
Mensuration and simulation of mold filling process in
semi-solid die-cast of aluminum alloy
YANG Yi-tao(杨弋涛), WANG Jian-fu(王建甫), ZHANG Heng-hua(张恒华) , SHAO Guang-jie(邵光杰)
School of Materials Science and Engineering, Shanghai University, Shanghai 200072, China
Received 28 July 2006; accepted 15 September 2006
Abstract: To understand the flow trace of semi-solid slurry in mold cavity, some thermocouples were inserted in mold cavity, and the reaction timing of thermocouples showed the arrival of fluid. The filling time and rate were estimated by comparison between the experiment and calculation. The introduction of computer simulation technique based on ADSTEFAN was to predict injection- forming process and to prevent defects during trial manufacture of various parts. By comparing the formed appearance of parts in experiment and in simulation, and observing the relationship between internal defects inspected by X-ray or microscope and the flow field obtained in simulation, it was indicated that both have quite good agreement in simulation and experiment. Right predictions for cast defects resulted from mold filling can be carried out and proper direction was also proposed. The realization of numerical visualization for filling process during semi-solid die-cast process will play an important role in optimizing technology plan.
Key words: mold filling; simulation; semi-solid process; Al alloy
1 Introduction
Semi-solid die cast process with various features [1-6] is a forming technology developed on the base of general molten metal die cast, and has gradually become maturity as near-net-shape processing of material. Compared with traditional die cast, there are a lot of unsolved theoretical and technological problems in semi-solid die cast process. Especially, because mature data are absent from the design of gating system, design experiences for die cast of molten metal are temporarily used. To grasp filling process of semi-solid die cast, the filling trace of semi-solid molten metal in mold cavity needs to be measured for storing some basic data by experiments. To optimize this filling process, to aid the design of die cavity, to forecast and to tackle cast defects concerned with flow and solidification, the introduction of computer simulation will play an effective promoting role in enhancing technique level of semi-solid die cast and product quality[7]. As one of the steps in which test samples and actual parts are systematically tried, using simulation technique during trial manufacture of Al alloy parts aims at optimizing forming technology and improving the quality of products.
2 Method
An induction device of medium frequency with circled multi-position heated the billets of Al alloy (A356) to semi-solid state, and then die-castings were formed by using die cast machine of 500 t in our laboratory. The chemical compositions of A356 used in this study is shown in Table 1. To measure the filling trace of semi-solid molten metal in die cavity, thermocouples were inserted in different positions of the mold cavity, and the reaction timing of thermocouples showed the arrival of fluid. The appearance of test piece and the inserted positions of thermocouple are shown in Fig.1. The trial manufacture of actual parts was carried out on the basis of previous works which had been completed by our group [8]. The reaction timing of thermocouples was recorded during experiment by industrial control computer with high recording speed of 100 points per second. Casting/die-casting simulation software ADSTEFAN [9] was used for simulating the filling process of semi-solid die cast. The main physical properties and calculation conditions in simulation are shown in Tables 2-4. Ref.[10] and standard database supplied by cast simulation software were referred in the selection of physical properties. The kinematic viscosity was so expressed with subsection function related to solid fraction that semi-solid state was reflected.
Table 1 Chemical compositions of aluminum alloy A356 used in experiment (mass fraction, %)

Table 2 Physical properties of aluminum alloy A356
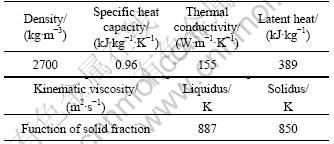
Table 3 Relationship between kinematic viscosity and solid fraction for aluminum alloy A356
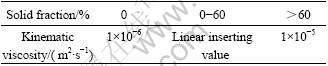
Table 4 Calculation conditions
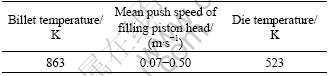
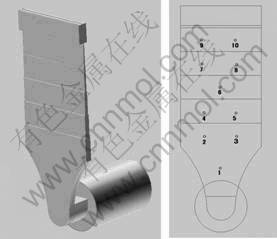
Fig.1 Outline of test piece: (a) 3-D model; (b) Earmarked points
3 Results and discussion
3.1 Mensuration of flow trace and its comparison between experiment and simulation
The reaction timing of thermocouples in earmarked points to grasp filling trace was measured and calculated in two filling patterns (slow and rapid), and the results of experiment and simulation (temporarily mean push speeds of filling piston head were 0.1, 0.2, 0.3, 0.4 and 0.5 m/s respectively) are shown in Fig.2(a) by plots(experiment) and lines(simulation) respectively, where point 1 as shown in Fig.1(b) was taken as an original reference (zero). As relative filling time (ordinate), the differences between the time that molten metal reaches other points and point 1 are plotted in the reference frame as shown in Fig.2. The mean push speed of filling piston head in rapid type is 0.2-0.3 m/s, and one in slow type is approximately 0.1 m/s. To compare the difference of push speeds between experiment and simulation, the reaction timings in the push speeds of 0.25 and 0.07 m/s are additionally calculated, and the results are shown in Fig.2(b). According to Fig.2, the results of experiment and calculation in the rapid type are quite in agreement when the push speed of 0.25 m/s is supposed, but ones in the slow type have a little difference. The mean speed of about 0.1 m/s is approximately accepted in the slow type. These results of mean push speed are prepared for use as the initial speed of further simulation so as to improve the precision of calculation. Because some filling defects often exist in the surface of die-casting under the condition of slow filling pattern, the rapid filling pattern is mainly used in developing actual parts.
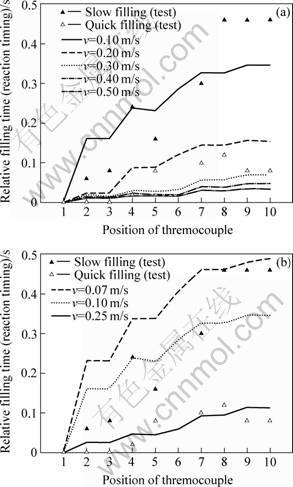
Fig.2 Mean push speeds of filling piston head
3.2 Simulation of filling process and defect analysis for die-castings
A series of results in mean push speed of 0.25 m/s was calculated and shown in Fig.3.
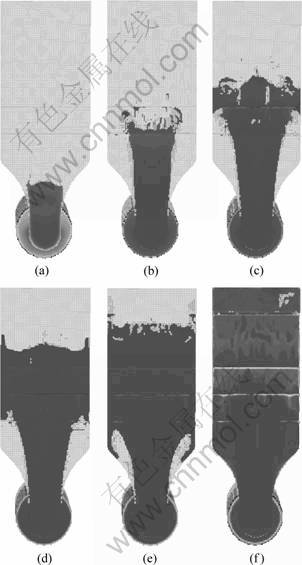
Fig.3 Simulated results of mold filling(0.25m/s): (a) t=0.036 2 s; (b) t=0.072 0 s; (c) t=0.100 0 s; (d) t=0.120 1 s; (e) t=0.140 0 s; (f) t=0.196 0 s
Turbulence and involving gas during filling process are observed from this simulation. According to the simulation result of t=0.148 0 s and experimental one of short-shot (as shown in Fig.4(a)) in test piece, both filling pattern and un-filling area with closed loop are quite similar. So, it is reliable to display filling process with the help of this simulation, that is to say, the visibility in numerical value may be realized. Comparison of filling state between simulation and X-ray inspection in another test sample was carried out and its result is shown in Fig.4(b). Foul-up spoor is a residual trace after short shot and shows the state of a midway turbulence during filling. This is a visualization method for indirectly observing filling process. According to the simulation results of Fig.4(b), later filled portion than surroundings expressed turbulence state is easy to bring on the immixture of gas and bad filling; the simulated turbulence area is a little inclined to left side and quite similar to that found in X-ray inspection. The good accordance between simulation and experiment is further proved to enhance the belief that simulation is able to act as a very useful tool to aid plan design and defect countermeasure.
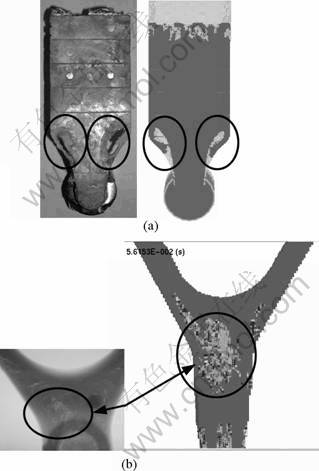
Fig.4 Comparison of filling process between simulation and experiment: (a) Filling appearance; (b) X-ray inspection and simulated cross-section
The distribution of cast defects in local section of test piece was minutely analyzed by microscope observation; and its results are shown in Fig.5.
Much more defects are found in both sides than in the middle of test piece. The filling process that is simulated in Fig.3 obviously affects the distribution of defects due to the turbulence and involving gas. Therefore, filling conditions are very important to the quality of semi-solid die-castings.
3.3 Development of automobile part
As a point automobile part in this study, the developed samples must be tested in desk frame fatigue experiment and are demanded to pass 450 000 cycles requested by customer. Because this part has quite complicated shape and is easy to result in some cast defects(e.g. cold shut, misrun and involved gas) concerned with filling process, the design of filling plan needs to be optimized to develop satisfied product. In the desk frame fatigue experiment, one part once cracked in the front of gate of die-casting is shown in Fig.6.
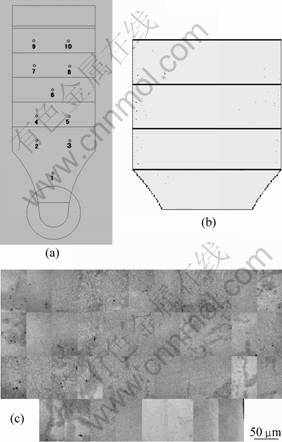
Fig.5 Defect analysis in local section of test piece: (a) Analysis position; (b) Distribution image; (c) Micrograph with low magnification
This rear bridge support cracked after desk frame experiment of 443 000 cycles, and its crack position just got across the entrance of gate. Because cold shut of about 1 mm in depth in cross-section of 7 mm in thickness and crack extension area was observed, crack source was considered to be in this position by breakage analysis. To estimate possibly conduced reasons, filling process was minutely analyzed by computer simulation and its results are shown in Fig.7.
According to the simulated results, the front area of gate is not sequentially filled during filling process. Air in mold cavity is easy to be involved and/or cold shut may be brought about in un-filling area. This position is entirely consistent with that of fatigue fracture in the desk frame fatigue experiment. Therefore, improving filling state near the gate as soon as possible is considered to be quite important to enhance the fatigue property of die-casting. This essential information is applied to optimize the filling plan of this part. Repeated simulations for acquiring an optimized plan were carried out in different filling plans (gating system), optimized plan (the thickness of gate was added from 6mm to 10mm, and the shape of gate was appropriately improved, but other technology parameters were temporarily fixed) was selected in a lot of supposed plans. The results of flow simulation during filling process and X-ray inspection of die-casting part are shown in Fig.8.
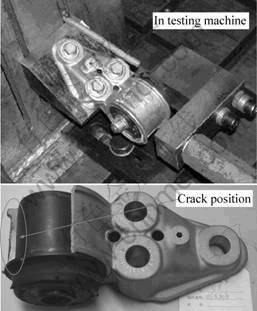
Fig.6 Crack position in fatigue experiment of desk frame
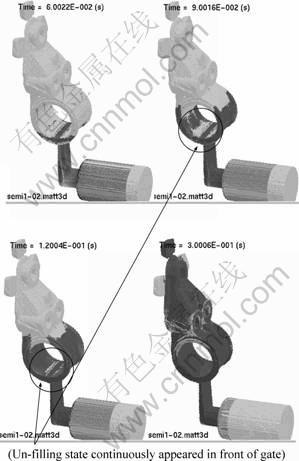
Fig.7 Simulated results of filling process for supporting part of rear bridge
It can be seen that the front area of gate by applying this optimized plan is more rapidly filled than by former plan, and better filling state is acquired. No defects in the front area of gate and in other areas are found by X-ray inspection. We have enough reason to believe that suitably using computer simulation can shorten the developing and making period of semisolid die and improve the quality of products. This method has been regularly used for developing semi-solid die-castings and other relative experiments in our research group.

Fig.8 Simulation and X-ray inspection results for optimized plan: (a) Simulation; (b) X-ray inspection
4 Conclusions
The measured results of the filling trace of semi-solid molten metal in mold cavity by arrangement of thermocouples can provide an aid for improving the accuracy of computer simulation. The defects, concerned with filling, can be forecasted by simulation and its results are quite similar to tested ones in actual parts. Simulation can dynamically show flow tracks in mold cavity and numerically realize the visibility of filling process. It is indicated that computer simulation is an effective method for the optimization of filling plans and the reduction of periods in the development of any new parts and the countermeasures of defects in existent parts.
References
[1] KANG Yong-lin, MAO Wei-min, HU Zhuan-lin. The Theory and Technology in Semi-Solid Process of Metal Materials[M]. Beijing: Science Press, 2004: 242. (in Chinese)
[2] MAO Wei-min. Semi-Solid Forming Technology[M]. Beijing: China Machine Press, 2004: 4-6. (in Chinese)
[3] WANG Chao, GUAN Ren-guo, SHANG Jian-hong, HU Fang-you, CUI Jian-zhong. Preparation of semi-solid Al-20Si alloy by novel sloping plate process [J]. Special Casting & Nonferrous Alloys, 2006, 26(7): 428-430. (in Chinese)
[4] KANG C G, SEO P K, LIM M D. Rheo and thixo die casting for automobile supension parts[A]. 8th International Conference of Semi-Solid Processing[C]. Limassol, Cyprus, 2004.
[5] KUROKI K, SUENAGA T, TANIKAWA H, MASAKI T, SUZUKI A, UMEMOTO T, YAMAZAKI M. Establishment of a manufaturing technology for the high strength aluminum cylinger block in diesel engines applying a rheocasting process[A]. 8th International Conference of Semi-Solid Processing[C]. Limassol, Cyprus, 2004.
[6] CHENG Zheng-wu, TANG Jinh-lin, LI Ke, LI Shuang-shou, ZENG Da-ben. Detection of the reheating state semisolid hypoeutectic Al-Si alloy [J]. Special Casting & Nonferrous Alloys, 2006, 26(6): 357-360. (in Chinese)
[7] SOLEK K, STUCZYNSKI T, BIALOBRZESKI A, KUZIAK R, MITURA Z. Detailed computer simulations of manufacturing of test incomplete casts[A]. 8th International Conference of Semi-Solid Processing[C]. Limassol, Cyprus. 2004
[8] ZHANG Heng-hua. Study on the technique and simulation of thixo-forming of aluminum alloy[D]. Shanghai: Shanghai University, 2003: 85-90
[9] HITACHI Co Ltd. Manual of ADSTEAN[M]. Tokyo: HITACHI Press, 2005: 1-2. (in Japanese)
[10] Japan Foundry Engineering Society. The Handbook for Foundry Engineering[M]. Tokyo: MARUZEN Press, 2002. (in Japanese)
(Edited by YUAN Sai-qian)
Foundation item: Projects(0414) supported by the Science and Technology Development Foundation of Shanghai Automotive Industry
Corresponding author: YANG Yi-tao; Tel: +86-21-56334465; E-mail: yyt@staff.shu.edu.cn