文章编号:1004-0609(2013)04-1027-07
含钙电解质对Mg-1.0Ca合金微弧氧化膜性能的影响
张勇强1,郭世柏1,张荣发2,张淑芳2,姚灵菊2,谢辛玲2
(1. 湖南科技大学 机电工程学院,湘潭 411201;
2. 江西科技师范大学 材料与机电学院,南昌 330013)
摘 要:在含6 g/L氢氧化钠和15 g/L植酸钠的基本溶液中,分别加入4种钙盐研究钙盐,对Mg-1.0Ca合金微弧氧化膜性能影响。使用SEM、EDS和XRD分析陶瓷氧化膜的表面形貌、成分及结构,通过点滴实验和动电位极化曲线来判定氧化膜的腐蚀降解速率。结果表明:CaCO3可稍微增加氧化膜的钙含量,使氧化膜厚度由3.4 μm增加到8.8 μm,且明显改善表面微孔均匀性。点滴实验和动电位极化曲线分析表明:CaCO3能显著提高氧化膜的耐蚀性能,其点滴时间由75 s提高至116 s,自腐蚀电流密度由3.898 μA/cm2降低至1.473 μA/cm2,且自腐蚀电位由-1.538 V升高至-1.465 V。
关键词:镁钙合金;微弧氧化;腐蚀降解速率;钙盐
中图分类号:TG174 文献标志码:A
Effects of calcium-containing electrolytes on property of
anodic coatings obtained by micro arc oxidation on Mg-1.0Ca alloys
ZHANG Yong-qiang1, GUO Shi-bo1, ZHANG Rong-fa2, ZHANG Shu-fang2, YAO Ling-ju2, XIE Xin-ling2
(1. College of Electro-mechanical Engineering, Hunan University of Science and Technology, Xiangtan 411201, China;
2. School of Materials and Electromechanics, Jiangxi Science and Technology Normal University,
Nanchang 330013, China)
Abstract: Four kinds of calcium salts were separately added into a base solution of 6 g/L NaOH and 15 g/L sodium phytate, and their influences on the property of anodic coatings formed on Mg-1.0Ca alloys were investigated. The surface morphologies, chemical compositions and structures were characterized by scanning electron microscopy (SEM), energy dispersive spectroscopy (EDS) and X-ray diffractometry (XRD). The dropping test and potentiodynamic polarization tests were applied to evaluate the corrosion degradation rate of anodic coatings. The results demonstrate that CaCO3 can slightly increase the calcium content. The coating thickness increases from 3.4 μm to 8.8 μm and the coating porous uniformity of anodic coatings is obviously improved. The dropping test and potentiodynamic polarization curve analysis shows that CaCO3 can significantly improve corrosion resistance of the anodic coatings. The drop time is extended from 75 s to 116 s, and the self-corrosion current density is reduced from 3.898 μA/cm2 to 1.473 μA/cm2,while the corrosion potential is improved from -1.538 V to -1.465 V.
Key words: magnesium-calcium alloys; micro arc oxidation; corrosion degradation rate; calcium salt
基金项目:国家自然科学基金资助项目(51061007);江西省教育厅资助项目(GJJ12585)
收稿日期:2012-05-22;修订日期:2012-11-04
通信作者:张荣发,教授,博士;电话:0791-83831266;E-mail: rfzhang-10@163.com
随着科学技术的发展、人口老龄化以及工业、交通、体育等导致的创伤增加,人们对生物医用材料及其制品的需求越来越大。目前,临床上广泛使用的骨折内固定器材多由不锈钢及钛合金制造。与以上金属材料相比,镁合金具有以下优势[1-5]:1) 其他金属生物材料在体液中腐蚀或磨损后可能释放出有毒的离子或颗粒,引起发炎、导致组织损坏,而镁是人体必须的元素之一。2) 镁合金的弹性模量(45 GPa)与人骨更接近,能有效地缓解应力遮挡效应。3) 镁及其合金作为可降解材料,可避免二次手术,减少患者痛苦和经济负担。虽然镁合金在生物医用领域具有独特的应用前景,但其在人体中腐蚀降解速度过快,制约了其临床应用,因此,改善镁合金本身的耐腐蚀性能以及完善表面改性技术成为镁合金在骨科内植入材料领域应用的关键。
微弧氧化是一种新兴镁合金表面处理技术,能有效提高氧化膜的耐蚀性、耐磨性以及与基体结合能 力。由于钙和磷是人体必须的宏量元素,且钙磷盐具有良好的生物活性,并能促进植入物/骨界面早期骨的生 长[6],因此筛选能使生成的氧化膜富含钙磷的电解质成为近年来制备生物涂层研究的重点。微弧氧化使用的含钙电解质有Ca(CH3COO)2[7]、CaCO3[8]、Ca(H2PO4)2[9]和Ca(OH)2[10]等,实验结果表明:在氧化过程中,电解质中的钙能进入氧化膜中[8-10]。目前,使用的含磷电解质主要是无机磷酸盐[8-12],但其氧化膜耐蚀性不如硅酸钠,在含氯化钠溶液中腐蚀速率达1.1 mm/a[11],不能满足镁合金作为可降解生物植入材料的鉴定标准。作为一种含磷的环保型有机物,植酸具有很多生理活性和保健功能,可用作抗癌剂、食品抗氧化剂和保鲜剂等[13]。近年来,植酸已用于镁合金微弧氧化的电解质[14-15],结果表明:植酸氧化膜耐蚀性比硅酸钠氧化膜好[15]。植酸钠是植酸的盐类衍生物,比植酸有着更广的应用范围,如作为食品添加剂,1995年,植酸没有被美国食品和药品管理部门赋予“公认安全”(Generally recognized as safe, GRAS)的身份,而植酸钠于1997年获得此身份[13],但目前未见将植酸钠用作镁合金微弧氧化电解质的研究报道。本文作者在含全新环保型有机含磷电解质-植酸钠的碱性溶液中添加不同钙盐,研究钙盐对镁合金微弧氧化膜性能的影响,筛选出使氧化膜富含钙磷成分且具有较低腐蚀降解速率的含钙电解质,为镁钙合金在生物材料领域的应用打下基础。
1 实验
使用Mg-1.0Ca合金,试样规格为50 mm×60 mm×10 mm。分别采用180#~1000#的水砂纸由粗到细逐级打磨,然后经蒸馏水清洗,无水乙醇擦洗,热吹风吹干,置入干燥器中待用。本文作者在含6 g/L氢氧化钠和15 g/L植酸钠的基本溶液中,分别添加 15 g/L CaCO3、2 g/L Ca(OH)2、0.5 g/L Ca(CH3COO)2和5 g/L Ca(H2PO4)2进行微弧氧化处理,并将溶液分别命名为基本溶液、CaCO3体系、Ca(OH)2体系、Ca(CH3COO)2体系、Ca(H2PO4)2体系。
采用国产MAOI-50C微弧氧化电源,使用单(正)脉冲恒流控制,各溶液使用相同的电参数,即电流密度40 mA/cm2,占空比35%,频率2 kHz,氧化时间210 s。
使用TT260型数字式覆层涡流测厚仪测量氧化膜厚度。采用ΣIGMA FE扫描电子显微镜观察试样表面形貌,并用其附带的能谱仪分析膜层的元素组成;采用D8 ADVANCE X射线衍射仪分析陶瓷膜的物相组成。参照HB5061-77点滴腐蚀法检测微弧氧化所得膜层的耐蚀性[16]。检测方法为在试样表面选定区域用滴定管滴下一滴腐蚀液,记录腐蚀液变色时间,取3次检测的平均值来评估膜层的耐蚀性。点滴液变色时间越长,表明氧化膜的耐蚀性越好。
电化学测试在CHI660C电化学工作站上进行。采用标准三电极体系:参比电极为饱和甘汞电极(SCE),辅助电极为铂电极,试样为工作电极(裸露面积为1 cm2),电解液为Hank’s溶液[17]。测试前在开路电位下浸泡20 min,以保证测试过程稳定。扫描参数为:初始电位-1.8 V,终止电位-1.0 V,扫描速度1 mV/s。
2 实验结果与讨论
2.1 电解液有效组分的筛选
根据点滴时间,初步筛选电解液的组分。Mg-1.0Ca合金在不同溶液中微弧氧化膜层厚度及点滴变色时间如图1所示。
从图1可知,在基本溶液中加入钙盐后对氧化膜的厚度和耐蚀性影响显著。CaCO3和Ca(H2PO4)2能显著提高氧化膜的厚度,而Ca(OH)2和Ca(CH3COO)2对氧化膜的厚度影响较小。从氧化膜点滴时间来 看,在基本溶液中制备的氧化膜变色时间只有75 s,当分别添加Ca(OH)2、CaCO3、Ca(H2PO4)2之后,变色时间分别延长到88、116和106 s;而当添加Ca(CH3COO)2后,氧化膜的变色时间只有60 s,比在基本溶液中制备的氧化膜缩短了15 s。由此可知,CaCO3不仅增加了微弧氧化膜的厚度,而且降低了腐
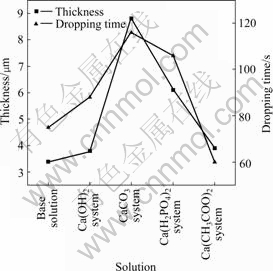
图1 不同钙盐对膜层厚度及点滴时间影响
Fig. 1 Effects of different calcium salts on coating thickness and dropping time
蚀降解速率;但Ca(CH3COO)2却使氧化膜的腐蚀降解速率加快。
2.2 不同钙盐对氧化膜的形貌的影响

在基本溶液中加入不同钙盐后制备的氧化膜层表面形貌见图2。
由图2可知,氧化膜表面都分布着小孔,这些孔洞是氧化继续进行的放电通道,加入的钙盐不同,氧化膜的表面形貌也不同。由图2(a)可知,在基本溶液中形成的氧化膜表面微孔分布不太均匀,孔与孔之间的距离较大。在基本溶液中加Ca(OH)2后,氧化膜表面微孔分布均匀,孔径变小,为0.5~1.5 μm,但孔与孔之间的距离也变小,为1~1.5 μm (图2(b))。当加入CaCO3后,氧化膜表面孔分布较均匀,孔径集中在1.5~2.5 μm,孔与孔之间的距离较大,为3~5 μm,且产生少量细小微裂纹(图2(c)),是由于氧化熔融物被电解液快速冷却时热应力过大所致。在Ca(H2PO4)2体系中,氧化膜表面微孔直径较大,为1.5~5 μm,孔与孔之间的距离较大,许多较大的孔向外凸起(图2(d))。由图2(e)可知,加入Ca(CH3COO)2后,氧化膜表面微孔分布较均匀,孔径为1.0~2.0 μm,孔与孔之间的距离也增大,但氧化膜表面裂纹较大,且产生脱落现象。
图2 Mg-1.0Ca在不同钙盐电解液体系中制备的氧化膜层表面形貌
Fig. 2 Surface morphologies of anodic coatings obtained in electrolyte systems with different calcium salts on Mg-1.0Ca: (a) Base solution; (b) Ca(OH)2 system; (c) CaCO3 system; (d) Ca(H2PO4)2 system; (e) Ca(CH3COO)2 system
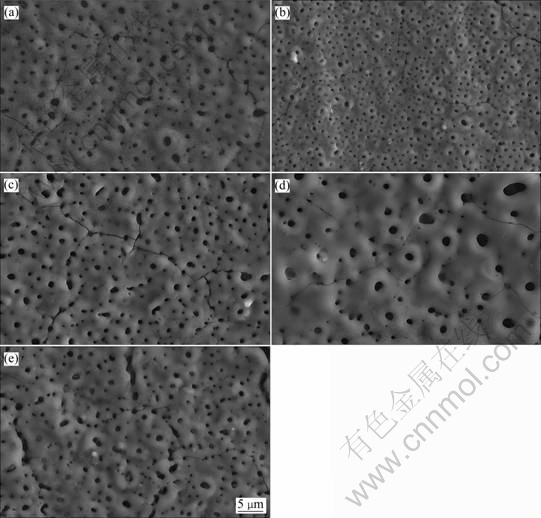
2.3 膜层能谱分析
为进一步研究不同钙盐对微弧氧化膜成分影响,分别对各组分制备的膜层进行能谱分析,结果见图3。
由图3可知,将钙盐加入基本溶液后,氧化膜中的Ca含量都得到了提高,其中加入CaCO3与Ca(CH3COO)2制备的氧化膜层中Ca元素的含量增加较多;而添加Ca(OH)2后,Ca含量增加最少,且P元素含量比基本溶液中有所降低,说明加入Ca(OH)2后,不利于植酸钠参与氧化膜形成。因此,通过添加不同的钙盐可以在一定程度上改变膜层中Ca和P的成分。
图3 Mg-1.0Ca在不同钙盐电解液体系中制备的氧化膜EDS能谱
Fig. 3 EDS results of anodic coatings obtained in electrolyte systems with different calcium salts on Mg-1.0Ca: (a) Base solution; (b) Ca(OH)2 system; (c) CaCO3 system; (d) Ca(H2PO4)2 system; (e) Ca(CH3COO)2 system
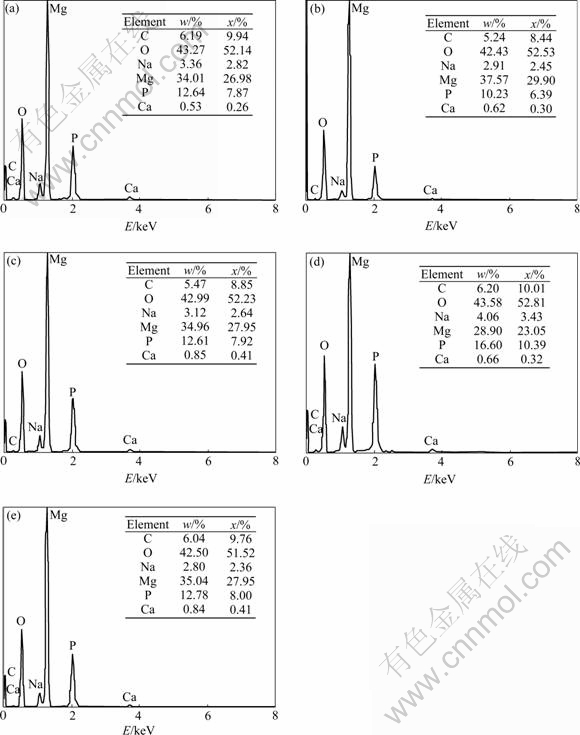
2.4 膜层的相组成
分别对添加不同钙盐制备的氧化膜进行XRD测试,其结果见图4。
根据图4,在5种溶液中生成的氧化膜主要晶相为MgO,由于膜层较薄且多孔,出现了基体中Mg和Mg2Ca合金相的衍射峰。结合图3可知,膜层中同时含有P、C、Ca元素,但在XRD谱分析中没有显示含P、C元素相的物质存在,这可能是由于此类产物较少或以非晶相存在。本实验以植酸钠为基本组分,且在5种溶液中得到的氧化膜含磷量都较高,说明植酸钠参与了氧化膜的形成,生成不能被XRD检测的螯合物如植酸镁[14]。
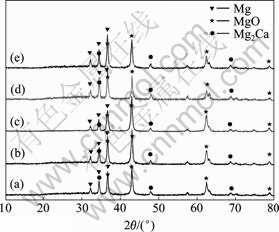
图4 Mg-1.0Ca在不同钙盐电解液体系中制备的氧化膜的XRD谱
Fig. 4 XRD patterns of anodic coatings obtained in electrolyte systems with different calcium salts on Mg-1.0Ca: (a) Base solution; (b) Ca(OH)2 system; (c) CaCO3 system; (d) Ca(H2PO4)2 system; (e) Ca(CH3COO)2 system
2.5 电化学极化曲线分析
镁合金分别在基本溶液及添加不同钙盐后制备的氧化膜在Hank’s溶液中测得的电化学塔菲尔极化曲线如图5所示。极化曲线的动力学参数见表1。
自腐蚀电位(φcorr)可衡量材料在介质中的腐蚀倾向,此值越大则代表腐蚀倾向越小。从表1可知,在基础溶液中制备的氧化膜的腐蚀电位为-1.538 V,腐蚀电流密度为3.898 μA/cm2。而加入不同钙盐后制备的微弧氧化膜的腐蚀电位相应都有所提高,表明加入钙盐制备的膜层的腐蚀倾向变小。但腐蚀发生反应的速率则要看实际发生反应的Jcorr的大小,也即腐蚀动力学意义上的速度,Jcorr值越大,则说明腐蚀反应速度越快,程度越深。由表1中可知,在Ca(CH3COO)2溶液体系中制备的微弧氧化膜的自腐蚀电流最大,表明添加Ca(CH3COO)2制备的膜层腐蚀反应速度最快;而其他钙盐的加入都相应的使自腐蚀电流有所减小,其中在CaCO3体系中制备的微弧氧化膜的电流降低最多(Jcorr=1.473 μA/cm2)。表明加入碳酸钙之后,腐蚀速率最小,腐蚀程度最小。根据图5和表1可知,在基本溶液中加入碳酸钙制备的微弧氧化膜具有更好的耐蚀性能,这与图1中的点滴实验结果相吻合。
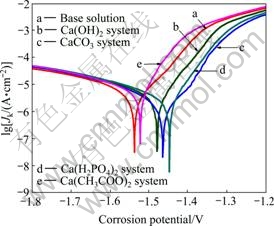
图5 Mg-1.0Ca在不同钙盐电解液体系中制备的氧化膜的动电位极化曲线
Fig. 5 Polarization curves of anodic coatings obtained in electrolyte with different calcium salts on Mg-1.0Ca
表1 不同钙盐组分下微弧氧化膜的动电位极化曲线参数
Table 1 Parameters of potentiodynamic polarization curves of anodic coatings obtained in solutions with different kinds of calcium salts on Mg-1.0Ca
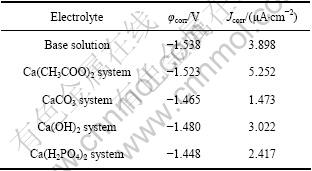
2.6 讨论
氧化膜的厚度和致密性以及相组成是影响其耐腐蚀性的3个主要因素[18]。由于膜层能防止或减缓外界腐蚀介质进入基体,从而可提高基体的耐蚀性。当陶瓷膜表面的孔径较大、孔洞较多、微裂纹等缺陷较多时,腐蚀介质就很容易进入基体,从而膜层对镁合金基体的保护作用就下降。本文作者在基本溶液中添加4种钙盐后,发现CaCO3不仅显著提高了微弧氧化膜的厚度,而且改善了微弧氧化膜的表面形貌和微观结构,表面微孔孔径大小和孔隙分布均匀,且表面没有明显缺陷,因此,加入CaCO3制备的膜层具有较高的耐蚀性能,这从点滴实验和电化学极化曲线得到了证实。另外,由EDS和XRD分析结果可知,加入CaCO3能有效地改善膜层中的钙、磷含量比,且膜层中的MgO以及含钙、镁的磷酸盐和碳酸盐非晶态化合物能有效地改善膜层的致密性,降低膜层的腐蚀降解速率。可见,CaCO3可以有效地增加微弧氧化膜层的厚度,改善表面微观形貌和化学组成及结构,进而提高膜层的耐腐蚀性能。
3 结论
1) 在基本溶液中加入钙盐后,所形成的氧化膜中Ca的含量都得到了提高,其中CaCO3与Ca(CH3COO)2使氧化膜层中Ca含量较多,而Ca(OH)2使氧化膜层中Ca含量增加较少。
2) 表面形貌表明,Ca(OH)2使氧化膜表面微孔分布更均匀、孔径更小;CaCO3能改善氧化膜表面微孔均匀性,增大孔间距,但会产生少量细小裂纹;Ca(H2PO4)2增大氧化膜微孔直径和孔间距;Ca(CH3COO)2会增加氧化膜表面裂纹,且产生脱落现象。
3) CaCO3、Ca(OH)2和Ca(H2PO4)2可显著降低氧化膜的腐蚀降解速率,其中CaCO3的作用效果最明显;而Ca(CH3COO)2 却增大了氧化膜的腐蚀降解速率。
4) X射线衍射分析表明,在各组分电解液中制备的微弧氧化膜层主要含MgO相。
REFERENCES
[1] WEN C L, GUAN S K, PENG L, REN C X, WANG X, HU Z H. Characterization and degradation behavior of AZ31 alloy surface modified by bone-like hydroxyapatite for implant applications[J]. Applied Surface Science, 2009, 255: 6433-6438.
[2] 朱生发, 徐 莉, 黄 楠. 可降解镁基生物材料的研究进展[J]. 生物医学工程学会杂志, 2009, 26(2): 437-439.
ZHU Sheng-fa, XU Li, HUANG Nan. Development of biodegradable magnesium based biomaterials[J]. Journal of Biomedical Engineering, 2009, 26(2): 437-439.
[3] SONG G L. Control of biodegradation of biocompatible magnesium alloys[J]. Corrosion Science, 2007, 49: 1696-1701.
[4] 高家诚, 李龙川, 王 勇, 乔丽英. 表面改性纯镁的细胞毒性和溶血率[J]. 稀有金属材料与工程, 2005, 34(6): 903-906.
GAO Jia-cheng, LI Long-chuan, WANG Yong, QIAO Li-ying. Biocompatibility of magnesium after surface modification by heat-organic films-treatment[J]. Rare Metal Materials and Engineering, 2005, 34(6): 903-906.
[5] 袁广银, 张 佳, 丁文江. 可降解医用镁基生物材料的研究进展[J]. 中国材料进展, 2011, 30(2): 44-47.
YUAN Guang-yin, ZHANG Jia, DING Wen-jiang. Research progress of Mg-based alloys as degradable biomedical materials[J]. Materials China, 2011, 30(2): 44-47.
[6] 葛淑萍, 王贵学, 沈 阳, 张 勤, 贾东丽. 镁基合金应用于生物医用材料的研究进展[J]. 材料导报, 2010, 24(3): 124-126.
GE Shu-ping, WANG Gui-xue, SHEN Yang, ZHANG Qin, JIA Dong-li. Research developments of magnesium alloys as biomedical material[J]. Materials Review, 2010, 24(3): 124-126.
[7] 夏琦兴, 姚忠平, 张亚军, 李梁梁, 姜兆华. 镁合金微弧氧化陶瓷膜的组织结构及耐腐蚀性能[J]. 材料保护, 2011, 44(5): 14-16.
XIA Qi-xing, YAO Zhong-ping, ZHANG Ya-jun, LI Liang-liang, JIANG Zhao-hua. Microstructure and corrosion resistance of micro-arc oxidation ceramic coating on magnesium alloy[J]. Journal of Materials Protection, 2011, 44(5): 14-16.
[8] 陈 娟. 镁锌基合金表面复合涂层制备及生物特性研究[D]. 郑州: 郑州大学, 2009: 1-95.
CHEN Juan. Fabrication and biocharacter of composite coating on Mg-Zn based alloy[D]. Zhengzhou: Zhengzhou University, 2009: 1-95.
[9] YAO Z P, LI L L, JIANG Z H. Adjustment of the ratio of Ca/P in the ceramic coating on Mg alloy by plasma electrolytic oxidation[J]. Applied Surface Science, 2009, 255: 6724-6728.
[10] SRINIVASAN P B, LIANG J, BLAWERT C, ST?RMER M, DIETZEL W. Characterization of calcium containing plasma electrolytic oxidation coatings on AM50 magnesium alloy[J]. Applied Surface Science, 2010, 256: 4017-4022.
[11] DURDU S, AYTAC A, USTA M. Characterization and corrosion behavior of ceramic coating on magnesium by micro-arc oxidation[J]. Journal of Alloys and Compounds, 2011, 509: 8601-8606.
[12] BAI K F, ZHANG Y, FU Z Y, ZHANG C L, CUI X Z, MENG E C, GUAN S K, HU J H. Fabrication of chitosan/magnesium phosphate composite coating and the in vitro degradation properties of coated magnesium alloy[J]. Materials Letters, 2012, 73: 59-61.
[13] DOST K, TOKUL O. Determination of phytic acid in wheat and wheat products by reverse phase high performance liquid chromatography[J]. Analytica Chimica Acta, 2006, 558: 22-27.
[14] ZHANG R F, XIONG G Y, HU C Y. Comparison of coating properties obtained by MAO on magnesium alloys in silicate and phytic acid electrolytes[J]. Current Applied Physics, 2010, 10: 255-259.
[15] ZHANG R F, ZHANG S F, DUO S W. Influence of phytic acid concentration on coating properties obtained by MAO treatment on magnesium alloys[J]. Applied Surface Science, 2009, 255: 7893-7897.
[16] HB5061—77. Standard quality test method for chemical oxidation film of magnesium alloys[S].
[17] ZHANG C Y, ZENG R C, CHEN R S, LIU C L, GAO J C. Preparation of calcium phosphate coatings on Mg-1.0Ca alloy[J]. Transactions of Nonferrous Metals Society of China, 2010, 20(s): s655-s659.
[18] 骆海贺, 蔡启舟, 魏伯康, 余 博, 何 剑, 李定俊. 添加剂浓度对微弧氧化陶瓷层结构及耐蚀性的影响[J]. 中国有色金属学报, 2008, 18(6): 1082-1087.
LUO Hai-he, CAI Qi-zhou, WEI Bo-kang, YU Bo, HE Jian, LI Ding-jun. Effects of additive concentration on microstructure and corrosion resistance of ceramic coatings formed by micro-arc oxidation on AZ91D Mg alloy[J]. The Chinese Journal of Nonferrous Metals, 2008, 18(6): 1082-1087.
(编辑 李艳红)