
Competitive growth of high purity aluminum grains in
directional solidification
ZHANG Jiao(张 佼)1, SHU Da(疏 达)1, WANG De-lin(王德林)2,
SUN Bao-de(孙宝德)1, CHEN Gang(陈 刚)3
1. State Key Laboratory of Metal Matrix Composites, Shanghai Jiao Tong University,
Shanghai 200030, China;
2. Huabei Petroleum Cangzhou Feida Oil Equipment Company Ltd, Cangzhou 061000, China;
3. Analysis and Testing Center for Inorganic Materials, Shanghai Institute of Ceramics,
Chinese Academy of Sciences, Shanghai 200037, China
Received 28 July 2006; accepted 15 September 2006
Abstract: A self-made directional solidification setup was used to prepare high purity aluminum ingots of 100mm in diameter. The morphology of the growth interface was detected by SEM and AFM, and the grain lattice orientation was detected by XRD. The results indicate that the grains suffer competitive growth under any conditions in experiments. The lattice orientation of the preferred grains is determined by the flow field above the solid-liquid interface. The horizontal lattice position does not change during the growth process. However, the lattice orientation in the growth direction varies with the growth velocity and approaches to [100] gradually during the growth process.
Key words: high purity aluminum; competitive growth; directional growth; lattice orientation
1 Introduction
The crystal properties are determined by grain morphology and lattice orientation in directional solidification[1]. For the refinement of high purity aluminum by directional solidification, the single crystal is of great advantage to the segregation of impurities. In addition, single crystal has homogeneous physical and chemical properties, and its processing property will be improved greatly. In order to obtain single crystal, seeds with a preferred orientation or crystal selection method was used[2-4]. However, in case that these technologies cannot be used, the competitive growth of grains can be utilized to form single crystal. In fact, the grain growth is a complex dynamic 3-D process affected by the temperature field, solute field and flow field. Most of the solidification processes undergo at high temperature and are unobservable. It is very difficult to investigate and control the grain growth. Thus, the model transparent alloy of succinonitrile-acetone is often used for observation of the dynamic process[5-9]. The limitation of these studies is that the orientation of grains can not be detected. Bi-crystal with different orientation[4,10] was used to research the effect on the growth, and the results[10] showed that the misoriented dendrite was retarded by the preferred. However, there is no more detailed results of the competitive growth of columnar and cellular crystal.
In order to avoid the wall effect on the grain growth, the d100 mm high purity aluminum ingots were fabricated under different growth rates by a self-made directional solidification device in the present work. Through the detection of XRD, the influence of lattice orientations on grain growth was studied. The variation of grains during growth process was also investigated.
2 Experimental
The self-made directional solidification setup is shown in Fig.1. The small coil at the lower part of the crucible acted as a booster heater to ensure that the growth interface keeps lightly convex during growth process. The toroidal electromagnetic stirrer may cause the circumferential fluid flow when applied. The raw material used in the experiments was the three-layer refined aluminum. The total of impurities was less than 60×10-6.
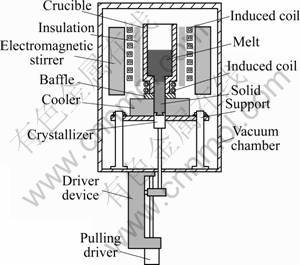
Fig.1 Experiment setup of bulk sample
The solidified bulk samples were cut and polished, then etched by 1?1 HF-HNO3 mixture, and rinsed by distilled water and alcohol for later detection.
The real-time growth interface was obtained by pouring the rest melt during the growth process and was detected after being rinsed by alcohol without etching.
3 Results and discussion
3.1 Characteristics of growth interface
Atom Force Microscope was used to detect the details of the boundary and the results are shown in Fig.2. As shown in Fig.2(a), there is a dune shape bulge at the sides of grains. This is similar to the phenomena reported in Ref.[5], but no details of the boundary were given there.
Due to the intercrystalline segregation, the concen- tration at boundary is far greater than that of inner grain. It is found that the depth of the tri-grain intersection is about 0.5 mm deeper than that of the double grain boundary, as shown in Fig.2(c).
3.2 Grain growth without electromagnetic stirring
When the electromagnetic stirrer is not adopted, there is only radial flow Vr in the melt above the solid-liquid interface resulting from natural convection and the standing wave caused by the induction heating coils. Because the frequency of the heating coils is 7 kHz, the stirring effect is quite weak. As a result, the magnitude of radial flow Vr is small, and the morphology of grains is not affected. The cross section of the grains is nearly hexagon.
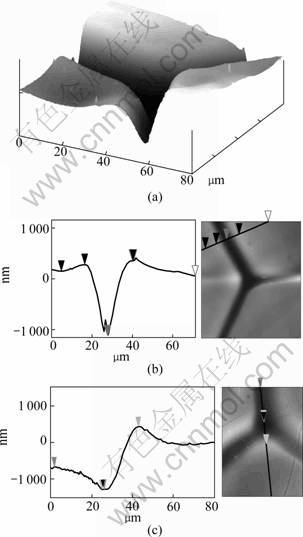
Fig.2 Morphologies of grain boundary: (a) Tri-grain inter- section; (b) Double grain boundary; (c) Change of depth of groove
In the primary solidification of ingot, the number of grains is great, and the diameter of cellular grain is small. After a period of growth, some grains grow up, while others are restrained, and a preferred grain grows up to a single crystal finally, as shown in Fig.3. By statistics, the number of grains at different heights along the ingots decreases gradually, and the grains become a single grain finally. Moreover, with increasing the growth velocity, the progress will be delayed as shown in Fig.4.
In this paper, the process of the preferred grain growth out of small grains to a single crystal is called the competitive growth. The investigation on the lattice orientation of the grains was performed by X-ray diffraction (Cr Kα) pole figures which were obtained byΦ-scan method. The sample position was confirmed by ω, χ and Φ. In this experiment, χ is 54.74?, while ω, i.e. half of the 2θ, is 32?. When Φ is changed from 0? to 360?, the data collection is carried out every 5?. After that, the pole figure can be calculated according to the 72 groups of data. Fig.5 shows the (100) pole figures of the marked grains in Fig.3.
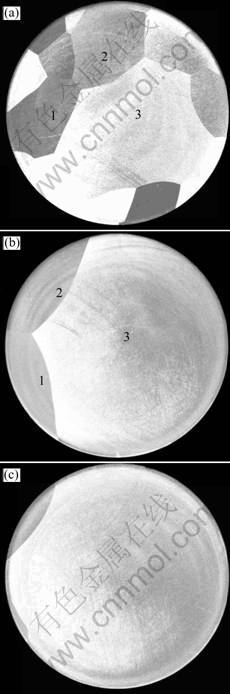
Fig.3 Cross-section at different heights of d100 mm ingot grown without stirring (velocity=10 mm/h): (a) 30 mm; (b) 60 mm; (c) 80 mm
The growth direction of all grains is almost (100). The only difference between each other is the angle shifting from the (100). It can be found from Fig.5 that the grain 3 which shifts the smallest angle develops to a single crystal finally.
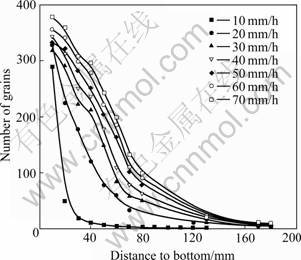
Fig.4 Relationship between number of grains of cross-section at different heights and growth velocities
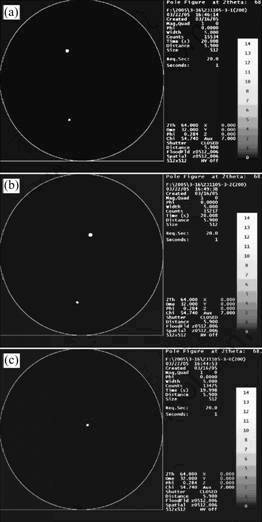
Fig.5 (100) pole figure of three adjacent grains marked in Fig.3(a): (a) Grain 1; (b) Grain 2; (c) Grain 3
The lattice orientation of the grains in the growth direction will approach to [100] gradually during the growth process, which is demonstrated in Fig.6, where the angle α increases after a period of growth.
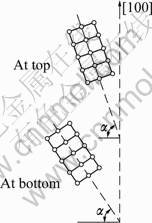
Fig.6 Sketch of process of grain approaching to [100] during growth
The lattice orientation of the final single crystals obtained at different velocities was also detected. The results indicate that the angle α decreases with the growth velocity (see Fig.7).
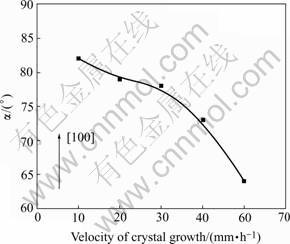
Fig.7 Lattice orientation of single crystal dependence on growth velocity without stirring
Although the grains look twisting or shifting during the competitive growth process in the macrograph, the horizontal lattice position does not vary in the crystal growth process or with the growth velocity.
3.3 Competitive growth with electromagnetic stirring
When the stirrer is applied, a strong shear flow is induced over the solid-liquid interface. As reported in Refs.[11-12], the columnar grains deflected from the growth direction towards the upstream direction when a flowing melt solidified. The deflection angle got to higher when the flow velocity became greater or the concentration of solute increased. However, the conditions referred above are different to the present work. The tip of the cellular grain is plane and the diameter of grains is so big that it is difficult to form the asymmetric concentration fields at bilateral side of grains. But the boundary between grains is groove about 1.2 mm in depth, and the solid region sides adopt a sand dune shape. It is possible to form the asymmetric concentration field beside the dune. In the present experiments, the melt flow is circumferential, and the greatest flow velocity exists near the crucible wall. The growth direction of the grain side will deflect towards upstream direction. This leads to the deformation of the boundaries, and this deformation becomes more serious near the edge of the grains, as shown in Fig.8. The tendency of competitive growth will not be broken. The number of grains varies along the length of the ingot as shown in Fig.9.
The lattice orientation of the grains cut by the cross-section at different heights was detected by XRD to determine the characteristics of the preferred grain.
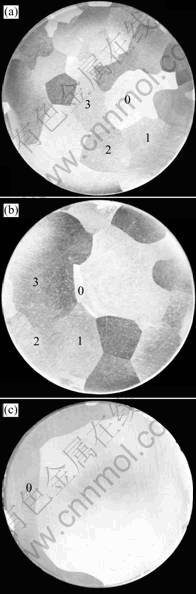
Fig.8 Cross-section at different heights of d100 mm ingot grown with stirring (velocity=40 mm/h): (a) 30 mm; (b) 80 mm; (c) 160 mm
And the (100) pole figures of the grains marked in Fig.8 are shown in Fig.10. Comparing Fig.5 with Fig.10, we can find that the grain 0 in Fig.10 which does not have the smallest deflection angle grows to a single crystal, instead of the grain 3 which shifts the smallest angle from [100]. This is quite different from the conditions of the sample made without stirring (see Fig.6). According to the difference of flow field under the two kinds of growth conditions, we can conclude that the drastic flow contributes to this.
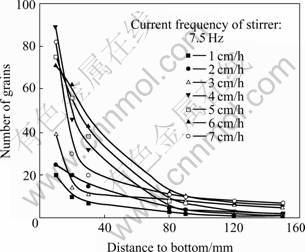
Fig.9 Number of grains of cross section at different heights
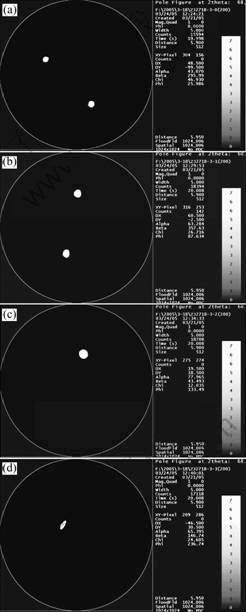
Fig.10 (100) pole figures of four adjacent grains marked in Fig.8(a): (a) Grain 0; (b) Grain 1; (c) Grain 2; (d) Grain 3
Although the grain shape changes from hexagon to a random geometry, the horizontal lattice position remains unchanged accordingly, as shown in Fig.11.
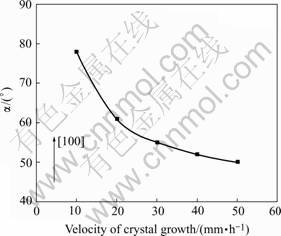
Fig.11 Dependence of lattice orientation of single crystal on growth velocity under stirring
When the flow melt solidifies[13], the columnar grains deflect to the upstream direction, and the lattice orientation of the grains declines at the same angle. On the contrary, in the present work the lattice orientation of the cellular grains will not vary along the reverse direction of the flow.
4 Conclusions
1) All the grains are suffered competitive growth process, and the variation of grain spatial location will not lead to the variation of horizontal lattice position either with electromagnetic stirring or not.
2) The lattice orientation of the preferred grain is associated with the flow field above the S/L interfaces. When only weak radial flow exists, the grain which has the smallest deflection angle to [100] grows up to a single crystal. On the contrary, while the strong circumferential flow exists, the preferred grain is determined by the matching between its lattice orientation and the flow field. However, the lattice orientation in the growth direction of the preferred grain approaches to [100] gradually during the growth process for both cases.
References
[1] ZHOU Yao-he, HU Zhuang-qi, JIE Wan-qi. Solidification Technology [M]. Beijing: China Machine Press, 1998. (in Chinese)
[2] FU Hen-zhi, HE Guo, LI Jian-guo. Observation of competitive growth in a directionally solidified Nickel base single crystal superalloy [J]. Acta Metall Sinica, 1997, 33(12): 233-239. (in Chinese)
[3] DING G L, TEWARI S N. Dendritic morphologies of directionally solidified single crystals along different crystallographic orientations [J]. J Crystal Growth, 2002, 236: 420-428.
[4] FU H Z, XIE F Q. The conduct of nucleation and recalescence in the process of the negative temperature gradient melt solidification [J]. Sci Tech Advan Mater, 1997, 2: 193-199.
[5] NO?L N, JAMGOTCHIAN H, BILLIA B. Influence of grain boundaries and natural convection on microstructure formation in cellular directional solidification of dilute succinonitrile alloys in cylinder [J]. J Crystal Growth, 1998, 187: 516-526.
[6] NO?L N, JAMGOTCHIAN H, BILLIA B. In situ and real-time observation of the formation and dynamics of a cellular interface in a succinonitrile -0.5wt% acetone alloy directionally solidification in a cylinder [J]. J Crystal Growth, 1997, 181: 117-132.
[7] REX S, KAUERAUF B, ZIMMERMANN G. Directional solidifica- tion of cellular arrays in a transparent organic alloy [J]. Adv Space Res, 2002, 29: 511-520.
[8] KAUERAUF B, ZIMMERMANN G. Directional cellular growth of succinonitrile-0.075wt% acetone bulk samples (Part 1): Results of space experiments [J]. J Crystal Growth, 2001, 223: 265-276.
[9] MA D X. Development of dendrite array growth during alternately changing solidification condition [J]. J Crystal Growth, 2004, 260: 580-589.
[10] D’SOUZA N, ARDAKANI M G, WAGNER A. Morphological aspects of competitive grain growth during directional solidification of a nickel-base superalloy [J]. CMSX4 Journal of Materials Science, 2002, 37: 481-493.
[11] XIAO Ya-ping, ZHANG Xin-ming, TANG Jian-guo, DENG Yun-lai, CHEN Zhi-yong. Textures in high purity aluminum foils and AA3004 sheets [J]. Trans Nonferrous Met Soc China, 2003, 13(3): 491-498.
[12] ENGLER O, HUH M Y. Evolution of the cube texture in high purity aluminum capacitor foils by continuous recrystallization and subsequent grain growth [J]. Mater Sci Eng A, 1999, 271(1): 371- 381.
[13] MURAKAMI K, FUJIYAMA T.
Influence of melt flow on the growth directions of columnar grains and columnar dendrites [J]. Acta Metall, 1983, 31(9): 1425-1432.
(Edited by HE Xue-feng)
Foundation item: Project(2002AA336072) supported by the High-tech Research and Development Program of China; Project(03XD14009) supported by the Program of Shanghai Subject Chief Scientist
Corresponding author: ZHANG Jiao; Tel: +86-21-64476859; E-mail: zj119@sjtu.edu.cn