
Cold welding sealing of copper-water micro heat pipe ends
TANG Yong(汤 勇), LU Long-sheng(陆龙生), DENG Da-xiang(邓大祥), YUAN Dong(袁 冬)
School of Mechanical and Automotive Engineering, South China University of Technology,
Guangzhou 510640, China
Received 13 August 2008; accepted 20 November 2008
Abstract: The quality of micro heat pipe(MHP) is strongly affected by sealing technology. Based on the analysis of requirements of sealing technology, a cold welding technology was presented to seal MHP. In the cold welding process, compression force was used to flatten micro groove copper(MGC) tube. Then the bonding of MGC tube was reached because of intensively plastic deformation of MGC tube under pressure. It is found that the plastic deformation area of the cold welding of MGC tube can be divided into three sections. The deformation of micro grooves in each section was investigated; the influence of the dimensions of cylindrical heads on the weld joint shape and strength was studied; and a comparison between smooth copper tube and MGC tube was done. The results show that a groove compression stage exists in the cold welding of MGC tube besides a flattened stage and a melting stage.
Key words: heat pipes; cold welding; sealing technology; groove copper tube
1 Introduction
Heat dissipation problem of electronic chip is severe as the integrated level increases quickly[1-2]. Nowadays, the thermal density of chips has overflowed heat transfer ability of pure metal. Micro heat pipe(MHP) is considered to be an optimal choice for heat dissipation [3], and its diameter ranges from microns to several millimeters[4]. Generally, MHP mainly consists of three parts: a wick, working fluid and a shell. The working fluid of MHP is sealed in the shell at a relatively high vacuum condition in order to slow down its boiling temperature. For a low vacuum condition will worsen the performance of MHP[5], it is very important to keep vacuum environment in the shell steady and reliable. So, sealing technology to keep vacuuming needs to be studied.
Micro groove copper-water heat pipes are the ideal equipment for heat dissipation of electronic product [6-7]. And they are widely used with outer diameters of 4-6 mm nowadays[6]. To reduce thermal resistance, the shell is made of thin-wall oxygen-free copper tube with wall thickness less than 0.4 mm. After fabricating wick, filling working fluid, vacuuming and sealing, the MHP is fabricated. Most of the works about MHP are concentrated on analyzing and testing heat transfer performance, optimizing structure, and fabricating wicks[8]. The sealing technology of MHP is seldom studied, except some manufacture technology introductions in patents. A patented MHP sealing technology uses a pair of concave-convex moulds to form an extrusion sealed structure[9]. Another presents a double layer sealing structure manufactured by transverse compression with two pairs of moulds[10]. The sealing principle of the two patents is that the shell forms a binding interface under the action of compression force. Without metallurgical bonding, the compression strength of the sealed structure is relatively small.
Generally, the sealing technology of MHP should satisfy the following requirements. 1) The compression strength of its sealed structure should be large enough to bear its internal saturated vapor pressure. 2) The sealed structure should have a shrinkage section or a taper. For heat pipes only provide a passage with high heat transfer coefficient, it needs to nest plates on the condenser[11]. Otherwise, MHP can not dissipate the heat into atmosphere and its operating cycle will be interrupted.
Cold welding is a technology that the welded material reaches its yield strength and bonds to each other after intensively plastic deformation. There is a metallurgical bonding on contact surface. The quality of cold welding is influenced by workpiece surface quality, material and compression force[12]. In this work, a cold welding technology was presented to seal micro groove copper(MGC) tubes. The influence of cylindrical heads on weld joint shape and strength was studied. The deformation of micro grooves in plastic deformation area was investigated. And a contrast experiment between smooth copper tube and MGC tube was also done.
2 Experimental
At first, MGC tube was flattened under compression force. And the bonding of MHP shell was obtained as an intensively plastic deformation appeared with increasing the compression force. At last, the MHP shell was separated from the atmosphere and the sealing procedure of MHP was finished. In this work, the MGC tube, with 6 mm in outer diameter and 63 MPa in yield strength (σ0.2), was manufactured by an oil-filled high-speed spinning technology[13]. Parameters of MGC tube in details are listed in Table 1, and SEM image of MGC tube on cross section is shown in Fig.1, where d0 is the outer diameter of MGC tube; l0 is the average width of the grooves; h is the depth of the grooves; n is the number of the grooves on the cross section; t is the wall thickness of the grooves; and α is the angle of the grooves.
Table 1 Parameters of micro groove copper tube

Fig.2(a) shows the schematic diagram of the experiment apparatus, which consists of two cylindrical heads, two mounting moulds, two slideways and a foundation. The cylindrical head material is GCr15, with hardness of HRC 62-65, roughness Ra of 0.8 ?m, length of 15 mm and radius of R. The material of mounting mould is Cr12MoV, with hardness of HRC 58-60. The foundation material is 45# steel, with hardness of HRC 48-50.
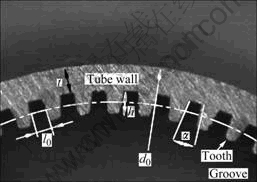
Fig.1 SEM image of MGC tube on cross section
The compression force was applied and detected by a minitype numeric-control general stretcher. The plastic deformation of the MGC tube by cold welding could be divided into three sections. SectionⅠwas the area that plastic deformation appeared but the contact of cylindrical head and MGC tube did not happen; section Ⅱ was the area that the contact of cylindrical head and MGC tube happened but the bonding of shell did not happen; and section Ⅲ was the area that the bonding of shell happened, as shown in Fig.2(b). In Fig.2, γ is the curvature of deformation section Ⅱ, β is the curvature of deformation section Ⅲ. Furthermore, as the cold welding finished, compressed air was pumped into the shell and the sealed structure was immersed into water. The pressure of compressed air was adjusted to increase gradually until bubble formed. Then, the pressure value was recorded. So the compression strength of the sealed structure can be calculated by the pressure of the compressed air.
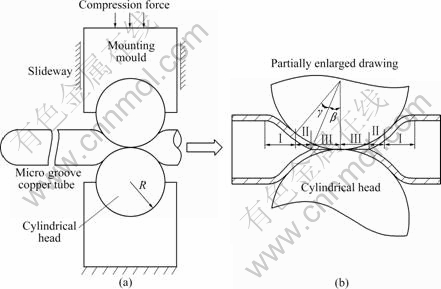
Fig.2 Schematic diagram of cold welding (a) and three sections of cold welding (b)
3 Results and discussion
3.1 Influence of cylindrical head diameter
Fig.3 shows the photo of MGC tube after cold welding, where L is the length of plastic deformation section in the axial direction, and B is the width of weld joint in maximum. Eq.(1) gives the values of L:
L=L1+L2+L3 (1)
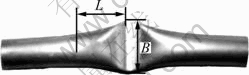
Fig.3 Photo of MGC tube after cold welding
where L1 is the length of sectionⅠ; L2 is the length of section Ⅱ, as shown in Eq.(2); and L3 is the length of section Ⅲ, as shown in Eq.(3).
L2=Rsin(γ+β)-L3 (2)
(3)
is the average wall thickness of MGC tube, as shown in Eq.(4):
(4)
The dimensions and strength of MGC tube after cold welding with different diameters of cylindrical heads are listed in Table 2. ΔL is the increment of length in the axial direction after cold welding; and p is the compression strength of the sealed structure.
Table 2 Parameters of weld joint of MGC tube
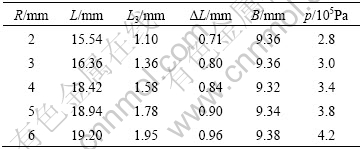
The experiment shows that the values of L, L3 and ΔL increase as the diameter of cylindrical head increases. The increase of L is caused by the reduced curvature γ and β, which results in the slope of sectionⅠslowing down. The increase of L3 could be explained by Eq.(3). The increase of ΔL results from the intensively plastic deformation of MGC tube during cold welding. It is found that the increases of ΔL and L3 are in a same dimension range. And it is also found that B, which is nearly equal to its ideal value as shown in Eq.(5), seldom changes as R changes.
B≈Bi=πd0/2 (5)
Because the deformation resistance in the width direction is larger than that in the axial direction for the action of hoop stress, the plastic deformation in section Ⅲ inclines to the axial direction. The compression strength experiments show that p increases as the diameter of cylindrical head increases. But the compression force for cold welding also increases. It could be attributed to the increase of L3.
In general, when designing the cold welding technology for the sealing of MHP, the choice of cylindrical head dimensions should be based on the factors of the compression strength requirement, the nest plate requirement and manufacture condition.
3.2 Changes of grooves in deformation section
The groove structure is an important factor that affects the performance of the micro groove copper- water heat pipes. The heat transfer coefficient of MHP becomes worse if the grooves are damaged. Thus, it is essential to study the changes of grooves during cold welding. Fig.4 shows the groove shapes at different deformation sections.
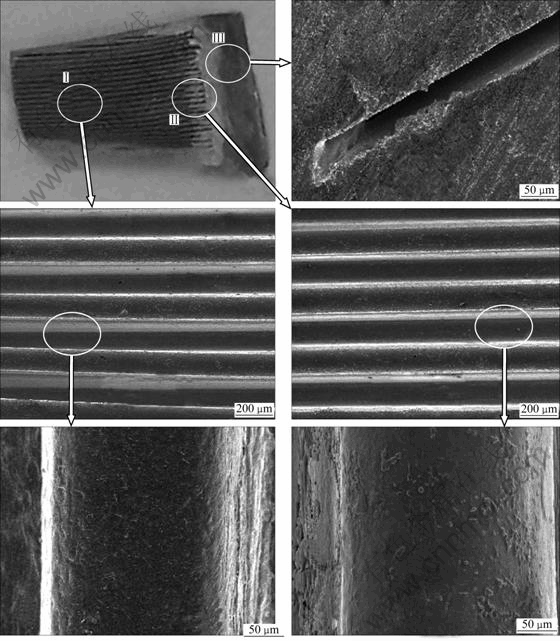
Fig.4 Groove shapes at different deformation sections
The changes of grooves in each deformation section could be divided into two areas for consideration: curving area and flattened surface area that face the cylindrical head. In the curving area, the grooves squeeze each other in all three deformation sections, but the intensity of squeeze grows from the sectionⅠto the section Ⅱ, and eventually the grooves disappear at the curving area in section Ⅲ. In the flattened surface area, at sectionⅠ, only α changes no more than 20% as the MGC roundness changes; at section Ⅱ, the change of α grows larger for a curvature appears in MGC tube, besides, the parameter h reduces gradually; at section Ⅲ, the grooves disappear eventually for an intensive plastic deformation happens under the compression force, but a small clearance channel still exists in the area close to section Ⅱ.
The manufacture and cold welding of MGC tube result in the work-hardening of the shell and grooves, but the work-hardening intensities of the shell and grooves are inconsistent. Furthermore, the huge plastic deformation results in a lot of residual stress concentrated on the contact surface. Thus, in the compression strength test, it is found that the weld joint tears along the contact surface when the pressure of compressed air overflows the sealed structure strength, although a metallurgical bonding has appeared at the contact surface in cold welding. In general, the weld joint is fragile when impact happens. And the compression strength of the weld joint in cold welding is only about 0.4 MPa, which makes the MHP can only work under 140 ℃. But for its high productivity and easy operating, the cold welding of MGC tube is useful and applicable for MHP working at room temperature or as a transitional sealing technology in MHP production. If using plasma welding, laser welding and braze welding for further treatment, the cold welding is applicable in lots of places, as shown in Fig.5.

Fig.5 Sealing structure of MHP with cold welding and plasma welding
3.3 Compression force curves in cold welding
3.3.1 Influence of groove
A contrast test of compression force curves between smooth copper tube and MGC tube was done, as shown in Fig.6, where R is 6 mm, wall thickness of smooth copper tube is 0.46 mm, which is equal to the sum of h and t.
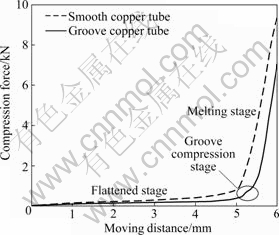
Fig.6 Compression force curves of smooth and groove copper tubes in cold welding
Experimental results show that a groove compression stage exists in the cold welding of MGC tube besides a flattened stage and a melting stage exist in the smooth copper tube and MGC tube. The flattened stage begins at the moment of the contact of cylindrical head and tube, and ends at the moment of the appearance of the section Ⅲ. At the flattened stage, the compression force increases slowly, but the slope of its curves also increases as the cylindrical head moves. This is due to the influence of work-hardening. The difference between the curves in the flattened stage is that the values of slope and compression force of MGC tube are smaller than those of the smooth copper tube, because the grooves weaken the rigidity of tube in MGC tube. Based on the least-energy principle, the plastic deformation will always happen in the grooves.
The groove compression stage begins at the moment of the contact of grooves top, and ends at the moment of the contact of groove bottom. For the difference between the force of groove squeezing and the force of tube flattening is relatively small, the curve in compression stage is a wave. But with the movement of the cylindrical head, the force of groove squeezing will take the dominant position gradually, and the fluctuation range will become small. The range of the compression groove stage is h-2 h.
The melting stage is the remaining range of MGC tube cold welding. For there is no gap between two cylindrical heads, a little movement of cylindrical head will result in huge plastic deformation and work- hardening in the section Ⅲ. Thus, the increase of compression force is quick, and the slope of compression force curves is larger than other two deformation sections. By comparing the two curves in Fig.6, it is found that the compression force of the smooth copper tube is still larger than that of MGC tube. This is because the wall thickness of smooth copper tube is larger than that of MGC tube. However, it is also found that the slope of the curve of MGC tube is larger than that of the smooth copper tube. It is because that the work- hardening of MGC tube is more intensive than that of the smooth copper tube.
3.3.2 Influence of shrinkage process
Because B is larger than d0, for the convenience of nest plate, it is essential for the sealed structure to have a shrinkage section or a taper before cold welding. The diameter of the shrinkage section could be deduced as
d1<2d0/π (6)
where d1 is the diameter of the shrinkage section, and d1=3.5 mm in this work. Fig.7 shows the images of shrinkage part of the MGC tube, which was fabricated by a radial forged machining technology[14]. It could be found that the wall thickness of the shell increases, while the depth of the grooves reduces. And parameters of the MGC tube at shrinkage section are listed in Table 3 in detail.
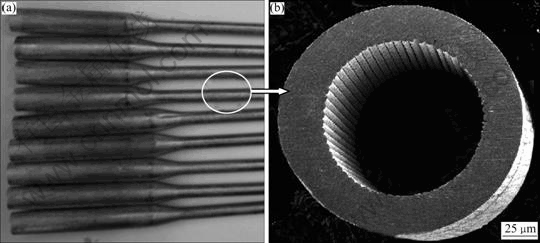
Fig.7 Shrinkage of MGC tube (a) and SEM image of cross section (b)
Table 3 parameters of MGC tube at shrinkage section

With a cylindrical head, in which R=12 mm, the shrinkage section is also sealed with cold welding, as shown in Fig.8. It could be found that the maximum width of weld joint is 5.3 mm, which is smaller than the original diameter (6 mm). Thus, nest plate on the condenser of MHP is convenient to use.
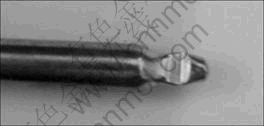
Fig.8 Cold welding after shrinking of micro groove copper tube
The compression force curve of the cold welding on the shrinkage section is shown in Fig.9. Compared with Fig.6, in the flattened stage, it is found that the compression force after shrinking is larger than that of unshrinking with the same moving distance of the cylindrical head. For example, the compression force is 835.76 N as moving distance is 2.8 mm after shrinking, but that of unshrinking is only 180 N. This is because the wall thickness of shell increases and the plastic deformation in shrinking results in the work-hardening of the workpiece, then the resistance of deformation after shrinking is increased. Furthermore, the range of the groove compression stage after shrinking reduces by 65%, which is just equal to the reduction of groove depth, compared with that of unshrinking. In the melting stage, both the slope of curves and the final compression force of the cold welding after shrinking are smaller than those of unshrinking. This is caused by the larger plastic deformation of the cold welding before shrinking than that of shrinking.
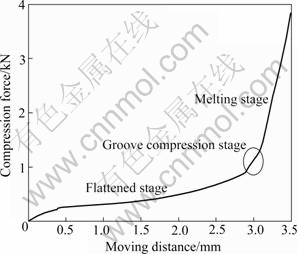
Fig.9 Compression force curve of MGC tube after shrinking
4 Conclusions
1) A cold welding can satisfy the sealing technology of MHP very well. And the plastic deformation of cold welding could be divided into three sections.
2) The shape and strength of the weld joint are influenced by the diameter of cylindrical head. But there is little relation between the maximum width of the weld joint and the diameter of cylindrical head.
3) In sectionⅠ, only α changes no more than 20%. In section Ⅱ, the change of α grows larger, besides, the parameter h reduces gradually. In section Ⅲ, the grooves disappear eventually because of an intensive plastic deformation. Although a metallurgical bonding appears at the section Ⅲ in cold welding, the weld joint tears along the contact surface when the pressure of compressed air overflows the sealed structure strength.
4) A groove compression stage exists in the cold welding of MGC tube. A flattened stage and a melting stage exist both in the smooth copper tube and MGC tube.
5) In the flattened stage, the compression force after shrinking is larger than that of unshrinking with the same moving distance of the cylindrical head. In the melting stage, both the final compression force and the slope of curves after shrinking are smaller than those of unshrinking.
References
[1] CHI Yong, TANG Yong, CHEN Jin-chang, DENG Xue-xiong, LIU Lin, LIU Xiao-kang, LIU Xiao-qing. Ploughing-extrusion mechanism of V-shaped capillary micro-grooves based on surface of copper strip [J]. Trans Nonferrous Met Soc China, 2006, 16(9): 277-282.
[2] JIAO A J, MA H B, CRITSER J K. Evaporation heat transfer characteristics of a grooved heat pipe with micro-trapezoidal grooves [J]. International Journal of Heat and Mass Transfer, 2007, 50(15/16): 2905-2911.
[3] VASILIEV L L. Micro and miniature heat pipes—Electronic component coolers [J]. Applied Thermal Engineering, 2008, 28(4): 266-273.
[4] BALRAM S. Modeling, experiment, and fabrication of micro-grooved heat pipes: An update [J]. J Appl Mech-T ASME, 2007, 60(3): 107-119.
[5] POPOVA N, SCHAEFFER C H, AVENAS Y, KAPELSKI G. Fabrication and thermal performance of a thin flat heat pipe with innovative sintered copper wick structure [C]// Industry Applications Conference, 2006. 41st IAS Annual Meeting. Conference Record of the 2006 IEEE,USA. 2006: 791-796.
[6] VASILIEV L L. Heat pipes in modern heat exchangers [J]. Applied Thermal Engineering, 2005, 25(1): 1-19.
[7] NILSON R H, TCHIKANDA S W, GRIFFITHS S K, MARTINEZ M J. Steady evaporating flow in rectangular microchannels [J]. International Journal of Heat and Mass Transfer, 2006, 49(9/10): 1603-1618.
[8] IOAN S, GREG C, RAVI M, MICHELE S. Air-cooling extension- performance limits for processor cooling applications [C]// Annual IEEE Semiconductor Thermal Measurement and Management Symposium, USA. 2003: 74-81.
[9] HSU H C. Extrusion-sealed structure of heat pipe: US, 7192064B2 [P]. 2007.
[10] HSU H C. Shrinkage-free sealing structure of heat pipe: US, 7229104B2 [P]. 2007.
[11] KIM K S, WON M H, KIM J W, BACK B J. Heat pipe cooling technology for desktop PC CPU [J]. Apply Thermal Engineering, 2003, 23(9): 1137-1144.
[12] DANESH MANESH H, MASHREGHI A, EHTEMAN HAGHIGHI S, KHAJEH A. Investigation of cold pressure welding of aluminum powder to internal surface of aluminum tube [J]. Materials & Design, 2009, 30(3): 723-726.
[13] TANG Yong, CHI Yong, CHEN Jin-chang, DENG Xue-xiong, LIU Lin, WAN Zhen-ping, LIU Xiao-kang. Experimental study of oil-filled high-speed spin forming micro-groove fin-inside tubes [J]. International Journal of Machine Tools & Manufacture, 2007, 47(7/8): 1059-1068.
[14] GHAEI A, TAHERI A K, MOVAHHEDY M R. A new upper bound solution for analysis of the radial forging process [J]. International Journal of Mechanical Sciences, 2006, 48(11): 1264-1272.
Foundation item: Projects(50436010, 50705031) supported by the National Natural Science Foundation of China; Projects(07118064, 8151064101000058) supported by the Natural Science Foundation of Guangdong Province, China
Corresponding author: LU Long-sheng; Tel/Fax: +86-20-87114634; E-mail: drgonly@126.com
DOI: 10.1016/S1003-6326(08)60314-3
(Edited by YANG Bing)