J. Cent. South Univ. (2017) 24: 1034-1039
DOI: 10.1007/s11771-017-3506-9

Effect of friction stir processing on microstructure and damping capacity of AZ31 alloy
ZANG Qian-hao(臧千昊)1, 2, CHEN Hong-mei(陈洪美)1, 3, LAN Fang-yuan(蓝方园)1,
ZHANG Jing(张静)1, JIN Yun-xue(金云学)1
1. Provincial Key Lab of Advanced Welding Technology, Jiangsu University of Science and Technology,
Zhenjiang 212003, China;
2. Key Laboratory for Liquid-Solid Structural Evolution & Processing of Materials of Ministry of Education,
Shandong University, Jinan 250061, China;
3. National Demonstration Center for Experimental Materials Science and Engineering Education (Jiangsu University of Science and Technology), Zhenjiang 212003, China
Central South University Press and Springer-Verlag Berlin Heidelberg 2017
Abstract: AZ31 alloy sheet fabricated by rolling was processed by friction stir processing (FSP) with different passes. The effect of FSP on the microstructure and damping capacity of AZ31 alloy sheet was discussed. The fine and equiaxed grains were obtained in the stirred zone (SZ) for FSPed samples from 1 pass to 3 passes with the average grain size of 10.6, 10.4 and 13.6 μm, respectively. The damping peak P1 was presented on the curves of temperature-dependent damping capacity for FSPed samples. The damping peak P2 was restrained after FSP and the damping peak P1 was a relaxation process. The FSPed samples (2-pass FSP and 3-pass FSP) obtained high damping capacity. The best damping values
(ε=10-4) and damping values
(ε=10-3) of the sample subjected to 3-pass FSP (0.0131 and 0.0496) increased by 33.7% and 157.0%, respectively.
Key words: Mg-Al-Zn alloy (AZ31); friction stir processing (FSP); damping peak; G-L model
1 Introduction
Magnesium alloys are the lightest structural material with high specific strength, high specific elastic modulus and high damping capacity [1-3]. Pure magnesium has the best damping capacity, but with poor mechanical properties, such as low hardness, low yield strength and tensile strength [4]. Therefore, higher strength and higher damping of magnesium alloys can be achieved through alloying or plastic deformation. Recently, severe plastic deformation (SPD) [5-7] processes such as accumulative roll bonding (ARB), equal channel angular pressing (ECAP), high pressure torsion (HPT), cyclic extrusion compression (CEC) and friction stir processing (FSP) have been applied to improvement of the microstructure and mechanical properties [8]. The method of FSP is convenient and used widely.
Based on the basic principles of friction stir welding (FSW), friction stir processing, as an effective method for microstructure modification, has been developed as a thermo-mechanical microstructural modification technique of metallic materials [9]. The homogenized and refined microstructure after FSP presented improved mechanical properties [10, 11]. Three distinct regions are present in the final microstructure: heat affected zone (HAZ), thermo-mechanically affected zone (TMAZ) and stirred zone (SZ). The SZ has a fine equiaxed recrystallized grain structure, which could be achieved as a result of severe plastic deformation and dynamic recrystallization (DRX) [12].
Many investigations have reported the effect of FSP on grain refining, microstructural evolutions, dynamic recrystallization and mechanical properties of Mg-Al-Zn alloys [13-15]. However, the effect of FSP on the damping capacity of Mg-Al-Zn alloy was seldom discussed. The damping capacity of magnesium alloys is considered to be caused by the movement of dislocations, which abide by the G-L theory [16, 17]. In order to improve the damping capacity of magnesium alloys, the dislocations, which are defined between the pining points, should be relatively free to move. Thus, the aim of the present study is to investigate the effect of FSP on the microstructure and damping capacity of Mg-Al-Zn alloy.
2 Experimental procedure
The material used in this study was AZ31 magnesium alloy of hot rolling state with the composition (in mass fraction, %) of Al 3.12, Zn 0.91, Mn 0.329, Si 0.032, Mg balance. The base material was cut into specimens of 4 mm×200 mm×200 mm. The shoulder diameter, pin diameter and pin height were 16.0 mm, 4.0 mm and 3.8 mm, respectively. The FSP tool rotated at 1500 r/min in the clock-wise direction. The traverse speed was 50 mm/min. The tilted angle was 2.5°. FSP was carried out different passes.
For optical examination, the samples were sectioned and cold mounted, and then they were polished with silicon dioxide paste with the grain size of 1 μm, finally they were etched in a solution of picric acid (5 g), acetic acid (5 mL), distilled water (10 mL) and ethanol (100 mL), and then examined by using a ZEISS optical microscope. Specimens for damping test were machined from the center region in the SZ. Damping samples were machined to the dimensions of 35 mm×10 mm×1 mm. Damping capacity was measured by dynamic mechanical analyzer (NETZSCH DMA-242C) in single cantilever deformation mode. For the measurements of strain amplitude dependence of damping capacity, the range of strain amplitude was from 1 μm to 200 μm, and the measurement frequency was 1 Hz. For the measurements of temperature-dependent damping capacity, the measurement frequency was 0.5, 1, 5 and 10 Hz, respectively. The temperature range was from 25 °C to 400 °C and the heating rate was 5 °C/min. The detailed microstructures of the samples were further examined with a transmission electron microscope (TEM, JEM- 2100F). The TEM foils were prepared by jet electron polishing using a solution of HClO4 (5%), butanol (35%) and methanol (60%), and followed by ion beam thinning.
3 Results and discussion
3.1 Macrostructure and microstructure of FSPed samples
Figure 1 shows the cross-sectional overview of the plate subjected to 1-pass FSP. No defects such as pin hole, tunnel and piping were found for all FSPed samples. Three distinct zones were present in the microstructure for FSPed samples: stirred zone (SZ), thermo- mechanically affected zone (TMAZ) and heat affected zone (HAZ). Compared the advancing side (AS) with the retreating side (RS), a sharp boundary was only visible on the advancing side (AS).
Figure 2 shows the microstructure of AZ31 base alloy and FSPed samples. The microstructure of AZ31 base alloy sheet consisted of elongated grains along the rolling direction (as shown in Fig. 2(a)), and the deformed microstructure was inhomogeneous.Figures 2(b), (c) and (d) exhibit the microstructure of the center region in the SZ for FSPed specimens from 1 pass to 3 passes. The specimen exhibited a significant change of microstructure after FSP. The FSPed specimens had homogenous and recrystallized small grains. The fine and equiaxed grains were obtained with the average grain size of 10.6, 10.4 and 13.6 μm, respectively. Apparently, the average grain size in Fig. 2(d) was increased after 3-pass FSP compared with Figs. 2(b), (c).
3.2 Damping capacity of FSPed samples
Temperature-dependent damping capacity of AZ31 base alloy and FSPed samples is shown in Fig. 3. The curves of AZ31 base alloy had two peaks (P1 was around 160 °C, P2 was around 300 °C). By comparison, P1 was only visible on the curves of FSPed samples. The damping peak P2 was restrained after FSP.
Temperature-dependent damping capacities of AZ31 alloy after 3-pass FSP (f=0.5, 1, 5, 10 Hz) at full temperature and low temperature are shown in Figs. 4(a) and (b), respectively. The temperature of damping peak P1 was increasing along with the increasing of measurement frequency, thus, the damping peak P1 was a relaxation process [18-20].
Strain-dependent damping capacity of AZ31 base alloy and FSPed samples (as shown in Fig. 5) can be divided into two classical regions. In the lower strain region, the dislocation was pinned by weak pinning points (such as solution atom, vacancies). The damping values
were independent of or only weakly dependent on the maximum strain amplitude. The damping growth of all the samples was very slow. The
dislocation moving between the weak pinning points contributes the damping values
In the higher strain region, the dislocation broke away the pinning of weak pinning points with the increasing of the strain amplitude. The unpinning of dislocation from the weak pinning points occurred in the snowslide-like mode, and the damping capacity increased rapidly. The dislocation was pinned by strong pinning points (such as grain boundaries, network nodes of dislocations). The damping can be divided into two components [21]:
(1)
The damping values at low strain and high strain are shown in Fig. 6. The damping value
(ε=10-4) of AZ31 base alloy was 0.0097, and that of the samples subjected to 1-pass FSP (0.0098), 2-pass FSP (0.0105) and 3-pass FSP (0.0131) increased by 1.0%, 7.2% and 33.7%, respectively. The damping value
(ε=10-3) of AZ31 base alloy was 0.0193, and that of the samples subjected to 1-pass FSP (0.0302), 2-pass FSP (0.0353) and 3-pass FSP (0.0496) increased by 56.5%, 82.9% and 157.0%, respectively. When the damping capacity was bigger than 0.01, it was generally considered that the alloys exhibit high damping capacity [22]. The FSPed samples (2-pass FSP and 3-pass FSP) obtained high damping capacity.
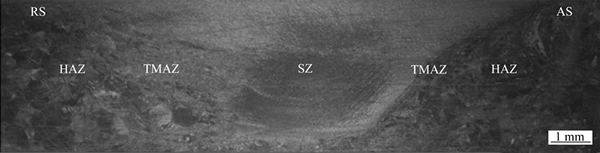
Fig. 1 Macrostructure of plate subjected to 1-pass FSP
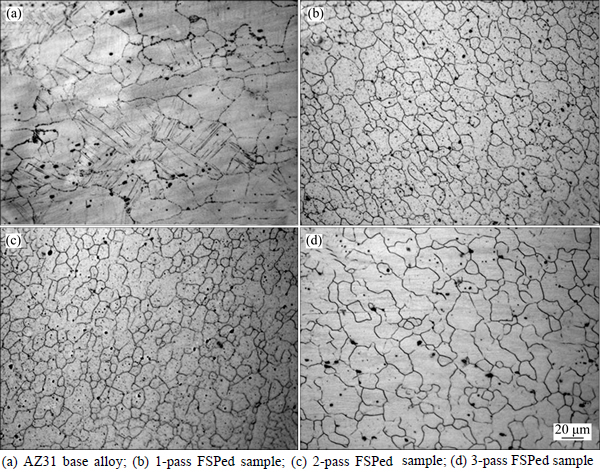
Fig. 2 Microstructure of AZ31 base alloy and FSPed samples:
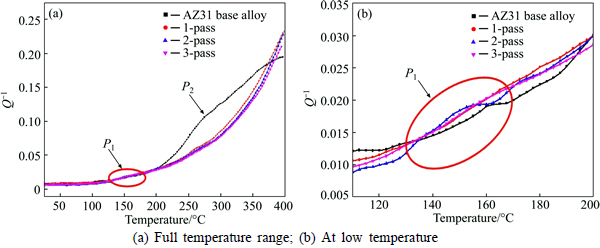
Fig. 3 Temperature-dependent damping capacity of AZ31 base alloy and FSPed samples:
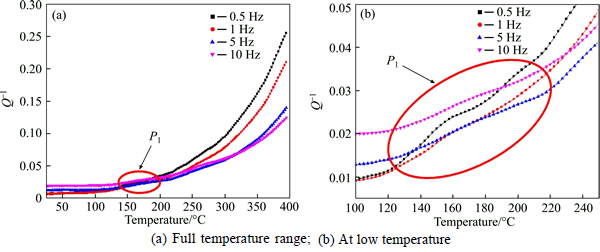
Fig. 4 Temperature-dependent damping capacity of AZ31 alloy after 3-pass FSP (f=0.5, 1, 5, 10 Hz):
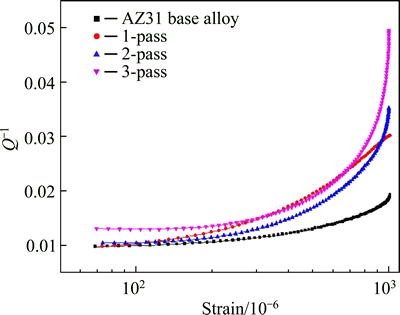
Fig. 5 Strain-dependent damping capacity of AZ31 base alloy and FSPed samples
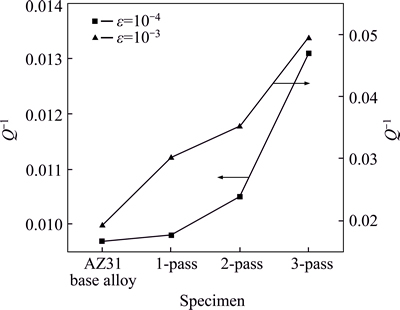
Fig. 6 Damping values of AZ31 base alloy and FSPed samples
The damping
can be expressed by G-L theory [16, 17]:
(2)
(3)
(4)
where C1 and C2 are the material constants; ρ is the dislocation density; FB is the binding force between dislocation and weak pinning points; LN is the average dislocation distance between strong pinning points; LC is the average dislocation distance between weak pinning points; b is the Burger’s vector; E is the elastic modulus.
In higher strains region, Eq. (2) can be altered as
(5)
From Eq. (5), G-L plots should be straight lines, whose intercept and slope were the values of lnC1 and -C2, respectively. Strain amplitude dependence damping capacity of AZ31 base alloy and FSPed samples abided by the G-L model from Fig. 7. The values of C1 and C2 calculated according to G-L plots [23] are shown in Table 1.
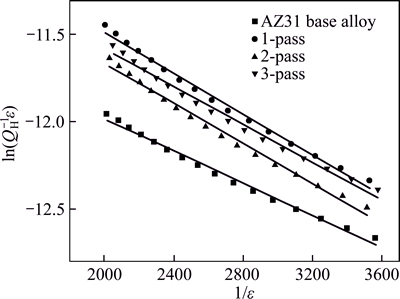
Fig. 7 G-L plots of AZ31 base alloy and FSPed samples
Table 1 Values of C1 and C2 according to G-L plots
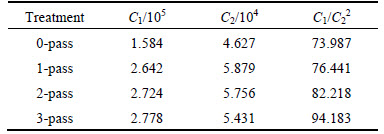
It can be noted from Eqs. (3), (4) that C1 and C2 were proportional to
and 1/LC, respectively. Equations (3), (4) can be altered as
(6)
From Eq. (6), the C1/C22 value was proportional to
. The C1/C22 values of AZ31 base alloy and FSPed samples increased with the increasing of FSP passes due to the increase of the average grain size. The LC did not change too much due to a fact that the C2 values had varied within a very small range.
The damping capacity mechanism of magnesium was determined by their dislocations movement, which can be explained through the G-L theory [24].
In the lower strains region,
can be described as
(7)
The damping values
(ε=10-4) of FSPed samples tended to increase with the increasing of FSP passes. This phenomenon is accounted for by the change of movable dislocations. In the lower strain region, the damping of AZ31 base alloy and FSPed samples was produced by the moving dislocations between weak pinning points. While the LC values did not changed too much and the number of movable dislocations affected the damping values
(ε=10-4). Dislocations morphology in AZ31 base alloy and FSPed samples is shown in Fig. 8. Dislocations and a number of tanglements were observed in AZ31 base alloy. The tangly dislocations do not benefit dislocation to move. Sparse dislocations and a few tanglements were observed in FSPed samples. A number of movable dislocations were produced during FSP, and the high temperature during FSP increased the number of movable dislocations. The movability of dislocations increased with the increasing of FSP passes, leading to the damping values
(ε=10-4) increased.
The damping values
(ε=10-3) of FSPed samples increased signally with the increasing of FSP passes. The reason for this tendency was multiple. At low strain amplitude, the dislocations were pinned by the weak pinning points. With the increasing of stress, the dislocation would bow out and continue to bow out until the breakaway stress is reached. Further increasing of stress leaded to the creation and expansion of new dislocations according to Frank-Read mechanism [25]. The higher density of movable dislocations and dislocation multiplication at high strain amplitude leads to the tendency. Meanwhile, the LN values also increased with the increasing of FSP passes, and the range of dislocations moving increased accordingly. In the higher strains region, the movement of dislocations between strong pinning points contributed the damping capacity
(ε=10-3). Due to the distance between strong pinning points and the number of movable dislocations increasing, the damping values
(ε=10-3) increased accordingly. The process in the higher strains region is shown in Fig. 9.
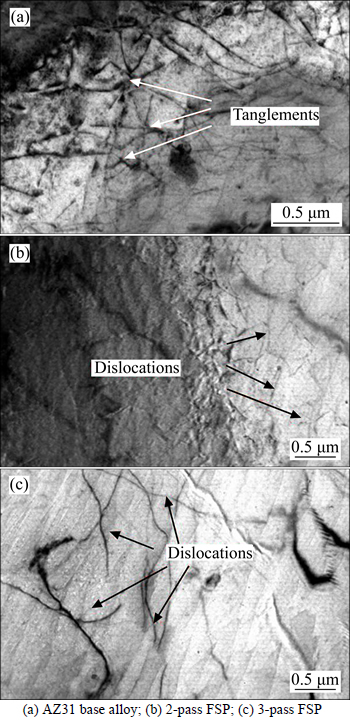
Fig. 8 Dislocations morphology in AZ31 base alloy and FSPed samples:
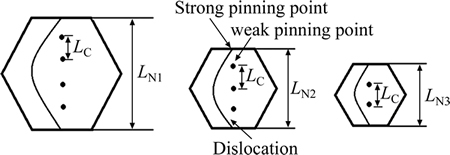
Fig. 9 Schematic diagram of G-L dislocation model
4 Conclusions
1) The curves of temperature-dependent damping capacity for AZ31 base alloy had two peaks. The damping peak P2 is restrained after FSP and the damping peak P1 is a relaxation process.
2) The FSPed samples (2-pass FSP and 3-pass FSP) obtained high damping capacity. The damping values
(ε=10-4) of the samples subjected to 2-pass FSP (0.0105) and 3-pass FSP (0.0131) increased by 7.2% and 33.7%, respectively. The damping values
(ε=10-3) of the samples subjected to 2-pass FSP (0.0353) and 3-pass FSP (0.0496) increased by 82.9% and 157.0%, respectively.
References
[1] MORDIKE B L, EBERT T. Magnesium properties-applications- potential [J]. Materials Science & Engineering A, 2001, 302(1): 37-45.
[2] SCHALLER R. Metal matrix composites: A smart choice for high damping materials [J]. Journal of Alloys and Compound, 2003, 355(1): 131-135.
[3] CHENG Wei-li, WANG Miao, QUE Zhong-ping. Microstructure and mechanical properties of high speed indirect-extruded Mg-5Sn- (1,2,4)Zn alloys [J]. Journal of Central South University, 2013, 20(10): 2643-2649.
[4] HU X S, ZHANG Y K, ZHANG M Y. A study of damping capacities in pure Mg and Mg-Ni alloys [J]. Scripta Materialia, 2005, 52(11): 1141-1145.
[5] ZAHID G H, HUANG Y, PRANGNELL P B. Microstructure and texture evolution during annealing a cryogenic-SPD processed Al-alloy with a nanoscale lamellar HAGB grain structure [J]. Acta Materialia, 2009, 57(12): 3509-3521.
[6] HANSRAJ K, SHARMA R S, SINGH P. Study of friction stir processing (FSP) and high pressure torsion (HPT) and their effect on mechanical properties [J]. Procedia Engineering, 2011, 10: 2904- 2910.
[7] CHANG C I, LEE C J, HUANG J C. Relationship between grain size and Zener-Holloman parameter during friction stir processing in AZ 31 Mg alloys [J]. Scripta Materialia, 2004, 51(6): 509-514.
[8] JAIN V, MISHRA R S, VERMA R. Superplasticity and microstructural stability in a Mg alloy processed by hot rolling and friction stir processing [J]. Scripta Materialia, 2013, 68(7): 447-450.
[9] MISHRA R S, MA Z Y. Friction stir welding and processing [J]. Materials Science and Engineering R: Reports, 2005, 50(1, 2): 1-78.
[10] HUTSH L L, HILGERT J, HERZBERG K. Temperature and texture development during high speed friction stir processing of magnesium AZ31 [J]. Advanced Engineering Materials, 2012, 14(9): 762-771.
[11] FARAJI G, ASADI P. Characterization of AZ91/alumina nanocomposite produced by FSP [J]. Materials Science & Engineering A, 2011, 528(6): 2431-2440.
[12] ASADI P, MAHDAVINEJAD R A, TUTUNCHILA S. Simulation and experimental investigation of FSP of AZ91 magnesium alloy [J]. Materials Science & Engineering A, 2011, 528(21): 6469-6477.
[13] HUNG Fei-yi, SHIH Chien-chih, CHEN Li-hui. Microstructures and high temperature mechanical properties of friction stirred AZ31-Mg alloy [J]. Journal of Alloys and Compound, 2007, 428(1): 106-114.
[14] VENKATESWARLU G, DAVIDSON M J, TAGORE G R N. Modelling studies of sheet metal formability of friction stir processed Mg AZ31B alloy under stretch forming [J]. Materials and Design, 2012, 40: 1-6.
[15] WOO W, CHOO H, PRIME M B. Microstructure, texture and residual stress in a friction-stir-processed AZ31B magnesium alloy [J]. Acta Materialia, 2008, 56(8): 1701-1711.
[16] GRANATO A, LUKER K. Theroy of mechanical damping due to dislocation [J]. Journal of Applied Physics, 1956, 27 (6): 583-593.
[17] GRANATO A, LUKER K. Application of dislocation theory to internal friction phenomena at high frequencies [J]. Journal of Applied Physics, 1956, 27(7): 789-805.
[18] HU X S, WU K, ZHANG M Y. Low frequency damping capacities and mechanical properties of Mg–Si alloys [J]. Materials Science & Engineering A, 2007, 452-453: 374-379.
[19] WU Y W, WU K, DENG K K. Damping capacities and tensile properties of magnesium matrix composites reinforced by graphite particles [J]. Materials Science & Engineering A, 2010, 527(26): 6816- 6821.
[20] WU Y W, WU K, DENG K K. Effect of extrusion temperature on microstructures and damping capacities of Grp/AZ91 composite [J]. Journal of Alloys and Compound, 2010, 506(2): 688-692.
[21] FENG Hao, YANG Yang, CHANG Hai-xia. Influence of W-phase on mechanical properties and damping capacity of Mg-Zn-Y-Nd-Zr alloys [J]. Materials Science & Engineering A, 2014, 609: 7-15.
[22] WAN Di-qing, WANG Jin-cheng, YANG Gen-cang. A study of the effect of Y on the mechanical properties, damping properties of high damping Mg-0.6%Zr based alloys [J]. Materials Science & Engineering A, 2009, 517(1): 114-117.
[23] QIN De-zhao, WANG Jing-feng, CHEN Yong-liang. Effect of long period stacking ordered structure on the damping capacities of Mg- Ni-Y alloys [J]. Materials Science & Engineering A, 2015, 624: 9-13.
[24] WAN Di-qing, WANG Jin-cheng, LIN Lin. Damping properties of Mg-Ca binary alloys [J]. Physica B, 2008, 403(13): 2438-2442.
[25] YADOLLAHPOUR M, ZIAEIRAD S, KARIMZADEH F. A numerical study on the damping capacity of metal matrix nanocomposites [J]. Simulation Modelling Practice and Theory, 2011, 19(1): 337-349.
(Edited by YANG Hua)
Cite this article as: ZANG Qian-hao, CHEN Hong-mei, LAN Fang-yuan, ZHANG Jing, JIN Yun-xue. Effect of friction stir processing on microstructure and damping capacity of AZ31 alloy [J]. Journal of Central South University, 2017, 24(5): 1034-1039. DOI: 10.1007/s11771-017-3506-9.
Foundation item: Project(51301077) supported by the National Natural Science Foundation, China; Project(BK20130470) supported by the Natural Science Foundation of Jiangsu Province, China; Project supported by Priority Academic Program Development of Jiangsu Higher Education Institutions, China
Received date: 2016-01-25; Accepted date: 2016-05-28
Corresponding author: CHEN Hong-mei, PhD, Associate Professor; Tel: +86-15996843996; E-mail: hmchen@just.edu.cn