
Effects of electromagnetic field intensity on as-cast microstructures and mechanical properties of Al-Zn-Mg-Cu-Zr alloy
ZUO Yu-bo(左玉波), ZHAO Zhi-hao(赵志浩), WANG Qi-wei (王启伟), CUI Jian-zhong(崔建忠)
Key Laboratory of Electromagnetic Processing of Materials, Northeastern University, Shenyang 110004, China
Received 28 July 2006; accepted 15 September 2006
Abstract: Al-Zn-Mg-Cu-Zr ingots with diameter of 200 mm were made by low frequency electromagnetic casting (LFEC) and conventional direct chill (DC) casting process. The results show that under the low frequency electromagnetic field (25 Hz, 32 mT) the microstructures of LFEC ingot from the border to the center on the cross section are all equiaxed grains, and the grains are much finer and more uniform than that of DC ingot. The magnetic flux density plays an important role in the microstructure formation of LFEC ingots. With increasing the magnetic flux density from 0 mT to 32 mT, grains become finer (from about 120 μm to 30 μm) and more uniform. While, with increasing the magnetic flux density from 32 mT to 46 mT, the grains change much slowly. In the range of experimental parameters, the optimum magnetic flux density for LFEC process is found to be 32 mT.
Key words: Al-Zn-Mg-Cu alloy; DC casting; low frequency electromagnetic field; magnetic flux density; microstructure
1 Introduction
Superhigh strength aluminum alloys are important materials in the aerospace industries, because of their light density and high strength. With the development of aerospace industry, larger size products with higher strength, higher toughness and higher corrosion resistance are needed[1-3]. Superhigh strength aluminum alloy containing high element content is difficult to be cast[4]. ZHANG et al[5] made superhigh strength aluminum alloy ingot by spray forming process, and got finer and uniform microstructures which are helpful for deformation and increasing properties, and the final tensile strength is more than 800 MPa. Based on VIVES[6-7], a new technique, low frequency electromagnetic casting (LFEC) process was developed by CUI and his co-workers[8-11]. In this process, a low frequency electromagnetic field was used to control the flow and temperature fields. In this paper, the LFEC was used to make superhigh strength aluminum alloy ingots and the effects of electromagnetic field intensity on the microstructures and as-cast mechanical properties were studied.
2 Experimental
Al-9.8%Zn-2.35%Mg-2.3%Cu-0.14%Zr alloy was used in this experiment. The d200 mm ingots were produced by LFEC process at melt temperature of 730 ℃, and the casting speed of 80 mm/min. The schematic diagram of the LFEC process is shown in Fig.1.
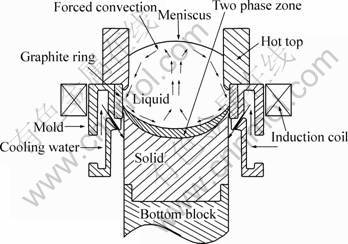
Fig. 1 Schematic diagram of LFEC process
The electromagnetic field was applied by an 80 turns water-cooling copper coil surrounding the mold made of stainless steel.
A graphite ring with inside diameter of 204 mm, outside diameter of 216 mm and height of 30 mm was set in the mold. During casting the frequency was kept at 25 Hz and the magnetic flux density was changed from 0, 17.1, 25, 32, 39.5, to 46 mT in sequence. The samples were ground and polished and then etched with dilute Keller’s reagent (2 mL HF, 3 mL HCl, 5 mL HNO3 and 190 mL H2O). Microstructures were observed under optical microscope (Leica DMR). The grain size analyses were carried out from the pictures taken using software SISCIA S8.0. The mechanical tests were conducted at room temperature. The tensile strength was measured using CMT5105 universal test machine at a constant ram velocity of 1 mm/min. All the cylindrical samples were parallel to the axes of the ingots. The average value of three tests results was used as final value.
3 Experiment results
3.1 Microstructures of DC and LFEC ingots
As shown in Fig.2, the microstructure of the LFEC ingots is much finer and more uniform than that of DC ingots. Figs.2(a) and (c) show the coarse dendritic microstructures of DC ingot. When cast under an electromagnetic field of 25 Hz and 32 mT, both the border and the center microstructures are dominated by very fine and uniform equiaxed grains as shown in Figs.2(b) and (d). In order to determine whether the microstructures of LFEC ingots are equiaxed grains, the electron back scattering diffraction (EBSD) technique was used. Fig.3 shows the EBSD image of LFEC ingot, which shows that the grains are all equiaxed grains. So, the microstructures of LFEC ingot from the border to the center are all fine equiaxed grains and are more uniform than that of DC ingot.
3.2 Effect of magnetic flux density on microstructures
Because the microstructures of LFEC ingots are uniform as shown above, only the microstructures at the center of the ingots produced at different magnetic flux densities are reported. The effects of the magnetic flux density on the microstructures can be visualized from Fig.4. With increasing the magnetic flux density from 0 mT to 17.1 mT, the grains change from very coarse equiaxed and dendritic grains to finer and more uniform equiaxed grains. When increasing the magnetic flux density from 17.1 mT to 25 mT and then to 32 mT, the grains become much finer and more uniform. While, with increasing the magnetic flux density from 32 mT to 39.5 mT and then to 46 mT, the grain morphologies do not show apparent difference. The effect of magnetic flux density on average grain size of the center part of ingots is shown in Fig.5.
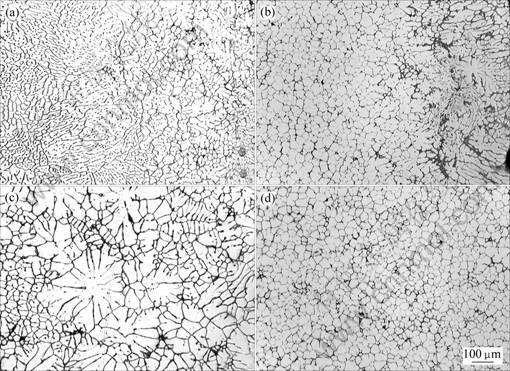
Fig. 2 Microstructures of DC and LFEC ingots: (a), (b) Border; (c), (d) Center; (a), (c) DC; (b), (d) LFEC
3.3 Effect of electromagnetic field on mechanical properties of as-cast ingots
As shown in Fig.6, the fracture strength of LFEC ingots at different locations is almost at the same level, while the fracture strength of DC ingots decreases form border to center. It is clear that the fracture strength of LFEC ingots is higher than that of DC ingots. For DC ingots no significant plastic deformation has taken place before fracture, while the elongation of the LFEC ingot covers the range of 1.3%-2.1%, which is much larger than that of the DC ingots (0.2%). Thus, with applying low frequency electromagnetic field the fracture strength and elongation of the ingot increase.
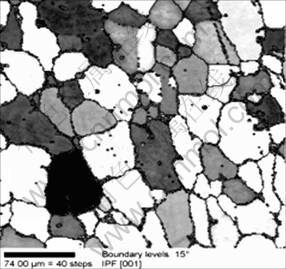
Fig. 3 Microstructure of LFEC ingot measured by EBSD
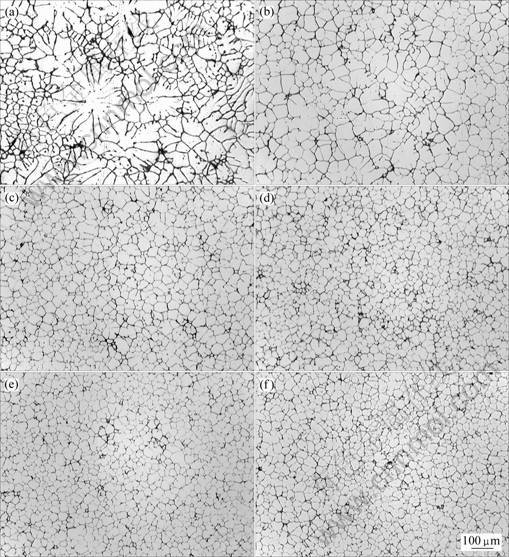
Fig. 4 Effect of magnetic flux density on microstructures of central part of ingots: (a) 0 mT; (b) 17.1 mT; (c) 25 mT; (d) 32 mT; (e) 39.5 mT; (f) 46 mT
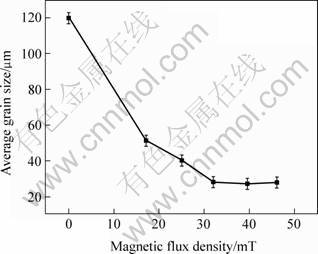
Fig.5 Effect of magnetic flux density on average grain size of center part of ingots
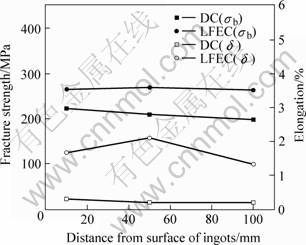
Fig.6 Effect of LFEC on fracture strength and elongation of ingots
4 Discussion
In the LFEC process the alternative current generates a time varying magnetic field in the melt, which, in turn, gives rise to an induced current in melt and ingot. Therefore, the melt is subjected to electromagnetic body forces caused by the interaction of the induced current and the magnetic field. The Lorentz force density consists of two parts [6]. One is a rotational component which results in a forced convection and flow in the melt, the other is a potential force balanced by static pressure of the melt, resulting in the formation of a convex surface (meniscus) and a decrease in the contacting pressure on the mold (soft contact).
The forced convection makes the low temperature melt near the mold flow into center, and high temperature melt into surface layer, which makes the temperature fields of the whole melt become more uniform and little lower than liquidus. This is helpful for mass nuclei formation in the liquid pool. It is also considered that the forced convection increases nucleation near the mold and liquid surface and accelerates nuclei separating. The broken dendrite crystal which is caused by electromagnetic field is another important source of nuclei. FLEMINGS[12] studied the break of secondary dendritic arms and block nucleation and concluded that the break of secondary dendritic arms increases the nucleating centers. Under electromagnetic fields the dendritic arm is broken by the forced convection and the transformation from broken blocks to nucleating center increases. The forced convection not only increases nucleation but also reduces nuclei remelting, so the microstructures of LFEC ingot are much finer than that of DC ingot, as shown in Fig.2.
Under electromagnetic fields, both the temperature fields and solute fields become uniform, and the constitutional supercooling near the liquid/solid interface is decreased, so the grains grow under a uniform and isotropic condition. If there is a little fluctuation on the interface, it will disappear when it encounters superheat melt. The movement of the nuclei is accelerated due to the forced convection with the application of the electromagnetic field. In the process of moving, the nuclei bump and frictionate each other. The grains also have a spin motion[13]. If there is a spike on the spun grain it will be remelted because of its high energy. Based on the solidification theories[14-15], all these conditions are helpful for the formation of equiaxed grains. So, under low frequency electromagnetic fields the grains grow spherically and the grains of LFEC ingot are equiaxed or nearly equiaxed.
With the increase of magnetic flux density, the electromagnetic field intensity in the melt becomes stronger and the forced convection becomes also stronger, which results in the formation of more nuclei and more nuclei moving to the inner melt. With the increase of magnetic flux density the microstructures become finer and more uniform, as shown in Figs.4 and 5. But when the magnetic flux density increases to a certain degree, the grain morphologies show no apparent difference. It is considered there are two reasons. One is LFEC reduces the contact area and pressure by the forced convection so that the premier cooling is reduced. The other is that Joule heat increases with increasing the magnetic flux density, which is harmful for increasing nucleation. If the magnetic flux density is too high, we can not get the finest microstructures. In this experiment, the optimum magnetic flux density for LFEC process is 32 mT.
The LFEC process refines microstructures greatly and makes grains be equiaxed, resulting in forming less amount of the eutectic phases and smaller constituent particles, which is helpful for improving mechanical properties. So the tensile properties of LFEC ingots are much higher than those of DC ingot, as shown in Fig.6.
5 Conclusions
1) Under the low frequency electromagnetic field (25 Hz, 32 mT) the microstructures of LFEC superhigh strength Al-Zn-Mg-Cu alloy ingot from the border to the center are all fine equiaxed grains and are much finer and more uniform than that of DC ingot.
2) Magnetic flux density plays an important role in the microstructures of LFEC ingots. With increasing the magnetic flux density the grains become finer; while, with increasing the magnetic flux density from 32 mT to 46 mT the grains change slowly. In the range of experimental parameters, the optimum magnetic flux density for LFEC process is 32 mT.
3) For the new superhigh strength Al-Zn-Mg- Cu-Zr alloy, the as-cast properties of LFEC ingot are higher than those of DC ingot.
References
[1] HEINZ A, HASZLER A, KEIDEL C, MOLDENHAUER S, BENEDICTUS R, MILLER W S. Recent development in aluminum alloys for aerospace applications[J]. Mater Sci Eng A, 2000, 280: 102-107.
[2] LI C G, WU S J, DAI S L, YANG S J. Application and development of advanced aluminum alloy in aerospace industry[J]. The Chinese Journal of Nonferrous Metals, 2002, 12(Special): 14-21. (in Chinese)
[3] WU Y L, FROSE F H, ALVAREZ A, LI C G LI, LIU J. Microstructure and properties of a new super-high-strength Al-Zn-Mg-Cu alloy C912[J]. Materials and Design, 1997, 18: 211-215.
[4] PARAMATMUNI R K, CHANG K M, KANG B S, LIU X B. Evaluation of cracking resistance of DC casting high strength aluminum ingots[J]. Mater Sci Eng A, 2004, 379: 293-301.
[5] ZHANG Yong-an, ZHU Bao-hong, LIU Hong-wei, ZHANG Zhi-hui, XIONG Bai-qing, SHI Li-kai. Influence of Zn content on microstructure and properties of spray-formed 7××× series aluminum alloys[J]. The Chinese Journal of Nonferrous Metals, 2005, 15(7): 1013-1018. (in Chinese)
[6] VIVES C. Electromagnetic refining of aluminum alloys by the CERM process: part Ⅰ. Working principle and metallurgical results [J]. Metall Trans B, 1989, 20: 623-629.
[7] VIVES C. Electromagnetic refining of aluminum alloys by the CREM process: part Ⅱ. Specific practical problems and their solutions[J]. Metall Trans B, 1989, 20: 631-643.
[8] ZHANG B J, CUI J Z, LU G M, ZHANG Q, BAN C Y. Effect of frequency on microstructure of electromagnetic casting 7075 aluminum alloy[J]. Acta Metallurgica Sinica, 2002, 38: 215-218. (in Chinese)
[9] ZHANG B J, CUI J Z, LU G M, ZHANG Q. Effect of electromagnetic field on macrosegregation of continuous casting 7075 aluminum alloy[J]. Journal of Northeastern University (Natural Science), 2002, 23: 968-971. (in Chinese)
[10] DONG J, CUI J Z, LIU X T, ZHAO Z H, BAO W P. Super-high strength 7A60 Al alloy by low frequency electromagnetic cast(1): As-cast structures of billets with diameter of 0.2 m[J]. The Chinese Journal of Nonferrous Metals, 2003, 13(6): 1494-1499. (in Chinese)
[11] ZUO Yu-bo, CUI Jian-zhong, DONG Jie, YU Fu-xiao. Effect of low frequency electromagnetic field on the as-cast microstructures and mechanical properties of superhigh strength aluminum alloy[J]. Mater Sci Eng A, 2005, 408: 176-181.
[12] FLEMINGS M C. Principles of control of soundness and homogeneity of large ingots[J]. Metall Trans A, 1991, 22: 957-962.
[13] ZHANG Q, LU G M, CUI J Z, ZHANG B J. Formation mechanism of non-dendritic structure of aluminum alloy produced by semi- continuous casting of CREM process[J]. Acta Metallurgica Sinica, 2001, 37: 873-876. (in Chinese)
[14] YU Yong-ning. Principles of Metallography[M]. Beijing: Metallurgical Industry Press, 2000: 243-249.
[15] ROBERT E, HILL R. Physical Metallurgy Principles[M]. New Jersey: D Van Nostrand Company, 1964: 377-389.
(Edited by YUAN Sai-qian)
Foundation item: Project(2005CB623707) supported by the National Basic Research Program of China
Corresponding author: ZUO Yu-bo; Tel: +86-24-83687734; E-mail: zuoyubo@epm.neu.edu.cn