利用测量光幕检测货物列车端部超限[J]. 铁道车辆, 2005, 43(11): 35-37.
XIONG Jun, ZHONG Si-dong, MAO Qing-zhou. Inspection of out-of-gauge of freight train ends with the application of measurement light curtain[J]. Rolling Stock, 2005, 43(11): 35-37.
[7] 张光远. 铁路超限检测系统研究[D]. 成都: 西南交通大学交通运输学院, 2005.
ZHANG Guang-yuan. Study on the detecting system of railway out of gauge[D]. Chengdu: College of Traffic and Transportation, Southwest Jiaotong University, 2005.
[8] 朱为鹏. 基于数字图像处理的货车超限监测算法研究[D]. 成都: 西南交通大学机械工程学院, 2003.
ZHU Wei-peng. The a1gorithm research on freight system train gauge monitoring based on digita1 image processing[D]. Chengdu: College of Mechanical Engineering, Southwest Jiaotong University, 2003.
[9] 毛庆洲, 李清泉, 陈长军, 等. 铁路货车装载尺寸超限自动测量技术研究[J]. 光学仪器, 2007, 29(5): 8-12.
MAO Qing-zhou, LI Qing-quan, CHEN Chang-jun, et al. Research of auto-measurement technology for railway wagon loading size[J]. Optical Instruments, 2007, 29(5): 8-12.
[10] Edwards J R. Improving the effectiveness and efficiency of railcar safety appliance inspection using machine vision technology[D]. Illinois: University of Illinois at Urbana- Champaign, 2006.
[11] Edwards J R, Hart J M, Todorovic S, et al. Development of machine vision technology for railcar safety appliance inspection [EB/OL]. [2007-10-25]. http://cee.uiuc.edu/railroad/CEE/pdf/ Edwards%20et%20al%20IHHA-STS-2007-07-0104F.pdf.
[12] 于 冬, 顾培亮, 陈 钟, 等. 铁路货车装载状态监视和超限检测系统的研究[J]. 中国铁道科学, 2004, 25(5): 141-144.
YU Dong, GU Pei-liang, CHEN Zhong, et al. Research on the monitoring state and overloading detection system of freight car loading[J]. China Railway Science, 2004, 25(5): 141-144.
[13] 孙丽丽, 肖世德. 基于结构光原理的铁路货车超限检测算法研究[J]. 计算机应用, 2005, 21(1): 213-214.
SUN Li-li, XIAO Shi-de. Algorithm research on freight train gauge inspection system based on structure lighting theorem[J]. Computer Applications, 2005, 21(1): 213-214.
[14] GB 146.1—83, 标准轨距铁路机车车辆限界[S].
GB 146.1—83, Rolling stock gauge for standard gauge railways[S].
[15] GB 146.2—83, 标准轨距铁路建筑限界[S].
GB 146.2—83, Structure gauge for standard gauge railways[S].
收稿日期:2008-03-05;修回日期:2008-05-20
基金项目:铁道部科技研究开发计划资助项目(Z2007-079)
通信作者:韩伯领(1964-),男,江苏淮安人,博士研究生,讲师,高级工程师,从事铁路运输研究;电话:0731-2655294;E-mail: qlzjzd@mail.csu.edu.cn