
Synthesis of TiAl-Al2O3 composites by
high energy milling and hot-press sintering
ZHU Jian-feng(朱建锋)1, 2, GAO Ji-qiang(高积强)1, WANG Fen(王 芬)2
1. State Key Laboratory for Mechanical Behavior of Materials,
Xi’an Jiaotong University, Xi’an 710049, China;
2. School of Materials Science and Engineering,
Shaanxi University of Science and Technology, Xianyang 712081, China
Received 28 July 2006; accepted 15 September 2006
Abstract: A sub-microstructure titanium aluminide alloy /Al2O3 (3A) composite was obtained by crystallization of the amorphous powders, which were prepared by mechanical alloying (MA) in a planetary ball milling system using Ti-Al-TiO2 as raw materials. The experimental results show that, when the milling time increases up to 30 h, the hcp Ti(Al) supersaturated solid solution disappears, only amorphous phase is left. The compact samples were synthesized by hot-press to 1 200 ℃ with the amorphous as a precursor; the final phases of the matrix and strengthened phase are γ-TiAl and Al2O3. The phases come from in situ crystallization and transformation. The samples, fabricated from the amorphous phase by hot press sintering, have high bending strength and fracture toughness.
Key words: titanium aluminide intermetallics; Al2O3; composite; mechanical alloying; crystallization
1 Introduction
Gamma-based titanium aluminides offer the potential for component mass savings up to 50% over conventional superalloys in aerospace applications [1]. These materials are also characterized by a high melting point, and high resistance against oxidation. Until now, the widespread use of TiAl is hampered by the poor ductility and fracture toughness at low temperatures and poor strength at high temperatures [2, 3]. To improve these deficiencies, attempts are made with respect to the control of the microstructure, such as grain refinement, and of precipitation of a second phase [4-6].
Conventional methods of these composite processes, such as hot pressing of TiAl-Al2O3 powder mixtures or high temperature pressure infiltration of porous alumina performs with the liquid intermetallic, lack economical feasibility [7]. The process of mechanical alloying by ball milling offers advantages for the production of TiAl compounds. This has been investigated [8], and later the TiAl intermetallic materials reinforced with ceramics particles were also studied, such as TiC, SiC, and Al2O3. Some high mechanical properties have been gained [9, 10].
The present investigation is to fabricate nano- structured TiAl composites strengthened with oxide dispersion (Al2O3) by mechanical alloying and in situ crystallization. The process of high energy milling of Al, Ti, and TiO2 blended powders was examined by analyzing the progress of mechanical alloying. The subsequent reaction process in hot press sintering was also investigated by XRD and SEM analyses in order to understand the reaction mechanism of this system. At the same time, the effects of TiO2 content on the mechanical properties were also studied to prepare high performance TiAl composites.
2 Experimental
Titanium (Ti) powder (50 μm) and aluminum(Al) powder(75 μm) were used as precursor powder mixtures in milling experiments.
The powders were blended in compositions accord-ing to reaction formula (1), and the detail constitute is shown in Table 1.
xTi+(x+7) Al +3TiO2→(x+3)TiAl+2Al2O3 (1)
Table 1 Compositions of starting powders
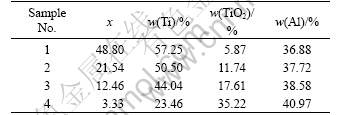
The mechanical alloying was carried out at room temperature in a planetary mill at a rotation speed of 750 r/min. The milling processes were interrupted every 6 h and an appropriate amount of the as-milled powders were extracted to examine the progress of milling. The milled powders with almost amorphous structure were consolidated by hot-pressing at 1 200 ℃ under 30 MPa in a vacuum furnace for 1 h. Techniques used to examine the status of MA included X-ray diffraction (XRD) and scanning electron microscopy (SEM). The X-ray analysis was performed using a D/max-2200PCX diffractometer with monochromatic Cu Kα radiation (40 kV, 30 mA). The mechanical properties were testified in a PT-1036 multifunctional mechanical test machine.
3 Results and discussion
Fig.1 shows the X-ray diffraction patterns of the mechanically alloyed Ti-Al-TiO2 powders after being milled for different time increments. With continuously increasing the milling time, all of the diffraction patterns are combined to one broadened pattern, as a result of the heavy deformation and the small size of the crystallites being transformed into a nonequilibrium phase.
Fig.2 shows the morphology of the mechanically alloyed Ti-Al-TiO2 powders less than 50 μm. It is seen that round-shaped particles are formed after milling as shown in the overall appearance of the powders. The composite structure becomes homogeneous with small sizes of particles. The surface morphology of the particle is shown where the heavily deformed surface can be observed, especially the relatively large-size particles.
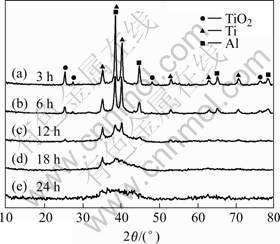
Fig.1 Alloying process of composite powders of sample 3
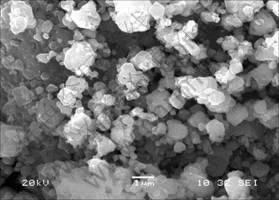
Fig.2 SEM micrographs of mechanically alloyed powder of sample 3
Fig.3 shows a typical X-ray diffraction pattern of the milled powders and that of their sintered compacts. The milled powders show broad amorphous phase. On the other hand, their sintered compacts show sharp crystalline peaks from γ-TiAl phase with small peaks from α2-Ti3Al and Al2O3 phase. The detail of the mechanical alloying process is described and discussed elsewhere [11].

Fig.3 X-ray diffraction patterns of amorphous powders and their hot-press sintered compacts at 1 200 ℃
Fig.4(a) shows the microstructure of the 24 h milled powders after being hot press sintered to 1 200 ℃. It is seen that the powder has a homogeneous structure, and the Al2O3 particles (light color) have fine grained microstructure with grain size of less than 1 μm. Fig.4(b) shows the microstructure of a sample made by direct hot-press sintering from the same composition of Fig.4(a); it has coarse and cluster microstructure with many pores. From the above image, one sees that the samples made by mechanical alloying and hot-press have a very fine and uniform microstructure with very few pores. The phases of TiAl and Ti3Al are not distinguished from SEM image.

Fig.4 SEM micrographs of sample 3 after sintered at 1 200 ℃: (a) Mechanically alloyed and hot-press sintered; (b) Hot-press sintered
Table 2 lists the mechanical properties of different samples. From this table, it is seen that the mechanical properties improve with the increase of TiO2. The bending strength and fracture toughness decline when TiO2 content exceeds 17.61%. Sample 2 has the highest fracture toughness with a little low bending strength compared with the other samples.
Table 2 Mechanical properties of samples made by MA-HP
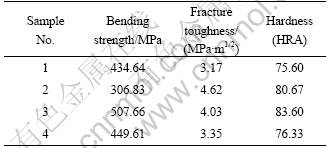
The TiAl-Al2O3 composites synthesized by high energy milling and hot-press sintering attributed to fine grain size and uniform microstructure. The fine Al2O3 dispersion along the γ-TiAl crystal boundary also strengthened the materials.
4 Conclusions
Mechanical alloying (MA) combined with hot press sintering (HP) processes were employed to synthesize TiAl/Al2O3 composite. The fully dense bulk samples have a fine grained and uniform microstructure. The mechanical tests show that the ratio of precursor blended materials of Ti, Al and TiO2 has important effect on the mechanical properties. When a proper composition is adopted, the bending strength and fracture toughness will be improved, and the value in this experiment is 507.66 MPa and 4.03 MPa?m1/2, respectively.
References
[1] DURLU N. Titanium carbide based composites for high-temperature applications [J]. J Eur Ceram Soc, 1999, 19: 2415-2419.
[2] GUAN Z Q, PFULLMANN TH, OEHRING M, BORMAN R. Phase formation during ball milling and subsequent thermal decomposition of Ti-Al-Si powder blends [J]. Journal of Alloys and Compounds 1997, 252: 245-251.
[3] PERKINS R A, CHIANG K T, MEIER G H. Formation of alumina on Ti-Al alloys [J]. Scripta Metall, 1987, 21: 1505-1510.
[4] WANG Fen, FAN Zhi-kang, ZHU Jian-feng. Reaction synthesized alumina fiber reinforced TiAl intermetallic matrix composite [J]. Rare Metal Materials and Engineering, 2006(Suppl 1): 1293-296.(in Cinese)
[5] VANMETER M L, KAMPE S L, CHRISTODOULOU L. Mechanical properties of near-γ titanium aluminides reinforced with high volume percentage TiB2 [J]. Scripta Metall Mater, 1996, 34(8): 125-1256.
[6] RAO K P, DU Y J. In situ formation of titanium silicides-reinforced TiAl-based composites[J]. Mater Sci Eng, 2000, A277: 46-56.
[7] CLAUSSEN N, GARCIA DE, JANSSEN R. Reaction sintering of alumina-aluminide alloys (3A)[J]. J Mater Rev, 1996, 11(11): 2884-2888.
[8] ITSUKAICHI, MASUYAMA K, UMEMOTO M, OKANE I, CABANAS-MORENO J G. Mechanical alloying of Al-Ti powder mixtures and their subsequent consolidation[J]. J Mater Res, 1993, 8(88): 1817-1828.
[9] ZHOU L Z, GUO J T, FAN G J. Synthesis of NiAl-TiC nanocomposite by mechanical alloying elemental powders[J]. Mater Sci and Eng, 1998, A249 (10): 103-108.
[10] CHOO H, NASH P, DOLLAR M. Mechanical properties of NiAl-AlN-Al2O3 composites[J]. Mater Sci and Eng, 1997, A239/240: 464-471.
[11] ZHU Jian-feng, GAO Ji-qiang, WANG Fen. Fabrication of Al2O3-Ti aluminides composite by mechanical alloying process [J]. Rare Metal Materials and Engineering, 2006(Suppl 1): 143-146.(in Chinese)
(Edited by PENG Chao-qun)
Foundation item: Projects(50432010, 50372037) supported by the National Natural Science Foundation of China; project(SUST-B14) supported by the Scientific Research Foundation of Shaanxi University of Science and Technology, China
Corresponding author: ZHU Jian-feng; Tel: +86-29-33579720; E-mail: zhujf@sust.edu.cn