EB-PVD热障涂层热扩散系数测试方法及其影响因素
牟仁德1,宋希文2,陶春虎1,何利民1
(1. 北京航空材料研究院 腐蚀与防护研究室,北京,100095;
2. 内蒙古科技大学 材料与冶金学院,内蒙古 包头,014010)
摘 要:采用激光脉冲法研究电子束物理气相沉积(EB-PVD)热障涂层热扩散系数的测定,对测定结果进行误差分析,研究试样热处理状况和遮挡层对热扩散系数的影响。结果表明:随着测试温度升高,EB-PVD热障涂层的热扩散系数先减小再增大,但在25~1 200℃的测试温度范围内,变化幅度不大;在25 ℃时测试相对误差为4.6%,其余各温度的相对误差均小于1.5%;热扩散系数的变化与陶瓷材料的本征热导率随温度的变化以及涂层的微结构密切相关;热处理使涂层中产生了垂直于基体表面的微裂纹,部分热流通过微裂纹可直接到达涂层表面,导致热扩散系数增加;喷Au加石墨复合遮挡层的试样其热扩散系数比单一石墨遮挡层试样的低,主要是由于低发射率的Au减弱了辐射对传热的贡献。
关键词:热扩散系数;热障涂层;电子束物理气相沉积;激光脉冲法
中图分类号:TG174.4 文献标识码:A 文章编号:1672-7207(2008)02-0256-06
Measurement of thermal diffusivity of EB-PVD thermal barrier coatings and influence factors
MU Ren-de1, SONG Xi-wen2, TAO Chun-hu1, HE Li-min1
(1. Division of Corrosion and Protection, Beijing Institute of Aeronautical Materials, Beijing 100095, China;
2. School of Materials and Metallurgy, Inner Mongolia University of Science and Technology, Baotou 014010, China)
Abstract: Thermal diffusivity of electron beam-physical vapor deposition (EB-PVD) TBCs was measured using laser flash method. The error ranges were analyzed and the effects of heat treatment and shelter layers on the thermal diffusivity were investigated. The results show that thermal diffusivity of TBC decreases at the beginning and then increases with the elevation of testing temperature. But the extent of thermal diffusivity variation is not vast in the whole testing temperature range from 25 ℃ to 1 200 ℃. The maximum relative error is 4.6% at 25 ℃ and less than 1.5% at other testing temperature. The thermal diffusivity is closely related with the intrinsic properties change of ceramic with the increase of temperature and the microstructure of TBCs. Micro-cracks in heat-treated samples, which are perpendicular to the sample surface, permitted part of the heat flow to directly reach the surface of coatings and finally result in the increase of thermal diffusivity. Thermal diffusivity of sample with multi-shelter of Au and graphite is smaller than that of sample with single graphite shelter. The main reason for this phenomenon is that Au with low emission rate weakens the radiation effect on thermal conduction.
Key words: thermal diffusivity; thermal barrier coatings; EB-PVD; laser flash method
新一代大功率、高推重比燃气涡轮发动机热端部件普遍采用陶瓷热障涂层(Thermal Barrier Coatings, TBCs)来提高高温合金的使用温度和寿命。TBCs能使带内部气冷的金属基体温度降低100~300 ℃[1]。服役时发动机热端部件及涂层内的传热过程十分剧烈,TBCs的热物理性能尤其是热扩散系数直接关系到基体材料实际承受的温度以及热循环过程中的热应力,因此,准确测定TBCs的热扩散系数对热端部件的材料体系设计、涂层寿命评估和工程应用都有十分重要的意义[2-9]。尽管热扩散系数的测定方法很多,但大多数测试主要使用以下3种方法:激光脉冲法,3ω法和光声法。研究表明,3ω法适用于厚度很小的薄涂层,并且到目前为止,其应用温度一般低于500 ℃;光声法的应用也受声-电转换器工作温度范围的限 制[10-11]。激光脉冲法是热扩散系数测定中应用最广泛的光热法[12],对于热障涂层,该方法在目前实际测试中还存在许多不足,如激光穿透性、脆性涂层薄片难以从基体上取下等[13]。目前,该方法主要应用于厚度较大的等离子喷涂TBCs、电子束物理气相沉积(Electron beam-physical vapor deposition, EB-PVD) TBCs等方面,由于涂层厚度较薄,陶瓷顶层脆性大,且与基体结合力大,取片更加困难,在此,本文作者采用激光脉冲法,直接对EB-PVD热障涂层加基体双层试样的热扩散系数进行测定,并对测试结果进行误差分析,研究涂层防穿透遮挡层情况、试样热处理状况对EB-PVD TBCs热扩散系数测试结果的影响。
1 测试原理
激光脉冲法的原理是建立在绝热无限大试样于恒温时的热行为基础上[14-16],该试样的一面受短时能 量脉冲作用。首先提出如下假设:a. 热流一维传输;b. 试样表面无热损;c. 受热面脉冲热量均匀吸收;d. 与试样热反应相比,脉冲时间极短;e. 脉冲能量吸收层极薄;f. 试样材料均匀,各向同性;g. 在测定温度点,试样热物理性能不发生变化。根据以上假设,一般传热方程
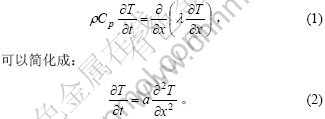
其中:
,表示试样材料的热扩散系数,m2/s;λ为热导率;ρ为密度;cp为比热容;T和t分别为热力学温度和时间。从假设(2)可以得出边界 条件:

方程(2)的通解为:
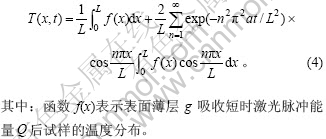
定义温度分布的初始条件为:

在这些初始条件下,式(4)可以变形为:

当g/L足够小时,可以近似认为,
,试样背部温度可以表示为:

经过足够长时间后,背部温度达到它的最大值:

若试样初始参考温度为Tr,则背部的相对温升 V(L, t)可以表示为:
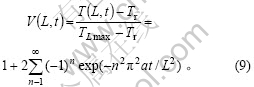
把最大温升的50%作为计算热扩散系数的参考点,即
,
,可以得到如下表达式:
2 试 验
2.1 试验材料
基体材料为DZ125镍基定向高温合金,合金成分为:9.5%~10.5% Co,8.4%~9.4% Cr,3.5%~4.1% Ta,4.8%~5.4% Al,0.7%~1.2% Ti,6.5%~7.5% W,1.5%~2.5% Mo,其余为Ni(质量分数,下同)。粘结层材料采用NiCrAlY,成分为20%~25% Cr,6%~10% Al,0.08%~0.4% Y,0.4%~0.8% Si,其余为Ni。陶瓷靶采用6%~8% Y2O3部分稳定的ZrO2即YSZ。
2.2 试验方法
2.2.1 涂层制备
粘结层采用A-1000真空电弧镀设备涂覆,厚度为30~50 μm,涂覆完成后于870 ℃进行真空扩散处理;粘结层上的陶瓷层采用EB-PVD工艺制备。
2.2.2 热扩散系数测试
热扩散系数测试采用NETZSCH LFA427设备,按照GJB 120.1—91进行。测试前,部分试样先进行1 000 ℃热处理消除非平衡相(或称预氧化),然后制备激光遮挡层。试样的厚度、遮挡层及热处理情况见表1。
表1 热扩散系数测试试样
Table 1 Samples for thermal diffusivity measurement
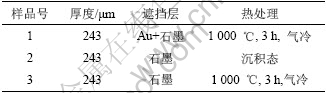
测试时首先将涂层试样加热到温,然后,通过激光脉冲1次,系统自动完成试样背部温升曲线记录、半温升时间确定及热扩散系数计算。首先测试涂层在室温的热扩散系数,然后从100 ℃开始,每隔100 ℃取1个测试点,一直到1 200 ℃,每个测试温度点进行3次测试,取平均值作为最后测试结果。
3 结果与讨论
3种试样的热扩散系数测试结果随温度的变化情况见图1。由图1可知,当温度较低时,随着测试温度的升高,EB-PVD热障涂层的热扩散系数逐渐减小,当温度达到700 ℃左右时,热扩散系数达到最小,然后,随着温度的升高,热扩散系数呈现增大的趋势。但是,在整个测试温度范围内,热扩散系数随温度的升高而减小或增大的幅度都不大,曲线变化趋势较平坦。
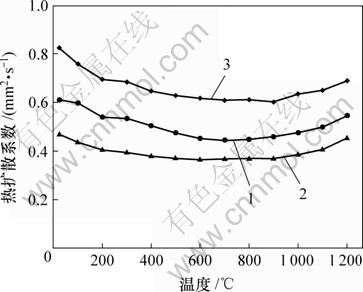
1—样品1;2—样品2;3—样品3
图1 EB-PVD热障涂层热扩散系数随温度变化曲线
Fig.1 Thermal diffusivity of EB-PVD TBCs as a function of temperature
热障涂层的热扩散系数的变化与其显微结构密切相关。EB-PVD热障涂层具有柱状树枝晶结构,见图2。柱与柱之间会形成封闭的气孔或气隙,封闭气孔的存在使得陶瓷涂层的热传导过程十分复杂,它除了陶瓷材料本身在不同温度条件下的电子热传导、声子热传导和光子热传导之外,还多了气孔或气隙对热传导的阻碍即热阻,对陶瓷涂层的热扩散系数产生了很大的影响。实体ZrO2陶瓷材料的热扩散系数随着温度的升高而缓慢下降,而且温度越高,下降的幅度越小;密封气孔或气隙中的气体可以认为是干空气,其热扩散系数随着温度的升高而增大;此外,温度对陶瓷的热传导有很大的影响,一般来说,当温度相对较低时,陶瓷的热传导主要为晶格间非谐振作用产生的声子传导,热扩散系数或热导率与温度成反比,即温度升高,热导率下降;但在高温下,由辐射产生的光子热传导作用增大,热扩散系数随着温度升高而增大。因此,受密闭气孔中的干空气传热、声子热传导和辐射光子热传导等因素的综合影响,随着测试温度升高,宏观上涂层的热扩散系数先减小再增大。
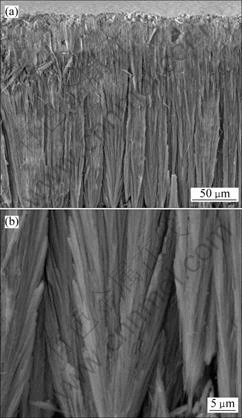
(a) 柱状结构;(b) 晶间密闭气孔
图2 涂层截面SEM形貌
Fig.2 SEM image of coatings’ cross section
3.1 测试误差分析
测试的热扩散系数见表2,其中:M(
)为测试平均误差最大值。由测试结果可知,除了25 ℃的测试误差为4.06%以外,其余各温度点的热扩散系数平均误差最大为1.48%,最小为0.28%,均小于1.5%。在整个测试温度范围内,热扩散系数测试相对误差均小于5%。
表2 不同温度下热扩散系数测试值
Table 2 Thermal diffusivity value of TBCs at different temperatures
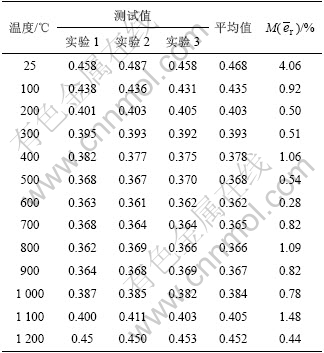
3.2 热处理状况对热扩散系数的影响
试样2和试样3的涂层与基体的材料种类、厚度及遮挡层完全相同,只是测试前2种试样的热处理状态不同。试样3在涂层沉积完成后进行了1 000 ℃/3 h的静态氧化处理,而试样2则为沉积态,即涂层沉积完成后在沉积设备的真空环境中逐渐冷却到室温,取出后直接进行测试。
由测试结果可知,测试前的热处理对EB-PVD热障涂层的热扩散系数产生了很大的影响。与沉积态涂层的热扩散系数相比,热处理后涂层的热扩散系数出现一定程度的升高,如图1中曲线2和曲线3所示。测试前进行热处理相当于对涂层进行了一定程度的预老化,以利于消除涂层中的非平衡相或使其相稳定。由于热处理时间较短,涂层中的柱状晶结构和密闭气孔等没有发生明显变化,与图2所示的结构形貌基本相同。但由于陶瓷热障层脆性较大,加热保温后的冷却过程使得涂层中产生微细的龟裂纹,如图3所示。
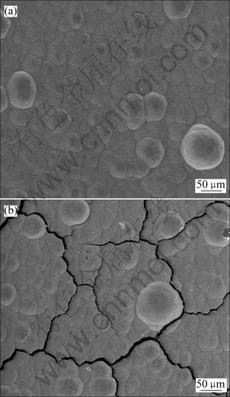
(a) 沉积态;(b) 热处理态
图3 EB-PVD热障涂层表面SEM形貌
Fig.3 SEM image of EB-PVD TBCs
在使用激光脉冲法进行热扩散系数测试时,由于涂层中存在微细裂纹,并且微裂纹的方向与热流的流向平行,因此,部分脉冲激光会通过裂纹直接到达金属基底,导致试样背部温度较快升高到最大值,其半温升时间t0.5比沉积态涂层的半温升时间小。由式(10)可知,t0.5减小引起热扩散系数a增大。
航空发动机叶片热障涂层服役初期的状况,与本研究中在测试前进行预老化热处理的情况类似,研究热处理状况或预老化程度对热扩散系数的影响,可以在一定程度上反映服役过程中热障涂层热物理性能的变化。刚装备的叶片热障涂层一般为沉积态,当发动机开始正常工作运转时,热障涂层会不断受到加热和冷却的交替冲击,涂层中也会因此产生微细裂纹,引起热扩散系数增大,从而降低热障涂层预期的隔热效果,对发动机的冷却产生不利影响。微细裂纹的产生也存在有利的一面。在热障涂层服役过程中,涂层受热和冷却过程中产生的应力可以通过微细裂纹的闭合和张开得到部分释放,减少涂层本身所受的热应力,有利于提高热障涂层服役寿命。
3.3 遮挡层对热扩散率的影响
由于ZrO2对测试用的脉冲激光是半穿透性的(或称半透明),为保证脉冲激光的能量被涂层良好吸收,测试前必须在涂层上添加遮挡层。为了比较不同遮挡层对热扩散系数测试的影响,本研究中采用2种遮挡方案:一种是吸收率高的石墨遮挡层;另一种是发射率低的Au+吸收率高的石墨组成的复合遮挡层。由于误差的传播,厚度参量L和半温升时间t0.5的测试误差必定引起热扩散系数a的误差。参量相对误差与解的相对误差的函数关系为:

若测试中半温升时间t0.5为准确值,则
。由于厚度参量L的测试误差引起的热扩散系数a的误差为

若测试中厚度L为准确值,则
。由于半温升时间t0.5的测试误差引起的热扩散系数a的误 差为

本研究中的热障涂层及基体厚度分别为0.243 mm和0.8 mm,而遮挡层的厚度一般只有3~5 μm,与基体和热障涂层的厚度相比很小,因此,添加遮挡层对热障涂层厚度参量L的影响很小,由此引起的热扩散系数a的误差可忽略不计。热扩散系数的测试误差主要来源于半温升时间t0.5。
遮挡层会影响试样背部温升情况,从而对半温升时间t0.5产生影响,引起热扩散系数的测试误差er(a)发生变化。单一的石墨遮挡层能使表面“黑化”,阻挡激光直接透进试样内部,保证激光脉冲能量被有效均匀地吸收。对于Au和石墨组成的复合遮挡层,由于喷金层发射率相对较低,能减少热辐射进入试样,使辐射对传热导的贡献减弱;在试样背部,喷金层可以作为红外温度探测器的信号发生层,还可以防止探测器探测进入试样内部,避免引起温度急剧升高。从图1所示试验结果可知,在相同厚度、相同热处理状态的条件下,添加复合遮挡层的涂层试样的热扩散系数在各个温度点均比只添加单一石墨遮挡层试样的低。这主要是激光脉冲时,喷金层减少了进入试样的热辐射量,减弱了辐射对传热的贡献,使热扩散系数a减小。
4 结 论
a. 使用激光脉冲法测试EB-PVD热障涂层的热扩散系数时,整个测试温度范围内的测试相对误差满足小于5%的要求。除了25 ℃的测试误差为4.06%以外,其余各温度点的测试平均误差最大为1.48%,最小为0.28%。
b. 随着测试温度升高,EB-PVD热障涂层的宏观热扩散系数先减小再增大,但在25~1 200 ℃的测试温度范围内,热扩散系数变化的幅度不大。热扩散系数的变化与陶瓷材料本征性质及涂层的微结构密切相关。
c. 热处理态试样的热扩散系数较沉积态的高,主要是因为测试前的热处理使EB-PVD热障涂层中产生了垂直于基体表面的微裂纹,使得平行于裂纹方向的部分热流直接通过微裂纹到达涂层表面,导致各个测试温度点的热扩散系数高于沉积态涂层。
d. 与添加单一石墨遮挡层的涂层试样相比,经过喷Au加石墨复合遮挡处理的试样的热扩散系数在各个测试温度点的热扩散系数均低于只添加单一石墨遮挡层试样的热扩散系数。低发射率的Au阻挡热辐射进入试样,减弱了辐射对传热的贡献,是造成热扩散系数较低的主要原因。
参考文献:
[1] Cernuschi F, Bison P G, Figari A, et al. Thermal diffusivity measurements by photothermal and thermographic technics[J]. International Journal of Thermophysics, 2004, 25(2): 439-457.
[2] Su Y J, Trice R W, Faber K T, et al. Thermal conductivity, phase stability, and oxidation resistance of Y3Al5O12 (YAG)/Y2O3-ZrO2 (YSZ) thermal barrier coatings[J].Oxidation of Metals, 2004, 61(4): 253-271.
[3] Almeida D S, Silva C R M, Nono M C A, et al. Thermal conductivity investigation of zirconia co-doped with yttria and niobia EB-PVD TBCs[J]. Materials Science and Engineering, 2007, A443: 60-65.
[4] GU S, LU T J, HASS D D, et al. Thermal conductivity of zirconia coatings with zig-zag pore microstructures[J]. Acta Mater, 2001, 49: 2539-2547.
[5] Orain S, Scudeller Y, Brousse T. Thermal conductivity of ZrO2 thin films[J]. International journal of thermal society, 2000, 39: 537-543.
[6] Davis J W, Haasz A A. Thermal diffusivity/conductivity of AECL Li2TiO3 ceramic[J]. Journal of Nuclear Materials, 1996, 232: 65-68.
[7] Mevrela R, Laizet JC, Azzopardi A, et al. Thermal diffusivity and conductivity of Zr1-xYxO2-x/2 (x=0, 0.084 and 0.179) single crystals[J]. Journal of the European Ceramic Society, 2004, 24: 3081-3089.
[8] Scardi P, Leoni M, Cernuschi F, et al. Microstructure and heat transfer phenomena in ceramic thermal barrier coatings[J]. Journal of the American Ceramic Society, 2001, 84(4): 827-835.
[9] Martinsons C, Heuret M. Recent progress in the measurement of the thermal properties of hard coatings[J]. Thin Solid Films, 1998, 317: 455-457.
[10] 孟 麦, 尤清照. 利用激光脉冲技术测量材料热物理性能[J]. 钢铁研究学报, 2000, 12(6): 46-49.
MENG Mai, YOU Qing-zhao. Measuring method for thermophysical properties of materials by laser flash[J]. Journal of Iron and Steel Research, 2000, 12(6): 46-49.
[11] 宋青林, 夏善红, 陈绍凤. 微尺度薄膜热导率测试技术[J]. 物理学进展, 2002, 22(3): 283-295.
SONG Qing-lin, XIA Shan-hong, CHEN Shao-feng, et al. Thermal conductivity measurement technology of microscale thin film[J]. Progress in Physics, 2006, 22(3): 283-295.
[12] Taylor R E, Wang X, Xu X. Thermophysical properties of thermal barrier coatings[J]. Surface and Coatings Technology, 1999, 120/121: 89-95.
[13] ZHU Dong-ming, Miller R A, Nagaraj B A, et al. Thermal conductivity of EB-PVD thermal barrier coatings evaluated by a steady-state laser heat flux technique[J]. Surface and Coatings Technology, 2001, 138: 1-8.
[14] Siegel R. Green’s Function to determine temperature distribution in a semitransparent thermal barrier coating[J]. Journal of Thermophysics and Heat Transfer, 1997, 11(2): 315-318.
[15] Parker W J, Jenkins R J, Butler C P, et al. Thermal diffusivity measurement using the flash technique[J]. Journal of Application Physics, 1961, 32(9): 1679-1684.
[16] Wang H, Dinwiddie R B. Reliability of laser flash thermal diffusivity measurements of the thermal barrier coatings[J]. Journal of Thermal Spray Technology, 2000, 9(2): 210-214.
收稿日期:2007-05-10;修回日期:2007-07-15
基金项目:国防基础科研项目(A1320061002)
通信作者:牟仁德(1975-),男,湖北利川人,博士,从事EB-PVD热障涂层研究;电话:010-62496446;E-mail: murende@163.com